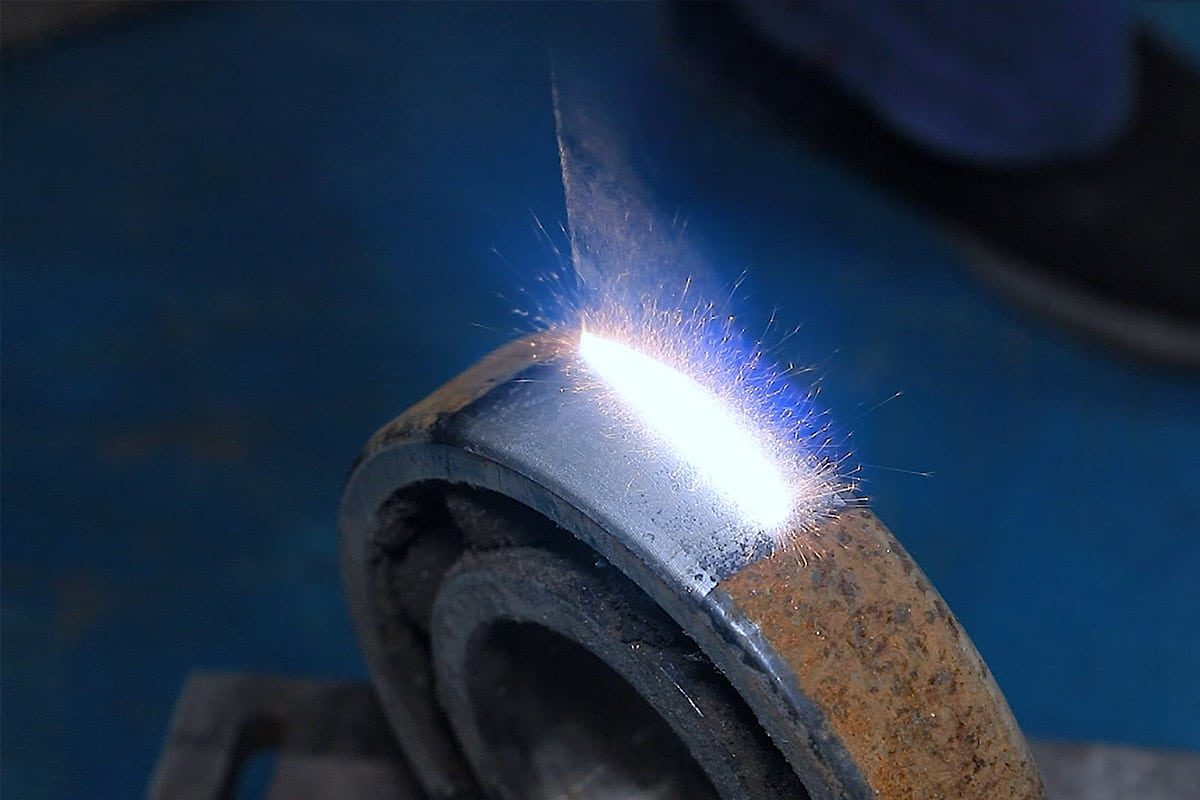
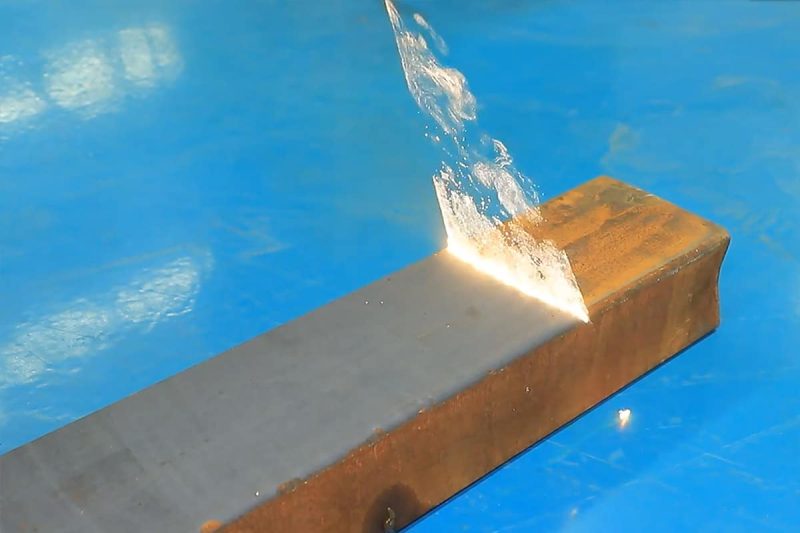
Laser Cleaning
Principles of laser cleaning
Laser cleaning operates based on two fundamental principles, the photothermal effect and the photoablation effect.
- Photothermal Effect: The photothermal effect involves the absorption of laser energy by the material’s surface. When the laser beam strikes the contaminated or coated surface, it generates heat, causing the contaminants or coatings to expand and vaporize. The expansion and vaporization create a pressure difference, which results in the removal of the unwanted material. This effect is highly efficient and can be used for a wide range of materials, including rust, paint, and organic coatings.
- Photoablation Effect: The photoablation effect occurs when a high-intensity laser beam rapidly ionizes and vaporizes the material on the surface, creating a plasma plume. This process is particularly effective for removing thin layers of contaminants or coatings, as it provides a clean and residue-free result. Photoablation is critical for applications that require minimal damage to the substrate, such as in art restoration or delicate electronic component cleaning.
Applications of laser cleaning
Laser cleaning has found diverse applications across various industries, including but not limited to:
- Industrial cleaning: Laser cleaning is used to remove rust, paint, grease, and other contaminants from metal surfaces in industries like automotive, shipbuilding, and aerospace.
- Automotive production: Laser cleaning is used to remove phosphate layers from bevel gears and other parts before welding to ensure less spatter and porosity. In the field of car maintenance, laser cleaning can be used to remove rust and paint on the car surface, thereby restoring the smoothness of the car surface.
- Cultural relics preservation: It is a preferred method for cleaning historical artifacts, sculptures, and delicate art pieces, as it ensures gentle and non-destructive removal of dirt and contaminants.
- Tire mold: Since the contours of the tire mold have diverse geometric shapes and tight textures, the laser can easily focus on the parts that need to be cleaned and effectively remove the dead corners of the tire mold and other parts that are difficult to clean.
- Aerospace and aviation: The aerospace industry relies on laser cleaning for surface preparation and maintenance, as it provides a residue-free and precise cleaning process.
Advantages of laser cleaning
As a new industrial cleaning method, laser cleaning is widely welcomed in the industrial market. Some of its advantages include:
- No damage to the substrate: This non-contact cleaning method does not use any cleaning media, avoiding mechanical wear and chemical corrosion problems in traditional cleaning.
- Clean fast: Powerful laser cleaners deliver short, powerful bursts of power to ensure the most consistent beam path. These characteristics enable the laser beam to quickly and efficiently remove dirt, rust, coatings, and other contaminants on the surface of the material, greatly improving the cleaning efficiency.
- High cleaning quality: Laser cleaning machines can effectively clean sub-micron particles adsorbed on the surface of materials that are difficult to clean with other methods.
- In line with the concept of environmental protection: the laser cleaning process does not use chemicals, so it does not produce pollutants and is more environmentally friendly.
- High safety: Laser cleaning does not produce splashes and does not require contact with corrosive liquids. Workers only need to wear laser-protective glasses.
- Convenient to move: The laser cleaning machine is small and easy to transport and take to other workplaces with cleaning needs.
- Cost-effective: Laser cleaning does not require the use of any media and only consumes a small amount of electricity. Because laser cleaning leaves behind no waste or debris, the cost of waste disposal is avoided.
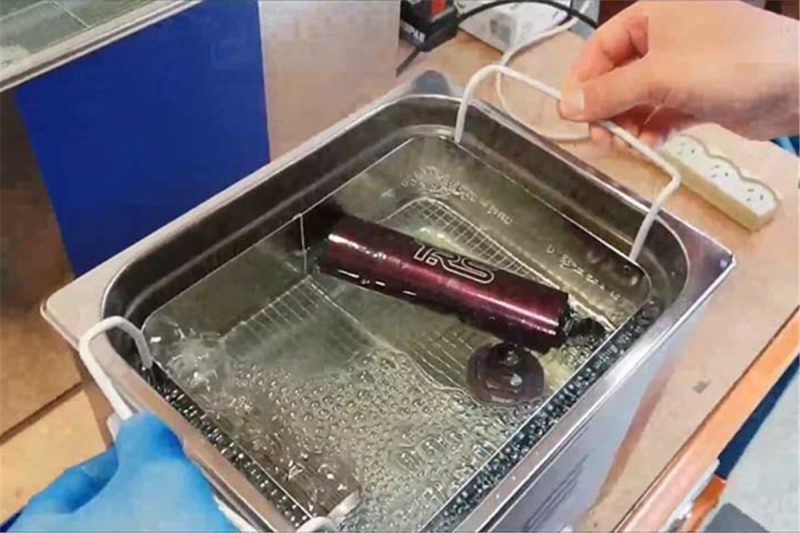
Traditional Non-Contact Cleaning Methods
Ultrasonic Cleaning
Ultrasonic cleaning is a non-contact cleaning method that uses high-frequency sound waves (ultrasound) to create microscopic bubbles in a cleaning solution. These bubbles implode upon contact with the surface, releasing energy that dislodges contaminants. Ultrasonic cleaning is particularly effective for intricate or hard-to-reach areas.
- Principles of ultrasonic cleaning: Ultrasonic cleaning operates based on the principle of cavitation, which is the formation and collapse of microscopic bubbles in a liquid. The collapse of these bubbles generates high-velocity liquid jets and shockwaves, which dislodge contaminants from the surface.
- Applications of ultrasonic cleaning: Ultrasonic cleaning is widely used in applications such as jewelry cleaning, medical instrument sterilization, and precision parts cleaning in industries like electronics and optics.
- Advantages of ultrasonic cleaning: Ultrasonic waves can effectively clean complex geometries, and because there is no abrasive effect, the risk of surface damage to the workpiece is reduced, making it ideal for small and precision parts.
- Limitations of ultrasonic cleaning: Because ultrasonic cleaning requires a liquid medium, the cleaning process is limited. On the other hand, some applications require the use of chemical cleaners to improve cleaning performance, which may lead to environmental contamination or health hazards to operators. Additionally, ultrasonic cleaning is ineffective or minimally effective against thick coatings, thick layers of contamination, or thick rust.
Dry Ice Blasting
Dry ice blasting, also known as CO2 cleaning, is a non-contact cleaning method that utilizes pressurized air to accelerate dry ice pellets (solid CO2) to high velocities. Upon impact with the surface, the dry ice pellets sublime (change from a solid to a gas), creating a micro-explosion that dislodges contaminants.
- Principles of dry ice blasting: Dry ice blasting relies on the kinetic energy of the dry ice pellets and the thermal shock of sublimation. The sudden phase change from solid to gas causes rapid expansion and contraction, leading to the removal of contaminants.
- Applications of dry ice blasting: Dry ice blasting is commonly used in industries like food processing, automotive manufacturing, and electrical equipment cleaning. It is particularly suitable for cleaning electrical components and machinery, as it leaves no residue.
- Advantages of dry ice blasting: The medium used in dry ice blasting is CO2, which leaves no secondary waste or residue and is more environmentally friendly. On the other hand, this cleaning method is non-abrasive and non-conductive, making it ideal for electrical components.
- Limitations of dry ice blasting: Dry ice blasting is expensive to operate because dry ice itself is costly and difficult to transport and store. Dry ice blasting, on the other hand, does not clean heavy rust or thick paint layers well. In addition, the use of dry ice blasting requires a well-ventilated space to avoid large accumulations of CO2 that may be dangerous to operators.
Plasma Cleaning
Plasma cleaning is a non-contact cleaning method that uses low-pressure plasma (ionized gas) to remove contaminants from surfaces. It is particularly effective for cleaning and activating surfaces for subsequent processes like bonding and coating.
- Principles of plasma cleaning: Plasma cleaning operates by creating a low-pressure, reactive gas environment, where gases are ionized into charged particles and radicals. These charged species chemically react with contaminants on the surface, breaking them down and rendering them volatile for removal.
- Applications of plasma cleaning: Plasma cleaning is widely used in semiconductor manufacturing, microelectronics, and biotechnology, where precision cleaning and surface activation are critical for device performance.
- Advantages of plasma cleaning: Plasma cleaning of the surface before bonding or plating will produce higher bonding properties between the coating and the material surface. This technique is suitable for cleaning delicate or temperature-sensitive materials.
- Limitations of plasma cleaning: In some cases, plasma treatment can leave carbonized residue on the surface, and these contaminants can be corrosive, which can cause material degradation or wear over time. Plasma cleaning often requires additional equipment to complete the job, adding additional expense to the process.
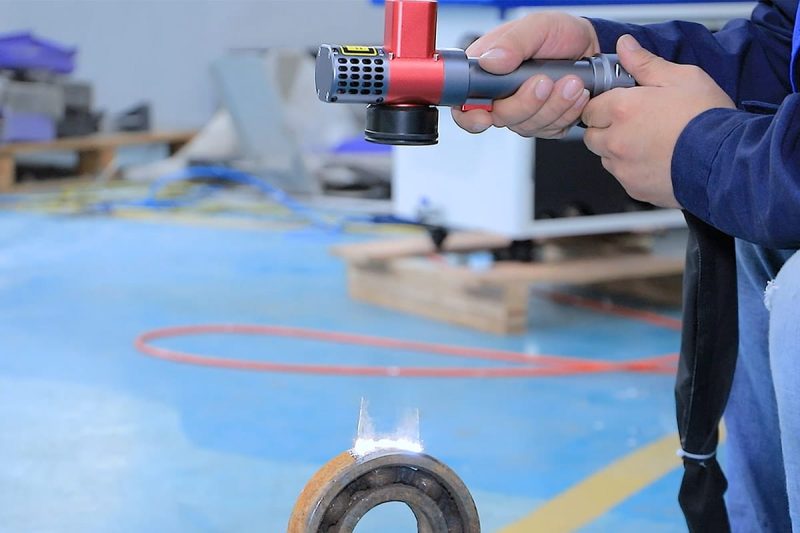
Laser Cleaning VS Other Non-Contact Cleaning Methods
Cleaning Efficiency
- Laser Cleaning: Due to its photothermal and photoablation effects, laser cleaning has high cleaning efficiency. It can effectively remove a wide range of contaminants, including rust, paint, grease, and organic coatings. The ability to customize laser parameters (wavelength, power, and pulse duration) enables cleaning accuracy and speed control, making it suitable for a wide range of applications.
- Ultrasonic Cleaning: Ultrasonic cleaning is highly efficient for removing contaminants in intricate or hard-to-reach areas. However, its effectiveness may be limited when dealing with heavy coatings, thick layers of contaminants, or rust. In addition to cleaning solutions, chemical cleaners are often required to increase cleaning efficiency.
- Dry Ice Blasting: Dry ice blasting is effective for removing a variety of contaminants, especially in applications where residue and secondary waste are concerns. However, its efficacy can be compromised when dealing with heavy rust or thick layers of paint. Additionally, the availability and cost of dry ice pellets may also impact its efficiency.
- Plasma Cleaning: Plasma cleaning excels in removing organic contaminants and activating surfaces. It is a precision cleaning method suited for specific applications in controlled environments. However, it is less effective when it comes to removing heavy coatings, and rust, or in situations where a residue-free surface is essential.
Application Scope
- Laser Cleaning: Laser cleaning is highly versatile and capable of addressing a wide range of applications, from industrial cleaning to cultural relic protection and wood paint removal. It can be tailored to specific cleaning requirements by adjusting laser parameters and beam delivery methods.
- Ultrasonic Cleaning: Ultrasonic cleaning is versatile in its own right, particularly for cleaning intricate or complex geometries. It is commonly used in industries where small and delicate parts require precision cleaning. However, since ultrasonic cleaning needs to be carried out in a liquid medium, it has limitations in cleaning large-volume objects.
- Dry Ice Blasting: Dry ice blasting is versatile for cleaning tasks where the absence of residue is crucial. It is often chosen in industries where sensitive equipment and electrical components need to be cleaned without the risk of damage.
- Plasma Cleaning: Plasma cleaning is highly specialized and typically suited for specific applications in industries like semiconductor manufacturing and biotechnology. Its versatility is somewhat limited compared to laser cleaning.
Cost-Effectiveness
- Laser Cleaning: Purchasing a laser cleaning machine requires a higher initial investment, which may make some users hesitant. However, laser cleaning has high efficiency and good quality, and can be used stably for a long time. Laser cleaning machines have almost no consumables and require no special maintenance because, in the long run, operating costs are much lower than other cleaning methods.
- Ultrasonic Cleaning: Ultrasonic cleaning equipment is generally more affordable than laser cleaning systems. However, consideration should be given to the ongoing costs of consumables associated with cleaning solutions and, in some cases, the expense of needing to dispose of used cleaners.
- Dry Ice Blasting: For cleaning applications that require a residue-free material surface, dry ice blasting is cost-effective and can save labor and time required for secondary cleaning after cleaning. However, the cost of dry ice and its transportation and storage costs are high, which requires ongoing expenses.
- Plasma Cleaning: Plasma cleaning equipment may involve a significant upfront investment, especially for specialized applications. Ongoing costs related to energy consumption and the supply of gases should be taken into account.
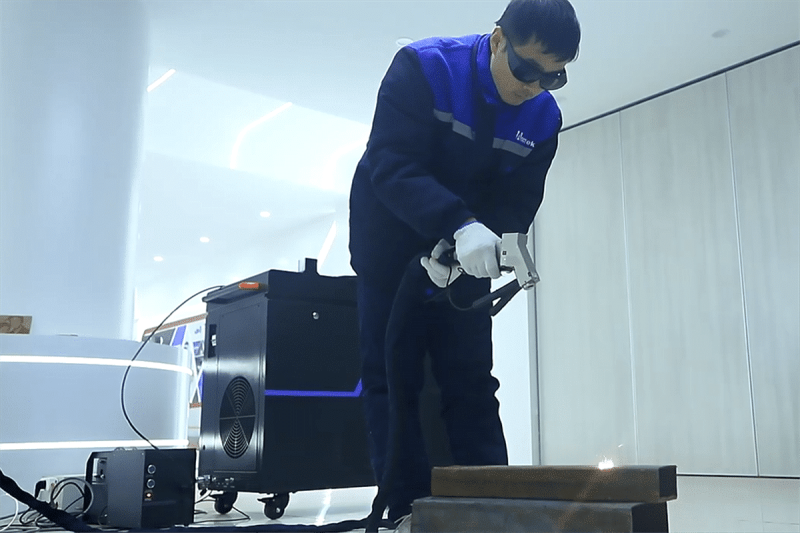
Limitations and Considerations
To make an informed decision on the choice of a non-contact cleaning method, it is essential to consider the limitations and specific requirements of each method.
- Laser Cleaning: Laser cleaning machines have a higher initial investment cost and may not fit all budgets. On the other hand, when incorrect laser parameters are used for surface cleaning, damage to the material surface may occur. In addition, when operating a laser cleaning machine, protective measures need to be taken to avoid harm caused by laser irradiation to the eyes or skin.
- Ultrasonic Cleaning: Ultrasonic cleaning relies on a liquid medium, so the scope of cleaning is limited to small parts. For larger or heavily soiled surfaces, the effectiveness of ultrasonic cleaning is reduced. In addition, to improve the cleaning effect, in some cases, it may be necessary to use chemical cleaners, which may be harmful to the health of operators and the environment.
- Dry Ice Blasting: Dry ice blasting may not be ideal for all contaminants and may not be effective on thicker layers of rust or paint. On the other hand, the cost of dry ice itself and its storage is high, and long-term use of enterprises will result in greater expenditures. In addition, since the temperature of dry ice is extremely low (the temperature of solid dry ice is -78.5°C) when cleaning dry ice, operators should wear multiple layers of protection such as gloves, cotton clothes, and earmuffs to ensure warmth and safety.
- Plasma Cleaning: Plasma cleaning equipment can be expensive, and the gas requirements increase operating costs. Plasma cleaning is typically performed in a controlled environment and is a cleaning method suited to specific industries and applications.
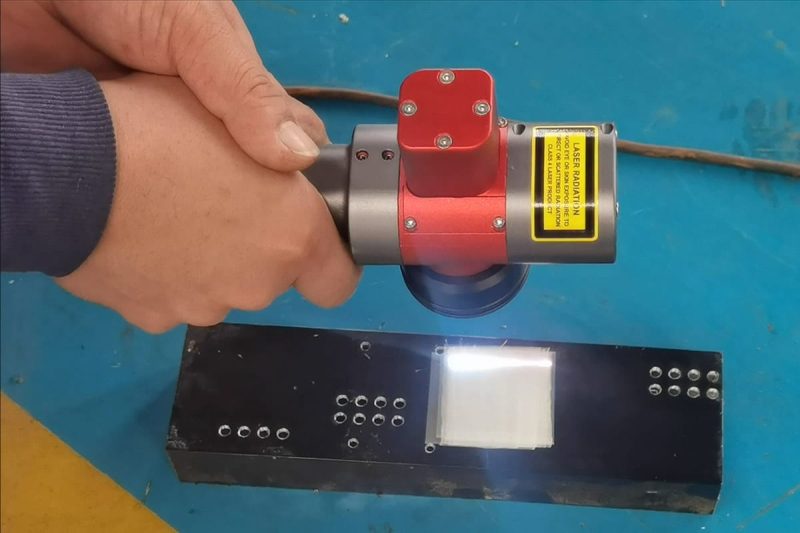
Choose the appropriate environmentally friendly cleaning method based on your needs
In the ever-evolving landscape of cleaning technologies, non-contact cleaning methods have gained prominence for their ability to efficiently and precisely remove contaminants while reducing environmental impact. Laser cleaning, ultrasonic cleaning, dry ice blasting, and plasma cleaning are all valuable options, each with its unique strengths and limitations.
- Laser cleaning, with its high cleaning efficiency and versatility, stands out as a powerful solution for various applications. It excels in removing a wide range of contaminants, including rust, paint, and organic coatings, while leaving minimal environmental footprint. However, its cost-effectiveness and safety considerations should be carefully evaluated for specific use cases.
- Ultrasonic cleaning offers efficiency in intricate or hard-to-reach areas and is generally considered environmentally friendly. It is cost-effective and suitable for small and delicate parts but may require the use of chemical detergents in some situations. In addition, ultrasonic cleaning is not suitable for cleaning large volumes of materials.
- Dry ice blasting, with its residue-free cleaning and eco-friendly approach, is a valuable method for applications where minimal environmental impact is essential. However dry ice is expensive and difficult to transport and store, so its availability and cost will affect the feasibility of cleaning.
- Plasma cleaning is a specialized method tailored for industries where precision cleaning and surface activation are critical. While its environmental impact is relatively low, the equipment and gas costs may be limiting factors.
Summarize
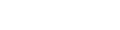
- [email protected]
- [email protected]
- +86-19963414011
- No. 3 Zone A, Lunzhen Industrial Zone,Yucheng City , Shandong Province.