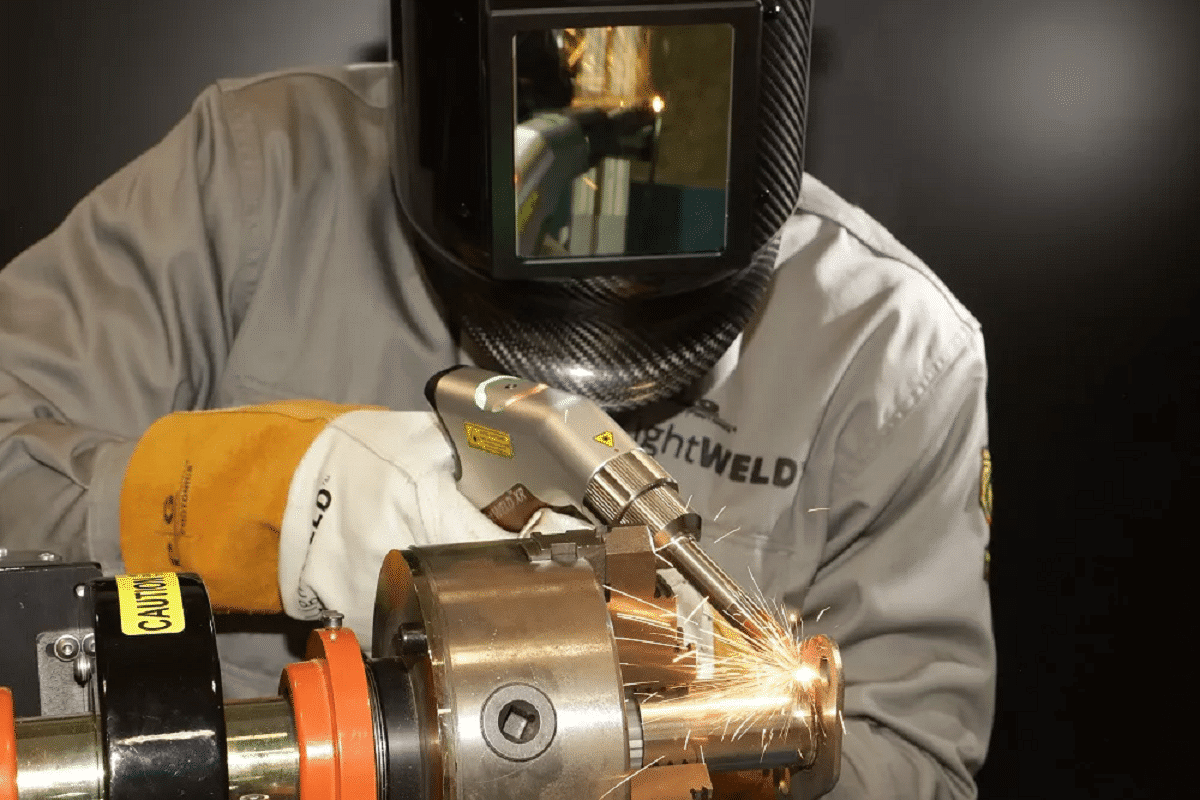
レーザー溶接の長所と短所
レーザー溶接は、レーザー ビームを使用して熱源を集中させ、複数の金属片を接合する溶接技術です。メーカーや板金加工業者は、高品質、高速スループット、後処理コストの削減を目的として、レーザー技術を使用した溶接のこのハイテクプロセスへの依存を高めています。始める前に、レーザー溶接について詳しく知りたいですか?レーザー溶接の長所と短所について詳しくは、以下をお読みください。
目次
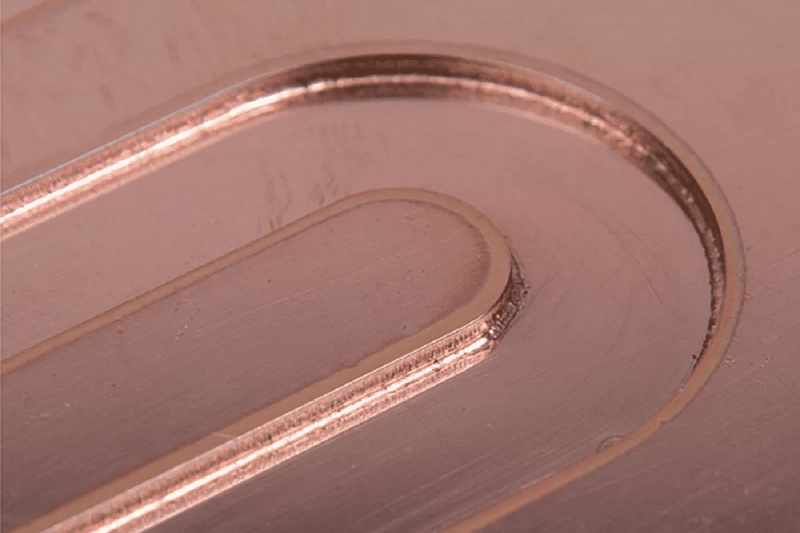
レーザー溶接はどのように行われるのですか?
レーザー溶接またはレーザー ビーム溶接は、レーザーを集中させた熱源を使用して材料を溶かすプロセスです。レーザー溶接は、伝導制限溶接と深穴溶接という 2 つの根本的に異なるモードで動作します。レーザー ビームと溶接対象材料との相互作用モードは、ビームがワークピースに当たるときの電力密度によって異なります。レーザー溶接の動作原理は、高電力密度レーザーを集中させ、2 つの金属表面の接合部に熱を加えることです。金属表面がレーザーを吸収すると、材料が加熱されて溶け、2 つの表面の間に溶接部が形成され、溶接が完了します。
レーザー溶接は溶接精度と品質が高くなります。レーザー自体はほとんど熱を発生しないため、レーザー溶接後に生じる溶接継ぎ目も比較的小さく、レーザー溶接は特にエレクトロニクスやガラス/金属シールなどの薄い材料に適しています。一方、厚い材料を溶接する場合、四角いエッジの部品間に狭くて深い溶接が行われます。現在、最新のレーザー溶接アプリケーションには高度な光学系が組み込まれており、プログラム可能なロボットを使用してワークピース内の領域を正確に特定できるようになります。

レーザー溶接のメリット
レーザー溶接には、従来の溶接技術に比べて多くの利点があります。まず、レーザー溶接は追加のツールや治具を必要とせずに行うことができるため、より正確な結果が得られます。さらに、レーザーは信じられないほどの高温に達する可能性があるため、レーザー溶接では非常に強力で耐久性のある溶接が行われます。
より高い精度
レーザー溶接では非常に細いレーザー ビームが生成され、直径がミリメートルほどの小さな領域であっても、溶接する領域に非常に正確に焦点を合わせることができます。溶接プロセスのより正確な制御に加えて、溶接材料の無駄やエラーも回避し、安定した品質を保証します。
高品質の溶接
レーザー溶接の主な利点の 1 つは、より高品質の溶接が行われることです。その理由は、レーザー溶接では他の方法よりも狭くて深い溶接が行われ、2 つの金属の間により強力な接合が形成され、極端な温度や過酷な環境に耐えることができるためです。レーザー溶接の均一なパルスにより、ガスシールド溶接や電気溶接では避けられないビーディングやバリがなく、レーザー溶接後に非常にきれいな継ぎ目が得られます。
レーザーにより溶接速度が向上します
レーザー溶接は、従来の方法よりも何倍も高速です (最大 5 ~ 10 倍)。溶接速度は使用するレーザー発生器の種類と出力によって異なります。溶接速度が速いと、1 時間あたりにより多くの部品を生産できるため、納期が短縮され、生産性が向上します。さらに、レーザー溶接は自動化装置と統合できるため、長期間の稼働が可能になります。
溶接後の処理コストを削減
従来の溶接およびレーザー溶接のプロセスでは、2 つの表面の接合部で熱が伝達されます。従来の方法を使用して溶接する場合、材料は曲げ、応力、その他の悪影響を受ける可能性があります。ただし、レーザーの出力密度は非常に高く、溶接部の両側の熱影響部の幅は狭く、溶接部付近の材料の熱損傷や性能損失は軽減されます。したがって、サンプルの変形は、他の多くのプロセスで溶接されたサンプルの変形よりも少なくなります。
通常、レーザー溶接後の研削は必要ないため、後処理コストを大幅に削減できます。このような装飾的な溶接継ぎ目があることは、製品の外観を向上させ、顧客に良い第一印象を与えるのにも役立ちます。
汎用性
レーザー溶接は非常に多用途であり、さまざまなレーザー ユニットがさまざまな種類の溶接に適しています。たとえば、レーザー溶接は、軟鋼、ステンレス鋼、チタンなどのさまざまな金属材料に実行できます。レーザー溶接は、海運業界で使用される厚い鋼板の溶接、宝飾品で使用される貴金属の溶接、または電気自動車のバッテリーの銅接点の溶接に使用できます。手の届きにくい箇所にも到達し、非接触で長距離溶接を実現し、柔軟性に優れています。レーザー溶接は、大量に生産される小型および小型ワークピースの組み立ておよび溶接に非常に適しています。
セキュリティの強化
非接触接合プロセスとしてのレーザー溶接のもう 1 つの利点は、安全性です。低出力のレーザー溶接機は安全上のリスクが少なく、通常は持ち運びが可能で、手持ち式の溶接ヘッドを使用して溶接を開始します。高出力 レーザー溶接機 遠隔制御されるため、作業者は溶接エリアに近づかなくてもレーザー ビームを照射できます。さらに、レーザー溶接は他の方法よりもヒュームの発生が少ないため、作業者の呼吸器疾患のリスクが軽減され、空気の質が改善されます。
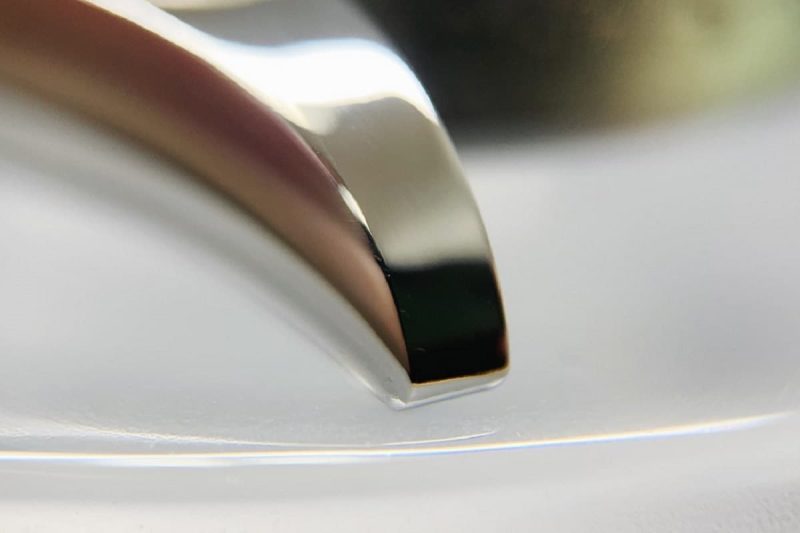
レーザー溶接のデメリット
レーザー溶接の使用には多くの利点がありますが、レーザー溶接に関連するいくつかの欠点もあり、この技術に投資する前に考慮する必要があります。これにより、マシンについての理解を深めることができ、マシンの故障に伴うコストを削減できます。
高額な初期費用
レーザー溶接の主な欠点は、初期コストが高いことです。レーザー ユニットの初期取得コストは通常、従来のシステムの 2 倍または 3 倍で、一度に多額の投資が必要になります。また、従業員に使用方法を指導するのにも費用がかかります。さらに、レーザー溶接機のメンテナンスおよび修理コストも、他のタイプの溶接装置よりも高くなる可能性があります。しかし、レーザー溶接は、その優れた速度、精度、および汎用性により、すぐに投資を回収できます。レーザー溶接の効率志向により、企業は生産を最適化し、材料の無駄を減らし、全体的な収益性を高めることができます。
低いバックラッシュ耐性
クリアランス公差が低いということは、溶接部の組み立て精度が高く、ワーク上のビームの位置に明らかなずれがないことを意味します。これは、集束レーザーのスポット サイズが小さく、溶接シームが狭いため、ワークピースの組み立て時やビームの位置決めが不正確な場合に溶接欠陥が発生しやすいためです。バックラッシュ許容値が低いということは、上流のプロセス/サプライヤーが厳しい許容レベルを確実に満たすことができることを確認する必要があることを意味します。
トレーニングが必要です
製造業や金属加工業において、レーザー溶接は比類のない精度と効率性を提供する革新的な技術となっています。しかし、レーザー溶接機の潜在能力を最大限に引き出すには、機器を購入するだけでは不十分です。安全な操作を保証し、パフォーマンスを最適化し、レーザー溶接機が提供する数多くのメリットを最大限に引き出すには、オペレーターの広範囲にわたる最新のトレーニングが必要です。オペレーターのトレーニング セッションにより、レーザー溶接機の全体的なコストが増加する可能性があります。
限定された用途
レーザー溶接機は多くの用途で優れた利点を提供しますが、厚い材料の溶接にはあまり適していない、特定のタイプの接合には使用できないなど、特定の制限もあります。また、反射性の高い表面などの特定の材料は、レーザー溶接に適さない場合があります。このような場合、アーク溶接や電子ブック溶接などの代替溶接方法の方が適切な場合があります。溶接プロジェクトを開始する前に、その特定の要件を評価し、専門家に相談して最適な溶接方法を決定することをお勧めします。
セキュリティ上のリスクがあります
レーザー溶接はその精度と効率によって溶接業界に革命をもたらしましたが、それでも一定の安全上のリスクが伴います。たとえば、レーザー溶接機を使用する場合、適切な目の保護具を使用しないと、溶接プロセス中に放射される強力なレーザー光線が重度の火傷を引き起こしたり、目に永久的な損傷を与える可能性があります。
レーザー溶接機を使用する場合、レーザー溶接に関連するリスクを最小限に抑えるために、包括的な安全プロトコル、適切なトレーニング、および機器の定期的なメンテナンスが必要です。レーザー溶接には、他の溶接方法よりも多くの保護措置が必要です。
要約する
レーザー溶接は、製造業者に効率的で低コストの溶接方法を提供できる優れた技術です。このプロセスには、溶接中のクリアランス許容差が低いなどの欠点もありますが、少し注意すれば克服できます。金属を迅速かつ正確に接合する信頼性の高い方法を探している企業であれば、レーザー溶接がまさに必要なものかもしれません。
実際のレーザー溶接の詳細については、このビデオをご覧ください。さらに質問がある場合は、 AccTek レーザー お客様が正しい決定を下せるよう、具体的なアプリケーションについて喜んでご相談させていただきます。
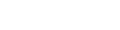
連絡先
- [email protected]
- [email protected]
- +86-19963414011
- No. 3 ゾーン A、Lunzhen 工業地帯、玉城市、山東省。
レーザー ソリューションを入手する