Mixed Laser Cutting Machine
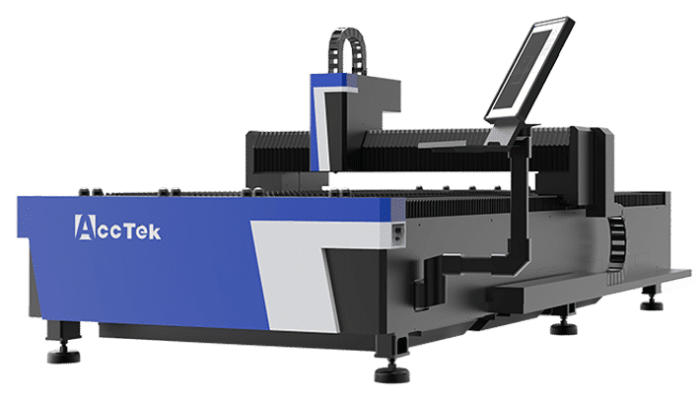
Product Range
-
Single Beam CO2 And Fiber Laser Cutting Machine
Rated 4.75 out of 5$16,300.00 – $36,000.00 Select options This product has multiple variants. The options may be chosen on the product page -
Double Beam CO2 And Fiber Laser Cutting Machine
Rated 4.75 out of 5$16,800.00 – $36,500.00 Select options This product has multiple variants. The options may be chosen on the product page
Laser Cutting VS. Other Methods
Laser Cutting vs. Mechanical Cutting
Laser cutting offers unparalleled precision and smooth edges, making it ideal for intricate designs. Unlike mechanical cutting, which can cause tool wear and may produce rougher finishes, laser cutting provides consistent results without physical contact, reducing the risk of material deformation and extending tool life.
Laser Cutting vs. Waterjet Cutting
Waterjet cutting is effective for various materials, but it can be slower and often requires additional post-processing to achieve smooth edges. Laser cutting, on the other hand, delivers faster results with finer detail and higher cutting speeds, making it more efficient for high-volume production, particularly with metals and plastics.
Laser Cutting vs. Plasma Cutting
Plasma cutting is suitable for thicker metals but can leave a rougher edge and require additional cleanup. Laser cutting excels in precision and finer cuts, especially for thinner materials, providing smoother edges with minimal heat distortion. It is also more energy-efficient and versatile across different material types.
Why Choose AccTek Laser
Cutting-Edge Technology
AccTek Laser machines utilize the latest laser technology, ensuring high precision and fast cutting speeds. Our systems provide unmatched accuracy and efficiency, ensuring the best quality cuts across various materials with minimal distortion.
Custom Solutions
We understand that every business has unique requirements. That's why we offer customizable options, including power ranges, work area sizes, and cutting speeds, allowing you to tailor our machines to fit your specific production needs and material types.
Exceptional Energy Efficiency
Our laser cutting machines are designed for maximum energy efficiency. With lower power consumption and optimized performance, AccTek Laser machines help reduce operational costs, making them a cost-effective solution for both small and large-scale manufacturing.
Durability and Reliability
AccTek Laser cutting machines are engineered for long-term durability, with high-quality components and precision manufacturing. Our machines are designed to provide consistent, reliable performance, reducing maintenance needs and extending the lifespan of your equipment.
After-Sales Support
We believe in building long-term relationships with our customers. AccTek Laser provides exceptional after-sales support, including installation, training, and ongoing technical assistance. Our team is always ready to help you optimize machine performance and resolve any issues quickly.
Competitive Pricing and Value
At AccTek Laser, we offer high-performance laser-cutting machines at competitive prices, ensuring that you get the best value for your investment. Our machines deliver outstanding quality at an affordable cost, making us a trusted partner for your manufacturing needs.
Frequently Asked Questions
What Are Mixed Laser Cutting Machines?
How Much Are Mixed Laser Cutting Machines?
How Long Is The Service Life of Mixed Laser Cutting Machines?
How Much Do Mixed Laser Cutting Machines Cost To Operate?
- Energy Consumption: Laser-cutting machines consume electricity to power the laser source, the machine itself, and any associated cooling systems. The energy consumption depends on the power of the laser and the duration of operation.
- Maintenance: Regular maintenance is necessary to keep the machine running smoothly and efficiently. This includes cleaning optics, replacing consumable parts like nozzles and lenses, and servicing mechanical components. Maintenance costs can vary based on the machine’s design and usage.
- Material Costs: The cost of materials being cut is a significant factor. Different materials have different cutting characteristics and may require adjustments to the laser settings or additional processing steps, affecting operating costs.
- Labor Costs: Labor costs include operator wages and any additional personnel required for setup, programming, and maintenance of the machine.
- Downtime Costs: Downtime due to machine breakdowns or maintenance can impact productivity and increase costs. Downtime can be minimized through preventive maintenance and timely repairs.
- Ventilation and Safety: Laser-cutting machines require proper ventilation and safety measures to protect operators and comply with regulations. Costs associated with ventilation systems, protective gear, and safety training should be considered.
- Depreciation and Financing: If the machine is purchased outright or financed, depreciation and financing costs should be factored into the overall operating expenses.
What Can Mixed Laser Cutting Machines Cut?
- Metal: It can cut various metals, including steel, aluminum, copper, brass, and titanium. It produces a high-powered laser beam that easily melts and vaporizes metal for clean, precise cuts.
- Plastic: It can cut various types of plastics, including acrylic, polycarbonate, PVC, ABS, and PET.
- Wood: It can cut wood and wood-based materials such as MDF, plywood, and solid wood.
- Leather: It can cut different types of leather and other similar materials, including genuine leather and artificial leather.
- Fabric: It can cut various types of fabrics, including cotton, silk, polyester, and nylon.
- Glass: It can cut glass, including tempered glass and borosilicate glass.
- Foam: It can cut various types of foam, including polyurethane foam, expanded polystyrene (EPS) foam, and extruded polystyrene (XPS) foam.
- Rubber: It can cut various types of rubber, including neoprene, silicone, and natural rubber.
What Are The Disadvantages of Mixed Laser Cutting Machines?
- Complexity: Mixed laser cutting machines are more complex than single-purpose machines. They typically require additional setup time, calibration, and programming due to the integration of multiple laser types or cutting processes. This complexity can lead to higher initial investment costs and may require more extensive operator training.
- Maintenance: Maintaining mixed laser cutting machines can be more challenging due to the presence of multiple laser sources and cutting technologies. Each component may have unique maintenance requirements, leading to increased downtime and maintenance costs compared to single-purpose machines.
- Limited Compatibility: Mixed laser cutting machines may not be compatible with all materials and thicknesses. Certain materials or combinations of materials may require specific laser wavelengths or cutting methods that the machine cannot accommodate. This limitation can restrict the range of applications and materials that can be processed.
- Cost: Mixed laser cutting machines tend to have higher upfront costs compared to single-purpose machines due to their advanced capabilities and integrated technologies. Additionally, operating costs, including energy consumption, maintenance, and consumables, may be higher due to the complexity of the equipment.
- Performance Trade-offs: While mixed laser cutting machines offer versatility, they may not excel in every cutting application compared to dedicated laser cutting systems. For example, mixed laser cutting machines that combine CO2 and fiber lasers may not achieve the same cutting quality or speed as a dedicated CO2 or fiber laser cutter for certain materials or thicknesses.
- Space Requirements: Mixed laser cutting machines often require more space than single-purpose machines due to the integration of multiple laser sources and additional equipment, such as chiller units and exhaust systems. This can be a consideration for facilities with limited space or layout constraints.
- Complexity in Programming: Programming mixed laser cutting machines to perform various cutting tasks with different laser sources and parameters can be more complex than programming a single-purpose machine. Operators may need advanced programming skills and specialized software to optimize cutting processes and achieve desired results.
In Which Industries Are Mixed Laser Cutting Machines Most Commonly Used?
- Automotive: Mixed laser cutting machines are employed in the automotive industry for cutting a wide range of materials used in vehicle manufacturing, such as steel, aluminum, and composites. They are used for cutting components like body panels, chassis parts, exhaust systems, and interior trim with high precision and efficiency.
- Aerospace: In the aerospace industry, mixed laser cutting machines are utilized for cutting lightweight materials like aluminum, titanium, and composites to fabricate aircraft components such as fuselage panels, wing sections, and engine parts. The ability to switch between different laser types enables manufacturers to handle a variety of materials and thicknesses.
- Metal Fabrication: Mixed laser cutting machines are widely used in metal fabrication shops for cutting metal sheets, tubes, and profiles for various applications. They offer the flexibility to cut different metals like steel, stainless steel, and aluminum, as well as non-metal materials like plastics and ceramics, catering to diverse customer requirements.
- Electronics: Mixed laser cutting machines are employed in the electronics industry for the precision cutting of circuit boards, semiconductor materials, and electronic components. They enable manufacturers to achieve intricate designs and precise dimensions critical for electronic devices and microelectronics production.
- Medical Devices: In the medical device manufacturing sector, mixed laser cutting machines are utilized for cutting medical-grade metals, polymers, and biocompatible materials to fabricate components for surgical instruments, implants, prosthetics, and medical devices. The ability to switch between laser types allows for processing a wide range of materials used in medical applications.
- Architectural and Interior Design: Mixed laser cutting machines are used in architectural and interior design industries for cutting decorative panels, signage, and intricate patterns in materials like wood, acrylic, glass, and metal. They enable designers to create custom designs with precision and detail, enhancing the aesthetic appeal of architectural spaces and interior environments.
- Packaging and Labeling: Mixed laser cutting machines find applications in the packaging and labeling industry for cutting flexible and rigid packaging materials, such as paperboard, cardboard, plastics, and foils. They are used for producing packaging prototypes, custom packaging designs, and intricate labels with high accuracy and speed.
How To Maintain Mixed Laser Cutting Machines?
- Regular Cleaning: Keep the machine clean by regularly removing dust, debris, and residues from the cutting area, optics, and surrounding components. Use appropriate cleaning materials and methods recommended by the manufacturer to avoid damaging sensitive parts.
- Optics Inspection and Cleaning: Periodically inspect the optics, including lenses, mirrors, and windows, for signs of contamination, scratches, or damage. Clean the optics using a lint-free cloth and a gentle cleaning solution to remove dirt, oils, and residues that can affect laser beam quality and cutting accuracy.
- Check Gas Supply: Ensure a consistent and sufficient supply of assist gases, such as oxygen, nitrogen, or air, depending on the cutting requirements and materials being processed. Monitor gas pressure and purity levels to maintain optimal cutting performance and quality.
- Monitor Cooling Systems: Regularly inspect and maintain the cooling systems, including chiller units and water circulation systems, to prevent overheating and ensure proper temperature control of laser components. Clean filters, check coolant levels, and perform routine maintenance according to the manufacturer’s guidelines.
- Calibration and Alignment: Periodically calibrate and align the laser beam delivery system, including mirrors, lenses, and beam delivery optics, to ensure accurate beam positioning and focus. Misalignment or degradation of optical components can affect cutting quality and consistency.
- Software Updates and Calibration: Keep the machine’s control software up to date with the latest updates and patches provided by the manufacturer. Perform regular software calibration and parameter adjustments to optimize cutting parameters and maintain consistent cutting results.
- Inspect and Replace Consumables: Regularly inspect and replace consumable parts such as nozzles, lenses, and cutting tips as needed. Worn or damaged consumables can affect cutting quality, efficiency, and safety. Follow the manufacturer’s recommendations for replacement intervals and compatible parts.
- Lubrication and Maintenance of Mechanical Components: Lubricate and maintain mechanical components, such as guide rails, bearings, and drive systems, to ensure smooth and precise motion of the cutting head and other moving parts. Clean and grease components according to the manufacturer’s guidelines to prevent wear and prolong component life.
- Safety Checks and Training: Conduct regular safety checks of the machine and its surroundings to identify potential hazards and ensure compliance with safety regulations. Provide comprehensive training for operators on safe machine operation, maintenance procedures, and emergency protocols.
Related Resources
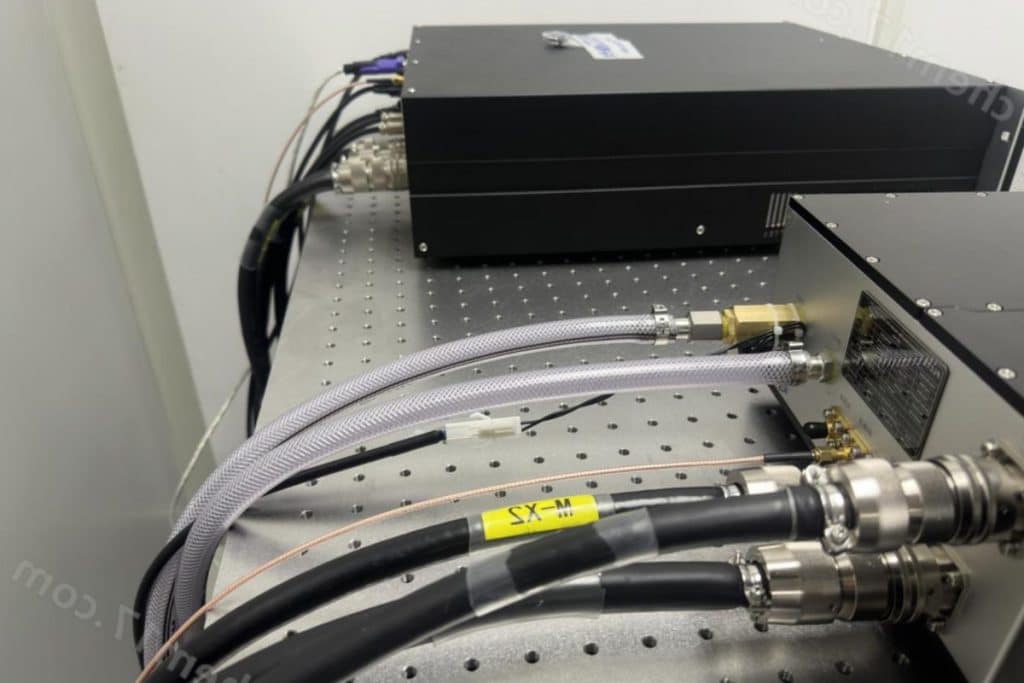
Do Fiber Laser Generators Lose Power over Time?
This article focuses on the reasons why fiber laser generator power decreases over time and proposes effective strategies to mitigate power loss through high-quality equipment, regular maintenance, and an optimized
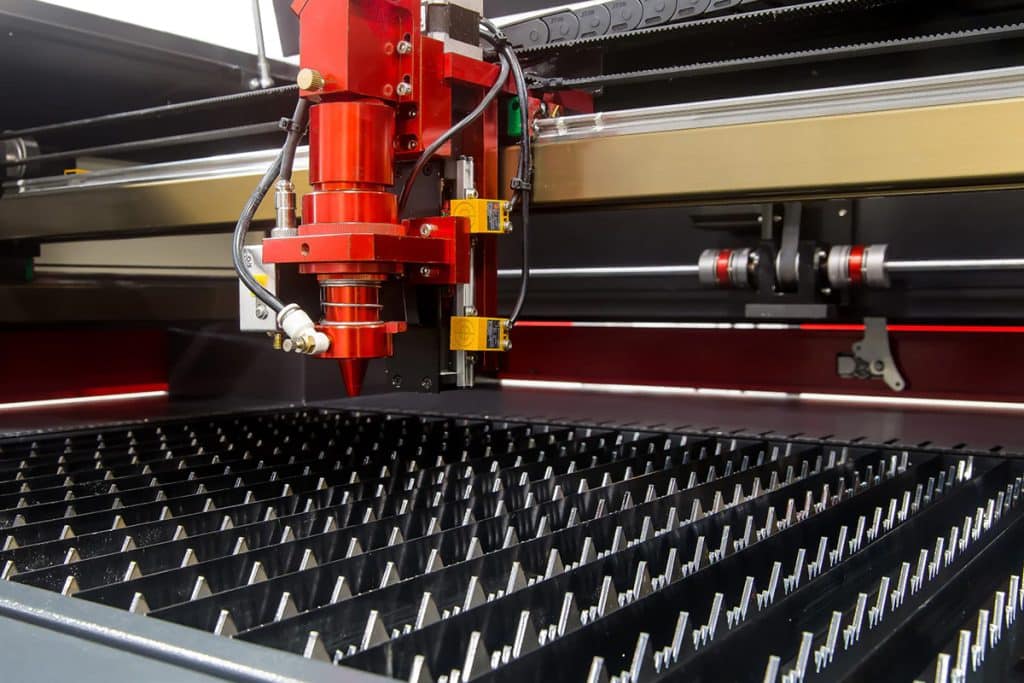
How Does a CO2 Laser Cutting Machine Achieve High-Precision Cutting?
This article mainly introduces the principles and key technologies behind the high-precision cutting capabilities of CO2 laser cutting machines, and analyzes their core structural components and advantages.
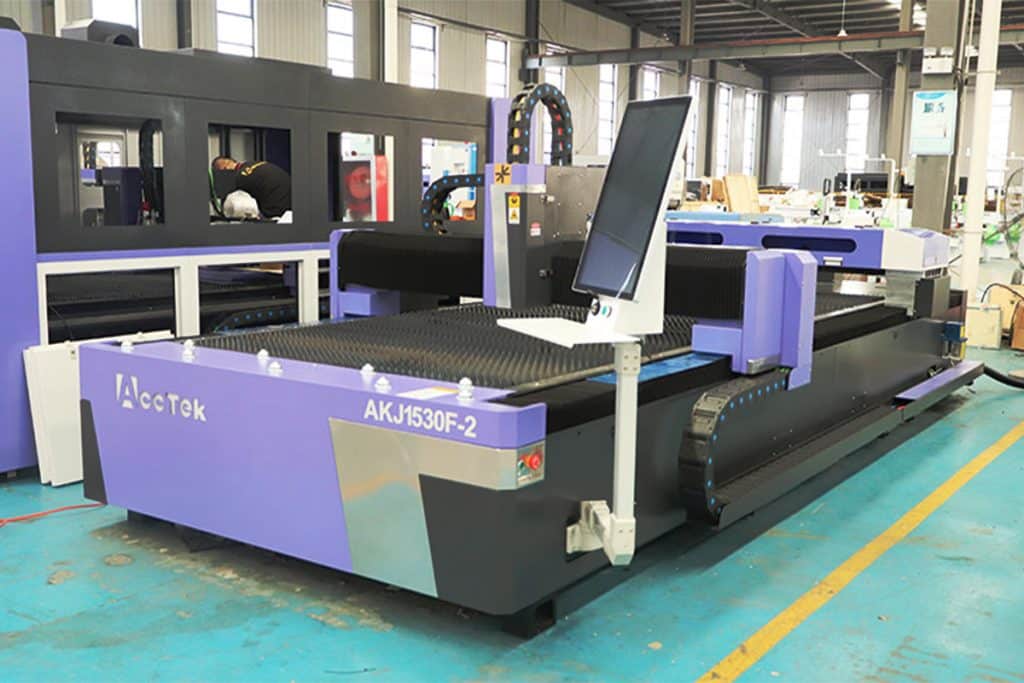
Gantry Fiber Laser Cutting Machine Vs Desktop Fiber Laser Cutting Machine: Comparative Analysis
This article compares and analyzes the structure, performance, and application scenarios of gantry and desktop fiber laser cutting machines to help companies choose the most suitable equipment.