Laser Cleaning Machine
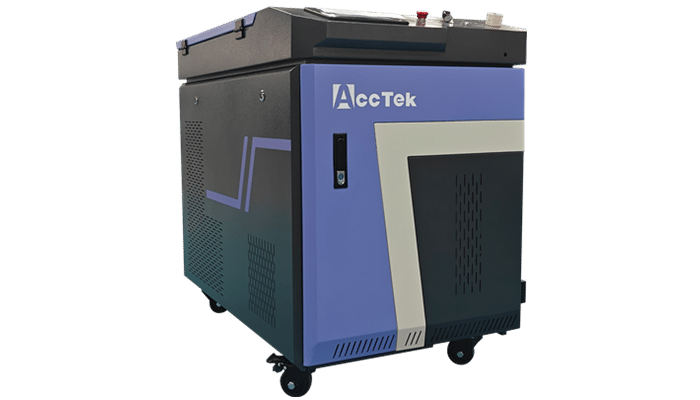
Product Range
-
Handheld Laser Cleaning Machine
Rated 4.75 out of 5$3,200.00 – $6,400.00 Select options This product has multiple variants. The options may be chosen on the product page -
Laser Rust Removal Machine
Rated 4.75 out of 5$3,200.00 – $6,400.00 Select options This product has multiple variants. The options may be chosen on the product page -
Portable Laser Cleaning Machine
Rated 5.00 out of 5$3,100.00 – $6,300.00 Select options This product has multiple variants. The options may be chosen on the product page -
Pulse Laser Cleaning Machine
Rated 4.75 out of 5$5,900.00 – $65,300.00 Select options This product has multiple variants. The options may be chosen on the product page -
Luggage Pulse Laser Cleaning Machine
Rated 4.75 out of 5$6,500.00 – $16,800.00 Select options This product has multiple variants. The options may be chosen on the product page -
Backpack Pulse Laser Cleaning Machine
Rated 4.75 out of 5$6,800.00 – $9,100.00 Select options This product has multiple variants. The options may be chosen on the product page
Optional Laser Cleaning Machine Power
Materials and Surfaces That Can Be Cleaned
Laser Cleaning VS. Other Methods
Laser Cleaning vs. Sandblasting
Laser cleaning is a non-abrasive, contact-free process that minimizes the risk of surface damage, unlike sandblasting, which can erode the material being cleaned. Laser technology is more precise and eliminates the need for abrasive media, making it a cleaner, environmentally friendly alternative for surface cleaning.
Laser Cleaning vs. Chemical Cleaning
Chemical cleaning uses harsh solvents and acids, which can be harmful to both workers and the environment. In contrast, laser cleaning requires no chemicals, making it safer, more sustainable, and cost-effective, while also eliminating waste disposal and the risk of corrosion from leftover residues.
Laser Cleaning vs. High-Pressure Water Cleaning
While high-pressure water cleaning is effective for certain applications, it can be messy and often ineffective on hard-to-remove contaminants like rust and coatings. Laser cleaning, on the other hand, provides precision and targeted cleaning without the need for water, drying, or additional post-treatment steps, making it faster and more efficient.
Why Choose AccTek Laser
Advanced Laser Technology
We use the latest laser technology to provide precise, efficient, and reliable cleaning solutions. Our machines are engineered for high-performance cleaning, ensuring superior results across a wide range of materials and contaminants.
Environmentally Friendly
AccTek Laser machines offer a sustainable cleaning solution. With no chemicals, no abrasive materials, and minimal waste, our technology reduces environmental impact while maintaining the highest cleaning standards.
Cost-Effective Solutions
By eliminating the need for consumables such as chemicals, abrasives, or solvents, our laser cleaning machines help you cut costs in the long term. The durability and low maintenance of our machines further enhance cost-effectiveness.
Versatility Across Industries
Whether in automotive, aerospace, manufacturing, or any other industry, our laser cleaning machines are designed for versatile use. They can handle a variety of materials and contaminants, making them ideal for a wide array of applications.
Precision and Safety
AccTek Laser's machines ensure a non-contact, precise cleaning process, reducing the risk of damage to delicate surfaces. The user-friendly design and safety features ensure your operators can work with confidence and efficiency.
Exceptional Customer Support
We provide comprehensive customer support before, during, and after the sale. Our dedicated team offers expert guidance on machine selection, operation, and maintenance, ensuring your investment performs at its best.
Frequently Asked Questions
Do Laser Cleaning Machines Work?
How Much Are Laser Cleaning Machines?
- Power and Capabilities: Higher-powered machines capable of removing tougher contaminants or covering larger surface areas will generally be more expensive.
- Size and Type: Standalone handheld units are typically less expensive than larger, automated systems designed for industrial use.
- Brand and Quality: Well-known brands with a reputation for quality and reliability may command higher prices.
- Additional Features: Machines with advanced features such as automation, multiple laser heads, or specialized optics may cost more.
- Market Demand: Prices may vary based on factors such as supply and demand dynamics, as well as fluctuations in the manufacturing and technology sectors.
What Are The Ongoing Operating Costs of Laser Cleaning Machines?
- Electricity: Laser cleaning machines require electricity to power the laser source, cooling systems, and other components. The exact electricity consumption will depend on the power of the laser, the duration of use, and any additional systems such as ventilation or cooling.
- Consumables: While laser cleaning itself doesn’t typically require consumables like chemicals or abrasive materials, there may be ancillary consumables needed for maintenance purposes. This could include items such as protective lenses, filters, or gases used in the laser system.
- Maintenance: Regular maintenance is necessary to ensure the continued performance and reliability of the laser cleaning machine. This may involve tasks such as cleaning optical components, replacing worn parts, calibrating the system, and servicing the laser source. Maintenance costs can vary depending on the complexity of the machine and the frequency of use.
- Operator Training: Proper operator training helps ensure the safe and efficient operation of laser cleaning machines. Training costs may include initial training sessions as well as ongoing education to stay updated on best practices and safety procedures.
- Safety Equipment: Depending on the application and local regulations, additional safety equipment such as personal protective gear or safety interlocks may be required. These items incur additional costs.
- Downtime: In the event of equipment failure or maintenance requirements, there may be associated costs related to downtime, including lost productivity and potential delays in production schedules.
Why Are Laser Cleaning Machines So Expensive?
- Advanced Laser Technology: Laser cleaning machines use sophisticated laser sources, such as pulse laser generators, and continuous laser generators, which are costly to produce. These lasers need to be highly engineered to provide the precision, power, and longevity required for industrial applications. The cost of these components is a significant portion of the overall price.
- Precision and Efficiency: Laser cleaning systems are designed to offer highly precise and efficient cleaning. This level of accuracy and control requires advanced optics, sensors, and software that ensure the laser beam can target specific areas of the surface. The technology needed to achieve such precision drives up the cost.
- Non-Contact Cleaning: One of the primary advantages of laser cleaning is that it’s a non-contact process, meaning there is no direct physical interaction with the material being cleaned. This results in less wear and tear on the machine, reducing long-term maintenance costs but requiring more complex engineering and higher upfront investment.
- Customization and Versatility: Laser cleaning machines are highly customizable to meet the specific needs of different industries (e.g., aerospace, automotive, manufacturing). Custom configurations, varying power levels, and additional features, like programmable controls, sensors, or automation, increase the cost of the machines.
- Durability and Longevity: Laser cleaning machines are built for long-term use in demanding environments. They need to be robust, reliable, and able to withstand harsh conditions such as high temperatures, dust, and contaminants. The materials and engineering involved in ensuring durability add to the cost.
- Research and Development: The technology behind laser cleaning is continually evolving. Companies invest heavily in research and development to improve performance, increase energy efficiency, and make the systems more user-friendly. These costs are often reflected in the pricing of the final product.
- Low Operational Costs: Although the initial investment is high, laser cleaning machines offer lower operational costs over time. They don’t require consumables like abrasives or chemicals, reducing recurring expenses. This makes them an attractive long-term investment, though it may take time to recoup the initial cost.
What Are The Disadvantages of Laser Cleaning?
- Initial Cost: Laser cleaning machines can be expensive to purchase compared to traditional cleaning methods. The initial investment may be prohibitive for some businesses or applications.
- Safety Concerns: Laser cleaning involves the use of high-intensity laser beams, which can pose safety risks if not used properly. Operators need to be trained in laser safety protocols, and appropriate safety measures must be in place to protect against hazards such as eye damage or fires.
- Limited Materials: While laser cleaning is effective for many materials, some surfaces may be difficult or impossible to clean with lasers. Certain materials, such as transparent plastics or materials with highly reflective surfaces, may not respond well to laser cleaning.
- Surface Damage: While laser cleaning is generally gentle on surfaces, there is still a risk of damaging delicate materials or substrates if the laser parameters are not carefully controlled. For example, excessive heat or power levels could cause thermal damage or changes in material properties.
- Environmental Considerations: While laser cleaning itself is a clean process that doesn’t involve the use of chemicals or produce hazardous waste, the energy consumption of the laser system and associated equipment can have environmental impacts. Additionally, some laser systems may require cooling systems that consume water or other resources.
- Limited Reach and Accessibility: Laser cleaning requires line-of-sight access to the surface being cleaned. This means that it may not be suitable for cleaning complex or hard-to-reach areas where direct access is limited.
- Complexity: Laser cleaning machines can be complex pieces of equipment that require specialized knowledge to operate and maintain. This complexity can lead to higher training and maintenance costs.
- Regulatory Compliance: Depending on local regulations and industry standards, there may be specific requirements or restrictions regarding the use of laser cleaning equipment. Compliance with these regulations may add complexity or cost to the implementation of laser cleaning processes.
Will Laser Cleaning Damage Material?
- Material Sensitivity: Some materials are more sensitive to heat and energy than others. For example, certain plastics, composite materials, or heat-sensitive coatings may be more prone to damage from laser cleaning. Understanding the characteristics of the material being cleaned can help adjust laser parameters accordingly.
- Laser Settings: The power, pulse duration, and other laser parameters must be optimized for the specific material and contaminants being cleaned. Using too much power or applying the laser for too long can result in excessive heating and potential damage to the surface.
- Surface Characteristics: The condition and characteristics of the surface being cleaned can also affect the likelihood of damage. Rough or uneven surfaces may absorb laser energy differently, leading to localized heating and potential damage.
- Surface Coatings: Laser cleaning can remove surface coatings such as paint or rust, but it’s important to consider the compatibility of these coatings with the laser process. Some coatings may be more difficult to remove or may require specific laser parameters to avoid damaging the underlying substrate.
- Quality of Equipment and Operator Skill: The quality of the laser cleaning equipment and the skill level of the operator play important roles in preventing material damage. Proper training and experience enable safe and effective operation of equipment.
What Is The Maximum Cleaning Area That Laser Cleaning Machines Can Handle?
- Continuous Fiber Laser Cleaning Machines
- Standard cleaning width: 270mm
- Machines Below 2kW: Maximum cleaning width of 450mm
- Machines Above 2kW: Maximum cleaning width of 600mm
- Pulse Laser Cleaning Machines
- 100W Pulse Laser Cleaning Machine: Standard Cleaning Area: 100x100mm, Optional Cleaning Areas: 130x130mm, 150x150mm
- 200W Pulse Laser Cleaning Machine: Standard Cleaning Area: 130x130mm, Optional Cleaning Areas: 150x150mm
- 300-2000W Pulse Laser Cleaning Machines: Standard Cleaning Area: 150x150mm, Optional Cleaning Areas: 180x180mm, 290x290mm
How To Maintain Laser Cleaning Machines?
- Regular Cleaning: Keep the exterior of the machine clean and free from dust, debris, and any other contaminants that could interfere with its operation.
- Optical Component Inspection and Cleaning: Periodically inspect and clean the optical components, including lenses, mirrors, and windows, to ensure they are free from dirt, smudges, or damage that could affect the laser beam quality. Use appropriate cleaning materials and techniques to avoid scratching or damaging the optical surfaces.
- Check Cooling Systems: If the laser cleaning machine has cooling systems, such as water cooling or air cooling, regularly check them for proper functioning. Monitor coolant levels, clean filters, and perform any required maintenance according to the manufacturer’s recommendations.
- Inspect and Replace Consumable Parts: Some components of the laser cleaning machine, such as protective windows or filters, may need periodic inspection and replacement as they wear out over time. Follow the manufacturer’s guidelines for the replacement of consumable parts.
- Monitor Laser Parameters: Regularly check and calibrate laser parameters such as power output, pulse duration, and beam quality to ensure they are within the specified range for optimal cleaning performance. Adjust as necessary to maintain consistent cleaning results.
- Software Updates: Keep the machine’s control software up to date by installing any available updates or patches provided by the manufacturer. Updated software can improve performance, add new features, and address potential security vulnerabilities.
- Operator Training: Ensure that operators are properly trained in the safe and effective operation of the laser cleaning machine. Provide refresher training as needed to keep operators up to date on best practices and safety procedures.
- Documentation and Records: Maintain detailed records of maintenance activities, including inspections, repairs, and part replacements. This documentation can help track the machine’s maintenance history and identify any recurring issues that may need attention.
- Safety Checks: Regularly inspect safety features such as interlocks, emergency stop buttons, and warning indicators to ensure they are functioning correctly. Address any issues promptly to maintain a safe working environment.
Related Resources
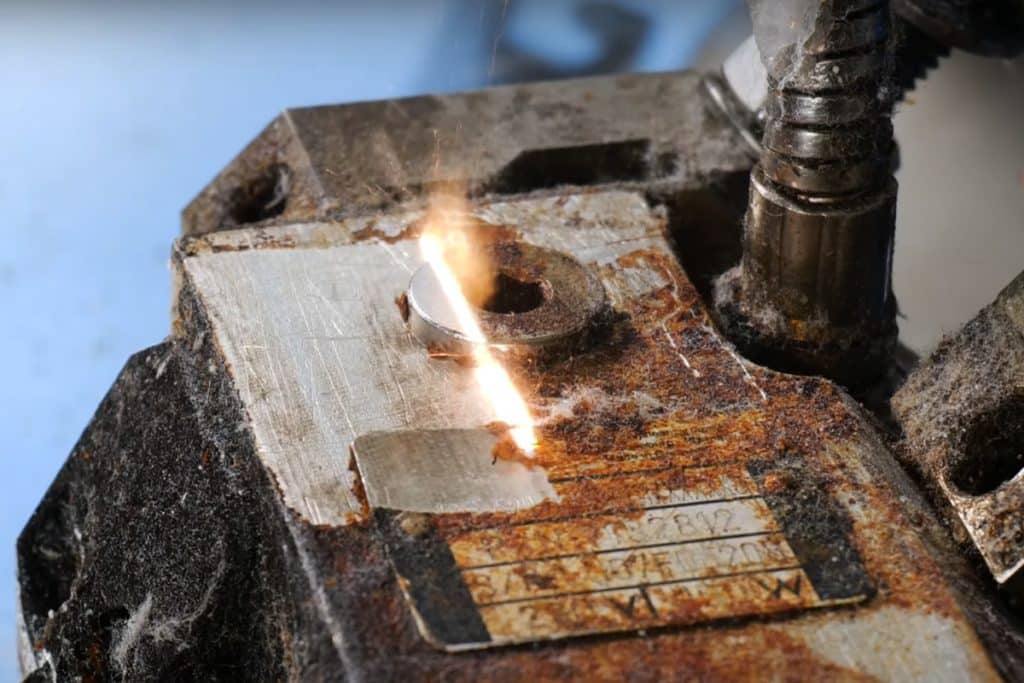
How Fast Is Laser Cleaning?
This article mainly discusses the principles of laser cleaning technology, factors affecting speed, and methods to improve cleaning efficiency, to help companies optimize laser cleaning processes and improve overall production
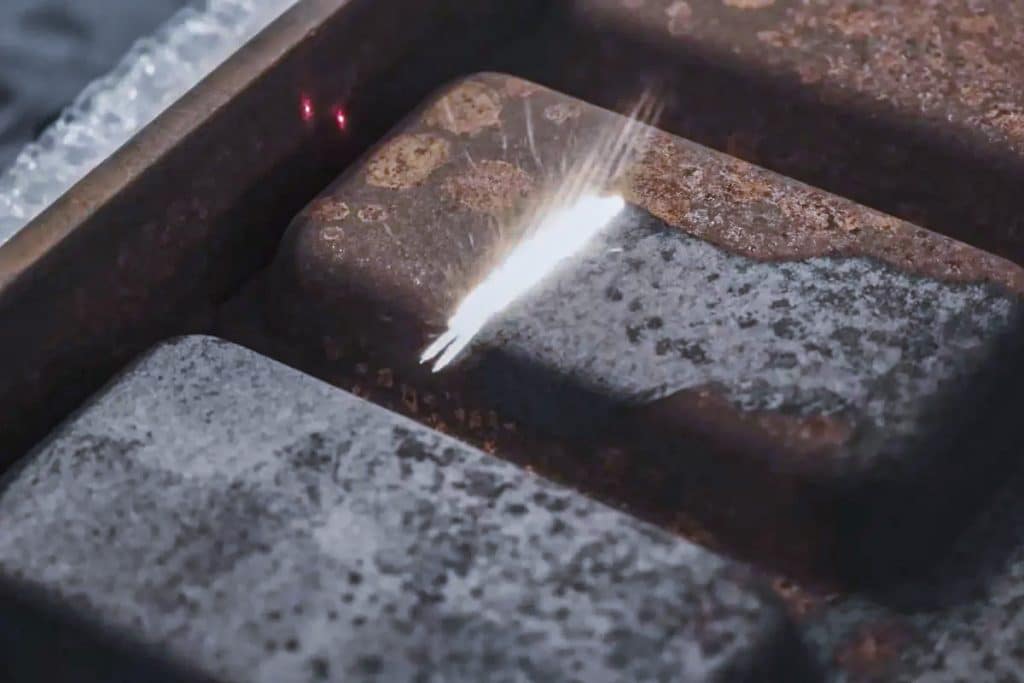
How Can Laser Cleaning Help Reduce Waste and Improve Sustainability?
This article will take a deep look at how laser cleaning technology can reduce waste, protect resources, and promote new possibilities for sustainable development!
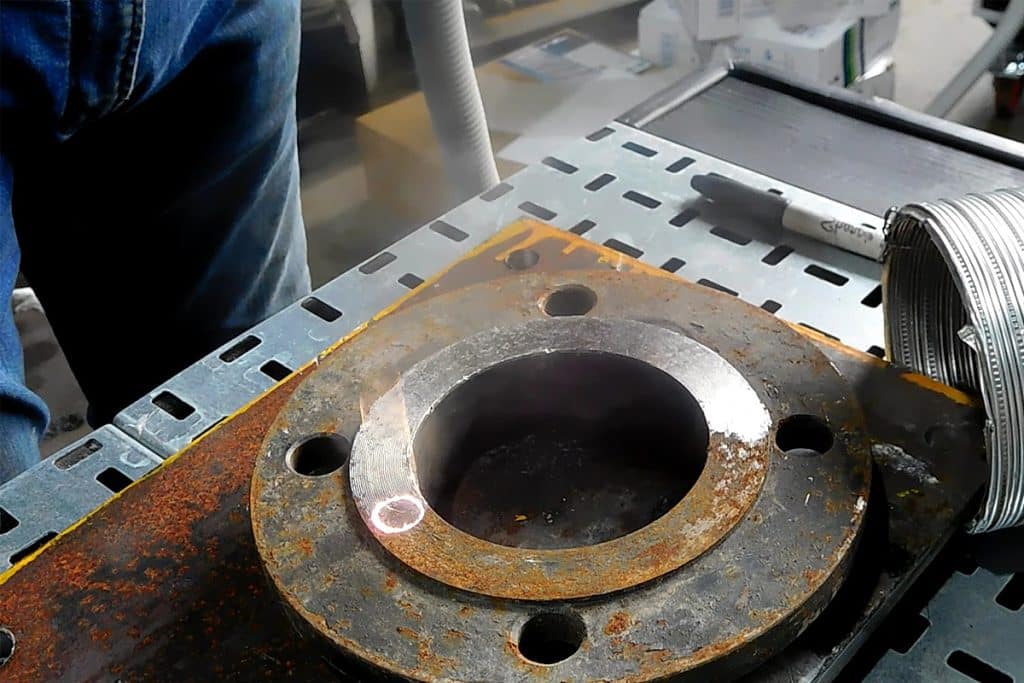
Advantages and Limitations of Pulse Laser Cleaning Machines
This article mainly discusses the principles and advantages of pulsed laser cleaning technology, focusing on its high efficiency, non-contact, and environmentally friendly characteristics, and provides guidance for selecting laser cleaning