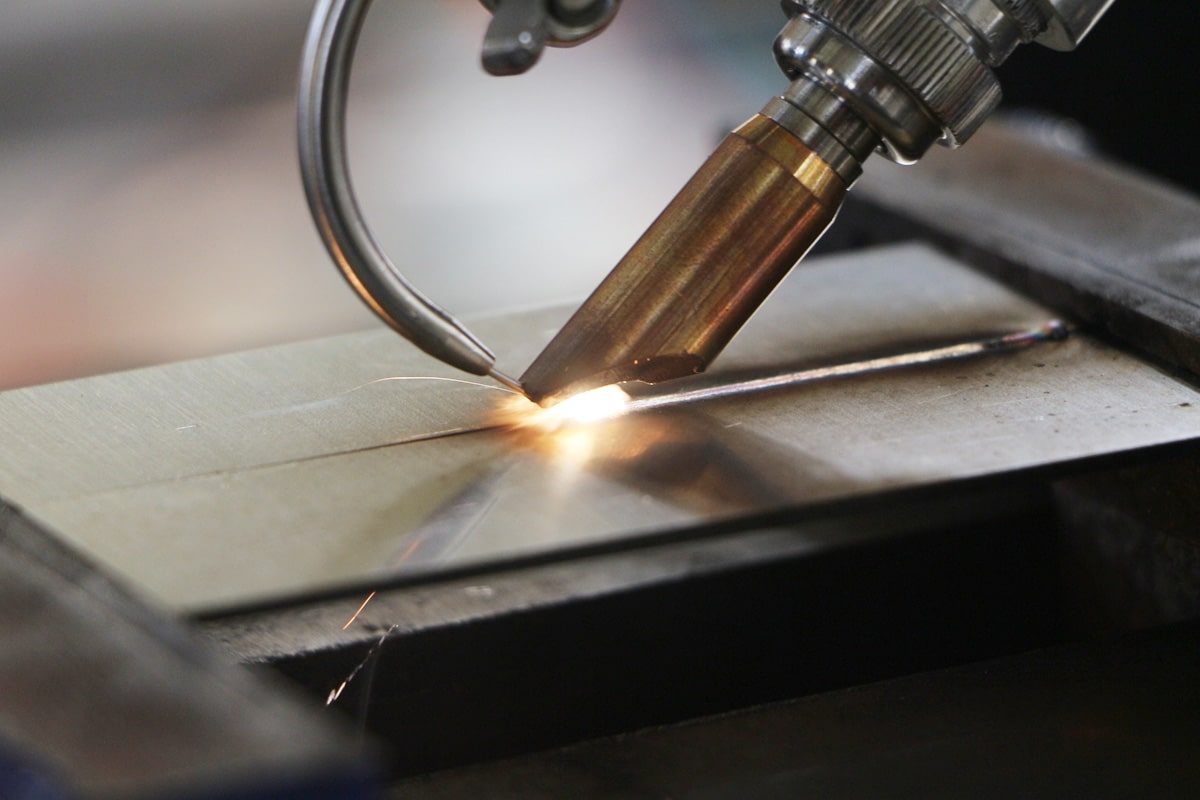
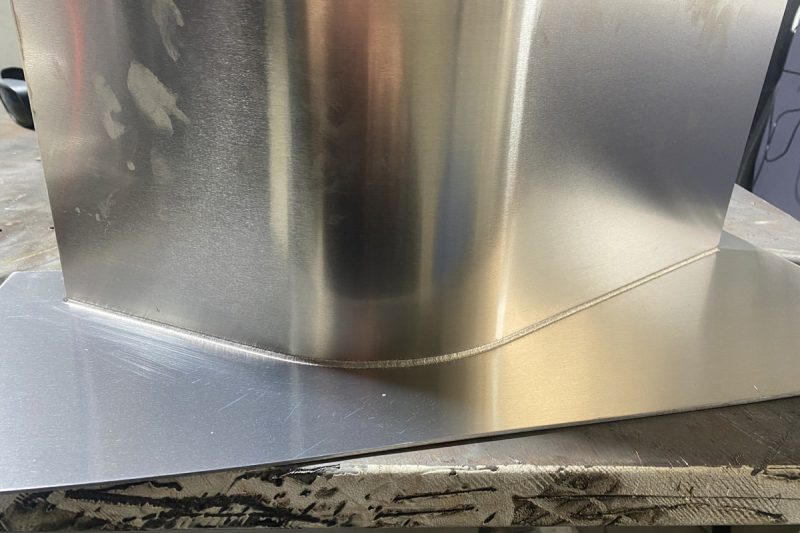
アルミニウム溶接の基礎
アルミニウムの特性
アルミニウムの独特な物理的特性により、溶接プロセスは鋼鉄などの他の金属とは大きく異なります。
- 高い熱伝導率: アルミニウムの熱伝導率は鋼鉄の約 4 倍です。つまり、溶接プロセス中に熱が溶接部全体に急速に広がり、効果的な溶接を行うために局所的に十分な熱を維持することが困難になります。
- 低融点:アルミニウムの融点は約 660°C で、鋼の融点よりもはるかに低いため、特に薄肉アルミニウムの場合、溶接時の過熱により金属の溶け落ちが発生しやすくなります。
- 酸化膜:アルミニウムは空気中で密な酸化膜(Al₂O₃)を形成しやすいです。この酸化膜の融点は2050℃と高く、アルミニウム自体の融点よりもはるかに高いです。この酸化膜を除去または処理しないと、溶接品質に影響を与え、溶接欠陥の原因となります。
- アルミニウムの強度対重量比: アルミニウムの密度は鋼鉄の 3 分の 1 しかありませんが、特に合金にすると強度が高くなります。このため、アルミニウムは自動車、航空宇宙、その他の業界で好まれる素材ですが、強度と軽量性の両方を考慮した溶接プロセスも必要です。
アルミニウム溶接の課題
- 熱処理の影響:アルミニウムは熱に敏感で、溶接時に発生する熱によって材料が弱くなる可能性があります。特に、熱処理によって強化されたアルミニウム合金の場合、溶接によって局所的な焼きなましが起こり、強度が低下します。
- 熱変形:アルミニウムは熱膨張係数が高いため、溶接時に熱変形が発生しやすくなります。特に広い面積を溶接する場合、加熱の不均一によりアルミニウム板が曲がったり変形したりすることがあり、溶接品質や完成品の精度に影響を及ぼします。
- 気孔と亀裂:アルミニウムを溶接する場合、溶融池は空気中の水素を吸収しやすく、溶接部に気孔が発生します。また、溶接中の急速な冷却により、溶接亀裂が発生する可能性があり、これは特にアルミニウム合金材料でよく見られます。
- 溶接表面処理:溶接前に、アルミニウム表面の酸化皮膜やその他の汚染物質を徹底的に除去する必要があります。適切に処理しないと、酸化皮膜が溶接部の融合に影響を与え、融合不足や気孔などの溶接品質の問題を引き起こす可能性があります。
適切な溶接技術の重要性
- 表面をきれいにする: 溶接する前に、機械的または化学的な方法を使用して、アルミニウム表面の酸化膜を必ず除去してください。これは、研磨または特別なクリーナーを使用して行うことで、溶接の品質を確保できます。
- レーザー溶接の利点: ファイバーレーザー溶接機 高精度と高効率を特徴とし、特にアルミニウムの溶接に適しています。レーザー溶接は、より安定した均一な溶接を提供し、熱影響部を減らし、溶接品質を向上させることができます。
- シールドガス: ファイバーレーザー溶接機のプロセスは従来の溶接方法とは異なりますが、シールドガスは依然として重要です。アルゴンまたはヘリウムを使用すると、溶接領域の酸化を効果的に防止し、溶接の清潔さと強度を確保できます。
- 溶接パラメータの最適化: アルミニウムを溶接する場合、溶接電流、電圧、溶接速度を正確に制御する必要があります。高電流で低速の溶接は過熱や材料の溶け落ちを引き起こす可能性があり、低電流で高速の溶接は浸透不足や溶接の不完全な融合を引き起こす可能性があります。
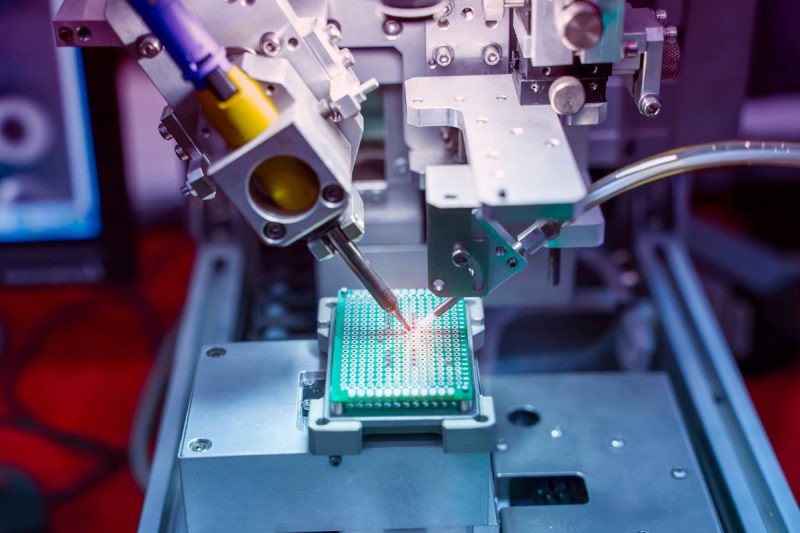
レーザー溶接の基礎
レーザー溶接の原理
- 高エネルギー密度: レーザー溶接の最大の特徴は、その高エネルギー密度です。つまり、短時間でもレーザービームは材料を溶かすのに十分な熱を生成できます。この高エネルギー密度により、溶接速度が向上するだけでなく、周囲の材料への熱の影響も軽減されます。
- 深溶融溶接と熱伝導溶接:レーザー出力密度の違いにより、レーザー溶接は深溶融溶接と熱伝導溶接に分けられます。深溶融溶接は通常、厚い材料の溶接に使用され、溶融深さが大きく、溶接強度が高いのに対し、熱伝導溶接は薄い材料に適しており、溶接速度が速く、溶接幅が狭く、熱影響部が小さいのが特徴です。
レーザー溶接プロセスの種類
レーザー溶接プロセスは主に以下のカテゴリに分類されます。
- 連続レーザー溶接:この溶接プロセスは、高い生産効率が求められるシナリオに適しています。溶接プロセス中にレーザービームが連続的に放射されるため、長い溶接部や厚い材料の溶接に適しています。その利点は、中断することなく均一な溶接品質を確保できることです。
- パルスレーザー溶接: パルスレーザー溶接は、薄い材料の溶接や精密溶接に適しています。溶接プロセス中、レーザー発生器はパルスの形でエネルギーを放出し、短時間の高エネルギーレーザービームを提供します。パルスレーザー溶接は、材料への熱影響を軽減できるため、溶接領域で高精度が求められるアプリケーションシナリオに適しています。
- ハイブリッドレーザー溶接:これはレーザー溶接と他の溶接プロセス(アーク溶接など)を組み合わせたプロセスであり、通常はより高い浸透深さを必要とする溶接に使用されます。ハイブリッドレーザー溶接は、レーザーの高エネルギー密度と従来の溶接の材料充填能力を組み合わせることで、より高い溶接強度と速度を実現します。
レーザー溶接の利点
現代の製造業でレーザー溶接が広く使用されているのは、さまざまな種類の工業用溶接における多くの利点によるものです。レーザー溶接プロセスの主な利点は次のとおりです。
- 高精度: レーザー溶接は非常に高い位置決め精度を実現できるため、航空宇宙や電子機器製造など、精密加工が必要な分野に特に適しています。
- 高い溶接強度: レーザー溶接は、深い溶け込み溶接特性により、優れた機械的特性を持つ溶接部を生成できます。溶接強度は通常、母材の強度に達するかそれを超えます。これは、需要の高いアプリケーション シナリオでは特に重要です。
- 熱影響部が小さい:レーザーエネルギーが集中し高速であるため、溶接時の材料の熱影響部が非常に小さく、材料の変形や熱損傷が軽減され、薄肉部品や精密部品の溶接に最適です。
- さまざまな材料に適応: レーザー溶接は、溶接が難しいアルミニウム、銅、ステンレス鋼など、ほぼすべての金属材料に使用できます。また、レーザーの波長と出力レベルを調整することで、さまざまな材料特性に適応することもできます。
- 高度な自動化: レーザー溶接プロセスは、自動化された生産ラインに簡単に統合でき、ロボットと組み合わせることで完全に自動化された操作を実現できます。これにより、生産効率が向上するだけでなく、溶接の一貫性と品質も保証されます。
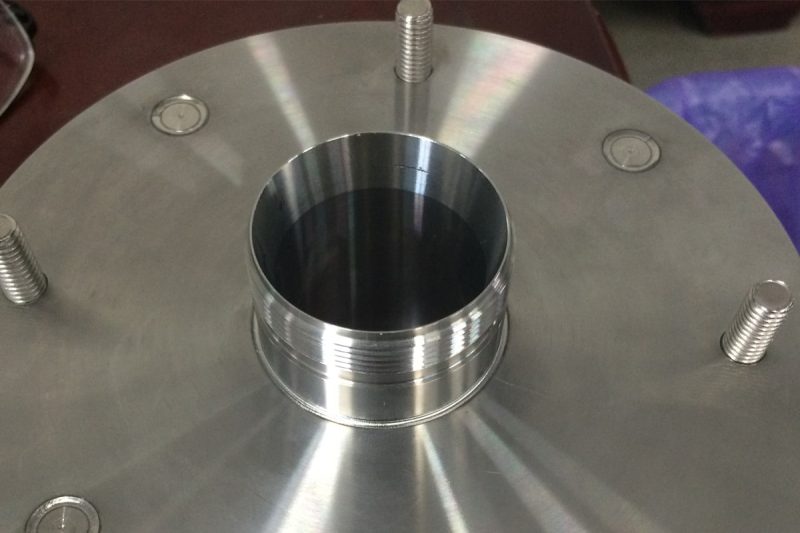
アルミニウムのレーザー溶接
レーザー光源と出力レベル
- レーザーの種類: ファイバーレーザージェネレーターは、小さな焦点で高い出力密度を生成できるため、アルミニウムの溶接の第一選択肢です。アルミニウムなどの反射率が高く、熱伝導率の高い材料に適しています。CO2レーザージェネレーターもアルミニウムの溶接に使用できますが、その波長はアルミニウムの表面反射率に似ており、通常はエネルギー損失が大きくなります。
- 電力制御:アルミニウムは熱伝導率が高いため、溶接中の熱が拡散しやすく、溶接箇所の熱が集中しにくくなります。そのため、アルミニウムをレーザー溶接する場合は、十分なエネルギーが溶接点に集中するように、通常、より高い電力が必要です。溶接の不均一や溶接箇所の過熱を防ぐために、電力制御を安定した範囲に保つ必要があります。
集束光学系とビーム伝送システム
- 光学システム: アルミニウムを溶接する場合、レーザービームを集束させるために高品質のレンズと反射鏡を使用する必要があります。集束光学系はレーザービームのエネルギーを非常に小さな領域に集中させ、材料表面のエネルギー密度を高め、アルミニウムを効果的に溶かすことができるようにします。
- ビーム伝送: レーザービームの高エネルギー密度を維持するために、ビーム伝送システムは良好な位置合わせと清潔な状態に保たれなければなりません。ビーム伝送プロセス中にエラーやエネルギー損失が発生すると、溶接品質に影響します。したがって、ビーム伝送システムの定期的な検査とメンテナンスが必要です。
保護ガスおよび雰囲気制御
アルミニウムのレーザー溶接では、シールドガスの選択と雰囲気制御が重要です。アルミニウムは高温で酸化されやすいため、溶接中にシールドガスを使用して酸化と気孔の形成を防ぐ必要があります。
- 一般的なシールドガス: アルゴンは、高温で不活性雰囲気を形成できるため、アルミニウムが空気中の酸素と反応するのを防ぎ、溶接部に酸化物層や気孔が形成されるのを防ぐことができるため、最も一般的に使用されるシールドガスです。ヘリウムも代替ガスとして使用できます。ヘリウムはアルゴンよりも軽く、酸化を誘発することなく溶接部をよりよくカバーできます。
- 雰囲気制御: シールドガスの流量と範囲を慎重に制御して、溶接プロセス全体にわたって均一な不活性雰囲気が形成されるようにする必要があります。ガス流量が高すぎたり低すぎたりすると、雰囲気が不均一になり、溶接品質に影響します。
表面の洗浄と準備
アルミニウムの表面は酸化しやすいため、溶接前の表面洗浄と準備は溶接品質を確保するための重要なステップです。アルミニウム表面の酸化層と汚染物質は溶接欠陥を引き起こす可能性があるため、適切な洗浄方法で除去する必要があります。
- 洗浄方法:アルミニウムの表面の酸化層と油汚れは、機械研磨、化学洗浄、またはサンドブラストによって除去できます。化学洗浄では通常、酸性またはアルカリ性の溶液が使用され、酸化層を効果的に除去できます。溶接の安定性と品質を向上させるには、溶接前に表面の汚染を最小限に抑える必要があります。
- 表面処理の重要性: アルミニウムの表面が適切に処理されていない場合、溶接中に気孔、亀裂、溶接強度不足などの問題が発生する可能性があります。表面処理が適切であれば、溶接プールの均一性が向上し、溶接欠陥を回避できます。
補助装置および付属品
アルミニウムのレーザー溶接では、補助装置と付属品の選択も同様に重要です。これらの装置には、溶接治具、溶接テーブル、冷却システムなどがあり、溶接プロセスのスムーズな進行に役立ちます。
- 溶接治具:アルミニウムは高温で変形しやすいため、溶接時に適切な治具を使用すると材料を固定し、変形を減らすことができます。高精度の治具を使用すると、溶接継手の位置合わせが確実になり、溶接時の位置誤差を減らすことができます。
- 冷却システム: 溶接中のアルミニウムの過熱を防ぐためには、冷却システムが不可欠です。冷却システムは、熱を素早く放散し、熱影響部の温度を下げるのに役立ち、それによって材料の変形や溶接欠陥を減らすことができます。
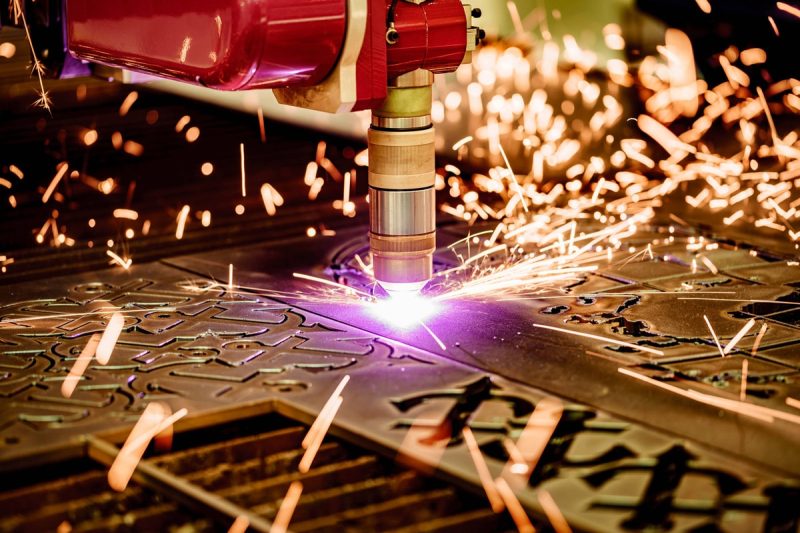
安全上の注意と注意事項
個人用保護具 (PPE)
レーザー溶接では高温、高輝度のレーザービームが発生し、金属の飛散や煙の発生を引き起こす可能性があるため、作業者は適切な個人用保護具(PPE)を装備する必要があります。
- レーザーゴーグル: 異なる波長のレーザーにはそれぞれ異なる危険性があり、レーザー光線が直接または反射して作業者の目に入ると、重大な損傷を引き起こす可能性があります。したがって、作業者は、レーザー放射による目の損傷を防ぐために、レーザーの種類に適した特別なレーザーゴーグルを着用する必要があります。
- 保護服と手袋: 溶接中に高温の金属が飛び散ると、皮膚に火傷を負う可能性があります。作業者は、溶接作業中の身体の安全を確保するために、耐熱性と耐火性のある保護服と手袋を着用する必要があります。
- マスクと呼吸保護具: レーザー溶接、特にアルミニウムやその他のコーティングされた材料を溶接する場合、有害なガスや煙が発生する可能性があります。作業者は、有害物質の吸入を避けるために適切な呼吸保護具を装備する必要があります。
換気と排気
レーザー溶接の際、材料の溶融とガス化により、大量の煙と、酸化アルミニウム粒子、一酸化炭素などの有毒ガスなどの有害ガスが発生します。これらの物質は、作業者の健康に有害であるだけでなく、環境を汚染します。
- 煙排出システム: 溶接中に発生する煙や有害ガスを作業エリアから速やかに排出するために、効率的な煙排出および換気システムを装備する必要があります。換気システムは、効率的に動作するように定期的に検査および保守する必要があります。
- フィルター装置: 煙排出システムには、空気中の粒子状物質や有害ガスを除去して、作業者や周囲の環境を汚染しないようにするための適切なフィルター装置を装備する必要があります。
設備の保守・点検
レーザー溶接装置は、安全な操作を確保し、潜在的な機械的故障を防ぐために、定期的なメンテナンスと検査が必要です。機械の摩耗、光学装置の汚染、またはレーザー光源の故障は、危険な事故につながる可能性があります。
- 光学システムのメンテナンス: レーザービームの伝送および集束システムは、定期的に清掃および調整する必要があります。レンズや反射鏡などの光学装置が汚れたり損傷したりすると、レーザービームが逸れたりエネルギーが失われたりして、溶接品質に影響を及ぼし、機器や作業員に危害を及ぼす可能性があります。
- 機器の検査: 溶接を行う前に、オペレーターはレーザー光源の冷却システム、電気接続、緊急停止ボタンなど、機器のすべての安全機能を点検し、機器が良好な状態であることを確認する必要があります。
安全上の考慮事項
レーザー溶接システムには、事故を回避するために異常な状況で直ちに操作を停止できるように、複数の安全機構が装備されている必要があります。
- 緊急停止ボタン:機器には緊急停止ボタンが装備されている必要があります。異常事態(機器の故障や操作ミスなど)が発生した場合、オペレーターは直ちに機器の操作を停止し、事故の拡大を防ぐことができます。
- 安全インターロック装置: レーザー溶接装置には通常、安全インターロックシステムが装備されており、装置のドアが開かれたときや作業者が作業エリアに入ったときにレーザー発生器が自動的にシャットダウンされ、誤操作による安全事故を防止します。
- 2 段階トリガー機構: レーザー溶接システムには通常、2 段階トリガー機構が備わっており、誤ってレーザーがトリガーされるのを防ぐために、レーザーを起動する前にオペレーターがシステムの準備ができていることを確認する必要があります。
- エリアの隔離と遮蔽:レーザー溶接作業エリアは、関係のない人が立ち入らないように適切に隔離する必要があります。また、レーザー遮蔽装置を使用すると、レーザービームの反射や散乱が周囲の環境に害を及ぼすのを防ぐことができます。
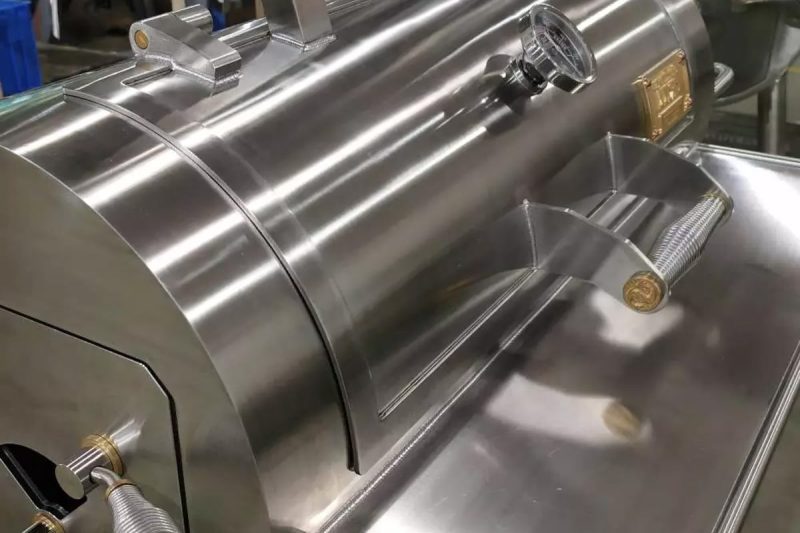
アルミニウムのレーザー溶接の応用
自動車産業
エレクトロニクス
航空宇宙
建物
消費財
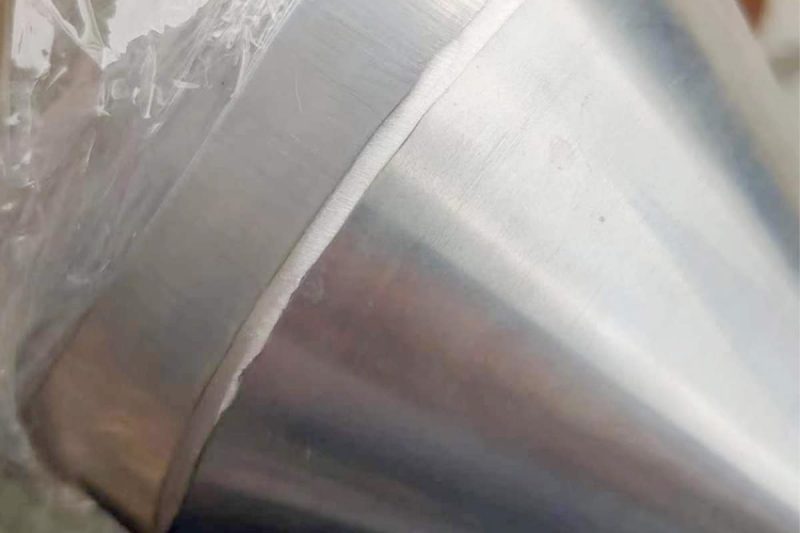
レーザー溶接アルミニウム技術とベストプラクティス
溶接パラメータと設定
レーザー溶接モード
よくある欠陥や問題を回避する
溶接後の洗浄と仕上げ
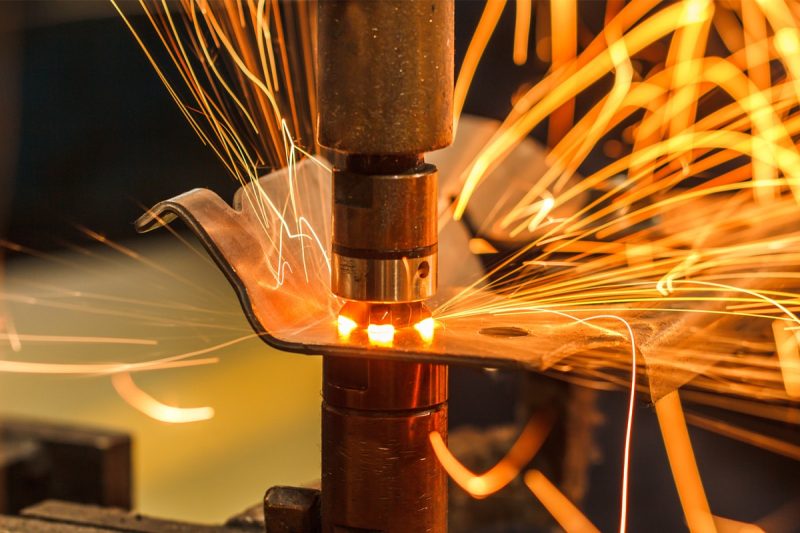
まとめ
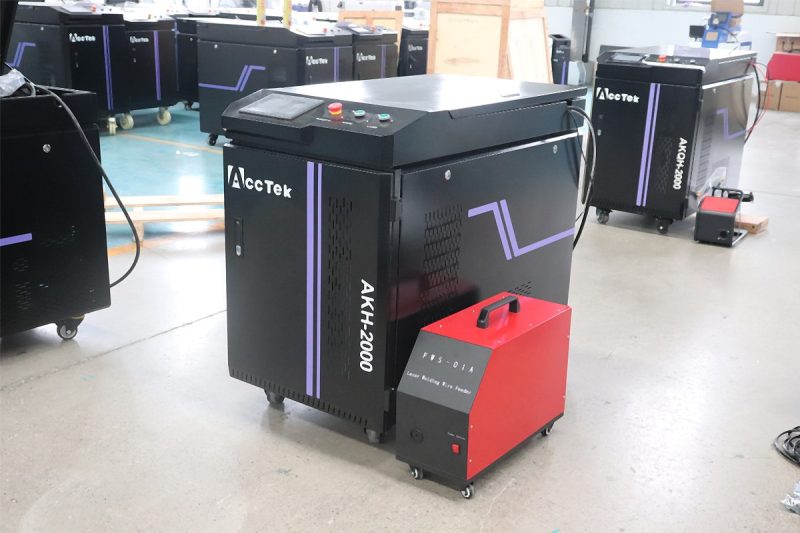
レーザー ソリューションを入手する
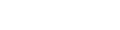
- [email protected]
- [email protected]
- +86-19963414011
- No. 3 ゾーン A、Lunzhen 工業地帯、玉城市、山東省。