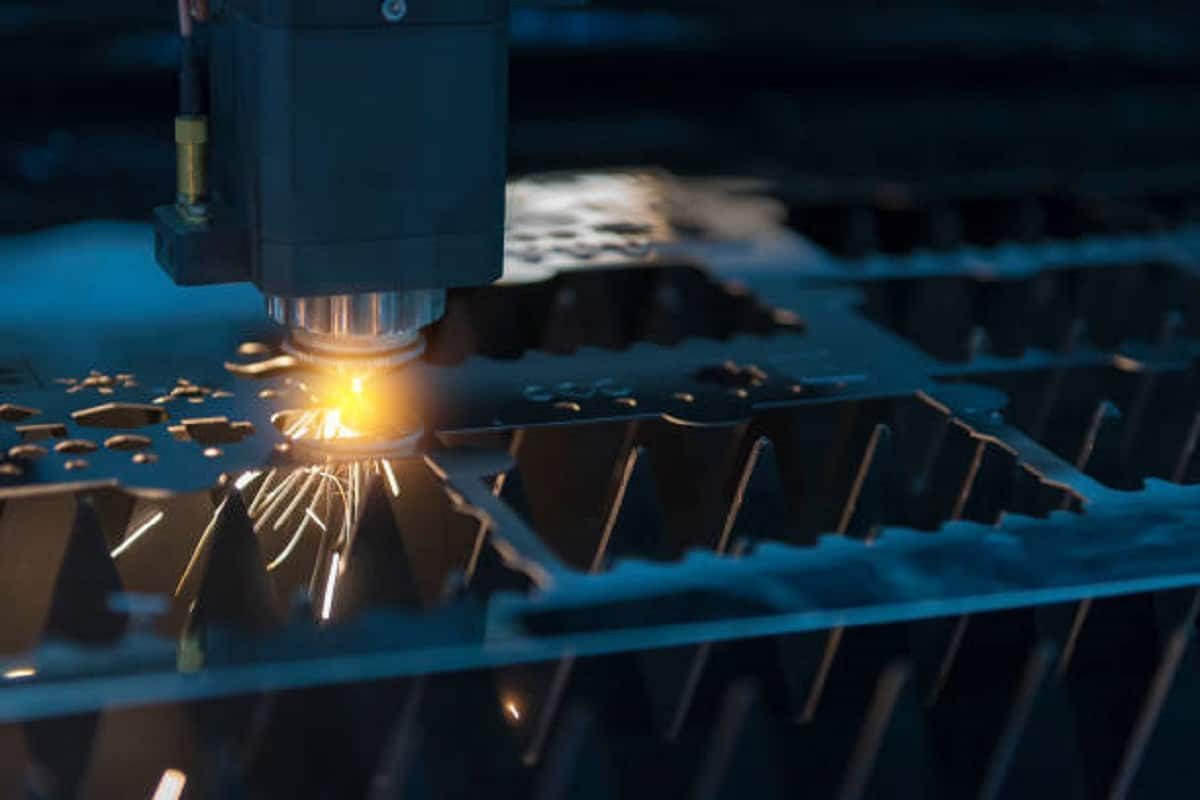
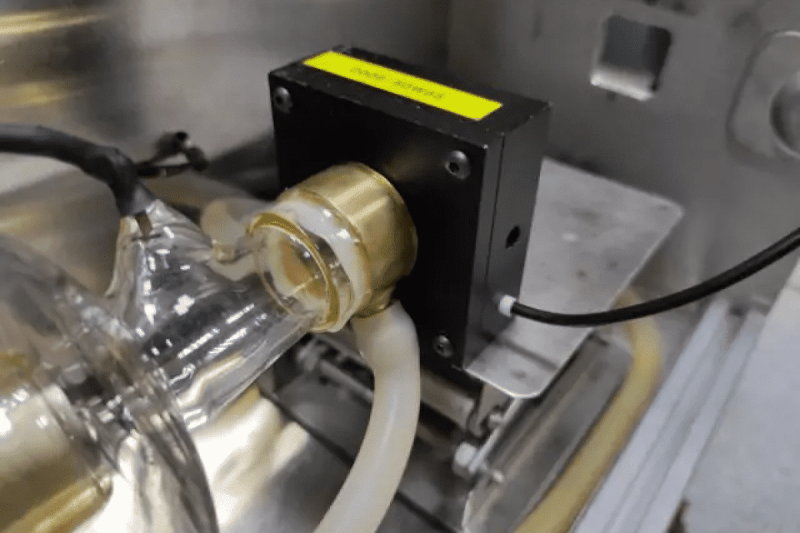
Fiber Laser and CO2 Laser
What is fiber laser?
The working principle of the fiber laser generator is based on the concept of fiber amplification, which excites the laser medium of the fiber through a laser diode. This excitation causes the atoms in the laser medium to emit spontaneous radiation, producing photons. After reflection by the optical element, the photon propagates multiple times and becomes a laser, which escapes through one of the ports to form an output laser beam. The following are some features of fiber lasers:
- Wavelength selectivity: The wavelength of a fiber laser generator is usually determined by the excitation source and doping material, so the selection of a specific wavelength can be achieved and suitable for various applications.
- High beam quality: The laser output by fiber laser generators usually has high beam quality, which makes it suitable for applications that require fine processing, such as laser cutting and laser marking.
- Compactness and portability: Due to the flexibility and lightness of fiber optics, fiber laser generators are relatively small and easy to install, making them suitable for use in environments with space constraints.
- Low maintenance costs: Fiber laser generators generally have lower maintenance costs than CO2 laser generators. The stability and durability of the fiber itself help reduce maintenance frequency.
- Wide adaptability: Fiber laser generators are suitable for a variety of application fields, including material processing, medical treatment, communications, etc., and have high flexibility and adaptability.
What is a CO2 laser?
The working principle of a CO2 laser generator involves exciting CO2 gas molecules, causing them to emit laser radiation. CO2 laser cutting uses CO2 gas as the gain medium in the laser system. A resonator purged with CO2 gas at high speed (turbine or blower) will use a variety of methods to split the ions of light particles, causing the light particles to collide with each other and form larger intervals that are split, thus completing the cut. The following are the main features of the CO2 laser:
- Wavelength: The main wavelength of CO2 laser is 10.6 microns, which belongs to the far-infrared spectrum range. Lasers of this wavelength have good penetration into many materials, making them excellent in applications such as cutting and welding.
- High power: CO2 laser generators generally provide relatively high power output and are suitable for many industrial applications that require high energy density, such as metal cutting and welding.
- Deep Penetration: Due to its wavelength and energy characteristics, the CO2 laser is capable of deep penetration in certain materials, making it very effective in some cutting and engraving tasks.
- Industrial applications: CO2 laser generators are widely used in industrial fields, including cutting, welding, engraving, marking, etc. It performs particularly well in applications that require high cutting quality and high power requirements.
- Complexity: The equipment of a CO2 laser generator is relatively complex, including a gas circulation system, optical components, and a high-voltage power supply. This makes its equipment maintenance relatively cumbersome, but it is still one of the first choices for many industrial applications.
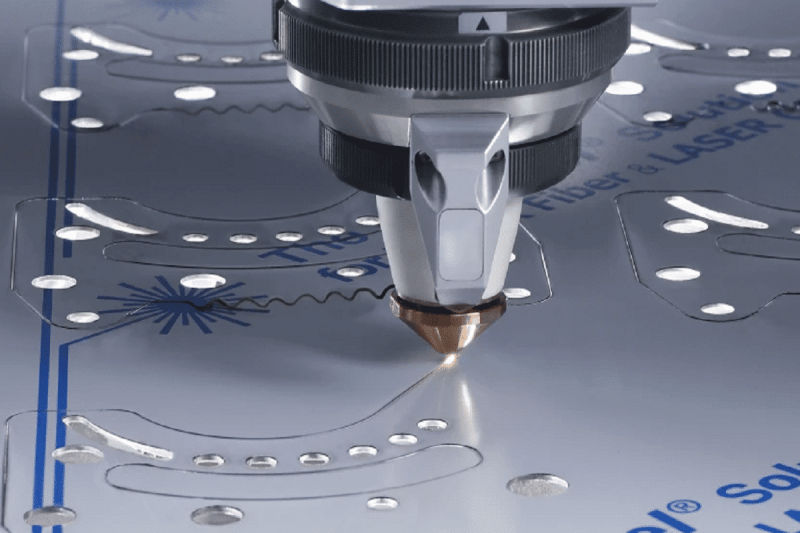
Factors to consider when choosing a laser generator
Application requirements
wavelength
power level
Beam quality
Stability and reliability
Maintenance cost
Adaptability and flexibility
space and dimensions
cost
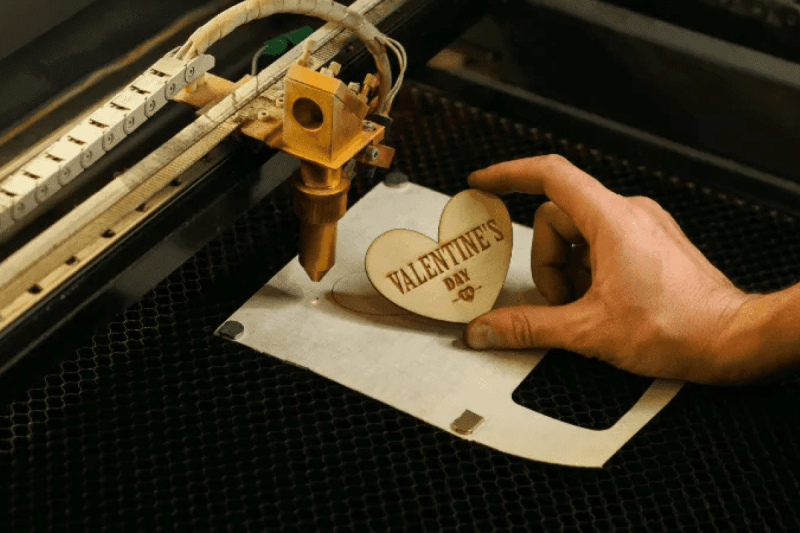
How to choose between CO2 laser and fiber laser for laser cutting
Material type and thickness
- CO2 Laser: suitable for a variety of materials, including metals, non-metals, and organic materials. Excellent at cutting thicker metals.
- Fiber Laser: Mainly used for metal cutting, and has a better effect on high-speed cutting of thin metal.
Cutting speed and efficiency
- CO2 Laser: It can achieve high cutting speed on thinner non-metallic materials, suitable for occasions that require high production efficiency.
- Fiber Laser: Fiber laser provides high laser energy, which can cut metal materials at a very fast speed. Even thicker metal materials, optical fiber laser can complete effective cutting.
Cutting quality and accuracy
- CO2 Laser: Provides high cutting quality, and can have better cutting performance even on thicker non-metallic materials, and the cutting surface can be smooth.
- Fiber Laser: It can achieve high cutting accuracy on thin materials and is suitable for applications that require high cutting quality.
Initial investment
- CO2 Laser: The initial investment in a CO2 laser cutting system is relatively low and may be suitable for businesses with a limited budget.
- Fiber Laser: The initial investment in a fiber laser cutting system may be higher, but its performance and efficiency may result in a better return on investment in the long term.
Maintenance and operating costs
- CO2 Laser: CO2 laser cutting systems typically require more frequent maintenance, such as gas changes and optics cleaning, which can result in higher operating costs.
- Fiber Laser: Fiber laser cutting systems typically have lower operating and maintenance costs, making them more attractive, especially over the long term.
applicability
- CO2 Laser: Suitable for tasks that require deep penetration and high power, such as thicker metal cutting.
- Fiber Laser: suitable for applications that require high cutting speed and precision, especially high-speed cutting on thin materials.
Special requirements for materials
- CO2 Laser: On some materials that are sensitive to the impact of cutting heat, a CO2 laser may not be as advantageous as a fiber laser.
- Fiber Laser: Fiber laser may be more suitable for some materials that are sensitive to the impact of cutting heat.
Summarize
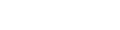
- [email protected]
- [email protected]
- +86-19963414011
- No. 3 Zone A, Lunzhen Industrial Zone,Yucheng City , Shandong Province.