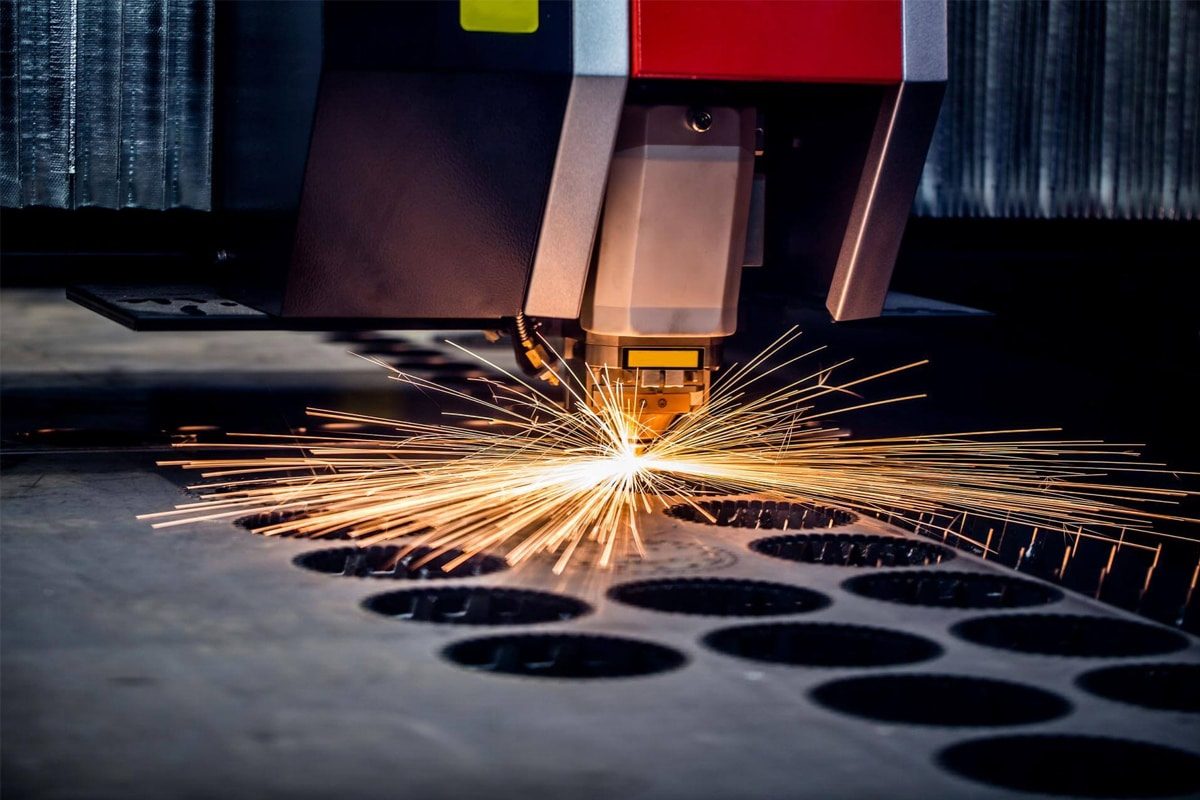
레이저 절단 속도와 효율성에 영향을 미치는 요인
In modern manufacturing, laser cutting stands out as a key technology, offering unparalleled precision and efficiency in shaping a wide range of materials. As industries continue to embrace the versatility of the laser cutting process, optimizing speed and efficiency becomes increasingly important. The process from raw materials to intricately cut final products involves a complex interplay of factors that require careful consideration. From the material’s inherent properties to the cutting machine’s complex configuration, it’s critical to fully understand the major factors that influence laser cutting speed and efficiency.
In this article, we comprehensively explore the major factors that influence laser cutting speed and efficiency, illustrating the complexity of material properties, laser parameters, cutting conditions, machine configurations, and design considerations. This exploration provides users with valuable insights that enable them to harness the full potential of laser-cutting technology and drive innovation in manufacturing processes.
목차
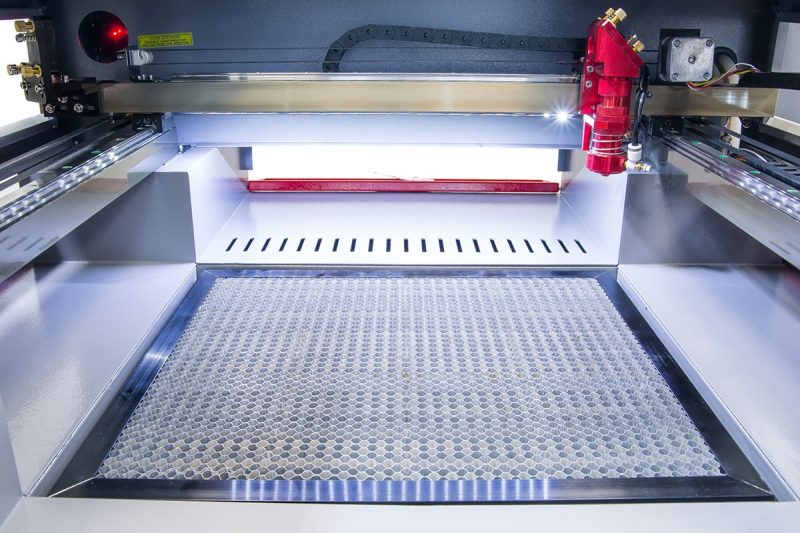
Understanding Laser Cutting Speed And Efficiency
Laser cutting, a sophisticated manufacturing technique, relies on a delicate balance of factors to achieve optimal speed and efficiency. Material properties, such as composition, thickness, and surface condition, influence cutting parameters. Laser parameters, including power density, beam quality, and focal length, determine the precision and effectiveness of cuts. Cutting conditions, like speed and assist gas selection, play vital roles in shaping cutting efficiency. Machine factors, such as system configuration and maintenance, contribute significantly to overall performance. Additionally, design considerations, such as geometric complexity and nesting optimization, impact cutting speed and efficiency. By comprehensively understanding and optimizing these factors, manufacturers can enhance the speed, accuracy, and efficiency of laser cutting processes, driving productivity and competitiveness in modern manufacturing environments.
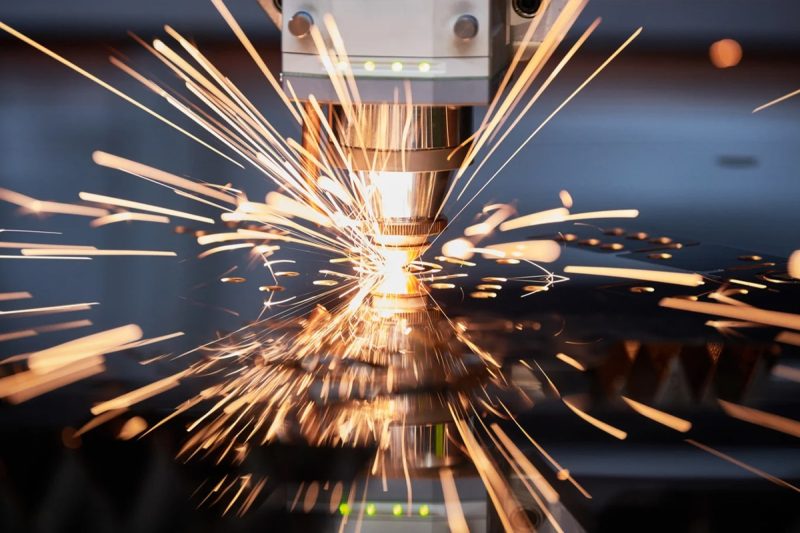
Main Factors Affecting Laser Cutting Speed And Efficiency
Laser cutting is the pinnacle of modern manufacturing precision, and a complex combination of factors determines its speed and efficiency. Delving deeper into the complexities of this change process reveals the comprehensive considerations that users must carefully navigate. Here, we explore the main factors that significantly affect laser cutting speed and efficiency.
재료 특성
- Material Type: The type of material being cut plays an important role in determining laser cutting speed and efficiency. Metals such as stainless steel, aluminum, and carbon steel have different thermal conductivities, melting points, and reflectivities that affect their response to laser cutting.
- Thickness: Material thickness directly affects cutting speed and efficiency. Thicker materials require more energy and time to cut than thinner materials. To obtain the best results on different thicknesses, the laser power, focal length, and cutting speed need to be adjusted.
- Surface Condition: Surface irregularities, such as rust, oxidation, or coating, can affect laser cutting quality and speed. For efficient cutting, the material surface may need to be prepared by cleaning or surface treatment.
레이저 매개변수
- Power Density: Laser power density is determined by the power of the laser beam focused on a given area, directly affecting cutting speed and efficiency. Higher power density allows for faster cutting speeds but requires careful calibration to prevent material damage.
- Beam Quality: The quality of the laser beam, including factors such as divergence, mode, and wavelength, will affect cutting accuracy and efficiency. The high-quality beam ensures even energy distribution, resulting in cleaner cuts and increased efficiency.
- Focal Length: The focal length of the laser lens determines the spot size and focal depth. Optimal focus selection ensures precise delivery of energy to the cutting surface, maximizing efficiency without compromising quality.
Cutting Conditions
- Cutting Speed: The rate at which the laser beam passes through the material surface significantly affects cutting efficiency. Finding the right balance between cutting speed and power can help achieve the desired results and minimize processing time.
- Auxiliary Gas Selection: Auxiliary gases such as oxygen, nitrogen, or compressed air aid in material removal and cooling during laser cutting. The choice of assist gas depends on the material type, thickness, and required edge quality, with different gases providing different levels of cutting efficiency and cleanliness.
- Nozzle Design and Alignment: Proper nozzle design and alignment help direct secondary airflow and maintain optimal separation distances. Improper alignment or worn nozzles can result in reduced cutting efficiency and quality.
Machine Factors
- Laser System Configuration: The design and functionality of the 레이저 절단기, including the beam delivery system, motion control, and automation features, affect cutting speed and efficiency. Advances in modern laser technology have increased processing speed and accuracy.
- Maintenance and Calibration: Regular maintenance, alignment, and calibration of laser cutting equipment help ensure consistent performance and extend machine life. Neglecting maintenance can result in reduced cutting efficiency, increased downtime, and expensive repairs.
Environmental Factor
- Temperature and Humidity: Ambient temperature and humidity levels can affect laser cutting performance. Extreme temperatures or high humidity can cause material deformation or interfere with laser beam propagation, affecting cut speed and quality.
- Air Quality: The presence of contaminants in the air, such as dust or particles, may interfere with laser-cutting operations. Keeping the air in your cutting environment clean helps prevent nozzle clogging and ensures consistent cutting efficiency.
Design Considerations
- Geometric Complexity: Complex designs with sharp corners, small features, or tight tolerances may require slower cutting speeds to maintain accuracy and edge quality. Advanced CAD software can optimize cutting paths for complex geometries, thereby increasing overall efficiency.
- Nesting Optimization: Effective utilization of materials through nesting optimization software can minimize material waste and reduce cutting time, ultimately improving overall process efficiency. Nesting algorithms arrange parts in the most space-efficient manner, maximizing material utilization.
- Edge Finish Requirements: The required edge quality, whether smooth, rough, or burr-free, affects cutting parameters and speed. Adjustments may be required to meet specific surface finish standards to ensure the final product meets quality standards.
In the complex process of laser cutting, manufacturers must carefully consider and balance these factors to unlock the full potential of this advanced technology. A detailed understanding of material interactions, laser dynamics, cutting conditions, machine configurations, environmental effects, and design complexities helps achieve optimal laser cutting speed and efficiency in modern manufacturing.
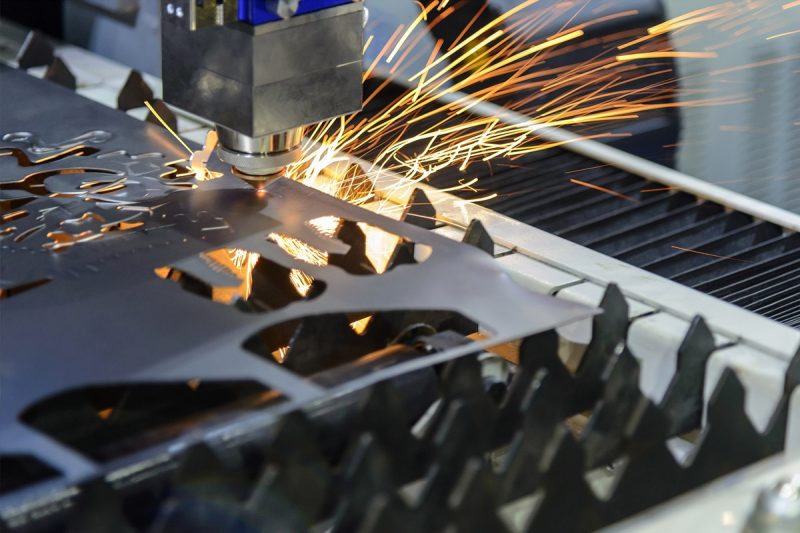
How To Improve Laser Cutting Speed And Efficiency
Optimizing laser cutting speed and efficiency requires a strategic approach that incorporates material considerations, machine setup, and operational best practices. Here is a detailed guide on how to enhance the performance of your laser-cutting process:
Material Selection And Preparation
- Choose The Best Material: Consider factors such as thermal conductivity and reflectivity and choose a material with good laser cutting characteristics.
- Material Thickness Optimization: Balance cut speed and quality with the right thickness for the intended application.
- Surface Preparation: Ensures material surfaces are clean and free of contaminants, optimizing efficiency by preventing interference during cutting.
Laser Parameter Fine-Tuning
- Power Density Calibration: Adjust laser power density based on material type and thickness to prevent excessive heat generation.
- Optimize Beam Quality: Fine-tune beam quality parameters to achieve a balance between accuracy and cutting speed.
- Focus Adjustment: Optimize focus settings for different materials and thicknesses, ensuring precise energy delivery to the cutting surface.
Optimization Of Cutting Conditions
- Cutting Speed Selection: Fine-tune cutting speed based on material type, thickness, and desired edge quality.
- Auxiliary Gas Management: Select appropriate auxiliary gas according to material requirements. Optimal gas selection improves material removal and cooling, resulting in more efficient cutting.
- Nozzle Maintenance: Regularly inspecting and maintaining nozzles to prevent wear and ensure consistent airflow helps improve cutting performance.
Advanced Machine Configuration
- Upgrade Laser System: Invest in a modern laser cutting machine with advanced features, improved motion control, and enhanced automation.
- Utilize Advanced Controls: Utilize an advanced control system to fine-tune cutting parameters in real-time to maximize operating efficiency.
- Implement Dynamic Focus Technology: Explore machines with dynamic focus capabilities to maintain optimal cutting conditions on different material surfaces and thicknesses.
Routine Maintenance And Calibration
- Regular Equipment Inspections: Establish a routine maintenance schedule that includes checking laser alignment, calibration, and overall equipment health.
- Prompt Problem Solving: Promptly address any discovered issues to prevent downtime and ensure continued reliable laser cutting performance.
환경 관리
- Temperature and Humidity Management: Keep the temperature and humidity of the cutting environment consistent to prevent material warping and ensure stable laser performance.
- Air Quality Maintenance: Implement an effective air filtration system to reduce airborne contaminants, maintain nozzle integrity, and maintain cutting efficiency.
Strategic Design Considerations
- Simplify Geometric Complexity: Where feasible, simplify complex designs to reduce cutting time and increase efficiency.
- Nest Optimization: Employ nest optimization software to maximize material utilization, minimize waste, and reduce overall cutting time.
- Edge Finish Planning: The process of adjusting cutting parameters based on desired edge finish requirements to optimize the process for specific surface features.
Employee Training And Skills Development
- Operator Training: Provide operators with comprehensive training on the intricacies of laser cutting, allowing them to make informed decisions for optimal performance.
- Skills Enhancement Program: Invest in ongoing skills development programs to keep operators up to date on new technologies and best practices.
By systematically addressing these issues, manufacturers can significantly increase laser cutting speed and efficiency, thereby increasing productivity, reducing operating costs, and delivering high-quality end products in a variety of industrial applications.
요약하다
The speed and efficiency of laser cutting are multifaceted and influenced by a myriad of factors ranging from material properties to machine configurations and design considerations. As technology continues to evolve, manufacturers must stay abreast of these factors and implement best practices to optimize their laser-cutting processes. This comprehensive exploration aims to provide a holistic understanding of the intricate dynamics at play in laser cutting, empowering manufacturers to make informed decisions and drive advancements in this pivotal field.
AccTek 레이저 provides users who optimize laser cutting speed and efficiency with cutting-edge solutions tailored to meet different industrial needs. Committed to innovation and excellence, we offer state-of-the-art laser cutting machines equipped with advanced features such as dynamic focus technology, precision beam control, and smart cutting software. These solutions enable companies to achieve faster processing speeds, higher productivity, and superior cut quality across a variety of materials and applications. With AccTek Laser, users can increase production capabilities and stay ahead of the curve in today’s competitive market landscape.
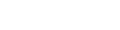
연락처 정보
- [email protected]
- [email protected]
- +86-19963414011
- No. 3 Zone A, Lunzhen Industrial Zone, Yucheng City, Shandong Province.
레이저 솔루션 받기