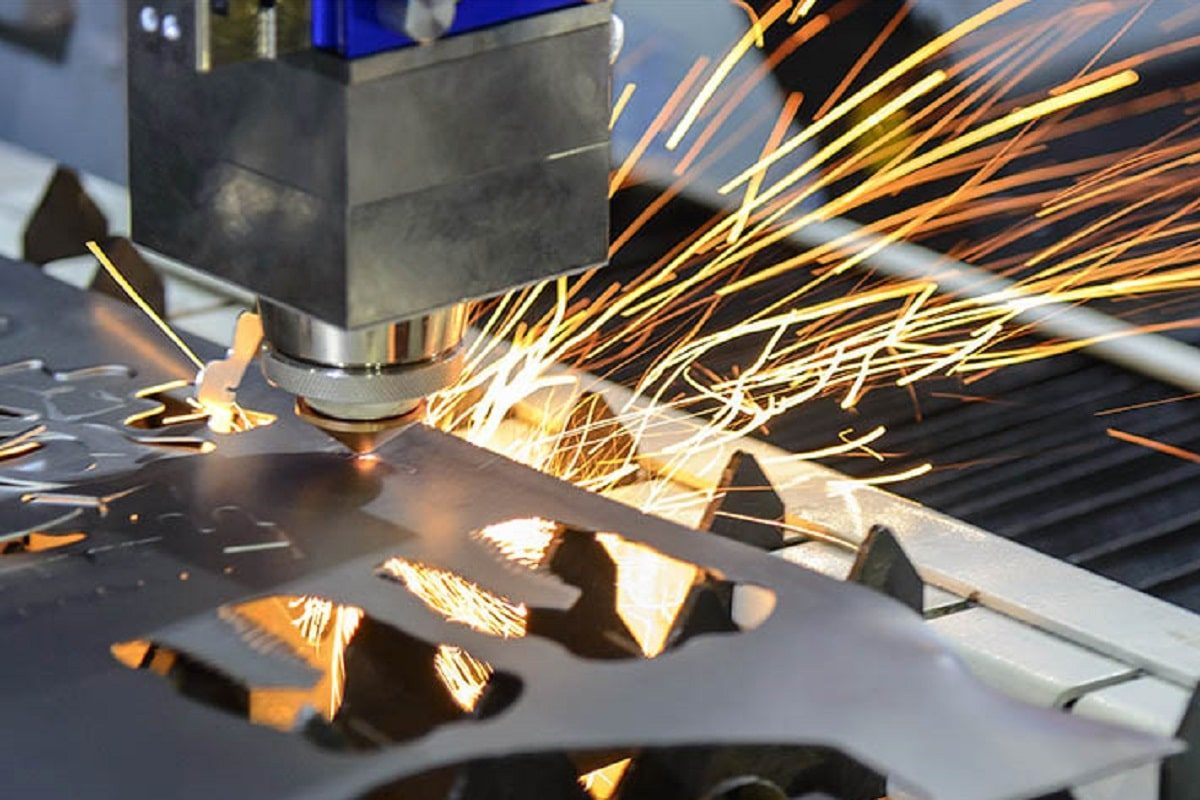
Laser Cutting Parameters: The Ultimate Guide
Laser cutting is a versatile and precise cutting process used in industries ranging from aerospace to jewelry manufacturing to cut a variety of materials with high precision. The quality and efficiency of laser cutting depend on several key factors. In order to obtain the best laser cutting results, it is intuitively important to understand and control the key parameters involved in this cutting process. In this comprehensive guide, we’ll delve into the details of these parameters to help you achieve the best cutting results in your laser cutting operation.
Table of Contents
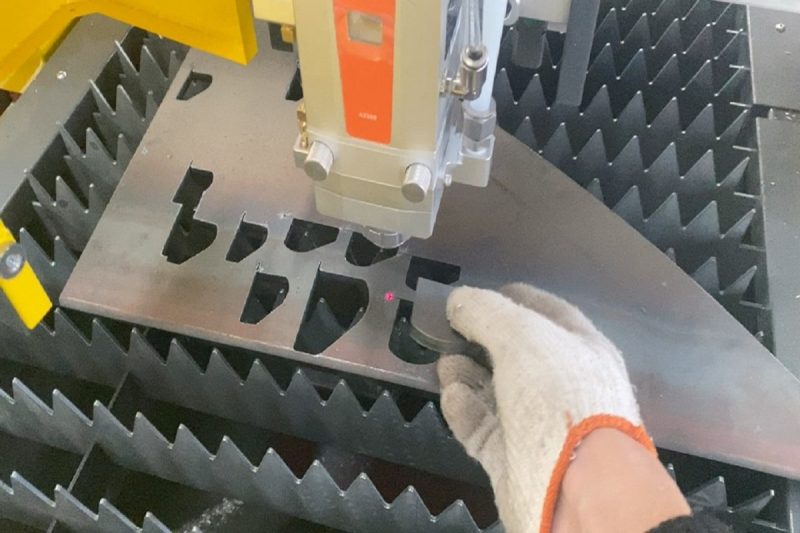
What is laser cutting?
Laser cutting is a manufacturing process that uses a highly focused laser beam to accurately and cleanly cut various materials such as metal, plastic, wood, etc. The intense heat generated by the laser beam vaporizes, melts, or burns away material along a programmed path, allowing for precise and intricate cuts without the need for physical contact with the cutting tool. Laser cutting is known for its precision, speed, and versatility in a wide range of applications.
The precision of laser cutting allows for intricate designs and fine details, making it suitable for both small-scale and mass production. It is known for its versatility, capable of cutting a variety of materials including metal, plastic, wood, and textiles. Laser cutting is favored for its minimal heat-affected zone, meaning it causes minimal distortion or damage to the surrounding material.
Whether used to manufacture precision parts, create intricate artwork, or shape materials in industrial applications, laser cutting is a key technology for achieving high-quality, customized results with exceptional precision.
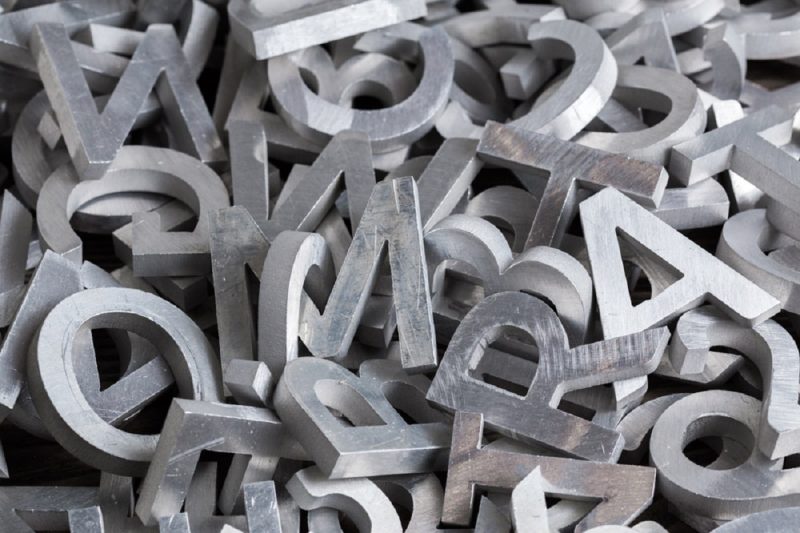
What are the most important parameters to control in laser cutting?
Laser cutting is a revolutionary cutting technology that offers unparalleled precision and versatility in material processing. To exploit the full potential of this cutting-edge technology, the key parameters that control its performance must be understood and manipulated. Let’s take a closer look at the basic parameters of laser cutting to understand their importance and how they affect the final result.
Laser power
- Meaning: Laser power is typically measured in watts (W), which determines the intensity of the laser beam and its ability to penetrate materials.
- Note: Higher laser power can cut thicker materials faster, but too high laser power can create unwanted heat-affected zones and inaccurate edges. Conversely, lower laser powers are ideal for intricate details and thinner materials. Precisely adjusting the laser power based on material thickness helps achieve optimal results.
Cutting speed
- Meaning: Cutting speed, measured in millimeters per second (mm/s) or inches per minute (in/min), determines how fast the laser head moves along the surface of the material.
- Note: Typically, slower speeds produce smoother edges and greater accuracy. Conversely, faster speeds are used for thinner materials or higher productivity. The choice of cutting speed depends on the thickness of the material and the required quality.
Focus/beam diameter
- Meaning: The focus or beam diameter refers to the width of the laser beam interacting with the material, which has a direct impact on cutting accuracy. Proper focusing ensures clean, precise cuts.
- Note: Accurate focus helps achieve consistent and high-quality cutting results. Incorrect focus can cause changes in cut quality and increase heat production. The focus should be carefully adjusted based on the material type and thickness of the machine for optimal cutting performance.
Auxiliary gas pressure and type
- Meaning: Auxiliary gases such as oxygen, nitrogen, or air play an important role in removing molten material from the cutting area and maintaining a clean cut.
- Note: Specific materials and thicknesses require precise assist gas types and pressure settings. For example, oxygen is typically used for cutting carbon steel, while nitrogen is preferred for non-ferrous metals and plastics. Choosing the right assist gas ensures efficient cutting and minimizes oxidation.
Material thickness
- Meaning: Material thickness is a key factor affecting various laser cutting parameters, including power, speed, and assist gas settings.
- Note: For accurate and optimal results, laser settings must be customized based on the thickness of the material. Manufacturer’s guidelines or making a test cut can help determine the correct cutting parameters.
Pulse frequency or continuous wave mode
- Meaning: Pulse frequency (measured in hertz (Hz)) determines the frequency of laser pulses, while continuous wave mode provides a continuous laser beam.
- Note: Higher pulse frequencies increase cutting speed and accuracy, but also generate more heat. Continuous wave mode provides a constant beam but may generate more heat. The choice of mode depends on specific cutting requirements and material properties.
Nozzle diameter and spacing distance
- Meaning: The nozzle diameter affects the focusing and interaction of the laser beam with the material, while the separation distance refers to the gap between the nozzle and the material surface.
- Note: The appropriate nozzle size needs to be selected based on the material and application. Smaller nozzles are good at fine work, while larger nozzles may result in faster cuts. Additionally, the separation distance should be adjusted to optimize cutting efficiency and quality.
Pre-processing and post-processing
- Meaning: Pre-processing involves tasks such as surface cleaning and masking, while post-processing involves activities such as deburring and cleaning, both of which are critical to successful cutting.
- Note: Cleaning the material helps achieve the best cutting results. Proper pre-treatment ensures that the material is free of contaminants before cutting. On the other hand, in order to obtain the desired final product, post-processing steps are often required, with deburring and cleaning ensuring a polished surface.

How to find the best laser-cutting parameters?
Finding the optimal laser cutting parameters requires a systematic and methodical approach as it involves optimizing various factors to achieve the desired cut quality, speed, and accuracy. Here is a detailed step-by-step guide on how to determine the best laser-cutting parameters for your specific material and application:
- Material evaluation: Start by thoroughly understanding the material you need to cut. Gather information on composition, thickness, and any unique properties such as emissivity, thermal conductivity, and hardness. Understanding the material’s properties helps select the correct laser-cutting parameters.
- Refer to the manufacturer’s guidelines: Refer to the manufacturer’s recommendations and guidelines for your laser cutter. These guidelines can often provide a starting point for setting parameters based on material type and thickness, and help ensure safety and machine compatibility.
- Set up a controlled environment: You need to create a controlled testing environment where you can safely conduct experiments, ensuring that the material is securely held and positioned correctly in the laser cutter.
- Develop a test plan: Create a structured test plan for your experiment, outlining the parameters you want to test and the range of values for each parameter you will carbonate.
- Determine critical parameters: Determine which laser cutting parameters are most critical for your specific application. The main parameters usually include laser power, cutting speed, focus/beam diameter, auxiliary gas type and pressure, and nozzle diameter.
- Laser power experiment: Begin the experiment by varying the laser power while keeping other parameters constant. Start with a range of power settings that meet the expected power requirements of the material and observe how the material reacts to different power settings, paying attention to factors such as depth of cut, heat-affected zone, and appearance of the cut edge. Look for a power setting that delivers the cut quality you want without causing excessive material damage.
- Adjust cutting speed: Once you have determined the optimal power setting, start experimenting with adjusting cutting speed while keeping laser power constant. Evaluate the effect of different cutting speeds on cut quality, paying attention to edge smoothness, accuracy, and any signs of distortion.
- Optimize focus and beam diameter: Fine-tune focus and beam diameter settings. Adjust the focus to find the sweet spot where the laser beam interacts most effectively with the material. Evaluate the effect of changes in focus and beam diameter on cut quality, specifically kerf width and heat-affected zone, to look for settings that produce clean, precise cuts.
- Explore assist gas parameters: Test different types of assist gases (e.g. oxygen, nitrogen, compressed air) and adjust their pressure settings. The choice of assist gas and its pressure can significantly affect the cutting process. Evaluate how the assist gas helps remove material and how it affects the final cut quality.
- Test pulse frequency or continuous wave mode: Test different pulse frequency or continuous wave mode settings to find a balance between cutting speed and accuracy. Consider the trade-off between faster cutting and potential heat generation, as different materials and thicknesses may require different pulse frequencies.
- Nozzle diameter and separation distance: Adjust nozzle diameter and nozzle-to-material separation distance to optimize beam focus and material interaction. Evaluate the impact of changes in these parameters on cut quality, taking into account factors such as edge smoothness and speed.
- Post-processing evaluation: After each test cut, carefully evaluate the cut quality. Check for edge smoothness, the presence of burrs, and any material distortion, take precise measurements and compare them to your required tolerances.
- Recording and analysis: Keep detailed records of each test, recording the specific parameters used, the cut quality observed, and any noteworthy observations or problems encountered. Use this data to identify trends and patterns that lead to optimal parameter combinations.
- Iterate and refine: Based on your observations and assessments, refine your parameter settings, making incremental adjustments as needed, aiming to achieve the best combination of parameters for your specific quality and efficiency requirements. In addition, continued experimentation is required to evaluate and improve the process until the cutting quality, efficiency, and precision required for the application are achieved.
- Consider safety and machine limitations: There needs to be limited consideration for safety throughout the testing process and ensuring that your laser cutter can handle the selected parameters without causing harm to the equipment or personnel.
- Seek expert advice and resources: If you encounter a challenge or have specific questions, feel free to seek advice from an experienced laser operator, engineer, or laser-cutting technology expert. Additionally, it is recommended to explore online forums, communities, and resources dedicated to laser cutting, which often provide valuable insights and solutions to common challenges.
- Validation and production: Once you have determined the optimal laser cutting parameters, verify them by performing additional test cuts to ensure consistency and reliability. Then apply the optimized parameters to your production process and regularly monitor and maintain the laser cutting machine to maintain performance.
Finding optimal laser-cutting parameters is a meticulous and iterative process that requires patience and attention to detail. By following these steps and conducting thorough experiments, you can determine the best parameters to produce precise, efficient, and high-quality laser cuts for your specific materials and applications.
Summarize
In summary, mastering laser cutting parameters helps achieve precise, high-quality cuts. Typically, experimentation and testing are required to fine-tune these parameters for specific materials and applications. When adjusting laser cutting parameters, always follow the manufacturer’s recommendations and guidelines to ensure safety and optimal results. Expertise in laser cutting requires experience, so if you’re new to the process, don’t hesitate to ask our team of experts. AccTek Laser’s expert team will recommend suitable parameter settings for you based on your requirements. Of course, we also provide a free proofing service, if you need it, you can contact us at any time.
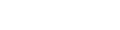
Contact information
- [email protected]
- [email protected]
- +86-19963414011
- No. 3 Zone A, Lunzhen Industrial Zone,Yucheng City , Shandong Province.
Get Laser Solutions