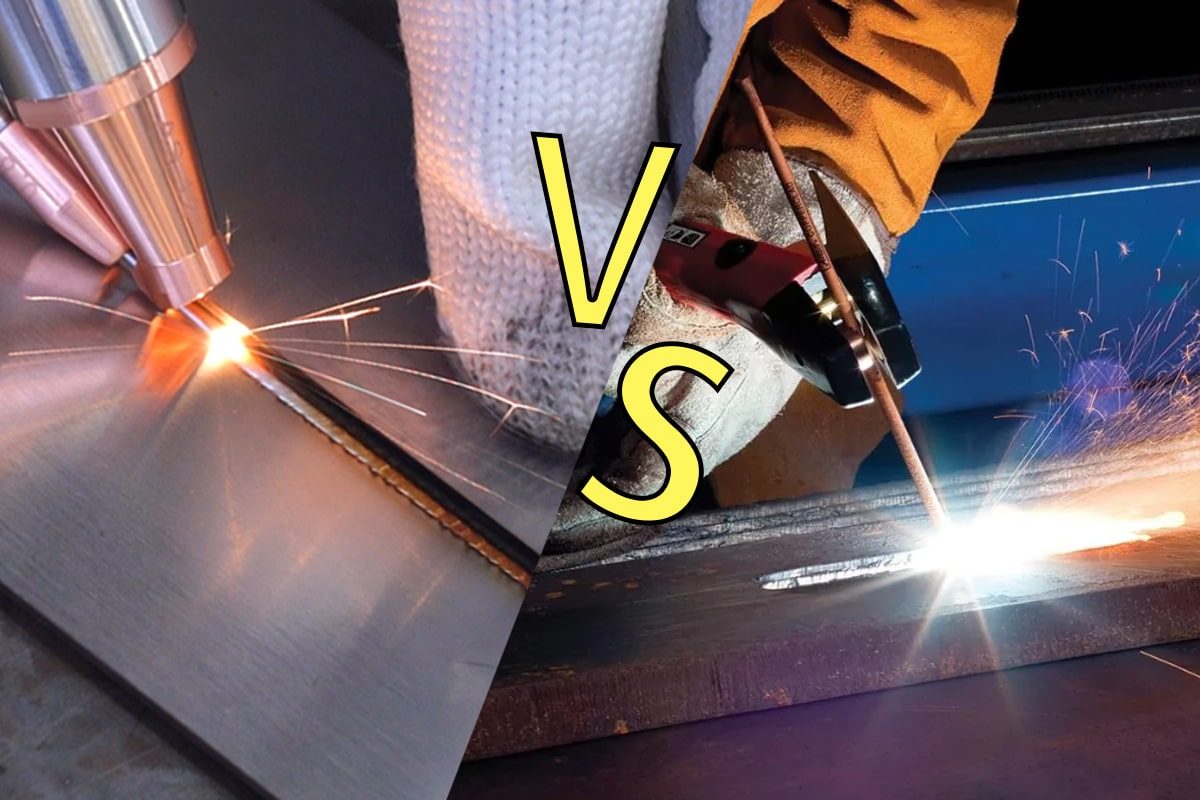
レーザー溶接とアーク溶接
現代の製造業や工業分野では、溶接技術が重要な役割を果たしています。さまざまな産業が、効率的な材料接続と製品の構造的信頼性を実現するために溶接プロセスに依存しています。多くの溶接方法の中で、レーザー溶接とアーク溶接は、それぞれ独自の特徴を持つ最も広く使用されている 2 つの技術です。製造業では、精度、速度、材料の適合性に対する要件が高まり続けているため、これら 2 つの溶接プロセスの長所と短所を理解することが特に重要です。
高エネルギー密度の精密溶接技術であるレーザー溶接は、集束したレーザービームを利用して材料を素早く溶かし、高品質で変形の少ない接合を実現します。レーザー溶接は、その優れた精度と速度により、自動車、航空宇宙、医療などのハイエンド製造分野で広く使用されており、特に薄板や複雑な部品の溶接に適しています。自動化された生産ラインでは、レーザー溶接の非接触性と高エネルギー利用により、生産効率を向上させる理想的な選択肢となっています。アーク溶接は、長い歴史があり、操作が比較的簡単で、手頃な価格の溶接方法です。アーク溶接は、電流によって発生したアークを使用して金属を溶かし、薄板から重い構造物までの溶接に適しています。設備コストが低く、操作が柔軟であるため好まれています。ただし、アーク溶接は熱影響部が大きく、材料が変形しやすく、精度はレーザー溶接ほど良くありません。
目次
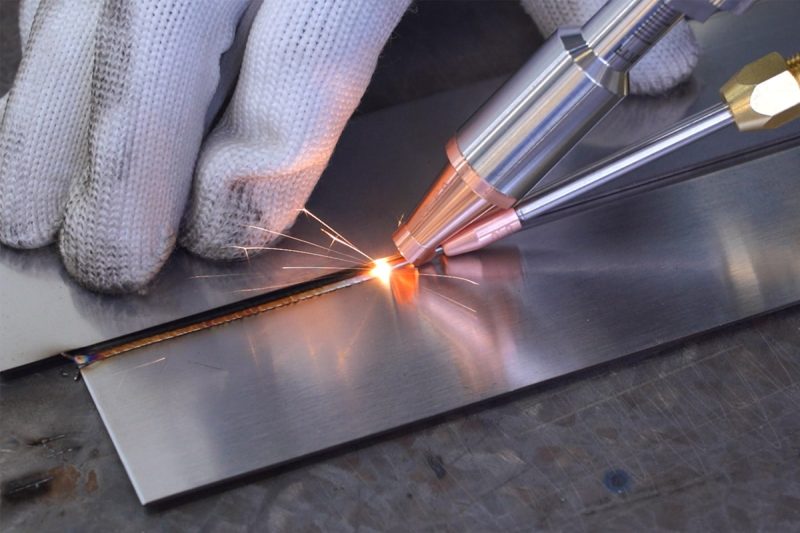
レーザー溶接の概要
レーザー溶接は、高エネルギーのレーザービームを集中させて金属やその他の材料を局所的に溶かして接合する高精度、高効率の溶接技術です。1960年代のレーザー技術の発展以来、レーザー溶接は精密製造における重要なプロセスの1つとなり、特に高強度と低変形を必要とする材料の接合に適しています。レーザー溶接は、航空宇宙、自動車、医療機器、電子産業で広く使用されており、これらの分野での精度と速度に対する高い要件を満たしています。
レーザー溶接の原理とプロセス
レーザー溶接の核となる原理は、レーザーによって生成された高エネルギービームを使用して材料の表面に照射し、それを融点または蒸発点まで急速に加熱することです。溶接プロセス中、レーザー発生器から放射されたビームはレンズまたは反射鏡によって焦点を絞られ、非常に小さな領域にエネルギーが集中して、高エネルギー密度の熱源が形成されます。この高温により、材料の表面が急速に溶け、レーザーの動きと出力を制御することで、正確な溶接操作を実現できます。ビームが移動すると、溶融池は徐々に冷却されて固化し、強力な溶接部が形成されます。
レーザー溶接プロセスは、一般的に次のステップに分けられます。
- 材料の準備: 溶接する材料の表面が清潔であることを確認し、酸化物、油、その他の汚染物質を除去して溶接品質に影響を与えないようにします。
- レーザービームの焦点合わせ: レンズまたは反射鏡を使用してレーザービームを溶接領域に集中させ、エネルギー密度が十分に高くなるようにします。
- 溶融池の形成:レーザービームが材料の表面に照射され、急速に加熱され、溶融して溶融池を形成し、レーザーの移動中に溶融池が徐々に拡大します。
- 凝固と冷却: レーザービームが除去された後、溶融池は冷却され、連続溶接が形成されます。
レーザー溶接技術の種類
レーザー溶接プロセスは、レーザーが材料とどのように相互作用するかに応じて、主に 2 つのタイプに分けられます。
レーザービーム溶接
- この方法は主に浅い溶接に使用されます。レーザービームは材料の表面を加熱し、局所的に溶かします。熱の拡散が遅く、溶融池が浅いため、一般的に薄い材料の接続や溶接の外観に対する要求が高いシーンに適しています。レーザービーム溶接は、精密電子機器や薄肉金属材料の溶接に適しています。
レーザーキーホール溶接
- 高エネルギーレーザー照射下では、材料は表面で溶けるだけではありません。レーザーの強力なエネルギーにより金属が蒸発し、溶接部分に小さな穴(「キーホール」と呼ばれる)が形成されます。この小さな穴は深く狭いため、レーザーは材料の奥深くまで浸透し、多重反射を通じて周囲の材料にエネルギーを伝達します。この技術は厚い材料の深溶け込み溶接に適しており、高い溶接強度が求められる自動車、航空、造船などの業界で広く使用されています。
レーザー溶接の利点と限界
レーザー溶接の利点:
- 高精度: レーザー溶接は、エネルギーを非常に狭い領域に正確に集中させ、溶接の深さと範囲を制御し、非常に高い溶接精度を実現できるため、複雑な部品の加工に特に適しています。
- 熱影響部が小さい: レーザー溶接ではエネルギーが集中するため、熱影響部が小さく、材料の変形や内部応力が軽減され、溶接品質が確保されます。
- 溶接速度が速い:レーザー溶接は非常に短時間で溶接を完了できるため、生産効率が大幅に向上し、特に大規模な自動化生産ラインに適しています。
- 非接触加工:レーザー溶接はワークピースに直接接触する必要がないため、外力が発生したり、機械的な損傷が発生したりすることはありません。
- さまざまな材料に適用可能: 従来の金属材料に加えて、レーザー溶接はプラスチックやセラミックなどの非金属材料にも適用でき、幅広い用途があります。
レーザー溶接の限界:
- 設備コストが高い: レーザー溶接設備は複雑で、レーザー発生器、制御システム、補助設備、特に高出力レーザーシステムのコストが高く、中小企業に経済的圧力をかける可能性があります。
- 材料表面に対する高い要件: レーザー溶接では、ワークピースの表面の清浄度に厳しい要件があります。油、酸化物、その他の不純物があると、レーザーの吸収効率と溶接品質に影響します。
- 薄い材料や精密溶接に適しています: レーザー溶接はさまざまな材料を溶接できますが、厚い構造材料では従来の溶接プロセスほど効率的ではない場合があります。
さまざまな産業におけるレーザー溶接の応用
- 自動車製造:レーザー溶接は自動車業界で広く使用されており、特にボディ溶接、ドア溶接、エンジン部品溶接に使用されています。その高速性と高精度により、生産ラインの自動化レベルが大幅に向上します。また、レーザー溶接は、アルミニウム合金と鋼などの混合金属の溶接にも使用されます。
- 航空宇宙:航空宇宙分野では、溶接材料に軽量かつ高強度が求められることがよくあります。レーザー溶接は、高精度で溶接品質に優れているため、タービンブレード、エンジンケース、その他の部品を含む航空機や宇宙船の構造に広く使用されています。
- 電子・マイクロエレクトロニクス業界:レーザー溶接は、非常に小さな領域の精密溶接が可能で、熱影響部が非常に小さいため、電子業界、特にマイクロエレクトロニクス製造で広く使用されています。たとえば、携帯電話、回路基板、バッテリーパッケージなどの小型精密部品の溶接などです。
- 医療機器: レーザー溶接は医療機器の製造において重要な役割を果たします。手術器具、インプラント、さまざまなステンレス鋼やチタン合金の機器など、精密で要求の厳しい金属器具の溶接に使用されます。
- エネルギー産業:新エネルギー、太陽エネルギー、電池製造の分野では、レーザー溶接は非接触、高効率、さまざまな材料への適応性などの理由から、特に新エネルギー電池のパッケージングと接合に広く使用されています。
レーザー溶接のさまざまな技術と利点により、多くの業界では生産効率と溶接品質が大幅に向上し、精密製造と自動化が大きく進歩しました。
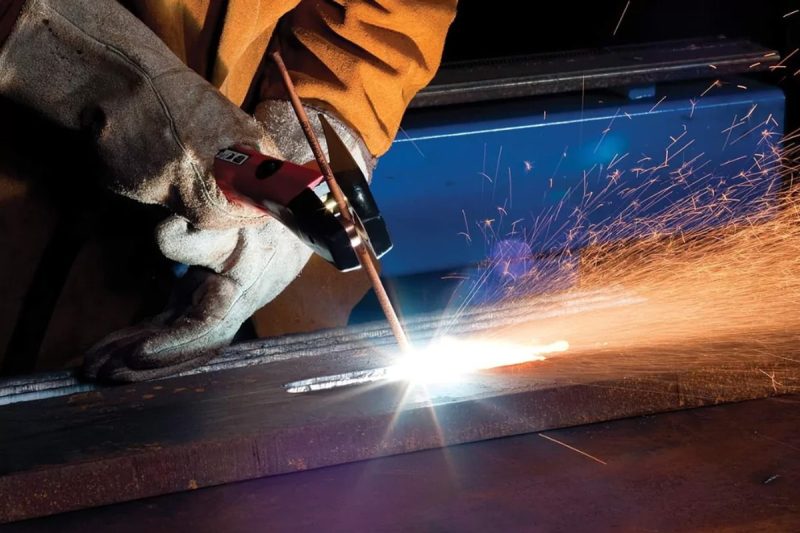
アーク溶接の概要
アーク溶接は、電気アークによって発生する高温を利用して金属を溶かして溶接する方法です。この溶接方法は100年以上の歴史があり、継続的な開発と改良を経て、工業製造業で最も広く使用されている溶接プロセスの1つになりました。アーク溶接は、鉄鋼やステンレス鋼からアルミニウムや銅などの合金材料まで、さまざまな金属材料を処理でき、建設、造船、石油・ガス、重機製造の分野で重要な位置を占めています。アーク溶接は、設備が簡単で、操作が柔軟で、コストが低いため人気があります。
アーク溶接の原理とプロセス
アーク溶接の基本原理は、電極とワークピースの間に発生したアークによって電極とワークピース表面の金属が溶けて溶融池を形成し、溶接が完了することです。電極がワークピースに近づくと、電流が空気を通過して高温のアークが発生し、電極とワークピースの局所領域の金属が溶けて溶融池に接続が形成されます。アークが移動すると、溶融池は徐々に冷えて固まり、固体溶接部になります。
アーク溶接プロセスには通常、次の手順が含まれます。
- アーク生成: 溶接電極をワークピースに近づけて、電極とワークピースの間にアークを形成します。
- 金属の溶融: アークによって発生した高温 (最大 5000 ~ 6000℃) により金属が溶けて溶融池が形成されます。
- 溶融池充填:電極の材料がワークピースの表面の溶融金属と混合して充填材を形成し、徐々に溶融池を満たします。
- 冷却と凝固: アークが移動した後、溶融池は急速に冷却され、溶接部に凝固します。
- アーク溶接プロセスでは、溶接パラメータ(電流、電圧、溶接速度など)と溶接姿勢の制御によって、溶接の品質と溶接効果が決まります。
アーク溶接技術の種類
アーク溶接技術には多くの種類があります。溶接電極とシールドガスの使用に応じて、アーク溶接は多くの種類に分けられます。一般的な種類には次のものがあります。
シールドメタルアーク溶接
手動溶接またはスティックアーク溶接とも呼ばれます。フラックスを塗布した電極を電極として使用します。電極が溶融するとシールドガスとスラグが形成され、空気中の酸素と窒素を遮断し、溶接部分の酸化を防ぎます。この技術は、建設、メンテナンス、構造用鋼の溶接に広く使用されており、設備が簡単で持ち運びに便利なため好まれています。
MIG/MAG溶接
MIG/MAG溶接とも呼ばれます。連続給電ワイヤを電極として使用し、溶接プロセス中にノズルから保護ガス(アルゴン、二酸化炭素など)を噴射して空気を遮断します。この技術は自動溶接に適しており、溶接速度が速いです。自動車製造、機械、パイプラインの溶接で広く使用されています。
ガスタングステンアーク溶接
TIG溶接とも呼ばれ、不溶性タングステン電極を使用して高エネルギーアークでワークピースを加熱し、同時に不活性ガス(通常はアルゴン)を使用して溶接領域を保護します。この方法は精密溶接に適しており、溶接品質が高いです。ステンレス鋼、アルミニウム、ニッケルなどの溶接材料によく使用され、航空宇宙、医療機器、精密製造で広く使用されています。
サブマージアーク溶接
溶接は、粒状フラックスの下で電気アークを使用して行われます。このフラックスは、空気を遮断する保護層を形成し、溶接性能を高める合金元素を提供します。この技術は、厚くて重い板の溶接によく使用され、大型構造物、パイプライン、圧力容器の製造に広く使用されています。
アーク溶接の利点と限界
アーク溶接の利点:
- 設備コストが低い: アーク溶接設備は比較的シンプルで、初期投資コストが低く、メンテナンスコストも経済的であるため、大規模な産業用途に適しています。
- 柔軟な操作: アーク溶接は、さまざまな溶接位置や複雑な構造に適応でき、屋内、屋外、または限られたスペースでも操作できます。
- 強力な材料適合性:アーク溶接は、低炭素鋼、ステンレス鋼、アルミニウム、銅など、さまざまな金属を溶接でき、適用範囲が広いです。
- 幅広い用途: 薄板から重い構造材料まで、アーク溶接は厚さや構造形状に優れた適応性があり、特に重機や建設業界で使用されています。
アーク溶接の限界:
- 大きな熱影響部: アーク溶接では熱入力が大きいため、広い熱影響部が発生しやすく、材料の変形、亀裂、その他の熱処理関連の問題が発生する可能性があります。
- 溶接精度が比較的低い:レーザー溶接などの高精度溶接プロセスと比較すると、アーク溶接は溶接精度が不足しており、溶接の細かさと美観は低くなります。
- 大量の煙とガスの排出: アーク溶接中に大量の煙と有害ガスが発生し、作業者の健康や環境に影響を与える可能性があるため、十分な換気と保護具が必要です。
- 高い技術要件: 特に手作業による溶接では、溶接工の技能レベルが溶接品質に大きな影響を与え、技術力が不十分だと溶接欠陥が発生します。
さまざまな産業におけるアーク溶接の応用
- 建設業界: アーク溶接は、建築構造物の溶接、特に鉄骨構造物や橋梁の建設に広く使用されています。アーク溶接は溶接強度が高く、操作性に優れているため、鉄骨構造物の溶接に好まれるプロセスの 1 つです。
- 造船業:船体製造には大量の鋼材溶接が必要であり、アーク溶接は重い鋼板を扱え、優れた機械的性質を提供できます。特に、サブマージアーク溶接は、大型船体やシェルの溶接に広く使用されています。
- 石油・ガス産業:パイプライン溶接では、アーク溶接の柔軟性と強力な材料適合性により、高圧環境下での信頼性を確保できる石油・ガスパイプラインの主な溶接方法となっています。
- 重機製造:鉱山機械、建設機械、農業機械などの重機の製造では、バケット、フレーム、ブームなどの大型構造部品の溶接にアーク溶接が広く使用されています。これらの部品には、高強度で耐久性のある溶接技術が必要です。
- 修理とメンテナンス:アーク溶接装置は操作が簡単で便利なため、さまざまな機械設備の修理とメンテナンスに広く使用されています。自動車の修理から産業機器の修理まで、アーク溶接はメンテナンス担当者にとって一般的なツールです。
アーク溶接は、長年実証された溶接技術であり、その高い適応性、低コスト、幅広い用途により、現代の産業において依然として重要な位置を占めています。
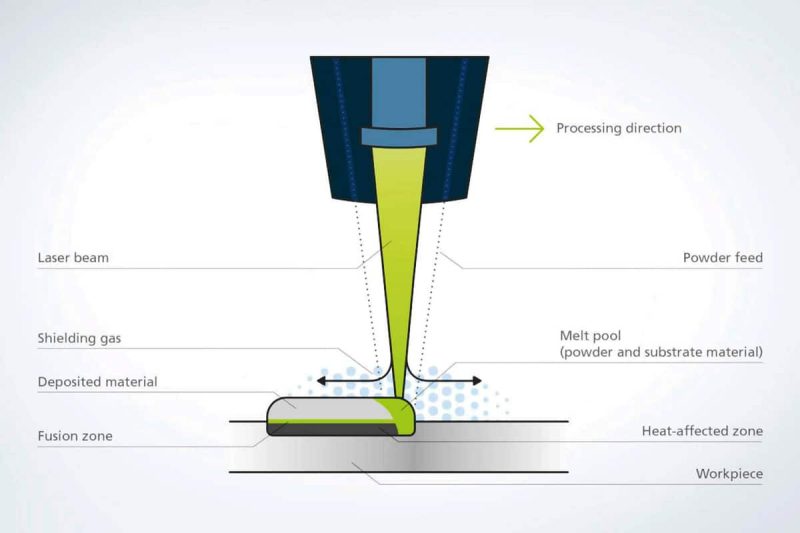
レーザー溶接の原理
レーザー溶接は、高エネルギー密度のレーザービームを使用して材料を急速に加熱、溶融し、精密に接続する高度な溶接技術です。主な利点は、溶接速度が速く、入熱量が少なく、制御が正確で、さまざまな材料に適用できることです。レーザー溶接は、非接触で高精度であるという特徴から、自動車製造、航空宇宙、電子機器、医療機器の分野で主流の溶接プロセスになっています。
レーザー溶接の仕組み
レーザー溶接の基本的な動作原理は、レーザービームの高エネルギー集中特性を利用してエネルギーを非常に小さな溶接領域に集中させ、材料を急速に加熱して溶かし、溶融池を形成することです。ビームが移動すると、溶融池が凝固して溶接部を形成します。溶接プロセス全体は通常、次の手順に分けられます。
- レーザービーム生成: 高強度レーザービームは、ファイバーレーザー発生器、CO₂レーザー発生器、または固体レーザー発生器などのレーザー発生器によって生成されます。レーザービームは、単一波長、高指向性、高エネルギー密度を特徴としています。
- レーザー ビームの集束: レーザー ビームは、光学システム (レンズや反射鏡など) によって、通常直径約 0.1 mm の非常に小さな点に集束されます。これにより、金属を急速に溶かすのに十分な非常に高い電力密度 (平方ミリメートルあたり数百から数千ワット) が可能になります。
- 材料の溶融と溶接:レーザービームが材料の表面に照射されると、材料はレーザーエネルギーを吸収し、急速に融点まで加熱され、溶融池を形成します。レーザービームが溶接経路に沿って移動すると、溶融池は徐々に膨張し、冷却後に固体溶接を形成します。
- 冷却と凝固:レーザービームが移動した後、溶融池領域が冷却され、溶融金属が凝固して連続溶接を形成します。レーザー出力、溶接速度、焦点位置を制御することで、溶接の形状と品質を正確に制御できます。
レーザーと金属の相互作用
レーザー溶接の鍵は、レーザーエネルギーと金属材料の相互作用にあり、それは具体的には以下の段階で現れます。
- レーザーエネルギーの吸収:レーザービームが金属表面に照射されると、金属はレーザーエネルギーの一部を吸収します。これは、金属の反射率とレーザーの波長によって異なります。たとえば、アルミニウムや銅などの高反射率の材料は、特定の波長のレーザーに対する吸収率が低いため、溶接にはより高い出力またはより適切な波長が必要です。一般的な鋼鉄やステンレス鋼の場合、吸収率は高く、レーザー溶接はより効率的です。
- 熱伝導と溶融: 金属に吸収されたレーザーエネルギーは熱伝導によって材料に拡散し、材料を加熱して融点に達します。電力密度が高いため、材料は局所的に急速に溶融し、溶融池が形成されます。レーザービームの移動中、溶融池内の金属は凝固を続け、最終的に溶接部を形成します。
- キーホール効果:高出力レーザー溶接では、レーザービームのエネルギーによって材料が溶けるだけでなく、金属の一部が気化して局所的な圧力が発生し、溶融金属が押し出されて小さな穴が形成されます。このキーホール効果により、レーザービームが材料の奥深くまで浸透し、さらに多重反射によってエネルギーが伝達され、溶接の深さと効率が向上します。キーホール溶接は、厚い材料や深溶け込み溶接に非常に適しています。
- 溶融池の動的挙動: 溶接プロセス中、溶融池の流動性と表面張力が溶接の品質と形状に影響します。適切なレーザー出力と溶接速度により、溶融池を安定させ、スパッタや気孔などの溶接欠陥を回避できます。
レーザー溶接に影響を与える主要なパラメータ
レーザー溶接プロセスには、溶接の品質と効果に直接影響を与える重要なパラメータがいくつかあります。これらのパラメータには、レーザー出力、溶接速度、焦点位置、シールドガスなどが含まれますが、これらに限定されません。
- レーザー出力:レーザーの出力によって、材料に適用されるエネルギー強度が決まります。高出力は厚板溶接や深溶け込み溶接に適していますが、出力が高すぎると、材料が過度に溶けたり飛び散ったりする可能性があります。低出力は薄板溶接や精密溶接に適しており、熱入力と変形を効果的に減らすことができます。
- 溶接速度: 溶接速度とは、レーザービームが材料の表面を移動する速度を指します。溶接速度が速いほど、熱影響部のサイズと材料の変形を減らすことができますが、速度が速すぎると、溶接が不完全または不安定になる可能性があります。速度が遅いと、深い溶け込み溶接が可能になりますが、熱入力が増加し、溶接が広くなりすぎたり、熱影響部が大きくなったりする可能性があります。
- 焦点位置: ワークピースの表面に対するレーザービームの焦点の位置は、溶接深さと溶接形状を制御する鍵となります。ワークピースの表面より下に焦点を合わせると溶接深さを深くすることができ、厚板溶接に適しています。表面より上に焦点を合わせると表面精密溶接に適しています。焦点位置を正確に制御すると、溶接の形状と強度を最適化できます。
- シールドガス: シールドガス (アルゴン、ヘリウム、二酸化炭素など) は、溶融池が空気中の酸素や窒素と反応するのを防ぎ、溶接部の酸化や気孔の形成を防ぐために、レーザー溶接でよく使用されます。ガスの種類によって、溶接部の形成と品質に及ぼす影響は異なります。アルゴンは通常、溶接面の仕上げを改善するために使用され、ヘリウムは溶接部の深さを深くするために使用されます。
- レーザー波長: レーザーの波長は材料の吸収効率に影響します。材料によってレーザー波長に対する感度が異なり、適切な波長を選択するとエネルギー効率と溶接結果が向上します。たとえば、ファイバーレーザー発生器は通常 1μm の波長範囲にあり、鋼、ステンレス鋼、その他の材料の溶接に適していますが、CO₂ レーザー発生器は波長が長く (10.6μm)、非金属材料の溶接に適しています。
- 溶接環境: 湿度、温度、空気の流れなどの環境条件も、特に屋外や過酷な環境で作業する場合、レーザー溶接の安定性に影響を与える可能性があり、溶接品質を確保するために必要な保護対策を講じる必要があります。
これらのパラメータを正確に制御することにより、レーザー溶接は、さまざまな産業用途のニーズを満たす高品質で歪みの少ない溶接結果を実現できます。
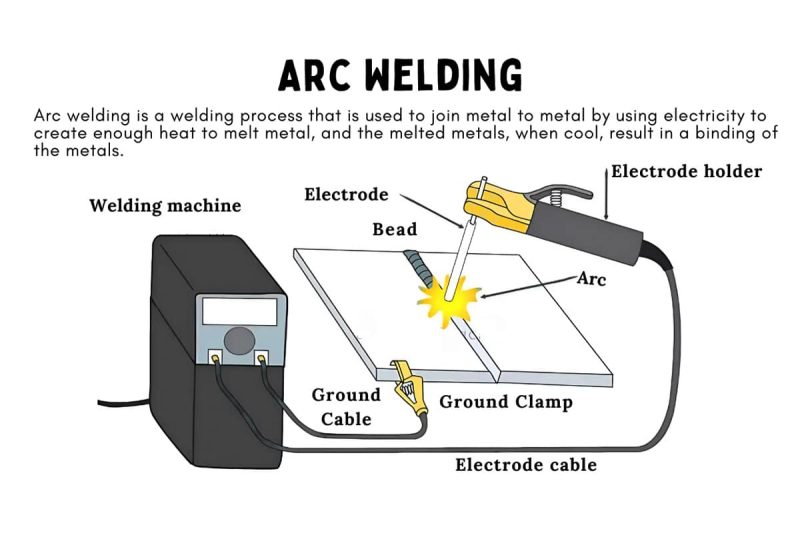
アーク溶接の原理
アーク溶接は、工業分野で広く使用されている溶接プロセスです。その主な特徴は、アークによって生成された高温を利用して金属を溶かし、材料の強固な接続を実現することです。アーク溶接は、電極とワークピースの間のアークを熱源として使用することで、さまざまな金属材料を処理でき、建設、造船、石油パイプライン、自動車製造など、さまざまな溶接シナリオに適しています。アーク溶接は、設備コストが低く、操作が柔軟であるなどの利点がありますが、熱影響部が大きく、溶接精度が比較的低いなどの制限もあります。アーク溶接の動作原理と主要なパラメータを理解することは、溶接効果を最適化し、溶接の品質を向上させるのに役立ちます。
アーク溶接の仕組み
アーク溶接の基本的な動作原理は、電極とワークピースの間の電流を通じて高温アークを発生させ、電極とワークピースの表面上の金属を溶かして溶融池を形成することです。アークがワークピースの表面を移動すると、溶融池は徐々に冷却されて固化し、最終的に固体溶接部を形成します。アーク溶接の操作プロセスには、通常、次の手順が含まれます。
- アーク発生:溶接電極がワークピースに接触すると回路が閉じ、電流が流れます。その後、電極がワークピースから離れ、発生したアークが空気またはシールドガスを介してエネルギーを伝達し、局所的な金属を急速に融点まで加熱します。
- 電極の溶融と充填:アークの高温により、ワークピースが溶融するだけでなく、溶接電極も溶融します。電極の溶融金属は溶融池に入り、ワークピースの溶融金属と結合して、溶接領域を徐々に充填します。
- 溶融池の形成と移動:アークが溶接経路に沿って移動すると、溶融池が連続的に形成され、移動し、溶融池の後ろの領域はアークを離れた後急速に冷却され、溶接部に固まります。
- 保護と冷却: 金属アーク溶接 (MIG/MAG 溶接) などの一部のアーク溶接技術では、溶融池を保護するために不活性ガス (アルゴン、二酸化炭素など) が使用されます。これにより、空気中の酸素と窒素が高温の金属と反応して酸化物や気孔が形成され、溶接の品質に影響が及ぶのを防ぎます。
アークと溶接プールの形成
アーク溶接の核心はアークと溶融池の形成であり、これが溶接の効率と品質を決定します。
アーク形成
アークは高電流と低電圧によって生成されます。電極とワークピースの間の空気は電流によって分解され、導電性媒体となり、プラズマ状態のアークを形成します。このプラズマは非常に高温(通常 5000 ~ 6000°C まで)で、金属を溶かすのに十分です。アークの形状と安定性は、溶接の成功にとって非常に重要です。安定したアークは熱を均等に伝達し、溶融池が均等かつ安定して形成されることを保証します。
溶融池の形成と動的挙動
アーク溶接では、アークが材料の表面に十分な熱を発生させると、局所的な金属が溶けて溶融池が形成されます。溶融池の形状、サイズ、流動性は、溶接の最終的な品質に影響します。溶融池内の金属は、溶融した電極金属と混ざり合って接続を形成します。アーク溶接における溶融池の動的挙動は複雑なプロセスであり、アーク電流、溶接速度、熱伝導など、多くの要因の影響を受けます。溶融池の凝固速度、表面張力、重力はすべて、溶接の形態と表面仕上げを決定します。
溶接姿勢と溶融池の流れ
平溶接、垂直溶接、水平溶接などの溶接姿勢の変化は、溶融池の流動挙動に影響を与えます。平溶接では、溶融池の流動性が向上し、溶接部の形成がより安定しますが、垂直溶接やオーバーヘッド溶接では、溶融池が重力の影響を受け、たるみや不均一な流れが発生しやすくなります。したがって、溶接者は、溶接姿勢に応じて溶接パラメータと技術を調整し、溶融池の制御を確保する必要があります。
アーク溶接に影響を与える主要なパラメータ
アーク溶接における多くのパラメータは、溶接効果と溶接品質に直接影響します。これらのパラメータを理解して制御することで、溶接工は理想的な溶接結果を得ることができます。
- 溶接電流: 電流は、溶接プロセスの熱入力を決定する重要なパラメータの 1 つです。電流が高いほど、より多くの熱が発生し、溶融池のサイズと溶接の深さが増すため、厚い材料の溶接に適しています。一方、電流が低いほど、薄い材料の溶接に適しており、過度の溶融と変形を回避できます。電流が高すぎると、溶接が溢れ、溶融池が不安定になります。一方、電流が低すぎると、溶融が不十分になり、溶接強度が不十分になります。
- 溶接電圧:電圧はアークの長さと安定性を制御します。電圧が高いほどアークが長くなり、熱分布がより均一になり、広い溶接の形成に適しています。電圧が低いほどアークが短くなり、熱がより小さな領域に集中するため、深い溶接に適しています。電圧の変化はアークの形状と安定性に直接影響し、それが溶融池の流動性と溶接の形状に影響します。
- 溶接速度: 溶接速度とは、アークがワークピース上で移動する速度のことで、溶融池の形状、熱影響部 (HAZ) のサイズ、溶接の品質に重要な影響を及ぼします。溶接速度が速いほど、溶融池の形成時間が短縮され、熱影響部が小さくなり、変形が減りますが、不連続な溶接や融合不良が発生する可能性があります。溶接速度が遅いほど、入熱量が増加し、深部溶融溶接に適していますが、材料の過熱、溶接幅が広すぎる、または大きな変形が発生する可能性があります。
- 電極の種類と直径:電極の選択は、溶接効果に直接影響します。さまざまな種類の電極(溶接棒、電気溶接ワイヤなど)は、さまざまな材料と溶接方法に適しています。電極の直径は、アークの安定性と溶接の幅にも影響します。厚い電極は厚い材料の溶接に適しており、幅広く厚い溶接部を形成できますが、薄い電極は精密溶接や薄板溶接に適しています。
- 溶接環境: 温度、湿度、風速などの環境要因もアーク溶接に影響します。風速が高すぎるとシールドガスが吹き飛ばされ、溶接部の酸化や気孔形成の原因になります。溶接品質を確保するには、厳しい屋外条件下では防風壁や加熱されたワークピースなどの適切な保護対策が必要です。
- シールドガス: 金属アーク溶接 (MIG/MAG 溶接) およびタングステンアーク溶接 (TIG 溶接) では、シールドガスを使用して空気を遮断し、溶融池が酸素や窒素と接触するのを防ぎます。シールドガスの種類 (アルゴン、二酸化炭素、ヘリウムなど) によって、溶接の形態、溶け込み深さ、表面仕上げにさまざまな影響があります。たとえば、アルゴンを使用すると表面仕上げが向上し、二酸化炭素を使用すると溶接の深さを増やすことができます。
これらの重要なパラメータを正確に制御することにより、アーク溶接はより高い溶接品質を実現し、さまざまな材料、厚さ、溶接位置のニーズに適応できます。
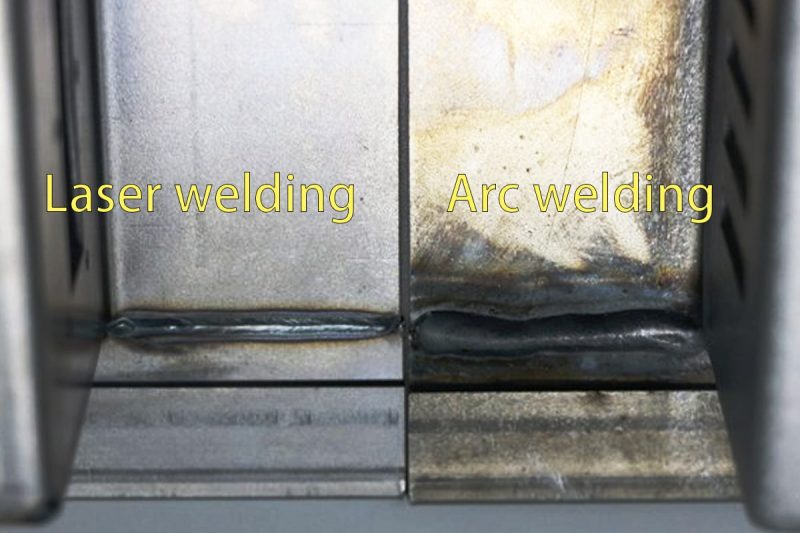
レーザー溶接とアーク溶接の比較
レーザー溶接とアーク溶接は、産業分野における 2 つの重要な溶接プロセスであり、それぞれに独自の利点と制限があります。レーザー溶接は、高速、高精度、低入熱で知られていますが、アーク溶接は、操作が簡単で、用途が広く、コストが低いため広く使用されています。効率、精度、熱影響部、溶接品質、機器要件、コストの点で、この 2 つには大きな違いがあるため、特定のプロジェクトのニーズと予算に基づいて、どの溶接技術を選択するかを決める必要があります。
効率とスピード
効率と速度の面では、レーザー溶接はアーク溶接よりもはるかに優れています。レーザー溶接の高エネルギー密度により、特に薄い材料や精密溶接の場合、非常に高速で溶接を完了できます。レーザー溶接の溶接速度は毎分数メートル以上に達する可能性があり、自動車製造やエレクトロニクス業界の高速組立ライン操作などの大量生産シナリオに適しています。
一方、アーク溶接は溶接速度が遅く、特に厚い材料や複雑な溶接位置を扱う場合には効率が大幅に低下します。また、アーク溶接の準備と清掃には通常、溶接電極の交換やスラグの除去などの手順が含まれており、時間がかかるため、小ロット、厚板、現場施工など、低速が求められる場面ではアーク溶接の方が適しています。
精度と精度
レーザー溶接は、高精度と制御性に優れていることで知られています。レーザービームを非常に小さな点に集中させることができるため、非常に高い溶接精度を実現でき、微細金属加工や複雑な部品の溶接に適しています。レーザー溶接は自動化度が高く、CNC 装置やロボットと統合して高精度の溶接パス制御を実現できます。このため、レーザー溶接は、マイクロエレクトロニクス、医療機器製造など、高精度と一貫性が求められる業界で人気があります。
アーク溶接は精度が比較的低く、主に作業者のスキルに依存します。現代のアーク溶接設備は自動制御によって精度を向上させることができますが、アークの不安定性と大きな入熱によって制限され、レーザー溶接の精度レベルを達成することは困難です。特に薄板や精密溶接では、アーク溶接によって材料が過熱したり変形したりして、溶接品質に影響を与える可能性があります。
熱影響部と変形
レーザー溶接のもう一つの大きな利点は、熱入力が低く、熱影響部(HAZ)が比較的小さいことです。レーザービームのエネルギー密度が高く、精密に制御されているため、溶接領域のみが急速に加熱されて溶融し、周囲の材料は熱の影響をあまり受けません。これにより、材料の変形が軽減されるだけでなく、溶接後の機械的特性も向上します。したがって、レーザー溶接は、熱に敏感な材料の溶接や、高強度と低変形が求められる場合に非常に適しています。
アーク溶接は入熱量が大きいため、溶接部周辺の材料が熱の影響を大きく受け、より広い熱影響部が形成されます。これにより、特に厚い材料や大面積の溶接では、材料の変形や残留応力が増加します。熱変形を減らすために、アーク溶接では通常、熱処理や修正などの複数の溶接および後処理が必要になり、溶接の複雑さとコストが増加します。
溶接品質と強度
レーザー溶接は、一般に、特に薄板や精密部品を溶接する場合に優れた溶接品質を提供します。レーザー溶接プロセスの自動制御と熱影響部が小さいため、溶接面が滑らかで、スパッタや気孔がほとんどない一貫した溶接を実現できます。レーザー溶接は一般に強度が高く、特に深溶け込み溶接では、良好な溶接深さ対幅比を実現できるため、溶接全体の強度が向上します。
アーク溶接の溶接品質は、作業者のスキルに大きく依存します。溶接の均一性と表面品質は、動作の不安定性、溶接電流、電極の選択などの要因によって影響を受ける可能性があります。アーク溶接は高強度の溶接部も生成できますが、特に厚板を溶接する場合は、スパッタ、スラグ、気孔などの欠陥が溶接部に現れることが多く、通常は追加の研磨と洗浄が必要です。一部の高強度材料では、アーク溶接の溶接強度が母材の強度に匹敵しない場合があります。
機器とセットアップ
レーザー溶接装置の設計は通常複雑ですが、技術の進歩により、現代のポータブル レーザー溶接機 は溶接業界で注目を集めています。これらの装置は、レーザー発生器、光学系、自動制御ユニットを統合しているだけでなく、効率的なシールドガス装置も備えており、溶接中の材料の品質と性能を確保しています。ポータブルレーザー溶接機のユーザーフレンドリーな操作インターフェースにより、オペレーターはすぐに作業を開始でき、複雑な設定への依存を減らすことができます。同時に、現代のレーザー溶接機のメンテナンスは比較的簡単で、機器の故障頻度を効果的に減らし、継続的な生産効率を確保できます。
対照的に、従来のアーク溶接装置は構造が比較的単純で、通常は溶接電源や溶接電極などの基本コンポーネントが含まれています。このタイプの装置は通常、手動または半自動で操作され、さまざまな産業用途、特に現場建設での使用に適しており、その携帯性と適応性により人気があります。ただし、アーク溶接装置は、特に要求の厳しい溶接用途では、溶接プロセス中に熱影響部が大きく、溶接品質が一定でないなどの問題に直面する可能性があり、理想的な結果を得るのが困難な場合がよくあります。
コストに関する考慮事項
コストの観点から見ると、アーク溶接には明らかな利点があります。アーク溶接装置は比較的安価で、メンテナンスと運用コストが低く、特に少量で精度の低い溶接のニーズに適しています。アーク溶接は操作が簡単で、必要なトレーニングと技術要件が低いため、全体的な溶接コストは比較的制御可能です。
レーザー溶接への初期投資は大きく、設備の調達、設置、メンテナンスのコストも比較的高いです。レーザー溶接の精密な操作と自動化の要件は、運用コストとトレーニングコストも高くなることを意味します。しかし、レーザー溶接の高効率と高品質は、大量生産のコストをすぐに希釈することができ、レーザー溶接の長期的な費用対効果はより顕著です。
レーザー溶接とアーク溶接はそれぞれ利点があり、異なるシナリオに適しています。レーザー溶接は高速、高精度、低入熱で知られており、高い溶接品質と精度が求められるプロジェクトに最適です。一方、アーク溶接は低コスト、厚板溶接への適応性、現場施工の面でより多くの利点があります。溶接方法を選択するときは、溶接品質、材料の厚さ、精度要件、予算などのプロジェクトのニーズを総合的に考慮する必要があります。
今日のレーザー溶接機はすでに現場での施工能力を備えており、持ち運びも簡単です。AccTekのポータブルレーザー溶接機は、高精度で高速な溶接を実現できるだけでなく、価格も手頃で移動も簡単なため、現場での加工作業に特に適しています。このタイプの機器は、生産効率を大幅に向上させ、企業に安定した長期的利益をもたらすことができます。
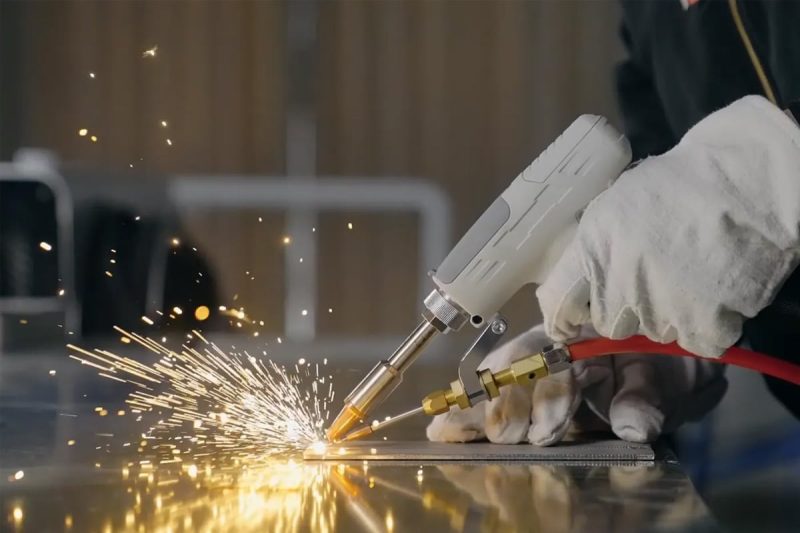
レーザー溶接とアーク溶接の応用
現代の産業では、レーザー溶接とアーク溶接はどちらも欠かせない溶接技術です。それぞれに独自の利点と応用シナリオがありますが、レーザー溶接は、その精度、効率、柔軟性により、多くの産業でますます明らかな利点を示しています。
自動車
自動車製造の分野では、レーザー溶接は車体製造やシャーシ接続に広く使用されています。高精度と低入熱特性により、車体部品の接続がより緊密になり、車両全体の安全性と信頼性が向上します。レーザー溶接技術は高速で自動化されているため、大量生産にも非常に効果的であり、大規模な溶接作業を迅速に完了できます。一部の厚肉部品の溶接には依然としてアーク溶接が使用されていますが、レーザー溶接が提供する正確な制御と溶接品質により、多くの重要な用途で第一の選択肢となっています。
航空宇宙
航空宇宙産業では、部品は過酷な条件下で高い応力と温度差に耐えなければなりません。レーザー溶接は、チタン合金やアルミニウム合金などの高強度材料を溶接する際に、優れた接合強度と溶接品質を提供できます。レーザー溶接の低熱影響部特性は、材料への熱損傷を軽減し、溶接部品の信頼性を確保するのに役立ちます。アーク溶接もこの分野で一定の用途がありますが、複雑な形状の溶接におけるレーザー溶接の利点により、航空宇宙産業で徐々に重要な選択肢になってきました。
エレクトロニクスおよびマイクロエレクトロニクス産業
レーザー溶接は、電子部品やマイクロ電子部品の溶接に特に効果的です。レーザー溶接は、高精度で制御性に優れているため、小型の回路基板、バッテリーコネクタ、その他の敏感な電子部品の溶接に適しています。この非接触溶接方法は、熱入力を効果的に低減できるため、小型部品の熱損傷を回避できます。対照的に、アーク溶接は小型電子部品の溶接時に熱損傷のリスクに直面することが多いため、レーザー溶接の方が間違いなく適しています。
医療機器製造
医療機器の製造では、溶接の精度と汚染のなさが重要です。レーザー溶接は、溶接継ぎ目が正確で熱影響部が小さいため、ステンレス鋼やチタン合金などの材料の溶接に非常に適しています。手術器具やインプラントの製造に広く使用されています。対照的に、アーク溶接では、これらの要求の厳しい医療機器を加工する際にレーザー溶接の基準を満たすことが困難です。
レーザー溶接は、多くの業界で大きな利点を示しており、特に高精度と高速処理を必要とするアプリケーションでは、そのかけがえのない価値を示しています。アーク溶接はまだいくつかの分野でその地位を維持していますが、レーザー溶接が提供する柔軟性と溶接品質により、現代の溶接技術ではますます優位になっています。溶接技術を選択するときは、特定のニーズとアプリケーションシナリオに基づいて両方の長所と短所を適切に評価することで、生産効率と製品品質を効果的に向上させることができます。
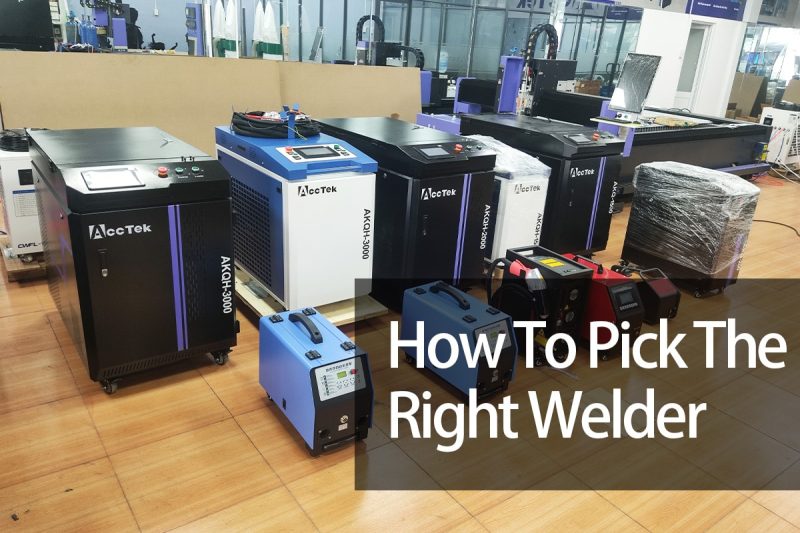
適切な溶接技術の選択
適切な溶接技術を選択することは、溶接品質、プロジェクトコスト管理、生産効率を確保する上で不可欠です。各溶接方法には、さまざまな材料、仕様、用途を扱う際に利点と制限があります。レーザー溶接であれアーク溶接であれ、選択する際には、材料の適合性、プロジェクト仕様、プロセス要件、予算、利用可能なリソースなど、考慮すべき要素が多数あります。溶接方法を適切に選択することで、生産プロセスを最適化できるだけでなく、コストを削減し、溶接の品質と効率を向上させることができます。
溶接方法を選択する際に考慮すべき要素
溶接技術を選択する際には、具体的なプロジェクト要件と実際の状況を組み合わせて、主に以下の要素を考慮する必要があります。
- 材料の種類と厚さ: 材料と材料の厚さが異なると、必要な溶接技術も異なります。たとえば、薄いシート材料はレーザー溶接に適していますが、厚い板や構造用鋼はアーク溶接で溶接されることが多いです。
- 溶接の精度と複雑さ: 複雑な部品、細かい溶接、または高精度の溶接要件には通常、レーザー溶接などの精密溶接技術が必要です。
- 溶接速度: 大規模かつ高速な生産が求められるため、短時間で高品質の溶接を完了できるレーザー溶接などの自動化度の高い溶接技術が好まれる傾向があります。
- 熱の影響と変形の制御: 熱に敏感な材料や、熱影響部を低く抑える必要があるプロジェクトでは、レーザー溶接が適していることが多いです。一方、熱に敏感でない構造用鋼や厚い材料の場合は、アーク溶接で深い溶け込み溶接が可能です。
プロジェクトの仕様と目標
プロジェクトの具体的な仕様と目標は、溶接技術の選択に直接影響します。自動車製造や電子製品生産などの大規模な自動化生産ラインの場合、レーザー溶接は、その高速性、高精度、自動化機器の統合能力により、生産効率を効果的に向上させ、高品質で大規模な生産のニーズを満たすことができます。さらに、レーザー溶接の非接触性により、溶接プロセス中の消耗品の使用と清掃作業も削減され、生産の継続性が向上します。
アーク溶接は、建設、造船、重機製造で最も一般的に使用される溶接方法の 1 つです。アーク溶接技術は、その優れた適応性と携帯性により、特に厚板や複雑な構造物を溶接する場合、厳しい建設条件下でも確実に動作できます。たとえば、石油およびガスパイプラインの溶接では、アーク溶接の深い浸透特性と低コストの利点により、最も人気のある溶接方法となっています。
予算とリソースの考慮
予算とリソースの可用性は、溶接技術を選択する上で重要な要素です。レーザー溶接装置は、レーザー光源、制御システム、冷却装置などのハードウェア投資を含めて高価であり、メンテナンスコストと操作技術要件も高くなります。したがって、レーザー溶接は高い利益をもたらすことができますが、初期投資が大きく、通常は大量生産と高度な自動化を必要とする業界に適しています。
アーク溶接設備は低コストで、メンテナンスが比較的簡単で、作業員が高強度の技術トレーニングを受ける必要がありませんが、高い溶接精度を必要としないプロジェクトに適しています。特に建設現場や現場メンテナンスなどの環境では、アーク溶接は柔軟な操作と安価な消耗品のため、予算が限られている中小規模のプロジェクトに適しています。ただし、アーク溶接の制限は、精度が比較的低いことです。特に薄板や熱に弱い材料を加工する場合、過度の入熱により変形や割れなどの品質問題が発生しやすくなります。また、アーク溶接の溶接速度は比較的遅いため、高速で正確な操作が求められるアプリケーションシナリオには適していません。
一方、レーザー溶接機は、高精度と高速という利点があるだけでなく、熱の影響を効果的に軽減し、溶接の美しさと品質を確保することもできます。今日のレーザー溶接設備は、非常に軽量でコンパクトで、持ち運びが簡単で、現場の作業に完全に適応し、材料の適用範囲が広くなっています。したがって、レーザー溶接は、精度、効率、長期的な投資収益を追求するプロジェクトにとって間違いなくより良い選択です。
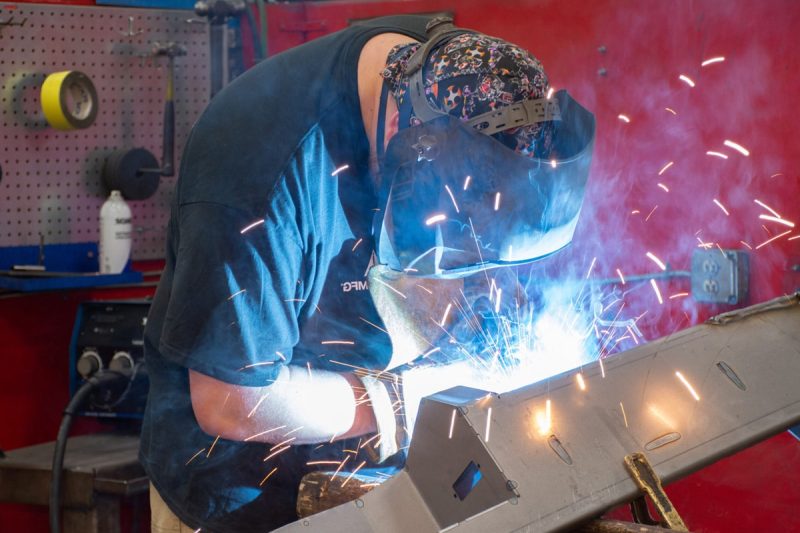
環境と安全に関する考慮事項
現代の産業では、環境と安全の問題がますます重要になっています。溶接技術の選択は、溶接の品質と効率に影響を与えるだけでなく、環境への影響や作業者の健康と安全の保護にも関係します。レーザー溶接とアーク溶接を比較すると、レーザー溶接にはいくつかの独自の利点があります。
排出と環境への影響
レーザー溶接は、効率が高く熱入力が少ないため、通常、煙や有害ガスの排出が少なくなります。この特徴により、レーザー溶接はより環境に優しいものになります。アーク溶接と比較すると、後者は溶接プロセス中により多くの溶接煙と有毒ガスを放出し、環境への悪影響を増大させる可能性があります。環境規制を厳格に遵守する必要がある業界では、レーザー溶接の低排出特性が企業にとってより有利な条件を提供することは間違いありません。
さらに、レーザー溶接では通常、溶接部分が小さくなるため、必要な材料の量とその後の処理が比較的少なくなり、環境への影響がさらに軽減されます。レーザー溶接を選択することで、企業は溶接効率を向上させるだけでなく、環境保護の面で社会的責任を示すこともできます。
労働安全衛生上の危険
労働安全衛生の観点から見ると、レーザー溶接の非接触性により、作業者が溶接熱や溶接煙にさらされるリスクが大幅に軽減されます。レーザー溶接作業中、溶接エリアの温度は通常より低いため、作業者が高温で火傷するリスクを軽減できます。さらに、レーザー溶接システムに装備されている安全保護手段(レーザー保護メガネや安全シールドなど)により、作業者の目と皮膚を効果的に保護し、怪我の可能性を減らすことができます。
一方、アーク溶接では溶接電源に直接接触する必要があるため、作業者は作業中に感電、火傷、煙の吸入などのリスクが高くなります。アーク溶接にも相応の安全保護対策が施されていますが、全体として、レーザー溶接は作業者の健康を保護する上でより明らかな利点があります。
規制遵守と基準
規制遵守と基準の面では、レーザー溶接の低排出と安全特性は、環境および安全規制を満たす上で一定の利点をもたらします。多くの業界では、溶接プロセスの環境基準と安全仕様が徐々に強化されており、レーザー溶接を使用すると、これらのますます厳しくなる規制要件を満たすことが容易になります。同時に、企業が溶接プロセスを改善すると、レーザー溶接技術を選択することで持続可能な開発への取り組みを示すこともできます。
全体的に、レーザー溶接は環境保護と労働者の安全の面で大きな利点を示します。環境保護と従業員の安全に注意を払う企業にとって、レーザー溶接装置への投資は生産効率を向上させるだけでなく、業界内での良好な企業イメージを確立することもできます。レーザー溶接を選択することは、技術のアップグレードであるだけでなく、持続可能な開発への取り組みでもあります。
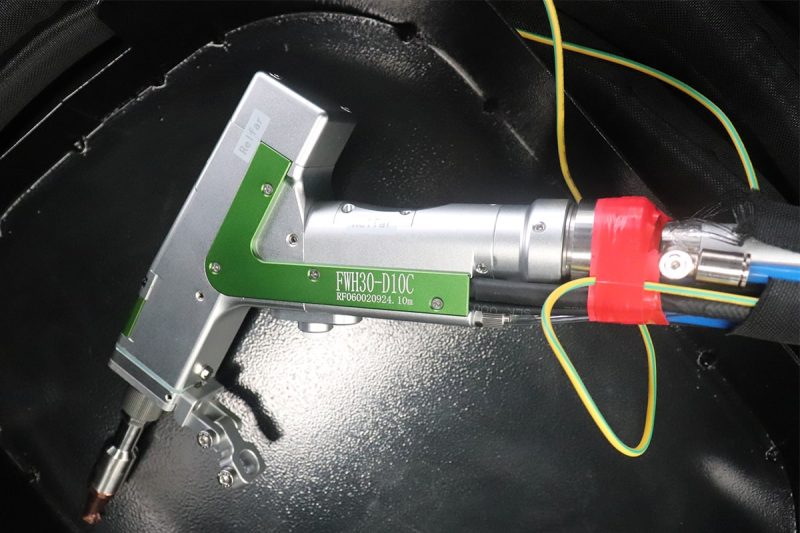
要約する
レーザー溶接機は、現代の工業溶接技術、特に溶接品質、精度、効率が極めて高い分野で徐々に重要な位置を占めるようになりました。従来のアーク溶接と比較して、レーザー溶接は熱影響部が低く、高速かつ高精度の溶接を実現できるため、材料の変形とその後の加工要件が軽減されます。このため、レーザー溶接は自動車製造、航空宇宙、医療機器、電子機器などの業界で広く使用されており、生産効率と製品品質を向上させる理想的な選択肢となっています。
さらに、環境保護と作業員の安全の面でのレーザー溶接の利点も無視できません。レーザー溶接は煙や有害ガスの発生が少なく、作業中の熱入力も低いため、環境規制を満たし、従業員の健康を守ることが容易です。この技術の持続可能性により、企業は経済的利益を追求しながら社会的責任を重視していることを実証できます。要約すると、レーザー溶接機は現代の産業に効率的で安全で環境に優しい溶接ソリューションを提供し、産業の発展を促進する重要な力となっています。
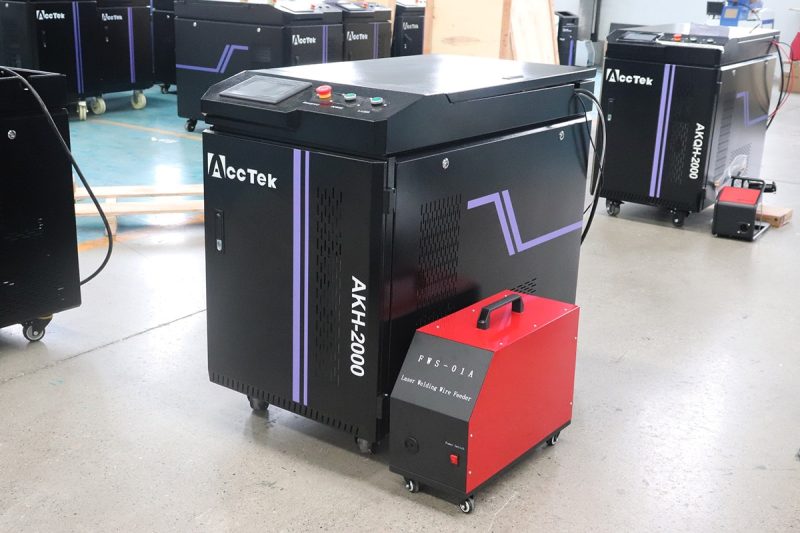
レーザー ソリューションを入手する
効率的で精密な溶接ソリューションを追求する場合、AccTek のレーザー溶接機は間違いなく最良の選択です。当社のレーザー溶接機器は、高度な技術を備えているだけでなく、溶接の品質と速度に関するさまざまな業界の厳しい要件を満たすことができ、優れた性能と信頼性も実証しています。自動車製造、航空宇宙、電子機器、医療機器の分野を問わず、当社のレーザー溶接機は生産効率の向上とコストの削減に役立ちます。
さらに、当社は包括的なアフターサービスも提供しており、使用中に心配する必要はありません。当社の専門チームは、いつでもお客様の質問にお答えし、技術サポートとメンテナンスサービスを提供し、最高の溶接結果を達成できるようお手伝いいたします。お気軽に当社にご連絡いただき、お客様のニーズに合わせたレーザーソリューションを入手し、AccTek レーザー溶接機をお客様の成功のパートナーにしてください。
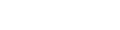
連絡先
- [email protected]
- [email protected]
- +86-19963414011
- No. 3 ゾーン A、Lunzhen 工業地帯、玉城市、山東省。
レーザー ソリューションを入手する