Plastic Laser Cutting Machine
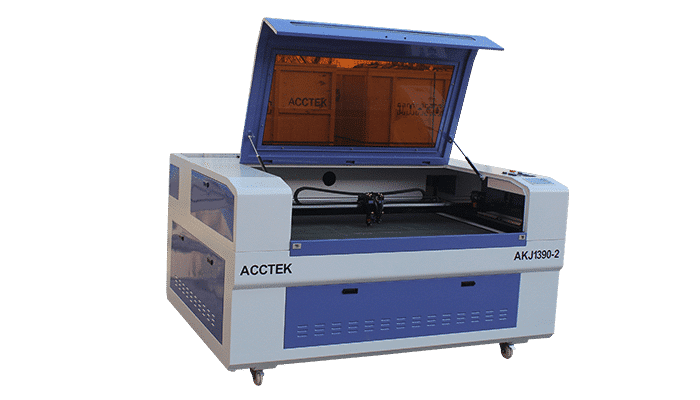
Product Range
-
Acrylic Laser Cutting Machine
Rated 4.75 out of 5$2,700.00 – $8,000.00Price range: $2,700.00 through $8,000.00 Select options This product has multiple variants. The options may be chosen on the product page -
PVC Laser Cutting Machine
Rated 4.75 out of 5$2,700.00 – $8,000.00Price range: $2,700.00 through $8,000.00 Select options This product has multiple variants. The options may be chosen on the product page -
ABS Laser Cutting Machine
Rated 4.75 out of 5$2,700.00 – $8,000.00Price range: $2,700.00 through $8,000.00 Select options This product has multiple variants. The options may be chosen on the product page -
Polycarbonate Laser Cutting Machine
Rated 4.75 out of 5$2,700.00 – $8,000.00Price range: $2,700.00 through $8,000.00 Select options This product has multiple variants. The options may be chosen on the product page -
Polypropylene Laser Cutting Machine
Rated 4.75 out of 5$2,700.00 – $8,000.00Price range: $2,700.00 through $8,000.00 Select options This product has multiple variants. The options may be chosen on the product page -
Delrin Laser Cutting Machine
Rated 4.75 out of 5$2,950.00 – $8,000.00Price range: $2,950.00 through $8,000.00 Select options This product has multiple variants. The options may be chosen on the product page -
PET Laser Cutting Machine
Rated 4.75 out of 5$2,700.00 – $8,000.00Price range: $2,700.00 through $8,000.00 Select options This product has multiple variants. The options may be chosen on the product page -
Polystyrene Laser Cutting Machine
Rated 4.75 out of 5$2,700.00 – $8,000.00Price range: $2,700.00 through $8,000.00 Select options This product has multiple variants. The options may be chosen on the product page -
Mylar Laser Cutting Machine
Rated 4.75 out of 5$2,700.00 – $8,000.00Price range: $2,700.00 through $8,000.00 Select options This product has multiple variants. The options may be chosen on the product page
Laser Cutting VS. Other Methods
Laser Cutting vs. Mechanical Cutting
Laser cutting uses focused light to achieve precise, smooth cuts with minimal heat distortion. In contrast, mechanical cutting involves physical tools like saws or blades, which can cause rough edges and tool wear. Laser cutting offers faster, more accurate results, especially for intricate shapes and detailed designs, with less maintenance required.
Laser Cutting vs. Waterjet Cutting
Waterjet cutting uses high-pressure water to slice through materials, making it effective for thicker plastics. However, laser cutting is faster and provides better precision for thinner plastics, leaving smoother edges. Waterjet cutting may require additional finishing processes, whereas laser cutting often produces cleaner cuts without the need for post-processing.
Laser Cutting vs. CNC Routing
CNC routing uses rotating bits to cut plastic, making it suitable for thicker materials and larger designs. However, laser cutting delivers higher precision for fine details and complex patterns. CNC routing can leave rougher edges and requires more frequent tool changes, whereas laser cutting offers cleaner, more consistent results with less material waste.
Why Choose AccTek Laser
Cutting-Edge Technology
AccTek Laser machines utilize the latest laser technology, ensuring high precision and fast cutting speeds. Our systems provide unmatched accuracy and efficiency, ensuring the best quality cuts across various materials with minimal distortion.
Custom Solutions
We understand that every business has unique requirements. That's why we offer customizable options, including power ranges, work area sizes, and cutting speeds, allowing you to tailor our machines to fit your specific production needs and material types.
Exceptional Energy Efficiency
Our laser cutting machines are designed for maximum energy efficiency. With lower power consumption and optimized performance, AccTek Laser machines help reduce operational costs, making them a cost-effective solution for both small and large-scale manufacturing.
Durability and Reliability
AccTek Laser cutting machines are engineered for long-term durability, with high-quality components and precision manufacturing. Our machines are designed to provide consistent, reliable performance, reducing maintenance needs and extending the lifespan of your equipment.
After-Sales Support
We believe in building long-term relationships with our customers. AccTek Laser provides exceptional after-sales support, including installation, training, and ongoing technical assistance. Our team is always ready to help you optimize machine performance and resolve any issues quickly.
Competitive Pricing and Value
At AccTek Laser, we offer high-performance laser-cutting machines at competitive prices, ensuring that you get the best value for your investment. Our machines deliver outstanding quality at an affordable cost, making us a trusted partner for your manufacturing needs.
Frequently Asked Questions
Can Lasers Cut Plastic?
How Accurate Are Plastic Laser-Cutting Machines?
How Much Do Plastic Laser-Cutting Machines Cost?
- Entry-Level or Small Machine: Entry-level or small plastic laser cutters typically cost between $1,500 and $5,000. These machines are suitable for hobbyists, small businesses, or educational purposes, but generally have lower power and cutting area.
- Mid-Range Machine: Mid-range plastic laser cutting machines typically range in price from $2,700 to $10,000. These machines offer more power, a larger cutting area, and enhanced functionality, making them suitable for small to medium-sized businesses.
- High-End Industrial Machine: Industrial-grade CO2 laser cutters with advanced features and higher power ratings range in price from $8,000 to $25,000 or more. These machines offer increased power, precision, automation, and customization options.
How Thick of Plastic Can Lasers Cut?
- Acrylic: Laser cutting machines can typically cut acrylic sheets with thicknesses ranging from 0.1 mm (0.004 inches) to over 25 mm (1 inch). Cutting capabilities depend on the power and quality of the laser generator.
- Polycarbonate (PC): Lasers can cut polycarbonate sheets ranging in thickness from as thin as 0.1 mm (0.004 in) to about 10 mm (0.39 in) or thicker.
- Polyethylene Terephthalate (PET): PET plastic sheet is commonly used in packaging and sheet applications and can be laser cut in thicknesses from less than 0.1 mm (0.004 inches) to about 10 mm (0.39 inches) or more.
- Polyvinyl Chloride (PVC): The laser can cut PVC sheet thicknesses ranging from 0.1 mm (0.004 in) to 15 mm (0.59 in) or thicker.
- Polypropylene (PP): PP plastic sheets can generally be laser cut in thicknesses ranging from about 0.1 mm (0.004 in) to 15 mm (0.59 in) or more.
- High-Density Polyethylene (HDPE): Laser cutting can handle thicknesses ranging from approximately 0.1 mm (0.004 in.) film to 20 mm (0.78 in.) or thicker HDPE sheets.
- Acrylonitrile Butadiene Styrene(ABS): Lasers can cut ABS plastic in thicknesses ranging from approximately 0.1 mm (0.004 inches) to 15 mm (0.59 inches) or more.
What Are The Disadvantages of Laser Cutting Plastic?
- Certain Plastics Have Limited Absorption: CO2 laser generators operate at a wavelength of approximately 10.6 microns, and many plastics absorb this wavelength well. However, CO2 laser generators may be less efficient or ineffective for certain plastic materials that have highly reflective or low absorption properties at this wavelength.
- Heat Generation: Laser cutting generates a lot of heat during the cutting process. This heat can sometimes cause localized melting, scorching, or deformation of plastic materials, especially when cutting thicker or heat-sensitive plastics.
- Not Suitable for All Plastics: Laser cutting may not be suitable for cutting some plastics, especially those with reflective surfaces or additives that do not readily absorb laser wavelengths. In this case, other cutting methods may be more appropriate.
- Material Odors and Fumes: Laser-cutting plastics can produce odors and fumes, especially those with additives or coatings. You may need adequate ventilation and filtration systems to address these emissions issues to maintain a safe and comfortable work environment.
- Edge Quality: Depending on the material and application, laser-produced cut edges may require additional post-processing steps, such as grinding or polishing, to achieve a smooth and desirable finish.
- Limited Thickness: While lasers can cut a variety of plastic materials, including acrylic and polycarbonate, their cutting efficiency decreases as the thickness of the material increases. Cutting very thick plastics may require extremely high-powered lasers or other cutting methods.
- Maintenance Requirements: Laser cutting machines require regular maintenance, including cleaning optics, aligning the laser beam, and replacing consumable parts such as lenses and mirrors. Failure to properly maintain your laser cutter can result in reduced cut quality and increased downtime.
- Initial Cost: While a laser cutting machine is cost-effective for many applications, the initial cost of purchasing and installing it can be high, making it less accessible to some small businesses or hobbyists.
Is Laser-Cutting Plastic Safe?
- Laser Radiation: Laser generators emit invisible infrared laser radiation. If not controlled properly, this radiation can cause damage to the eyes and skin. Therefore, safety precautions need to be implemented, including the use of appropriate laser safety goggles and protective clothing. Operators and other personnel near laser-cutting machines should be trained in laser safety protocols.
- Ventilation and Smoke Evacuation: Laser-cutting plastic produces smoke and odors, some of which may be harmful to health. Adequate ventilation and fume extraction systems help eliminate these emissions from the workspace and protect operators from inhaling potentially toxic fumes.
- Material Compatibility: Make sure the plastic being cut is compatible with laser cutting. Some plastics can produce harmful gases or exhibit unpredictable behavior when exposed to laser energy. Research and follow the Material Safety Data Sheet (MSDS) for the plastics you use.
- Fire Hazard: Laser cutting generates heat and, in some cases, sparks, which can create a fire hazard, especially when flammable plastics are used or combustible materials are present. It is recommended that work areas be cleared of flammable materials and fire-fighting equipment be available.
- Personal Protective Equipment (PPE): Operators should wear appropriate personal protective equipment (PPE), including safety goggles that protect the laser wavelength used. Specific personal protective equipment requirements may vary depending on the laser system and materials being processed.
- Training and Certification: Operators should receive appropriate training in laser safety and equipment operation. Certification programs for laser operators can increase safety awareness and competency.
- Regular Maintenance: Keep your laser cutting equipment well-maintained to ensure safe and reliable operation, including routine inspections, cleaning of optics, and replacement of worn or damaged parts.
How Long Is The Service Life of Plastic Laser-Cutting Machines?
- Machine Quality: The quality of the laser tube, optical devices, motion control system, cooling system, and other parts of the laser cutting machine plays a vital role in its service life. Higher-quality components are generally more durable and last longer.
- Intensity of Use: How often and for how long a machine is used affects its service life. Machines used daily for heavy production may have a shorter lifespan than machines used intermittently or with light workloads.
- Maintenance: Regular and proactive maintenance can help extend the life of your laser-cutting machine. This includes cleaning optics, aligning the laser beam, lubricating moving parts, and replacing consumable parts such as lenses and mirrors as needed.
- Environmental Conditions: The working environment of the laser cutting machine will affect its service life. Machines that operate in clean, temperature-controlled, and well-ventilated spaces tend to last longer than machines that operate in harsh or dusty environments.
- Laser Tube Life: The service life of the CO2 laser tube itself is a key factor. CO2 laser tubes have a limited service life and may need to be replaced. The life of a CO2 laser tube depends on its quality and usage but is generally 5,000 to 15,000 hours.
How To Maintain Plastic Laser Cutting Machines?
- Regular Cleaning: Clean the machine regularly to remove dust, debris, and residue that can accumulate on the laser optics, lenses, mirrors, and cutting beds. Use compressed air, lint-free cloths, and appropriate cleaning solutions recommended by the manufacturer.
- Inspect Optics and Mirrors: Check the condition of the laser optics and mirrors frequently for any signs of damage, dirt, or degradation. Clean or replace them as necessary to maintain optimal laser beam quality and cutting accuracy.
- Alignment Checks: Periodically check and adjust the alignment of the laser beam to ensure it remains properly aligned with the cutting path. Misalignment can result in poor cutting quality and accuracy.
- Maintain Exhaust System: Ensure the exhaust system is functioning correctly to remove smoke, fumes, and debris generated during the cutting process. Clean or replace filters, fans, and ducts as needed to maintain proper ventilation and air quality in the workspace.
- Cooling System Maintenance: If your laser cutting machine uses a water cooling system to cool the laser tube, regularly inspect and maintain the cooling system to prevent overheating and ensure efficient operation. Check water levels, clean filters, and replace coolant as necessary.
- Software Updates: Keep the machine’s control software up to date by installing any available updates or patches provided by the manufacturer. Updated software can improve performance, add new features, and address security vulnerabilities.
- Lubrication: Lubricate moving parts such as rails, bearings, and drive mechanisms according to the manufacturer’s recommendations to reduce friction, prevent wear, and ensure smooth operation.
- Safety Checks: Regularly inspect safety features such as interlocks, emergency stop buttons, and laser safety enclosures to ensure they are working correctly and compliant with safety regulations.
- Training and Education: Provide training for operators on proper machine operation, maintenance procedures, and safety precautions. Educated operators are better equipped to identify potential issues and perform routine maintenance tasks effectively.
- Professional Service: Schedule regular maintenance checks and servicing by qualified technicians to identify and address any potential issues before they escalate into major problems. Follow the manufacturer’s recommended service intervals and guidelines.
Related Resources
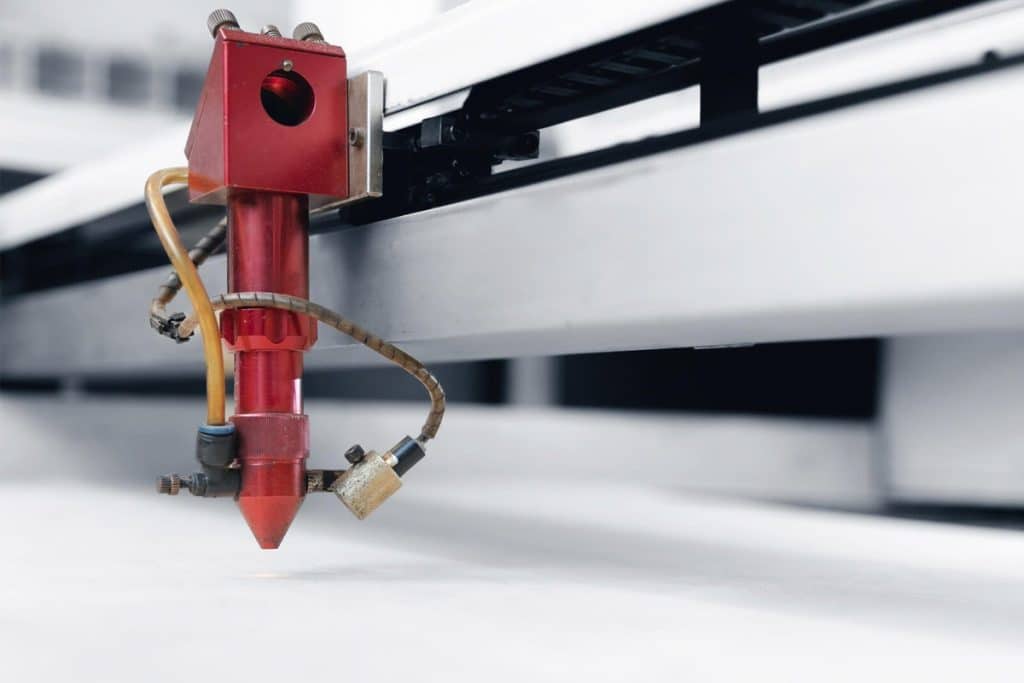
Can a CO2 Laser Cutting Machine Perform Cutting and Engraving Tasks at the Same Time?
Can CO2 laser cutting machines achieve “multi-purpose use” of precise cutting and fine engraving? This article combines the principle with the functional characteristics of AccTek’s CO2 laser cutting machines to
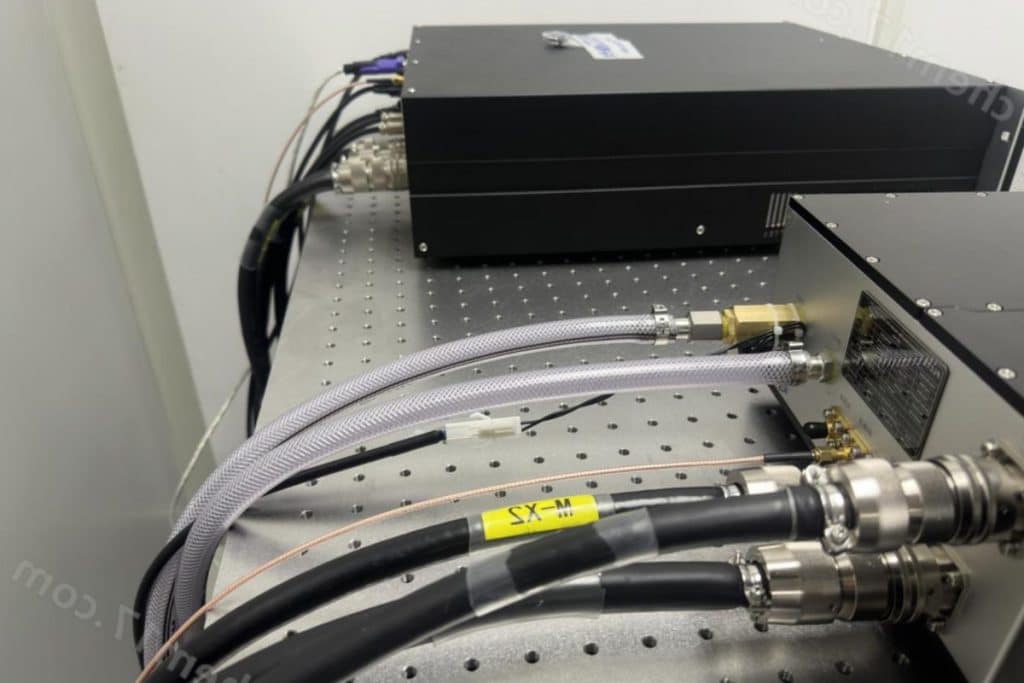
Do Fiber Laser Generators Lose Power over Time?
This article focuses on the reasons why fiber laser generator power decreases over time and proposes effective strategies to mitigate power loss through high-quality equipment, regular maintenance, and an optimized
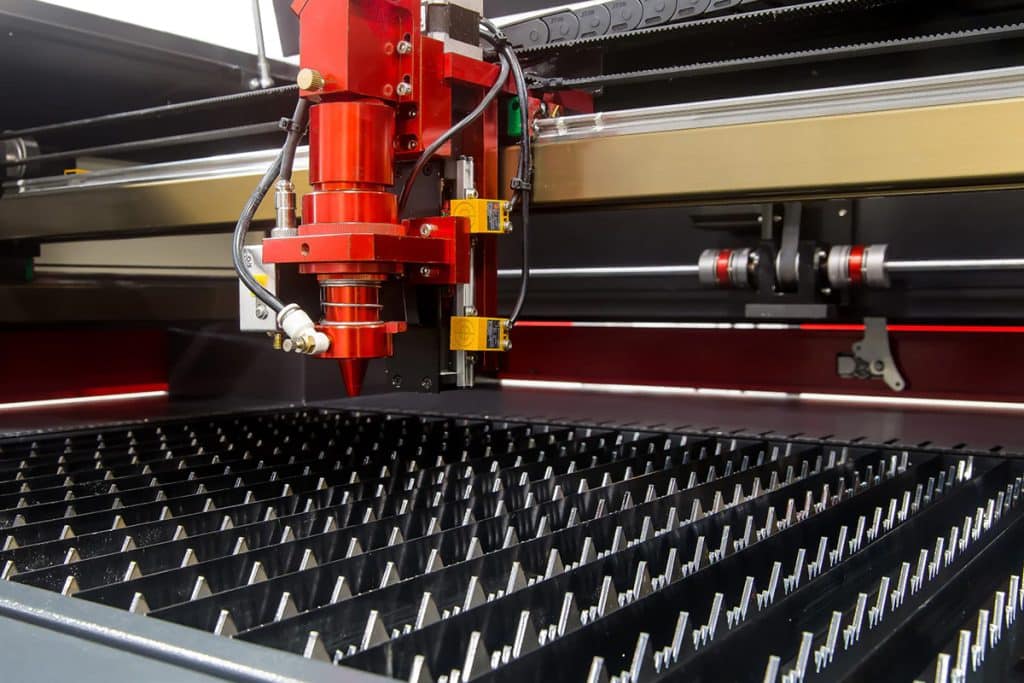
How Does a CO2 Laser Cutting Machine Achieve High-Precision Cutting?
This article mainly introduces the principles and key technologies behind the high-precision cutting capabilities of CO2 laser cutting machines, and analyzes their core structural components and advantages.