
レーザー溶接はどれくらい高温になりますか?
レーザー溶接は、効率的で精密な溶接技術です。その核心は、高強度のレーザービームを使用して材料を局所的に溶かし、急速冷却によって強力な接続を実現することです。従来の溶接方法とは異なり、レーザー溶接のエネルギーは集中しており制御可能であり、動作温度は非常に高く、ほとんどの金属や合金を溶かすのに十分な6000℃以上に簡単に達します。温度は、レーザー溶接プロセスにおいて重要なパラメータです。温度は、材料の溶融速度と溶接深さを決定するだけでなく、溶接継手の強度と表面仕上げにも影響します。レーザービームの熱入力が非常に集中しているため、レーザー溶接は速度、精度、熱影響部(HAZ)制御の点で明らかな利点があり、多くの分野で好まれるプロセスとなっています。
レーザー溶接における温度制御も、プロセスの適合性と最終的な性能に直接影響します。溶接温度が高すぎると、材料が過度に焼けたり、気孔や亀裂などの溶接欠陥が現れたりする可能性があります。温度が低すぎると、材料が完全に溶融せず、溶接の浸透が不完全などの問題が発生する可能性があります。さらに、溶接材料の種類、レーザー出力、ビーム焦点、溶接速度などのさまざまな要因が溶接温度に大きな影響を与えます。実際の操作では、エンジニアは通常、材料の融点と熱伝導率に基づいてプロセスパラメータを調整することにより、溶接効果を最適化します。この正確な温度制御により、レーザー溶接は自動車製造、航空宇宙、医療機器などの需要の高い業界で広く使用されており、優れた性能と適応性を実証しています。
目次
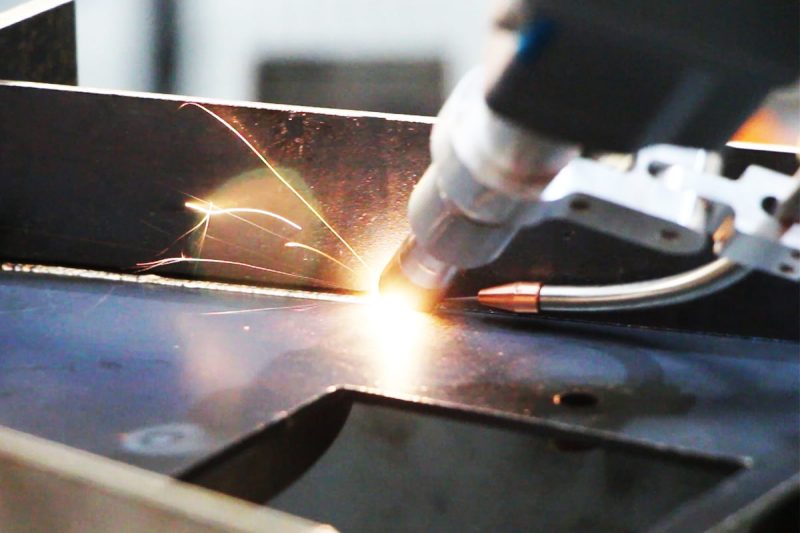
レーザー溶接温度の理解
レーザー溶接における高温の原理
レーザー溶接は、高エネルギー密度のレーザービームを集束させて材料を溶接し、強力な溶接継手を形成します。レーザー溶接プロセス中、レーザービームの焦点温度は非常に高くなり、通常は6000℃を超え、場合によっては10000℃に達することもあります。この高温は、次のような一般的な金属材料のほとんどを溶かすのに十分です。 ステンレス鋼、アルミニウム合金、銅、チタン合金などの金属材料のレーザー溶接に適しています。レーザー溶接は高温特性があるため、溶融溶接工程を短時間で完了でき、集中した入熱により熱影響部(HAZ)を最小限に抑えることができ、熱変形や残留応力のリスクを軽減できます。
従来の溶接プロセスと比較して、レーザー溶接には次のような独自の利点があります。
- 高エネルギー密度:レーザー溶接の焦点領域のエネルギーが集中しているため、金属を素早く溶かすことができ、精密溶接に適しています。
- 高い制御精度: レーザー出力、ビーム焦点、その他のパラメータを正確に調整できるため、温度分布を高度に制御できます。
- 急速加熱: レーザー溶接では金属を数ミリ秒で素早く溶かすことができるため、溶接速度が大幅に向上します。
レーザー溶接温度と他の溶接プロセスとの比較
他の従来の溶接プロセスと比較すると、レーザー溶接は温度特性と熱影響モードが異なります。以下は、レーザー溶接、アーク溶接、抵抗溶接の温度比較です。
レーザー溶接
- 温度範囲: 通常は 6000℃ ~ 10000℃ ですが、焦点領域の温度は非常に高くなることがあります。
- 温度分布:レーザー溶接の温度は溶接部分に集中し、周囲の材料に熱が拡散することはほとんどありません。
- 特徴: レーザー溶接は、高濃度の温度と精密な制御により、非常に短時間で溶融を完了でき、溶接速度が速く、熱影響部が小さいため、溶接精度と品質に対する要求が非常に高いシーンに適しています。
アーク溶接
- 温度範囲: アークの種類と溶接条件によって異なりますが、通常は 3500℃ ~ 6000℃ です。
- 温度分布: アーク溶接では温度分布が広く、温度がより広い範囲に広がるため、熱影響部が大きくなる可能性があります。
- 特徴:アーク溶接は通常、厚い材料の溶接に使用されます。温度は高くなりますが、入熱量が大きいため熱変形や応力が大きくなり、制御精度が比較的悪くなります。
抵抗溶接
- 温度範囲:抵抗溶接の温度は通常 3000℃ 以下で、接触点に集中します。
- 温度分布: 抵抗溶接の温度は、主に 2 つの電極が材料に接触する場所に集中し、局所的な加熱が発生します。
- 特徴:抵抗溶接は薄板材料の溶接に適しています。低温で溶接領域が集中しているため過熱を回避できますが、適用範囲が狭いです。
レーザー溶接は、高温と集中入熱特性のため、溶接温度の微細な制御と小さな熱影響部を必要とする高精度の溶接作業に適しています。従来のアーク溶接や抵抗溶接プロセスと比較して、レーザー溶接はエネルギー密度が高く、溶接プロセスが速く、熱影響部が小さいため、航空宇宙、自動車製造、電子機器などの分野で広く使用されています。異なる溶接プロセスの温度制御と溶接品質の違いにより、異なる材料や産業ニーズにおいて利点と限界があります。
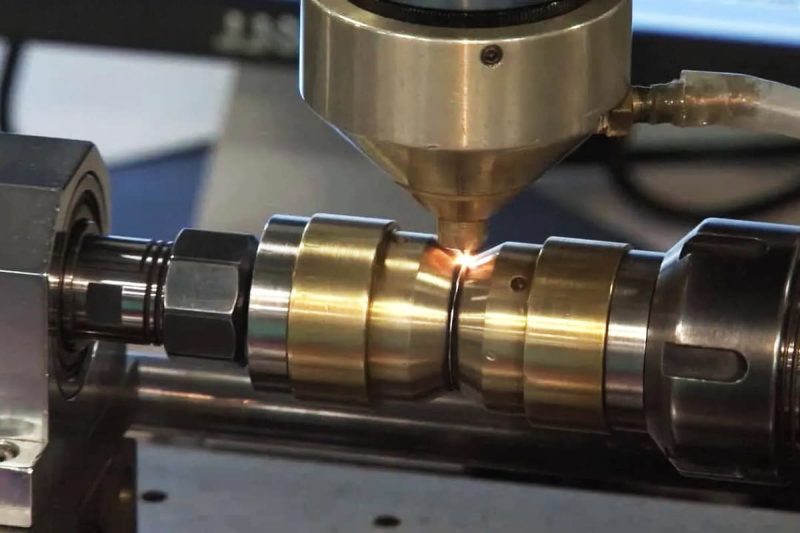
溶接温度に影響を与える要因
レーザー溶接は精密溶接技術であり、その溶接温度は多くの要因の影響を受けます。これらの要因は、溶接効果、溶接品質、最終製品の性能に直接関係しています。次に、いくつかの主要な要因がレーザー溶接の温度にどのように影響するかについて詳しく説明します。
レーザーパワー
レーザーの出力は、レーザー溶接温度に影響を与える最も重要な要素の 1 つです。出力が高いほど、レーザービームから放出されるエネルギーが大きくなり、溶融できる材料が厚くなりますが、過度の燃焼や熱による損傷などの問題が発生する可能性もあります。
- 高出力レーザー:厚い材料に使用され、材料を溶かすのに十分なエネルギーを素早く供給できます。産業グレードの レーザー溶接機 通常、500W〜6000Wです。さまざまなニーズに応じて、さまざまな材料の厚さと種類に合わせて電力を調整できます。高出力のレーザー溶接は厚い材料や大規模生産に適していますが、熱が蓄積されやすく、熱変形や溶接の不均一さが生じる可能性があります。
- 低出力レーザー: 薄い材料に適しており、熱入力を制御して微細な溶接が可能です。低出力レーザー溶接は材料への熱影響を軽減できますが、出力が低すぎると材料が完全に溶けず、溶接接合部の強度が不十分になる可能性があります。
ビームフォーカス
ビームの焦点は、レーザー溶接の温度分布を決定する重要な要素の 1 つです。レーザー ビームの焦点の度合いはエネルギー密度に直接影響し、エネルギー密度が溶接プロセス中の温度を決定します。
- 正確な焦点: レーザービームの焦点が正確であればあるほど、エネルギー密度と温度が高くなり、材料を素早く溶かして溶接を完了できます。正確な焦点合わせにより、溶接中の熱分布が均一になり、溶接結果が良好になります。
- 焦点オフセット: レーザービームの焦点がオフセットされていたり、焦点精度が十分でなかったりすると、エネルギー分布が不均一になり、溶接領域の温度も不均一になり、溶接継手の強度が低下したり、冷間溶接や亀裂などの品質問題が発生する可能性があります。
材料の種類
異なる材料の熱伝導率特性と融点の違いによって、必要な溶接温度が決まります。材料の熱伝導率、融点、反射率は、レーザー溶接の結果に大きな影響を与える可能性があります。
- 熱伝導率: 熱伝導率の高い材料 (銅やアルミニウムなど) は、溶接部分から周囲に熱を素早く拡散するため、これらの材料を溶かすにはより高い温度が必要です。対照的に、熱伝導率の低い材料 (ステンレス鋼やチタンなど) は、局所的に熱が蓄積される可能性が高いため、必要な溶接温度に達するのは比較的簡単です。
- 融点: 異なる材料の融点の違いも、溶接温度に直接影響します。たとえば、ステンレス鋼の融点は 1450℃ ですが、アルミニウム合金の融点はそれより低く、約 660℃ です。つまり、ステンレス鋼の溶接にはより高い温度とより強いレーザー出力が必要ですが、アルミニウム合金の溶接にはより低い温度で済みます。
溶接速度
溶接速度も温度に影響を与える重要な要素です。溶接速度によって単位時間あたりの材料への入熱量が決まり、溶接温度に影響します。
- 溶接速度の向上: 溶接速度が速いほど、レーザービームが溶接部を通過する時間が短くなり、材料への熱入力が減少します。これにより、溶接部の温度が低下し、熱の蓄積が少なくなり、熱影響部、変形、残留応力の減少に役立ちます。ただし、溶接速度が速すぎると、溶接金属の溶融が不十分になり、溶接品質の問題が発生する可能性があります。
- 溶接速度が遅い: 溶接速度が遅いと、レーザービームが溶接ゾーンに長時間留まるため、熱が蓄積され、溶接ゾーンの温度が上昇します。これは厚い材料の溶接に役立ちますが、熱影響部の過熱、変形、膨張につながる可能性もあります。
レーザー溶接温度は、レーザー出力、ビーム焦点、材料の種類、溶接速度など、多くの要因の影響を受けます。各要因は溶接温度にさまざまな程度で影響を及ぼし、それによって溶接の効果と品質が決まります。実際の操作では、材料の種類、厚さ、およびプロセス要件に応じて溶接パラメータを最適化する必要があります。これにより、スムーズな溶接プロセスが確保され、高品質の溶接継手が得られます。
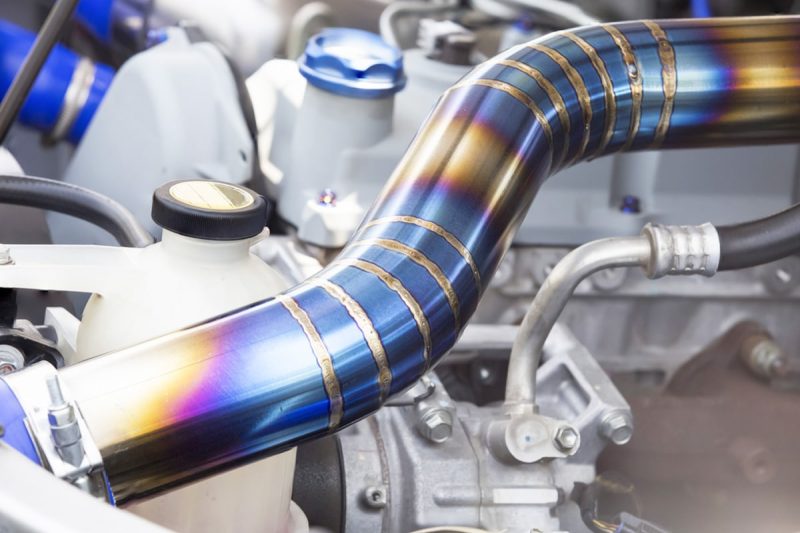
レーザー溶接の温度範囲
レーザー溶接は、集中エネルギーのレーザービームで材料を加熱する高精度の溶接プロセスです。溶接プロセス中、温度分布範囲は、材料の融点から溶接部のピーク温度まで広範囲にわたります。温度の制御と管理は、溶接の品質にとって非常に重要です。以下では、材料の融点、熱影響部 (HAZ) 温度、溶接プールのピーク温度など、レーザー溶接における温度のさまざまな側面について詳しく説明します。
材料の融点
レーザー溶接プロセスでは、材料を溶かして溶接接合部を形成するために、レーザー ビームで材料を融点以上に加熱する必要があります。材料によって融点は異なり、それがレーザー溶接に必要な温度に直接影響します。一般的な材料の融点範囲は次のとおりです。
- 鋼:鋼の融点は通常 1200℃ ~ 1500℃ です。融点は鋼の種類(炭素鋼、合金鋼など)によって異なります。炭素鋼の融点は比較的低く、合金鋼やステンレス鋼の融点は高くなる場合があります。
- アルミニウム:アルミニウムの融点は比較的低く、一般的には 600℃ ~ 700℃ です。融点が低いため、アルミニウムはレーザー溶接が容易ですが、過熱の影響を受けやすく、熱変形を引き起こします。
- チタン合金:チタン合金の融点は約1660℃で、鋼やアルミニウムよりも高いです。そのため、チタン合金を溶接する場合、溶融と溶接の品質を確保するために、レーザー温度をより高い範囲で制御する必要があります。
これらの融点範囲によってレーザー出力の選択と調整が決まり、溶接プロセス中の熱管理にも要件が課せられます。
熱影響部(HAZ)温度
熱影響部(HAZ)とは、溶接工程中にレーザービームの加熱により材料の温度が上昇するが、融点には達しない領域を指します。この領域では、溶融は発生しませんが、温度上昇により材料の微細構造が変化し、材料の機械的特性に影響を及ぼす可能性があります。
- 温度範囲: 熱影響部の温度は通常、材料の融点よりも低くなりますが、材料の格子構造に変化を引き起こすには十分な温度であり、通常は 500°C ~ 1000° の範囲です。一部の高強度材料の場合、これらの温度は硬度の変化を引き起こすのに十分であり、脆化を引き起こす可能性もあります。
- 影響要因: 熱影響部の温度は、レーザー出力、ビーム焦点、溶接速度、材料の熱伝導率など、多くの要因によって影響を受けます。レーザー出力が大きく、溶接速度が遅いほど、熱影響部は大きくなり、温度が高くなります。
HAZ 温度を制御することは、溶接継手の品質を確保する上で非常に重要です。HAZ 温度が高すぎると、材料の性能が低下し、全体的な溶接強度や疲労寿命にも影響する可能性があります。
ピーク溶接プール温度
溶接プールは、レーザー溶接プロセス中に溶融金属によって形成される液体金属の領域です。溶接プールのピーク温度は、溶接プロセス中に最も集中する温度であり、通常は溶接ゾーンの中央に位置します。溶接プールの温度は通常3000℃〜6000℃で、ほとんどの金属を溶かすのに十分であり、強力な溶接継手を形成するための鍵となります。
- 溶接プールの温度範囲: 溶接プールの温度は、材料とレーザーパラメータによって異なります。高融点材料(チタン合金、ステンレス鋼など)の場合、溶接プールの温度は3000°Cを超えることがありますが、低融点材料(アルミニウム合金など)の場合、温度は比較的低く、通常は3000°Cから4500°Cの間です。
- 温度が溶接品質に与える影響: 溶接プールの温度は、溶融池の深さと幅、および最終的な溶接継手の形状を直接決定します。溶接プールの温度が高すぎると、溶融池が深くなりすぎて熱変形のリスクが高まり、温度が低すぎると、溶接が不十分になり、継手強度が不十分になる可能性があります。
レーザー溶接中、温度は材料の融点から溶接プールのピーク温度までの範囲です。融点はレーザーが到達する必要がある最低温度を決定し、熱影響部の温度と溶接プールのピーク温度は溶接の深さ、接合部の強度、および材料の最終的な特性に影響します。異なる材料、溶接パラメータ、およびプロセス設定は溶接中の温度分布に影響を与えるため、実際の操作では、溶接の品質と溶接継手の信頼性を確保するために温度を正確に制御する必要があります。
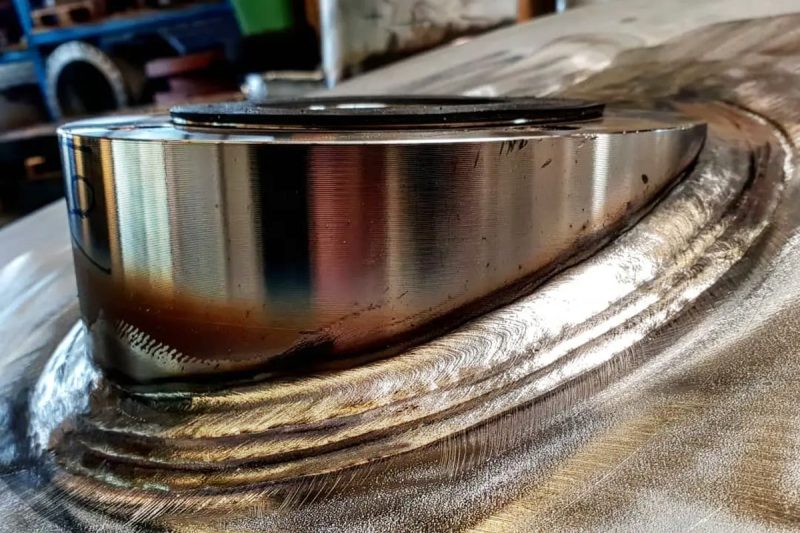
温度が溶接品質と性能に与える影響
温度はレーザー溶接プロセスにおいて重要な要素であり、溶接品質、材料特性、および最終ワークピースの性能に影響します。レーザー溶接では、材料を十分な温度に加熱して溶融結合させる必要がありますが、温度が高すぎたり低すぎたりすると、溶接品質と材料特性に悪影響を及ぼします。以下では、温度が溶接品質と性能に及ぼす具体的な影響について詳しく説明します。
材料特性
溶接プロセス中、温度変化によって材料の微細構造が変化し、溶接接合部の機械的特性に直接影響を及ぼします。
- 結晶粒の微細化または粗大化: レーザー溶接中、材料は急速な加熱と冷却を受け、温度変化により結晶粒が微細化または粗大化することがあります。結晶粒の大きさは材料の強度と靭性に直接影響します。温度が高すぎると結晶粒が粗大化し、溶接接合部の強度が低下する可能性があります。逆に、溶接温度が低いと結晶粒が細かすぎて、溶接部の靭性が弱まる可能性があります。
- 相変化: 鋼鉄が高温でフェライトからオーステナイトに変化するなど、一部の材料は加熱中に相変化を起こします。この相変化により、材料の機械的特性が変化する場合があります。溶接温度が異なると、異なる熱処理プロセス (焼きなまし、焼き入れなど) が発生する場合もあり、材料の硬度、引張強度、疲労耐性に影響を及ぼします。
溶接品質
温度は、特に接合部の完全性と安定性の点で、溶接接合部の品質に直接影響を及ぼします。
- 温度が高すぎる: 温度が高すぎると、気孔、亀裂、過度の燃焼など、一連の溶接欠陥が発生する可能性があります。高温では、金属の溶融池が大きすぎるため、ガスが溶融池に入りやすくなり、気孔が形成されます。また、高温により、材料の表面に酸化または脆性相が発生し、溶接亀裂のリスクが高まります。温度が高すぎると、材料が過度の燃焼を引き起こし、溶接部分が過剰に溶融し、最終的に接合部の強度が低下する可能性があります。
- 温度が低すぎる: 溶接温度が低すぎると、金属が完全に溶けず、溶け込みが不完全になる可能性があります。溶け込みが不完全とは、溶接接合部の溶融部分が完全に結合していないことを意味し、接合部の強度が低下します。また、溶接温度が低いと、溶接接合部の表面が不均一になったり、冷間割れが発生したり、引張強度が低下したりすることもあります。
残留応力と変形
レーザー溶接では、高温の影響により溶接部に熱膨張、収縮が生じ、残留応力や熱変形が発生します。
- 残留応力: 高温溶接中、金属は膨張と収縮を起こしますが、溶接部分の熱膨張は通常、溶接されていない部分の熱膨張よりも大きいため、残留応力が発生します。残留応力が大きすぎると、使用中に材料が変形したり、接合部が破裂したり、疲労破壊したりすることがあります。残留応力が存在すると、溶接部分に亀裂が広がり、構造全体の信頼性に影響を与えることもあります。
- 熱変形: レーザー溶接の高温により、特に薄い材料では材料の熱変形が発生する可能性があります。熱変形の程度は、溶接温度、材料の熱膨張係数、溶接速度などの要因によって異なります。熱変形により部品の寸法が不正確になり、部品の組み立てや機能に影響する可能性があります。特に、航空宇宙や電子機器製造などの一部の精密製造業界では、過度の熱変形により部品が許容範囲の要件を満たさなくなる可能性があります。
溶接後の熱処理と修正
溶接中に発生する残留応力や熱変形を制御・低減するために、通常は溶接後に適切な熱処理や修正が必要となります。
- 熱処理:溶接後、残留応力を除去し、材料の微細構造を最適化し、機械的特性を向上させるために、材料を焼鈍、焼き入れ、または焼入れする必要があることがよくあります。加熱と冷却のプロセスを制御することで、過度に高い温度または低い温度によって引き起こされる悪影響を効果的に軽減できます。
- 修正: 熱変形が大きい場合は通常、機械的な修正またはレーザー レベリング技術を使用して、ワークピースの形状とサイズの偏差を修正する必要があります。これにより、溶接部品の元の形状が復元され、使用中の精度と安定性が確保されます。
温度はレーザー溶接の品質と性能に大きな影響を与えます。材料の微細構造の変化から溶接継手の強度と安定性、溶接プロセス中の残留応力と熱変形まで、温度制御は溶接品質を確保するための鍵です。温度が高すぎたり低すぎたりすると溶接欠陥が発生し、最終製品の性能と信頼性に影響を与える可能性があります。したがって、レーザー溶接プロセスでは、高品質の溶接継手を得るために、正確な温度制御と溶接パラメータの適切な管理が不可欠です。
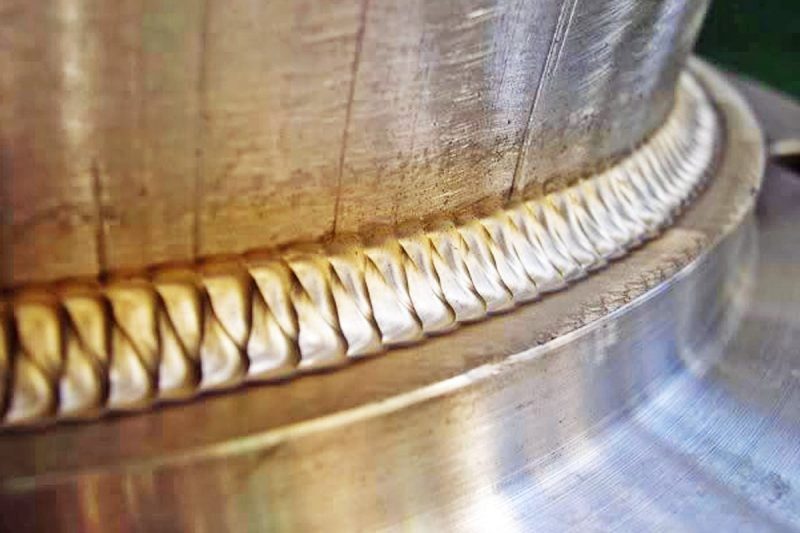
レーザー溶接温度の制御
高品質の溶接結果を確保するには、レーザー溶接の温度を正確に制御することが不可欠です。溶接温度は、溶接継手の強度、溶接領域の微細構造、最終製品の性能に直接影響します。以下は、溶接プロセスを最適化し、溶接品質の安定性と一貫性を確保するために役立つ、温度を制御するための一般的な戦略です。
プロセスパラメータを調整する
溶接プロセス中、レーザー出力、溶接速度、ビームモードなどのプロセスパラメータは、溶接温度に影響を与える重要な要素です。これらのパラメータを正確に調整することで、必要な温度制御を実現できます。
- レーザー出力: レーザー出力はエネルギー入力量を直接決定し、溶融池の温度に影響します。出力が高いほど厚い材料の溶接に適していますが、過度の燃焼や熱損傷を引き起こす可能性があります。出力が低いほど薄い材料の溶接に適していますが、溶け込みが不完全になる可能性があります。出力は材料の厚さと溶接要件に応じて調整する必要があります。
- 溶接速度: 溶接速度は入熱量に反比例します。溶接速度が速いほど入熱量が少なくなり、溶接温度が低くなるため、薄い材料や必要な熱量が少ない場合に適しています。溶接速度が遅いほど入熱量が多くなるため、厚い材料やより強い溶接が必要な場合に適しています。
- ビーム モード: レーザー ビームのフォーカス モード (円形、長方形、線形モードなど) は、ビームのエネルギー密度、ひいては温度分布に影響します。正確なビーム フォーカスにより、レーザー エネルギーを小さな領域に集中させ、材料を素早く加熱できます。また、拡張ビーム モードでは、熱を均等に分散させ、局所的な過熱のリスクを軽減できます。
予熱と後熱
特定の材料、特にアルミニウム合金や高強度鋼などの材料は、熱に対して非常に敏感です。熱入力を制御する戦略には、予熱と後加熱が含まれ、これにより、亀裂、熱変形、残留応力を軽減できます。
- 予熱:予熱とは、溶接前に材料を一定の温度まで加熱することです。アルミニウム合金やマグネシウム合金などの低融点材料の場合、予熱により、溶接中に材料が急速に冷却されることで生じる熱応力や亀裂のリスクを軽減できます。また、予熱により、溶接中の熱衝撃を軽減し、過度の温度差による亀裂を防ぐこともできます。
- 後加熱: 溶接後の加熱 (またはアニーリング) は、溶接領域の残留応力を軽減し、熱変形のリスクを軽減し、溶接継手の機械的特性を向上させるのに役立ちます。後加熱は通常、溶接後の冷却速度を制御することによって実現され、特に高強度鋼やその他の熱に敏感な材料の溶接では重要です。
監視およびフィードバックシステム
現代のレーザー溶接装置には通常、高精度の温度監視システムが装備されており、溶接温度をリアルタイムで監視し、リアルタイムデータに基づいてプロセスパラメータを調整できます。これらのシステムは、溶接プロセスの精度を向上させるだけでなく、溶接品質の一貫性も保証します。
- 温度センサー:温度センサーは、溶接領域の温度をリアルタイムで測定し、温度変化情報を制御システムにフィードバックします。一般的に使用されるセンサーには、赤外線温度センサーとレーザースペクトルセンサーがあり、溶接領域の温度を非接触で監視できます。
- 自動フィードバック調整システム:温度監視システムは、レーザー出力制御システムおよび溶接速度制御システムとリンクして、実際の溶接温度に応じてレーザー出力と溶接速度を動的に調整し、温度を必要な範囲内に維持します。このような自動フィードバックシステムは、溶接の安定性を向上させるだけでなく、人的操作によるエラーも削減します。
その他の温度制御戦略
上記の方法に加えて、レーザー溶接では他の技術を組み合わせて温度をさらに制御することもできます。
- レーザーパルス制御: レーザーパルスの周波数と持続時間を調整することで、熱入力を正確に制御できます。短いパルスはより低い温度入力を実現でき、熱に敏感な材料に適しています。一方、長いパルスはより高い温度を必要とする溶接作業に適しています。
- マルチビーム溶接: 溶接プロセス中に複数のレーザービームを並行して使用すると、溶接領域に熱が均等に分散され、局所的な過熱が回避され、溶接品質が向上します。
レーザー溶接温度は、プロセスパラメータ、予熱と後加熱、効果的な冷却戦略、高度な温度監視およびフィードバックシステムを正確に調整することで効果的に制御できます。これらの制御により、溶接中の温度が最適な範囲内に保たれ、高品質の溶接接合部が得られ、欠陥のリスクが軽減され、最終製品のパフォーマンスが最適化されます。
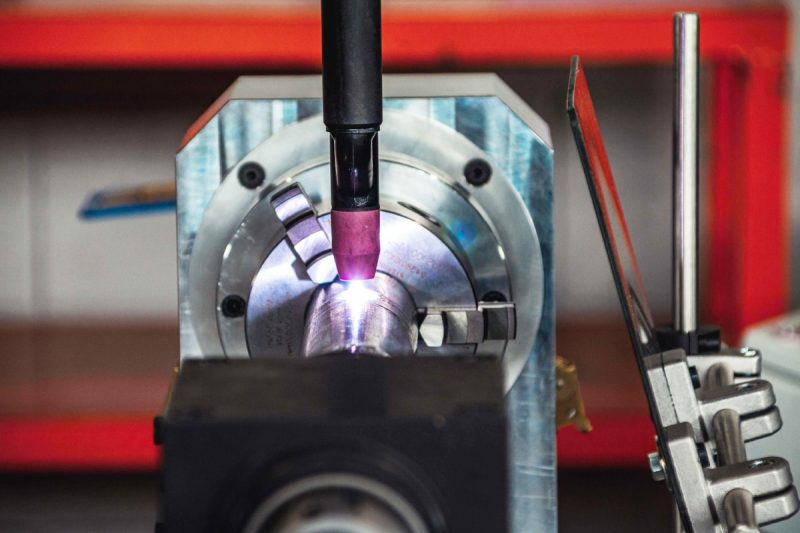
特定のアプリケーションにおける温度に関する考慮事項
レーザー溶接技術は多くの業界で広く使用されており、分野によって溶接温度要件に大きな違いがあります。あらゆる業界でレーザー溶接を使用する場合、材料特性、溶接目標、品質要件に基づいて溶接温度を正確に制御する必要があります。ここでは、主要な業界の温度制御に関する考慮事項をいくつか紹介します。
自動車産業
自動車業界では、ドア、ルーフ、シャーシなどの車体構造部品の溶接にレーザー溶接が広く使用されています。この業界では溶接の品質と効率に対する要件が非常に高いため、温度制御が特に重要です。
- 溶接強度:車体構造は、運転の安全性を確保するために高い溶接強度を備えている必要があります。そのため、溶接温度は、溶接領域の良好な融合を確保し、高い強度要件を満たすのに十分な高さである必要があります。ただし、温度が高すぎると溶接接合部が脆くなる可能性があるため、入熱を正確に制御する必要があります。
- 効率と生産速度: 自動車製造業界では生産速度に対する要求が厳しく、溶接中の温度制御は溶接品質を確保するだけでなく、溶接効率も考慮する必要があります。したがって、適切な溶接温度を制御することで、高品質の溶接継手を維持しながら生産ラインの速度を上げることができます。
- 熱影響部(HAZ):ボディの材質は主に高強度鋼またはアルミニウム合金であり、熱影響部の制御は特に重要です。過度の温度は熱影響部を軟化させ、材料の機械的特性に影響を与えます。したがって、材料の性能低下を防ぐために、過度に高い溶接温度を避ける必要があります。
航空宇宙産業
航空宇宙産業では材料の性能に対する要求が非常に厳しく、溶接時の温度管理は特に重要です。特に航空機の構造部品やエンジン部品の製造では、溶接温度が高すぎたり低すぎたりすると、材料の性能に大きな影響を与えます。
- 熱影響部制御: 航空宇宙産業で使用されるチタン合金や耐熱合金などの材料は、一般的に強度と耐腐食性が高くなっています。溶接プロセス中は、熱影響部 (HAZ) が過度に大きくなるのを避けるために、入熱を正確に制御する必要があります。過熱すると、材料の強度が低下し、ひび割れが発生する可能性があり、構造部品の全体的な性能に影響を及ぼします。
- 温度精度: 高精度の温度制御は航空宇宙産業の中心的な要件です。材料は温度変化に非常に敏感なので、溶接中に低出力レーザーを使用して熱入力を減らし、溶接接合部があまり影響を受けないようにする必要があります。
- 溶接品質: 航空宇宙分野では、溶接品質は飛行の安全性に直接関係します。そのため、溶接中の温度が常に最適な範囲内に保たれ、不均一な加熱や過熱を防ぐことが重要です。
電子機器製造
電子機器製造の分野では、マイクロ回路、コネクタ、コンポーネントなどの小型精密部品を接続するためにレーザー溶接が使用されます。これらのコンポーネントは小さく、熱に非常に敏感であるため、温度制御が特に重要です。
- 過熱のリスク: 電子アセンブリのコンポーネントと回路は、温度上昇に非常に敏感です。溶接温度が高すぎると、回路基板の損傷やコンポーネントの溶接不良など、コンポーネントの損傷や性能低下を引き起こす可能性があります。そのため、過熱を避けるために、溶接中にレーザー出力を低くして熱入力を減らす必要があります。
- 低出力レーザーの使用: 部品への熱損傷を減らすために、電子機器製造業界では通常、低出力レーザーを使用し、レーザービームの焦点と溶接時間を正確に制御します。このような低出力溶接方法は、敏感な電子部品を損傷することなく、高品質の接続を実現できます。
- 温度上昇監視: 溶接中の正確な温度制御を確保するために、電子機器製造業界では通常、温度監視システムを使用して、溶接中の温度に関するリアルタイムのフィードバックを提供します。温度上昇を監視することで、レーザー出力または溶接速度が調整され、溶接温度が常に安全な範囲内に保たれます。
医療機器製造
医療機器の製造では、手術器具、インプラント、医療機器ハウジングなどの小さな部品を接続するために精密溶接技術が広く使用されています。これらの用途では、溶接精度と非汚染に対する要件が非常に高くなります。
- 精度要件: 医療機器の溶接部品は通常非常に小さく繊細なため、正確な温度制御が必要です。温度が高すぎると溶接部分が過熱し、材料が損傷したり、接合部が破損したりする可能性があります。これを回避するため、レーザー溶接では通常、低電力を使用し、ビームの焦点を正確に制御して、溶接点の温度を均一に保ちます。
- 無公害要件: 医療機器の溶接は、製品の品質に影響を与える汚染物質を避けるために、クリーンな環境で実行する必要があります。最終製品の安全性と衛生に影響を与える過度の温度による金属の酸化や有害ガスを避けるために、溶接温度を厳密に制御する必要があります。
- 適度な温度: 医療機器の精密溶接では、通常、溶接温度を適度な範囲に制御する必要があります。これにより、材料が完全に溶融することを保証する必要がありますが、過熱して材料の性能が低下しないようにする必要があります。適切な温度制御は、溶接接合部の強度と耐久性を高め、最終製品の信頼性と長期的な性能を保証します。
レーザー溶接は、応用分野によってそれぞれ独自の温度制御要件があります。自動車産業は溶接の強度と効率を重視し、航空宇宙産業は熱影響部の制御を重視し、電子機器製造は敏感な部品を保護するために低温溶接を重視し、医療機器製造は精密溶接と非汚染を必要とします。各産業の溶接温度制御戦略は、製品の品質と性能を確保するために、特定の材料特性と溶接目標に応じて正確に調整する必要があります。
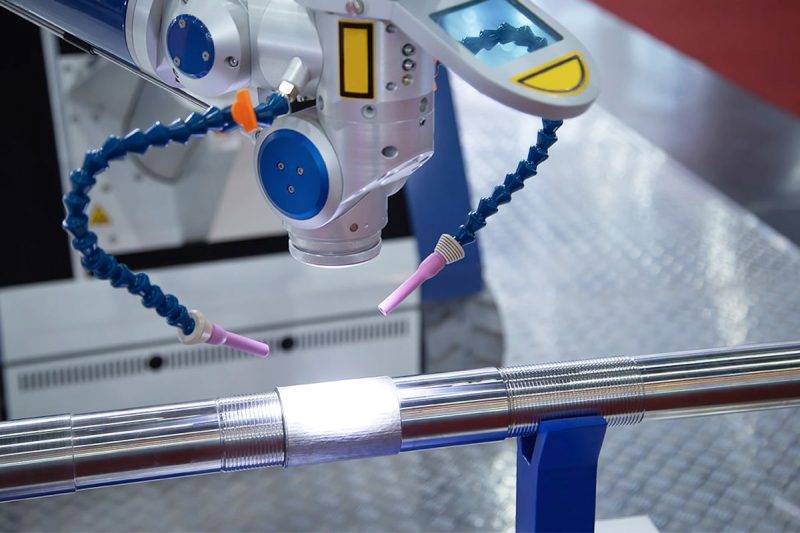
要約する
レーザー溶接は、自動車、航空宇宙、電子機器製造、医療機器など、さまざまな業界で広く使用されている高温、高精度の高度なプロセスです。このプロセスでは、レーザービームを高エネルギーの熱源として使用し、材料を迅速かつ効率的に溶かして強力な接合部を形成します。レーザー溶接の主な利点は、高精度と高速性であり、溶接品質に対する要件が厳しい多くの業界で広く使用されています。ただし、レーザー溶接の成功は、レーザービームの出力と材料の特性だけでなく、溶接プロセス中の温度の正確な制御にも依存します。温度が高すぎたり低すぎたりすると、溶接接合部の品質が損なわれ、気孔、亀裂、過度の燃焼、不完全な浸透などの欠陥が発生する可能性があります。したがって、温度制御は溶接品質を確保するための中核です。安定した温度制御システムを備えたAccTek Laserのレーザー溶接機は、より正確で信頼性の高い溶接体験をユーザーに提供し、業界の競争で際立つのに役立ちます。
高品質のレーザー溶接を実現するためには、プロセスパラメータを最適化し、適切な機器を選択し、監視フィードバックシステムを実装することが不可欠です。レーザー出力、溶接速度、焦点位置などのパラメータを調整することで、材料の特性と溶接要件に応じて熱入力を正確に制御できます。さらに、現代のレーザー溶接装置には通常、溶接プロセス中の温度変化に応じてパラメータを適時に調整できるリアルタイム監視システムが装備されており、溶接品質が常に最良の状態になるようにします。技術の継続的な進歩により、レーザー溶接の温度制御はより正確になり、ますます多くのハイエンド産業の溶接品質と性能のニーズを満たすことができます。将来、レーザー溶接技術が発展するにつれて、より多くの産業に効率的で信頼性の高い溶接ソリューションを提供し、製造業の進歩と革新を促進するでしょう。
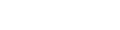
連絡先
- [email protected]
- [email protected]
- +86-19963414011
- No. 3 ゾーン A、Lunzhen 工業地帯、玉城市、山東省。
レーザー ソリューションを入手する