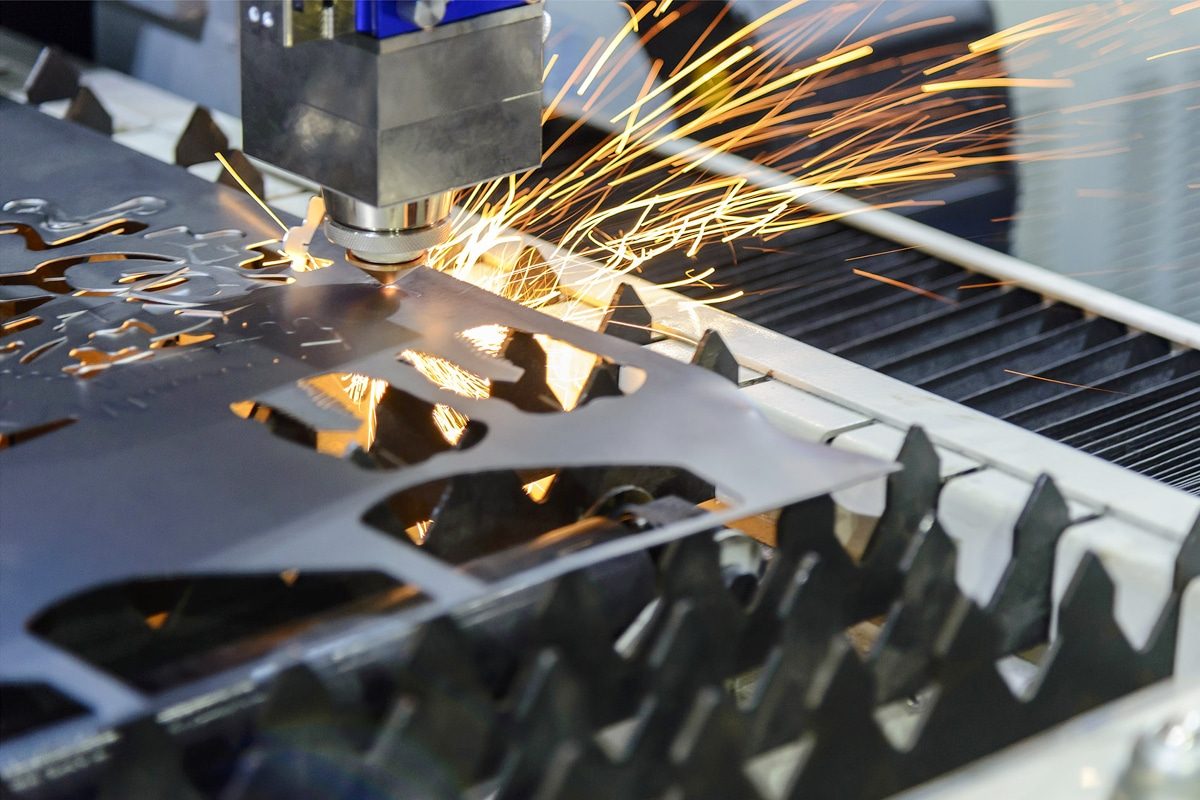
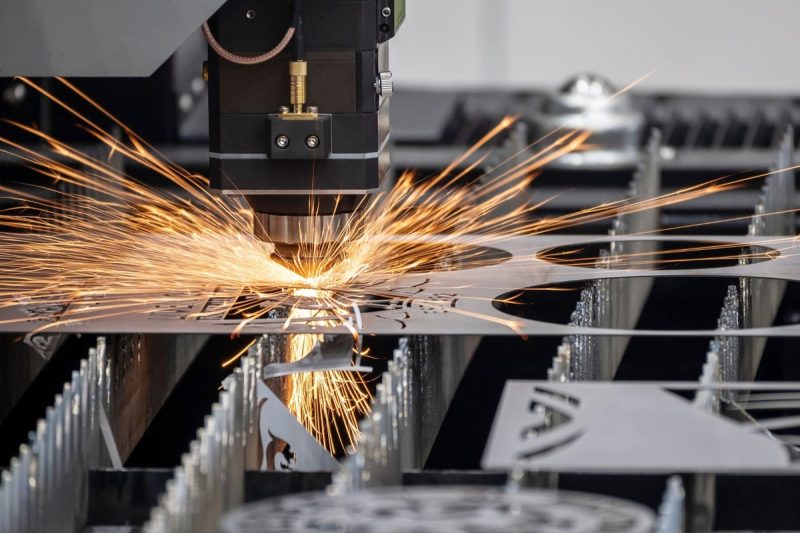
レーザー切断について学ぶ
レーザーカットの説明
切断用途で使用されるレーザーの種類
ファイバーレーザー
CO2レーザー
レーザー切断システムのコンポーネント
典型的な レーザー切断システム 正確で効率的な切断性能を実現するために連携して動作するいくつかの主要コンポーネントで構成されています。
- レーザー ソース: これはレーザー ビームを生成するコア コンポーネントです。用途に応じて、レーザー ソースはファイバー レーザー ジェネレーター、CO2 レーザー ジェネレーター、または他のタイプのレーザー ジェネレーターになります。
- 光学系: ミラーとレンズは、レーザー光線を切断する材料に向け、焦点を合わせるために使用されます。光学系の品質は、切断プロセスの精度と効率に影響します。
- 切断ヘッド: 切断ヘッドには、レーザー光線と補助ガスを導く集束レンズとノズルが含まれています。切断ヘッドは、正しい焦点距離を維持し、最適な切断条件を確保する役割を果たします。
- 作業台: 切断される材料を支え、通常は切断ヘッドの下で材料を移動する機構を備えています。
- CNC コントローラー: CNC コントローラーは、プログラムされた切断パスに従ってレーザー切断ヘッドとワークピースの動きを管理し、目的の形状とパターンを生成します。
- 補助ガス供給: 補助ガスは、溶融材料を吹き飛ばし、切断領域を冷却し、酸化を防ぐことで切断プロセスを補助します。一般的な補助ガスには、酸素、窒素、圧縮空気などがあります。
- 排気システム: 切断プロセス中に発生する煙や破片を除去して、清潔な作業環境を維持し、光学系とレーザー部品を保護します。
- 冷却システム: レーザー切断では大量の熱が発生するため、レーザー光源やその他のコンポーネントの損傷を防ぐために放散する必要があります。最適な動作温度を維持するために、水冷却装置などの冷却システムが使用されます。
レーザー切断性能に影響を与える主要なパラメータ
レーザー切断プロセスのパフォーマンスと品質に影響を与えるパラメータはいくつかあります。これらのパラメータを理解して最適化することで、望ましい結果を得ることができます。
- レーザー出力: レーザー ソースの出力によって、切断できる材料の厚さと種類が決まります。出力が高いほど厚い材料を切断できますが、切断品質を維持するために他のパラメータを調整する必要がある場合があります。
- 切断速度: 切断ヘッドがワークピース上で移動する速度。最適な切断速度により、生産性と切断品質のバランスが確保されます。速度が速すぎると切断が不完全になる可能性があり、速度が遅すぎると過度の熱の蓄積や材料の損傷を引き起こす可能性があります。
- 焦点位置: 材料の表面に対するレーザー ビームの焦点の位置。焦点が正しいと、切断点でのエネルギー密度が最大になり、きれいで正確な切断が可能になります。位置がずれると、切断品質が低下し、効率が低下する可能性があります。
- アシストガスの種類と圧力: 使用されるアシストガスの種類と圧力 (酸素、窒素、または圧縮空気) は、切断プロセスに大きな影響を与えます。適切なガスの選択と圧力により、溶融材料の除去が最適化され、酸化が防止され、切断品質が向上します。
- 材料の種類と厚さ: 材料と厚さによって、レーザー切断に対する反応が異なります。切断パラメータを設定するときは、反射率、熱伝導率、融点などの材料特性を考慮する必要があります。
- ビーム品質: 焦点とモード構造によって特徴付けられるレーザー ビームの品質は、カットの精度と品質に影響します。焦点サイズが小さい高品質のビームを使用すると、カット幅が最小で、より細かいカットが得られます。
- ノズル設計: ノズルの直径や形状などの設計は、アシストガスの流れや溶融材料の除去に影響します。最適化されたノズル設計により、切断効率と品質が向上します。
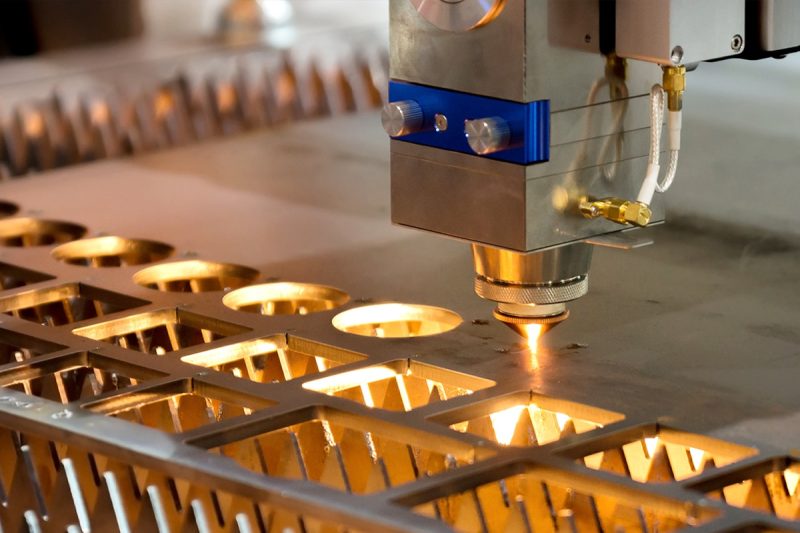
レーザー切断におけるアシストガスの役割
溶融物質の除去
レーザー切断プロセスでは、高強度のレーザー ビームが切断箇所の材料を溶かします。アシスト ガスがノズルから切断領域に送られ、切断部分 (レーザーによって作成された隙間) から溶けた材料を除去します。溶けた材料を効果的に除去することで、切断品質が維持され、欠陥を防止できます。
- 効率的な噴射: アシストガスの高圧により溶融材料が切り口から吹き飛ばされ、ワークピース上で再凝固するのを防ぎ、きれいな切断を実現します。
- スラグ生成の防止: アシストガスは溶融材料を急速に排出することで、スラグ (切断面の底面に付着した残留材料) の生成を最小限に抑え、後処理の必要性を減らします。
- 切り口幅の維持: 溶融材料を継続的に除去することで、希望する切り口幅を維持し、最終カットの寸法精度と精密さを確保します。
切断ゾーンの冷却
レーザービームによって発生する高熱は、ワークピースに反り、変形、材料特性の変化など、重大な熱影響を引き起こす可能性があります。アシストガスは、切断ゾーンを冷却することで、これらの熱影響を抑制するのに役立ちます。
- 熱の放散: アシストガスの流れにより、切断エリアの余分な熱を吸収して放散し、過熱を防ぎ、材料の熱変形を最小限に抑えます。
- 熱影響部 (HAZ) の削減: 切断ゾーンを冷却すると、HAZ のサイズが制限され、材料の機械的特性が維持され、反りやその他の熱による損傷のリスクが軽減されます。
- 切断速度の向上: 効率的な冷却により、材料に熱による欠陥が発生する可能性が低くなるため、切断速度が向上し、より高速で効率的な生産が可能になります。
レンズの保護
切断ヘッドのレンズは、レーザー光線をワークピースに集中させます。切断プロセス中に発生する煙、ほこり、破片などの汚染物質は、レンズを損傷したり、レンズの性能を低下させる可能性があります。アシストガスは、レンズを汚染物質から保護します。
- レンズシールド: アシストガスがレンズと切断領域の間にバリアを形成し、汚染物質がレンズ表面に到達して堆積するのを防ぎます。
- 光学品質の維持: レンズを清潔に保ち、ゴミを取り除くことで、アシストガスは最適なビーム焦点と一貫した切断性能を保証します。
- レンズ寿命の延長: 汚れを防ぐことでレンズの摩耗が減り、レンズの寿命が延び、メンテナンスコストが削減されます。
切削反応の強化
補助ガスはレーザー切断中に発生する化学反応に影響を与え、さまざまな材料の切断性能を向上させます。使用するガスの種類によって特定の反応が促進または抑制され、切断の品質と効率に影響する場合があります。
- 酸素 (O₂): 酸素は炭素鋼の切断によく使用されます。酸素は溶融金属との発熱反応を促進し、余分な熱を発生させて切断速度を上げます。この反応により、ドロスが少なくきれいな切断面が得られますが、切断面が酸化される可能性があります。
- 窒素 (N₂): 窒素は、ステンレス鋼、アルミニウム、その他の非鉄金属の切断によく使用される不活性ガスです。切断ゾーンの周囲に不活性雰囲気を形成することで酸化を防ぎます。これにより、酸化物のないきれいな切断面が得られるため、高品質の表面仕上げが求められる用途に最適です。
- 圧縮空気: 圧縮空気は、さまざまな材料を切断するために使用できるコスト効率の高い代替手段です。圧縮空気は酸素と窒素の特性を組み合わせ、低コストで十分な切断性能を提供します。ただし、切断品質に影響を与える不純物が混入する可能性があります。
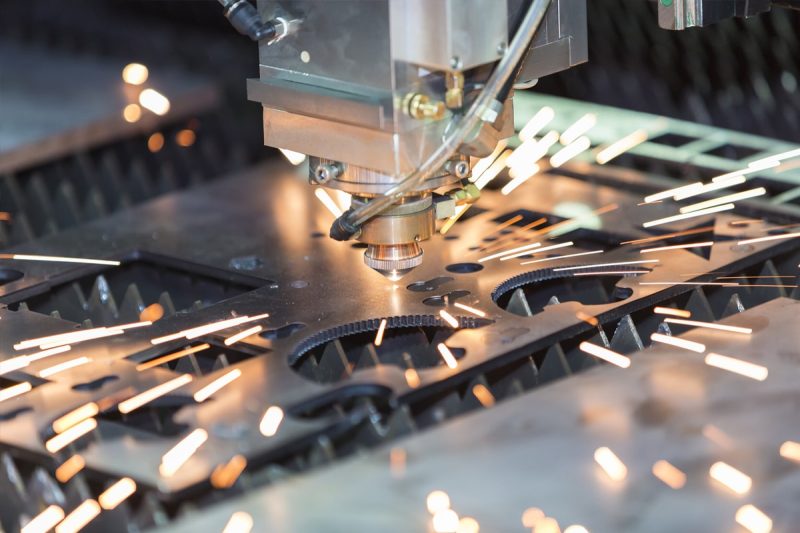
アシストガスの種類
酸素(O₂)
利点
- 切断速度の向上: 酸素は発熱反応で材料と反応し、追加の熱を放出します。この追加の熱により切断速度が上がり、特に厚い材料の場合、酸素アシスト切断が大幅に高速化されます。
- 効率の向上: 発熱反応により、材料の切断に必要なレーザー出力が削減され、切断プロセスの全体的なエネルギー効率が向上します。
- 厚い材料をよりきれいに切断: 酸素は厚い材料をよりきれいに切断するのに役立ち、ドロスとスラグを削減し、大規模な後処理の必要性を減らします。
短所
- 酸化: 酸素と材料の反応により切断面が酸化され、表面仕上げが粗くなり、腐食の問題が発生する可能性があります。
- 熱影響部 (HAZ): 発熱反応によって発生する追加の熱によって HAZ のサイズが大きくなり、切断端付近の材料の機械的特性が変化し、反りや構造的完全性の低下などの問題が発生する可能性があります。
- 非鉄金属の制限: 酸素は、酸素と容易に反応しないアルミニウムや銅などの非鉄金属ほど効果的ではありません。
窒素(N₂)
利点
- 酸化のない切断: 窒素は不活性ガスで、切断プロセス中に材料と反応しません。この特性により酸化が防止され、きれいで明るい、酸化物のない切断面が得られます。これは、高品質の表面仕上げが求められる用途に最適です。
- 高品質の表面仕上げ: 酸化がないため、エッジと表面仕上げがより滑らかになり、後処理の必要性が軽減または排除されます。
- 熱影響部 (HAZ) の最小化: 窒素は熱影響部を小さく保ち、材料の機械的特性を維持し、熱変形を最小限に抑えます。これにより、精密な切断や厳しい許容誤差が求められる用途を実現できます。
短所
- 切断速度が遅い: 酸素による発熱反応がないため、窒素アシスト切断では、特に厚い材料の場合、切断速度が遅くなるのが一般的です。この速度の低下は、全体的な生産性に影響します。
- より高いレーザー電力要件: 窒素は切断プロセスに追加の熱を提供しないため、レーザーは材料の切断に必要なすべてのエネルギーを提供する必要があります。この要件により、エネルギー消費量と運用コストが増加する可能性があります。
- コストに関する考慮事項: 窒素は他のガスよりも高価になる可能性があり、レーザー出力要件の上昇による消費量の増加により、運用コストがさらに増加する可能性があります。
圧縮空気
利点
- コスト効率が高い: 圧縮空気は、窒素や酸素などの純粋なガスよりも入手しやすく、安価です。このため、多くのレーザー切断アプリケーション、特に薄い材料を扱うアプリケーションでは、圧縮空気が経済的な選択肢となります。
- 汎用性: 圧縮空気は、軟鋼、ステンレス鋼、アルミニウムなど、さまざまな材料の切断に使用できます。汎用性が高いため、汎用的な切断に適しています。
- 運用コストの削減: 圧縮空気は安価で広く入手可能であるため、圧縮空気を使用すると全体的な運用コストを削減でき、小規模な運用や予算重視のプロジェクトに適しています。
- 環境上の利点: 圧縮空気を使用するとボンベガスへの依存が減り、ガスの生産と輸送に伴う二酸化炭素排出量が削減され、環境上の利点がもたらされます。
短所
- 切断品質の低下: 圧縮空気中の酸素や不純物は切断品質に影響を及ぼし、切断面が粗くなり、ドロスが増加し、切断面が汚染される可能性があります。この問題は、高い表面品質や精度が求められる用途で特に顕著になります。
- 切断速度の制限: 圧縮空気による切断は、一般的に酸素による切断よりも遅くなります。特に厚い材料の場合はその傾向が顕著です。この制限は生産性に影響し、大量生産には適さない場合があります。
- 結果の一貫性の欠如: 圧縮空気による切断の品質と性能は、空気供給の組成と圧力の違いにより一貫性がなくなる可能性があります。この一貫性の欠如により、切断作業ごとに均一な結果を得ることが困難になります。
- 酸化とドロスの形成: 圧縮空気には酸素を含むさまざまなガスが含まれており、切断端で酸化とドロスの形成を引き起こす可能性があるため、望ましい結果を得るには追加の後処理が必要になります。
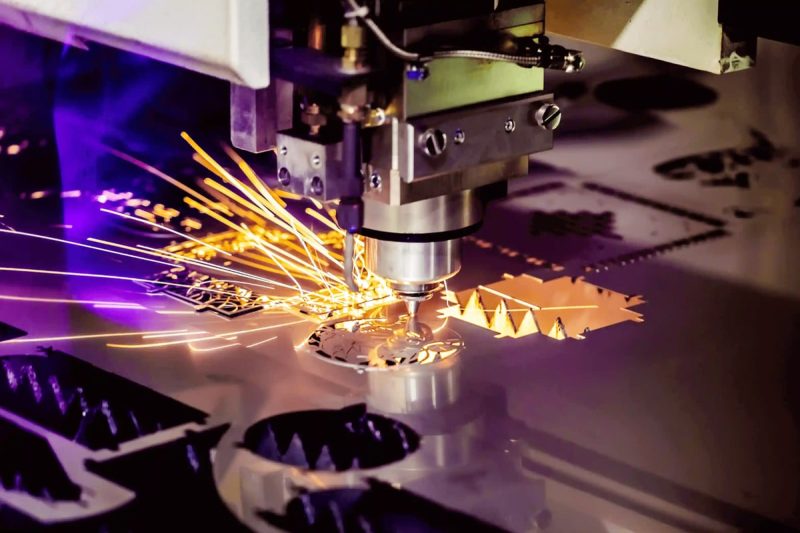
さまざまな材料への影響
炭素鋼
酸素
- 利点: 酸素は炭素鋼の切断によく使用されます。これは、酸素が材料と発熱反応を起こすためです。この反応により追加の熱が発生し、切断速度と効率が大幅に向上します。切断結果は通常、ドロスが最小限に抑えられ、きれいな仕上がりになります。また、熱が強化されるため、厚い炭素鋼の切断にも役立ちます。
- デメリット: 酸素との発熱反応により酸化が起こり、処理しないと表面仕上げが粗くなり、腐食が発生する可能性があります。また、熱影響部 (HAZ) も大きくなり、切断端付近の材料の機械的特性に影響を及ぼす可能性があります。
窒素
- 利点: 窒素は炭素鋼と反応しないため、酸化を防ぎ、きれいな酸化物のない切断面が得られます。その結果、高品質の表面仕上げと HAZ の縮小が実現し、材料の機械的特性が維持されます。
- デメリット: 発熱反応がないため、窒素アシスト切断は酸素アシスト切断よりも遅くなります。同じ切断速度を達成するには、より高いレーザー出力が必要となり、運用コストが増加します。
圧縮空気
- 利点: 圧縮空気は、炭素鋼を切断するためのコスト効率の高い代替手段です。コストとパフォーマンスのバランスが取れており、薄い炭素鋼セクションの切断に適しています。
- デメリット: 圧縮空気中の酸素は酸化やドロス形成を引き起こし、切断品質に影響を及ぼします。切断速度と品質は、通常、純酸素または窒素を使用する場合よりも低くなります。
ステンレス鋼
酸素
- 利点: 酸素はステンレス鋼の切断に使用でき、発熱反応により切断速度が速くなります。この反応により、ドロスを最小限に抑えてきれいな切断を実現できます。
- デメリット: 酸素を使用すると酸化が起こり、エッジの変色や腐食の問題が発生する可能性があります。酸化物層では、望ましい表面品質を実現するために追加の後処理が必要になる場合があります。
窒素
- 利点: 窒素はステンレス鋼の切断に最適なガスです。酸化を防ぎ、きれいで明るい、酸化物のない切断面が得られるからです。窒素の不活性な性質により、後処理を最小限に抑えながら高品質の切断面が得られます。また、窒素は熱影響部を最小限に抑えることで、材料の機械的特性を維持するのにも役立ちます。
- デメリット: 窒素は酸素よりも切断速度が遅く、より高いレーザー出力が必要なため、エネルギー消費量と運用コストが増加します。
圧縮空気
- 利点: 圧縮空気を使用すると、ステンレス鋼の薄い部分を切断できます。純粋なガスよりもコスト効率が高く、高精度を必要としない用途に適したオプションです。
- デメリット: 圧縮空気中の酸素は酸化やドロス形成を引き起こし、切断品質に影響を及ぼします。切断後には、エッジをさらに洗浄および仕上げする必要がある場合があります。
アルミニウムおよび非鉄金属
酸素
- 利点: 酸素は、アルミニウムやその他の非鉄金属のレーザー光線の反射率が高く、吸収率が低いため、通常は切断には推奨されません。ただし、場合によっては、酸素は発熱反応を促進して厚い部分の切断に役立つことがあります。
- デメリット: 酸素は激しい酸化を引き起こし、切断面が粗く多孔質になります。この酸化は材料の特性と外観に悪影響を及ぼす可能性があり、大規模な後処理が必要になります。
窒素
- 利点: 窒素はアルミニウムやその他の非鉄金属の切断に非常に効果的です。窒素は酸化を防ぎ、きれいで明るい高品質の刃先を実現します。また、窒素は熱影響部を最小限に抑え、材料の機械的特性を維持するのにも役立ちます。
- デメリット: 窒素アシスト切断は酸素を使用する場合よりも遅く、材料を切断するためにより高いレーザー出力が必要なため、運用コストが増加します。
圧縮空気
- 利点: 圧縮空気は、アルミニウムや非鉄金属の薄い部分を切断するためのコスト効率の高いオプションです。精度が重要でない用途では、満足のいく切断性能を提供できます。
- デメリット: 圧縮空気中の酸素は酸化やドロス形成を引き起こし、切断品質に影響を及ぼします。希望の仕上がりを得るには、エッジに追加の後処理が必要になる場合があります。
非金属材料
酸素
- 利点: 酸素は、木材、アクリル、プラスチックなどの非金属材料の切断に使用できます。酸素との発熱反応により、一部の材料の切断速度と効率が向上します。
- デメリット: 酸素を使用すると、木材やアクリルなどの材料が焦げて燃え、表面品質に悪影響を与える可能性があります。その結果、望ましい外観を実現するために追加の仕上げ工程が必要になる場合があります。
窒素
- 利点: 窒素は、酸化から保護する必要があるプラスチックやセラミックなどの非金属材料の切断に最適です。変色を防ぎ、熱による損傷を最小限に抑えながら、きれいで高品質のエッジを生成します。
- デメリット: 窒素アシスト切断は酸素よりも遅くなる可能性があり、望ましい切断速度を達成するにはより高いレーザー出力が必要になります。
圧縮空気
- 利点: 圧縮空気は、非金属材料を切断するためのコスト効率の高いソリューションであり、さまざまな用途に十分な切断性能を提供します。精度と品質が重要でない用途に適しています。
- デメリット: 圧縮空気中の不純物が切断品質に影響し、粗いエッジや汚染の原因となる可能性があります。切断品質と速度は、酸素や窒素などの純粋なガスの場合と同等ではない可能性があります。
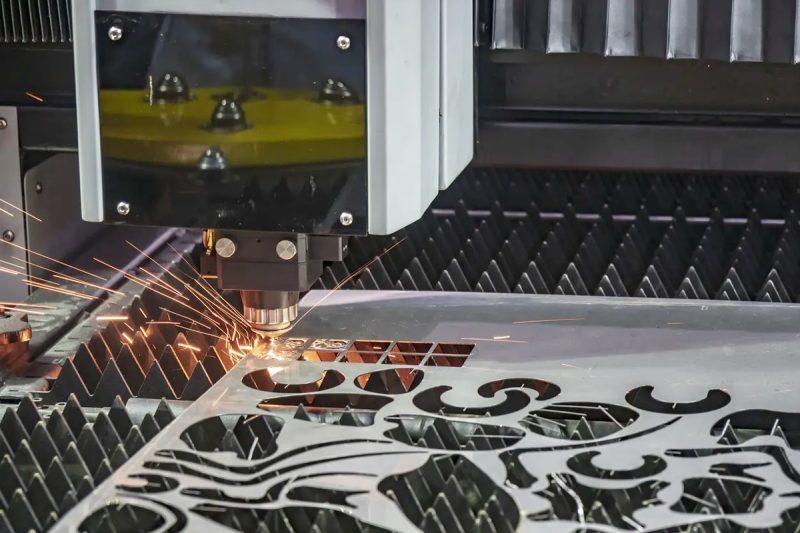
アシストガスの選択の最適化
素材の種類と厚さ
補助ガスを選択する際は、切断する材料の種類と厚さが主な考慮事項となります。材料によってガスに対する反応が異なり、切断品質と効率に影響します。
- 炭素鋼: 酸素は発熱反応を起こし、切断速度と効率を高めるため、炭素鋼の切断には酸素が第一選択肢となることがよくあります。厚い炭素鋼の場合、酸素は材料を効果的に切断するために必要な熱を供給できます。薄い炭素鋼の場合、窒素を使用すると、速度は遅くなりますが、きれいで酸化のない切断を実現できます。
- ステンレス鋼: 窒素は酸化を防ぎ、高品質で滑らかな刃先を生み出すため、ステンレス鋼の切断に最適です。非常に厚いステンレス鋼の場合、酸素を使用して切断速度を上げることができますが、酸化を引き起こすため、後処理が必要になります。
- アルミニウムおよび非鉄金属: アルミニウムおよび非鉄金属を切断する場合、酸化を防ぎ、きれいな切断を実現するために窒素が第一選択肢となります。それほど重要でない用途では、圧縮空気がコスト効率の高い代替手段となりますが、多少の酸化を引き起こす可能性があります。
- 非金属材料: プラスチック、セラミック、木材などの非金属を切断する場合、変色を防ぎ、高品質の刃先を実現するために窒素がよく使用されます。酸素を使用すると、特定の非金属をより速く切断できますが、焦げ付きや燃焼を引き起こす可能性があります。
必要なカット品質
必要な切断品質は、適切なアシストガスを選択する上で重要な要素です。精密アプリケーションでは通常、酸化が最小限でエッジが滑らかな高品質の切断が求められます。
- 高品質の表面仕上げ: 窒素は、正確でクリーン、かつ酸化のない切断を必要とする用途に最適な選択肢です。窒素は酸化を防ぎ、滑らかなエッジと高品質の表面仕上げを実現します。
- 一般的な品質: 酸素を使用すると、ドロスが最小限で高品質の切断が可能になりますが、エッジは酸化により追加の洗浄が必要になる場合があります。圧縮空気は、最高品質の表面仕上げが必要ない、それほど重要でない用途に適しています。
切断速度と効率
切断速度と効率は、使用するアシストガスの種類によって左右されます。目標は、切断品質を損なわずに可能な限り最高の速度を達成することです。
- 最大速度: 酸素の発熱反応により切断プロセスに追加の熱が加わるため、炭素鋼や厚い材料に対して最速の切断速度を実現します。
- バランスのとれた速度と品質: 窒素は、酸素に比べてレーザー出力が高く、切断速度が遅くなる場合がありますが、速度と高品質の切断のバランスが取れています。
- コスト効率の高い速度: 圧縮空気は速度とコストのバランスが取れており、中程度の切断速度と妥当な品質が許容される用途に適しています。
コストに関する考慮事項
コストはガスの選択を支援する重要な要素であり、運用費用と全体的な費用対効果に影響します。
- 運用コストの削減: 圧縮空気は入手しやすく、酸素や窒素などの純粋なガスよりも安価なため、最も経済的な選択肢です。重要度の低い材料を切断する場合や、予算の制約が優先される場合に最適です。
- 高品質と高コスト: 窒素は高価ですが、切断品質は向上します。品質が向上し、後処理の必要性が減るため、追加コストは正当化されます。
- コストと効率のバランス: Oxygen は、中程度のコストで高速切断と妥当な品質を提供する中間的なソリューションを提供します。速度と品質の両方が重要な多くの産業用途に適しています。
後処理の要件
後処理のニーズはアシストガスの選択に影響を与える可能性があります。一部のガスはよりきれいなカットを生み出し、仕上げ作業を軽減できるからです。
- 後処理が最小限: 窒素を使用すると、きれいで酸化のない切断面が得られるため、大規模な後処理の必要性が減り、仕上げ作業にかかる時間とコストが節約されます。
- 中程度の後処理: 酸素切断では、酸化物を除去して目的の表面仕上げを実現するために追加の手順が必要になる場合があります。ただし、切断速度を速くすることで、追加コストの一部を相殺できます。
- 後処理の増加: 圧縮空気によってドロスや酸化が増加する可能性があり、エッジを洗浄して仕上げるために、より大規模な後処理が必要になります。これにより、全体的な製造時間とコストが増加する可能性があります。
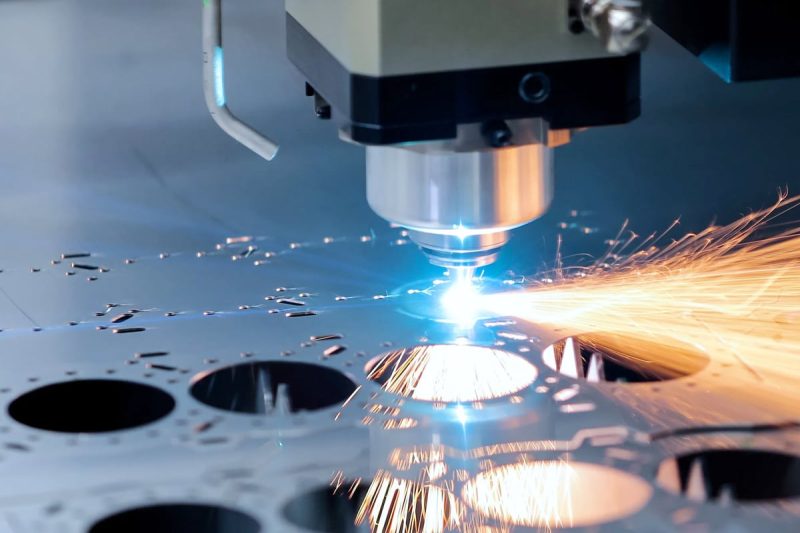
まとめ
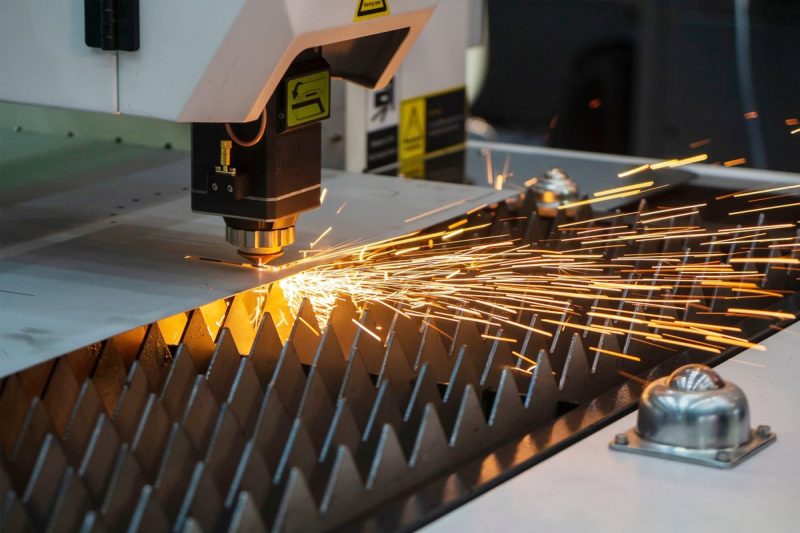
レーザー切断ソリューションを入手
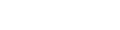
- [email protected]
- [email protected]
- +86-19963414011
- No. 3 ゾーン A、Lunzhen 工業地帯、玉城市、山東省。