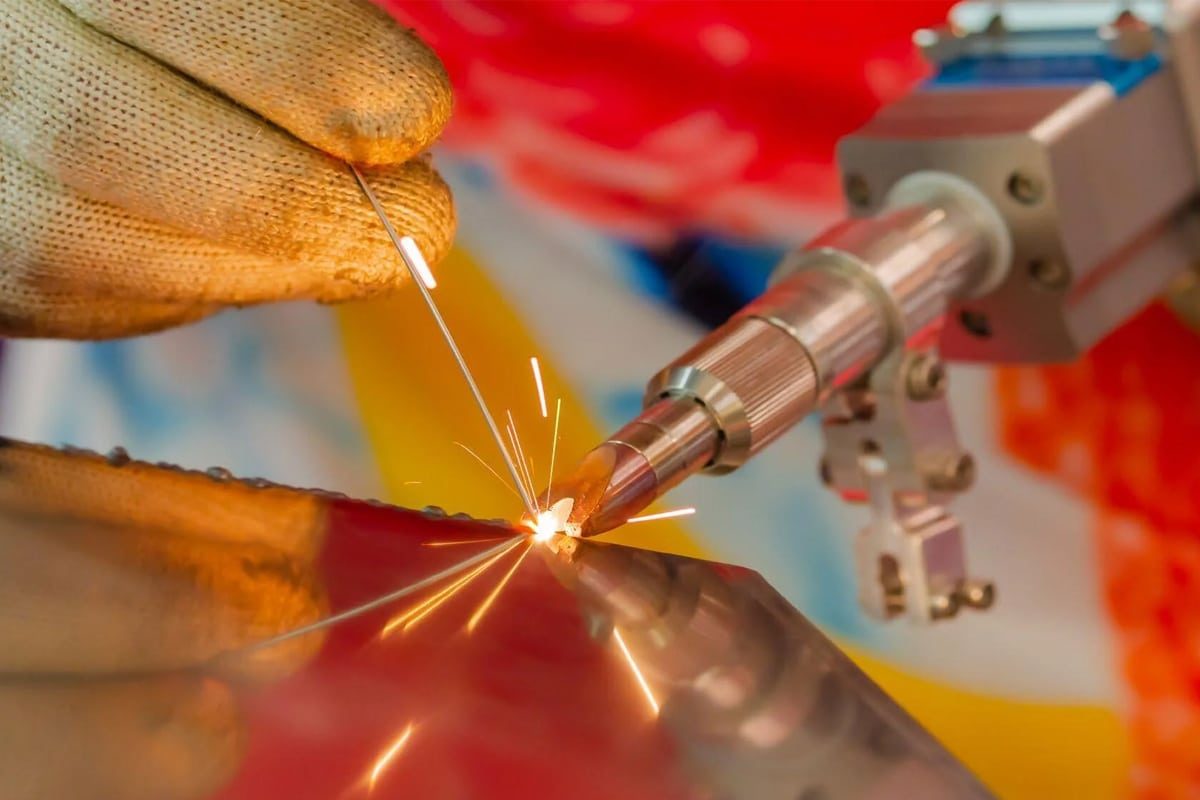
自溶レーザー溶接 VS フィラーレーザー溶接
レーザー溶接は、その精度、効率、汎用性により、現代の製造業の基盤となっています。さまざまな既存の技術の中でも、自溶性レーザー溶接とフィラーレーザー溶接は、独自の利点と用途により際立っています。自溶性レーザー溶接では、他の材料を追加せずにワークピースを融合し、きれいで高精度の溶接を実現します。対照的に、フィラーレーザー溶接では、溶接に他の材料を組み込むため、接合部の強度が向上し、より幅広い材料と厚さに対応できます。
この記事では、2 つの方法の基本的な違いを詳しく説明し、その原理、用途、利点、制限について考察します。自溶レーザー溶接とフィラーレーザー溶接の固有の特性と最適な使用例を理解することで、メーカーとエンジニアは情報に基づいた決定を下し、溶接プロセスを強化して、製品の品質と性能を向上することができます。
目次
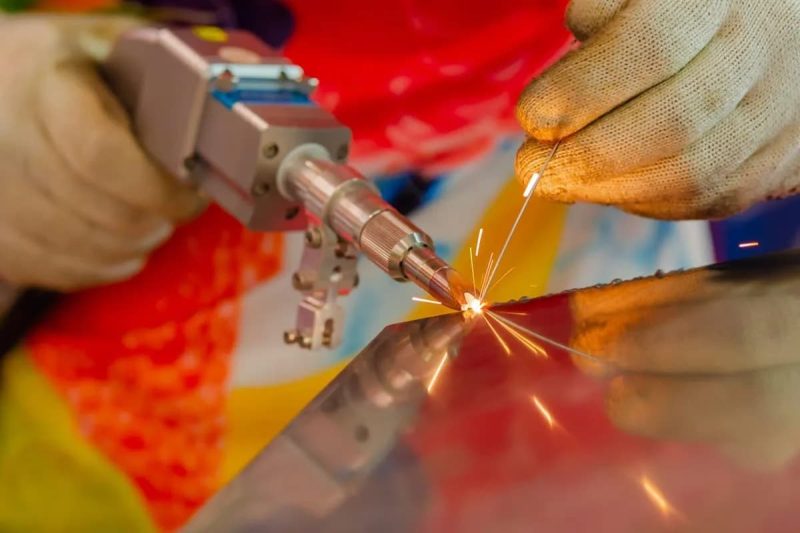
レーザー溶接入門
レーザー溶接は、製造業に革命をもたらした高精度技術であり、従来の溶接方法に比べて多くの利点があります。レーザー溶接は、集束したレーザービームを熱源として使用し、驚くほどの精度と速度で材料を接合します。このプロセスでは、集中した光線を放射し、ワークピースに照射すると、高熱が発生し、材料が溶けて冷却され、強力で耐久性のある接合部が形成されます。
レーザー溶接の主な利点の 1 つは、熱変形を最小限に抑えて高品質の溶接を行えることです。レーザーの高エネルギー密度により、溶接プロセスの深い浸透と正確な制御が可能になり、厳格な基準が求められる用途に最適です。さらに、レーザー溶接は効率性に優れ、高速で溶接できるため、産業環境での生産性が大幅に向上します。
レーザー溶接は、フィラー材の有無によって、大まかに自溶レーザー溶接とフィラーレーザー溶接の 2 つのカテゴリに分けられます。自溶レーザー溶接では、レーザービームが接合するワークピースのエッジを直接溶かし、完全に母材の溶融に依存します。一方、フィラーレーザー溶接では、フィラー材が追加され、母材とともに溶けて溶接を形成します。
自溶レーザー溶接とフィラーレーザー溶接はどちらも独自の利点があり、特定の用途要件、材料特性、および望ましい溶接特性に基づいて選択できます。これらの方法の基本と違いを理解することで、溶接プロセスを最適化し、さまざまな産業用途で最高の結果を得ることができます。レーザー技術が進歩し続けるにつれて、レーザー溶接の機能と用途は拡大し、現代の製造業における重要なツールとしての役割をさらに強化することが期待されます。
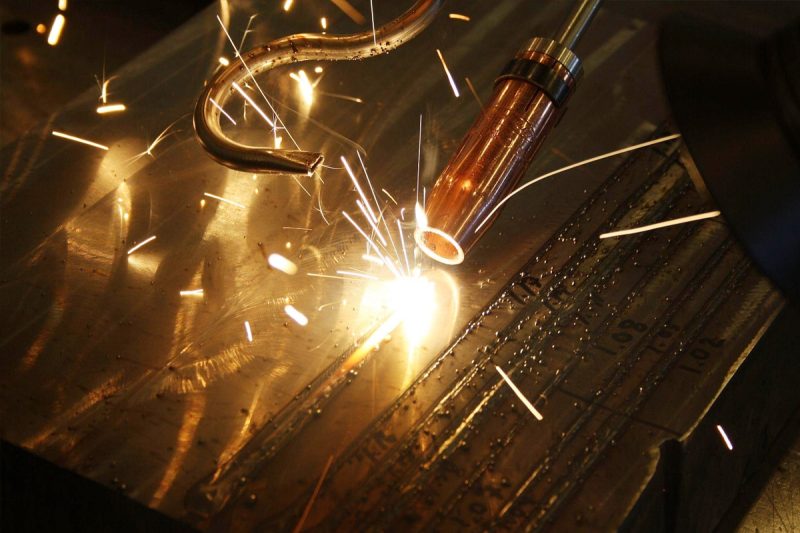
自溶性レーザー溶接
定義とプロセス
自溶性レーザー溶接は、追加の充填材を使用せずに材料の端を溶かして材料を接合するタイプのレーザー溶接です。この方法は、ベース材料が冷却時に融合する能力に完全に依存しており、その結果、強力でシームレスな接合部が得られます。このプロセスでは、ワークピース間の接合部に高強度のレーザー ビームを照射し、材料を局所的に溶かしてその後固化させます。
自生レーザー溶接プロセスの手順:
- 準備: ワークピースは徹底的に洗浄され、溶接プロセスを妨げる可能性のある油、汚れ、酸化物などの汚染物質が除去されます。
- 位置合わせ: ワークピースのエッジを正確に位置合わせして、均一な接合を実現します。
- レーザー ビームの照射: 焦点を絞ったレーザー ビームを接合部に照射します。レーザーのエネルギー密度は、材料の端を溶かすのに十分です。
- 融合: 溶融したエッジが融合し、レーザー ビームが接合部に沿って移動すると、材料が冷却されて固化し、溶接部が形成されます。
機構
自己生成レーザー溶接のメカニズムは、局所的な加熱と急速な冷却の原理に基づいています。レーザービームの高エネルギー密度により、接合部の温度が急上昇し、材料が溶けます。レーザーのエネルギーによって材料が蒸発して空洞が形成されると、キーホールが形成されます。これは、深浸透レーザー溶接の特徴です。このキーホールは溶融材料に囲まれており、レーザービームが遠ざかると、溶融材料が崩壊して固化し、溶接が形成されます。
このプロセスは、主に次の 2 つのモードに分けられます。
- 熱伝導モード: 薄い材料に適用可能で、レーザーエネルギーが表面に吸収され、材料を通して伝導され、溶融を引き起こします。
- キーホール モード: 厚い材料に使用され、レーザーが材料を蒸発させてキーホールを形成し、より深い浸透とより強力な溶接を実現します。
技術的な考慮事項
自溶性レーザー溶接で最良の結果を得るには、いくつかの技術的要素を考慮する必要があります。
- レーザーパラメータ: 十分な浸透と融合を確保するには、出力、焦点、ビーム品質、速度を正確に制御する必要があります。
- 材料特性: 熱伝導率、反射率、融点などの材料の溶接性がプロセスに影響します。
- ジョイント設計: ギャップ幅や位置合わせなどのジョイントの形状は、一貫した溶接を保証するために正確に制御する必要があります。
- シールドガス: 溶接プールを酸化や汚染から保護するために、通常はアルゴンや窒素などの不活性ガスが使用されます。
- 冷却速度: 制御された冷却により、溶接材料の熱応力と歪みが防止されます。
利点
- 高精度: 集中したレーザービームにより溶接を正確に制御でき、複雑で繊細な用途に適しています。
- きれいな溶接: 充填材がないため、汚染の可能性がなくなり、きれいで見た目にも美しい溶接が実現します。
- 最小限の熱影響部: 局所的な熱入力により熱変形が軽減され、周囲の材料の機械的特性が維持されます。
- 速度と効率: プロセスを高速で実行できるため、生産性が向上し、サイクル時間が短縮されます。
- 自動化の互換性: 自動化システムへの簡単な統合により、一貫性と再現性が向上します。
制限事項
- 材料の適合性: すべての材料が自溶溶接に適しているわけではありません。特に、融点が大きく異なる材料や溶接性が悪い材料は適していません。
- ジョイントの準備: 正確な位置合わせときれいな表面が必要であり、アプリケーションによっては時間がかかり、困難な場合があります。
- 厚さの制限: 隙間を埋める充填材がなければ厚い材料を溶接するのは困難であり、この方法は薄い部分には適していません。
- 応力集中: 充填材がないと溶接接合部に応力が集中し、機械的特性に影響を与える可能性があります。
アプリケーション
自溶性レーザー溶接は、高精度できれいな溶接を必要とするさまざまな業界で使用されています。
- エレクトロニクス: 民生用電子機器や半導体装置の小さな部品や繊細なアセンブリの溶接。
- 医療機器: 高精度と清潔さが求められる手術器具、インプラント、その他の医療ツールの製造に使用されます。
- 航空宇宙: 航空機や宇宙船の薄い材料や部品を接合し、重量を軽減して構造の完全性を維持します。
- 自動車: 車体部品、排気システム、および高精度で高品質の溶接を必要とするその他のコンポーネントの製造に使用されます。
- ジュエリー: 貴金属の外観や特性を変えずに、細かく正確な溶接を行います。
自溶レーザー溶接は、きれいな溶接と最小限の熱変形を必要とする用途に適した高精度で効率的な溶接技術です。その有効性は、技術的パラメータの厳密な制御と材料特性の考慮によって決まるため、さまざまな高精度産業で価値のある方法となっています。
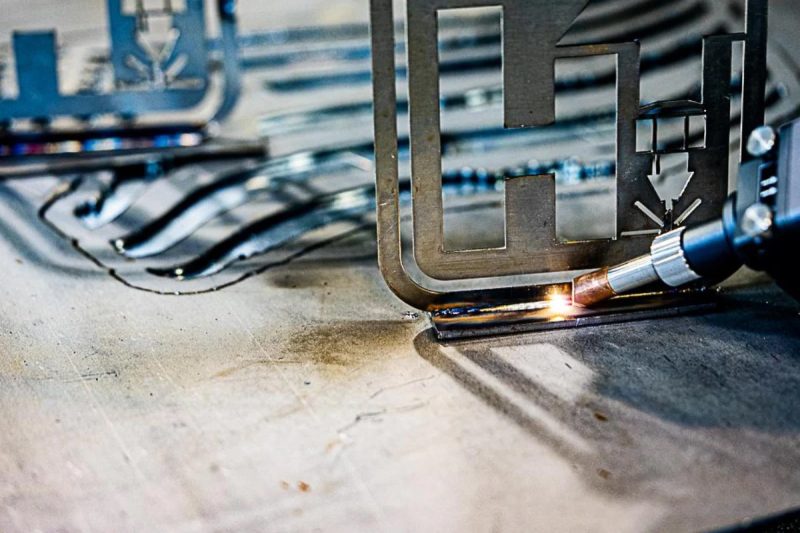
フィラーレーザー溶接
定義とプロセス
フィラー レーザー溶接は、溶接接合部にフィラー材料を追加し、それをレーザー ビームと組み合わせて材料を接合する技術です。この方法は、異なる特性を持つ材料を接合する場合や、接合部の強度を高め、隙間を埋める能力を必要とする用途に特に有効です。
- 準備: 接合する材料の表面をきれいにして、汚染物質を除去し、接合部を適切に位置合わせします。
- フィラー材料の追加: ワイヤ、粉末、または事前に設定されたストリップの形のフィラー材料を手動または自動で溶接領域に導入します。
- レーザービームの照射: 焦点を絞ったレーザービームを接合部に照射し、ベース材料と充填材の両方を溶かします。
- 融合: 溶融したフィラー材料が溶融したベース材料と結合して均一な溶接プールを形成します。
- 凝固: 冷却すると溶融池が凝固し、充填材を含む強力な溶接接合部が形成されます。
このプロセスは、厚い材料、溶接性の悪い材料、または自溶溶接では簡単に埋めることができない大きな隙間のある接合部の溶接に特に役立ちます。
機構
フィラーレーザー溶接のメカニズムには、いくつかの重要な段階が含まれます。
- 吸収: レーザーエネルギーはベース材料とフィラー材料の両方に吸収され、急速な加熱を引き起こします。
- 溶解: レーザーによって生成された強力な熱により、ベース材料とフィラー材料の両方のエッジが同時に溶解します。
- 溶融ゾーンの形成: 溶融した充填材とベース材料が融合して均一な溶融ゾーンを形成し、隙間を埋めて接合部を強化します。
- 凝固: レーザーが遠ざかると、溶融池は冷却されて凝固し、充填材を含む連続した強力な溶接部が形成されます。
このメカニズムの有効性は、充填材の種類、レーザーパラメータ、ベース材料の特性などの要因によって異なります。
技術的な考慮事項
フィラーレーザー溶接の性能と品質を最適化するには、いくつかの技術的要素を考慮する必要があります。
- フィラー材料の選択: フィラー材料は、融点、化学組成、熱膨張、機械的特性、耐腐食性などの点で母材と互換性がある必要があります。
- レーザー出力とビーム品質: ベース材料とフィラー材料の両方を溶かすには十分なレーザー出力が必要です。ビーム品質が高いと、正確なエネルギー供給が保証されます。
- フィラー材料の供給: フィラー材料 (ワイヤ、粉末、またはプリセット材料) を供給する方法は、溶接プールに一貫して均一に材料が追加されるように慎重に制御する必要があります。
- 溶接速度と送り速度: 均一な溶接を実現するには、レーザーの速度と溶接領域に充填材を導入する速度を慎重に制御する必要があります。
- シールドガス: シールドガスを使用すると、溶接プールの酸化や汚染を防ぎ、溶接品質を向上させることができます。
- ジョイントの設計と準備: 適切なジョイントの設計と準備により、充填材を適合させ、強力で欠陥のない溶接を確保できます。
利点
- 接合強度の向上: フィラー材料を追加すると、溶接部の機械的特性が向上し、強度と耐久性が向上します。
- 材料選択の柔軟性: この方法では、異なる材料や融点の異なる材料の溶接が可能になり、汎用性が高まります。
- ギャップを埋める機能: 充填材はギャップを埋めてジョイントのずれを吸収できるため、ジョイントの正確な準備の必要性が軽減されます。
- 汎用性: 薄い材料と厚い材料の両方に適用でき、強力で信頼性の高い接合部を実現します。
制限事項
- 複雑さ: 充填材を管理するには追加の機器と制御システムが必要となり、溶接プロセスが複雑になります。
- 汚染の可能性: 充填材の導入により汚染のリスクが高まり、溶接品質に影響を及ぼす可能性があります。
- コストの上昇: 充填材の使用と追加機器の必要性により、溶接プロセス全体のコストが増加する可能性があります。
- プロセス制御: 一貫した充填材の追加とレーザーパラメータの制御を維持することは困難な場合があります。
アプリケーション
フィラーレーザー溶接は、強力な接合部と材料の多様性が求められる幅広い業界で使用されています。
- 自動車: 厚い材料、隙間が大きい部品、特別な強度が必要な構造部品の溶接に適しています。
- 航空宇宙: 複雑な部品の製造および修理において、強力で耐久性のある接合部を確保します。
- 建設: 高強度のジョイントとさまざまなジョイント構成に対応する能力を必要とする構造溶接作業に適しています。
- 製造: 機械、装置、およびさまざまな産業部品の強力で信頼性の高い接合部を作成します。
- 石油・ガス: 高圧や過酷な環境条件に耐える必要があるパイプやその他の部品に。
フィラー レーザー溶接は、フィラー材料を組み込むことで接合部の強度を高め、隙間を埋め、より幅広い材料や用途に対応し、自溶溶接の多くの制限に対処する、多用途で強力な溶接技術です。ただし、複雑さとコストが増すため、最適な結果を得るには、技術的なパラメータとプロセス制御を慎重に検討する必要があります。
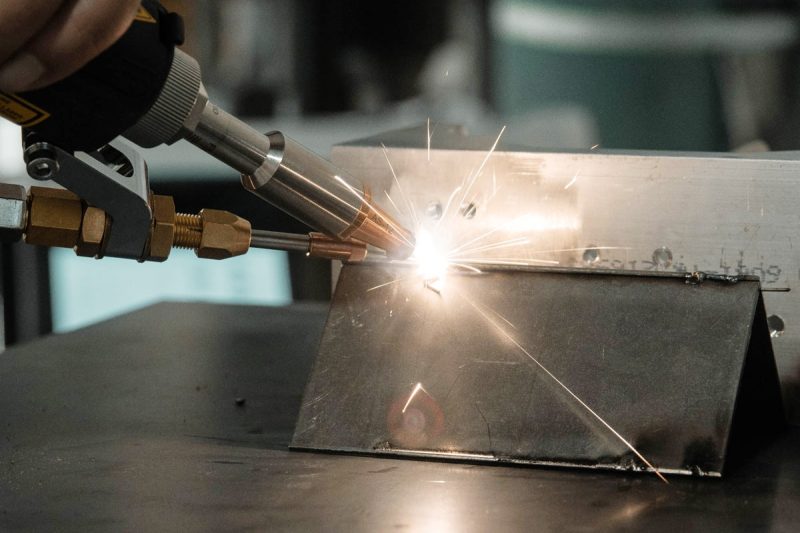
比較解析
材質の適合性
自溶性レーザー溶接
- 材料要件: 自溶性レーザー溶接は、溶接性がよく、融点が類似している材料で最も効果的に機能します。特に、熱伝導率が高く、組成が均一な金属に適しています。
- 制限事項: この方法は、異なる金属や、融点や熱膨張係数が大きく異なる材料には適していません。たとえば、アルミニウムと鋼鉄の物理的特性が大きく異なるため、自溶溶接を使用してアルミニウムを鋼鉄に溶接することは困難です。
フィラーレーザー溶接
- 材料の柔軟性: フィラーレーザー溶接は、材料の適合性に関してより柔軟性があります。フィラー材料を追加することで、異なる金属や異なる特性を持つ材料の溶接が可能になります。これにより、アルミニウム、チタン、ステンレス鋼などの金属を含む、より幅広い用途に適しています。
- 接合品質の向上: フィラー材料を使用すると、融点と熱膨張の差を埋めることができ、より強力で信頼性の高い溶接が可能になります。
ジョイントの準備と取り付け
自溶性レーザー溶接
- 精度要件: 自溶溶接では、正確な接合部の準備と位置合わせが必要です。ワークピースの端は清潔で、汚染物質がなく、しっかりとフィットして、強力な溶接を確保する必要があります。隙間や位置ずれがあると、溶接の品質に影響します。
- 表面の清浄度: フィラー材料が存在しないということは、基材の表面の不純物が溶接の完全性に直接影響することを意味するため、ワークピースは徹底的に洗浄して準備する必要があります。
フィラーレーザー溶接
- 許容度の高いプロセス: フィラー レーザー溶接は、ジョイントの準備とフィットアップに関してより許容度の高いプロセスです。フィラー材料は隙間を埋め、わずかなずれを吸収できるため、ジョイントの準備が完璧でなくても強力な溶接を実現しやすくなります。
- ギャップ ブリッジング: この方法は、正確なフィットが困難な場合や、ジョイントの形状にばらつきがある場合に特に役立ちます。フィラー材料はギャップを埋めるのに役立ち、より一貫性のある強力な溶接を実現します。
強度と耐久性
自溶性レーザー溶接
- 強度は母材に依存: 自溶性レーザー溶接における溶接の強度と耐久性は、母材に完全に依存します。母材の機械的特性が優れている場合、溶接部も通常同様の特性を示します。
- 強化の限界: フィラー材料を追加しないと、溶接部の機械的特性を母材のレベル以上に高める機会はほとんどありません。
フィラーレーザー溶接
- 強度強化: フィラー材を使用すると、溶接部の強度と耐久性を大幅に向上できます。フィラー材を選択して、母材の機械的特性を補完または改善することで、より強力な接合部を実現できます。
- カスタマイズ可能な特性: 適切な充填材を選択することで、引張強度、靭性、耐疲労性などの溶接部の機械的特性を、特定のアプリケーション要件に合わせてカスタマイズできます。
コストに関する考慮事項
自溶性レーザー溶接
- 材料コストの削減: 自溶溶接では、充填材が使用されないため、一般的に材料コストが削減されます。これは、材料コストの節約が積み重なるため、大量生産に非常に有利です。
- よりシンプルな装置: 充填材が不要になるため、溶接装置が簡素化され、追加の制御システムの必要性が減り、初期投資とメンテナンスコストを削減できます。
- 効率: 自溶溶接は、特に薄い材料や、正確な接合準備が可能な用途では非常に効率的です。溶接速度が速く、溶接後の処理の必要性が減るため、コスト削減につながります。
フィラーレーザー溶接
- 材料コストの上昇: フィラー材料を追加すると、溶接プロセス全体の材料コストが増加します。フィラー材料の選択もコストに影響する可能性があります。特に特殊な合金が必要な場合に顕著です。
- 複雑な設備: 充填材の管理にはより複雑な設備と制御システムが必要となり、初期投資とメンテナンスコストが増加する可能性があります。
- 汎用性と品質: コストは高くなりますが、フィラー レーザー溶接は、材料の適合性、接合部の強度、ギャップのブリッジが重要な用途では、全体的な価値を高めることができます。多くの産業用途では、高品質で耐久性のある溶接を生成できる能力があれば、追加費用を正当化できます。
自溶レーザー溶接とフィラーレーザー溶接のどちらを選択するかは、材料の適合性、接合部の準備要件、必要な溶接強度と耐久性、コストの考慮など、さまざまな要因によって決まります。自溶溶接は、特に同様の特性を持つ材料の場合、熱変形を最小限に抑えた高精度でクリーンな溶接を必要とする用途に適しています。対照的に、フィラーレーザー溶接は、コストは高くなりますが、汎用性が高く、接合強度が強化され、より幅広い材料と接合部構成に対応できます。これらの違いを理解することで、メーカーとエンジニアは特定のニーズに最も適した溶接方法を選択し、パフォーマンスとコスト効率を最適化できます。
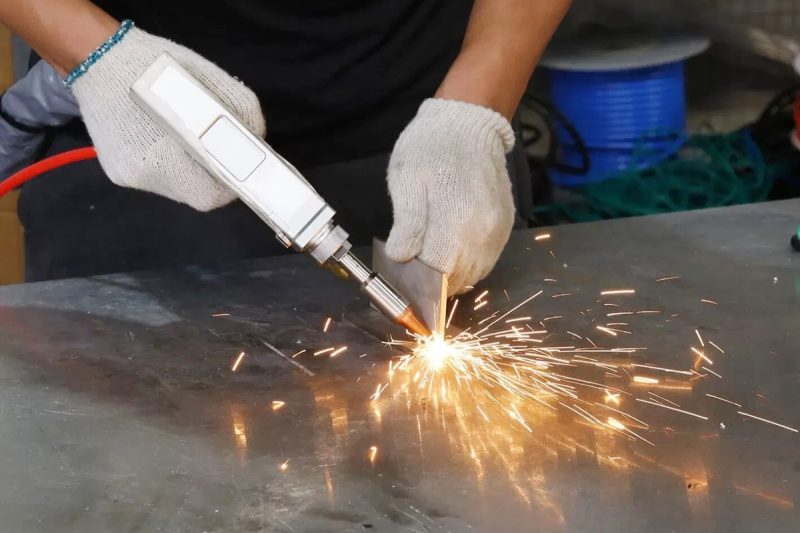
まとめ
レーザー溶接の分野では、自溶レーザー溶接とフィラーレーザー溶接の両方に独自の利点と用途があります。自溶レーザー溶接は、高精度、最小限の汚染、低コストが求められるシナリオに優れており、大量生産や電子機器や医療機器などの業界に最適です。ベース材料の融合のみに依存するため、隙間のない、きれいでよく準備された接合部が必要です。一方、フィラーレーザー溶接は柔軟性が高く、より幅広い材料と複雑な接合設計に対応します。自動車、航空宇宙、建設業界で普及している、接合部の強度を高め、隙間を埋める能力が求められる用途には不可欠です。フィラー材料とより複雑な装置のためにコストが高くなりますが、特殊な用途ではメリットがこれらの費用を上回ることがよくあります。これらの方法の選択は、材料特性、接合部設計、用途要件、生産量、コストの考慮事項によって決まり、特定のニーズに最適な溶接アプローチが確保されます。
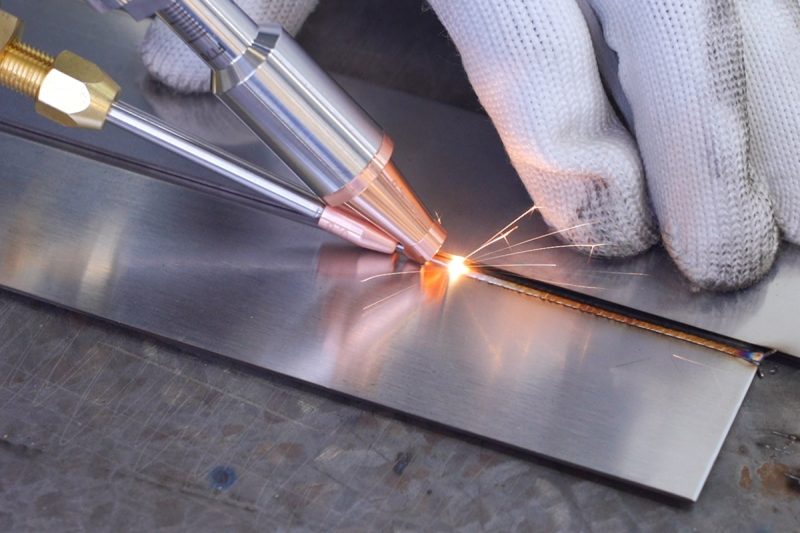
レーザー溶接ソリューションを入手
最先端のレーザー溶接ソリューションをお探しなら、AccTek Laserにお任せください。プロフェッショナルなレーザー溶接ソリューションのリーディングプロバイダーとして、 レーザー溶接機AccTek Laser は、現代の製造業の多様なニーズを満たすようにカスタマイズされた包括的な機器を提供しています。自溶性レーザー溶接の精度と清潔さが必要な場合でも、フィラー レーザー溶接の汎用性と強度が必要な場合でも、AccTek Laser には優れた結果を提供する専門知識と技術があります。
当社の最先端のレーザー溶接機は、さまざまな材料や接合構成に対応できるように設計されており、熱変形を最小限に抑えた高品質の溶接を保証します。 AccTek レーザー当社は、イノベーション、信頼性、顧客満足を最優先に考え、生産性と効率性を高めるカスタマイズされたソリューションを提供しています。当社の製品ラインナップをご覧いただき、当社の高度なレーザー溶接技術が製造プロセスをどのように向上できるかをご確認ください。当社のカスタマイズされた溶接ソリューションの詳細と、特定のアプリケーションで優れた溶接性能を実現する方法については、今すぐ AccTek Laser にお問い合わせください。
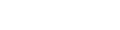
連絡先
- [email protected]
- [email protected]
- +86-19963414011
- No. 3 ゾーン A、Lunzhen 工業地帯、玉城市、山東省。
レーザー ソリューションを入手する