Sheet Laser Cutting Machine
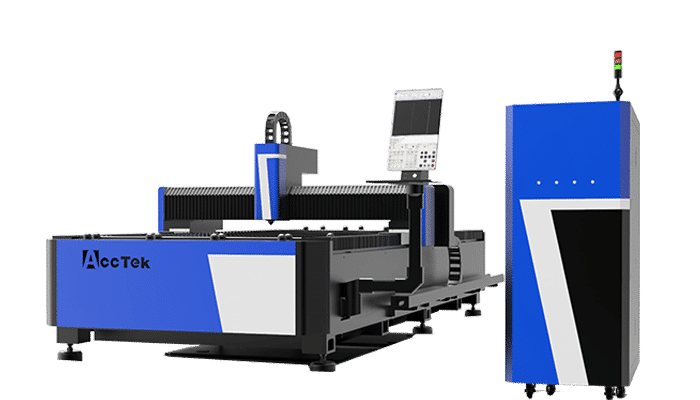
Product Range
-
AKJ-F1 Laser Cutting Machine
Rated 5.00 out of 5$13,300.00 – $33,000.00 Select options This product has multiple variants. The options may be chosen on the product page -
AKJ-F2 Laser Cutting Machine
Rated 5.00 out of 5$18,000.00 – $66,000.00 Select options This product has multiple variants. The options may be chosen on the product page -
AKJ-F3 Laser Cutting Machine
Rated 5.00 out of 5$19,300.00 – $168,000.00 Select options This product has multiple variants. The options may be chosen on the product page -
AKJ-FB Laser Cutting Machine
Rated 4.75 out of 5$22,000.00 – $174,000.00 Select options This product has multiple variants. The options may be chosen on the product page -
AKJ-FC Laser Cutting Machine
Rated 4.75 out of 5$22,500.00 – $175,000.00 Select options This product has multiple variants. The options may be chosen on the product page -
AKJ-FBC Laser Cutting Machine
Rated 4.75 out of 5$26,500.00 – $182,000.00 Select options This product has multiple variants. The options may be chosen on the product page
Optional Sheet Laser Cutting Machine Power
Materials That Can Be Cut
Laser Cutting VS. Other Methods
Laser Cutting vs. Mechanical Cutting
Laser cutting outperforms mechanical cutting in precision and edge quality. It requires no physical contact with the material, reducing wear and tear on tools. Mechanical cutting, while cost-effective, can result in rough edges, slower speeds, and more material wastage, especially for complex shapes.
Laser Cutting vs. Water Jet Cutting
Laser cutting offers faster speeds and higher accuracy, especially for thin materials. Water jet cutting, while versatile and effective for thick or heat-sensitive materials, is slower and requires maintenance of the abrasive used in the process. Laser cutting leaves smoother edges with minimal post-processing.
Laser Cutting vs. Plasma Cutting
Laser cutting delivers superior edge quality and precision compared to plasma cutting. While plasma cutting is faster and more economical for thicker materials, it produces rougher edges and causes heat distortion. Laser cutting offers clean, fine cuts with minimal thermal impact, reducing the need for additional finishing.
Why Choose AccTek Laser
Cutting-Edge Technology
AccTek Laser machines utilize the latest laser technology, ensuring high precision and fast cutting speeds. Our systems provide unmatched accuracy and efficiency, ensuring the best quality cuts across various materials with minimal distortion.
Custom Solutions
We understand that every business has unique requirements. That's why we offer customizable options, including power ranges, work area sizes, and cutting speeds, allowing you to tailor our machines to fit your specific production needs and material types.
Exceptional Energy Efficiency
Our laser cutting machines are designed for maximum energy efficiency. With lower power consumption and optimized performance, AccTek Laser machines help reduce operational costs, making them a cost-effective solution for both small and large-scale manufacturing.
Durability and Reliability
AccTek Laser cutting machines are engineered for long-term durability, with high-quality components and precision manufacturing. Our machines are designed to provide consistent, reliable performance, reducing maintenance needs and extending the lifespan of your equipment.
After-Sales Support
We believe in building long-term relationships with our customers. AccTek Laser provides exceptional after-sales support, including installation, training, and ongoing technical assistance. Our team is always ready to help you optimize machine performance and resolve any issues quickly.
Competitive Pricing and Value
At AccTek Laser, we offer high-performance laser-cutting machines at competitive prices, ensuring that you get the best value for your investment. Our machines deliver outstanding quality at an affordable cost, making us a trusted partner for your manufacturing needs.
Frequently Asked Questions
What Are Sheet Laser Cutting Machines?
What Software Do Sheet Laser Cutting Machines Use?
What Is The Price Of Sheet Laser Cutting Machines?
How Precise Are The Cuts Achieved With Sheet Laser-Cutting Machines?
- Laser Beam Quality: High-quality laser beams with consistent power distribution and focus produce cleaner and more accurate cuts. Beam quality is influenced by factors such as the type of laser (CO2, fiber, etc.), beam mode, and stability.
- Control Systems: Advanced CNC (Computer Numerical Control) systems precisely control the movement of the laser beam and cutting head, ensuring accurate positioning and trajectory during the cutting process.
- Material Thickness and Type: Thinner materials generally allow higher precision cuts due to reduced heat-affected zones and less material distortion. However, modern laser-cutting machines can achieve precise cuts on various materials, including metals, plastics, wood, and composites.
- Cutting Speed: Optimal cutting speeds must be maintained to ensure clean and accurate cuts. Too slow or too fast cutting speeds can affect cut quality and precision.
- Maintenance and Calibration: Regular maintenance and calibration of machine components, including the laser source, cutting head, and motion control system, can help maintain cutting accuracy over the long term.
What Is The Lifespan of Sheet Laser-Cutting Machines?
- Quality of Components: Higher-quality machines with durable components, such as robust laser sources, cutting heads, motion control systems, and cooling systems, tend to have longer lifespans.
- Maintenance: Regular maintenance, including cleaning, lubrication, calibration, and replacement of worn parts, helps extend the life of your machine. Neglecting maintenance can lead to premature wear and tear and reduced performance.
- Usage Intensity: The frequency and intensity of usage can impact the machine’s lifespan. Machines used for high-volume production with continuous operation may experience more wear and tear compared to those used for occasional or low-volume production.
- Environmental Factors: The operating environment, including temperature, humidity, dust levels, and vibration, can affect the machine’s performance and longevity. Proper environmental controls and safeguards can help mitigate these factors.
- Technological Advancements: Technological advancements in laser cutting technology may lead to the obsolescence of older machines over time. However, many machines can still be upgraded or retrofitted with newer components to extend their usefulness.
- Manufacturer Support: The availability of manufacturer support, including spare parts, technical assistance, and software updates, can also influence the machine’s lifespan. Machines from reputable manufacturers with good support infrastructure may have longer service lives.
What Maintenance Do Sheet Laser Cutting Machines Require?
- Daily Maintenance
- Clean the Machine: Remove dust, debris, and metal shavings from the cutting area, guide rails, and other components using compressed air or a vacuum.
- Check for Coolant and Oil Levels: Ensure adequate levels of coolant and lubricating oil in the machine’s reservoirs and top up as needed.
- Inspect Optics: Check laser optics, including lenses, mirrors, and protective windows, for cleanliness, damage, or signs of degradation. Clean or replace as necessary.
- Check Gas Supply: Ensure proper supply and pressure of assist gases (e.g., oxygen, nitrogen) used during cutting.
- Weekly or Bi-Weekly Maintenance
- Inspect and Clean Filters: Check and clean or replace air and coolant filters to maintain optimal airflow and cooling efficiency.
- Lubricate Moving Parts: Apply lubricants to bearings, ball screws, linear guides, and other moving parts according to the manufacturer’s recommendations.
- Check Alignment: Verify the alignment of the laser beam, cutting head, and motion system components. Adjust or realign as needed to maintain cutting accuracy.
- Test Safety Features: Verify the functionality of safety interlocks, emergency stop buttons, and other safety features.
- Monthly Maintenance
- Inspect Electrical Connections: Check for loose or damaged electrical connections, wires, and cables. Tighten connections and repair or replace damaged components as necessary.
- Perform Calibration: Calibrate the machine’s motion control system, laser power, and other parameters to ensure accurate cutting performance.
- Check Water Chiller: Inspect and clean the water chiller system, including filters, pumps, and hoses. Monitor coolant temperature and flow rate.
- Quarterly or Semi-Annual Maintenance
- Perform Preventive Maintenance: Follow the manufacturer’s recommended preventive maintenance schedule, which may include more in-depth inspections, adjustments, and component replacements.
- Test Laser Power: Verify the laser’s power output using a calibrated power meter and adjust as needed.
- Annual Maintenance
- Conduct Thorough Inspection: Perform a comprehensive inspection of all machine components, including mechanical, electrical, and laser-related systems. Address any issues identified during the inspection.
- Replace Consumable Parts: Replace consumable components such as cutting nozzles, protective windows, and gas filters.
- As Needed
- Address Issues Promptly: Address any performance issues, abnormal sounds, or error messages promptly to prevent further damage or downtime.
- Software Updates: Keep machine control software and firmware up to date by installing the latest updates and patches provided by the manufacturer.
What Are The Operating Costs Of Sheet Laser Cutting Machines?
- Material Costs: The cost of materials being cut is a significant factor in operating expenses. This includes the cost of metal sheets, acrylic, wood, or other materials being processed. Material costs can vary depending on material type, thickness, quality, and market prices.
- Energy Consumption: Laser-cutting machines require electricity to power the laser source, motion systems, cooling systems, and other components. The energy consumption of the machine depends on its power rating, usage patterns, and efficiency. Higher-powered machines and longer cutting times typically result in higher energy costs.
- Consumables: Laser cutting machines use consumable components that need regular replacement, such as cutting nozzles, protective windows, gas filters, and coolant. The frequency of replacement depends on usage patterns, material types, and machine maintenance practices.
- Maintenance and Repairs: Regular maintenance is essential for ensuring optimal performance and longevity of the machine. Maintenance costs include expenses related to cleaning, lubrication, calibration, component replacement, and repairs. The frequency and cost of maintenance depend on the machine’s quality, usage, and manufacturer recommendations.
- Labor Costs: Labor costs include wages for machine operators, maintenance personnel, and other staff involved in operating and maintaining the laser cutting machine. The number of operators required and their skill level can impact labor costs.
- Overhead Expenses: Overhead expenses include indirect costs such as facility rent, insurance, taxes, utilities, and administrative expenses. These costs are typically allocated across all operations within a manufacturing facility.
- Software and Tooling: Additional costs may arise from purchasing and maintaining software for designing and programming cutting patterns, as well as any specialized tooling or fixturing required for specific applications.
- Waste Disposal: Disposal costs may apply for handling and disposing of waste materials generated during the cutting process, such as metal scraps, slag, and coolant.
Are There Environmental Considerations For Sheet Laser-Cutting Machines?
- Emissions: Laser-cutting machines produce emissions, primarily in the form of fumes and particulate matter, especially when cutting certain materials like metals, plastics, and composites. These emissions can contain hazardous substances, such as metal oxides and volatile organic compounds (VOCs), which may pose health and environmental risks if not properly controlled. It’s essential to implement appropriate ventilation and filtration systems to capture and remove these emissions from the workplace.
- Noise: Sheet laser cutting machines can generate significant noise levels during operation, particularly when cutting thicker materials or operating at higher speeds. Prolonged exposure to high noise levels can cause hearing damage and other health issues for operators and nearby workers. Implementing soundproofing measures, providing hearing protection, or scheduling noisy operations during off-peak hours can help mitigate noise pollution.
- Energy Consumption: Laser-cutting machines require electricity to power the laser source, motion systems, and other components. Depending on the machine’s power and usage patterns, this can result in significant energy consumption. Implementing energy-efficient practices, such as optimizing cutting parameters, scheduling jobs efficiently, and investing in energy-saving technologies, can help reduce energy usage and minimize environmental impact.
- Coolant and Lubricants: Some laser cutting machines use coolant and lubricants to maintain optimal cutting performance and extend the lifespan of machine components such as bearings and ball screws. However, these fluids can pose environmental risks if not properly managed and disposed of. Implementing proper fluid management practices, such as recycling coolants and using environmentally friendly lubricants, can help minimize environmental impact.
- Waste Generation: Laser cutting processes can generate waste materials such as metal scraps, slag, and offcuts, especially during initial setup and when cutting complex shapes. Proper waste management practices, such as recycling metal scraps and segregating hazardous waste, can help minimize the environmental impact of waste generation.
- Water Usage: Some laser cutting machines use water for cooling purposes, particularly in the case of CO2 lasers. It’s essential to monitor water usage and implement water-saving measures where possible to minimize water consumption and reduce environmental impact.
Related Resources
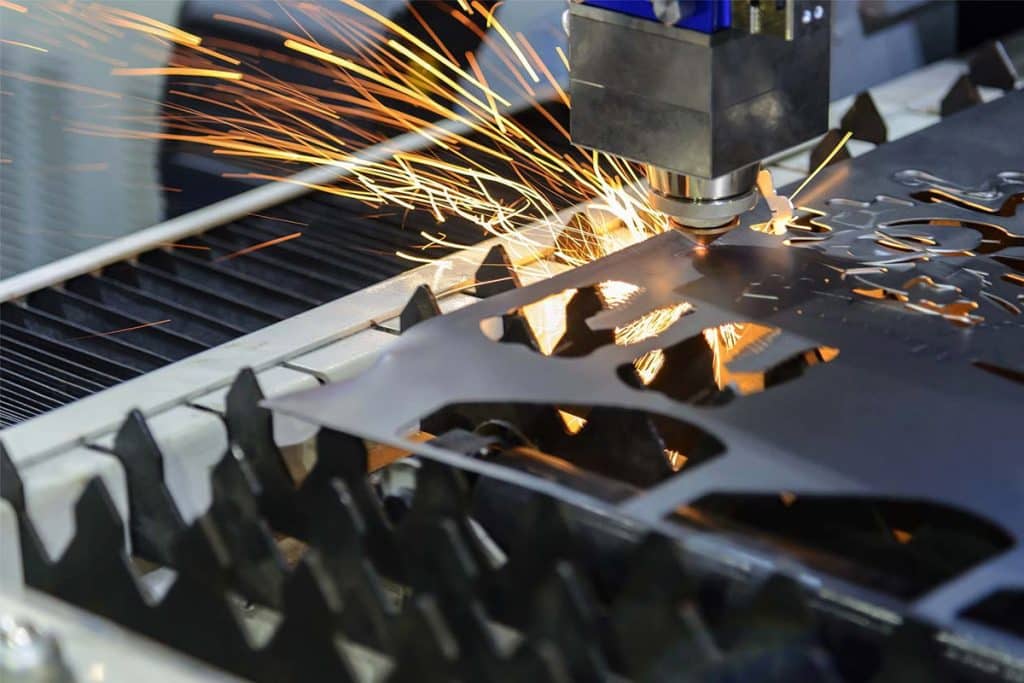
The Influence of Control System on Fiber Laser Cutting Machine
The control system of the fiber laser cutting machine plays a vital role in ensuring cutting accuracy, improving production efficiency and operating convenience, and is one of the indispensable core
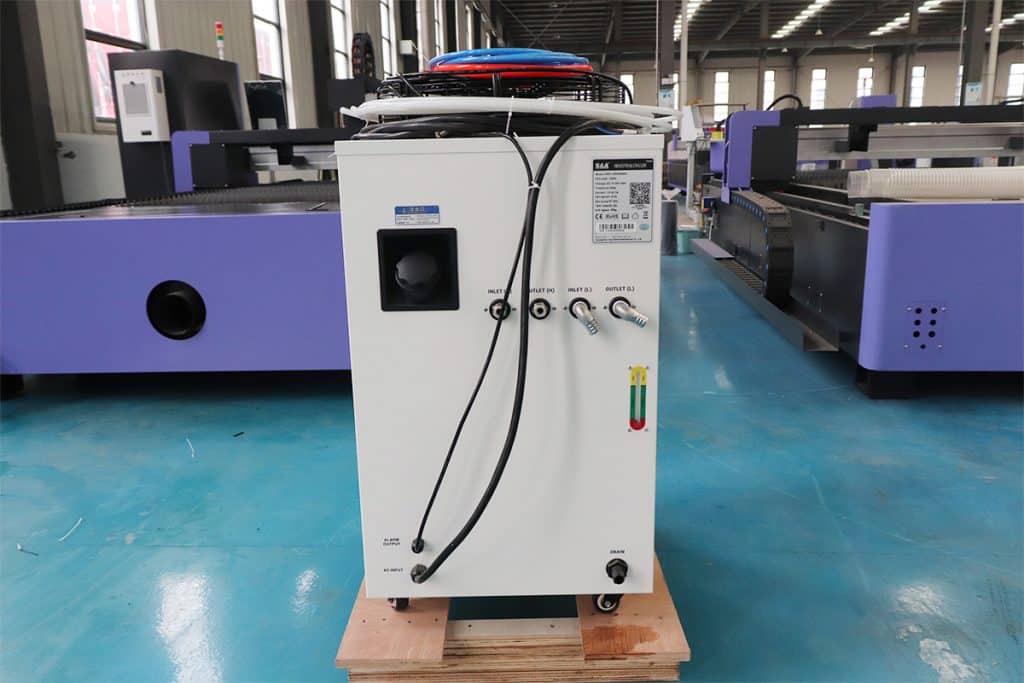
Understanding the Cooling System of Fiber Laser Cutting Machine
This article mainly introduces the functions, types, and maintenance points of the cooling system of the fiber laser cutting machine, highlighting its importance to equipment stability and cutting quality.
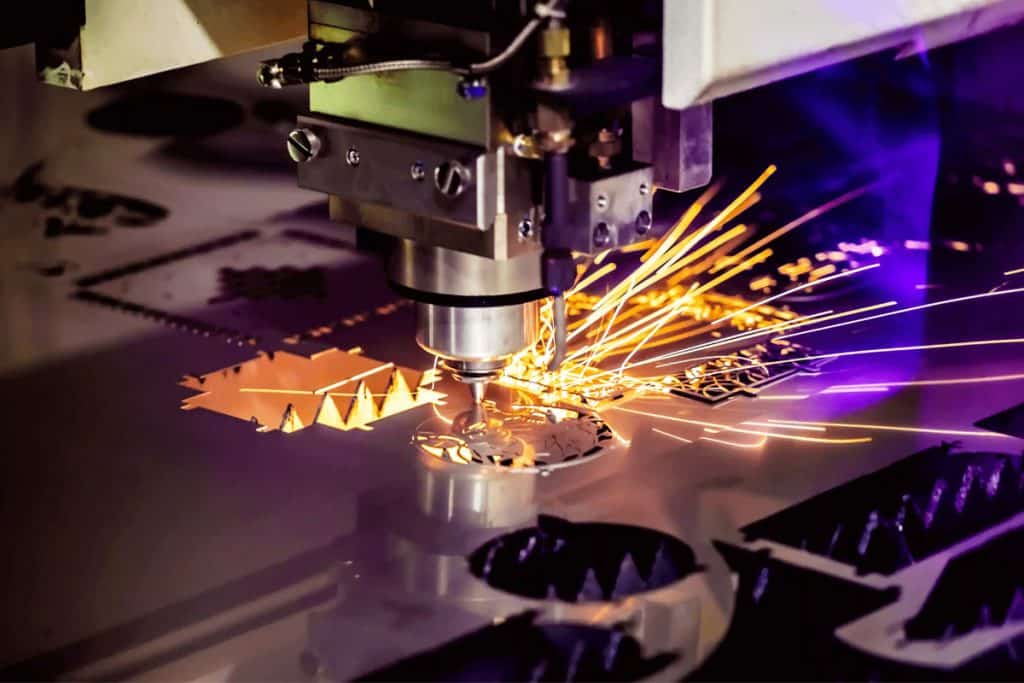
Challenges and Limitations of Fiber Laser Cutting Technology
This article discusses the challenges and solutions of fiber laser cutting technology, emphasizing the importance of technological innovation and management optimization in improving efficiency and reducing costs.