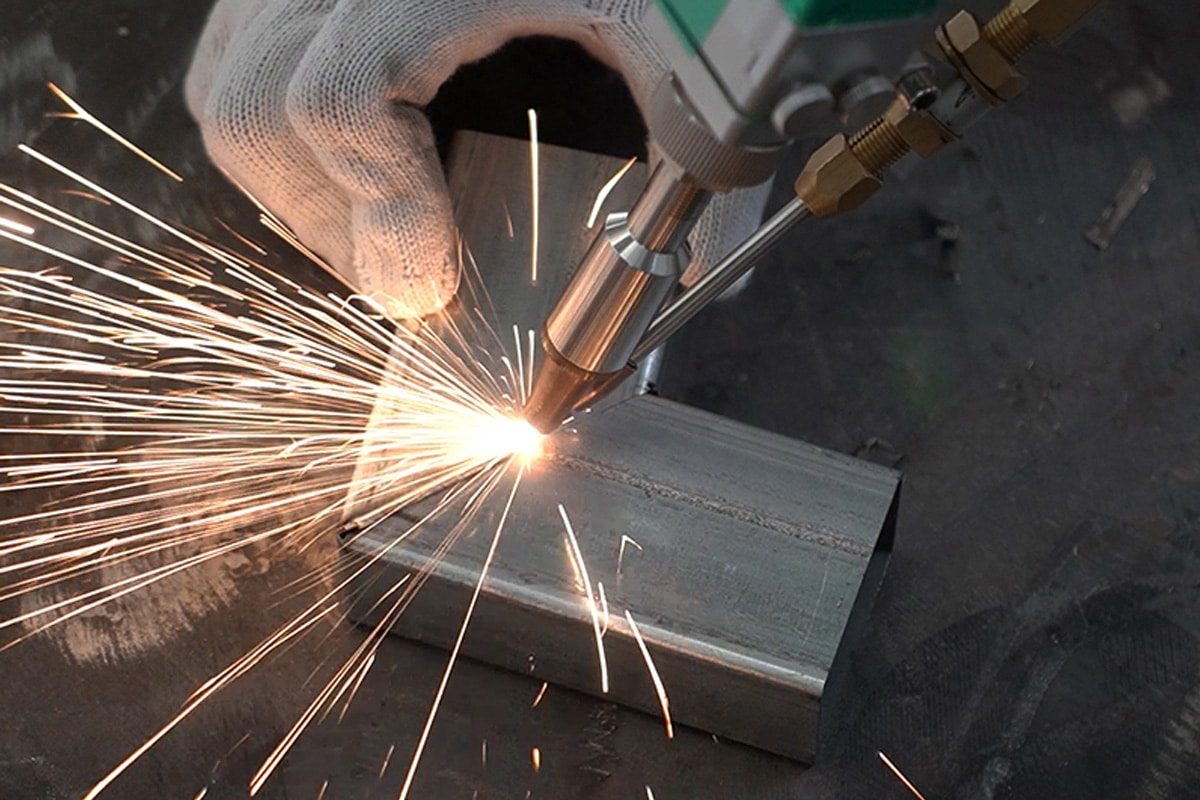
効率的で精密な溶接技術として、レーザー溶接は現代の製造業で広く使用されています。レーザービームを熱源として使用し、レーザージェネレーターが高エネルギー密度のレーザービームを放射して材料を溶かして接続します。従来の溶接方法(ガスメタルアーク溶接(GMAW / MIG)、ガスタングステンアーク溶接(GTAW / TIG)、シールドメタルアーク溶接(SMAW)、フラックス入りアーク溶接(FCAW))と比較して、レーザー溶接には、溶接プロセスの高精度と高効率、熱影響部が小さいなど、多くの独自の利点があります。ただし、レーザー溶接の効果と品質は多くの要因の影響を受けますが、その中で材料の厚さは重要な要素です。この記事では、材料の厚さがレーザー溶接の選択にどのように影響するかについて説明します。 レーザー溶接機 パラメータを設定し、さまざまな材料の厚さに合わせた最適化方法を提供します。
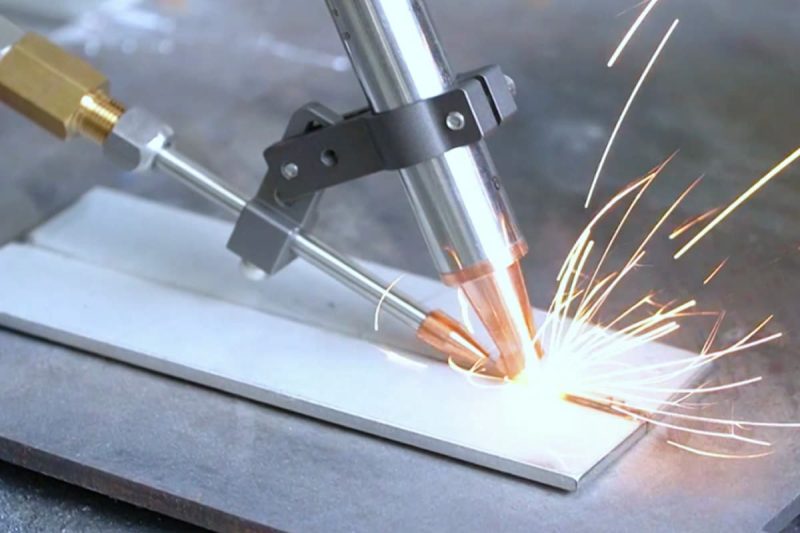
レーザー溶接の基礎
レーザー溶接プロセスの説明
レーザー溶接は、レーザービームを熱源として使用し、金属やその他の材料を溶かして接合する溶接プロセスです。このプロセスには、次の手順が含まれます。
- レーザービームの焦点合わせ: レーザー発生器から放射されたレーザービームは、光学系を介して溶接ヘッドに焦点を合わせられます。
- 材料の加熱: レーザー ビームの高エネルギー密度により、材料が融点まで加熱され、局所的に溶融または気化します。
- 溶融プールの形成: 溶融した材料は溶融プールを形成し、レーザービームの継続的な作用により溶融プールは液体のまま維持されます。
- 凝固と接続: レーザービームが移動または停止すると、溶融池が冷却されて凝固し、溶接プロセスが完了します。
レーザー溶接プロセスには、熱伝導溶接とキーホール溶接の 2 種類があります。
- 熱伝導溶接:レーザービームは材料の表面を材料の融点以上に加熱し、溶接表面のみに溶融を生じ、ワークピースの内部は完全には浸透せず、基本的に蒸発は発生しません。このプロセスは主に薄肉材料の溶接に使用されます。熱伝導溶接は滑らかで美しい溶接を生み出します。
- キーホール溶接:キーホール溶接では、レーザービームが材料の表面を蒸発点まで加熱し、材料に浸透します。材料が蒸発して小さな穴が形成されます。蒸気で満たされた穴は、入射ビームのエネルギーをほぼすべて吸収します。穴内の平衡温度は約2500℃です。熱は高温の穴の外壁から伝達され、穴の周りの金属を溶かします。キーホールは、ビームの照射下で材料が継続的に蒸発することによって生成された高温の蒸気で満たされています。レーザービームは穴に連続的に入り、穴の外側の材料は連続的に流れます。ビームが移動すると、穴は常に安定した流動状態になります。つまり、小穴と穴壁の周りの溶融金属は、ビームの速度で前方に移動します。溶融金属は、小穴の移動によって残された隙間を埋め、その後凝縮して溶接部を形成します。
レーザー溶接システムの主要コンポーネント
レーザー溶接システムの主要コンポーネントは次のとおりです。
- レーザー発生器: レーザーエネルギーを生成して放出します。一般的なレーザー発生器には、ファイバー レーザー発生器、ガス レーザー発生器などがあります。
- 光学システム: レーザービームを調整および焦点を合わせるための焦点レンズとミラーが含まれます。
- レーザー伝送システム:レーザー光源から溶接位置までレーザービームを伝送するシステム。
- 溶接ヘッド: 実際の溶接作業用のレーザー集束ミラー、コリメートミラー、保護ガスノズルが含まれています。
- 制御システム: レーザー出力、溶接速度など、レーザー溶接のさまざまなパラメータを制御するために使用されます。
従来の溶接方法と比較したレーザー溶接の利点
溶接品質
- レーザー溶接の熱影響部は小さく、レーザービームのエネルギー密度が高く、加熱時間が短く、熱損失が少ないため、材料の熱影響部が小さくなり、材料の変形、ひび割れ、酸化などの問題を軽減できます。
- レーザー溶接の溶接部の深さと幅の比率は高く、レーザービームの直径が小さく、エネルギーが集中しているため、深く狭い溶接部を形成でき、溶接部の強度と密閉性が向上します。
- レーザー溶接の溶接は、レーザービームのスポットが安定しており、溶接位置とパラメータを正確に制御できるため、滑らかで美しい溶接を形成でき、その後の研磨や磨きを減らすことができます。
- レーザー溶接では、電極、溶接棒、シールドガスなどの補助材料を使用する必要がないため、電極汚染、気孔、スラグ混入、割れなどの溶接欠陥の発生を回避でき、溶接欠陥が少なくなります。
溶接効率
- レーザー溶接は溶接速度が速く、レーザービームのエネルギー密度が高く、加熱時間が短いため、溶接工程を素早く完了でき、生産効率が向上します。
- レーザー溶接は溶接の柔軟性が高く、レーザービームは非接触熱源であるため、光ファイバー、反射鏡、ロボットなどによって伝送および制御できるため、さまざまな複雑な溶接位置や形状に適応でき、生産の柔軟性が向上します。
- レーザー溶接は溶接の自動化度が高く、コンピューターやCNCシステムによって正確に制御・調整できるため、高度な自動化とインテリジェンスを実現し、手動介入やエラーを削減できます。
溶接アプリケーション
- レーザー溶接は、非接触熱源であるため、材料適応性が強く、さまざまな金属や非金属材料を溶接でき、異なる種類の材料を溶接して異種材料の接続も実現できます。
- レーザー溶接は、その熱源が効率的な熱源であり、高品質、高速、高度に自動化された溶接を実現できるため、産業適応性が強く、航空宇宙、自動車、電子機器、医療など、さまざまなハイエンド産業に適用できます。
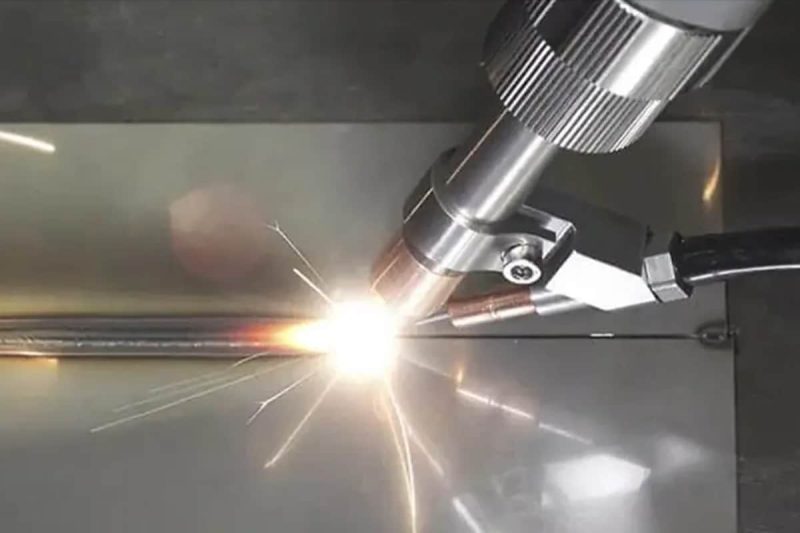
材料の厚さが溶接パラメータに与える影響
レーザーパワー
パルス持続時間と周波数
溶接速度
フォーカス位置
ビーム径
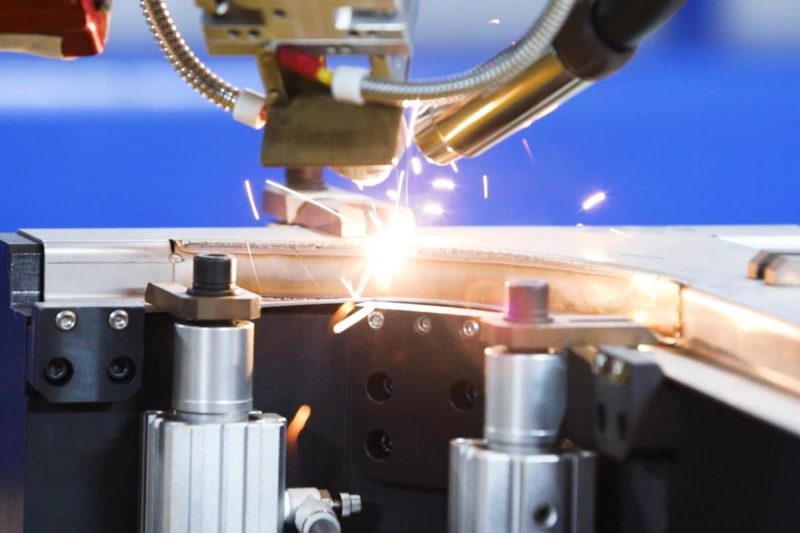
異なる材料の厚さに合わせたレーザー溶接パラメータの最適化
薄い材料(<1mm)
- レーザー出力: 過熱や過度の溶融を避けるため、低いレーザー出力を選択する必要があります。通常は数十ワットから数百ワットの範囲で選択します。
- パルス持続時間と周波数: パルス持続時間が短く、周波数が高いほど、加熱と冷却のサイクルが速くなり、熱の影響が軽減されます。
- 溶接速度: 溶接速度を上げると、生産効率が向上し、過熱を防ぐことができます。
- 焦点位置: 最良の溶接効果を得るには、レーザーの焦点を材料の表面近くに設定する必要があります。
- ビーム径: より小さなビーム径を使用すると、溶接の精度と詳細な制御が向上します。
中厚素材(1mm~5mm)
- レーザー出力: 溶接の深さと品質を確保するには、適度なレーザー出力を選択する必要があります。通常は、数百ワットから数キロワットの範囲で選択します。
- パルス持続時間と周波数: 特定の材料の厚さに応じて、加熱効果と冷却効果のバランスをとるために中程度のパルス持続時間と周波数を選択します。
- 溶接速度: 溶接品質と生産効率を確保するために、材料の厚さに応じて適度な溶接速度を選択する必要があります。
- 焦点位置: 溶接の深さと均一性を確保するために、レーザーの焦点を材料の中央に設定する必要があります。
- ビーム径: エネルギー分布と溶接精度のバランスをとるために、適度なビーム径を選択します。
厚い素材(>5mm)
- レーザー出力: 溶接の深さと品質を確保するために十分な熱入力を提供するには、より高いレーザー出力を選択する必要があります。通常は数キロワットの範囲で選択します。
- パルス持続時間と周波数: パルス持続時間が長く、周波数が低いほど、より厚い材料を溶かすのに十分な熱入力が得られます。
- 溶接速度: レーザービームが材料を効果的に貫通して溶かすことができるように、より遅い溶接速度を選択する必要があります。
- 焦点位置: レーザービームが効果的に材料を貫通して溶かすことができるように、レーザー焦点を材料の内側に設定する必要があります。
- ビーム径: 十分なエネルギー密度と溶接深度を確保するには、より大きなビーム径を使用します。
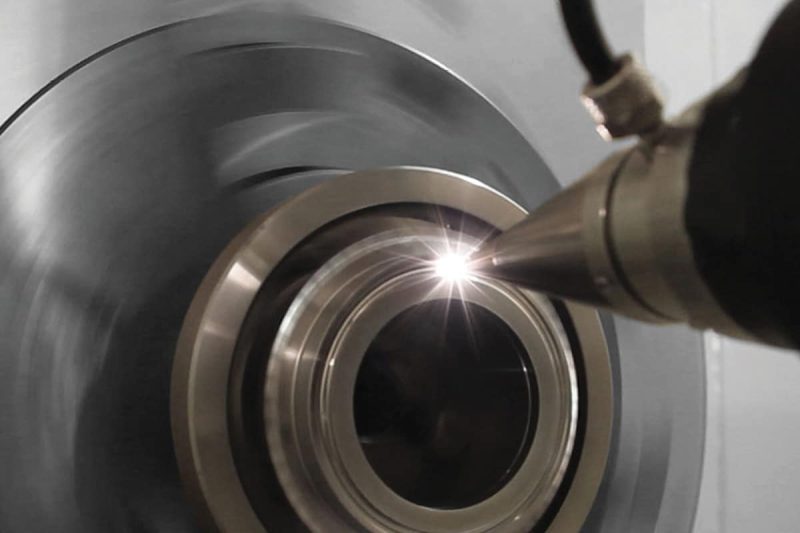
要約する

レーザー ソリューションを入手する
適切なレーザー溶接機を選択すると、電力消費を最適化し、高い運用効率を実現できます。信頼できるサプライヤーと協力することで、高度なテクノロジー、カスタマイズされたアドバイス、継続的なサポートを利用できます。AccTek Laserでは、さまざまな産業ニーズを満たすように設計された包括的なレーザー溶接機器を提供しています。当社の専門家は、材料の種類、厚さ、生産量などの要素を考慮して、最もエネルギー効率の高いモデルと構成を選択するお手伝いをします。また、高効率レーザージェネレーター、インテリジェント冷却システム、エネルギー管理ソフトウェアなどの最先端の機能を提供し、パフォーマンスを最大化し、エネルギー使用量を最小限に抑えます。さらに、当社のチームは定期的なメンテナンスサービスと技術サポートを提供し、機器を最高の効率に保ちます。当社と提携することで、大幅なエネルギー節約、運用コストの削減、持続可能性への取り組みの強化を実現できます。ご質問がある場合は、すぐにご連絡ください。AccTek Laserは、すべてのお客様に完璧なレーザーソリューションを提供することに尽力しています。
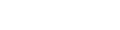
- [email protected]
- [email protected]
- +86-19963414011
- No. 3 ゾーン A、Lunzhen 工業地帯、玉城市、山東省。