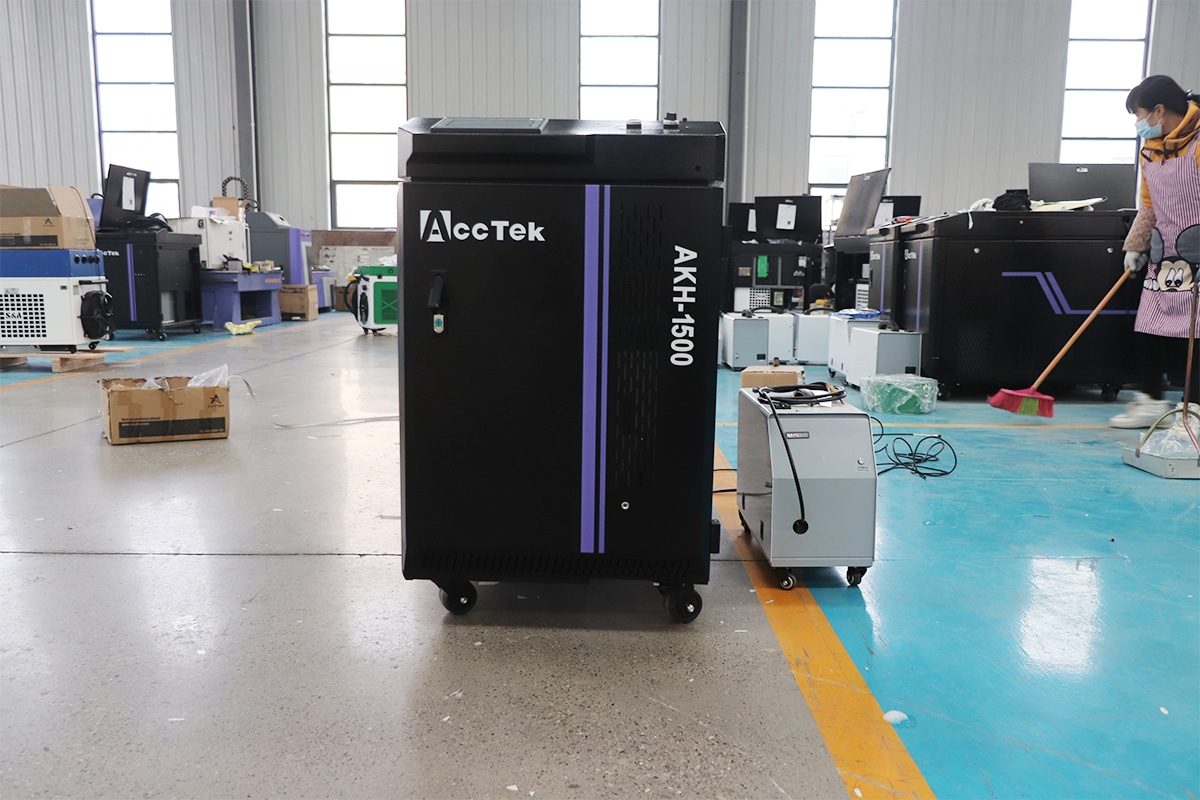
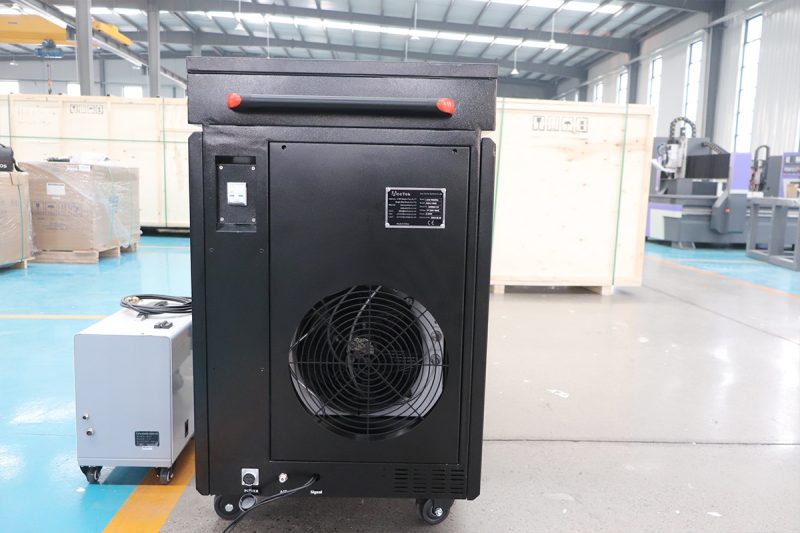
レーザー溶接のパワーを理解する
溶接におけるレーザーパワーの役割
レーザー出力は、通常ワット (W) またはキロワット (kW) で測定され、溶接される材料に供給されるエネルギーの量を決定します。出力設定は、溶接プロセスのいくつかの重要な側面に影響します。
- 浸透深さ: レーザー出力の主な機能の 1 つは、浸透深さを決定することです。出力レベルが高いほど、レーザーは材料のより深く浸透し、より厚い部分の溶接が可能になります。出力と浸透の関係は、通常、ある一定の点までは直線的ですが、それを超えると、ビーム品質や焦点などの他の要因が影響します。
- 溶接速度: レーザーの出力も溶接速度に影響します。出力が高いほど溶接速度が速くなり、大量生産環境に適しています。ただし、強力な溶接を確保するには、速度の増加と十分な浸透および熱入力のバランスをとる必要があります。
- 熱入力と熱管理: レーザー溶接では局所的な加熱が行われ、熱入力の量はレーザー出力に直接関係します。熱入力を管理することで、溶接の完全性と外観を損なう可能性のある過度の熱変形を回避できます。出力レベルが高い場合は、熱を放散してワークピースと周囲の過熱を防ぐための効率的な冷却システムが必要です。
- 溶接品質: 溶接品質はレーザー出力に大きく影響されます。出力が不十分だと不完全な融合が生じ、接合部が弱くなる可能性があります。一方、出力が多すぎると溶け落ちや過剰なスパッタが発生する可能性があります。適切な出力バランスを実現することで、きれいで強度があり、見た目にも美しい溶接を実現できます。
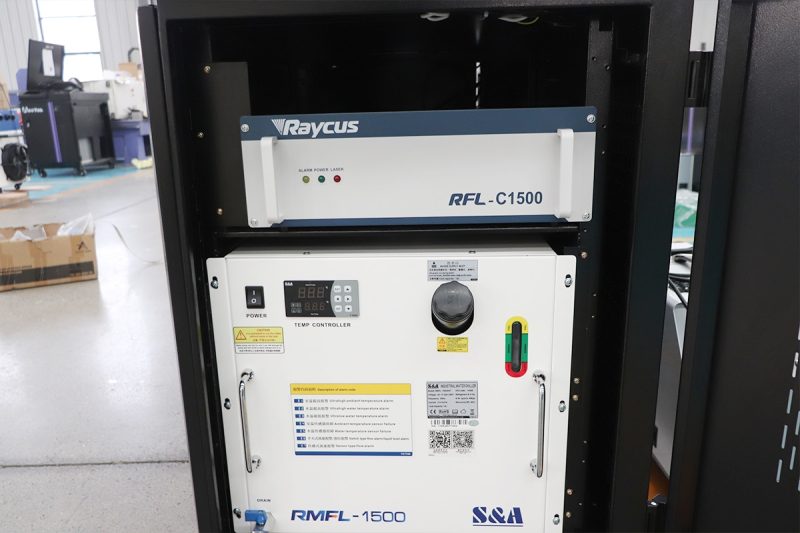
出力選択に影響する要因
材料の種類
材料はそれぞれ独自の物理的および化学的特性を持っているため、レーザー エネルギーに対する反応も異なります。材料の種類に関する主な考慮事項は次のとおりです。
- 吸収率と反射率: アルミニウムや銅などの材料は反射率が高く、吸収率が低いため、効果的な溶接を実現するにはより高いレーザー出力が必要です。対照的に、ステンレス鋼やチタンなどの材料はレーザーエネルギーをより効果的に吸収するため、より低い出力設定が可能です。
- 熱伝導率: 銅などの熱伝導率の高い材料は熱を急速に放散するため、適切な溶接の溶け込みと品質を維持するにはより高い電力が必要です。
材料の厚さ
溶接する材料の厚さは、必要なレーザー出力に正比例します。材料が厚いほど、十分な浸透と強力な溶接を実現するために、より多くの出力が必要になります。考慮すべき重要なポイントは次のとおりです。
- 浸透の深さ: 厚い部分を効果的に溶接するためには、レーザー ビームが十分に深く浸透するように、より高い出力レベルが必要です。
- マルチパス溶接: 非常に厚い材料の場合、熱入力を制御して熱歪みを最小限に抑えるために、シングルパスの高出力溶接よりも中出力レーザーによるマルチパス溶接の方が適している場合があります。
ジョイント構成
ジョイントの種類と構成は、レーザー溶接の電力要件に大きく影響します。一般的なジョイントの種類は次のとおりです。
- 突合せジョイント: レーザーが単一のインターフェースを貫通する必要があるため、これらのジョイントでは通常、他のジョイント タイプよりも必要な電力が少なくなります。
- ラップジョイント: 材料が重なり合うため、レーザーが貫通する厚さが増すため、より多くの電力が必要になります。
- T ジョイントとコーナー ジョイント: これらの構成では複雑な形状と複数のインターフェイスが含まれることが多く、一貫した溶接品質を実現するにはレーザー出力の正確な制御が必要です。
溶接速度
必要な溶接速度はレーザー出力を決定する重要な要素です。
- 高速溶接: 溶接速度が速いほど、レーザーと材料の間の相互作用時間が短くなり、十分なエネルギーが供給されるように、より高いレーザー出力が必要になります。
- 低速溶接: レーザーが材料にエネルギーを伝達する時間が長くなるため、より低い電力設定が可能になり、望ましい浸透と溶接品質が達成されます。
熱管理および冷却システム
効果的な熱管理により、熱による変形、材料の劣化、その他の熱関連の問題を防止します。
- 冷却システム: 高出力レーザーは大量の熱を発生するため、最適な動作温度を維持し、レーザー溶接機と材料の損傷を防ぐために強力な冷却システムが必要です。
- 熱影響部 (HAZ): 適切な熱管理により HAZ が最小限に抑えられ、溶接材料の機械的特性と完全性が維持されます。
ビーム品質と焦点
レーザービームの品質と焦点は、溶接プロセスの効率と精度に影響します。
- ビーム品質: 一貫した強度分布を持つ高品質のビームを使用すると、低品質のビームよりも低い電力レベルでより優れた溶接が可能になります。
- フォーカス制御: 正確なフォーカス制御により、レーザー エネルギーが溶接領域に集中し、効率が最大化され、電力要件が削減されます。
アプリケーション固有の要件
さまざまな業界やアプリケーションには、それぞれのニーズに基づいた独自の電力要件があります。
- 自動車産業: ボディパネルやフレームなどの薄い部品から中程度の厚さの部品を溶接する場合、十分な浸透と強度を得るためには通常 2 ~ 3 kW の範囲の電力レベルが必要です。
- 航空宇宙産業: チタンおよびニッケルベースの合金で作られた薄壁構造物や重要な部品を溶接する場合、精度を保ち、熱歪みを最小限に抑えるために、通常、1.5~2.5 kW の範囲の電力設定が必要です。
- 電子機器製造: 繊細な部品のマイクロ溶接では、精度を確保し、熱の影響を最小限に抑えるために、通常は 1 ~ 1.5 kW の低電力レベルが必要です。
- 医療機器製造: ステンレス鋼やチタンなどの生体適合性材料を溶接する場合、熱による損傷を最小限に抑えながら、きれいで高品質な溶接を行うために、通常、1.5~2.5 kW の範囲の電力レベルが必要です。
経済的考慮
経済的要因も電力出力の選択に影響します。
- 初期コストと長期的な節約: 一般的に、高出力レーザーは初期コストが高くなりますが、効率と品質の向上により、生産性の向上、サイクル時間の短縮、長期的なコストの節約につながります。
- 運用コスト: エネルギー消費や冷却システムのメンテナンスなど、より高い電力設定に関連する運用コストを考慮してください。
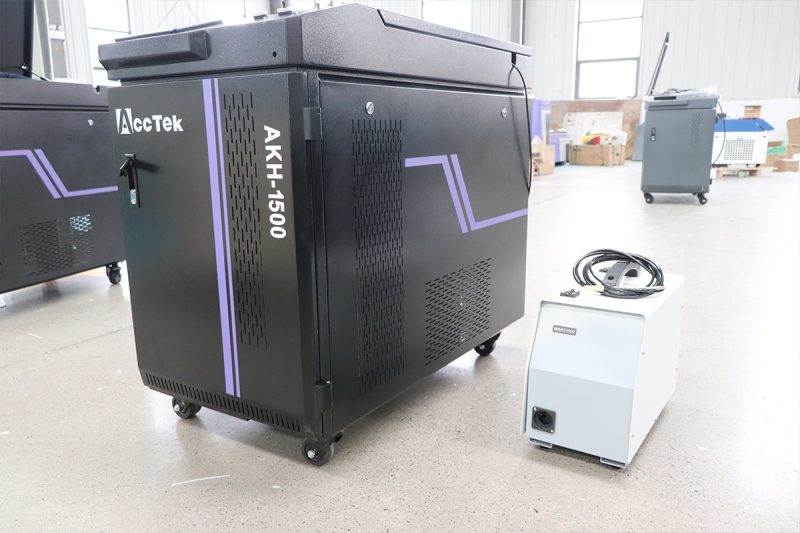
溶接プロセスにおける出力の影響
浸透深度
浸透深さは、レーザー出力によって影響を受ける最も重要な側面の 1 つです。これは、レーザー ビームが溶接対象の材料をどの程度深く溶かして結合できるかを示します。
- 高出力: 出力レベルが高いほど、より深い浸透が可能になり、より厚い材料を効果的に溶接できます。たとえば、3 kW で動作するレーザー溶接機は、最大 5 mm の厚さの材料を溶接するのに適した、大きな浸透深さを実現できます。
- 低~中出力: より薄い材料を溶接する場合は、低出力設定 (1~2 kW) で十分です。これらの設定では、材料を過度に貫通させることなく溶かして融合させるのに十分なエネルギーが得られるため、薄いシートや繊細な部品に最適です。
溶接速度
溶接の速度も、出力によって影響を受ける重要な要素です。一般的に、出力レベルが高いほど、溶接速度は速くなります。
- 高出力: 高速溶接が可能になり、生産性が向上し、サイクル時間が短縮されます。たとえば、3 kW レーザー溶接機は 1 kW レーザー溶接機よりも大幅に高速で溶接できるため、大量生産環境に最適です。
- 低~中出力: 低速溶接に適しており、高精度と制御を必要とする複雑な溶接作業に有利です。低速では、敏感な材料の欠陥のリスクも軽減されます。
熱の影響と熱管理
レーザー溶接では集中した熱が適用され、出力は溶接材料への熱効果に直接影響します。
- 高出力: より多くの熱を発生するため、熱影響部 (HAZ) が大きくなる可能性があります。これは、より深い浸透が必要でありながら、熱を管理し、熱による歪みや周囲の領域への損傷を防ぐために効果的な冷却システムを必要とする用途に適しています。
- 低~中出力: 発生する熱が少なくなり、HAZ が小さくなります。これは、材料の機械的特性を維持することが重要な薄い材料やコンポーネントの溶接に有効です。熱入力が低いため、反り、歪み、その他の熱問題のリスクが軽減されます。
溶接品質
溶接の品質は、レーザー出力によって左右される重要な結果です。溶接の一貫性、強度、外観などの要素はすべて、出力レベルによって影響を受けます。
- 高出力: 構造用途に適した強力で深い溶接を実現できます。ただし、過度の電力は、適切に管理しないと、スパッタ、多孔性、ひび割れなどの欠陥につながる可能性があります。高出力設定では、高品質の溶接を保証するために、正確な制御と最適化されたパラメータが必要です。
- 低~中出力: 溶接プロセスをより適切に制御し、きれいで正確な溶接を実現します。これは、電子機器や医療機器の製造など、高精度と美観が求められる用途にとって特に重要です。
素材の種類への適応性
さまざまな材料には独自の特性があり、さまざまな出力レベルでのレーザー溶接に対する反応に影響を与えます。
- 高出力: アルミニウムや銅など、反射率と熱伝導率の高い材料の溶接に不可欠です。これらの材料を適切に融合するには、より多くのエネルギーが必要です。
- 低~中出力: ステンレス鋼やチタンなど、レーザーエネルギーを効率的に吸収する材料に適しています。これらの材料は、低出力設定で効果的に溶接できるため、過熱や熱による損傷のリスクが軽減されます。
ジョイントの構成と複雑さ
ジョイント構成の複雑さによって、効果的な溶接に必要な出力も決まります。
- 高出力: 複数層の材料を貫通するために多大なエネルギーが必要となる、マルチパス溶接や厚い重ね継ぎなどの複雑な継ぎ目構成に適しています。
- 低~中出力: 強力な接合を実現するために少ないエネルギーしか必要としない、突合せ接合や薄い重ね接合などのより単純な接合に最適です。
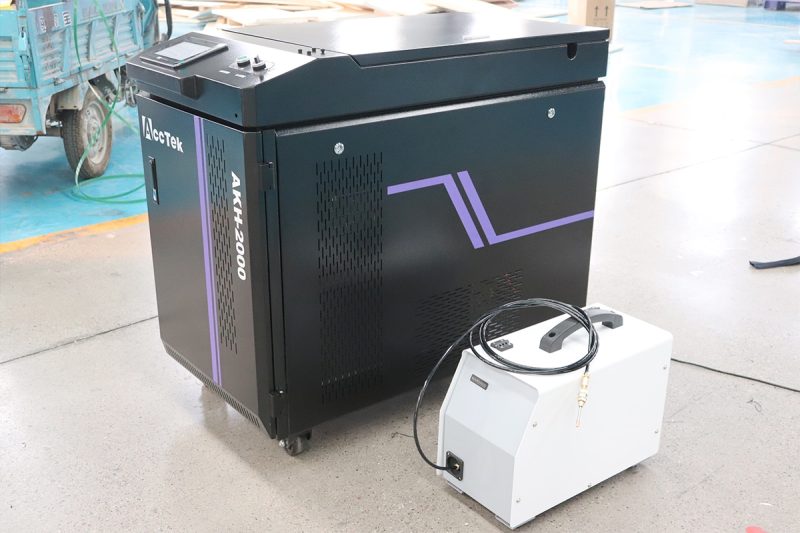
適切な出力を選択する方法
材料特性を評価する
適切な出力を選択するための最初のステップは、溶接する材料の特性を徹底的に理解することです。
- 材料タイプ: 材料のタイプ (鋼、アルミニウム、銅、チタンなど) と、反射率、熱伝導率、融点などの特定の特性を特定します。アルミニウムや銅などの反射率と熱伝導率の高い材料には、より高い電力レベルが必要です。
- 材料の厚さ: 材料の厚さを決定します。厚い材料では十分な浸透を得るために高い電力が必要ですが、薄い材料は低い電力設定で溶接できます。たとえば、厚さ 2 mm 未満の材料には 1 ~ 1.5 kW のレーザー溶接機が必要になる場合がありますが、厚さ 5 mm までの材料には最大 3 kW のレーザー溶接機が必要になる場合があります。
溶接要件の定義
次に、溶接アプリケーションの具体的な要件を概説します。
- ジョイント構成: ジョイントの種類 (突合せジョイント、重ねジョイント、T ジョイントなど) を考慮します。突合せジョイントは、必要な表面積と浸透深さが異なるため、一般的に重ねジョイントよりも必要な電力が少なくなります。
- 溶接速度: 希望する溶接速度を決定します。高速溶接アプリケーションでは、短時間で十分なエネルギーを供給するために、より高い電力が必要です。逆に、より低い電力設定でより遅い溶接速度を実現できるため、精密作業には有利です。
熱管理の必要性を評価する
適切な熱管理により欠陥を防ぎ、溶接品質を維持できます。
- 熱影響部 (HAZ): 許容できる HAZ のサイズを考慮してください。高電力設定では HAZ が大きくなり、熱影響を最小限に抑える必要がある用途では悪影響が生じる可能性があります。低電力設定では HAZ が小さくなり、材料の機械的特性が維持されます。
- 冷却システム: 特に高出力レベルで動作しているときは、溶接機に熱を放散するための適切な冷却システムがあることを確認してください。効率的な冷却により過熱を防ぎ、機械と材料の両方の完全性を維持します。
アプリケーション固有の要因を考慮する
業界や用途によって電力要件は異なります。
- 自動車産業: 厚い鋼鉄やアルミニウムの部品を溶接する場合、ボディパネルやフレームに深くて強い溶接を施すには、2~3 kW の電力レベルが必要になることがよくあります。
- 航空宇宙産業: 薄壁構造と重要なコンポーネントに、通常 1.5 ~ 2 kW の電力設定を使用して、正確で高品質の溶接が必要です。
- 電子機器製造: 繊細な部品のマイクロ溶接には、精度と熱の影響を最小限に抑えるために、通常 1 ~ 1.5 kW の低電力レベルが必要です。
- 医療機器製造: ステンレス鋼やチタンなどの生体適合性材料を溶接する場合、熱による損傷を最小限に抑えながら、きれいで高品質な溶接を実現するために、1.5~2 kW の範囲の電力設定が必要になることがよくあります。
材料試験を実施する
サンプル材料をテストすることで、最適な電力設定を決定することができます。
- 試し溶接: さまざまな電力設定を使用して試し溶接を実行し、結果を観察します。溶接品質、溶け込み深さ、HAZ の範囲を分析します。
- パラメータの最適化: 試し溶接の結果に基づいて、電力、速度、フォーカスなどの溶接パラメータを微調整します。この反復プロセスは、特定のアプリケーションに最適な電力設定を特定するのに役立ちます。
専門家に相談する
レーザー溶接の専門家と機器メーカーの専門知識を活用します。
- 製造元の推奨事項: レーザー溶接機の製造元に問い合わせて、アプリケーション要件と材料特性に基づいた推奨事項を入手してください。
- 業界の専門家: 同様のアプリケーションの経験を持つ業界の専門家と連携してください。彼らの洞察は、適切な出力を選択し、溶接プロセスを最適化する上で貴重なガイダンスを提供します。
経済的考慮を評価する
電力選択による経済的影響を考慮してください。
- 初期投資: 出力の高いレーザーは、通常、初期コストが高くなります。生産性の向上と長期的な節約の可能性を考慮して、投資収益率を評価します。
- 運用コスト: 電力設定を高くすると、エネルギー消費量とメンテナンス コストが増加する可能性があります。これらのコストと、溶接速度の向上と溶接品質の向上によるメリットとのバランスを取ってください。
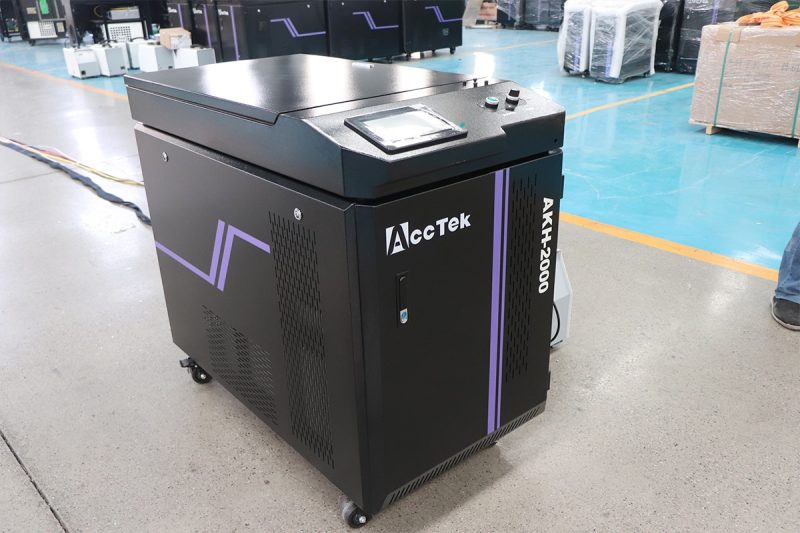
アプリケーション固有の考慮事項
自動車産業
自動車業界では、ボディパネル、構造部品、パワートレイン要素などの部品の製造にレーザー溶接が広く使用されています。この業界の主な考慮事項は次のとおりです。
- 材料の種類: 一般的な材料には鋼鉄やアルミニウムがあり、反射率や熱伝導率は異なります。これらの材料を効果的に溶接するには、通常 2 ~ 3 kW のより高い電力レベルが必要です。
- 材料の厚さ: 自動車部品には、深い溶け込みを必要とする厚い材料が使用されることがよくあります。2 ~ 3 kW の出力により、厚い部分を溶接するのに十分な深さと強度が確保されます。
- 溶接速度: 大量生産環境で生産性を維持するには、高速溶接が不可欠です。出力が高ければ溶接速度が速くなり、サイクル時間が短縮され、スループットが向上します。
- ジョイントの種類: 突合せジョイント、重ねジョイント、T ジョイントが一般的です。ジョイントの種類ごとに必要な電力レベルが異なりますが、重ねジョイントでは材料の重なりが大きくなるため、一般的により多くの電力が必要になります。
航空宇宙産業
航空宇宙産業では、機体、エンジン部品、燃料タンクなどの部品の製造にレーザー溶接が使用されているため、溶接精度と溶接品質が非常に重要です。
- 材料の種類: 航空宇宙材料にはチタン、アルミニウム、ニッケルベースの合金があり、それぞれきれいで正確な溶接を実現するために特定の電力設定が必要です。これらの材料の場合、1.5~2.5 kW の電力レベルで十分な場合がよくあります。
- 薄壁構造: 多くの航空宇宙部品は薄壁であるため、過度の熱入力や歪みを防ぐために電力レベルを低く抑える必要があります。慎重な電力管理により、構造の完全性を維持できます。
- 品質と一貫性: 高品質で欠陥のない溶接が不可欠です。一貫した溶け込みと最小限の欠陥を達成し、熱入力を正確に制御するには、電力設定を最適化する必要があります。
- 複雑な形状: 航空宇宙部品は多くの場合、複雑な形状と厳しい許容誤差を特徴としています。溶接品質を損なうことなく、これらの複雑さに対応するには、電力レベルを調整する必要があります。
電子機器製造
エレクトロニクス業界では、回路基板、コネクタ、マイクロエレクトロニクスなどの繊細な部品の組み立てにレーザー溶接が採用されています。
- 材料の種類: 一般的な材料には、銅、金、さまざまな合金などがあります。これらの材料は薄く、導電性が高いため、通常は低い電力レベル (1 ~ 1.5 kW) が必要です。
- マイクロ溶接: マイクロ溶接作業では精度が重要であり、敏感な部品の損傷を防ぐためにレーザー出力を細かく制御する必要があります。低出力設定により、必要な精度を維持できます。
- 熱感度: 電子部品は熱に敏感な場合が多く、損傷を防ぐためには最小限の熱入力が必要です。電力設定を低くすると、これを実現でき、部品の機能性と信頼性が維持されます。
- 高精度: 熱影響部を最小限に抑えながら高精度を実現することが不可欠です。熱影響を最小限に抑えて、きれいで正確な溶接を実現するには、電力設定を最適化する必要があります。
医療機器製造
レーザー溶接は、医療機器業界で、手術器具、インプラント、診断装置などの部品を製造するために広く使用されています。
- 材料の種類: ステンレス鋼、チタン、特定のポリマーなどの生体適合性材料が一般的です。これらの材料には通常、1.5~2.5 kW の範囲の電力レベルが必要です。
- 無菌性と清潔さ: 医療機器には、汚染が最小限に抑えられた無菌で清潔な溶接が必要です。出力設定により、飛散と酸化が最小限に抑えられた、滑らかで高品質な溶接が保証される必要があります。
- 精度と制御: 医療機器の機能性と安全性を維持するには、高精度が不可欠です。低から中程度の電力設定により、溶接プロセスを正確に制御できます。
- 薄壁コンポーネント: 多くの医療機器には薄壁コンポーネントが採用されており、過度の熱入力や歪みを避けるために慎重な電力管理が必要です。
ジュエリーと時計製造
レーザー溶接は、宝石や時計製造業界でも繊細な部品の組み立てや修理に利用されています。
- 材料の種類: 一般的な材料には、金、銀、プラチナ、およびさまざまな貴金属合金が含まれます。これらの材料は薄く、反射率が高いため、必要な電力レベルが低くなることがよくあります (1 ~ 1.5 kW)。
- 繊細な部品: 小さくて複雑な部品を扱うには精度が重要です。低電力設定にすると、部品を損傷することなく必要な精度を実現できます。
- 美観品質: 溶接はきれいで見た目も美しくなければなりません。飛散や変色を最小限に抑え、高品質の仕上がりを確保するには、電力設定を最適化する必要があります。
- 熱感度: 貴金属は熱に敏感なので、素材の変形や損傷を防ぐためには最小限の熱入力が必要です。電力設定を低くすると、コンポーネントの完全性を維持するのに役立ちます。
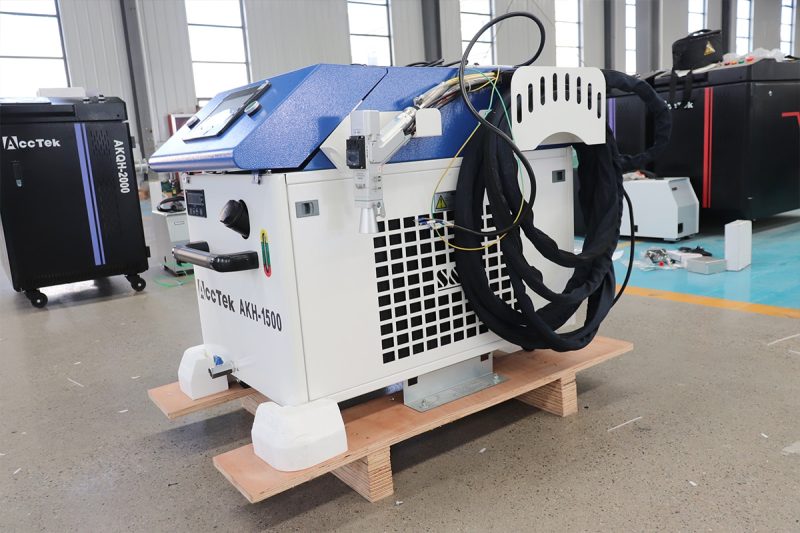
まとめ
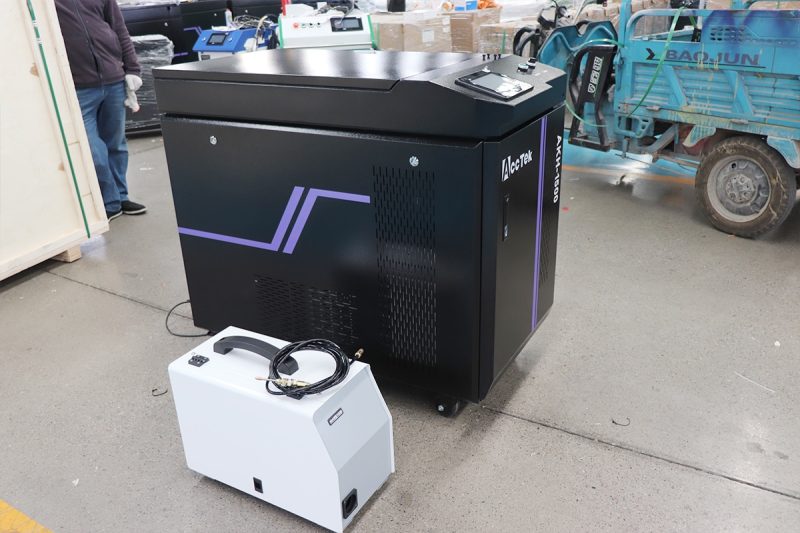
レーザー溶接ソリューションを入手
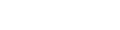
- [email protected]
- [email protected]
- +86-19963414011
- No. 3 ゾーン A、Lunzhen 工業地帯、玉城市、山東省。