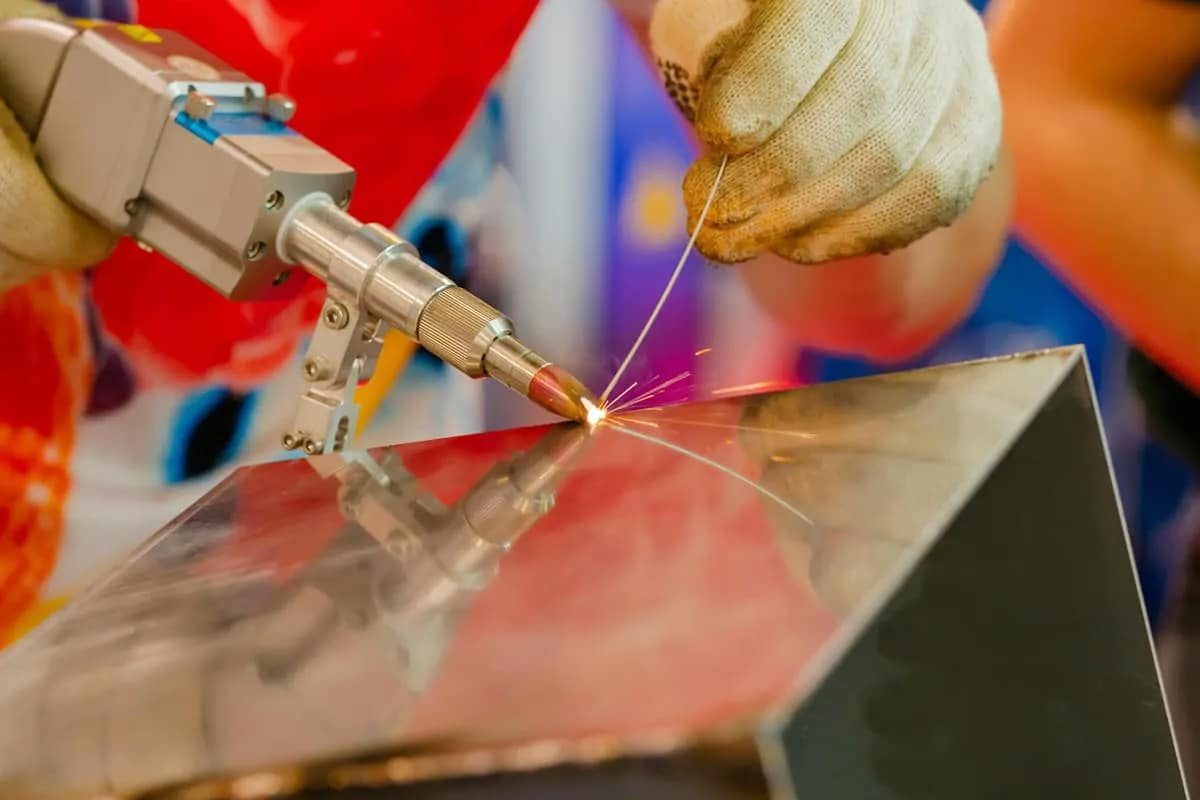
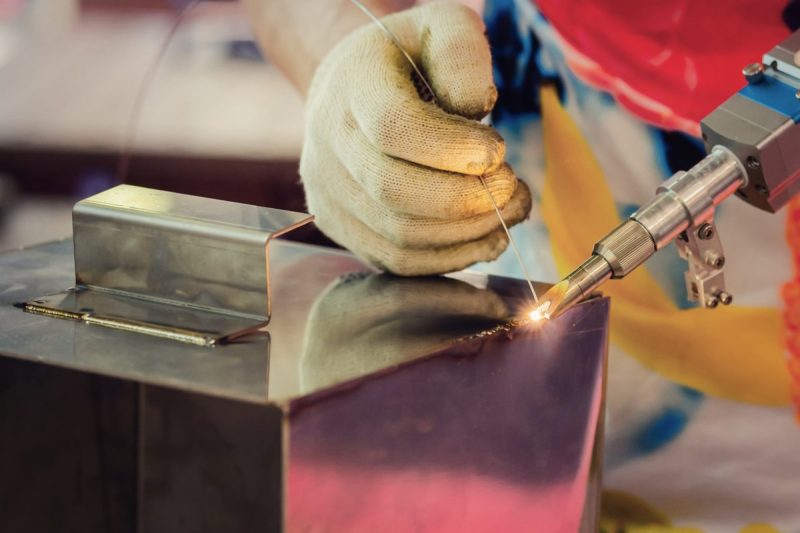
レーザーパラメータ
レーザーパワー
レーザー出力はレーザー溶接の基本的なパラメータであり、溶接領域に供給されるエネルギーの量を決定します。出力設定は溶接速度と浸透深さに影響します。
- 高出力: レーザー出力を高くすると、溶接速度と浸透深さが増し、より厚い材料の溶接が可能になります。これは、深い溶接や高い生産性が求められる用途に特に役立ちます。ただし、出力が高すぎると、過熱、過剰な溶融、スパッタや多孔性などの欠陥が発生する可能性があります。
- 低出力: レーザー出力が低いほど、薄い材料や、マイクロ溶接などの高精度が求められる用途に適しています。ただし、出力が不十分だと、不完全な融合や不十分な浸透により、溶接が弱くなる可能性があります。
- 最適化: 最適なレーザー出力を実現するには、浸透性と速度のニーズと欠陥リスクのバランスを取る必要があります。そのためには、材料の種類、厚さ、特定の溶接要件に基づいた慎重な調整が必要です。
波長
レーザーの波長は、溶接される材料がレーザーエネルギーをどれだけ吸収するかに影響します。材料によって、波長によって吸収特性が異なります。
- 一般的な波長: レーザー溶接で使用される一般的な波長には、赤外線 (IR)、可視光、紫外線 (UV) などがあります。材料や用途に応じて、各波長にはそれぞれ利点があります。
- 赤外線 (IR) レーザー: CO2 レーザーやファイバー レーザーなどの IR レーザーは、金属の溶接によく使用され、赤外線スペクトルの吸収率が高い材料に効果的です。
- 可視光線および紫外線レーザー: これらの波長は非金属や一部の反射性金属に吸収されやすいため、プラスチックやセラミックスを扱う用途に適しています。
- 材料固有の考慮事項: 赤外線領域で反射率の高いアルミニウムや銅などの材料には、これらの金属に吸収されやすい波長のレーザーが必要になる場合があります。特殊なコーティングや特定の波長のレーザー光源を使用すると、吸収と溶接の効率を高めることができます。
パルス持続時間と周波数
パルス持続時間と周波数は、レーザーが連続波ではなく短いパルスで動作するパルスレーザー溶接における重要なパラメータです。
- パルス持続時間: 各レーザー パルスの長さは、溶接の熱特性に大きな影響を与える可能性があります。パルスが短いほど、エネルギーが短時間で集中的に放出され、熱影響部 (HAZ) が最小限に抑えられ、熱変形が減少します。パルス持続時間が長いほど、エネルギーは多く放出されますが、HAZ が増加し、熱による損傷のリスクが高まります。
- パルス周波数: パルスの周波数、つまり 1 秒あたりのパルス数は、全体的なエネルギー供給と溶接速度に影響します。周波数が高いほど溶接速度は速くなりますが、累積熱蓄積のリスクも高くなり、欠陥の原因となる可能性があります。
- 最適化: パルス持続時間と周波数の組み合わせは、材料特性と必要な溶接特性に基づいて最適化する必要があります。これらのパラメータを微調整すると、溶接速度、浸透、熱効果のバランスを実現できます。
ビーム品質
レーザービームの品質は、モード構造やビームプロファイルなどのパラメータによって定義され、溶接効率に直接影響します。
- ビーム モード: レーザー ビームのモード (例: TEM00) によって、その強度分布が決まります。高品質のモード構造により、集中した均一なエネルギー供給が保証され、一貫した正確な溶接が実現します。
- ビーム プロファイル: 均一で明確に定義されたビーム プロファイルは、エネルギー損失を最小限に抑え、溶接領域への最大のエネルギー供給を保証します。ビーム品質が悪いと (歪んだプロファイルや不規則なプロファイルを特徴とする)、加熱が不均一になり、溶接欠陥が発生します。
- 実現可能性: ビーム品質が高いため焦点合わせが向上し、高精度と微細なディテールが求められるアプリケーションでレーザーのスポットサイズを小さくすることができます。
焦点位置
材料表面に対するレーザー焦点の位置は、溶接の効率と品質に影響を与える重要なパラメータです。
- 正しい焦点: レーザー ビームを溶接領域に正しく焦点を合わせると、エネルギー密度が最大になり、材料が効率的に溶解されます。最適な焦点位置は、材料の厚さと必要な溶接特性によって異なります。深溶け込み溶接の場合、焦点は通常、材料表面よりわずかに下に設定されます。
- 焦点距離: レーザー光学系の焦点距離によって、焦点深度と焦点サイズが決まります。焦点距離が短いと、スポット サイズが小さくなり、エネルギー密度が高くなるため、細かい溶接作業に適しています。焦点距離が長いと、焦点深度が大きくなり、厚い材料の溶接に適しています。
- 焦点許容度: 一貫した焦点位置を維持すると、均一な溶接品質を実現できます。焦点位置が変化すると、不均一な浸透、不完全な融合、欠陥が発生する可能性があります。リアルタイムの焦点調整機能を備えた自動化システムは、溶接プロセス中に最適な焦点を維持するのに役立ちます。
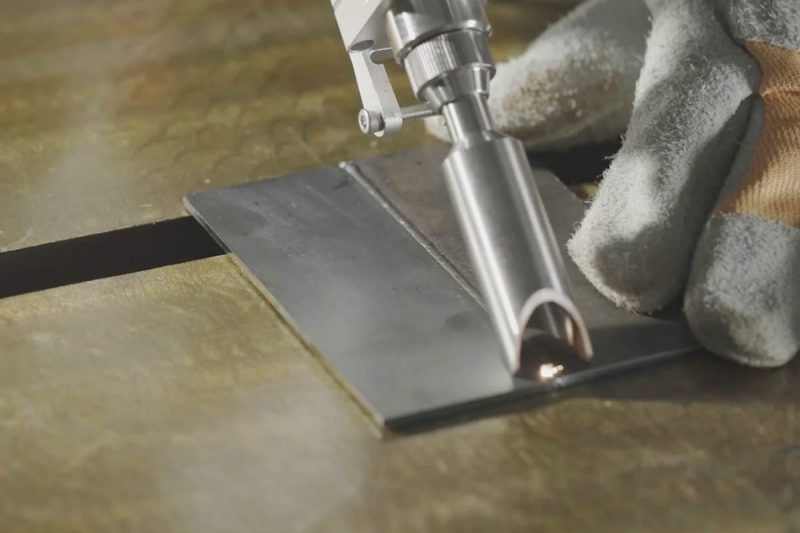
材料特性
材料の種類
溶接される材料の種類は、レーザー溶接の効率を決定する主な要因です。材料によってレーザーエネルギーの吸収と伝導の仕方が異なり、溶接の品質とプロセスパラメータに影響します。
- 金属: 一般的に溶接される金属には、鋼、アルミニウム、チタン、銅などがあります。各金属にはそれぞれ異なる特性があります。
- 鋼: レーザーエネルギーの吸収率が高いため、一般的にレーザーでうまく溶接できます。炭素鋼、ステンレス鋼、合金鋼など、鋼のグレードによって、必要なレーザー設定が異なる場合があります。
- アルミニウム: アルミニウムは反射率と熱伝導率が高いことで知られており、レーザーでアルミニウムを溶接するのは難しい場合があります。特殊な波長やコーティングにより吸収率を向上させることができます。
- チタン: チタンは適度な反射率と熱特性を備えているため、レーザーで効果的に溶接できます。航空宇宙や医療の分野で広く使用されています。
- 銅: 銅は反射率と熱伝導率が高いため、従来のレーザー設定では溶接が困難です。効率を向上させるために、特定の波長のファイバー レーザーがよく使用されます。
- 非金属: プラスチック、セラミック、複合材などの材料もレーザー溶接できます。効率的な溶接には、それぞれの非金属に固有のレーザー パラメータが必要です。
- プラスチック: プラスチックは一般にレーザー エネルギーをよく吸収しますが、その熱特性により、燃焼や溶解を防ぐために溶接パラメータを慎重に制御する必要があります。
- セラミック: セラミックは脆く、熱応力によって割れることがあります。セラミックのレーザー溶接では、通常、予熱と特定の波長のレーザーを使用して応力を軽減する必要があります。
- 複合材料: 複合材料はさまざまな材料を組み合わせたもので、さまざまなコンポーネントにわたって均一な溶接品質を確保するためにパラメータを慎重に調整する必要があります。
厚さ
材料の厚さは、レーザー溶接の効率に影響を与える重要な要素です。必要なレーザー出力、溶接速度、全体的なプロセス安定性に影響します。
- 薄い材料: 薄い材料の場合、溶け落ちや過剰な熱入力を防ぐために、レーザー出力を低くし、溶接速度を高くする必要があります。レーザー パラメータを正確に制御することで、きれいで欠陥のない溶接が可能になります。
- 厚い材料: 厚い材料を溶接するには、十分な浸透と融合を確保するために、より高いレーザー出力とより遅い溶接速度が必要です。完全な浸透を実現するために、マルチパス溶接やハイブリッド溶接 (レーザー溶接とアーク溶接の組み合わせ) などの高度な技術を使用できます。
- 遷移領域: 異なる厚さの材料を溶接する場合、熱の吸収と伝導の違いに対応するためにレーザーパラメータを動的に調整する必要があります。
表面状態
材料の表面状態は、レーザーの吸収、熱伝達、および全体的な溶接品質に影響を与える可能性があります。適切な表面処理は、効率的なレーザー溶接の実現に役立ちます。
- 清潔さ: 油、グリース、汚れ、酸化層などの汚染物質はレーザーの吸収を妨げ、溶接に欠陥を引き起こす可能性があります。最適な結果を得るには、溶接前に表面を徹底的に洗浄する必要があります。
- 表面粗さ: 材料の表面粗さは、レーザー ビームの相互作用に影響する可能性があります。一般的に、表面が滑らかであれば、レーザーの吸収が良くなり、溶接の一貫性が高まります。研磨やグリット ブラストなどの表面処理を使用して、表面状態を改善できます。
- コーティングと処理: 一部の材料には、レーザー溶接に影響を与えるコーティングや処理が施されている場合があります。たとえば、亜鉛メッキ鋼には亜鉛コーティングが施されており、蒸発や多孔性を防ぐために特定のレーザー設定が必要です。これらのコーティングの効果を理解することで、溶接パラメータを適切に調整できます。
熱特性
熱伝導率、比熱容量、融点などの材料の熱特性は、材料がレーザー エネルギーとどのように相互作用するかに影響します。
- 熱伝導率: 銅やアルミニウムなどの熱伝導率の高い材料は熱を素早く放散するため、適切な融合を実現するにはより高いレーザー出力が必要です。ステンレス鋼などの熱伝導率の低い材料は熱を長く保持するため、過剰な溶融を避けるために熱入力を慎重に制御する必要があります。
- 比熱容量: 材料の比熱容量によって、温度を上げるために必要なエネルギーの量が決まります。比熱容量の高い材料は溶接に多くのエネルギーを必要とするため、レーザー出力と溶接速度の選択に影響します。
- 融点: 材料の融点によって、溶融と融合を開始するために必要なエネルギーの量が決まります。チタンや特定の合金などの高融点材料では、効率的な溶接を実現するために、より高いレーザー出力と溶接パラメータの正確な制御が必要です。
冶金特性
材料の組成、微細構造、相転移などの冶金特性は、レーザー溶接プロセスにおいて重要な役割を果たします。
- 組成: 材料の化学組成は溶接性に影響します。合金元素は、材料のレーザーエネルギーの吸収、溶融挙動、および亀裂や多孔性などの欠陥に対する感受性に影響します。組成を理解することは、適切なレーザーパラメータとシールドガスを選択するのに役立ちます。
- 微細構造: 材料の微細構造は、結晶粒度や相分布など、その機械的特性や溶接に対する反応に影響します。一般に、細粒の材料は粗粒の材料よりも溶接性に優れていますが、粗粒の材料では、ひび割れや変形を防ぐために特別な注意が必要になる場合があります。
- 相変態: 一部の材料は溶接中に相変態を起こし、最終的な溶接特性に影響を与える可能性があります。たとえば、一部の鋼は冷却時にオーステナイトからマルテンサイトに変態し、硬くて脆い溶接部になります。冷却速度と溶接後の熱処理を制御することで、これらの変態を制御し、溶接品質を向上させることができます。
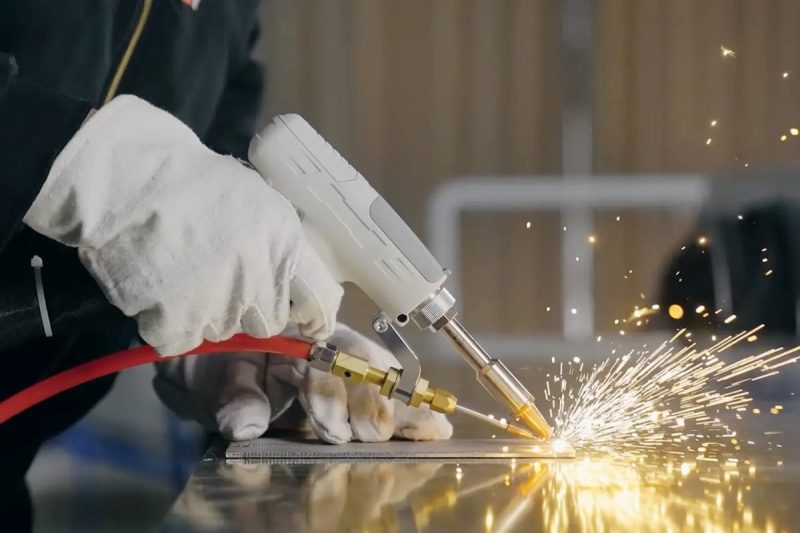
ジョイントデザイン
ジョイント構成
ジョイントの構成はレーザー溶接プロセスに大きな影響を与えます。ジョイントの種類によって、アクセス性、溶接のしやすさ、機械的強度が異なります。
- 突合せ接合: 突合せ接合では、2 つの材料が端と端を合わせて配置されます。この構成はシンプルで深い溶け込みを可能にするため、レーザー溶接では一般的です。ただし、正確な位置合わせと最小限の隙間によってのみ、高品質の溶接が保証されます。
- 重ね継ぎ: 重ね継ぎでは、1 つの材料が別の材料と重なります。この構成は薄い材料を溶接するのによく使用され、組み立ても簡単です。ただし、過度の溶融を避け、2 つの層が適切に融合されるように、レーザー パラメータを慎重に制御する必要があります。
- T ジョイント: T ジョイントは、1 つの材料を別の材料に対して垂直に溶接することによって形成されます。この構成は、構造用途でよく使用されます。T ジョイントの課題は、均一な溶け込みを実現し、交差部分の欠陥を回避することです。
- コーナー ジョイント: コーナー ジョイントは、2 つの材料を直角に接合するために使用されます。箱型の構造やフレームでよく使用されます。コーナーでの適切な融合を確実にするには、レーザー パラメータとジョイントの準備を正確に制御する必要があります。
- エッジ ジョイント: エッジ ジョイントでは、材料の片方または両方の端に沿って溶接を行います。この構成は、薄い材料や、重なりが最小限で済むアプリケーションに適しています。エッジ ジョイントで一貫した溶接を実現するには、正確な位置合わせとギャップ制御が必要です。
関節の準備
適切な接合部の準備は、高品質の溶接の実現に役立ちます。接合面の状態は、レーザーの吸収、熱伝達、および全体的な溶接の完全性に直接影響します。
- 清潔さ: 接合面には、油、グリース、汚れ、酸化物などの汚染物質が付着していない必要があります。汚染物質はレーザーの吸収を妨げ、多孔性や不完全な融合などの欠陥を引き起こす可能性があります。材料や存在する汚染物質に応じて、脱脂、ワイヤー ブラッシング、化学洗浄などの洗浄方法を使用できます。
- 表面処理: サンドブラスト、研磨、機械加工などの表面処理により、表面状態を改善し、レーザー吸収を高めることができます。これらの処理により、滑らかで均一な表面が作られ、欠陥のリスクが軽減されます。
- エッジの準備: 適切なエッジの準備により、良好なフィットが保証され、隙間が最小限に抑えられます。ベベル、面取り、エッジの丸めなどのテクニックにより、ジョイントのフィット感が向上し、より良好な融合が促進されます。
ギャップ許容度
隙間の許容範囲を狭く保つことで、一貫した高品質のレーザー溶接を実現できます。接合面の間に隙間があると、不完全な融合、溶接の弱化、欠陥が生じる可能性があります。
- 最小ギャップ: 理想的には、完全な融合と強力な溶接を確保するために、接合面のギャップは最小限に抑える必要があります。小さなギャップは溶融材料で埋めることができますが、ギャップが大きすぎると、融合が不完全になり、接合部が弱くなります。
- 許容公差: 許容ギャップ公差は、材料、ジョイント構成、溶接パラメータによって異なります。一般に、高精度のアプリケーションや薄い材料ではより厳しい公差が求められますが、厚い材料では若干大きいギャップを許容できます。
- 調整: 隙間がある場合は、レーザー出力、溶接速度、焦点位置を調整することで、隙間を補正し、適切な融合を確保できます。ただし、隙間が大きすぎると溶接の品質と強度に影響する可能性があるため、避けてください。
固定具とクランプ
効果的な固定具とクランプ装置は、レーザー溶接プロセス中の接合部の安定性と位置合わせを保証します。適切な固定具とクランプ装置は、動き、変形、位置ずれを防ぎ、溶接の効率と品質を向上させます。
- 安定性: 溶接プロセス中に材料が動かないように、固定具で材料をしっかりと固定する必要があります。わずかな動きでも、位置ずれ、欠陥、溶接品質の変化が生じる可能性があります。
- 位置合わせ: クランプ システムでは、接合面が正確に位置合わせされていることを確認する必要があります。位置合わせがずれていると、融合が不十分になり、溶接が弱くなる可能性があります。調整可能な固定具と精密クランプ ツールを使用すると、正確な位置合わせを実現できます。
- 熱管理: 固定具とクランプは、溶接プロセス中に発生する熱も管理する必要があります。過度の熱は接合部の変形や移動の原因となります。固定具に熱伝導率の高い材料を使用したり、冷却システムを統合したりすると、熱を管理して安定性を維持するのに役立ちます。
- アクセス性: 固定具とクランプ システムの設計により、レーザー ビームが溶接領域に容易に到達できる必要があります。複雑な形状と狭いスペースでは、適切なレーザー アクセスと最適な溶接条件を確保するために、カスタム固定具が必要です。
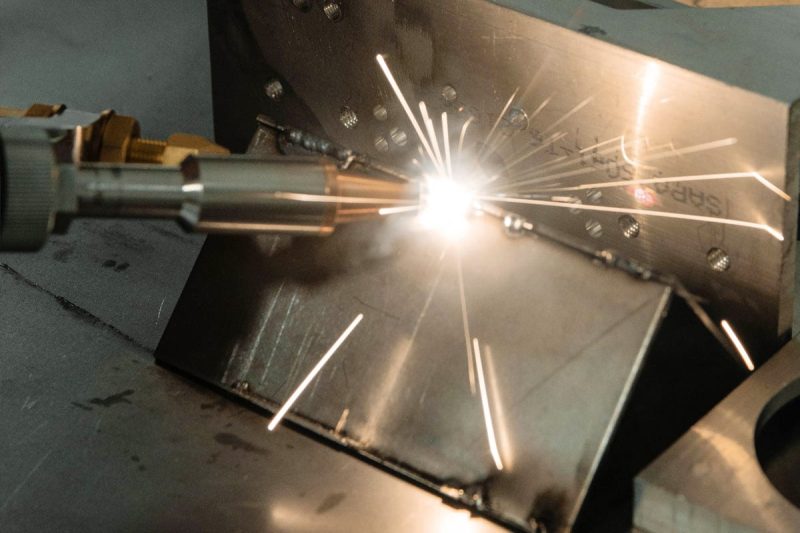
環境条件
周囲温度
周囲温度は、レーザー溶接プロセスにさまざまな影響を与える可能性があります。制御された温度環境を維持することで、一貫した溶接品質が確保され、機器の問題を防ぐことができます。
- 一貫した溶接性能: 極端な温度 (高すぎる、または低すぎる) は、溶接される材料の熱特性に影響を及ぼす可能性があります。周囲温度が高いと、熱入力が過剰になり、熱変形が増加する可能性があります。一方、温度が低いと、急速な冷却とひび割れが発生する可能性があります。
- 装置の安定性: レーザー光源や冷却システムを含むレーザー溶接装置は、特定の温度範囲内で最もよく動作します。
- 高温: 過度の熱は溶接材料の熱膨張を引き起こし、位置ずれや変形につながります。また、溶接部の冷却速度にも影響を及ぼし、接合部の微細構造や機械的特性にも影響を及ぼします。
- 低温: 極端に低温の環境では、レーザー光学系と材料表面に結露が発生し、レーザー吸収が妨げられ、欠陥が発生する可能性があります。低温は、材料の熱伝導率と溶融挙動にも影響を与える可能性があります。
- 制御手段: 溶接環境に気候制御システムを実装すると、安定した周囲温度を維持できます。これにより、材料の挙動と機器のパフォーマンスの一貫性が確保され、より効率的で信頼性の高い溶接プロセスが実現します。
湿度
溶接環境の湿度レベルは、レーザー機器と溶接される材料の両方に影響を及ぼす可能性があります。
- 結露: 湿度が高いと、レーザー光学系と材料の表面に結露が生じる可能性があります。これによりレーザー ビームが散乱し、強度と精度が低下するほか、溶接部に汚染物質が混入する可能性もあります。
- 酸化と腐食: 酸化と腐食の影響を受けやすい材料は、高湿度の影響を受けます。湿気があると、これらのプロセスが加速され、表面の汚染や溶接欠陥につながる可能性があります。
- 材料の挙動: 一部の材料、特に湿気に敏感な材料は、湿度によって特性が変化することがあります。これは、溶接性や最終的な溶接の品質に影響を及ぼす可能性があります。
- 制御対策: 除湿器を使用し、適切な換気を確保することで、湿度レベルを制御することができます。溶接エリアを乾燥した状態に保ち、湿気を取り除けば、最適な溶接条件を維持できます。
シールドガス
シールドガスを使用すると、溶接領域を大気中の汚染物質から保護し、溶接品質を向上させることで、レーザー溶接を成功させることができます。
- シールドガスの種類: レーザー溶接で使用される一般的なシールドガスには、アルゴン、ヘリウム、窒素、およびこれらのガスの混合物があります。シールドガスの選択は、溶接材料と必要な溶接特性によって異なります。
- アルゴン: アルゴンは不活性であり、酸化や汚染に対する優れた保護機能を備えているため、広く使用されています。鋼鉄、アルミニウム、チタンなど、さまざまな金属の溶接に適しています。
- ヘリウム: ヘリウムは溶接の溶け込みを高め、気孔率を減らすことができるため、深い溶接や銅やアルミニウムなどの高熱伝導率材料に最適です。
- 窒素: 窒素は、一部の材料の溶接品質を向上させるために他のガスと組み合わせて使用されることがよくありますが、一部の金属との反応性がある可能性があるため、注意して使用する必要があります。
- フローおよびカバレッジ: 溶接領域を適切に保護するには、シールド ガスのフローおよびカバレッジを慎重に制御する必要があります。ガスのフローが不十分だと汚染や欠陥が発生する可能性があり、フローが多すぎると乱流や冷却の問題が発生する可能性があります。
- ノズル設計: シールドガス ノズルの設計と配置により、効果的なガスの適用範囲を実現できます。適切なノズル設計により、溶接領域全体にガスが連続して均一に流れるようになり、溶接の品質と効率が向上します。
換気
溶接エリアを適切に換気することで、安全で効率的な溶接環境を維持できます。
- 煙の除去: レーザー溶接では、作業者に有害で溶接プロセスに影響を及ぼす可能性のある煙やガスが発生します。効果的な煙除去システムは、これらの汚染物質を作業エリアから除去し、清潔で安全な環境を確保します。
- 気流制御: 気流を制御すると、煙の蓄積を防ぎ、溶接エリアのガスの均一なカバーを維持して、安定した溶接環境を維持できます。制御されていない気流や乱流は、シールド ガスを乱し、溶接品質に影響を与える可能性があります。
- 熱管理: 換気は、溶接プロセス中に発生する熱の管理に役立ちます。適切な空気の流れは材料や機器の過熱を防ぎ、熱による歪みや機器の故障のリスクを軽減します。
- 空気の質: 溶接環境の空気の質を良好に保つことで、レーザー ビームや溶接プロセスに干渉する可能性のあるほこりやその他の微粒子の蓄積を防ぐことができます。空気がきれいであれば、ビームの品質が一定になり、欠陥のリスクが軽減されます。
- 安全対策: 適切な換気を確保することで、有害な煙にさらされるリスクが軽減され、職場全体の安全性が向上します。また、汚染や粒子の蓄積を防ぐことで、レーザー光学系やその他の敏感なコンポーネントの完全性を維持するのにも役立ちます。
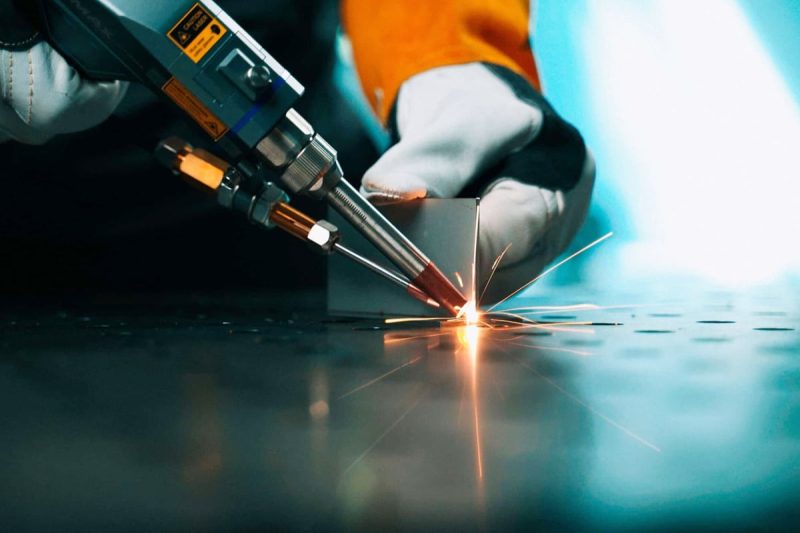
溶接速度
最適な溶接速度
最適な溶接速度を達成するには、溶接品質と生産性の間の微妙なバランスを保つ必要があります。適切な速度であれば、欠陥を生じさせることなく材料が完全に融合されます。
- 完全な融合: 最適な溶接速度で、レーザーは材料を完全に溶かして融合するのに十分なエネルギーを供給します。これにより、優れた機械的特性を備えた、強力で欠陥のない溶接が実現します。
- 一貫した品質: 一貫した溶接速度により、溶接部に沿って均一な熱入力が確保され、一貫した溶接品質が得られます。速度の変動により不規則性が生じ、溶接部の強度と外観に影響する可能性があります。
高速溶接の影響
溶接速度を速くすると生産性が向上しますが、特定の課題や潜在的な欠点も伴います。
- 生産性の向上: 溶接速度が速いとサイクル時間が短縮され、一定時間内により多くの溶接を完了できるようになります。これは、大量生産環境で特に有益です。
- 潜在的な欠陥: 溶接速度が速すぎると熱入力が不十分になり、不完全な融合、溶接の弱化、ひび割れが発生する可能性があります。動きが速いと、材料が溶けて適切に結合するための時間が十分に取れない場合があります。
- 表面の不規則性: 速度が非常に速い場合、溶融池が落ち着く時間が十分になく、波紋や飛沫などの表面の不規則性が生じる可能性があります。
低速溶接の影響
溶接速度を遅くすると溶接品質が向上しますが、一定の制限と考慮事項があります。
- 浸透の改善: 溶接速度が遅いと溶接の単位長さあたりの熱入力が増加し、浸透が改善され、厚い材料の完全な融合が保証されます。
- 熱影響部 (HAZ) の増加: 速度が遅いと熱入力が過剰になり、HAZ が大きくなります。これにより、熱変形、機械的特性の低下、溶接部品の反りが発生する可能性があります。
- 生産性の低下: 溶接速度が遅いと生産性が低下し、溶接作業を完了するのに必要な合計時間が長くなります。大量生産環境では、これは大きなデメリットとなる可能性があります。
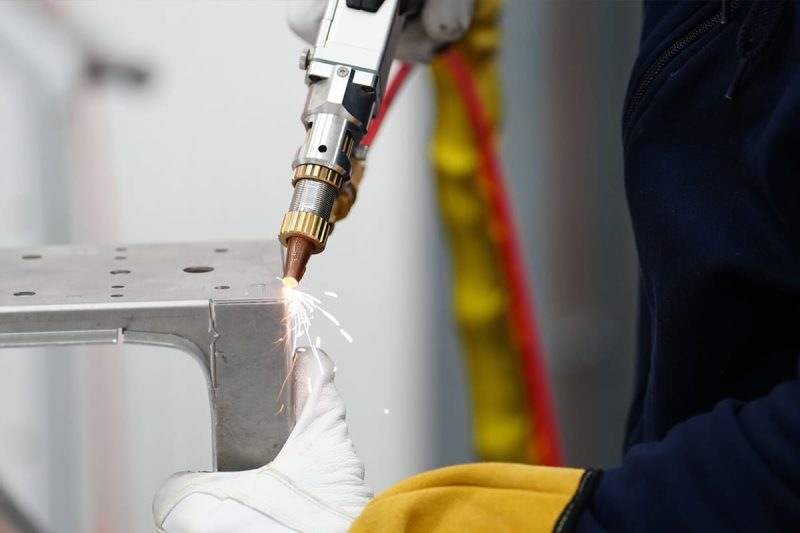
オペレーターのスキルと経験
オペレーターのスキルと経験の重要性
オペレーターの熟練度は、溶接機器の適切なセットアップ、正確なパラメータ調整、溶接プロセス中に発生する可能性のある問題を迅速に特定して解決する能力など、いくつかの理由で重要です。
- セットアップと調整: 熟練したオペレーターは、レーザー溶接機器のセットアップと調整に長けています。これには、レーザーの位置合わせ、焦点の調整、適切なレーザー出力の設定、シールド ガス フローの構成が含まれます。適切なセットアップにより、溶接プロセスが適切な基礎から開始され、欠陥や非効率のリスクが最小限に抑えられます。
- パラメータ調整: 経験豊富なオペレーターは、溶接パラメータと溶接品質の関係を深く理解しています。溶接速度、レーザー出力、パルス周波数などのパラメータを正確に調整して、さまざまな材料や接合構成に合わせて溶接プロセスを最適化できます。
- トラブルシューティングと問題解決: 溶接プロセス中には、位置ずれ、溶け込み不良、気孔や亀裂などの欠陥の形成など、さまざまな問題が発生する可能性があります。熟練したオペレーターは、これらの問題を迅速に診断して是正措置を実施し、ダウンタイムを最小限に抑え、一貫した溶接品質を確保できます。
- プロセスの適応性: さまざまな材料、ジョイント構成、溶接タスクには、特定の調整が必要です。経験豊富なオペレーターは、さまざまな条件に合わせてプロセス パラメータを調整し、アプリケーション全体で一貫した溶接品質を確保できます。
トレーニングと認定
適切なトレーニングと認定は、オペレーターの高いスキルの開発と維持に役立ちます。包括的なトレーニング プログラムには、次の内容が含まれる必要があります。
- 理論的知識: レーザー エネルギーと材料の相互作用を含むレーザー溶接の原理を理解することが重要です。オペレーターは、情報に基づいた決定を下すために、プロセスの背後にある科学に精通している必要があります。
- 実践的な経験: レーザー溶接機器を使用した実践的なトレーニングにより、オペレーターは機械の設定、調整、操作の経験を積むことができます。実践的な経験は、現実世界での自信と能力の構築に役立ちます。
- 安全プロトコル: レーザー溶接には、強い光、煙、熱などの潜在的な危険が伴います。トレーニングでは、オペレーターを保護し、安全な作業環境を確保するための安全プロトコルに重点を置く必要があります。
- 認定プログラム: 認定プログラムは、オペレーターのスキルと知識を検証し、その専門知識を正式に認めます。認定されたオペレーターは、通常、複雑な溶接タスクを処理し、問題を効果的にトラブルシューティングする能力が優れています。
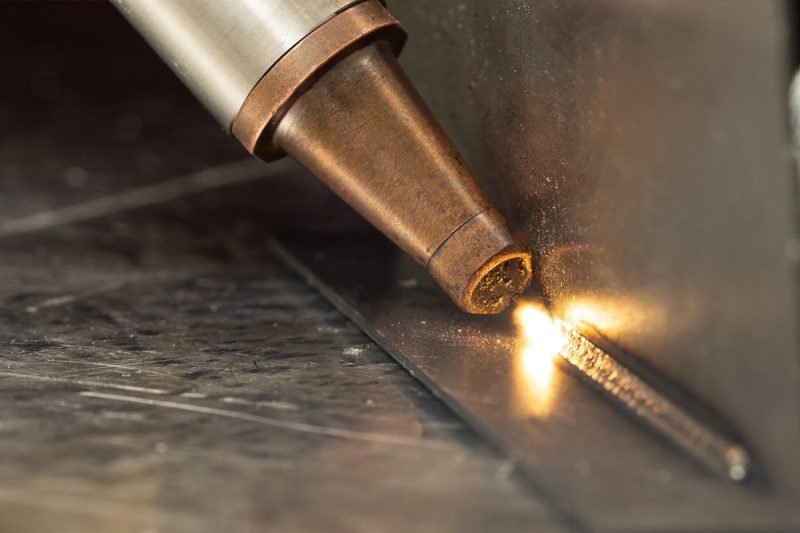
設備とメンテナンス
レーザー光源
レーザー光源は ファイバーレーザー溶接システム溶接に必要な高強度ビームを生成します。
- ファイバーレーザー: 高い効率、優れたビーム品質、耐久性で知られるファイバーレーザーは、アルミニウムや銅などの反射性金属を含むさまざまな材料の溶接に最適です。
- メンテナンス: 一貫したパフォーマンスを確保するために定期的に出力を監視し、汚染を防ぐために光学系を清掃し、ビームの精度を維持するために位置合わせを確認します。
光学
光学系はレーザービームを溶接領域に向け、焦点を合わせ、正確なエネルギー供給を保証します。
- ビーム伝送システム: 損失を最小限に抑えてレーザー ビームを伝送するための光ファイバーとコリメータが含まれています。
- 集束光学系: レーザービームを小さなスポットサイズに集中させ、エネルギー密度を高めるレンズまたは集束ヘッド。
- メンテナンス: レンズ、ミラー、保護ウィンドウの定期的なクリーニング、損傷の検査、位置合わせのチェックを行うことで、最適なビーム品質を維持できます。
モーションシステム
モーション システムはレーザー ビームとワークピースの動きを制御し、正確な位置決めとスムーズな操作を保証します。
- タイプ: 3 軸直線運動用の直交座標系、多軸運動用のロボット アーム、大規模アプリケーション用のガントリー システム。
- メンテナンス: 可動部品の定期的な潤滑、正確な動作のための定期的な調整、摩耗やずれのチェックにより、信頼性の高い動作が保証されます。
冷却システム
冷却システムはレーザー光源やその他の主要コンポーネントの過熱を防ぎ、安定した動作を維持します。
- 水冷:優れた放熱効果により、高出力ファイバーレーザー発生器でよく使用されます。
- コンポーネント: ポンプ、熱交換器、および冷却液リザーバーは、冷却システムの重要な要素です。
- メンテナンス: 漏れや詰まりがないか定期的に確認し、冷却液の品質を監視し、必要に応じてフィルターを交換して、効率的な冷却を確保します。
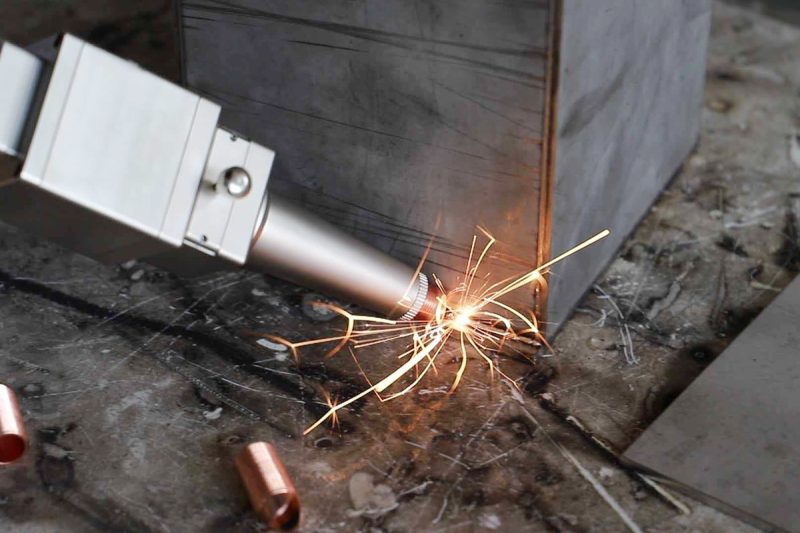
自動化および制御システム
リアルタイム監視
リアルタイム監視システムは溶接プロセスに関する継続的なフィードバックを提供し、最適なパフォーマンスを確保するために即座に調整を行うことができます。
- 溶接品質監視: センサーとカメラが溶接プールを監視し、気孔、亀裂、位置ずれなどの欠陥をリアルタイムで検出します。これにより、オペレーターはレーザー出力、速度、焦点をリアルタイムで調整できます。
- レーザー出力監視: システムはレーザー出力を継続的に追跡し、希望の範囲内に維持します。これにより、一貫したエネルギー供給と溶接の浸透が維持されます。
適応制御
適応制御システムは、リアルタイム データに基づいて溶接パラメータを動的に調整し、さまざまな条件に合わせてプロセスを最適化します。
- パラメータ調整: これらのシステムは、材料特性、厚さ、接合部構成の変化に基づいて、レーザー出力、溶接速度、焦点位置を自動的に調整します。これにより、ワークピースのさまざまな部分にわたって均一で一貫した溶接品質が保証されます。
- フィードバック ループ: フィードバック ループを組み込むことで、システムは以前の溶接から学習し、時間の経過とともに精度と効率を向上させることができます。
ロボットシステムとの統合
ファイバーレーザー溶接をロボット システムに統合すると、自動化、柔軟性、再現性が向上します。
- 多軸モーション: ロボット アームは、複雑な形状や届きにくい領域を正確に溶接するための多軸モーションを提供します。
- 一定の品質: ロボットは溶接パス、速度、角度を正確に制御することで一貫した溶接品質を確保し、手動溶接に伴う変動を減らします。
- スループットの向上: ロボットによる自動化により、連続操作が可能になり、サイクルタイムが短縮されるため、スループットが向上し、生産性が大幅に向上します。
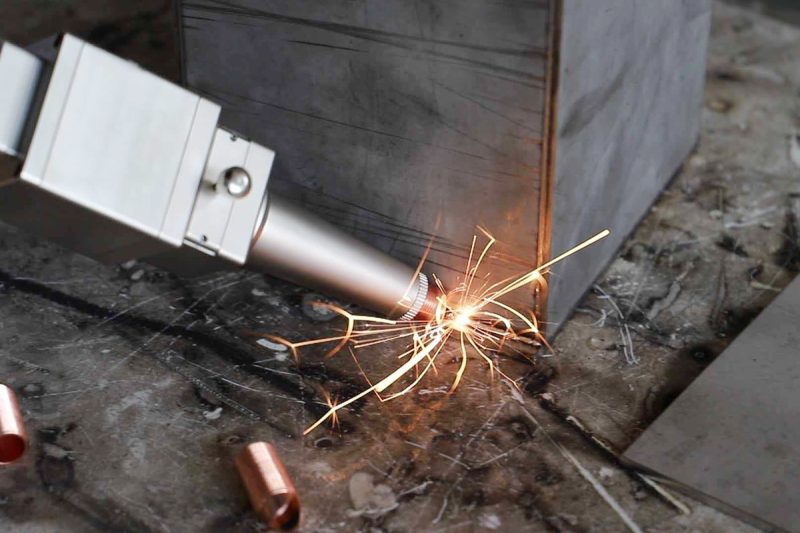
アプリケーション固有の考慮事項
素材の組み合わせ
さまざまな材料がレーザー溶接に対して独自の反応を示し、それらの組み合わせによって特定の課題が生じる可能性があります。
- 異種材料: アルミニウムと鋼鉄などの異種材料の溶接は、融点、熱伝導率、レーザー吸収率の違いにより困難な場合があります。ファイバー レーザーはこれらの組み合わせの溶接に効果的ですが、熱入力を管理して欠陥を回避するために、パラメータを正確に制御する必要があります。
- 反射性材料: 銅やアルミニウムなどの材料はレーザーエネルギーの大部分を反射するため、溶接効率が低下する可能性があります。特に波長の短いファイバーレーザーはこれらの材料に適していますが、効果的なエネルギー吸収を確保するにはレーザーパラメータを最適化することが不可欠です。
- 合金および複合材料: 合金または複合材料ごとに、最適な溶接を行うために特定の設定が必要になる場合があります。材料の特性を理解し、それに応じてレーザー出力、速度、焦点を調整することが、高品質の溶接を実現するための鍵となります。
溶接形状
溶接継手の形状は溶接プロセスに影響を与えるため、効率を確保するには慎重に考慮する必要があります。
- 複雑な形状: 曲線や入り組んだ形状などの複雑な形状を溶接するには、レーザー ビームとモーション システムを正確に制御する必要があります。ファイバー レーザーは、高度なモーション システムやロボット アームと統合することで、これらの形状を効果的に処理できます。
- 薄いセクションと厚いセクション: 薄いセクションを溶接する場合は、溶け落ちを防ぐために低電力と高精度が必要ですが、厚いセクションを完全に貫通するには、高電力と低速が必要です。レーザー パラメータを特定の形状に合わせて調整すると、効率的な溶接を実現できます。
- エッジの準備: 面取りやクリーニングなどの適切なエッジの準備により、フィット感と融合が向上します。エッジの品質を一定に保つことで、均一な溶接を実現できます。
生産量
生産量はレーザー溶接装置とプロセスパラメータの選択に影響します。
- 小ロットまたはカスタム生産: 小ロットまたはカスタム生産では、柔軟性と適応性が重要です。ファイバーレーザーの汎用性により、溶接パラメータと構成をすばやく調整できるため、さまざまな特殊な溶接作業に適しています。
- 大量生産: 大量生産には一貫性、スピード、自動化が必要です。自動制御システムとロボット アームを統合したファイバー レーザー システムは、必要な精度と再現性を提供し、生産性と効率を大幅に向上させます。
- サイクル タイムの最適化: 生産環境では、サイクル タイムを最小限に抑えることで効率を向上させることができます。リアルタイム監視と適応制御を備えたファイバー レーザー システムは、セットアップ時間を短縮し、最適な溶接速度を確保することで、全体的な生産性を向上させます。
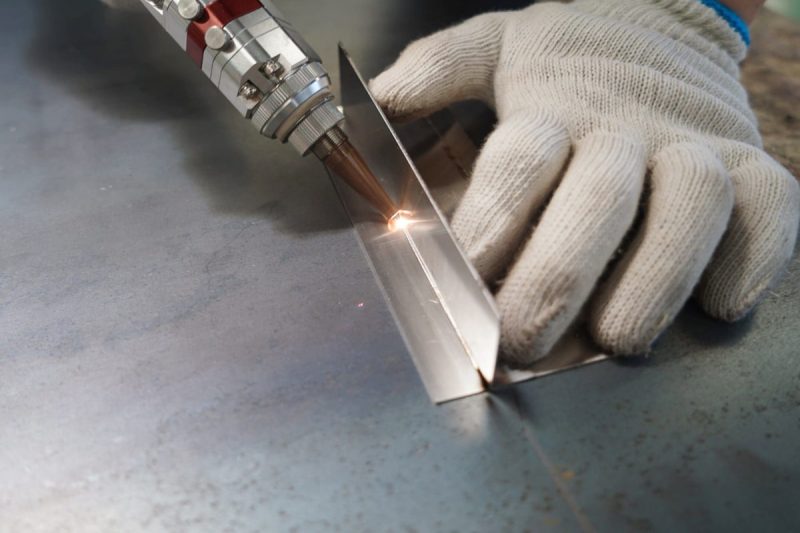
まとめ
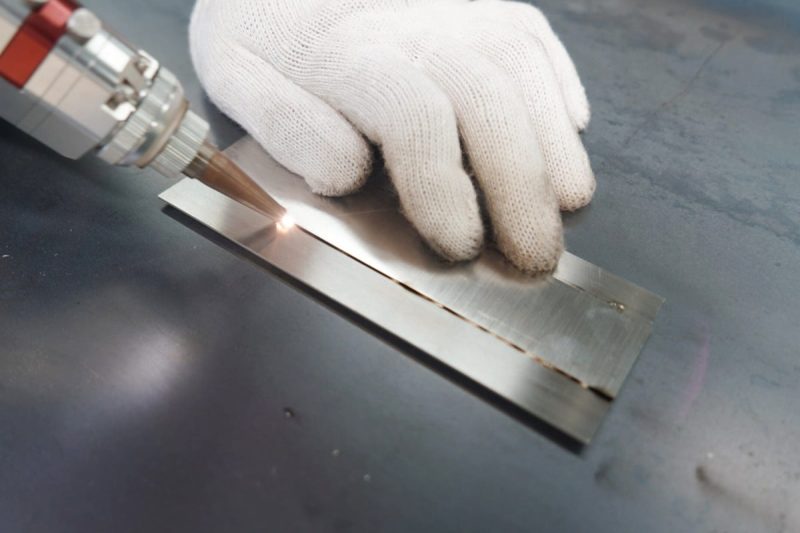
レーザー溶接ソリューションを入手
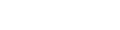
- [email protected]
- [email protected]
- +86-19963414011
- No. 3 ゾーン A、Lunzhen 工業地帯、玉城市、山東省。