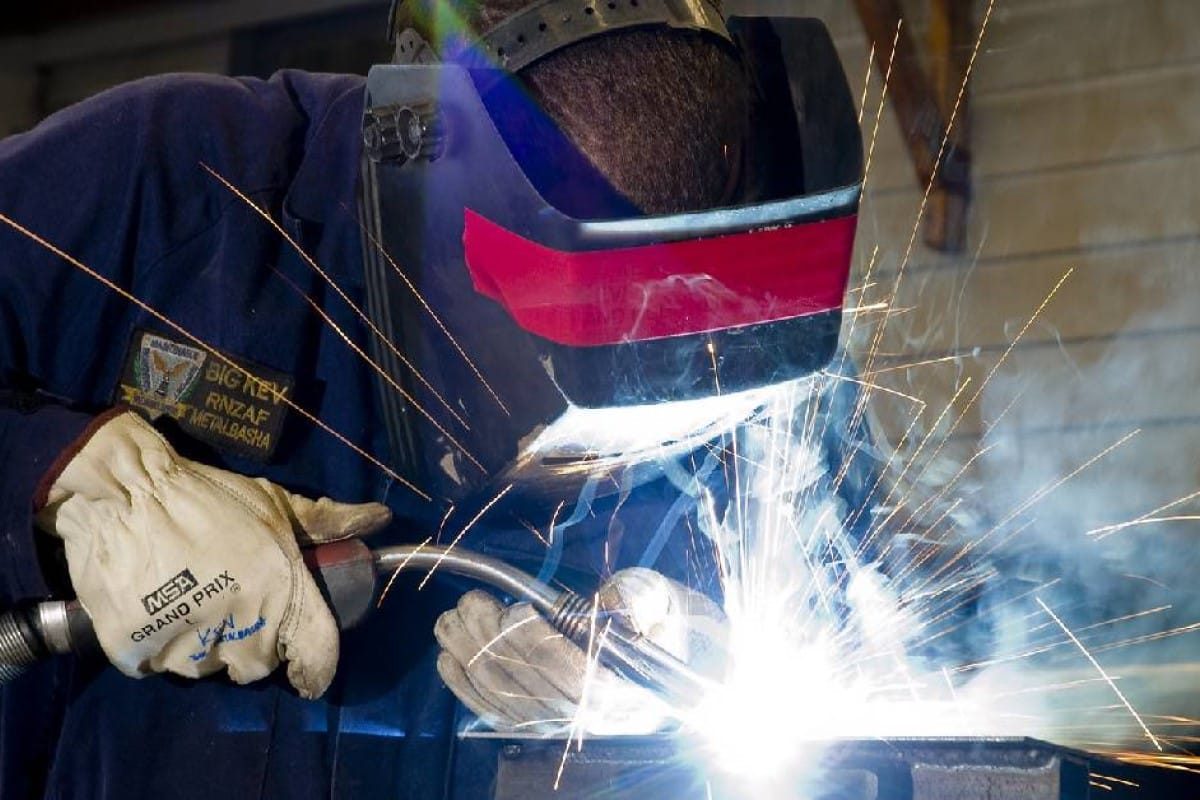
溶接方法の比較: 最適なパフォーマンスを明らかにする
現代の産業において、溶接は金属部品を結合するために使用される重要なプロセスです。さまざまな溶接方法がさまざまな用途で重要な役割を果たします。溶接強度を左右する要素には、溶接材料、作業者のスキル、溶接の長さや大きさなどに加えて、溶接方法も溶接強度を決める要素の1つです。
この記事では、レーザー溶接、タングステン不活性ガス溶接、金属不活性ガス溶接、被覆金属アーク溶接、サブマージアーク溶接、抵抗スポット溶接などのいくつかの一般的な溶接方法を比較し、その動作原理を理解し、どの溶接方法が最も優れた性能を備えているかについて説明します。傑出したパフォーマンス。
目次
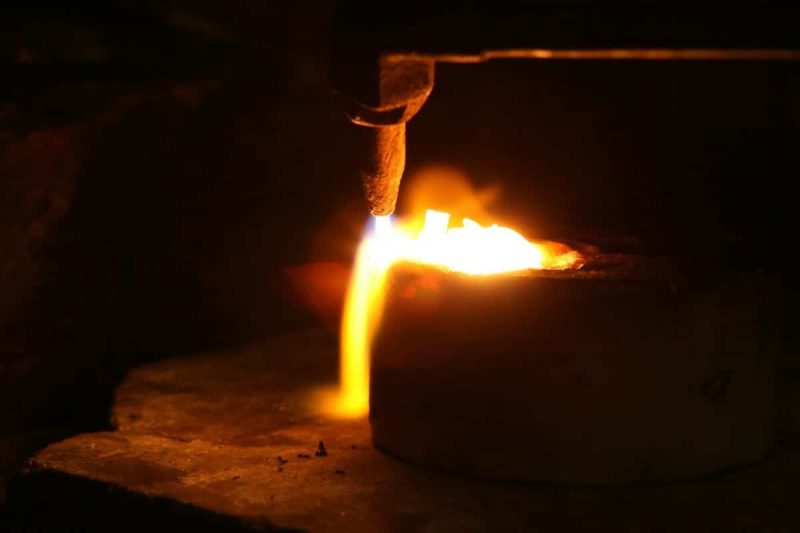
溶接の応用にはどのようなものがありますか?
溶接は、2 つ以上のワークピースの金属を加熱して溶かし、冷却後に強力な接続を形成するプロセスです。この接続は、アプリケーションのニーズに応じて、永続的または取り外し可能にすることができます。溶接は次の方法で適用できます。
- 材料の接合: 溶接は、金属材料を接合する主な方法です。このタイプの接続を使用して、小さなコンポーネントから大きな産業用コンポーネントまで、さまざまな構造を作成できます。
- 補強と修理: 溶接は材料を強化し、損傷した部品や構造を修復するために使用できます。これはメンテナンスと耐用年数の延長にとって非常に重要です。
- 製造: 製造において、溶接はさまざまなコンポーネントを組み立てて完成品を完成させるための重要なステップです。たとえば、自動車、飛行機、建築構造物などでは、さまざまな部品を接続するために溶接が必要です。
- カスタマイズ: 溶接は、製品を特定のニーズに合わせて調整する柔軟な方法を提供します。これは、アート、建築、個別製造などのさまざまな業界にとって重要です。
- エネルギー産業: エネルギー産業、特に石油、ガス、原子力エネルギー分野では、パイプ、容器、機器の製造とメンテナンスに溶接が使用されます。
- イノベーションと研究開発: 新しい溶接技術の研究開発は、レーザー溶接、電子ビーム溶接などの新興分野のためのより高度で効率的なソリューションも提供します。
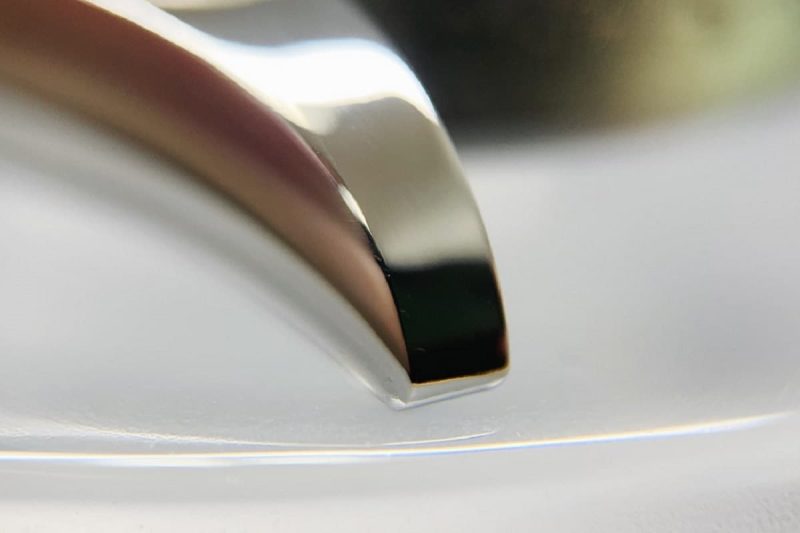
溶接にはどのような種類がありますか?
経験レベルや用途に応じて、さまざまな種類の溶接が適しています。溶接の経験と溶接したい材料を検討することで、どのタイプの溶接が自分に適しているかを判断できます。一般的な溶接の種類、その仕組み、およびその長所と短所をまとめました。
レーザー溶接
レーザー溶接は、高エネルギーの集中ビームを使用して金属を溶かす溶接方法です。レーザーの特性を利用し、集中した光エネルギーにより溶接部に高温を発生させ、ワーク表面を瞬時に溶かします。溶接プロセスでは、レーザー光の動きやワークの動きを制御することで、溶接部の溶融と凝固を層ごとに完了させ、強固な溶接継手を形成できます。
利点
- 精度:レーザー溶接は高精度であり、微細な領域の溶接が可能なため、電子機器や医療機器など、非常に高い溶接品質と外観が要求される用途に適しています。
- 速度: 従来の溶接方法と比較して、レーザー溶接は高速です。レーザー光は高速に移動するため、高効率な生産が可能であり、大規模大量生産に適しています。
- 熱影響が小さい:レーザー溶接は溶着面積が非常に小さいため、隣接する領域への熱影響が比較的小さく、変形や熱損傷が軽減されます。
- 自動化: レーザー溶接は自動化システムと簡単に統合でき、高度に自動化された生産ラインを実現し、生産効率を向上させます。
短所
- 設備コストが高い。レーザー溶接装置の取得およびメンテナンスのコストは比較的高いため、用途によってはレーザー溶接の投資コストが高くなります。
- 材料の選択に敏感: レーザー溶接は材料の選択により敏感であり、一部の材料はレーザー溶接に適さない可能性があり、その適用範囲が制限されます。
- 高い操作スキル要件: レーザー溶接には、溶接の精度と品質を確保するために高度な訓練を受けた操作スキルが必要であり、オペレーターに一定の要件が課されます。
- 溶接深さの制限: レーザー溶接の溶接深さは比較的浅いため、深い溶接が必要な特定の用途には適さない場合があります。
ガスタングステンアーク溶接
ガスタングステンアーク溶接は、タングステン電極によって生成される電気アークを使用します。 TIG溶接では、純タングステンまたはタングステン合金を電極として使用し、電極とワークとの間にアークを形成します。溶接プロセス中、溶接領域は外部から供給される不活性ガス (通常はアルゴン) によって保護され、酸素やその他の不純物の侵入を防ぎ、溶接の品質を確保します。
利点
- 高品質の溶接部: TIG溶接による溶接部は高品質です。溶接プロセス中、ガス保護により酸素やその他の不純物が溶接部に影響を与えるのを効果的に防ぐことができ、それにより気孔や介在物が減少します。
- 多様な材質に適したTIG溶接は、ステンレス、アルミ、銅などのさまざまな金属の溶接に適しており、材質への適応性に優れています。
- 溶接プロセスは高度に制御可能です。オペレータは電流、電圧、溶接速度などのパラメータを調整することで溶接プロセスを正確に制御でき、高い溶接品質要件が求められるシナリオに適しています。
- 熱変形が少ない:TIG溶接は溶接熱が比較的小さいため、熱変形の可能性が少なく、ワークの形状に精密な要求がある場合に特に適しています。
短所
- 溶接速度が比較的遅い: 他の溶接方法と比較すると、TIG 溶接は遅いため、大量生産では他の方法よりも効率が低くなる可能性があります。
- 高度な設備とスキルの要件: TIG 溶接には高度な訓練を受けたスキルが必要で、オペレーターには高い技術レベルが必要であり、設備のコストは比較的高価です。
- 厚板溶接には不向き:ワークが厚い場合、TIG溶接では溶接時間が長くなる場合があります。
- 溶接電流制限: 材料によっては、TIG 溶接の電流制限により溶接深さが不十分になり、溶接の強度に影響を与える場合があります。
金属の不活性ガス溶接
金属不活性ガス溶接は、溶接プロセス中の保護のために不活性ガスを使用する溶接方法です。 MIG 溶接では、金属電極が溶接ガンを通して溶接領域に供給され、ワークピースとアークを形成します。同時に、酸素などの不純物の侵入を防ぐために不活性ガス(通常はアルゴン、ヘリウム、またはそれらの混合物)を注入して溶接領域を保護します。
利点
- 高能率:MIG溶接は量産に適した高能率溶接法です。
- さまざまな金属に適しています: MIG 溶接は、鋼、アルミニウム、ニッケル銅などを含むさまざまな金属に適しており、材料適応性が優れています。
- 溶接変形が少ない:MIG溶接は溶接熱が比較的小さいため、溶接時の熱変形が少なくなります。
- 溶接棒を頻繁に交換する必要がない:他の手動溶接法と比較して、MIG溶接は溶接棒を頻繁に交換する必要がないため、ダウンタイムが短縮され、生産効率が向上します。
短所
- 装置コストが高い: MIG 溶接装置の購入とメンテナンスのコストは比較的高くなります。
- 風の影響を受けやすい: 屋外で溶接を行う場合、風は溶接エリアのガス保護に影響を与え、溶接品質の低下につながる可能性があります。
- 溶接場所の制限:MIG溶接には電力とガスの供給が必要なため、環境や場所によっては溶接が不便になります。
- 操作スキルの要件: MIG 溶接は TIG 溶接よりも操作スキルの要件が低くなりますが、溶接の品質を確保するには一定のトレーニングと経験が必要です。
被覆金属アーク溶接
被覆金属アーク溶接の動作原理は、溶接ガンの電極とワークピースの間に発生するアークに基づいており、これにより電極上の金属が溶解し、ワークピース上に堆積して溶接部が形成されます。 SMAW で使用される電極はフラックスの層で覆われており、溶接中にガスを発生して溶接部の保護雰囲気を形成し、空気中の酸素やその他の不純物が溶接部に影響を与えるのを防ぎます。
利点
- 幅広い適用性: SMAWは、炭素鋼、ステンレス鋼、アルミニウム合金などを含む多くの種類の金属の溶接に適しており、高い汎用性を備えています。
- 外部電源に依存しない:SMAWは外部電源に依存しない手動溶接方式であるため、修理やメンテナンス作業など電源のない現場や環境に適しています。
- 比較的シンプルな設備:SMAWに必要な設備はアーク溶接機と電極だけであり、複雑な制御システムを必要としないため、設備コストが削減されます。
- 厚板溶接に最適:SMAW は厚いワークに適しており、より深い溶接が可能で、高強度が必要な溶接作業に適しています。
短所
- 遅い溶接速度: 一部の自動溶接方法と比較して、SMAW の溶接速度は比較的遅く、大量生産には適していません。
- 高い操作スキル要件: SMAW では、アーク制御、溶接位置の選択、溶接パラメータの調整など、溶接工に高いスキルが求められます。
- 熱影響部が大きくなる: 溶接熱が大きいため、SMAW では熱影響部が大きくなり、ワークピースの熱変形と応力が増大する可能性があります。
- 電極を頻繁に交換する必要がある: SMAW 溶接では、使用中に電極が摩耗するため、頻繁に交換する必要があり、操作が複雑になり、ダウンタイムが増加します。
サブマージアーク溶接
サブマージアーク溶接の動作原理は、アークが溶接粉末の下に「埋もれる」ように、溶接領域に溶融した溶接粉末の層を置くことです。外部電源によってアークが発生し、ワイヤが加熱されて溶融し、溶接池が形成されます。溶接ワイヤを連続的に供給して徐々に溶接を形成します。
利点
- 高能率:サブマージアーク溶接は量産に適した高能率溶接法です。溶接ワイヤと溶接粉末を継続的に供給することで、溶接を比較的早く行うことができます。
- 厚いワークピースに最適: サブマージアーク溶接は、厚い金属ワークピースの溶接に適しており、溶接深さが深いため、高強度が必要な一部の用途に適しています。
- 安定した品質:サブマージアーク溶接で得られる溶接部の品質は比較的高く、気孔やスラグの介在物が少ないです。
- 高度な自動化: サブマージ アーク溶接は通常、自動または半自動の溶接プロセスであり、手動作業が減り、生産効率が向上します。
短所
- 設備とエネルギーの消費量: サブマージ アーク溶接装置は比較的複雑で、大規模な電力と供給システムを必要とするため、設備とエネルギーの消費量が比較的多くなります。
- 小型構造物には不向き:サブマージアーク溶接で生成される溶接線は大きいため、小型構造物や溶接線の外観を高くする必要がある場合には適していません。
- 垂直溶接または頭上溶接には適さない: 溶接池は重力の影響を受けるため、サブマージ アーク溶接は垂直溶接または頭上溶接には適しておらず、その適用範囲が制限されます。
抵抗溶接
抵抗溶接では通常、外部電源から電力が供給される 2 つの電極を使用して金属ワークをクランプし、閉回路を形成します。閉回路では、抵抗によって発生する熱により 2 つの金属ワーク間の接触点が加熱され、最終的には溶融温度に達してはんだ接合が形成されます。溶接時間は通常ミリ秒から数秒と短く、電流と圧力を調整することで溶接スポットのサイズと強度を制御できます。
利点
- 高速かつ効率的: 抵抗溶接は溶接時間が短く、はんだ接合が迅速に形成されるため、大量生産環境に適しています。
- 薄板に最適:抵抗溶接は溶接時の発熱が比較的少なく変形しにくいため、薄板の溶接に適しています。
- 外部溶加材は不要: 抵抗溶接では、金属自体の溶融によって溶接が形成されるため、追加の溶接材は必要ありません。
- 溶接後処理が不要:溶接時間が短く、熱影響が少ないため、通常は溶接後処理が不要で、生産工程が削減されます。
短所
- 導電性金属にのみ適しています: 抵抗溶接は主に金属の導電性に依存するため、非導電性金属または合金には一定の制限がありますが、導電性金属にのみ適しています。
- はんだ接合部の形状は制限されます。溶接中に電極のクランプ部分で金属が加熱されて溶融するため、はんだ接合部の形状は比較的限定され、通常は円形または楕円形になります。
- 複雑な形状には適さない: 抵抗溶接ではワークピースの形状についてより高い要件が求められるため、複雑な形状や不規則な形状のワークピースには適していません。
- はんだ接合部の強度は材料の影響を受けます。 はんだ接合部の強度は金属材料の特性に影響されます。高強度、高硬度の金属によっては、理想的な溶接結果を得ることが難しい場合があります。
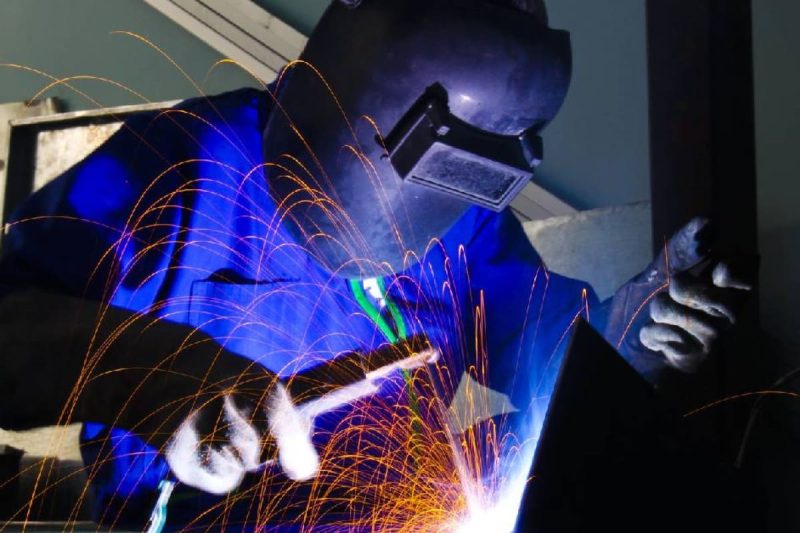
最も強力な溶接の種類は何ですか?
レーザー溶接、タングステンイナートガス溶接、金属イナートガス溶接、被覆金属アーク溶接、サブマージアーク溶接、抵抗溶接のうち、どの溶接法がより強力ですか?これらの溶接方法の特徴と用途をよりよく理解するために、以下でこれらの溶接方法を比較します。
レーザー溶接
レーザー溶接 高精度・高能率な溶接方法です。その利点としては、溶接が小さいこと、熱影響が少ないこと、さまざまな材料に適していることが挙げられます。レーザー溶接は、電子機器や医療機器などの精密製造や要求の厳しい用途に非常に効果的です。
タングステン不活性ガス溶接(TIG溶接)
TIG溶接は、高品質の溶接と緻密な制御で知られています。さまざまな金属、特にステンレス鋼やアルミニウムの溶接などの要求の厳しい用途に適しています。 TIG 溶接の欠点としては、高度な操作スキルが要求されることと、速度が比較的遅いことが挙げられます。
金属不活性ガス溶接(MIG溶接)
MIG溶接は大量生産に適した効率的な溶接方法です。溶接速度が速く、さまざまな金属に適しており、溶接棒を頻繁に交換する必要がないことが利点です。ただし、MIG 溶接には設備と環境に対する高い要件があり、すべての作業条件に適しているわけではありません。
被覆アーク溶接(SMAW)
SMAW は、さまざまな金属に適しており、高い汎用性を備えた伝統的な手動溶接方法です。外部電源に依存しない利点があり、フィールドメンテナンスなどの環境に適しています。ただし、SMAWは溶接速度が遅く、高い操作スキルが必要なため、小ロット生産や修理作業に適しています。
サブマージアーク溶接(SAW)
サブマージアーク溶接は、量産に適した自動溶接法であり、高強度が要求される用途に優れています。ただし、設備とエネルギーの消費量は比較的大きくなります。
抵抗溶接
抵抗溶接は溶接点を重視した溶接方法で、薄板や小物部品の接合に適しています。その利点は高速かつ効率的であることですが、金属の導電性に対する要件が高く、はんだ接合の形状が比較的制限されています。
要約する
上記の溶接方法の長所と短所を考慮すると、どの溶接方法が最も強力であるかを判断することは困難です。アプリケーションシナリオが異なれば、異なる溶接方法が必要になります。レーザー溶接は高精度・高品質の用途に適しており、MIG溶接は大量生産に適しています。 TIG や SMAW などの手動溶接法は、小規模生産や高度な技術管理が必要な分野に優れていますが、サブマージ アーク溶接は大規模な構造物の製作に適しています。
溶接方法を選択する際には、生産要件、材料の種類、コスト、効率など、いくつかの要素を考慮する必要があります。さまざまな溶接技術を包括的に使用し、特定のニーズに応じて柔軟に選択することで、さまざまなプロジェクトの要件をより適切に満たし、溶接プロセスの安定性、効率性、品質管理を確保できます。レーザー溶接をご検討の方はぜひご相談ください。 AccTek レーザー お客様のニーズに合わせて最適なオプションをご提案いたします。
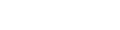
連絡先
- [email protected]
- [email protected]
- +86-19963414011
- No. 3 ゾーン A、Lunzhen 工業地帯、玉城市、山東省。
レーザー ソリューションを入手する