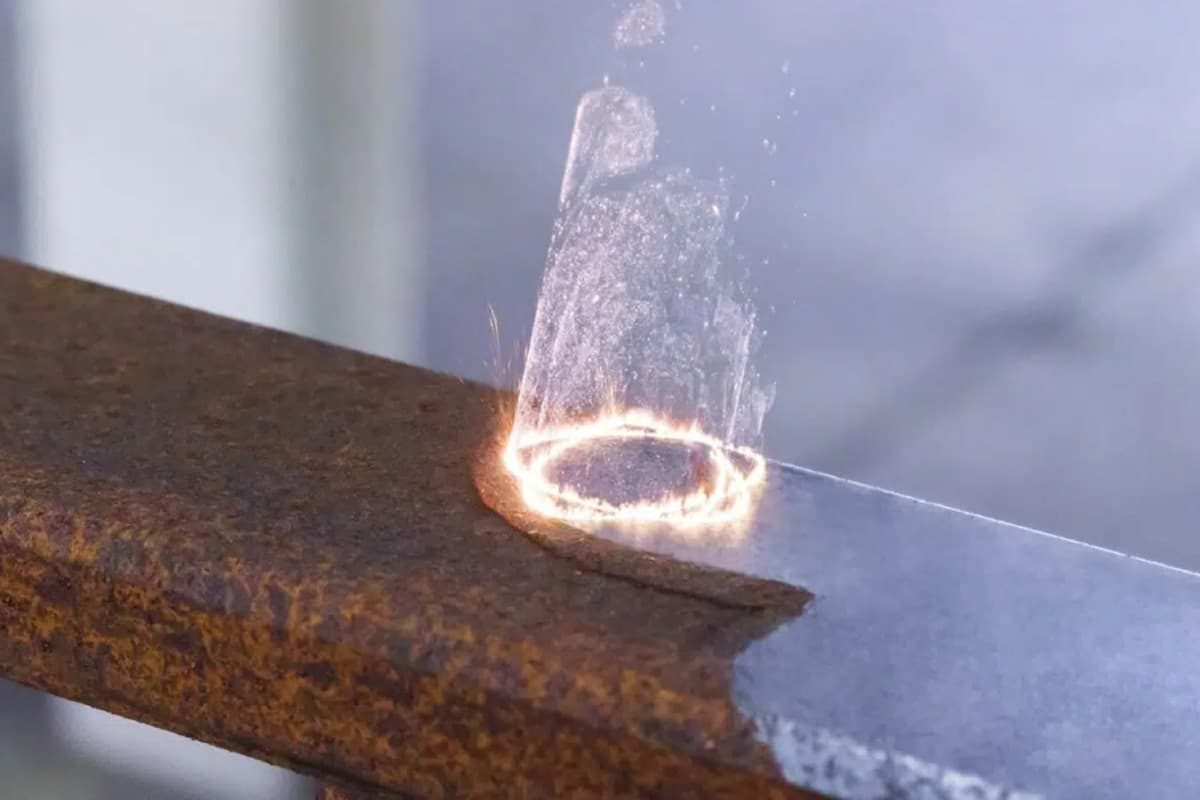
レーザー洗浄は表面粗さと清浄度にどのような影響を与えますか?
レーザー洗浄は、高エネルギー密度、方向制御可能、強力な収束能力などのレーザービームの特性を利用して、汚染物質と基板間の結合力を破壊したり、汚染物質を直接気化させて汚染物質を除去したりすることで、汚染物質と基板間の結合力を低下させ、ワークピースの表面を洗浄する効果を実現します。ワークピース表面の汚染物質がレーザーのエネルギーを吸収すると、熱によって急速に気化したり、瞬間的に膨張したりして、汚染物質と基板表面間の力を克服します。熱エネルギーの増加により、汚染物質の粒子が振動して基板表面から剥がれます。レーザー洗浄は、基板表面を損傷することなく、基板表面の粒子構造と配向を変更できるだけでなく、基板の表面粗さを制御することもできるため、基板表面の総合的な性能が向上します。さまざまな材料のレーザーパラメータを調整することで、材料表面の粗さと清浄度に影響を与え、洗浄効果を最大化できます。
目次
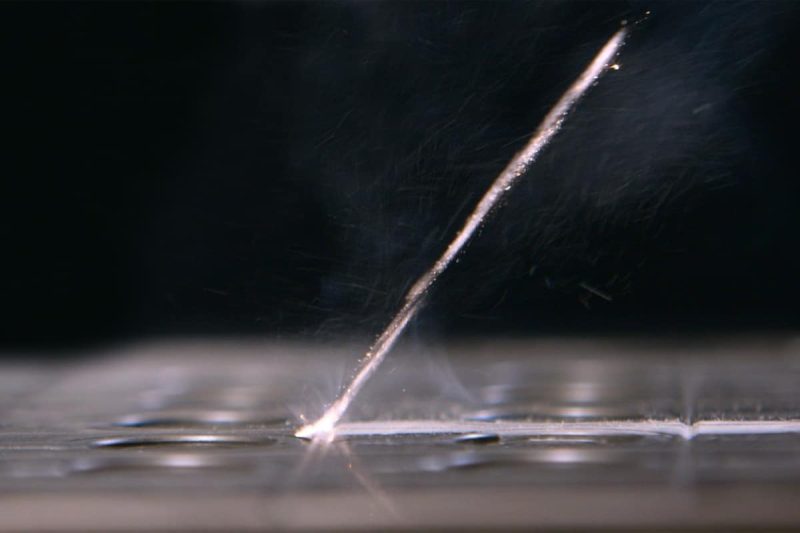
表面粗さと清浄度を理解する
表面粗さと清浄度を理解することで、レーザー洗浄機が材料表面に与える影響を理解するのに役立ちます。
表面粗さ
表面粗さは、間隔が狭く、山と谷が小さい部品の機械加工面の粗さを指します。通常、2 つの波の山または 2 つの波の谷の間の距離 (波の距離) が小さいと定義されます。一般に、波の距離は 1 mm 以下です。また、マイクロ輪郭の測定値として定義することもでき、一般にマイクロエラー値として知られています。エンジニアリングでは、表面粗さは、公称形状からの表面の小さな局所偏差として定義されます。これらの偏差は、製造プロセス (機械加工、鋳造など) によって引き起こされる場合もあれば、自然に発生する場合もあります (酸化、腐食など)。これらの局所的な表面の不規則性は、エンジニアリング表面の機能と性能に大きな影響を与える可能性があります。
表面の清浄度
表面清浄度とは、部品、アセンブリ、完成機械の特定の部分が不純物によって汚染されている度合いを指します。指定された方法を使用して指定された特性部分から収集された不純物粒子の品質、サイズ、量で表されます。ここで言う「指定された部分」とは、製品の信頼性を危険にさらす特性部分を指します。ここで言う「不純物」には、製品自体に残留する不純物、外部から混入する不純物、製品の設計、製造、輸送、使用、保守中にシステムによって生成される不純物がすべて含まれます。
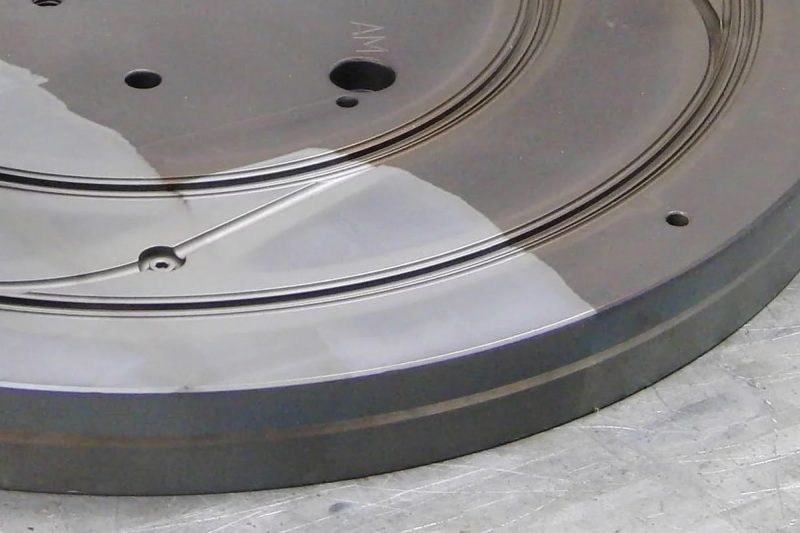
レーザー洗浄による表面粗さへの影響
クリーニング機構
レーザー洗浄のメカニズムは、アブレーションと熱効果の2種類に大別できます。アブレーションとは、レーザーの作用により材料表面の不純物が蒸発または分解されることを指します。レーザー洗浄は、材料自体に熱効果をもたらしません。レーザー洗浄の熱効果とは、レーザー照射下で不純物が熱効果を受け、除去されることを指します。具体的な原理は次のとおりです。
アブレーション
各材料には、分子結合に基づいた特定のアブレーションしきい値があり、このしきい値は他の材料とは異なります。レーザーが表面に当たると、そのエネルギーが加熱され、存在する汚染物質が蒸発またはアブレーションされます。レーザービームが表面と相互作用すると、不要な物質が蒸発またはアブレーションされます。つまり、レーザーによって生成された強力な熱によって、汚染物質が蒸発または分解されます。このアブレーションプロセスによって衝撃波が発生します。汚染物質が突然膨張して加熱されると、衝撃波が発生し、表面から汚染物質が急速に除去されます。これらの衝撃波は、不要な物質を効果的に分離して排出するための強力な推進力として機能します。
熱の影響
レーザー洗浄機の熱効果とは、レーザー洗浄機がレーザービームを集束させ、高エネルギー密度のビームを対象表面に照射するプロセスを指します。表面の汚れ、コーティング、または酸化物がレーザーエネルギーを吸収した後、エネルギーを熱エネルギーに変換します。レーザーエネルギーを吸収した後、材料の表面は急速に加熱され、高温領域を形成します。この高温により、汚れやコーティングが緩んだり、分解したり、揮発したりして、その後の物理的除去が容易になります。熱効果はレーザー洗浄の効果に直接影響します。高温は汚れの分解と蒸発を加速し、洗浄プロセスをより徹底的かつ効率的にします。同時に、熱効果は表面の粗さと接着を改善し、その後の洗浄と処理を容易にすることもできます。レーザー洗浄では、材料や表面に損傷が発生しないように、熱効果の影響を制御して最適化する必要があります。レーザー出力、パルス持続時間、繰り返し周波数などのパラメータを調整することで、熱効果の大きさと深さを正確に制御し、さまざまな洗浄ニーズと材料の種類に適応できます。要約すると、レーザー洗浄機の熱効果とは、レーザーエネルギーによって生成された熱エネルギーを使用して、洗浄プロセス中に汚れの除去を加速することを指します。
レーザーパラメータ
レーザー洗浄は、基板表面を損傷することなく、基板表面の粒子構造と配向を変更し、基板の表面粗さを制御することで、基板表面の総合的な性能を向上させることができます。レーザー洗浄技術を適用する場合、最適な洗浄効果を得るために適切なレーザーパラメータを選択する必要があります。ここでは、主にパルス持続時間、滑らかさ、スポットサイズ、ビーム品質が表面粗さに与える影響について説明します。
パルス持続時間
- より短いパルス持続時間: 短パルスレーザー (ナノ秒レーザーなど) では、エネルギー放出をより正確に制御できるため、基板への熱の影響が軽減されることがよくあります。この短いパルスは、材料表面の熱拡散と過熱を軽減し、基板への損傷と粗さの増加を軽減するのに役立ちます。この場合、レーザーエネルギーは主に汚染物質に集中し、基板表面の微細構造を大幅に変更することなく、表面汚染をより効果的に除去できます。
- より長いパルス持続時間: より長いパルス (マイクロ秒以上など) は、熱拡散が大きくなり、基板表面の熱影響領域が拡大する可能性があります。これにより、材料表面で溶融層、蒸発、またはアブレーションが形成され、表面粗さが増加する可能性があります。また、長いパルスは、過剰な材料除去や不均一な熱効果を引き起こし、表面粗さが増加する可能性があります。
パルス持続時間はレーザー洗浄において重要な役割を果たします。実際のアプリケーションでは、特定の材料処理要件を満たすために、実験を通じて最も適切なパルス持続時間を見つける必要があります。
脈拍の滑らかさ
- 高いパルス平滑性: レーザーパルスのエネルギー出力がより均一かつ安定していることを意味します。これにより、通常、材料の表面処理における熱の影響と局所的な過剰除去が軽減され、滑らかな表面と低い粗さが得られます。
- パルスの滑らかさが低い: パルスエネルギーが不安定になり、材料表面の加熱が不均一になり、溶融層や蒸発が増え、粗さが増加する可能性があります。
一般的に、パルスの滑らかさが高いほど表面粗さは低減されます。
スポットサイズ
- 高精度かつ繊細な加工を必要とするアプリケーション(マイクロマシニングや精密洗浄など)では、より小さなスポット サイズの方が適しています。
- 広範囲の洗浄や処理(広範囲の錆や汚染の除去など)の場合は、スポット サイズを大きくすると効果的です。
スポットサイズは表面粗さに大きな影響を与えます。実際のアプリケーションでは、特定の材料処理要件を満たすために、実験を通じて適切なスポットサイズを見つける必要があります。
ビーム品質
- 高いビーム品質: 高いビーム品質とは、レーザービームの発散角が小さく、エネルギー分布が均一であることを意味します。これにより、より一貫した処理結果が得られ、局所的な過熱や溶融が軽減され、表面粗さが軽減されます。ビーム品質が高いほど、より正確な処理が実現し、小さな構造や特徴を処理でき、粗さがさらに軽減されます。
- ビーム品質が低い: ビーム品質が低いと、レーザービームのエネルギー分布が不均一になり、スポットサイズが大きくなり、熱の影響を受ける領域が広くなり、表面処理が不均一になり、粗さが増す可能性があります。ビーム品質が低いと、処理の精度と詳細パフォーマンスに影響し、表面処理の欠陥と粗さが増加します。
実際のアプリケーションでは、ビーム品質とその関連パラメータは、理想的な表面粗さを達成するための最適な設定を見つけるために実験を通じて調整されます。高品質のビームは、低い粗さを実現する可能性が高くなります。
材料特性
レーザー洗浄プロセス中、材料自体の特性が表面粗さに大きな影響を与え、主に以下の側面に反映されます。
熱伝導率
- 高い熱伝導率: 熱伝導率の高い材料は、レーザー作用点から周囲にレーザー誘起熱をより速く拡散し、局所的な熱蓄積を軽減します。これにより、局所的な溶融と蒸発の程度が軽減され、表面粗さが軽減されます。材料の熱伝導率が高いため、レーザーエネルギーがより均等に分散され、温度勾配によって生じる表面の凹凸が軽減されます。
- 熱伝導率が低い: 熱伝導率が低い材料では、レーザーエネルギーが材料の表面領域に集中し、熱影響部が大きくなり、局所的な溶融、蒸発、またはアブレーションが発生し、表面粗さが増します。熱伝導率が低い材料では、熱応力が大きくなり、材料の変形や亀裂が発生し、さらに粗さが増すこともあります。
吸収係数
- 高い吸収係数: 吸収係数が高いということは、材料がレーザー エネルギーを効果的に吸収し、局所的な加熱効果が向上することを意味します。適切なエネルギー吸収は汚染物質を効果的に除去するのに役立ちますが、吸収率が高すぎると過度の加熱が発生し、粗さが増す可能性があります。吸収係数が高いと、一般に洗浄効率が向上し、汚染物質がより徹底的に除去されるため、熱効果が制御されていれば、より滑らかな表面を実現できます。
- 吸収係数が低い: 吸収係数が低い材料はレーザーの吸収率が低いため、レーザーエネルギーが汚染物質の除去や表面処理に効果的に使用されず、洗浄効果が低下し、より多くのエネルギーやより長い処理時間が必要になる場合があります。吸収係数が低いと、洗浄結果が悪く、汚染物質の除去が不完全になり、表面の品質と粗さに影響する可能性があります。
材料の熱伝導率と吸収係数は、レーザー洗浄における表面粗さに大きな影響を与えます。これらの特性を理解して考慮することで、レーザー洗浄プロセスを最適化し、レーザーパラメータを調整して、望ましい表面品質を実現できます。

レーザー洗浄による表面清浄度への影響
選択的汚染物質除去
レーザー洗浄は、さまざまな材料の表面からさまざまな種類の汚染物質を除去し、従来の洗浄では達成できないレベルの清浄度を実現します。また、材料の表面を傷つけることなく、材料の表面の汚染物質を選択的に洗浄することもできます。レーザー洗浄は効率が高く、時間を節約できます。
特定の汚染物質の洗浄
レーザー洗浄では、波長、パルス持続時間、エネルギー密度などのレーザーパラメータを正確に制御して、特定の種類の汚染物質を効果的に除去できます。たとえば、レーザーの波長とエネルギー密度を調整することで、錆、油、コーティング、その他の汚染物質を具体的に洗浄できます。この選択的除去機能により、レーザー洗浄では、基板を損傷することなく、汚染物質をターゲットに除去できるため、表面の清浄度が向上します。
残留廃棄物なし
レーザー洗浄プロセスにおける汚染物質は通常、直接ガス化または蒸発するため、従来の洗浄方法でよく見られる廃棄物残留の問題が軽減されます。汚染物質はレーザーの高エネルギー下ですぐにガスに変換されるため、レーザー洗浄によって生成される廃棄物の量は少なく、取り扱いが容易です。この機能により、化学残留物や固形廃棄物が表面の清浄度に与える影響を心配することなく、洗浄後の表面が清潔であることが保証されます。
基板の完全性の維持
レーザー洗浄機 さまざまな分野での幅広い用途に適しており、基材の完全性を維持しながら、さまざまな汚染物質やコーティングを効果的に洗浄できます。
非破壊洗浄
レーザー洗浄は、機械的な接触や摩耗を必要とせず、基板への物理的損傷を効果的に低減できる非接触洗浄技術です。レーザービームは、基板に直接摩耗や傷を与えることなく、汚染層に正確に作用し、基板の元の表面状態を維持し、洗浄プロセス中に基板の完全性と表面の清浄性を確保します。
最小熱影響ゾーン
レーザー洗浄プロセスでは、レーザービームを高精度に制御することで、熱影響部を最小限に抑えます。レーザーパルスの持続時間とエネルギー密度を適切に制御することで、基板に大きな影響を与えることなく、熱を汚染物質に集中させることができます。これにより、熱拡散による基板表面の変形、溶解、その他の熱影響を回避でき、洗浄後の表面の清浄度をさらに確保できます。
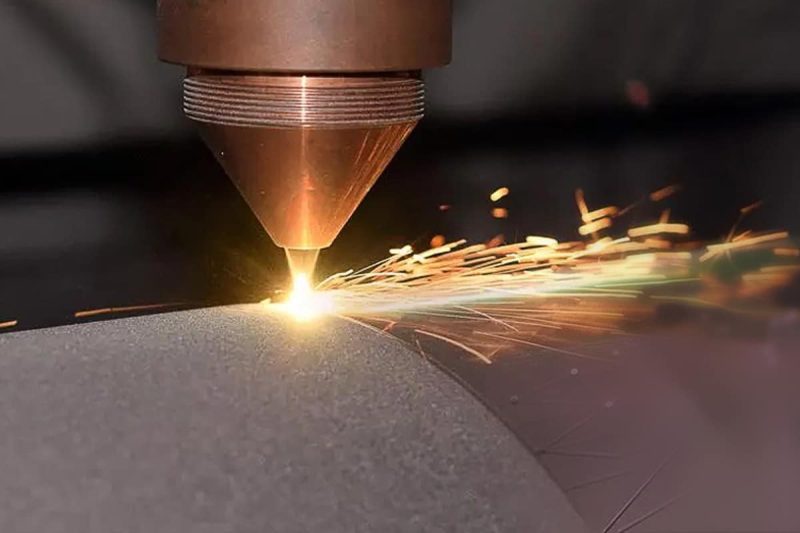
レーザー洗浄のための表面粗さと清浄度の最適化
材料特性と適合性
- 材料の種類: 適切なレーザーの種類とパラメータを選択するために、融点、熱伝導率、反射率、吸収係数など、洗浄する材料の物理的および化学的特性を理解します。
- 適合性分析: レーザー洗浄プロセスと材料の適合性を評価し、レーザーが材料を損傷したり表面特性を変えたりしないことを確認します。
レーザーパラメータの最適化
- レーザー波長の選択:材料の吸収特性に応じて適切なレーザー波長を選択し、洗浄効率と効果を向上させます。
- 出力とエネルギー密度: レーザーの出力とエネルギー密度を調整して、材料自体を損傷することなく汚染物質を効果的に除去できるようにします。
- パルス幅と周波数: レーザーのパルス幅と周波数を最適化して、最高の洗浄効果と表面粗さの制御を実現します。
- スキャン速度とオーバーラップ率: レーザー ビームのスキャン速度とオーバーラップ率を調整して、均一な洗浄を実現し、表面仕上げを向上させます。
プロセス検証と品質管理
- 実験検証: さまざまなパラメータの組み合わせをテストして最適な洗浄ソリューションを見つけるために、実験室条件下でプロセス検証が実行されます。
- 品質検査:光学顕微鏡、走査型電子顕微鏡(SEM)などの検査方法を使用して、洗浄後の表面粗さや清浄度を評価します。
- 標準化されたプロセス: 洗浄プロセスの再現性と一貫性を確保するために、標準的な操作手順と品質管理基準を確立します。
- フィードバックと改善: 品質検査結果と実際のアプリケーションのフィードバックに基づいて、洗浄プロセスを継続的に最適化および調整します。
オペレーターのトレーニングとスキル開発
- トレーニング プラン: オペレーターがレーザー洗浄と機器操作の基本原理を理解できるように、詳細なトレーニング プランを作成します。
- スキル向上: 実践的な操作と技術交流を通じて、オペレーターがレーザーパラメータ調整とプロセス最適化のスキルを習得できるように支援します。
- 安全な操作: 起こりうる安全上の危険を特定して防止し、レーザー機器の安全な使用を確保するためにオペレーターをトレーニングします。
- 継続教育: 技術の進歩に合わせてオペレーターのスキル レベルを維持するために、定期的に技術アップデートとトレーニング コースを実施します。
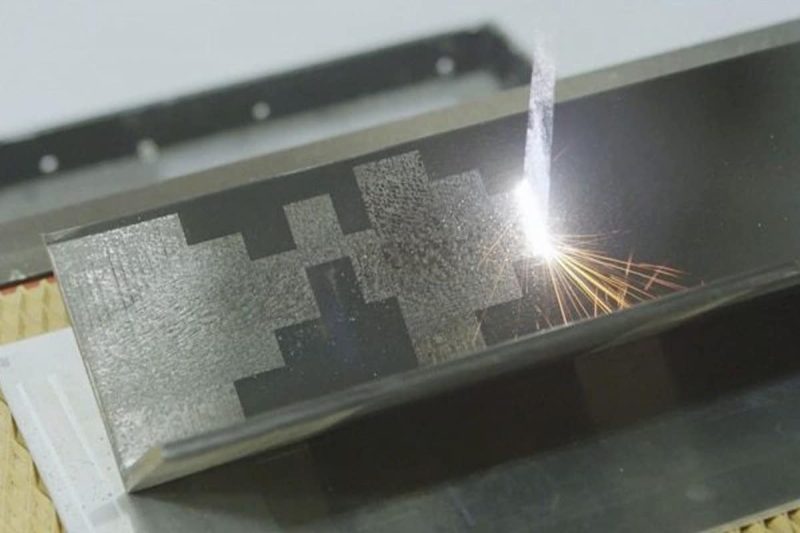
要約する
レーザー洗浄は、材料の表面粗さと清浄度を効果的に改善できる、効率的で環境に優しい表面処理技術です。材料特性を理解し、レーザーパラメータを最適化し、高度な表面分析技術を適用することで、高品質のレーザー洗浄効果を実現できます。工業生産では、継続的なプロセス改善とオペレーターのトレーニングの強化により、レーザー洗浄の応用価値がさらに高まります。
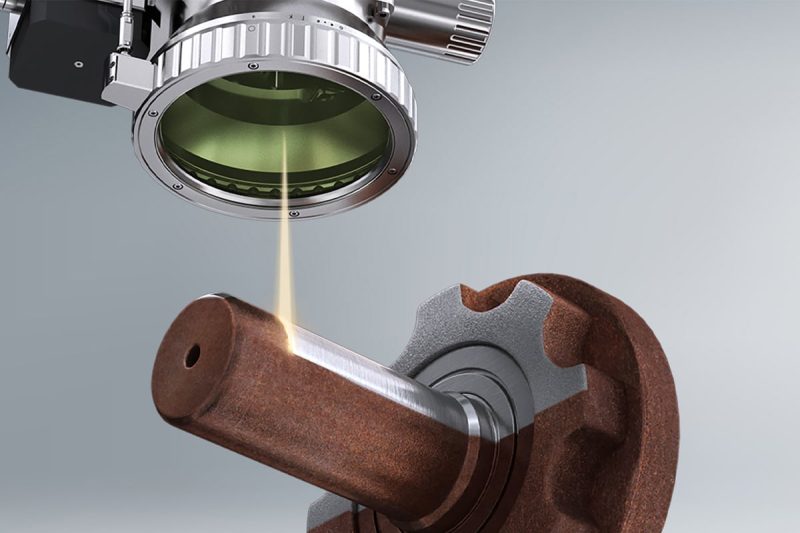
レーザー ソリューションを入手する
適切なレーザー洗浄機を選ぶことで、電力消費を最適化し、高い運用効率を実現できます。信頼できるサプライヤーと協力することで、高度な技術、カスタマイズされたアドバイス、継続的なサポートを利用できます。AccTek Laser では、さまざまな産業ニーズを満たすように設計された包括的なレーザー洗浄装置を提供しています。当社の専門家は、材料の種類、厚さ、生産量などの要素を考慮して、最もエネルギー効率の高いモデルと構成を選択するお手伝いをします。また、高効率レーザージェネレーター、インテリジェント冷却システム、エネルギー管理ソフトウェアなどの最先端の機能を提供し、パフォーマンスを最大化し、エネルギー使用量を最小限に抑えます。さらに、当社のチームは定期的なメンテナンスサービスと技術サポートを提供し、機器を最高の効率に保ちます。当社と提携することで、大幅なエネルギー節約、運用コストの削減、持続可能性への取り組みの強化を実現できます。ご質問がある場合は、お早めにお問い合わせください。AccTek Laser は、すべてのお客様に完璧なレーザーソリューションを提供することに尽力しています。
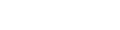
連絡先
- [email protected]
- [email protected]
- +86-19963414011
- No. 3 ゾーン A、Lunzhen 工業地帯、玉城市、山東省。
レーザー ソリューションを入手する