Continuous Laser Cleaning Machine
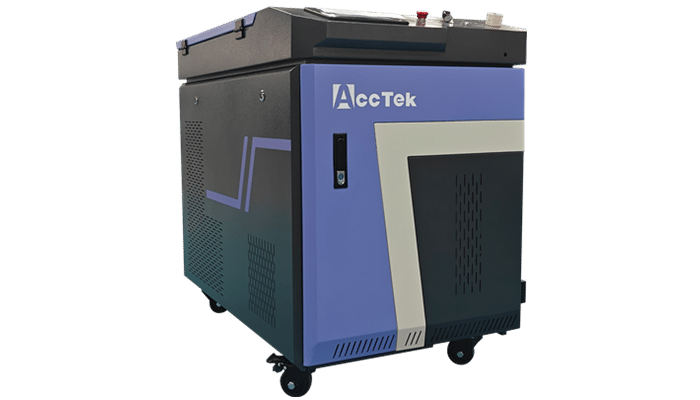
Product Range
-
Handheld Laser Cleaning Machine
Rated 4.75 out of 5$3,200.00 – $6,400.00 Select options This product has multiple variants. The options may be chosen on the product page -
Laser Rust Removal Machine
Rated 4.75 out of 5$3,200.00 – $6,400.00 Select options This product has multiple variants. The options may be chosen on the product page -
Portable Laser Cleaning Machine
Rated 5.00 out of 5$3,100.00 – $6,300.00 Select options This product has multiple variants. The options may be chosen on the product page
Optional Continuous Laser Cleaning Machine Power
Materials and Surfaces That Can Be Cleaned
Laser Cleaning VS. Other Methods
Laser Cleaning vs. Sandblasting
Laser cleaning is a non-contact process that avoids the abrasive surface damage associated with sandblasting. It removes rust, paint, and contaminants without causing wear, preserving the integrity of the material. Additionally, it eliminates the need for media disposal, making it more eco-friendly and cost-efficient.
Laser Cleaning vs. Chemical Cleaning
Chemical cleaning relies on harsh solvents that pose risks to both human health and the environment. In contrast, laser cleaning requires no chemicals, reducing exposure to hazardous substances while offering a more sustainable solution. It effectively cleans surfaces without leaving chemical residues.
Laser Cleaning vs. High-Pressure Water Cleaning
High-pressure water cleaning can be less effective on certain materials and requires post-drying. Laser cleaning, however, is a dry, non-contact process that removes contaminants with precision, without mess and water usage, making it ideal for intricate or sensitive components.
Why Choose AccTek Laser
Advanced Laser Technology
We use the latest laser technology to provide precise, efficient, and reliable cleaning solutions. Our machines are engineered for high-performance cleaning, ensuring superior results across a wide range of materials and contaminants.
Environmentally Friendly
AccTek Laser machines offer a sustainable cleaning solution. With no chemicals, no abrasive materials, and minimal waste, our technology reduces environmental impact while maintaining the highest cleaning standards.
Cost-Effective Solutions
By eliminating the need for consumables such as chemicals, abrasives, or solvents, our laser cleaning machines help you cut costs in the long term. The durability and low maintenance of our machines further enhance cost-effectiveness.
Versatility Across Industries
Whether in automotive, aerospace, manufacturing, or any other industry, our laser cleaning machines are designed for versatile use. They can handle a variety of materials and contaminants, making them ideal for a wide array of applications.
Precision and Safety
AccTek Laser's machines ensure a non-contact, precise cleaning process, reducing the risk of damage to delicate surfaces. The user-friendly design and safety features ensure your operators can work with confidence and efficiency.
Exceptional Customer Support
We provide comprehensive customer support before, during, and after the sale. Our dedicated team offers expert guidance on machine selection, operation, and maintenance, ensuring your investment performs at its best.
Frequently Asked Questions
What Are Continuous Lasers?
- Steady Output: It produces a continuous, unbroken beam of light, as opposed to pulses or bursts.
- Stable Power: The power output remains constant, which is crucial for processes needing uniform energy application.
- Various Wavelengths: Continuous lasers are available in a range of wavelengths, suitable for different applications.
- High Precision: They offer high precision in applications like cutting, welding, and cleaning, where consistent energy is required.
What Is The Difference Between Pulse Laser and Continuous Laser?
- Emission Mode
- Pulse Laser: Emits light in short, intense bursts or pulses. Each pulse lasts for a very short duration, typically ranging from femtoseconds to milliseconds.
- Continuous Laser: Emits a continuous, unbroken beam of light. The output is steady and uninterrupted over time.
- Energy Delivery
- Pulse Laser: Delivers energy in concentrated, high-power bursts. This is useful for applications requiring high peak power, such as material ablation, medical procedures, and precise cutting.
- Continuous Laser: Delivers energy at a constant, lower power level. This is ideal for applications needing uniform energy distribution over a period, such as continuous cutting, welding, and surface cleaning.
- Heat Management
- Pulse Laser: Generates less heat overall because the energy is delivered in short bursts, allowing cooling between pulses. This reduces thermal effects on the material being processed.
- Continuous Laser: Generates more heat due to the constant energy output. Effective cooling systems are often required to manage the heat and prevent damage to the material.
- Applications
- Pulse Laser: Used in applications requiring high precision and minimal thermal impact, such as micromachining, medical treatments (e.g., laser eye surgery), and scientific research.
- Continuous Laser: Suited for applications where continuous energy application is needed, such as industrial cleaning, continuous welding, and long-term material processing.
- Peak Power
- Pulse Laser: Can achieve extremely high peak powers during each pulse, even if the average power is relatively low.
- Continuous Laser: The power output is consistent and generally lower than the peak power of a pulsed laser.
How Do Continuous Laser Cleaning Machines Work?
- Laser Generation: The machine generates a continuous wave (CW) laser beam using a laser source. The wavelength and power of the laser are selected based on the type of material and the contaminants to be removed.
- Beam Delivery: The continuous laser beam is directed through an optical system that includes lenses and mirrors to focus and guide the laser precisely onto the surface to be cleaned.
- Surface Interaction: When the laser beam strikes the surface, its energy is absorbed by the contaminants, causing them to rapidly heat up and vaporize or sublimate. This process effectively breaks the bond between the contaminants and the underlying material.
- Material Removal: As the contaminants are vaporized or converted into small particles, they are either blown away by an integrated air or gas flow or collected using a vacuum system. The underlying material remains mostly unaffected because the laser parameters are carefully controlled to target only the contaminants.
- Continuous Operation: The machine is designed for continuous operation, meaning the laser beam is constantly emitted and the cleaning process occurs without interruption. This ensures high efficiency and consistent cleaning over large areas or extended periods.
- Control System: The machine includes a user-friendly control interface that allows operators to adjust the laser parameters such as power, focus, and scanning speed to optimize the cleaning process for different materials and contamination levels.
- Scanning Mechanism: A scanning head, often equipped with galvanometer mirrors, moves the laser beam back and forth across the surface in a controlled pattern, ensuring thorough and uniform cleaning.
- Safety Measures: Continuous laser cleaning machines are equipped with safety features such as enclosures, interlocks, and sensors to protect operators from laser exposure and ensure safe operation.
What Are The Disadvantages of Continuous Laser Cleaning Machines?
- High Initial Cost: The purchase and setup cost of continuous laser cleaning machines can be significant compared to traditional cleaning methods. This can be a barrier for small businesses or those with limited budgets.
- Complexity and Training: Operating and maintaining these machines require specialized training. Employees need to be well-versed in handling laser equipment, adjusting settings, and following safety protocols, which can involve additional training costs and time.
- Energy Consumption: Continuous laser systems can consume a substantial amount of energy, leading to higher operational costs. Efficient energy management is necessary to mitigate these costs.
- Material Limitations: While laser cleaning is effective on many materials, it may not be suitable for all types of surfaces or contaminants. Some materials may not absorb laser energy effectively, making the cleaning process less efficient or even ineffective.
- Potential Surface Damage: Although laser cleaning is non-abrasive, improper use or incorrect settings can potentially damage delicate or sensitive surfaces. Careful calibration and control are required to avoid this risk.
- Size and Portability: Continuous laser cleaning machines can be bulky and may lack portability. This can limit their use in certain environments or applications where mobility and flexibility are crucial.
- Maintenance Requirements: Despite having fewer consumables than traditional methods, laser cleaning machines still require regular maintenance to ensure optimal performance. This includes cleaning optics, calibrating the system, and replacing parts when necessary.
- Safety Concerns: Lasers pose inherent safety risks, including eye and skin injuries. Comprehensive safety measures, such as protective eyewear, enclosures, and interlock systems, are essential to prevent accidents, adding to the complexity of operation.
- Environmental and Health Risks: The process of laser cleaning can generate fumes and particles that may need to be managed through proper ventilation and filtration systems to prevent environmental and health hazards.
- Initial Setup and Calibration: The setup and calibration of the machine can be time-consuming. Ensuring the correct parameters for different materials and contaminants requires expertise and precise adjustments.
Are There Any Limitations to Using Continuous Laser Cleaning Machines?
- Material Compatibility: Not all materials can be effectively cleaned with laser technology. Materials that do not absorb laser energy well, such as certain plastics or glass, may not respond effectively to laser cleaning.
- Surface Damage Risk: While laser cleaning is generally non-abrasive, improper settings or techniques can damage delicate or sensitive surfaces. Careful calibration and control are necessary to avoid surface damage.
- Cost: The initial investment for purchasing and setting up a continuous laser cleaning machine can be high. This includes the cost of the machine, installation, and training for operators.
- Energy Consumption: Continuous laser systems can consume significant amounts of energy, which may result in higher operational costs.
- Safety Concerns: Lasers pose inherent safety risks, including potential eye and skin injuries. Comprehensive safety measures, such as protective eyewear, enclosures, and interlock systems, are essential to prevent accidents, adding to the complexity of operation.
- Limited Portability: These machines can be bulky and may not be easily portable. This limits their use in certain environments where mobility and flexibility are crucial.
- Ventilation and Filtration Needs: The process of laser cleaning can generate fumes and particles that need to be managed through proper ventilation and filtration systems to prevent environmental and health hazards.
- Maintenance Requirements: Continuous laser cleaning machines require regular maintenance to ensure optimal performance. This includes cleaning optics, calibrating the system, and replacing parts when necessary.
- Surface Reflectivity: Highly reflective surfaces can pose challenges for laser cleaning, as they can reflect the laser beam away from the target area, reducing the effectiveness of the cleaning process.
- Initial Setup and Calibration: The setup and calibration of the machine can be time-consuming. Ensuring the correct parameters for different materials and contaminants requires expertise and precise adjustments.
- Thickness of Contaminants: Very thick layers of contaminants may require multiple passes or may not be completely removable with laser cleaning alone, necessitating additional cleaning methods.
What Is The Service Life of Continuous Laser Cleaning Machines?
- Laser Source Lifetime: The laser source is one of the most critical components of the cleaning machine. Fiber lasers, commonly used in continuous laser cleaning systems, typically have a service life of 25,000 to 30,000 hours of operation, which translates to several years of use under normal conditions.
- Maintenance and Upkeep: Regular maintenance, including cleaning and inspecting the cooling system, optics, and other components, can significantly extend the lifespan of the machine. Following manufacturer guidelines for maintenance schedules is crucial to ensure optimal performance over time.
- Operational Environment: Machines used in harsh environments, such as high temperatures, dust, or moisture, may experience a shorter service life. Proper installation in a clean, controlled environment can help maximize durability.
- Quality of Components: High-quality components and advanced engineering typically result in longer-lasting machines. Choosing a well-built, reputable model is essential for achieving a longer service life.
- Operational Hours: The more frequently the machine is used, the shorter its lifespan may be. However, if used within its rated operating hours and with adequate cooling and rest, the machine can last for a long time.
What Maintenance Is Required for Continuous Laser Cleaning Machines?
- Regular Cleaning
- Optics: Clean the laser optics (lenses, mirrors) regularly to remove dust, debris, and any residues. Dirty optics can reduce laser efficiency and cause beam distortion.
- Housing and Ventilation: Keep the machine’s housing and ventilation systems clean to prevent overheating and dust accumulation.
- Inspection
- Laser Source: Periodically inspect the laser source for any signs of wear or damage. Ensure that it is functioning within the specified parameters.
- Cooling System: Check the cooling system (if applicable) to ensure it is working properly. Look for any leaks or blockages in the coolant lines.
- Electrical Connections: Inspect electrical connections and wiring for signs of wear, corrosion, or loose connections.
- Alignment
- Beam Alignment: Regularly check and adjust the laser beam alignment to ensure accurate targeting and efficient cleaning.
- Scanning System: Verify the calibration of the scanning system (galvanometers or mirrors) to maintain precise movement and positioning of the laser beam.
- Component Replacement
- Worn Parts: Replace worn parts such as protective windows, filters, and seals as needed to maintain machine performance and prevent contamination.
- Consumables: Replenish consumables such as lubricants and coolant fluids according to the manufacturer’s recommendations.
- Software Updates
- Firmware and Software: Keep the machine’s firmware and software up to date with the latest versions provided by the manufacturer. This ensures optimal performance and access to new features or improvements.
- Safety Checks
- Safety Interlocks: Test safety interlocks and emergency stop functions regularly to ensure they are functioning correctly.
- Protective Enclosures: Inspect protective enclosures and barriers for integrity and proper functioning.
- Performance Monitoring
- Output Power: Regularly measure the laser’s output power to ensure it is within the specified range. Any significant deviation may indicate a need for maintenance or repair.
- Cleaning Efficiency: Monitor the cleaning efficiency and quality. A decrease in performance may signal the need for maintenance or adjustment.
- Documentation
- Maintenance Log: Maintain a detailed log of all maintenance activities, inspections, and replacements. This helps in tracking the machine’s condition and scheduling preventive maintenance.
What Are The Customization Options Available for Continuous Laser Cleaning Machines?
- Double Woddle Cleaning Mode: This mode allows the laser beam to oscillate in a woddle-like motion, enhancing cleaning efficiency and uniformity. It is particularly useful for cleaning larger surfaces or complex geometries.
- 3-in-1 Functionality: Machines can be customized to perform not only cleaning but also welding and cutting. This multifunctionality makes the machine versatile and useful for various applications within a single unit, reducing the need for multiple pieces of equipment.
- Cleaning Width: The cleaning width can be adjusted to suit different surface areas. Customizing the cleaning width allows for precise control over the area being cleaned, which is beneficial for both small and large-scale cleaning tasks.
Related Resources
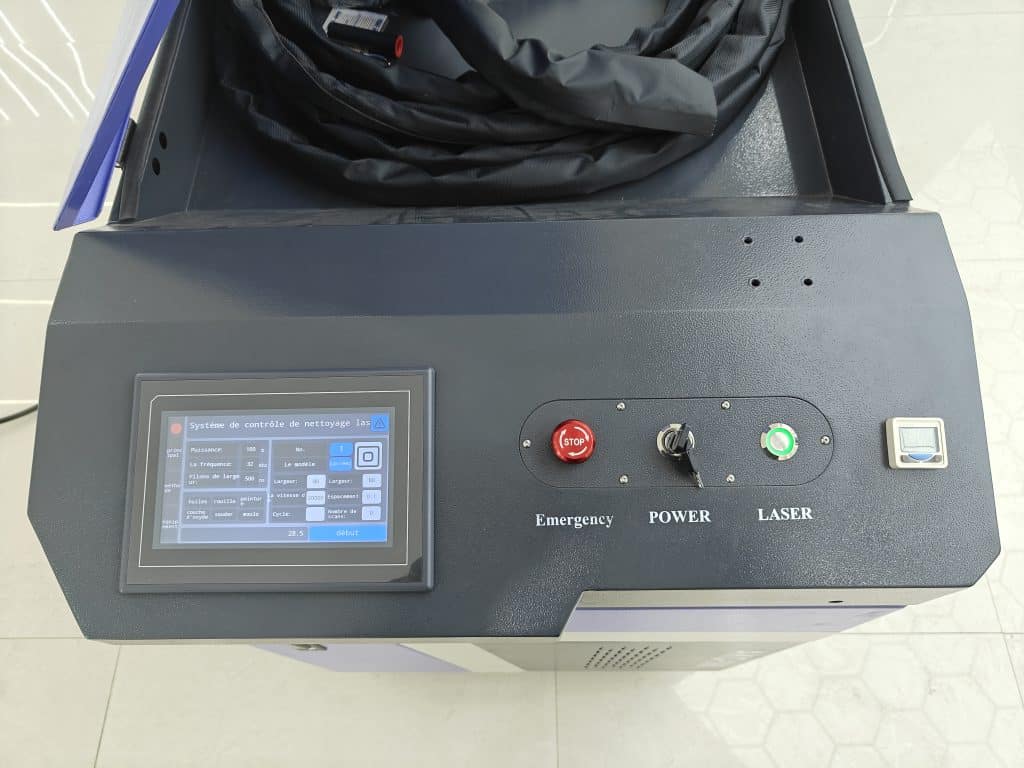
How to Set up a Pulse Laser Cleaning Machine?
This article mainly introduces the key points of the full process setting of the pulse laser cleaning machine from working condition evaluation, equipment selection, parameter setting to safety specifications and
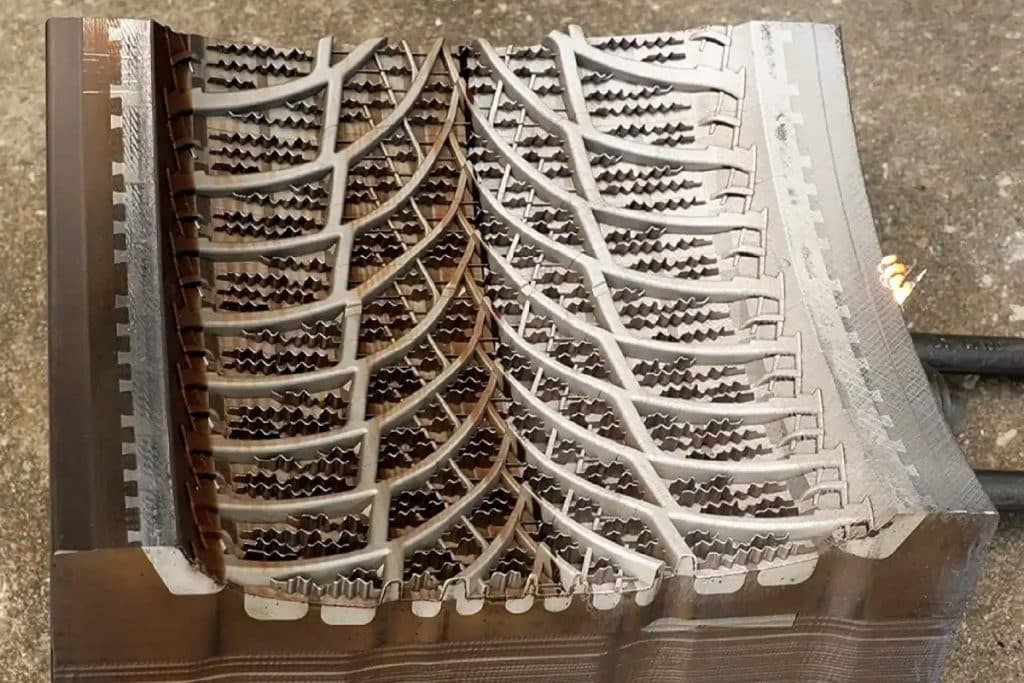
Why Are Pulsed Lasers More Powerful?
This article mainly discusses the scientific principles, advantages, design considerations, application areas, and challenges of pulsed lasers and deeply explores their high peak power and versatility.
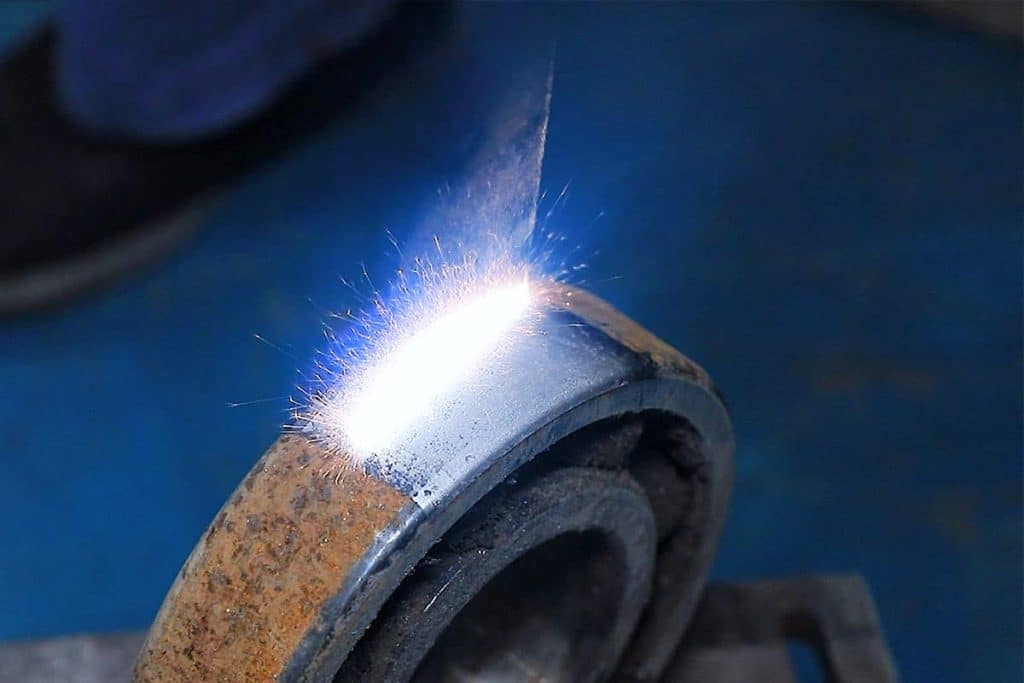
Will Pulsed Laser Cleaning Damage the Substrate?
This article provides a comprehensive overview of how pulsed laser cleaning works, the mechanisms that may cause substrate damage, influencing factors, and effective strategies to ensure safe and efficient cleaning