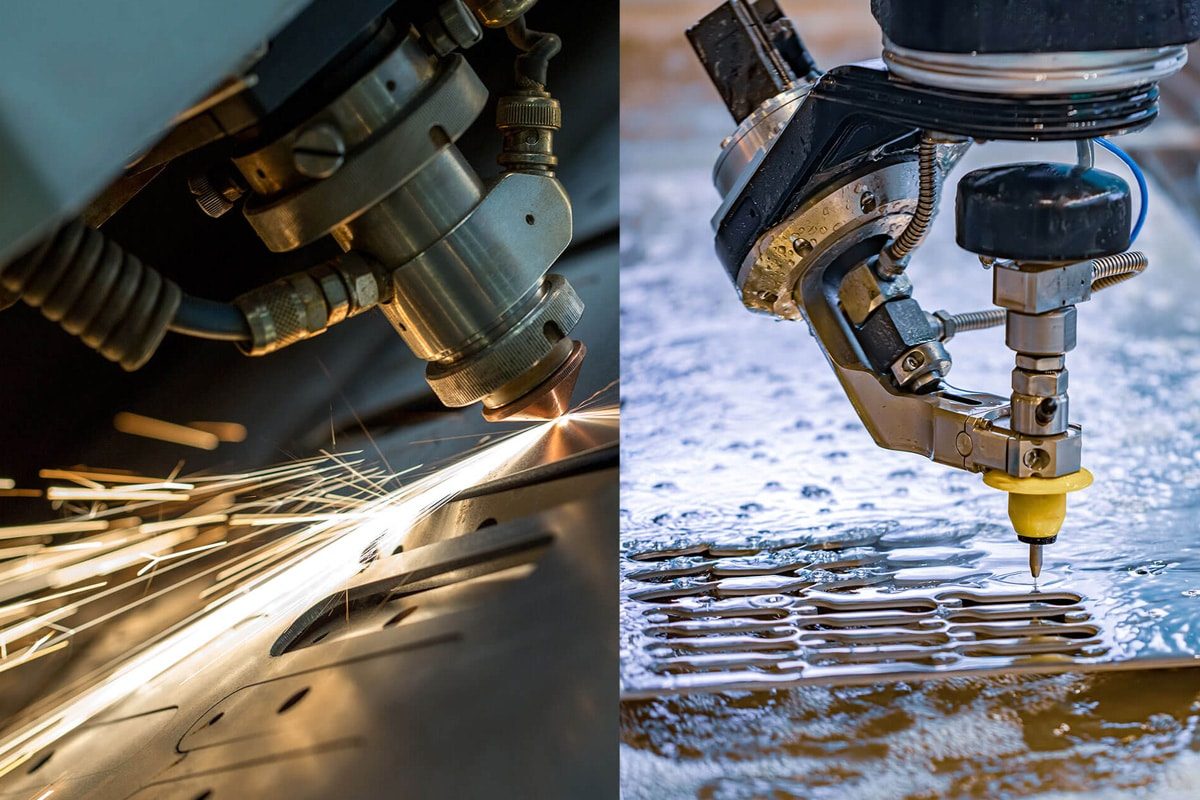
Laser Cutting VS Waterjet Cutting
In modern manufacturing and processing industries, laser cutting and waterjet cutting are two popular high-precision cutting technologies that are widely used in complex processing needs in different industries. Both technologies are the preferred solution for cutting a variety of materials due to their superior performance and versatility. Each technology has its unique characteristics, advantages, and limitations to meet the cutting needs of different materials ranging from metals and plastics to composites. Choosing the appropriate cutting method can not only improve processing efficiency but also significantly affect product quality and production costs.
This article will analyze the working principles of laser cutting and waterjet cutting in detail, and delve into their specific performance in terms of cutting accuracy, material adaptability, operating costs, environmental protection, and application scenarios. By comparing these key factors, you will have a clearer understanding of the applicable scenarios and potential value of these two technologies, helping you make more informed choices in actual production.
Table of Contents
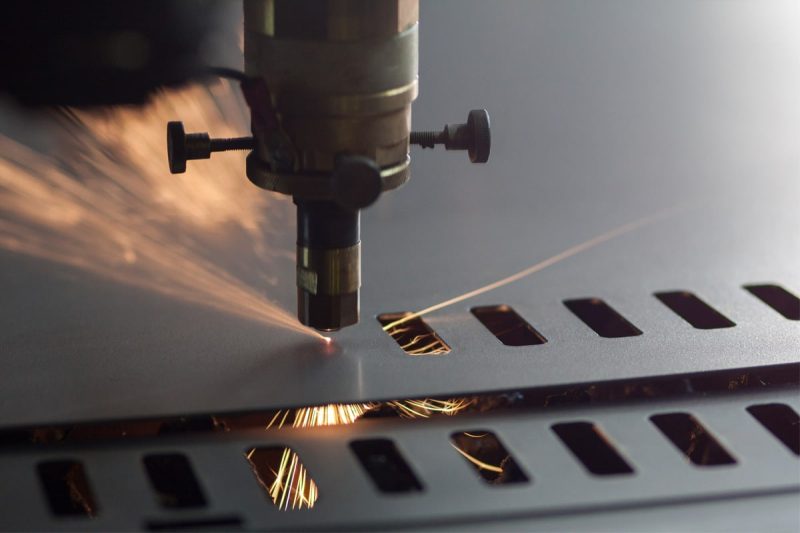
Laser Cutting Introduction
Laser cutting is the most advanced and widely used cutting process in modern manufacturing technology. It uses a high-energy-density laser beam to process materials with high precision and is known as the “invisible knife” in many industries. The following will explore its working principle, unique advantages, and limitations.
Laser Cutting Principle
Laser cutting relies on the high energy and high precision of lasers. Its basic process can be divided into the following key steps:
- Laser generation: The core of laser cutting is the laser generator, which converts electrical or chemical energy into a high-energy beam. Common types of lasers include CO2 laser generators, fiber laser generators, and solid-state laser generators, and different types are suitable for different materials and cutting needs.
- Beam transmission: The laser is transmitted to the cutting head through an optical fiber or a reflector. This transmission process requires precise calibration and high-quality optical components to ensure the concentration and stability of the beam energy.
- Focusing: After the laser is focused by the lens, the energy is highly concentrated on the surface of the material, forming a laser spot with a small diameter and high temperature. This extremely high energy density can instantly melt or vaporize the material locally, thereby achieving cutting.
- Material interaction: The focused laser beam contacts the material, causing the material to undergo a chemical reaction of melting, vaporizing, or burning rapidly when heated. This process can accurately control the cutting depth and path to ensure cutting quality.
- Auxiliary gas: Auxiliary gas (such as oxygen, nitrogen, or compressed air) is ejected through the cutting head and works in conjunction with the laser beam. On the one hand, the gas can blow away the melt to obtain a smooth cutting edge; on the other hand, the oxygen can also react with the material to further improve the cutting efficiency.
Advantages of Laser Cutting
Laser cutting is an ideal choice for a variety of industrial processing needs due to its precision and efficiency:
- Precision and accuracy: Laser cutting is famous for its ultra-high precision, which can achieve micron-level cutting tolerances and meet the strict requirements of high-precision industries such as electronic manufacturing and aerospace. Lasers excel even in cutting complex patterns or tiny parts.
- Cutting speed: Laser cutting speed is significantly faster than traditional cutting methods, especially in thin plate material processing, the efficiency is particularly outstanding. It greatly shortens the production cycle and is especially suitable for mass-production environments.
- Versatility: Laser cutting is suitable for a variety of materials, including metals (steel, stainless steel, aluminum), non-metals (plastics, wood, glass), and more. Regardless of material hardness, thickness, or shape, laser cutting can handle it with ease.
- Minimal material waste: The laser beam’s cutting slit is extremely narrow and only has a minimal impact on the material surface, ensuring minimal material waste. This not only reduces production costs but is also more environmentally friendly.
- Non-contact process: Laser cutting is a non-contact processing process. There is no direct contact between the cutting head and the material, which avoids mechanical stress and cutting surface deformation, thereby protecting the integrity of the material.
- Automation and flexibility: Laser cutting technology is compatible with CNC systems, enabling highly automated operations. Whether it is mass production or small batch customization, laser cutting can be flexibly handled and has strong adaptability.
Limitations of Laser Cutting
Although laser cutting has many advantages, it still has certain limitations in some application scenarios:
- Heat-affected zone: Laser cutting is a thermal processing process, and high temperatures may cause hardening or deformation of the edges of the material. This problem is particularly significant when cutting thin materials, but the impact of the heat-affected zone can be effectively mitigated by optimizing parameters such as laser power and cutting speed.
- Material limitations: For highly reflective materials (such as copper, and aluminum), laser cutting may suffer from reduced efficiency or unstable cutting. However, modern fiber laser generators have gradually overcome this limitation through improved wavelength and energy control technology.
- Initial cost: The purchase and installation cost of laser cutting equipment is relatively high, especially for small and medium-sized enterprises. But in the long run, this initial investment usually pays back quickly due to low operating costs and high productivity.
- Safety issues: The high energy output of lasers poses certain safety hazards, such as potential damage to the eyes and skin. However, most modern laser cutting equipment is equipped with strict safety guards to ensure operator safety.
From the above analysis, it can be seen that laser cutting has become an irreplaceable and important technology in industrial processing due to its precision, speed, and flexibility. When choosing a cutting process, laser cutting is especially suitable for scenarios that require high efficiency and precision.
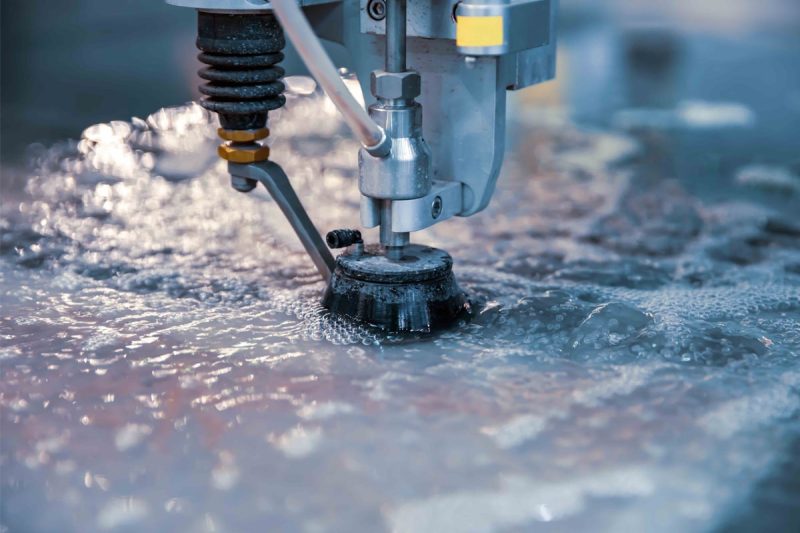
Introduction to Waterjet Cutting
Waterjet cutting is a cold-cutting process that separates materials by combining high-pressure water flow and abrasives. As an efficient and environmentally friendly processing technology, waterjet cutting is widely used in industries that require precision processing and cutting of multiple materials. The following will introduce its principles, advantages, and limitations in detail.
Water Jet Cutting Principle
- Water pressurization: The high-pressure pump is one of the core equipment of water jet cutting. It forms an ultra-high-pressure water flow by pressurizing ordinary water to 3000-4000 bar or even higher pressure. This strong pressure is the basis of the cutting process.
- Abrasive addition: During the cutting process, abrasives (such as pomegranate sand) are usually added to the water flow to enhance the cutting ability. The addition of abrasives enables water jets to cut harder materials such as metal, glass, and stone.
- Nozzle transmission: High-pressure water flow is ejected through the nozzle at a very high speed to form a high-speed cutting jet. These nozzles are made of wear-resistant materials (such as tungsten carbide or diamond) to ensure their durability and stability.
- Material interaction: High-speed water flow and abrasives jointly impact the surface of the material, and the kinetic energy of the water flow and the grinding action of the abrasives quickly remove the material to complete the cutting.
- CNC control: Water jet cutting combined with CNC system can achieve precise control of cutting path and speed, so as to adapt to complex cutting needs, such as processing of curves, special-shaped patterns, or high-precision parts.
Advantages of Waterjet Cutting
Water jet cutting performs well in many application scenarios due to its unique process characteristics:
- Cold cutting process: Unlike laser or plasma cutting, waterjet cutting does not generate high temperatures, so there is no heat-affected zone on the material. The physical properties of the material (such as hardness and toughness) will not change due to cutting, which is very suitable for processing heat-sensitive materials.
- Versatility: Waterjet cutting is suitable for almost all materials, including metals (such as steel, and aluminum), non-metals (such as glass, stone, and ceramics), composite materials (such as carbon fiber), etc. Whether it is soft or hard materials, waterjets can do it.
- Thickness capability: The thickness capability of waterjet cutting is impressive. It can cut materials over 30 cm thick, which is unmatched by other cutting processes, especially in the processing of ultra-thick materials.
- Environmental benefits: Waterjet cutting mainly uses water and natural abrasives as media, does not produce harmful gases or chemical waste, and is an environmentally friendly processing method. In addition, wastewater can be recycled after treatment, further reducing the impact on the environment.
- Edge quality: The cut surface of waterjet cutting is smooth and burr-free, and usually no additional subsequent processing is required. This improves production efficiency while reducing production costs.
- Non-contact process: Water jet cutting is a non-contact processing method that does not impose mechanical stress on the material, thus avoiding material deformation or mechanical damage and ensuring cutting accuracy and quality.
Limitations of Waterjet Cutting
Although waterjet cutting has many advantages, it still has certain limitations under certain specific conditions:
- Slower speed: The cutting speed of waterjet cutting is slower than that of laser cutting, especially when processing thin materials. This difference is particularly obvious. Therefore, waterjet cutting may not be the best choice in scenarios where high-efficiency production is required.
- Abrasive cost: The consumption of abrasives (such as garnet) is one of the larger operating costs in waterjet cutting. Especially when cutting hard materials, the use of abrasives will increase significantly, thereby increasing the total processing cost.
- Material Handling: Wastewater generated during high-pressure water cutting often contains abrasives and cutting debris and requires specialized treatment before it can be discharged or recycled. This process increases equipment and operating costs.
- Precision: Compared with laser cutting, the precision of waterjet cutting is slightly lower. Especially when processing complex patterns or tiny parts, it may be difficult to achieve the precision of laser cutting. But for most routine machining needs, the accuracy of the waterjet is still sufficient.
Waterjet cutting occupies an important position in industrial processing due to its environmental protection, cold cutting, and versatility. It is an irreplaceable technology choice, especially in scenarios where thick materials or heat-sensitive materials need to be cut. By optimizing cutting parameters and material handling methods, waterjet cutting can further improve efficiency and applicability, providing more possibilities for modern manufacturing.
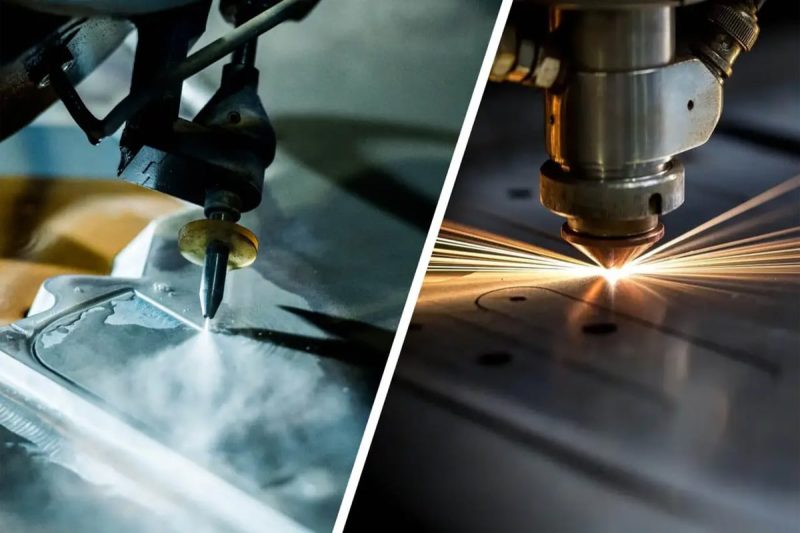
Comparative Analysis
In this section, we discuss in depth the differences between laser cutting and waterjet cutting in several key dimensions, including accuracy, cutting speed, material versatility, cost, environmental impact, and edge quality.
Precision and accuracy:
Laser cutting is known for its high precision and is particularly suitable for areas that require precision machining, such as aerospace, electronics manufacturing, and jewelry processing. Its cutting accuracy can reach the micron level, making it easy to complete complex patterns and detailed designs. This feature makes it dominant in applications requiring high accuracy and repeatability. Although waterjet cutting also has high precision, due to the physical characteristics of its cutting jet, it is slightly less effective than laser cutting when processing wonderful details and complex patterns. Therefore, laser cutting is a better choice for tasks requiring higher precision.
Cutting speed and efficiency:The speed of laser cutting has significant advantages in cutting thin and medium-thick materials. Its efficient cutting capacity can significantly improve production efficiency, especially in mass production. In comparison, waterjet cutting is slower due to its cold cutting process and the need to add abrasives, especially when cutting thinner materials. However, the cutting capabilities of water jets work well when processing extremely thick materials, but this is only suitable for certain scenarios. In most industrial applications, laser cutting is more efficient.
Material Versatility:Waterjet cutting demonstrates strong advantages in material adaptability, cutting almost all types of materials, including highly reflective metals, glass, ceramics, and composites. This makes it a very versatile cutting tool. However, laser cutting also performs well in material diversity, being able to easily cut metals (such as steel, stainless steel, and aluminum) and non-metals (such as plastics, wood, and textiles). Although laser cutting requires additional adjustments when processing highly reflective materials (such as copper and aluminum), the development of modern laser technology (such as fiber laser generators) has greatly improved its cutting efficiency and quality on these materials. Overall, laser cutting is a more efficient and economical choice for most metal and common material processing needs.
cost:The initial investment in laser cutting equipment is higher, especially high-power industrial-grade laser generators, but due to its rapid processing capabilities and lower operating costs (such as energy consumption and maintenance expenses), it is more economical in long-term use. In addition, laser cutting has a high degree of automation and its high compatibility with CNC systems can further reduce labor costs. In comparison, the initial investment in waterjet cutting equipment is slightly lower, but the cost of abrasives is higher. Especially in large-scale production, the continuous consumption of abrasives will significantly increase operating expenses. Therefore, on the whole, laser cutting is more suitable for enterprises that require long-term and large-volume production.
Environmental impact: Although laser cutting generates a certain amount of heat and may require additional exhaust treatment equipment, modern industrial equipment is usually equipped with a complete filtration system to minimize thermal effects and harmful gas emissions. In contrast, water jet cutting, as a cold-cutting process, does not generate any heat and has no effect on the physical properties of the material, so it has more advantages in terms of environmental performance. However, the wastewater and abrasive residues generated during water jet cutting require special treatment, otherwise they may cause environmental pollution. This makes laser cutting more prominent in modern industrial green manufacturing, especially in industries that focus on environmental protection and clean production.
Edge quality: Both laser cutting and water jet cutting are excellent in cutting edge quality, but laser cutting can achieve very smooth edges due to its extremely fine beam focus and highly controllable cutting trajectory, which is suitable for precision components and processing requirements that require high aesthetics. Water jet cutting has no heat-affected zone, so the cutting edge is relatively smooth and does not require additional processing. However, under the dual requirements of high speed and high precision, laser cutting performs better, especially in the processing of medium-thin materials and high-precision parts.
Thermal effect:Due to the high temperature generated during laser cutting, a heat-affected zone (HAZ) may be formed at the cutting edge, which may cause hardening or deformation of the material edge. Modern laser equipment can significantly reduce this effect by optimizing cutting parameters (such as power, speed, and gas flow) so that thermal effects have almost no impact on the processing of most materials. Waterjet cutting has no thermal effects at all, which makes it even more advantageous when processing heat-sensitive materials such as glass, ceramics, or composites. However, for most metal materials and industrial applications, the efficiency and precision of laser cutting are more suitable.
Environmental and safety considerations:Laser cutting requires special attention to the safety of laser radiation, but modern laser equipment is usually equipped with comprehensive safety protection measures (such as protective covers and radiation shielding) to ensure the safety of operation. On the other hand, water jet cutting requires proper treatment of wastewater and abrasive residues, otherwise it may cause environmental pollution. With the increasing focus on environmental protection in modern manufacturing, this feature may limit the application of water jet technology.
Through a comprehensive comparison of laser cutting and water jet cutting, it can be seen that laser cutting has obvious advantages in terms of precision, cutting speed, and efficiency, and is especially suitable for high-precision requirements and mass production scenarios. Although water jet cutting has unique advantages in processing complex materials and avoiding thermal effects, laser cutting is widely used in modern manufacturing due to its fast, efficiency, and cost-effectiveness. The selection of appropriate cutting technology should be based on specific application requirements and material properties. Laser cutting is undoubtedly the preferred solution for many industries pursuing precision and efficiency.
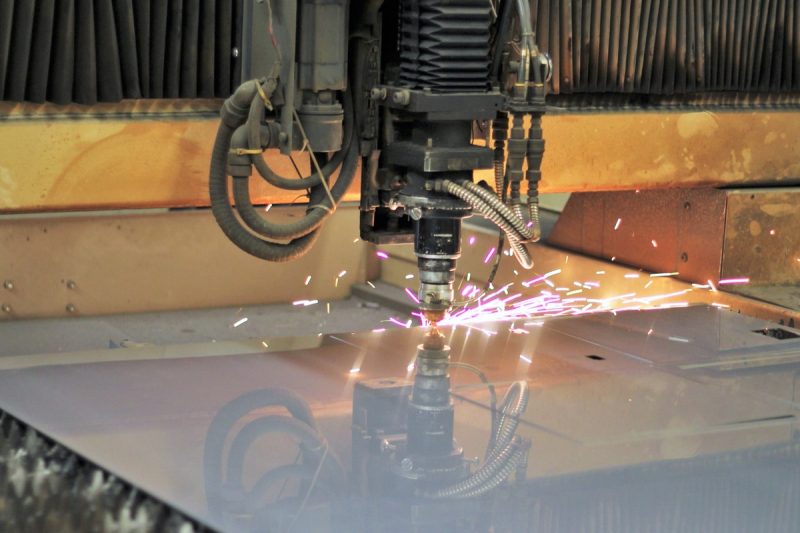
Summarize
Laser cutting and water jet cutting each have their unique advantages and limitations and are suitable for different industrial needs. When choosing a cutting technology, it is important to make a judgment based on the specific processing requirements. If you are looking for high precision and high cutting speed, especially when cutting thin materials, laser cutting is undoubtedly the most efficient choice. Laser cutting not only provides extreme precision but also improves production efficiency and reduces material waste.
On the other hand, if your needs involve cutting thicker materials, or needing to avoid heat effects to protect the physical properties of the material, water jet cutting is a more suitable solution. Water jet cutting is suitable for a wider range of materials, and due to its cold cutting characteristics, it can avoid damage to heat-sensitive materials.
AccTek Laser is committed to providing customers with advanced and cost-effective laser cutting equipment, with excellent performance and reliability to meet the production needs of various industries. By choosing laser cutting, you can not only improve production efficiency but also achieve more refined processing results. For more information and professional advice on equipment, please feel free to contact us, we will provide you with a tailor-made solution!
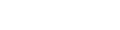
Contact information
- [email protected]
- [email protected]
- +86-19963414011
- No. 3 Zone A, Lunzhen Industrial Zone,Yucheng City , Shandong Province.
Get Laser Solutions