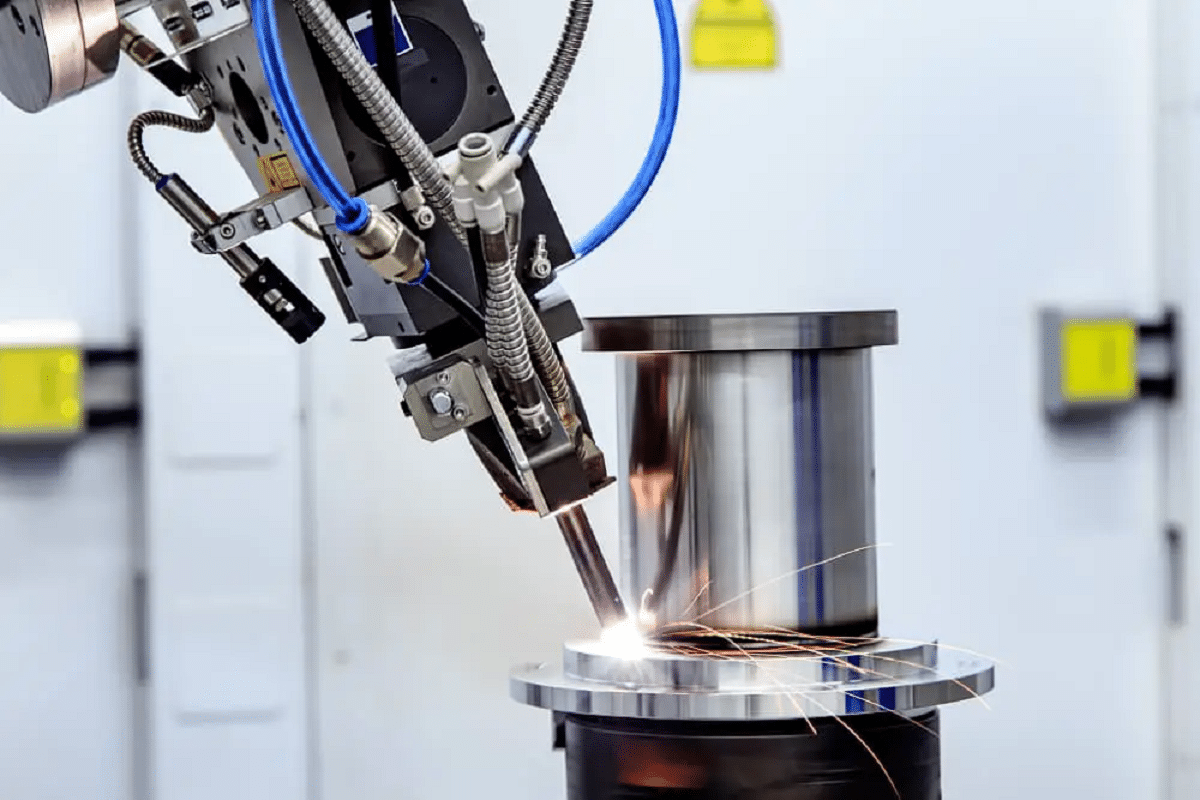
レーザー溶接ではどのような溶接欠陥が発生する可能性がありますか?どうやって解決すればいいでしょうか?
レーザー溶接は、高効率、高精度、優れた効果、自動化の容易な統合などの利点により、さまざまな業界で広く使用されています。軍事、医療、航空宇宙、新エネルギーなどの産業を含む工業生産と製造において重要な役割を果たしています。ただし、どのような加工方法でも、その原理とプロセスが適切に理解されていない場合、欠陥や不良品が発生する可能性があります。レーザー溶接も例外ではありません。レーザー溶接の価値を最大限に引き出し、完璧な外観の高品質な製品を生産するには、これらの落とし穴を理解し、回避する方法を学ぶことが重要です。
目次
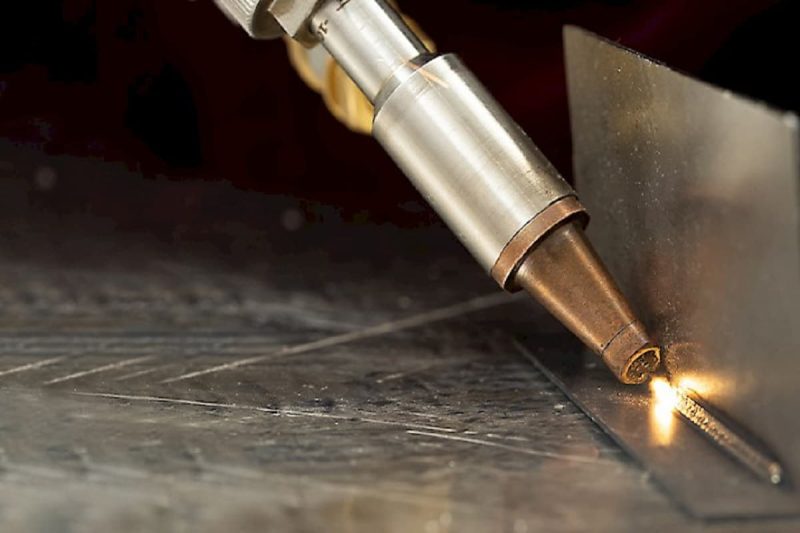
レーザー溶接の原理
レーザー溶接は、レーザー材料加工技術の重要な用途の 1 つです。レーザー溶接は、伝導制限溶接と深穴溶接という 2 つの根本的に異なるモードで動作します。溶接プロセス中に熱伝導が行われます。つまり、レーザー放射によって表面が加熱され、表面の熱が熱伝導によって内部に拡散します。レーザーのパルス幅、エネルギー、ピークパワーと繰り返し周波数、元素の溶融、その他のパラメーターを制御することにより、金属表面に特定の溶融池が形成されます。熱によって材料が溶けて 2 つの表面の間に溶接ビードが形成され、溶接が完了します。
レーザー溶接は高い溶接精度と溶接品質を誇ります。レーザー自体はほとんど熱を発生しないため、レーザー溶接後に生じる溶接継ぎ目も比較的小さく、レーザー溶接は特にエレクトロニクスやガラス/金属シールなどの薄い材料に適しています。一方、厚い材料を溶接する場合、四角いエッジの部品間に狭くて深い溶接が行われます。さらに、レーザーは信じられないほどの高温 (摂氏数千度) に達する可能性があるため、極端な温度や過酷な環境に耐えられる、非常に強力で耐久性のある溶接を行うことができます。
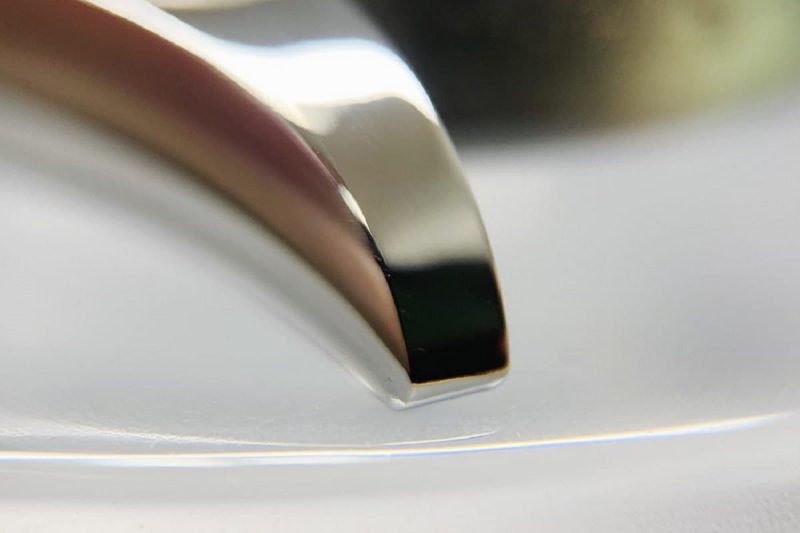
レーザー溶接でよくある溶接欠陥とその解決方法
レーザー溶接は、高効率、高精度、良好な効果、容易な自動化、統合などの利点がありますが、不適切な操作は製品の重大な品質欠陥につながる可能性もあります。これらの欠陥をよく理解してこそ、レーザー溶接の価値が最大限に発揮され、見た目も美しく高品質な製品を加工することができます。レーザー溶接で起こりやすい溶接欠陥は以下の8つです。
気孔率
ポアはレーザー溶接で発生しやすい欠陥の一つです。レーザー溶接における気孔は、グリース、油、酸化物、吸収された水蒸気、切削液の残留物などの基板または表面の汚れ、または不十分な前洗浄によって発生する可能性があります。レーザー溶接プールは深くて狭く、冷却速度が遅いためです。速いです。液体溶融池で発生したガスは表面汚染により逃げる時間がなくなり、気孔が形成されやすくなります。ただし、レーザー溶接は急速に冷却され、生成される気孔は一般に従来の溶融溶接よりも小さくなります。
レーザー溶接での気孔発生を回避するには:
- 適切なシールド ガスを確保する: 高品質のシールド ガス (通常はアルゴンまたはヘリウムの混合物) を使用して、大気ガスから適切に保護します。
- ガス流の最適化: 適切なシールドガスの流れと方向を設定して、溶接領域を最大限に効果的に保護します。
- ワークピースの表面を洗浄します。ガスの閉じ込めを防ぐために、溶接する表面を徹底的に洗浄して、油、グリース、錆、汚れなどの汚染物質を除去します。必要に応じて、溶剤洗浄、機械洗浄、化学洗浄などの適切な洗浄方法を使用してください。
- 適切なジョイントの準備: ガスが閉じ込められる可能性のある隙間ができないように、適切なジョイントの取り付けと位置合わせを確認します。該当する場合は、バックパージ技術を使用してガスの閉じ込めを防ぎます。
アンダーカット
アンダーカットは、溶接の端に形成される溝またはくぼみです。通常、過剰な入熱または溶接速度が原因で発生します。溶接速度が速すぎると、溶接中心の小さな穴の背後にある液体金属が再分布する時間がなくなり、溶接の両側で凝固してアンダーカットが形成されます。
レーザー溶接でのアンダーカットを回避するには:
- レーザーパラメーターの最適化: レーザー出力、パルス幅、焦点位置を調整して、適切な熱入力を実現します。過熱やアンダーカットの原因となる可能性があるため、出力が高すぎたり、溶接が速すぎたりしないようにしてください。
- 一定の溶接速度を維持する: レーザー ビームまたはワークピースの動きを制御して、一定の移動速度を維持します。急激な速度変化は、不均一な熱分布やアンダーカットの形成を引き起こす可能性があります。
- 適切なジョイントの設計とフィット: 正確なフィット、適切なベベル角度、適切なギャップ許容差など、適切なジョイントの準備を確保します。しっかりとしたフィット感を維持することで、エッジの過度の溶けを防ぎ、アンダーカットを軽減します。
溶接亀裂
溶接高温亀裂とは、溶接プロセス中に溶接部および熱影響部の金属が固相線近くまで冷えるときに、高温領域で発生する亀裂を指します。一般に高温亀裂と低温亀裂に分けられます。レーザー溶接では、レーザーの入熱が小さいため、溶接後の変形が小さく、溶接により発生する応力も小さいため、一般に高温割れは発生しません。ただし、材料の違いやプロセスパラメータの不適切な選択により、高温亀裂が欠陥の形で現れます。
溶接亀裂を避けるには:
- 入熱の制御: レーザーパラメータを最適化して入熱を制御し、熱応力を軽減します。亀裂が発生する可能性があるため、過剰な熱の蓄積や急激な冷却速度を避けてください。これは、レーザー出力とパルス持続時間を調整するか、パルス整形技術を使用することによって実現できます。
- 予熱および溶接後の熱処理: 溶接前にワークピースを予熱すると、熱勾配と応力が軽減され、溶接性が向上します。アニーリングや応力緩和などの溶接後の熱処理技術を使用して、残留応力を緩和し、機械的特性を向上させ、亀裂のリスクを軽減することもできます。
- 充填材の選択: 亀裂のリスクを最小限に抑えるために、基材に適合する適切な組成と延性を備えた充填材を使用します。
不完全な融合または浸透の欠如
不完全な溶融または不完全な溶け込みは、溶接金属が木材と完全に溶けていない場合、または接合部の厚さ全体に浸透していない場合に発生します。
不完全な融合または非貫通融合を回避するには、次の手順を実行します。
- レーザーパラメータの最適化: レーザー出力、パルス持続時間、焦点位置を調整して、材料の適切な融合と浸透を実現します。より高い出力設定または焦点位置の調整は、より深い浸透を達成するのに役立ちます。
- ジョイントの準備と組み立て: ジョイントの設計と組み立てが適切であることを確認します。適切な融合と浸透を促進するために、溝角度、ギャップ公差、および接合準備技術を選択する必要があります。
- 溶接速度を調整する: 溶接速度を調整して、接合部への十分な入熱と浸透を可能にします。溶接速度を最適化することで、レーザー エネルギーが材料と十分に相互作用するようになります。
スプラッシュ
レーザー溶接で発生するスパッタは、溶接部の表面品質に重大な影響を及ぼす可能性があります。溶接後、ワークピースや材料の表面に多くの金属粒子が現れる可能性があり、外観に影響を与えるだけでなく、使用にも影響します。飛散がひどい場合は、レンズを汚染したり損傷したりします。
レーザー溶接でのスパッタを回避するには:
- レーザー光の焦点と位置を最適化: レーザー光の焦点位置と形状を適切に調整して、安定した正確な溶接を実現します。スパッタの原因となるレーザービームの位置ずれや焦点の不安定な状態を避けてください。
- 適切なシールド ガスと流量を使用する: 適切な保護を提供するには、適切なシールド ガスの組成と流量を選択します。シールドガスは溶接池の酸化と汚染を防ぎ、スパッタを低減します。ガス流量は溶接要件に応じて調整する必要があります。
- ワークピースの表面を洗浄します。ワークピースの表面を徹底的に洗浄し、スパッタの形成の原因となる可能性のある汚染を除去します。
変形
変形とは、溶接プロセスによる溶接構造またはワークピースの変形または曲がりを指します。
レーザー溶接による変形を避けるには:
- 正しい固定とクランプ技術を使用してください。溶接中の動きや変形を最小限に抑えるために、ワークピースまたは構造を固定します。ワークピースの適切なサポートと位置合わせにより、寸法安定性が維持されます。
- ワークピースの予熱: 熱勾配を低減し、歪みを最小限に抑えるために、ワークピースを予熱することを検討してください。
- 制御された冷却: ヒートシンクや固定具の使用などの制御された冷却技術を実装して、冷却速度を調整し、温度勾配を最小限に抑えます。
熱影響区域 (HAZ) の問題
レーザー溶接では、溶接部の周囲に高度に集中した熱影響ゾーンが形成されます。熱の影響を受けたゾーンでは、熱サイクルや微細構造の変化が起こり、その結果、強度が低下したり、材料の硬度が変化したりする可能性があります。
HAZ の問題を回避するには:
- レーザー パラメーターの最適化: レーザー パラメーターを調整して、熱影響ゾーンのサイズと深さを最小限に抑えます。これには、レーザー出力、パルス幅、ビーム焦点の制御が含まれます。
- スイープまたは振動技術の使用: スイープまたは振動技術を使用すると、より均一な熱の分布が可能になり、特定の領域への熱の集中が軽減されるため、熱の影響を受けるゾーンに関連する問題が最小限に抑えられます。
- 溶接後の熱処理を実行する: アニーリングや応力除去などの適切な溶接後の熱処理プロセスを適用して、微細構造を改善し、熱影響部に関連する問題を軽減します。熱処理は、熱影響を受けた部分の材料特性を回復するのに役立ちます。
溶接崩壊
レーザー溶接崩壊とは、溶接プロセス中の溶接シームの内側への変形または沈みを指します。これは、高すぎるレーザー出力、不十分な溶融プール制御、不十分な材料サポート、不適切な接合アセンブリ、不十分な熱管理、材料選択の問題、プロセスの監視と制御の欠如など、さまざまな理由で発生する可能性があります。
溶接の崩壊を避けるには:
- レーザーパラメータの最適化: レーザー出力またはエネルギー密度を下げて、周囲の材料の過剰な溶解を防ぎます。レーザー出力、パルス幅、ビーム形状を調整して、浸透と崩壊につながる過度の溶融の回避とのバランスを保ちます。
- 適切な材料サポート: 治具、ジグ、またはクランプを使用して溶接中に適切な材料サポートを提供し、ワークピースを所定の位置に保持し、安定性を提供します。熱を放散し、関節をさらにサポートするために、サポート ロッドまたはヒート シンクの使用を検討してください。
- ジョイントが適切に組み立てられていることを確認します。ジョイントが適切に組み立てられていると、崩壊を防ぐことができます。溶接する前に、合わせ面が適切に準備され、位置合わせされていることを確認してください。適切なジョイント設計とエッジ処理技術を導入することで、ジョイントの強度と安定性を高めます。
- 入熱の管理: 入熱を制御し、熱サイクルを適切に管理します。熱を均等に分散し、局所的な過熱を回避するために、スキャンまたは移動戦略を最適化します。予熱または制御された冷却技術を導入して、熱勾配を最小限に抑え、崩壊のリスクを軽減します。
- 材料の選択と互換性: 適切な材料と相互に互換性のある溶接パラメータを選択します。熱伝導率や融点などの材料特性を考慮して、適切な熱伝達を確保し、局所的な過度の融解を防ぎます。
- プロセスの監視と制御: リアルタイムのプロセス監視および制御システムを実装して、崩壊の兆候や望ましい溶接パラメータからの逸脱を検出します。溶接中にフィードバック メカニズムを使用して、レーザー パラメーター、スキャン速度、または材料サポートを調整します。適応制御システムや閉ループフィードバック制御などの先進技術を採用し、一貫した安定した溶接条件を実現します。
- 適切な溶融プール制御を確保する: レーザー パラメーターとスキャン速度を調整することにより、溶融プールのサイズと形状を制御します。キーホール溶接や伝導モード溶接などの適切な溶接技術を使用して、安定した制御された溶接池の形成を確保します。
要約する
もちろん、レーザー溶接に関連して他の欠陥が発生する可能性もあります。技術的な操作上の問題に加えて、一部の欠陥は材料の特性の変化につながる可能性があります。レーザー溶接プロセスで発生する可能性のある欠陥とさまざまな欠陥の原因を正しく理解することによってのみ、異常な溶接の問題をより的を絞った方法で解決することができます。
AccTekレーザーは幅広い レーザー溶接機ポータブル、清掃、溶接を含む 3-in-1レーザー溶接機金属板やパイプの溶接に適しています。特殊な用途の機械をお探しの場合は、 AccTek レーザー 顧客の要件に応じてカスタマイズされたソリューションを実現するために、適切なコンポーネントを装備することもできます。
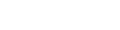
連絡先
- [email protected]
- [email protected]
- +86-19963414011
- No. 3 ゾーン A、Lunzhen 工業地帯、玉城市、山東省。
レーザー ソリューションを入手する