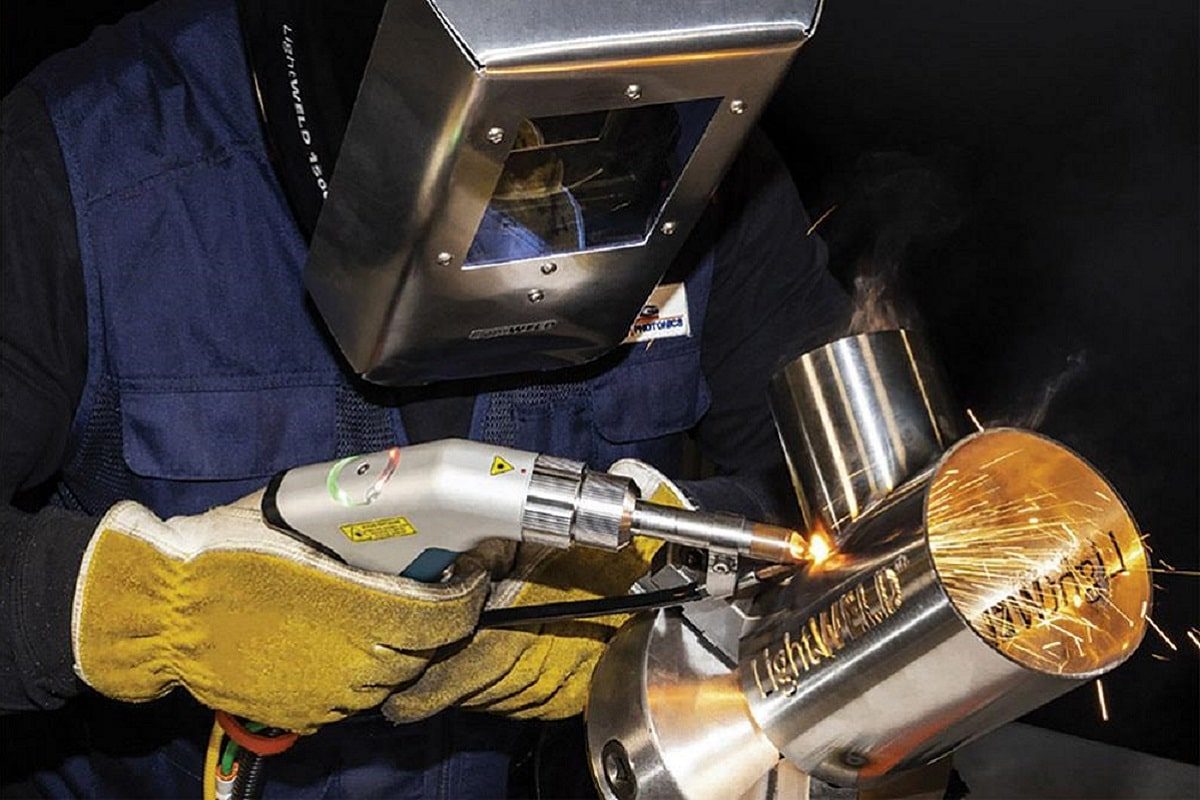
レーザー溶接 VS 従来の溶接
溶接は、熱を利用して2つ以上の別々の部品を接合する製造プロセスです。従来の溶接技術は数十年にわたって開発され、成熟した産業基盤を持っています。近年、レーザー溶接は、新興の近代的な溶接技術として急速に登場しました。両方の溶接技術にはそれぞれ特徴があり、さまざまな状況に適しています。この記事では、 レーザー溶接 と従来の溶接について、その動作原理、利点、制限、相違点を含めて説明し、最適な溶接方法を選択するのに役立ちます。
目次
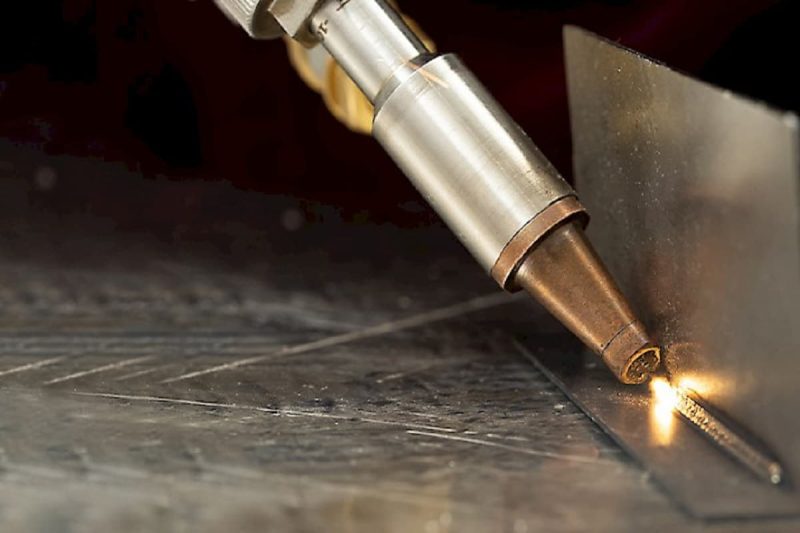
レーザー溶接とは何ですか?
レーザー溶接は、レーザービームを使用してエネルギーを集中させます。高度に集中したビームは、溶接材料を瞬間的に溶融温度まで局所的に加熱し、その後急速に冷却して凝固させます。このプロセスは数ミリ秒以内に完了し、ビームのエネルギー密度が非常に高いため、高精度の溶接を実現できます。レーザー溶接では通常、二酸化炭素レーザー、ファイバーレーザー、またはダイオードレーザーが使用されます。
レーザー溶接の仕組み
レーザー溶接では、集束レーザー ビームを使用して金属または熱可塑性プラスチックを接合します。航空宇宙や医療機器から高級宝飾品の製造まで、多くの業界で使用できます。レーザー溶接の基本的な動作原理は次のとおりです。
- レーザー源: 一般的に使用されるレーザー源には、二酸化炭素レーザー発生器、ファイバー レーザー発生器、ダイオード レーザー発生器などがあります。これらのレーザー源は、単色でコヒーレント性が高く、指向性の高いレーザー ビームを生成できます。
- ビームの集束: ワークピースを迅速に加熱するために、ビームのエネルギーを溶接領域に集中させるには、レンズまたは反射板を通してレーザー ビームを集束する必要があります。
- 吸収と伝導: レーザー光線がワークピースの表面に照射された後、エネルギーは反射されずにワークピースに吸収されます。レーザーエネルギーがどの程度吸収されるかは、素材の種類と色によって異なります。
- 溶融と溶融: レーザー ビームの高エネルギー密度により、溶接領域が融点以上に急速に加熱され、加工材料が瞬時に溶融します。
- 冷却と凝固:レーザー光の照射が止まると、溶接部分は急速に冷却され、溶融金属は凝固します。ワークはしっかりと接続されています。
レーザー溶接のメリット
レーザー溶接は非常に多用途であり、従来のアーク溶接と組み合わせてハイブリッド レーザー アーク溶接を形成できます。得られる溶接は、レーザー溶接とアーク溶接の利点を組み合わせたものです。レーザー溶接には、従来の溶接技術に比べて次のようないくつかの利点があります。
- 高精度:レーザー溶接は位置決め精度と溶接品質が非常に高く、ミクロンレベルの溶接精度を達成できます。また、レーザー溶接によって生成される溶接は一般に高品質であるため、マイクロエレクトロニクス製造や医療機器など、高精度の溶接が必要な用途に特に適しています。
- 非接触: レーザー溶接は、ワークピースの表面に損傷を与えず、物理的接触を必要としない非接触プロセスです。レーザー溶接で脆性材料や繊細な部品を扱う場合に非常に有利です。
- 環境保護: 従来の溶接と比較して、レーザー溶接は通常、廃棄物や有害なガスの排出が少なく、より環境に優しいです。
- 低入熱: レーザー溶接は溶接面積が非常に小さいため入熱が低く、変形や熱影響部のサイズが小さくなります。これは、薄いシート材料や熱に弱い部品を溶接する場合に非常に重要です。
- 処理時間の短縮: レーザー溶接は高速であり、溶接タスクを迅速に完了し、生産効率を向上させることができます。さらに、レーザー溶接では溶加材が不要なため、材料の無駄が削減されます。また、このプロセスは従来の溶接よりもコスト効率が高いことが証明されています。
- 幅広い応用性:レーザー溶接は、金属、プラスチック、セラミックスなどを含むさまざまな材料に使用できるため、さまざまな産業分野で広く使用されています。
- レーザー溶接は非常に多用途であり、従来のアーク溶接と組み合わせてハイブリッド レーザー アーク溶接を形成できます。得られる溶接は、レーザー溶接とアーク溶接の利点を組み合わせたものです。
レーザー溶接のデメリット
レーザー溶接は、高精度と効率を備えた最新の溶接技術ですが、いくつかの欠点と制限もあります。レーザー溶接の主な欠点は次のとおりです。
- 高コスト: レーザー発生器、光学部品、冷却システムなどを含むレーザー機器の購入およびメンテナンスのコストは比較的高額です。このため、予算が限られている中小企業や製造業者によるレーザー溶接の導入が制限される可能性があります。
- 高い材料選択要件: レーザー溶接には、ワークピースの材料と品質に関して比較的高い要件があります。金属などの導電性の高い材料にはより適していますが、一部の非導電性または透明な材料では、その適用範囲が制限されます。
- 高融点材料の加工の難しさ:タングステンやモリブデンなどの高融点材料と比較して、レーザー溶接はより高い出力と長い溶接時間を必要とするため、熱影響や変形の問題が発生する可能性があります。
- 高い洗浄要件: レーザー溶接では、ワークピースの表面の品質に対して非常に高い要件が求められます。たとえ小さな汚れ、酸化層、またはグリースであっても、溶接の品質に影響を与える可能性があります。したがって、通常は溶接前に慎重な表面処理と洗浄が必要です。
- 安全性の問題: レーザー光線は高エネルギーを持っており、人間の目や皮膚に損傷を与える可能性があります。したがって、オペレータは適切な保護メガネや保護服を着用するなど、必要な安全対策を講じる必要があります。
- 可視光の干渉: 可視光レーザーは可視光によって干渉される可能性が高いため、作業エリアの光が適切に制御されていることを確認するための対策が必要です。
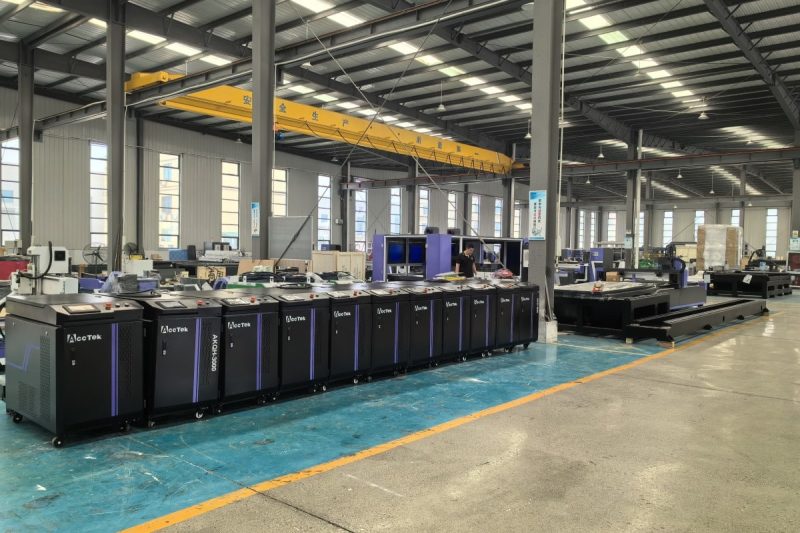
従来の溶接とは何ですか?
従来の溶接技術では、熱源を使用して溶接材料を溶かし、その後冷却して固化させて 2 つ以上の部品を接合します。従来の溶接には、ガスシールド溶接、スポット溶接、抵抗溶接などの方法も含まれます。これらの伝統的な溶接技術にはそれぞれ利点と適用範囲があります。特定の用途や要件に応じて、製造や修理に適切な溶接方法を選択できます。
従来の溶接の仕組み
従来の溶接技術は、金属やその他の材料を接合するための長年使用されている一連の伝統的な方法であり、さまざまな製造や修理の分野で使用されています。一般的な伝統的な溶接技術をいくつか紹介します。
- アーク溶接: アーク溶接は、アークを使用して高温を発生させ、溶接材料とワークピースを溶かし、その後冷却して凝固させて溶接部を形成する、一般的な伝統的な溶接方法です。主なアーク溶接方法には、手動アーク溶接、ガスシールド溶接(MIG)、手動金属アーク溶接(SMAW/ARC)、TIG溶接(GTAW)があります。
- ガス溶接:溶接材料を炎を使って加熱し、溶かして接合すること。最も一般的なガス溶接方法はアセチレン酸素溶接です。これは、アセチレンと酸素の炎を使用してワークピースを加熱し、板金、パイプ、金属の修理に適しています。
- 抵抗溶接: ワークピースに電流を流して熱を発生させ、2 つの金属片を接合します。抵抗溶接の主な方法には、スポット溶接、シーム溶接、はんだ付けなどがあります。
- 圧力溶接: 圧力溶接は、熱と圧力を加えて 2 つの金属を接合する方法で、抵抗スポット溶接、抵抗シーム溶接、およびエレクトロニクスが含まれます。
従来の溶接の利点
しかし、従来の溶接プロセスは依然として多くの業界にとって耐久性のある製造ソリューションであり、レーザー溶接には従来の溶接方法に比べていくつかの利点があります。具体的なポイントは以下の通りです。
- 低コスト: 従来の溶接装置は一般に比較的安価であり、オペレーターのトレーニングも低コストです。これにより、初期投資と運用コストが削減され、予算が限られているビジネスに適しています。
- 幅広い用途: 従来の溶接技術は、金属からプラスチックまで、さまざまな種類の材料やさまざまな厚さのシートに使用できます。この多用途性により、さまざまな用途に適しています。
- 大型構造物の溶接: 従来の溶接技術は、橋、建物、造船などの大型構造物の溶接に適しています。強力な接続性と適用性を備えています。
- 耐久性: 従来の溶接技術は一般に強力な接続を実現し、車両やエンジニアリング構造物など、高強度の接続が必要な用途に適しています。
- 自動化アプリケーション: 従来の溶接技術を自動化やロボット工学と組み合わせることで、特に大量生産の生産効率を向上させることができます。
- 基材の適応性: 従来の溶接方法は、さまざまな種類の金属材料や非金属材料を含む、さまざまな種類の基材に適しています。
- 修理と修復: 従来の溶接技術は、特に電源から離れた場所や複雑な環境での修理とメンテナンスにおいて依然として重要な役割を果たしています。
- 溶融深さ: 従来の溶接は通常、溶接深さがより深く、より深い溶接が必要な用途に適しています。
- 溶接材料の入手可能性: 従来の溶接方法では、多くの場合、容易に入手できる一般的な溶加材料が使用されます。
従来の溶接の欠点
従来の溶接技術は依然として多くの用途で価値を持っていますが、いくつかの欠点や制限もあります。レーザー溶接技術と比較した従来の溶接技術の主な欠点のいくつかを以下に示します。
- 精度の低下: 溶接プロセスでは、大きな溶接幅と熱の影響を受ける部分が生じる可能性があり、これによりワークピースの変形、寸法の不安定性、または溶接接続の不正確さが生じる可能性があります。
- 大きな熱影響: 従来の溶接技術によって生成される入熱は比較的高く、ワークピースに大規模な熱影響を簡単に引き起こす可能性があり、特に熱に弱い材料の場合、ワークピースの性能と品質に悪影響を与える可能性があります。 。
- 生産効率の低下: 従来の溶接では、溶接速度が遅いため、通常、比較的長い溶接時間を必要とします。これにより、大規模生産の効率が制限され、製造コストが増加する可能性があります。
- 廃棄物とガスの排出量の増加: 従来の溶接では通常、より多くの溶加材と廃棄物が必要となり、大量の廃棄物と有害なガスの排出が発生し、環境に悪影響を及ぼします。
- 大きな安全上のリスク: 従来の溶接中に発生する炎や熱スパッタは、作業者や周囲の環境に危険を引き起こす可能性があります。
- 洗浄と後処理の要件: 従来の溶接プロセスでは、溶接残留物を除去したり溶接の品質を向上させるために後続の洗浄と処理ステップが必要になることが多く、これにより生産時間とコストが増加します。
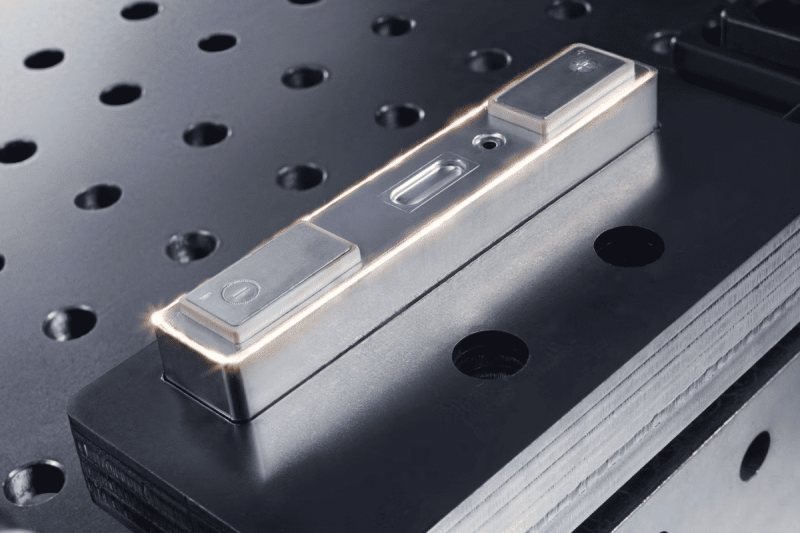
レーザー溶接 VS 従来の溶接: どちらの溶接方法を選択すべきでしょうか?
レーザー溶接と従来の溶接にはそれぞれ独自の利点があります。従来の溶接は実装が簡単で、習得には低投資で済むため、すべての製造業に適しています。レーザー溶接は最も先進的なタイプの溶接であり、高精度、低い熱歪み、より速い処理時間を実現します。用途、プロジェクトの種類、予算に基づいて、どの溶接方法が最適であるかを検討する必要があります。
材料の種類
最初に考慮すべきことは、溶接する材料の種類です。一般にレーザー溶接は金属や溶接に適していますが、従来の溶接技術は多くの場合、金属、プラスチック、ガラスなどのさまざまな種類の材料に適しています。
精度要件
高精度で精密な溶接が必要な場合は、精度と溶接品質が高いレーザー溶接の方が良い選択肢となることがよくあります。従来の溶接技術では、この精度要件を満たすことができません。
熱影響
溶接プロセスがワークピースに及ぼす熱の影響を考慮してください。特に熱に弱い材料を溶接する場合など、熱の影響を受ける部分を減らす必要がある場合は、入熱が少ないレーザー溶接の方が適していることがよくあります。
生産効率
大量の溶接が必要な場合は、従来の溶接技術の方が一般的に高速であるため、大量生産に適している可能性があります。レーザー溶接は低速であり、小ロット生産や精密プロセスに適しています。
コストに関する考慮事項
コストの見積もりは重要な要素です。レーザー機器は一般に高価であり、メンテナンス費用も高くなります。従来の溶接技術は、特に小規模なプロジェクトや予算が限られている企業にとっては、より安価なことがよくあります。
材料の厚さ
ワークの厚みを考慮してください。レーザー溶接は薄い材料に適していますが、厚い材料の場合は複数のパスが必要になる場合があります。従来の溶接は一般に、さまざまな厚さの材料に適しています。
環境および安全要件
作業環境と安全要件を考慮してください。レーザー溶接では、オペレータの安全を保護するために、より厳格な環境管理と安全対策が必要となる場合があります。
要約する
従来の溶接方法には利点がありますが、レーザー溶接は金属の接合によく使用され、その精度、制御性、繊細な金属部品や薄い金属部品の溶接能力により、さまざまな部品製造業界で人気が高まっています。適切な溶接方法の選択は、特定のアプリケーションのニーズ、コスト、品質基準によって異なります。レーザー溶接機をお探しの場合は、次の点を考慮してください。 AccTek レーザー。当社にはレーザー溶接の分野での実績のある経験があります。当社のレーザー溶接能力に関する情報が必要な場合は、当社を訪問し、お問い合わせください。
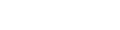
連絡先
- [email protected]
- [email protected]
- +86-19963414011
- No. 3 ゾーン A、Lunzhen 工業地帯、玉城市、山東省。
レーザー ソリューションを入手する