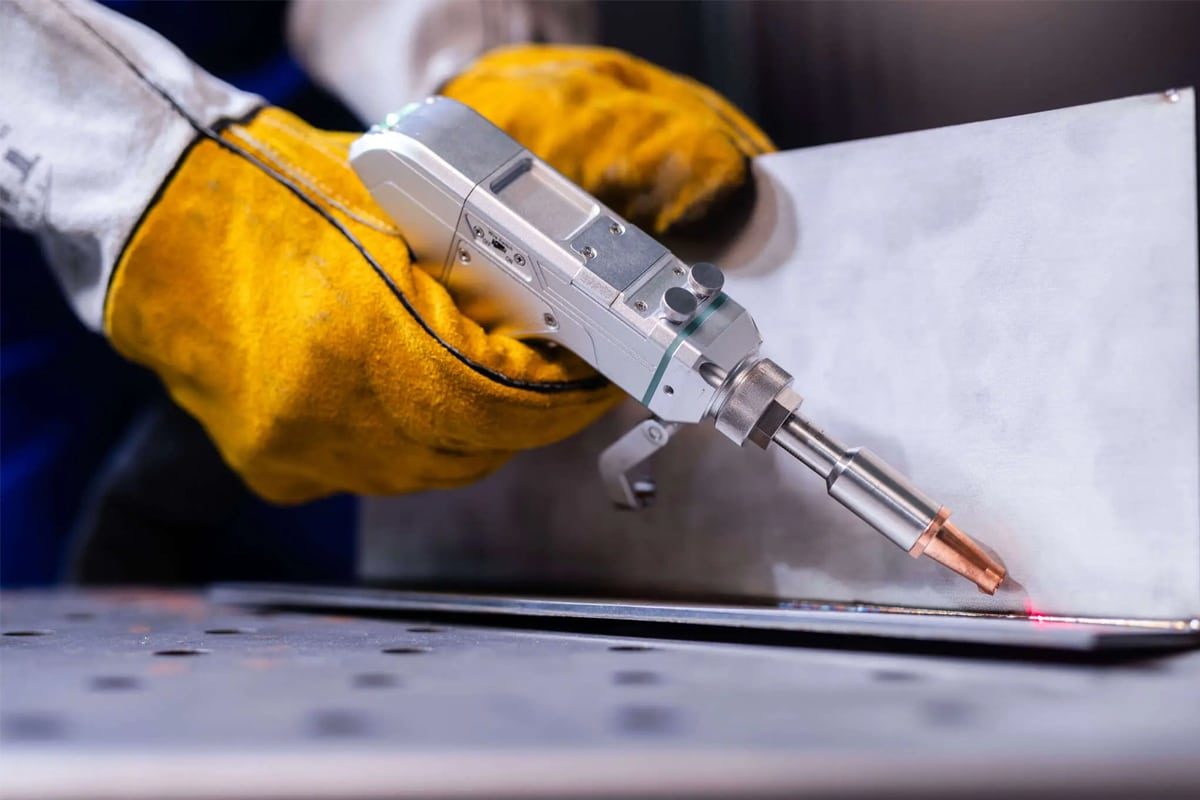
レーザー溶接の長所と短所
レーザー溶接は、集束したレーザー光線を使用して材料を融合し、正確で耐久性のある接合を作成する高度な接合技術です。電気アークやガス燃料の炎に依存する従来の溶接方法とは異なり、レーザー溶接は集中した光エネルギーを利用し、比類のない精度、速度、および最小限の熱歪みを提供します。このプロセスは、高品質で一貫した結果が不可欠な自動車、航空宇宙、医療機器製造、電子機器などの業界で貴重な資産となっています。レーザー溶接の集中したエネルギーにより、深い浸透と狭い溶接が可能になり、溶接後の大規模な処理の必要性が軽減されます。ただし、その利点にもかかわらず、レーザー溶接には、初期投資コストが高い、ジョイントの位置合わせに敏感、熟練したオペレーターが必要であるなど、特定の制限もあります。レーザー溶接の長所と短所の両方を理解することで、メーカーは情報に基づいた決定を下し、この強力な技術を最適化して特定の生産ニーズと品質基準を満たすことができます。
目次
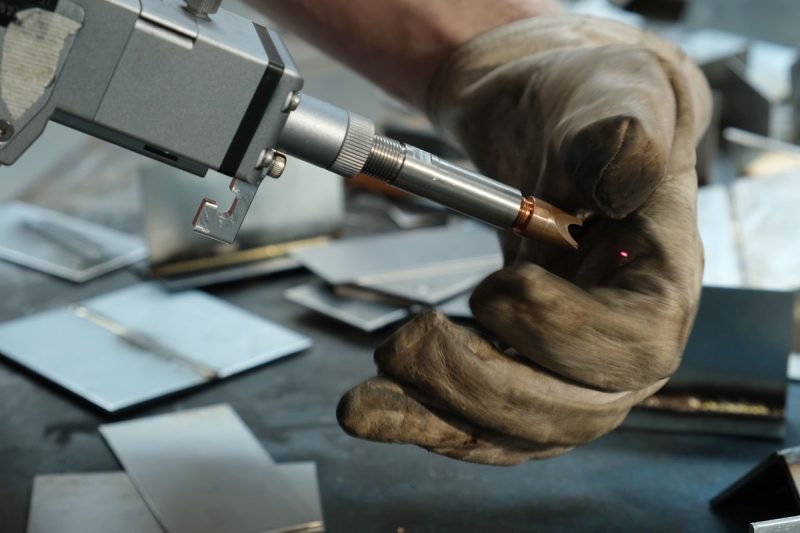
レーザー溶接の仕組み
レーザー溶接は、強力なレーザー ビームを使用して材料を融合し、強力で耐久性のある接合部を作成する高精度のプロセスです。レーザー溶接の原理とレーザー溶接モードの種類 (伝導とキーホール) を理解することで、メーカーはさまざまな産業用途にレーザー溶接を効果的に活用できます。
レーザー溶接の原理
レーザー溶接は、高エネルギーのレーザー光を材料の小さな領域に集中させることで機能します。この集中したエネルギーにより材料が急速に加熱され、溶融して融合します。広い加熱ゾーンに依存することが多い従来の溶接とは異なり、レーザー溶接は熱影響ゾーンを最小限に抑え、歪みを減らし、よりきれいで高品質の接合部を提供することに重点を置いています。融合は、伝導モードまたはキーホール モードの 2 つの主要なモードのいずれかで発生します。
- レーザー出力と焦点: レーザーの出力密度とスポット サイズによって、溶接の深さと幅が決まります。出力密度が高いほど溶接が深くなり、出力設定が低いほど溶接が細かく浅くなります。
- 熱制御: レーザー溶接では、熱に敏感な材料や複雑な部品を接合するために不可欠な、熱入力の正確な制御が可能になります。
エネルギーを制御し、熱を集中的に適用するというこれらの原理により、レーザー溶接は最小限の後処理で高速かつ正確な結果を達成できるため、自動車、航空宇宙、医療機器製造などの分野に最適です。
レーザー溶接モードの種類
レーザー溶接は通常、それぞれ異なる特性と用途を持つ 2 つの主なモードのいずれかで動作します。
伝導モード溶接
伝導モードでは、レーザーエネルギーが材料の表面で吸収され、熱が材料に伝導されます。材料は融点に達し、蒸発することなく浅い溶接プールを形成します。このモードは、より広く浅い溶接を特徴とし、美観と最小限の熱影響が求められる用途に適しています。
特徴:
- 浅い溶接溶け込み、通常は 2 mm 未満。
- 表面の変形を最小限に抑えた、滑らかで幅広の溶接。
- キーホール形成のリスクが最小限に抑えられ、多孔性や空隙の可能性が減少します。
用途:
- 薄い素材や見た目の品質が重要となる用途によく使用されます。
- きれいな表面仕上げが求められるジュエリー、医療機器、電子機器などの用途に最適です。
キーホールモード溶接
キーホール モードは、レーザー出力密度が材料を蒸発させるほど高く、溶接部内に「キーホール」または狭い空洞が形成される場合に発生します。キーホールにより、レーザー エネルギーが深く浸透し、高アスペクト比の溶接 (深く狭い) が生成されます。このモードは、深い浸透と強力な溶接が特徴で、厚い材料や構造用途に効果的です。
特徴:
- 幅が狭く、溶接の溶け込みが深い(最大数センチメートル)。
- アスペクト比が高いため、強力で集中した溶接が可能になります。
- キーホール内での多重反射による効率的なエネルギー吸収により、より深い溶接の浸透が促進されます。
用途:
- 自動車や航空宇宙部品など、強力で耐久性のあるジョイントを必要とする高負荷用途に適しています。
- 深い溶融が必要な厚い材料や高強度金属に効果的です。
伝導モードとキーホール モードの違いを理解することで、レーザー溶接で最高の結果を得ることができます。伝導モードは、美観と熱の影響を最小限に抑えることを優先する表面レベルの溶接に最適です。一方、キーホール モードは、浸透と耐久性が重要となる、より深く強度の高い接合部に適しています。適切なモードを選択することで、メーカーはさまざまな業界の溶接アプリケーションで効率、品質、信頼性を高めることができます。
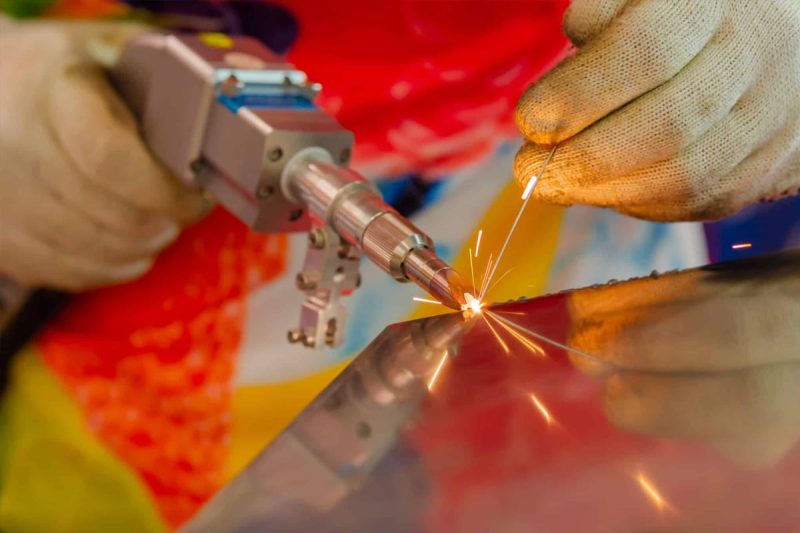
レーザー溶接の利点
レーザー溶接は従来の溶接技術に比べて多くの利点があり、精度、スピード、きれいな溶接を必要とする業界では欠かせないツールとなっています。
精度と精度
レーザー溶接は、従来の溶接方法では実現が難しい並外れた精度を実現します。高度に焦点を絞ったレーザー ビームにより、メーカーは正確な溶融点を制御できるため、複雑な溶接パターンや狭い接合幅が可能になります。この精密な制御により、医療機器、電子機器、航空宇宙部品など、厳しい許容差が重要な用途では特に、エラーのリスクが最小限に抑えられ、やり直しの必要性が減ります。レーザー溶接は、誤差の範囲を最小限に抑えることで、生産工程全体で一貫した品質レベルを確保できるため、信頼性の高い高精度の溶接を必要とする業界に最適です。
高い溶接速度
レーザー溶接は、レーザービームによって供給される集中エネルギーのおかげで、従来の溶接技術よりも大幅に高速で動作できます。これにより、メーカーは溶接を短時間で完了でき、生産サイクルの高速化とスループットの向上につながります。自動車製造や家電製品などの大量生産環境では、レーザー溶接の高速化により、時間と労力を大幅に節約できます。さらに、この高速プロセスにより、リソースをより効率的に使用でき、溶接品質を損なうことなく厳しい生産スケジュールを満たすことができます。
非接触プロセス
非接触溶接法であるレーザー溶接では、溶接ツールとワークピースの物理的な接触が回避されます。これにより、ツールの摩耗がなくなり、汚染の可能性が大幅に減少します。非接触溶接は、従来の方法では簡単に損傷する可能性のある繊細な部品や小さな部品を扱う場合に特に役立ちます。レーザーは物理的に接触しないため、摩耗した溶接チップを交換したり、機械的衝撃を管理したりする必要がなく、作業スペースをより清潔に保つことができます。この非侵襲的なアプローチにより、レーザー溶接は、ワークピースの完全性を維持することが不可欠なマイクロエレクトロニクスやジュエリーなどの用途に最適です。
深い溶け込みと狭い溶接
レーザー溶接の集中エネルギーにより、厚い材料でも、狭い溶接ビードで深い溶け込みが可能になります。この機能は、レーザーのエネルギーを小さなスポットに集中させることで実現され、深くて狭い、高アスペクト比の溶接を作成します。その結果、周囲の材料に余分な熱が広がることなく強力な接合部が実現し、ワークピースの全体的な構造的完全性を維持するのに役立ちます。航空宇宙、自動車、重機製造などの業界では、狭くて深い溶接を作成できる機能により、厚い耐荷重材料を強度と耐久性のある状態で接合できます。
難溶接材料の溶接能力
レーザー溶接は、従来の方法では溶接が難しいさまざまな難題材料に非常に適応性があります。高強度金属、熱に弱い材料、さらには融点や熱伝導率の違いにより通常は難しい異種金属の接合も成功させることができます。たとえば、航空宇宙や医療機器の製造でよく使用されるチタンやステンレス鋼は、材料の特性を損なうことのない正確な温度制御が可能なため、レーザー溶接でよく使用されます。この汎用性により、メーカーは材料の選択肢を広げ、溶接品質に自信をもって先進的な金属や合金を設計に取り入れることができます。
歪みと熱影響部を最小限に抑える
レーザー溶接の最も重要な利点の 1 つは、熱による歪みを最小限に抑えられることです。レーザー ビームは溶接接合部に熱を正確に集中させるため、熱影響部 (HAZ) は小さく抑えられ、周囲の材料の特性が歪んだり変化したりするリスクが軽減されます。この正確な熱の適用は、ワークピースの機械的完全性を維持するために不可欠であり、熱に弱い材料を扱う場合に特に役立ちます。寸法安定性と材料特性が重要な電子機器や医療機器製造などの分野では、レーザー溶接によって歪みが軽減され、HAZ が小さくなるため、パフォーマンスを犠牲にすることなく一貫した品質を確保できます。
きれいで美しい溶接
レーザー溶接により、滑らかできれいで見た目に美しい溶接継ぎ目が作られます。集中したレーザーエネルギーが材料を正確に溶かし、スパッタ、酸化、その他の一般的な溶接欠陥を減らします。このきれいな仕上がりは、多くの場合、溶接後の処理や仕上げがほとんどまたはまったく必要ないことを意味します。これにより、時間と追加コストの両方を節約できます。ジュエリー、消費者製品、高級自動車部品など、溶接が目に見える用途では、レーザー溶接によるきれいな溶接により、完成品の美観が向上します。滑らかな溶接は機能上の利点にも貢献し、重要な環境での汚染や腐食の可能性を減らします。
メンテナンスと運用コストが低い
レーザー溶接装置への初期投資は高額になる場合がありますが、この技術は一般的にメンテナンスが少なく、長期的には経済的です。レーザー溶接は非接触プロセスであるため、部品の摩耗が最小限で、消耗品を頻繁に交換する必要がありません。さらに、レーザー システムは通常、非常に効率的であるため、無駄を最小限に抑えながら、より多くのエネルギーを溶接に向けることができます。これは、長期的には、メンテナンスとエネルギー使用の両方の面でコスト削減につながり、長期的な運用効率が優先される業界にとって、レーザー溶接は魅力的な選択肢となります。
エネルギー効率
レーザー溶接は、電気エネルギーを集中した光エネルギーに変換する効率が非常に高いです。大量の熱を無駄にする可能性のある従来の溶接方法とは異なり、レーザー溶接はエネルギーを正確に使用するため、全体的なエネルギー消費が少なくなります。この効率性により、運用コストが削減されるだけでなく、生産の二酸化炭素排出量が削減され、環境的に持続可能な製造方法もサポートされます。自動車や家電製品などのグリーン製造に取り組む業界では、レーザー溶接のエネルギー効率は、高品質の溶接を提供しながら、より広範な持続可能性の目標と一致しています。
自動化と柔軟性
レーザー溶接システムは、自動化された生産ライン、ロボット、CNC システムと簡単に統合できるため、製造プロセスに柔軟性が加わります。自動化されたレーザー溶接により、メーカーは最小限の手動介入で、一貫性のある繰り返し可能な溶接を実現できます。さらに、レーザー溶接装置の柔軟性により、製品の種類や構成をすばやく切り替えることができるため、メーカーは変化する生産需要に適応できます。この自動化機能は、大量生産と短いターンアラウンド タイムが標準である自動車や電子機器などの業界では不可欠です。自動化によって溶接プロセスを合理化することで、メーカーは人件費を削減し、生産性を高め、全体的な製品品質を向上させることができます。
これらの詳細な利点は、製造プロセスで精度、効率、品質が求められる業界にとってレーザー溶接が強力なツールである理由を示しています。それぞれの利点は、さまざまな用途にわたる現代の製造業にとって貴重な資産としてのこの技術の評価に貢献しています。
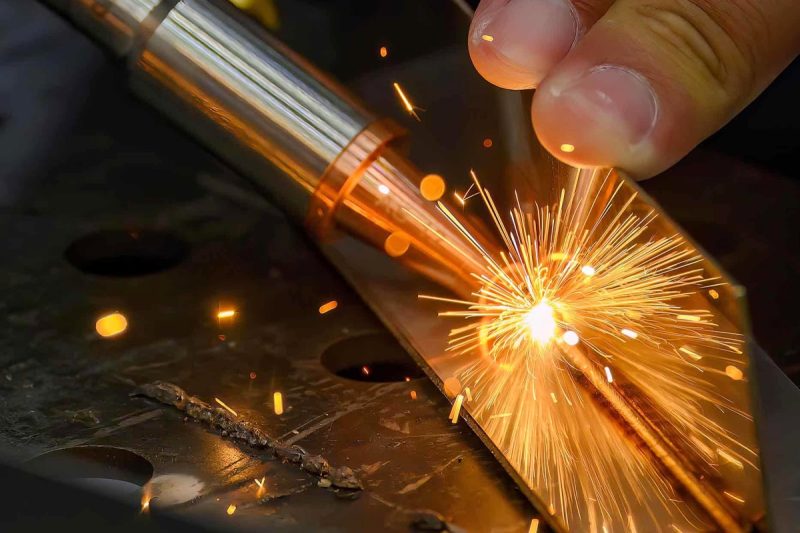
レーザー溶接のデメリット
レーザー溶接には数多くの利点がありますが、特定の用途への適合性を制限する可能性のある欠点もいくつかあります。
初期投資額が高い
レーザー溶接システムには、通常、多額の先行投資が必要です。高出力レーザー、精密光学機器、冷却システム、自動化コンポーネントなど、高度な技術が関係するため、機器コストは高くなります。中小企業にとって、この初期コストの高さは、特に導入コストが比較的手頃な従来の溶接方法と比較すると、障壁となる可能性があります。さらに、特殊な機器や適切な安全対策の全体的なセットアップ コストが初期投資に加算されるため、レーザー溶接は、長期的なコスト削減によって初期費用を相殺できる高生産または高価値のアプリケーションに適しています。
限定厚さ溶接
レーザー溶接は、薄い材料から中程度の厚さの材料には非常に効果的ですが、非常に厚い部分の溶接には限界があります。アーク溶接やサブマージアーク溶接などの従来の溶接方法は、より大きな溶接断面をより効率的に構築できるため、非常に厚い材料に適しています。キーホール モードのレーザー溶接では、ある程度の深い溶け込みを実現できますが、数センチメートルを超える厚さの溶接が必要な材料の場合、このプロセスは一般に費用対効果が高くなく、効率的でもありません。その結果、レーザー溶接は通常、より薄い材料に高精度が求められる用途に限定されます。
関節フィットアップに対する感受性
レーザー溶接では、接合する部品間の正確な位置合わせとフィットアップが必要です。接合部に隙間や位置ずれがあると、集中したレーザーエネルギーが従来のフィラーベースの溶接プロセスのように隙間を適切に埋めることができないため、溶接品質が低下したり、融合が不完全になったりする可能性があります。この敏感さは、材料を慎重に準備する必要があることを意味し、多くの場合、しっかりとフィットするように高精度の機械加工やクランプが必要になります。材料や部品にばらつきがある場合、必要な接合品質を達成するために徹底的な準備を行わない限り、レーザー溶接は最適な選択ではない可能性があります。
安全性の懸念
高出力レーザー システムの操作には、レーザー照射による目や皮膚の損傷、火傷、火災の危険など、安全上のリスクが伴います。レーザーから放出される強烈な光は、レーザー保護眼鏡などの適切な保護手段を講じないと、目に回復不可能な損傷を引き起こす可能性があります。反射面はレーザー光線の迷走のリスクも高め、オペレーターや他の機器に危険をもたらします。さらに、有害な煙の漏れを防ぎ、反射を制御するために、特殊なレーザー エンクロージャと換気装置が必要になることが多く、レーザー溶接システムの安全要件とコストがさらに高まります。
反射率の問題
銅やアルミニウムなどの反射率の高い材料は、レーザー溶接に問題を引き起こす可能性があります。レーザーがこれらの材料に当たると、エネルギーの大部分が吸収されるのではなく反射されるため、溶接の効率と効果が低下します。この反射率により、迷光反射が発生し、システム内のレーザー光学系やその他の敏感なコンポーネントが損傷する可能性もあります。特定のレーザー タイプと波長調整により、反射率の問題をある程度軽減できますが、反射性材料を溶接するには、レーザー吸収を高めるために、表面の前処理や特殊コーティングなどの追加の調整が必要です。
技術的な複雑さ
レーザー溶接装置は、従来の溶接設備の多くよりも技術的に複雑です。この複雑さにより、トラブルシューティングやメンテナンスがさらに困難になる可能性があります。システムには、専門知識を必要とする繊細な光学系、高精度のコンポーネント、冷却システムが含まれるためです。アライメント、ビーム品質、または電力安定性に関する問題は、溶接品質に影響を与える可能性があり、修理にはレーザーメンテナンスの訓練を受けた熟練した技術者が必要になる場合があります。技術的に複雑なため、スペアパーツやサポートの入手が困難で費用もかかる可能性があり、問題が発生した場合のダウンタイムが長くなる可能性があります。
機器の感度
レーザー溶接システム、特に高精度の光学系と制御機構を備えたシステムは、ほこり、振動、温度変動などの環境要因に敏感です。ビーム品質を維持し、正確な溶接を確実に行うには、システム内の光学系を清潔に保ち、正確に調整する必要があります。レンズやミラーが汚れていると、ビームが歪んで溶接品質が低下したり、システムが損傷したりする可能性があります。さらに、レーザー機器を最適に動作させるには、通常、安定した環境条件が必要であり、制御された作業環境と定期的な清掃ルーチンへの追加投資が必要になる場合があります。
限定されたフィールド使用
レーザー溶接は管理された環境では非常に効果的ですが、現場作業や屋外での用途には適していません。不安定な足場、温度の変動、直射日光などの要因は、レーザーの精度や溶接の品質に影響を与える可能性があります。さらに、レーザー機器は感度が高く、高出力を必要とするため、安定した電源と管理された環境を必要とするため、運搬が困難になることがあります。建設や大規模な構造物の溶接など、携帯性と現場での即応性が重要な用途では、アーク溶接や MIG 溶接などの従来の溶接技術の方が一般的に実用的です。
熟練したオペレーターが必要
レーザー溶接システムでは、設定を管理および最適化し、適切な位置合わせを保証し、安全プロトコルを維持するために、高度なスキルを持つオペレーターが必要です。レーザー溶接機を操作するには、レーザー パラメータを理解し、ビームの焦点を調整し、機器の状態を監視して、一貫した溶接品質を確保する必要があります。レーザーの操作とメンテナンスのトレーニングは必須です。小さなミスでも溶接が損なわれたり、機器が損傷したりする可能性があるためです。この専門的なスキルの必要性は、人件費を増大させるだけでなく、特にレーザー溶接の専門知識が不足している地域では、有能な人材の確保を制限する可能性があります。
レーザー溶接のこうした制限により、製造業者は、この技術が自社の特定のニーズやリソースに適合しているかどうかを慎重に評価することが不可欠になります。この技術は精密製造に大きなメリットをもたらしますが、その欠点により、特にコスト重視の用途や現場での用途では、レーザー溶接が最適な選択肢ではない可能性がある領域が浮き彫りになります。
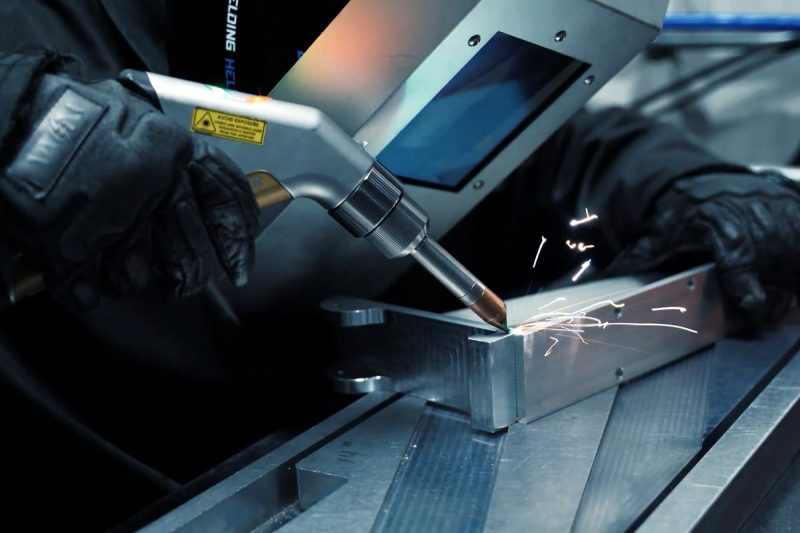
レーザー溶接の用途
レーザー溶接は、接合プロセスにおいて高い精度、品質、効率が求められる業界で広く採用されています。
自動車産業
自動車業界は、そのスピード、精度、大量生産への適性から、レーザー溶接を最も早く導入した業界の 1 つです。レーザー溶接は、構造部品から複雑な電子部品まで、さまざまな自動車部品の接合に使用されます。特に、レーザー溶接では、異なる金属または金属の厚さを接合して軽量でありながら強度のある部品を作成するテーラード ブランクを作成できます。これにより、メーカーは材料の使用を最適化し、燃費と車両の安全性を向上させることができます。
自動車分野での応用:
- ボディパネルとテーラードブランク。
- トランスミッション部品を含むエンジン部品。
- エアバッグケースには精度と信頼性が求められます。
- 排気システムには、高温と高圧に耐えられる溶接が必要です。
航空宇宙産業
航空宇宙産業では、強度、重量、精度に関して厳格な基準が定められているため、レーザー溶接は理想的なソリューションとなっています。この業界では、従来の方法では溶接が難しいことが多いチタンや特殊合金などの高強度軽量金属の接合にレーザー溶接を利用しています。熱による歪みを最小限に抑えるレーザー溶接の能力は、わずかな偏差でも性能や安全性に影響する可能性がある航空宇宙用途で特に有益です。
航空宇宙分野での応用:
- 燃料システムと油圧ラインには漏れのない溶接が必要です。
- 胴体部品や着陸装置などの構造部品。
- 強度と耐熱性が重要となるタービンブレードやその他のエンジン部品。
- 航空宇宙電子機器では、長期的な信頼性を確保するために、正確できれいな溶接が必要です。
医療機器製造
医療機器業界では、溶接にわずかな欠陥があっても安全性が損なわれたり、汚染につながったりする可能性があるため、精度と清潔さが最も重要です。レーザー溶接は、小さくて繊細な部品に変形を起こさずにマイクロ溶接を施すことができます。特に、外科用器具やインプラントに使用されるステンレス鋼やチタンなどの生体適合性材料の溶接に有効です。
医療機器製造におけるアプリケーション:
- 耐腐食性と清潔さが不可欠な外科用器具。
- ペースメーカーのケースや整形外科用デバイスなどの医療用インプラントには、生体適合性のある気密溶接が必要です。
- カテーテルや内視鏡では、小さな部品に細かく精密な溶接を施す必要があります。
- 医療機器のバッテリーエンクロージャでは、長期使用には溶接の完全性が非常に重要です。
エレクトロニクス産業
電子産業は、レーザー溶接の精度と、熱の影響を最小限に抑えて小型で熱に弱い部品を接合する能力の恩恵を受けています。この分野では、レーザー溶接は寸法安定性と汚染物質のない状態を維持する必要がある部品によく使用され、マイクロエレクトロニクスから大型の筐体まであらゆるものの製造に最適です。レーザー溶接の非接触性は、敏感な電子部品への機械的ストレスを回避するため、特に有利です。
エレクトロニクスにおけるアプリケーション:
- 回路基板の接続では、近くのコンポーネントを損傷することなく、細かく正確な溶接を実現します。
- センサーハウジングとバッテリー接続には、強力で耐久性のあるジョイントが必要です。
- 敏感な電子部品を環境要因から確実に保護する筐体。
- 精度と清潔さが極めて重要な半導体製造におけるマイクロ溶接。
ジュエリー業界
レーザー溶接はジュエリー業界では欠かせないツールとなり、宝石職人はレーザー溶接によって複雑なデザインを作ったり、繊細な作品を修復したり、損傷のリスクを最小限に抑えながら貴金属を接合したりできるようになりました。レーザー ビームを制御することで、宝石に影響を及ぼすことなく宝石の近くで溶接することができ、高いレベルのディテールが求められる小さな部品の加工に適しています。レーザー溶接の精度と最小限の熱入力により、大規模な後処理の必要性が減り、最終製品の品質と外観が維持されます。
ジュエリーへの応用:
- リングのサイズ調整や壊れたチェーンの修理など、既存のジュエリーの修理。
- 熱によるダメージを与えることなく、宝石の近くを安全に溶接できる石のセッティング。
- 詳細かつ繊細な溶接が求められる、カスタムジュエリーデザインの複雑な金属細工。
- 金とプラチナを接合するなど、きれいで目に見えない溶接継ぎ目を使用して、混合金属のデザインを作成します。
エネルギー部門
エネルギー分野、特に再生可能エネルギーでは、発電と貯蔵用の信頼性が高く長持ちする部品を作成するために、レーザー溶接への依存度が高まっています。これには、環境ストレスに耐え、長期間にわたって一貫したパフォーマンスを提供する必要があるソーラーパネル、バッテリー、燃料電池の部品が含まれます。石油およびガス業界では、過酷な条件に耐えるために不可欠な、配管と圧力容器の高強度ジョイントを作成するためにレーザー溶接も使用されています。
エネルギー分野における応用:
- バッテリー製造では、レーザー溶接によりセルと端子間の耐久性のある接続が作成されます。
- 燃料電池と太陽電池パネルのコンポーネントは、きれいで正確な溶接の恩恵を受けます。
- 高圧下での安全確保のために高強度溶接が不可欠な石油・ガス配管。
- 構造部品を含む風力タービンのコンポーネントは、天候への暴露や機械的ストレスに耐える必要があります。
レーザー溶接は、その適応性、精度、クリーンな処理により、これらの業界全体で貴重なツールとなり、厳しい性能基準を満たす高品質の溶接を製造業者に提供します。この技術により、製造業者は耐久性と信頼性だけでなく、効率的で見た目も美しい製品を作ることができ、現代の製造業における重要なツールとしてのレーザー溶接の地位を強化します。
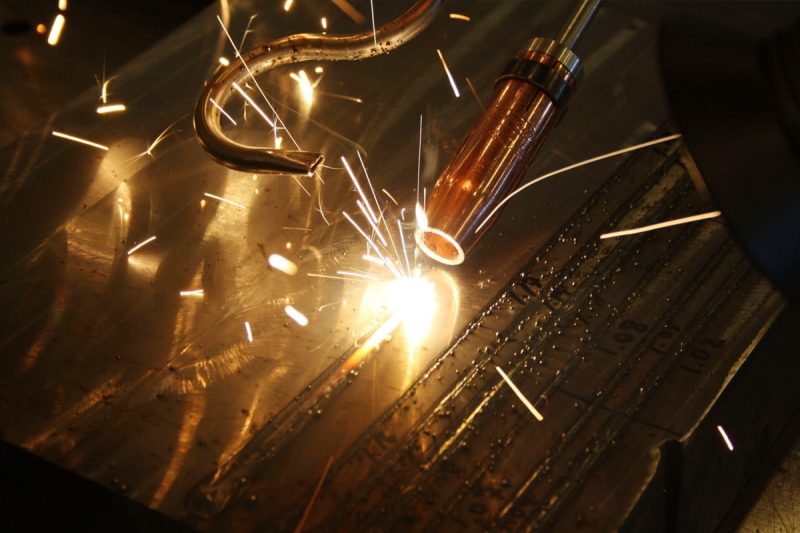
従来の溶接方法との比較
溶接方法を選択する際には、レーザー溶接が TIG、MIG、電子ビーム溶接などの従来の技術とどのように比較されるかを理解することが重要です。各方法には長所と限界があり、最適な選択は材料の種類、精度要件、生産環境などの要因によって異なります。
レーザー溶接とTIG溶接
- タングステン不活性ガス (TIG) 溶接は、アルミニウム、ステンレス鋼、銅など、さまざまな金属に高品質できれいな溶接を施すことで知られています。TIG 溶接では、タングステン電極を使用して電極とワークピースの間にアークを発生させ、金属を溶かします。多くの場合、フィラー材料が必要になります。
- 精度と正確性: レーザー溶接と TIG 溶接はどちらも高精度ですが、レーザー溶接はビームを集中させるため、熱影響部 (HAZ) を最小限に抑えた非常に狭い溶接部を作成できるという利点があります。TIG 溶接は手動制御が必要で速度も遅いため、繊細な部品の小さくて複雑な溶接には適していません。
- 熱入力と歪み: レーザー溶接はエネルギー入力が集中するため、TIG 溶接に比べて HAZ がはるかに小さくなります。これにより熱歪みのリスクが軽減されます。これは、薄い材料や熱に敏感な用途では特に重要です。TIG 溶接は制御されているものの、より広い領域に熱が拡散するため、薄い材料では反りが生じる可能性があります。
- 速度: レーザー溶接は TIG 溶接よりも大幅に高速であるため、大量生産に適しています。TIG 溶接は高品質の結果を生み出すことができますが、手動操作と精度が求められるため速度が遅く、小規模なプロジェクトや修理に適しています。
- 用途: TIG 溶接は、航空宇宙や自動車部品などの小規模で精密なプロジェクトでよく使用されますが、一般的に速度と自動化の互換性が制限されます。レーザー溶接は、電子機器、医療機器、大量の自動車部品など、速度と精度の両方を必要とするアプリケーションに最適です。
レーザー溶接とMIG溶接
- 金属不活性ガス (MIG) 溶接は、厚い材料を接合するために使用される一般的な溶接方法であり、特に速度と生産量が優先される用途で使用されます。MIG 溶接では、連続的に供給されるワイヤ電極が溶けて溶接部を形成するため、溶接領域が広くなることが多く、スパッタを除去する後処理が必要になります。
- 溶け込みと溶接幅: レーザー溶接は、厚い材料でも、充填材を必要とせずに、狭い溶接ビードで深い溶け込みを実現できます。MIG 溶接では、幅が広く精度の低い溶接が行われるため、追加の洗浄と仕上げが必要になることがよくあります。強度が高く狭い溶接が必要な用途には、レーザー溶接の方が適しています。
- 熱影響部: MIG 溶接はレーザー溶接よりも多くの熱を発生するため、HAZ が大きくなり、熱変形のリスクが高まります。レーザー溶接の集中した熱によって HAZ が軽減され、周囲の材料の機械的特性が維持され、特に薄い材料や熱に弱い材料の場合、溶接後の変形が最小限に抑えられます。
- 自動化と生産速度: レーザー溶接は自動化との互換性が高く、はるかに高速で動作できるため、大量生産環境に最適です。MIG 溶接は TIG 溶接よりも高速ですが、ワイヤ供給とシールド ガスが必要なため、通常は手動または半自動プロセスに適しています。
- 材料: MIG 溶接は、厚い材料や、鋼やアルミニウムなどの一般的な金属には効果的ですが、精度と低入熱が求められる異種材料や非常に薄い材料の接合には不向きです。レーザー溶接は、エネルギーを正確に制御できるため、銅とステンレス鋼など、薄い金属と異種金属の接合に優れています。
レーザー溶接と電子ビーム溶接
- 電子ビーム (EB) 溶接は、深く精密な溶接を行うことができる点でレーザー溶接に似た高エネルギー溶接プロセスです。EB 溶接は、真空中で集束した電子ビームを使用して材料を接合するため、非常に深い浸透と制御された環境を必要とする厳しい用途に適しています。
- 環境とセットアップ: 大気中で操作できるレーザー溶接とは異なり、EB 溶接では電子ビームを維持するために真空チャンバーが必要です。この真空セットアップにより、EB 溶接は、クリーン ルームや半自動生産ラインなど、より幅広い環境で使用できるレーザー溶接よりも複雑でコストがかかり、柔軟性が低くなります。
- 溶け込み深さと強度: EB 溶接はレーザー溶接よりも深い溶け込みを実現できるため、厚い材料や非常に強い溶接を必要とする構造用途に最適です。ただし、中程度の厚さから薄い材料の場合、レーザー溶接の方が効率的で実装が簡単な場合が多くあります。
- 速度と自動化: レーザー溶接は高速化が可能で、自動化された生産ラインに簡単に統合できるため、大量生産に適しています。EB 溶接は効果的ですが、真空チャンバーの要件により、一般的に速度が遅く、自動化されたペースの速い生産環境には適応しにくいです。
- コストとメンテナンス: EB 溶接システムはコストが高く、特に真空システムでは専門的なメンテナンスが必要です。レーザー溶接はメンテナンスの必要性が低いため、通常の製造ではより利用しやすく、コスト効率に優れています。さらに、EB 溶接のセットアップ時間とメンテナンスにより、レーザー溶接に比べてダウンタイムが長くなる可能性があります。
比較
- 精密できれいな溶接: レーザー溶接は、精度の点では MIG 溶接や TIG 溶接を上回り、きれいで正確な結果では EB 溶接と競合します。
- 速度: レーザー溶接は TIG 溶接や MIG 溶接よりも高速であり、特に精度が求められる自動化された高速生産に適しています。
- 環境: レーザー溶接は空気ベースの環境で柔軟に使用できるため、真空を必要とする EB 溶接よりも汎用性に優れています。
- 熱影響部: レーザー溶接の HAZ は最小限であるため、薄くて熱に敏感な材料に最適であり、この点では TIG 溶接や MIG 溶接よりも優れています。
- コストと複雑さ: レーザー溶接は初期コストは高いですが、より複雑な設備とメンテナンスが必要となる EB 溶接に比べてメンテナンスと運用のコストが低くなります。
これらの溶接方法にはそれぞれ特定の長所があり、選択は材料、用途要件、生産環境によって異なります。レーザー溶接は、精度、速度、適応性において明確な利点があり、品質と効率を優先する業界にとって最適な選択肢となっています。
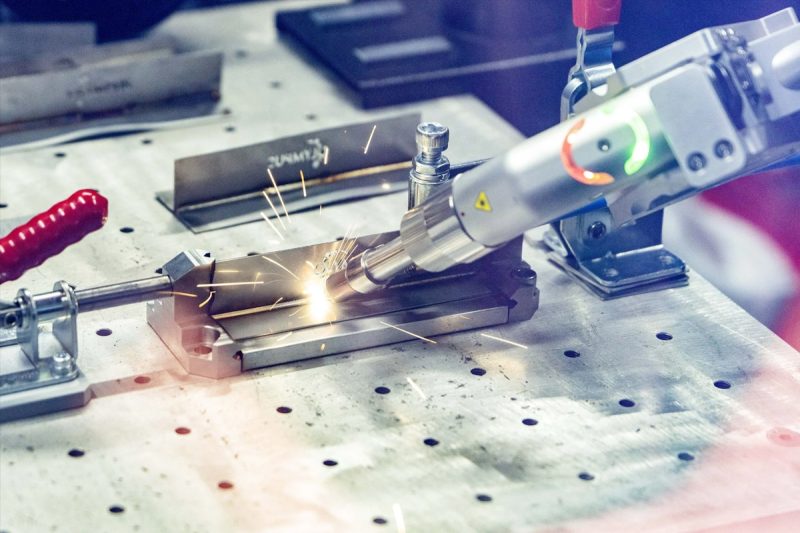
レーザー溶接品質に影響を与える要因
レーザー溶接を使用する場合、いくつかの重要な要素が溶接の品質に影響します。これらの要素を理解することで、メーカーは溶接プロセスを最適化し、強力で正確な接合部を実現できます。
レーザーパラメータ
レーザー自体の設定と特性は、溶接の品質を決定する上で重要な役割を果たします。主要なレーザー パラメータには、出力、焦点スポット サイズ、溶接速度、パルス周波数 (パルス レーザーの場合) などがあります。
- レーザー出力: 出力が高いほど浸透深度が深くなり、溶接が速くなりますが、適切に制御しないと過熱が発生する可能性があります。出力が高すぎると飛び散りや焼けが発生する可能性があり、出力が低すぎると溶接が弱くなったり不完全になったりする可能性があります。
- 溶接速度: レーザーがワークピース上を移動する速度は、溶接品質に影響します。溶接速度が速いと、熱入力が減り、熱影響部 (HAZ) が最小限に抑えられ、歪みが減ります。ただし、速度が速すぎると、材料が完全に融合されず、接合部が弱くなる可能性があります。速度が遅いと、より深く溶け込むことができますが、熱の蓄積が増加し、熱歪みが発生する可能性があります。
- 焦点スポット サイズ: 焦点スポット サイズが小さいほど、エネルギーが小さな領域に集中し、細かく狭い溶接が可能になります。焦点スポット サイズはジョイントの幅に合わせる必要があります。大きすぎると、過度の熱や歪みが生じる可能性があります。小さすぎると、厚い材料に十分に浸透しない可能性があります。
- パルス周波数 (パルス レーザー): パルス レーザーを必要とするアプリケーションでは、パルス周波数を調整することで、溶接部に供給されるエネルギーの量を制御することができます。パルス周波数を高くすると、より滑らかで連続的な溶接が可能になります。一方、周波数を低くすると、断続的なエネルギー バーストが実現し、最小限の熱入力を必要とするアプリケーションに役立ちます。
材料特性
溶接される材料は、レーザーが表面と相互作用し、金属を貫通する方法に影響を与えます。反射率、熱伝導率、合金組成などの要因はすべて溶接の品質に影響します。
- 反射率: アルミニウムや銅などの反射率の高い材料は、レーザーのエネルギーの大部分を反射し、吸収を低下させます。レーザーの波長を低くしたり、反射性材料を前処理したりすると、吸収を高めて溶接品質を向上させることができます。
- 熱伝導率: 銅などの熱伝導率の高い材料は熱を素早く放散するため、適切な浸透を得るにはレーザー出力を高くするか、パラメータを調整する必要があります。チタンなどの熱伝導率の低い材料は熱を保持するため、少ない出力でより深い溶接が可能になります。
- 合金の組成: 合金は融点が異なる場合が多く、一貫した溶接を実現するために異なるレーザー設定が必要になることがあります。また、溶接温度で蒸発する可能性のある元素を含む合金は、スパッタが多く発生したり、割れを防ぐために異なるパルス周波数が必要になる場合があります。
- 表面状態: 材料の表面の清潔さと仕上げは、レーザー ビームの吸収度に影響します。酸化物、油、表面の汚染物質は溶接プロセスを妨げ、接合部の強度を低下させる可能性があります。溶接前に洗浄または表面処理を行えば、溶接の一貫性と強度を高めることができます。
ジョイント設計とフィットアップ
ジョイントの設計とフィットアップの品質は、最終的な溶接品質に大きく影響します。適切なジョイント設計とタイトなフィットアップにより、レーザーは隙間やずれなく材料を正確に溶接することができます。
- ジョイント設計: さまざまなジョイント タイプ (突合せジョイント、重ねジョイント、フィレット ジョイントなど) では、最適な結果を得るために特定のレーザー設定と焦点が必要です。たとえば、突合せジョイントではより深い浸透が必要になる場合がありますが、重ねジョイントでは浅くできますが、過度の熱拡散を避けるための制御が必要です。
- フィットアップの精度: 部品間の正確な位置合わせは、一貫した溶接品質に不可欠です。隙間や位置ずれがあると、不完全な融合につながり、溶接に弱い部分ができてしまいます。ぴったりとフィットアップすることで、レーザーエネルギーが接合部全体に効果的に吸収され、欠陥の可能性を最小限に抑えることができます。極めて厳しい許容誤差が求められる用途では、クランプおよび固定システムを使用して、溶接中に部品をしっかりと固定することができます。
- 厚さの適合性: 接合部の厚さも溶接の強度に影響します。厚い材料を溶接する場合、周囲の材料を過熱することなく完全に貫通するようにレーザー パラメータを調整する必要があります。一方、薄い材料の場合は、反りや溶け落ちを防ぐために、出力設定を低くする必要があります。
シールドガス
シールドガスを使用すると、溶接部を汚染や酸化から保護することができ、溶接の品質や外観に影響を及ぼす可能性があります。シールドガスの選択と流れは、高品質の溶接を実現する上で重要な役割を果たします。
- ガスの種類: 一般的なシールド ガスには、アルゴン、ヘリウム、窒素などがあります。アルゴンは安定した雰囲気を提供し、さまざまな金属に広く使用されています。ヘリウムは熱伝導率が高いため、深い浸透によく使用されますが、高価です。窒素はステンレス鋼などの特定の材料に使用されることがありますが、一部の金属では窒化物が発生し、強度に影響を与える可能性があります。
- ガス流量: シールドガスの流量は、材料と溶接パラメータに応じて調整する必要があります。流量が高すぎると、溶接プールが乱れて乱流が発生する可能性があります。一方、流量が低すぎると、溶接部が完全に保護されず、酸化が起こり、変色や多孔性が生じる可能性があります。
- 供給方法: シールド ガスは、レーザー ヘッド近くのノズルから直接供給できますが、場合によっては、より広範囲に供給するために二次ガス ラインを介して供給することもできます。適切なガス供給により、均一な分布が確保され、溶接部が空気にさらされるのを防ぎ、きれいで美しい溶接仕上がりが実現します。
レーザーパラメータ、材料特性、ジョイント設計、シールドガスなどの要素を慎重に管理することで、メーカーはレーザー溶接プロセスを最適化し、品質、強度、信頼性を向上させることができます。各アプリケーションの固有の要件を理解することで、微調整が可能になり、さまざまな業界で一貫した高品質の溶接を実現できます。

まとめ
レーザー溶接は強力で多用途な接合技術であり、精密さが求められる業界に大きなメリットをもたらします。レーザー溶接は、クリーンで正確、かつ深い溶接部を作成できるため、自動車、航空宇宙、医療機器、電子機器、宝飾品などの分野では欠かせないものとなっています。主な利点としては、高速動作、熱変形の最小化、自動化との互換性、複雑な材料や複雑なデザインへの適合性などが挙げられます。ただし、レーザー溶接には、初期コストの高さ、接合部の位置合わせに対する敏感さ、反射性材料の問題など、限界もあります。レーザー システムの技術的な複雑さと潜在的な危険性のため、安全プロトコルと熟練したオペレーターが不可欠です。
TIG、MIG、電子ビーム溶接などの従来の方法と比較すると、レーザー溶接は速度、効率、適応性に優れています。大量生産と特殊用途の両方に適しているため、現代の製造業にとって貴重な資産となっています。その利点と限界を慎重に評価することで、メーカーはレーザー溶接を自社のプロセスに統合し、生産性と品質を最大化するための情報に基づいた決定を下すことができます。
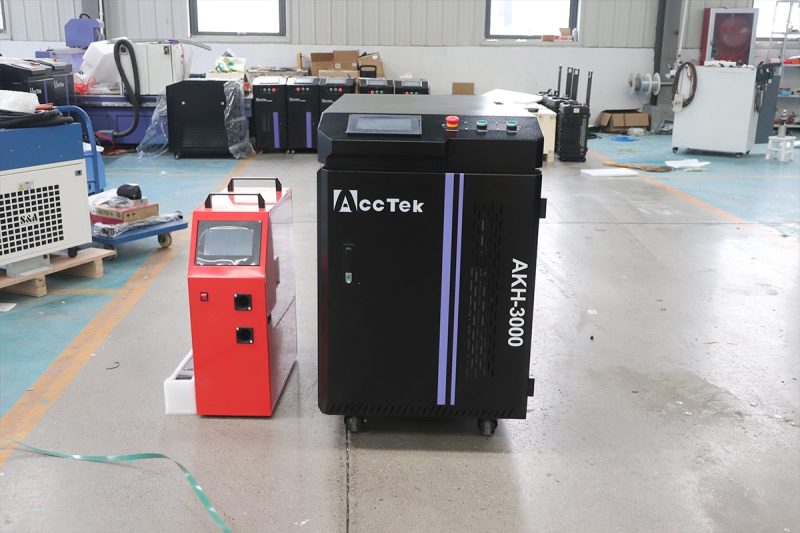
レーザー溶接ソリューションを入手
AccTek Laser は、生産効率、精度、品質の向上を目指す企業向けに、幅広い産業ニーズを満たすように設計された高度なレーザー溶接ソリューションを提供しています。レーザー溶接機の専門メーカーとしての専門知識を持つ AccTek Laser は、自動車、航空宇宙、電子機器、医療機器製造などの産業の需要に合わせたソリューションを提供しています。当社のレーザー溶接システムは、高速動作と精密な制御を組み合わせ、熱影響部を最小限に抑えた深くきれいな溶接を実現します。
AccTek Laser のレーザー溶接機は柔軟性を重視して設計されており、自動化された生産ラインに統合できるため、大量生産と特殊な用途の両方に対応できます。当社では、材料、溶接要件、生産目標に基づいて最適なシステムを選択できるよう、販売前の総合的なコンサルティングを提供しています。AccTek Laser は、堅牢な技術サポートと継続的なメンテナンス サービスにより、お客様の溶接プロセスが最適化され、一貫した品質と効率が確保されるようにします。AccTek Laser をお選びいただくと、最先端のレーザー溶接ソリューションで生産能力を高めることができます。
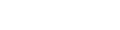
連絡先
- [email protected]
- [email protected]
- +86-19963414011
- No. 3 ゾーン A、Lunzhen 工業地帯、玉城市、山東省。
レーザー ソリューションを入手する