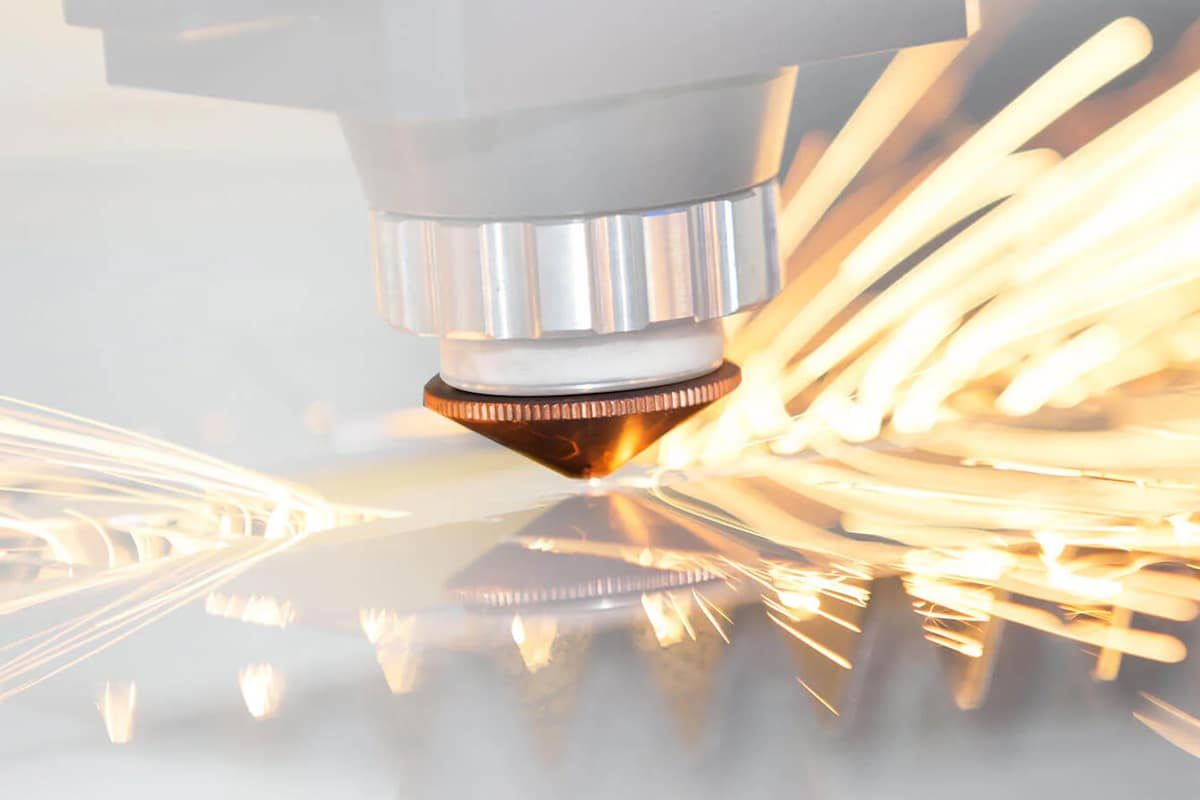
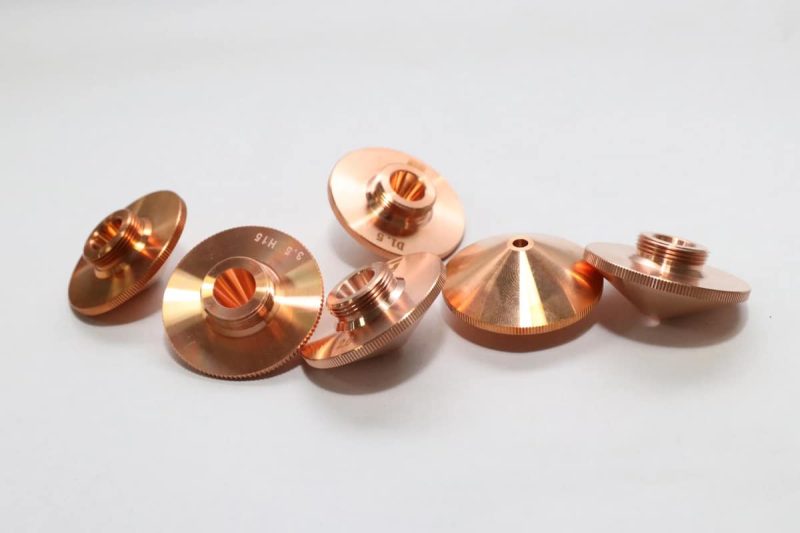
Understanding Laser Cutting Nozzles
Definition
Function
The primary function of a laser cutting machine nozzle is to direct the laser beam and assist gas to the cutting area with high precision. Here is a breakdown of its main functions:
- Beam Focusing and Direction: The nozzle helps focus and direct the laser beam onto the workpiece. Proper focusing ensures that the laser beam has the optimal strength and precision required to effectively cut different materials.
- Assist Gas Delivery: Assist gas (such as oxygen, nitrogen, or air) is directed to the cutting zone through the nozzle. The choice of gas and its pressure can significantly affect the cutting speed, quality, and type of materials that can be cut. The nozzle ensures that the gas flow is consistent and properly directed, assisting the cutting process by blowing away molten material, cooling the cut, and preventing oxidation.
- Heat Management: By directing the assist gas flow, the nozzle helps dissipate the heat generated during the cutting process. This helps maintain a steady cutting temperature and prevents overheating, which can cause material deformation or damage.
- Cut Quality Enhancement: The design and size of the nozzle affects the quality of the cut. A well-chosen nozzle can produce cleaner cuts with minimal slag, smoother edges, and higher precision, reducing the need for post-processing.
- Laser Optics Protection: The nozzle also acts as a protective barrier for the laser head optics, protecting them from debris and spatter generated during the cutting process. This protection preserves the life and performance of your laser-cutting machine.
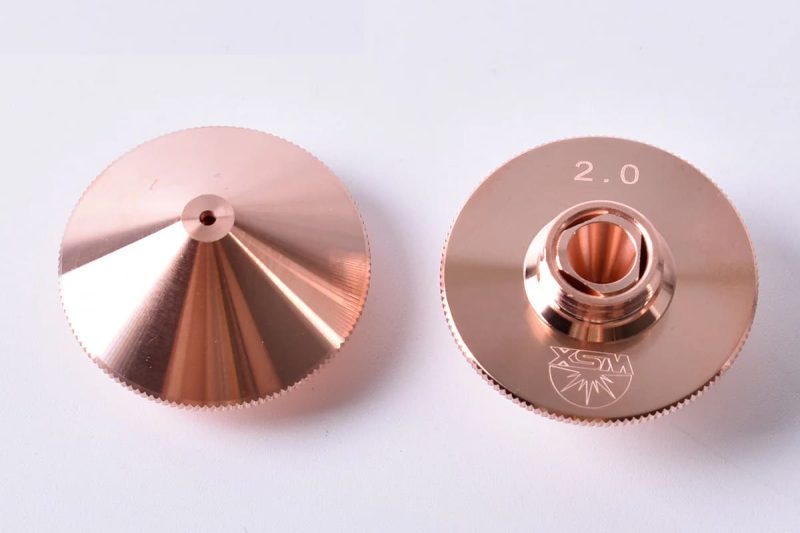
Types of Laser Cutting Nozzles
Single-Layer Nozzles
Definition
Features
- Simple: The design of single-layer nozzles is simple, making them easy to manufacture and maintain.
- Durability: Single-layer nozzles are made from sturdy materials such as brass or copper to withstand the high temperatures and wear encountered during the metal cutting process.
- Cost-Effective: These nozzles are generally less expensive than dual-layer nozzles, providing an affordable option for many metal-cutting applications.
- Precision: Single-layer nozzles provide precise control of the laser beam and assist gas, ensuring high-quality cuts on thinner metal sheets.
Applications
Single-layer nozzles are versatile and suitable for a variety of metal-cutting tasks. They are ideal for:
- Thin to Medium-Thick Metals: Particularly suitable for cutting less thick metals, such as sheet metal, where precise and clean cuts are required.
- Everyday Use: These nozzles are often used in standard laser cutting operations because they are reliable and easy to use when cutting metals such as stainless steel, aluminum, and mild steel.
Dual-Layer Nozzles
Definition
Features
- Enhanced Cooling: The dual-layer construction provides better heat dissipation, which helps maintain cut quality and extend the life of the nozzle when cutting metal.
- Improved Gas Flow: These nozzles help deliver assist gas more efficiently, which improves cutting speed and accuracy by effectively removing molten metal and preventing oxidation.
- Increased Durability: The additional layer provides additional protection against wear, making them more durable during intensive metal-cutting operations.
- Superior Performance: They allow for better control of the laser beam and gas flow, which is beneficial for high-precision cutting and processing of thicker metal sheets.
Applications
Dual-layer nozzles are designed for specialized and demanding metal-cutting tasks. They are best suited for:
- Thick Metal Cutting: Ideal for cutting thicker metals where effective heat management and accuracy are critical, such as in the automotive and aerospace industries.
- High-Precision Tasks: Ideal for applications that require intricate designs and high-quality edges on metals such as titanium, copper, and brass.
- Industrial Use: Typically used in industrial environments where laser cutting operations are intensive and nozzle life is important.
- Specialty Metal Cutting: Ideal for cutting harder, more challenging metals, offering enhanced performance characteristics.
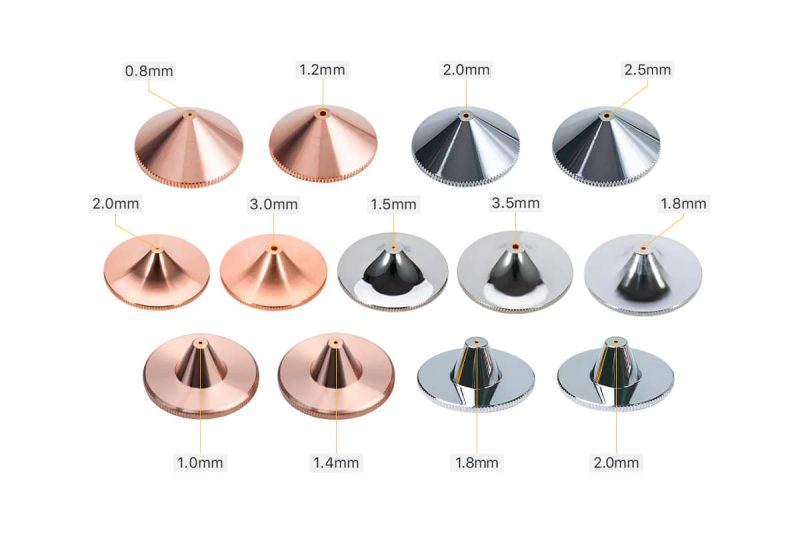
Nozzle Dimensions
Diameter of the Nozzle Opening
Small Diameter Nozzles (1.0-1.5 mm)
- Applications: Best suited for precision cutting of thin materials where a fine, concentrated laser beam is required.
- Advantages: Provides higher accuracy and detail in cuts, and is effective in reducing the width of the heat-affected zone (HAZ).
- Limitations: Smaller openings can restrict the flow of assist gases, which may impact the efficiency of cutting thicker materials.
Medium Diameter Nozzles (1.5-2.5 mm)
- Applications: Suitable for a wide range of general-purpose cutting tasks on medium-thickness materials.
- Advantages: Offers a good balance between precision and gas flow, making it versatile for various cutting conditions.
- Limitations: May not provide the highest precision for very thin materials or the best efficiency for very thick materials.
Large Diameter Nozzles (2.5 mm and above)
- Applications: Ideal for cutting thicker materials where a broader assist gas flow is needed to remove molten material efficiently.
- Advantages: Enhances cutting speed and efficiency for thick materials, helps in the effective removal of slag, and minimizes the risk of dross formation.
- Limitations: Larger openings may reduce the precision of cuts and increase the width of the heat-affected zone (HAZ).
Length of the Nozzle
Short Nozzles
- Applications: Typically used for high-precision cutting tasks where proximity to the material is necessary.
- Advantages: Provides better control over the laser beam and assists gas, enhancing precision.
- Limitations: Shorter nozzles may increase the risk of collisions with the material surface or other obstacles.
Long Nozzles
- Applications: Suited for cutting thicker materials or in situations where the material surface is uneven.
- Advantages: Allows for greater flexibility in standoff distance, reducing the risk of collisions and accommodating material irregularities.
- Limitations: May reduce the precision of the cut due to the increased distance from the material surface.
Shape of the Nozzle Tip
Conical Tips
- Applications: Generally used for cutting tasks requiring high precision and smooth edges.
- Advantages: Facilitates a more focused laser beam and gas flow, enhancing cutting quality and precision.
- Limitations: Conical tips may wear out faster due to their shape, especially when used for cutting thick or abrasive materials.
Cylindrical Tips
- Applications: Suitable for cutting thicker materials and for general-purpose cutting tasks.
- Advantages: Provides a more uniform gas flow, which is beneficial for efficient removal of molten material during cutting.
- Limitations: May not offer the same level of precision as conical tips for very fine cutting tasks.

Nozzle Material
Brass Nozzle
Definition
Features
- Thermal Conductivity: Brass has good thermal conductivity, which helps to effectively dissipate heat during the cutting process. This reduces the risk of overheating and extends the life of the nozzle.
- Durability: Brass nozzles are strong and durable, resistant to wear and tear, and suitable for high-frequency use in industrial environments.
- Corrosion Resistance: Brass is corrosion-resistant, ensuring that the nozzle maintains its performance and integrity for a long time even in harsh environments.
- Cost-Effective: Brass nozzles are often more affordable than other high-performance materials, providing a cost-effective solution for many laser-cutting applications.
Applications
Brass nozzles are widely used in a variety of metal cutting applications due to their balanced conductivity and durability. They are ideal for:
- General Metal Cutting: Suitable for cutting a variety of metals such as stainless steel, aluminum, and carbon steel.
- High-Frequency Use: Their durability makes them suitable for continuous and high-frequency cutting operations in industrial environments.
- Budget-Conscious Operation: Ideal for users looking for a cost-effective solution without compromising performance.
Considerations
Copper Nozzles
Definition
Features
- Excellent Thermal Conductivity: Copper has the highest thermal conductivity among common nozzle materials, allowing it to dissipate heat more efficiently. This property helps maintain the temperature of the nozzle and prevent overheating, ensuring consistent cutting performance.
- Electrical Conductivity: Copper’s excellent electrical conductivity makes it ideal for applications where electrostatic discharge may be an issue, improving safety and performance.
- Durability and Strength: Copper nozzles are rugged and can withstand the rigors of intensive cutting operations, making them suitable for demanding applications.
- Enhanced Cut Quality: Copper’s superior thermal properties enable smoother, more precise cuts, especially when dealing with high-power laser operations and challenging materials.
- Oxidation Resistance: Copper nozzles are often coated or treated to prevent oxidation, which would otherwise affect performance and lifespan.
Applications
Due to their superior performance characteristics, copper nozzles are the top choice for high-precision and high-speed cutting tasks. They are ideal for:
- Precision Metal Cutting: Suitable for cutting tasks that require high accuracy and clean edges, such as aerospace and automotive components.
- Thick Sheet Metal: Ideal for cutting thicker sheet metal, effective heat management helps prevent warping and maintain cut quality.
Considerations
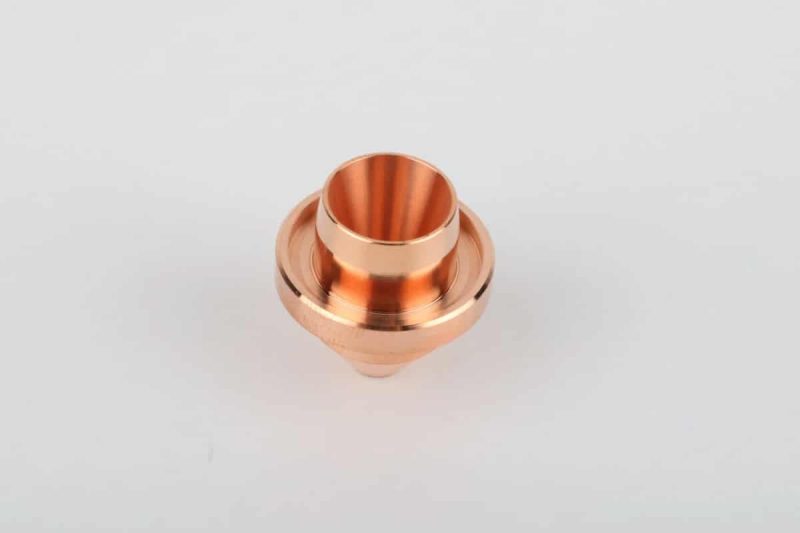
Factors Affecting Nozzle Performance
Nozzle Material
- Thermal Conductivity: The material of the nozzle (e.g., brass or copper) affects its ability to dissipate heat. Copper has excellent thermal conductivity and generally performs better in high-precision and high-speed cutting applications.
- Durability: Materials such as brass have good durability and wear resistance, making them suitable for general cutting tasks. The choice of material will affect the life of the nozzle and the frequency of maintenance.
Nozzle Size
The diameter and length of the nozzle opening have a large impact on nozzle performance:
- Diameter: Smaller diameter nozzles provide a more focused beam and finer gas flow, which helps with precision cutting. Larger diameter nozzles allow for higher gas flow and cutting speeds for thicker materials.
- Length: Nozzle length affects heat dissipation and gas flow stability. Shorter nozzles are easier to handle and change, while longer nozzles provide better cooling and are suitable for cutting thicker materials.
Gas Flow and Pressure
- Assist Gas Type: The type of assist gas (oxygen, nitrogen, or air) affects the cutting process. Oxygen is often used to cut carbon steel due to its reactivity, while nitrogen is used to cut stainless steel and aluminum to prevent oxidation.
- Gas Pressure: Proper gas pressure ensures efficient removal of molten material and prevents oxidation. High gas pressure is suitable for cutting thick materials, while lower gas pressure is suitable for thin materials to avoid over-ejection.
Beam Alignment and Focus
- Alignment: Precise alignment of the nozzle with the laser beam can help achieve a clean cut. Misalignment can result in poor cut quality and increased nozzle wear.
- Focal Position: The focus of the laser beam must be set precisely relative to the workpiece. Incorrect focusing can result in poor edge quality, reduced cutting speeds, and increased material waste.
Cutting Speed and Power
- Speed: Cutting speed affects the interaction between the laser beam and the material. Faster speeds provide more laser power and more efficient airflow, while slower speeds provide better-cut quality but may increase the risk of heat buildup.
- Power: Sufficient laser power is required to penetrate the material and achieve a clean cut. Power settings must be optimized based on material type and thickness.
Nozzle Maintenance and Condition
- Cleanliness: Regularly cleaning the nozzle prevents debris buildup, which can block airflow and affect beam quality. Dirty nozzles can lead to inconsistent cutting and reduced performance.
- Wear and Damage: Checking the nozzle for wear and damage ensures optimal performance. Worn or damaged nozzles should be replaced promptly to maintain cutting quality.
Environmental Conditions
- Temperature and Humidity: Environmental factors such as temperature and humidity can affect the cutting process. High temperatures can cause overheating, while high humidity can cause condensation, which can affect the laser beam and gas flow.
- Workpiece Condition: The surface condition of the workpiece, including cleanliness and flatness, can also affect nozzle performance. Contaminants on the workpiece can cause irregular cuts.
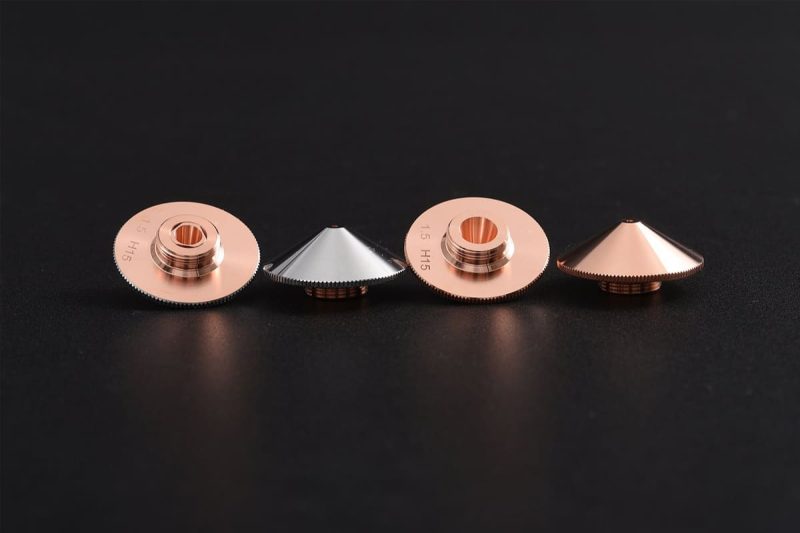
Choosing the Right Nozzle
Factors to Consider When Choosing Nozzles
Material Type
- Mild Steel: For cutting mild steel, single-layer nozzles with oxygen-assist gas are often used because they can increase cutting speeds and produce cleaner cuts through an exothermic reaction.
- Stainless Steel: Stainless Steel cutting often uses a dual-layer nozzle with nitrogen as the assist gas to prevent oxidation and achieve a clean cut without discoloration.
- Aluminum: Cutting aluminum often requires the use of a dual-layer nozzle with nitrogen or compressed air to avoid oxidation and ensure a smooth cut. Nitrogen is the preferred choice for high-quality cuts, while compressed air can be a cost-effective alternative.
Material Thickness
- Thin Materials (< 5mm): Smaller diameter nozzles (e.g. 0.8mm to 1.2mm) provide a more focused beam and finer gas flow, which helps achieve precision cuts. They are often used with high-pressure nitrogen or oxygen.
- Medium Thickness (5mm – 12mm): Medium diameter nozzles (e.g. 1.2mm to 2mm) strike a balance between focus and gas flow, and are suitable for a wide range of metals. Oxygen is often used for mild steel, while nitrogen is used for stainless steel and aluminum.
- Thick Materials (> 12mm): Larger diameter nozzles (e.g. 2mm to 3mm or larger) allow for higher gas flow, which helps effectively remove molten material and prevent overheating. They are often used with low-pressure oxygen for mild steel or high-pressure nitrogen for stainless steel and aluminum.
Cutting Speed and Accuracy
- High Precision: For intricate designs and high-precision cuts, smaller nozzles with narrower openings are ideal. These nozzles are often used in conjunction with high-pressure nitrogen to ensure clean, precise edges that do not oxidize.
- High Speed: A large nozzle with a wider opening is recommended for faster cutting speeds to maintain cut quality and effectively control heat. Oxygen is often used to increase cutting speeds on mild steel.
Common Nozzle Recommendations
Single-Layer Nozzle
- 8-1.2mm Diameter: Suitable for cutting thin metals (e.g. stainless steel and aluminum up to 5mm thick). It provides precise cutting and fine details and is often used with high-pressure nitrogen.
- 2-2mm Diameter: Suitable for medium-thick metals (e.g. stainless steel, carbon steel, and aluminum from 5mm to 12mm thick). It balances precision and airflow and is often used with oxygen for cutting mild steel and with nitrogen for cutting stainless steel and aluminum.
- 2-3mm Diameter: Best for thick metals (>12mm). It ensures efficient airflow and heat management and is suitable for heavy-duty cutting with low-pressure oxygen or high-pressure nitrogen.
Dual-Layer Nozzle
- 0-1.5mm Diameter: For high-precision cutting of thin to medium-thick metals. It enhances beam focusing and airflow for clean, detailed cuts. Ideal for use with nitrogen for cutting stainless steel and aluminum.
- 5-2.5mm Diameter: Suitable for a wide range of thicknesses, providing better cooling and durability. Ideal for industrial applications requiring high-quality cuts, typically used with oxygen for mild steel and nitrogen for stainless steel and aluminum.
- 5-3mm Diameter: Designed for thick metals, providing superior performance in heat dissipation and cut quality. Best for demanding and continuous cutting tasks, typically used in combination with high-pressure nitrogen for stainless steel and aluminum.
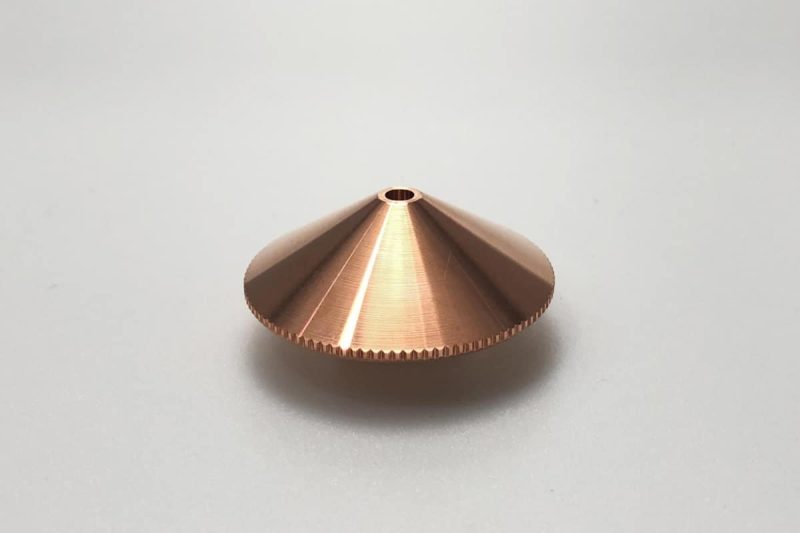
Maintenance and Care
Regular Cleaning
Daily Cleaning
- Visual Inspection: Visually inspect the nozzle daily for debris, spatter, or any visible damage.
- Cleaning Tools: Use a soft brush, microfiber cloth, and appropriate cleaning solution to remove any accumulated debris. Avoid using abrasive materials that could scratch or damage the nozzle.
- Compressed Air: Use compressed air to blow away any fine particles from the nozzle opening and threads.
Weekly Deep Cleaning
- Nozzle Removal: Carefully remove the nozzle from the laser head, following the manufacturer’s instructions to avoid misalignment or damage.
- Soaking: Soak the nozzle in a cleaning solution designed for laser cutting equipment to dissolve any stubborn deposits.
- Ultrasonic Cleaning: For a thorough cleaning, use an ultrasonic cleaner to remove fine particles and residue from the inside and outside surfaces of the nozzle.
Nozzle Inspection
Check for Wear
- Signs of Wear: Regularly inspect the nozzle for signs of wear, such as erosion at the nozzle tip, widening of the nozzle opening, or any deformation.
- Nozzle Opening: Use a magnifying glass or microscope to inspect the nozzle opening for any irregularities that could affect laser beam focus and airflow.
Alignment Verification
- Proper Alignment: Make sure the nozzle is properly aligned with the laser beam. Misalignment can result in uneven cutting, increased wear, and poor cut quality.
- Alignment Tool: Use the alignment tool and gauge provided by the manufacturer to check and adjust the nozzle alignment as needed.
Replacement Guide
When to Replace
- Degraded Performance: Replace the nozzle if you notice a noticeable decrease in cutting performance, such as poor cut quality, increased dross, or inconsistent cutting.
- Visible Damage: Replace the nozzle if it shows visible signs of damage or wear that cannot be corrected by cleaning or readjusting.
Spare Nozzles
- Spare Parts Inventory: Keep a stock of spare nozzles to minimize downtime. Make sure you have a variety of nozzle sizes and types that match your cutting requirements.
- Manufacturer Specifications: Always use nozzles specified by the manufacturer of your laser cutting machine to ensure compatibility and optimal performance.
Preventative Maintenance
Regular Maintenance
- Routine Inspections: Incorporate nozzle inspections and maintenance into your regular machine maintenance schedule.
- Maintenance Logs: Keep a detailed log of maintenance activities, including cleaning, inspections, and replacements, to track nozzle performance and life.
Environmental Controls
- Clean Environment: Maintain a clean work environment to reduce the risk of debris and contaminants affecting the nozzle.
- Temperature and Humidity: Ensure the operating environment is within the recommended temperature and humidity ranges to prevent nozzle and machine damage.
Operator Training
Proper Handling
- Training Program: Provide operators with a training program on the proper handling, cleaning, and maintenance of nozzles.
- Best Practices: Educate operators on best practices to avoid mishandling and ensure the longevity of the nozzles.
Safety Protocols
- Safety Gear: Ensure operators use proper safety gear, such as gloves and goggles, when handling and cleaning nozzles.
- Safety Procedures: Implement safety procedures for nozzle maintenance and replacement to prevent accidents and injuries.
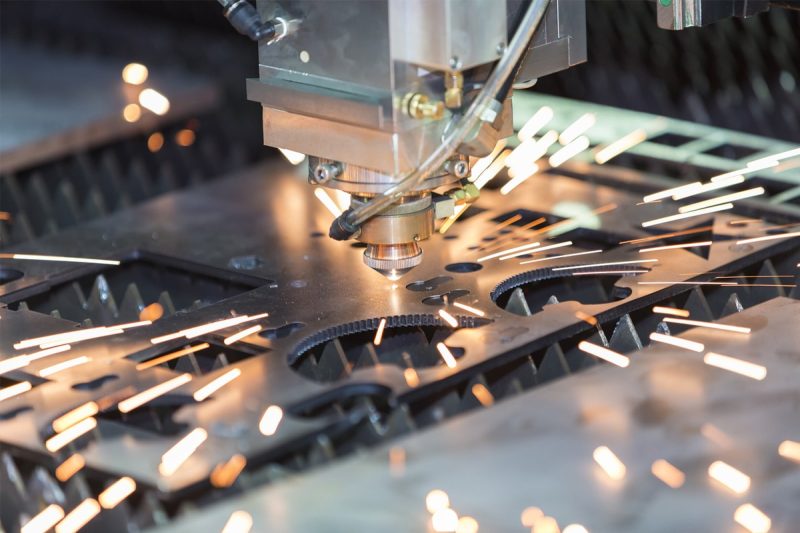
Troubleshooting Common Nozzle Problems
Poor Cut Quality
Symptoms
- Rough edges or burrs on cut material
- Incomplete or uncut portions of cut
- Excessive dross or slag on the bottom surface of the cut
Possible Causes and Solutions
- Worn or Damaged Nozzle: Inspect the nozzle for wear or damage. Replace the nozzle if it shows signs of corrosion or deformation.
- Incorrect Nozzle Size: Make sure the nozzle size matches the material type and thickness. Use a smaller nozzle for precision cuts and a larger nozzle for thicker materials.
- Misalignment: Check the alignment of the nozzle with the laser beam. Re-adjust using the manufacturer’s recommended tools and procedures.
- Assist Gas Pressure: Make sure the assist gas pressure is set correctly. Low pressure will result in poor cut quality, while high pressure will result in rough edges. Adjust the pressure according to the manufacturer’s recommendations.
Inconsistent Cutting
Symptoms
- Variation in cut quality on different parts of the material
- The cut starts good but deteriorates over time
Possible Causes and Solutions
- Nozzle Contamination: Clean the nozzle to remove any debris or buildup that may be blocking airflow or laser focus.
- Air Pressure Fluctuations: Ensure consistent assist gas pressure throughout the cut. Check the gas supply system for leaks.
- Laser Beam Instability: Check the laser generator for issues that may be causing beam instability. The laser generator may need maintenance or recalibration.
Clogged Nozzle
Symptoms
- Reduced or uneven airflow
- Increased resistance when air or gas blows through the nozzle
Possible Causes and Solutions
- Debris Buildup: Clean the nozzle using the appropriate tools and solutions to clear any blockages.
- Assist Gas Quality: Make sure the assist gas is clean and free of contaminants. Use filters to keep the gas supply clean.
- Material Coating: Be aware that some coatings on the material may cause the nozzle to clog. Adjust cutting parameters or clean the material surface before cutting.
Frequent Nozzle Wear
Symptoms
- Quick degradation or corrosion of the nozzle tip
- Frequent nozzle replacement required
Possible Causes and Solutions
- Incompatible Nozzle Materials: For high-intensity cutting operations, use nozzles made of more durable materials, such as copper.
- Cutting Too Fast: Reduce cutting speed to reduce nozzle wear.
- Incorrect Assist Gas: Make sure the assist gas type and pressure are appropriate for the material and cutting conditions.
Assist Gas Leaks
Symptoms
- Hissing sound or visible leak around the nozzle area
- Inconsistent or insufficient assist gas flow
- Decreased cutting efficiency
- Poor cut quality
Possible Causes and Solutions
- Loose Nozzle: Tighten the nozzle to ensure a secure fit. Avoid over-tightening, which can damage the nozzle or threads.
- Damaged Seals: Check seals and gaskets for damage. Replace any faulty seals to prevent leaks.
- Nozzle Cracks: Check the nozzle for cracks that could cause leaks. Replace the nozzle if necessary.
Beam Divergence
Symptoms
- Laser cut becomes wider or unfocused
- Loss of cutting accuracy
Possible Causes and Solutions
- Nozzle Misalignment: Realign the nozzle with the laser beam to ensure that the beam is properly focused.
- Nozzle Damage: Check the nozzle for any deformation or wear that could affect beam focus. Replace the nozzle if necessary.
- Lens Contamination: Check the laser lens for dirt or damage. Clean or replace the lens as needed.
- Incorrect Focus: Verify that the focus is set correctly for the material and thickness you are cutting. Adjust the focus if necessary.
Damaged Nozzle
Symptoms
- Visible cracks or deformations
- Inconsistent laser beam focus
- Frequent adjustments required
Possible Causes and Solutions
- Physical Effects: Handle the nozzle carefully to avoid physical damage. Make sure the workpiece is securely fastened to prevent collisions.
- Thermal Stress: Overheating can damage the nozzle. Ensure proper cooling and use nozzles made of quality materials such as copper or brass to withstand high temperatures.
- Improper Cleaning Tools: Avoid using abrasive tools or harsh chemicals that can damage the nozzle surface.
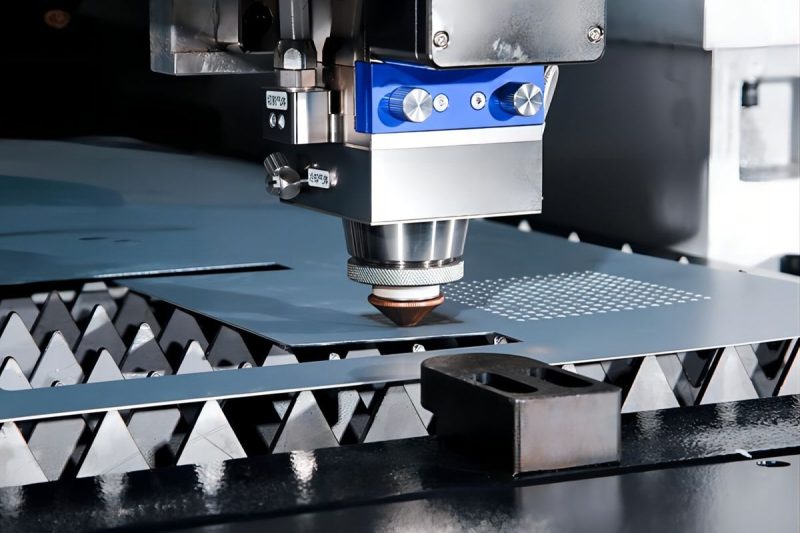
Summary
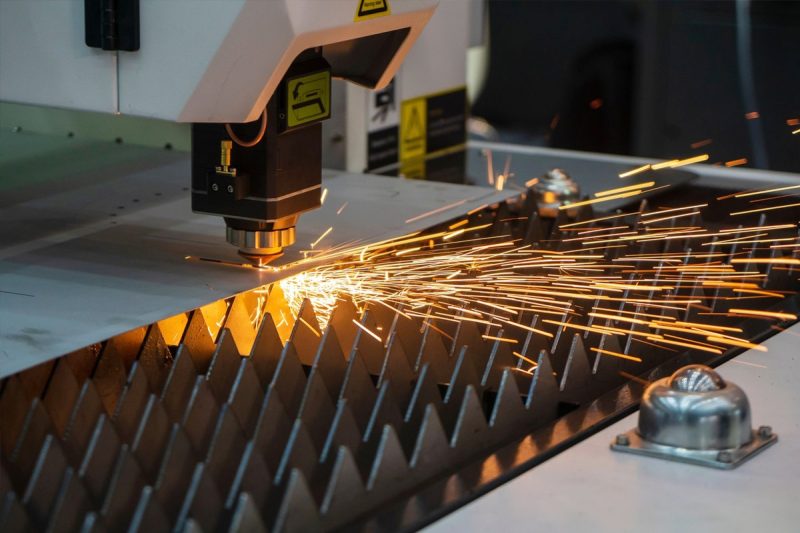
Get Laser Cutting Solutions
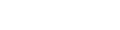
- [email protected]
- [email protected]
- +86-19963414011
- No. 3 Zone A, Lunzhen Industrial Zone,Yucheng City , Shandong Province.