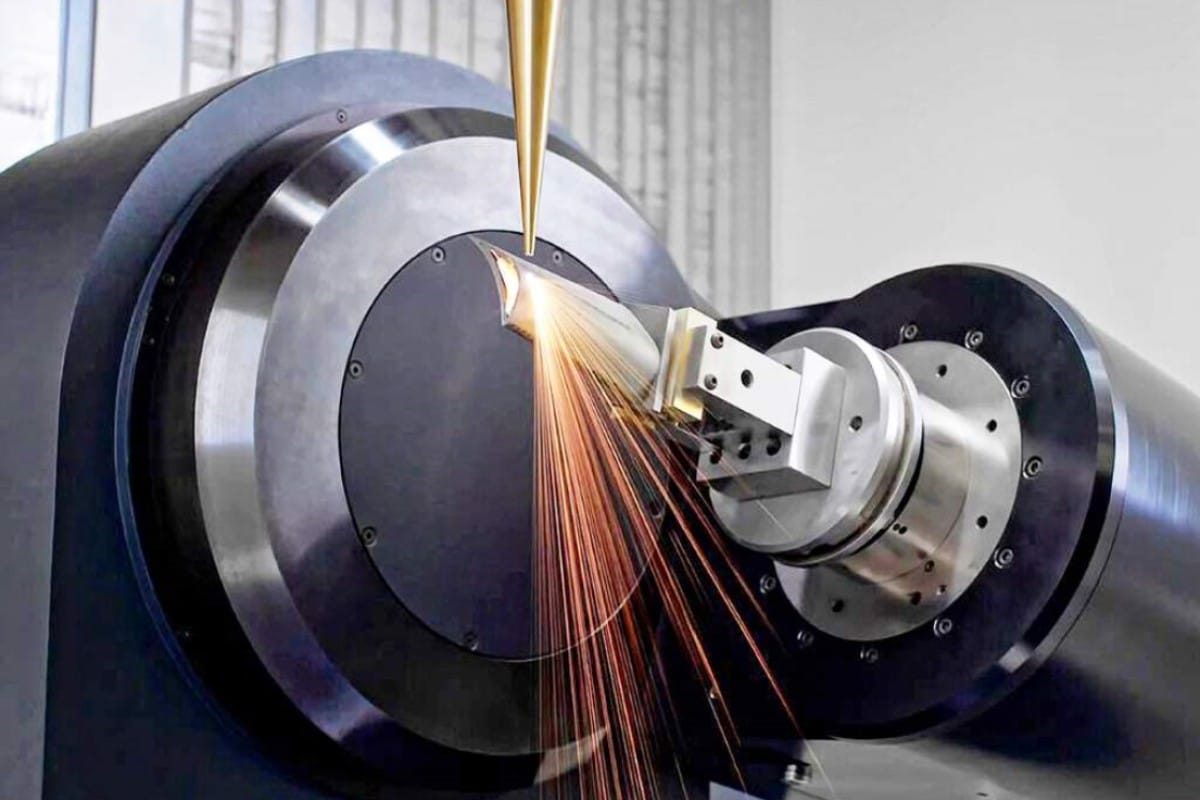
Laser Drilling Comprehensive Guide
In precision engineering and manufacturing, the pursuit of perfection and accuracy is endless. Laser drilling is a cutting-edge technology that enables precision drilling in a variety of materials. In this comprehensive guide, we’ll explore what laser drilling is, how it works, the difference between laser cutting and laser drilling, its advantages and disadvantages, and its wide range of applications.
Table of Contents
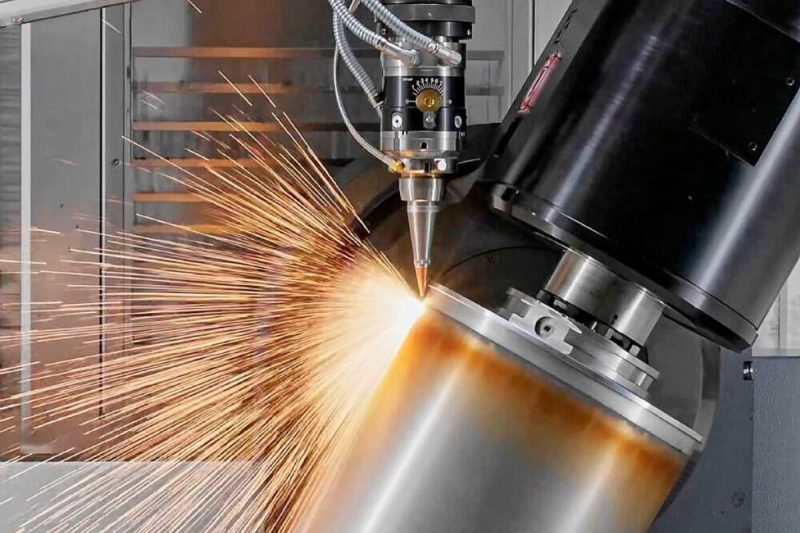
What is laser drilling?
Laser drilling is a highly precise, controlled material removal process that uses the energy of a focused laser beam to create holes, perforations, or openings in a variety of materials. The technology has gained prominence in industries that require exceptional precision and complex hole patterns. Unlike traditional drilling methods that use mechanical tools to remove material, laser drilling relies on heat energy generated by the laser to vaporize, melt, or ablate material, effectively creating holes with minimal heat-affected zones and precisely sized holes.
Laser drilling is known for its precision, versatility, and ability to create holes of varying sizes and shapes, making it a valuable tool in industries such as aerospace, electronics, medical devices, and micromachining. It is typically used when traditional drilling methods may not be suitable because ultra-precision holes are required or when drilling materials that are difficult to machine using traditional methods.
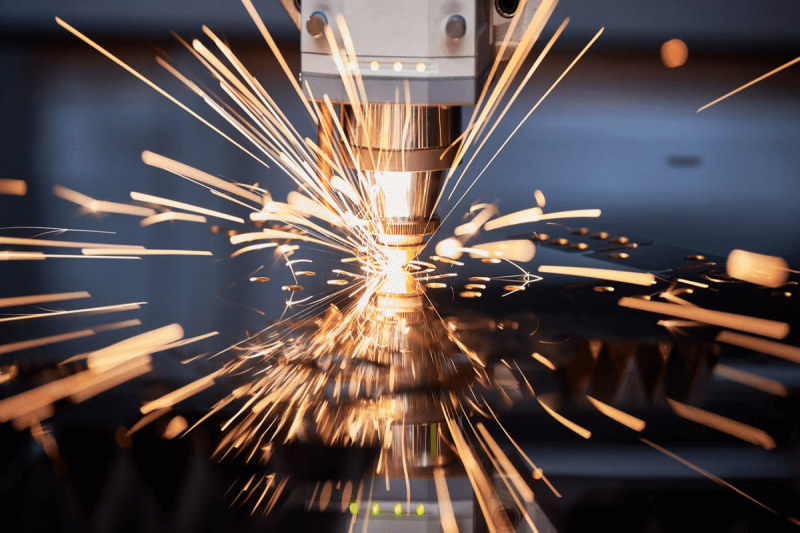
Laser Drilling For The Working Principle
The laser drilling process relies on the principle of a focused laser, which is a highly concentrated laser beam that vaporizes or melts materials on contact. Here’s a step-by-step explanation of how laser drilling works:
- Laser source selection: The process begins with selecting an appropriate laser source based on the material to be drilled and the desired hole characteristics. Common types of laser generators used in laser drilling include carbon dioxide (CO2) lasers, fiber lasers, and solid-state lasers. The choice of laser type depends on factors such as material type, thickness, and required accuracy.
- Focusing optics: The laser beam produced by a laser generator is usually a divergent beam or a broad beam. To make it suitable for drilling, the beam passes through a series of focusing optics. These optics include lenses and mirrors that precisely focus the laser beam into a highly focused, intense spot. The accuracy of the focusing optics is critical to achieving precision in the drilling process.
- Material interaction: A highly focused laser beam is directed onto the surface of the material to be drilled. When a laser beam contacts a material, several possible interactions may occur, depending on the material type and laser parameters:
- Absorption: Depending on the characteristics of the material, laser energy is absorbed, causing rapid heating. In some cases, material may evaporate, melt, or be removed by ablation (the process of removing material by evaporation).
- Melting and vaporization: For some materials, laser energy can cause localized melting and then vaporization. The rapid expansion of steam creates a hole in the material.
- Ablative: In other cases, laser energy directly removes material through ablation without melting. This is common in materials such as plastics and ceramics.
- Computer numerical control (CNC): The entire laser drilling process is carefully controlled by computer software, often combined with CNC. The software takes a digital design or CAD (computer-aided design) model of the desired hole pattern and converts it into specific instructions for the laser drill machine. These instructions include parameters such as hole size, location, shape, and drilling speed.
- Real-time adjustment: Throughout the drilling process, the CNC system continuously monitors and adjusts various parameters to maintain consistent hole quality and size. This includes controlling the power of the laser, adjusting the beam focus, and adjusting the drilling speed. Real-time adjustments help ensure that desired hole characteristics are achieved without damaging surrounding materials.
- Gas assist: In some laser drilling processes, gases such as oxygen or nitrogen are used as assist gases. This gas can help clear molten material and debris from the hole, improving drilling efficiency and preventing burrs or irregularities from forming around the edges of the hole.
Laser drilling is favored for its precision and versatility. It can create holes of varying sizes and shapes, making it a valuable tool in industries such as aerospace, electronics, medical devices, and micromachining. Laser drilling is often chosen when traditional drilling methods are not suitable due to the need for ultra-precision holes, drilling difficult-to-machine materials, or a desire to minimize material waste. However, since the process involves high-powered lasers, it does require careful controls and safety measures.
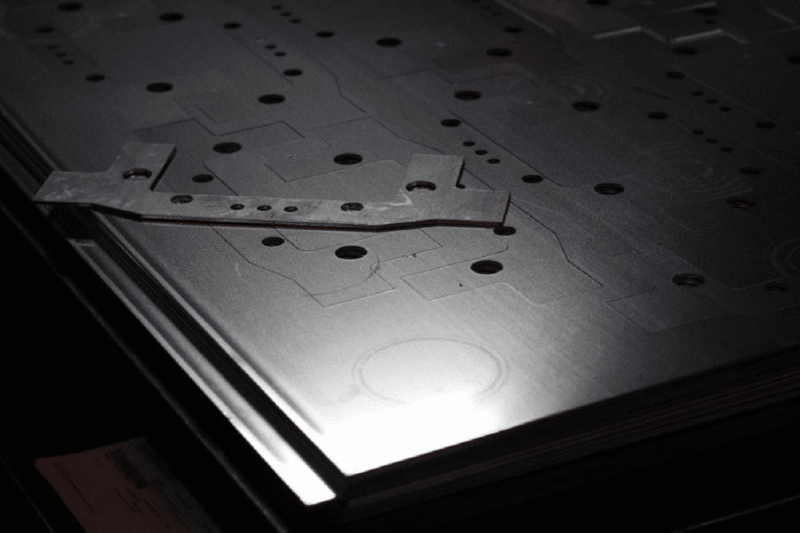
The difference between laser cutting and laser drilling
Laser cutting and laser drilling are two different laser processing processes that serve different purposes and have different operating principles and applications. Here’s a breakdown of the main differences between laser cutting and laser drilling:
Purpose
- Laser cutting: Laser cutting is primarily used to cut materials along a defined path, shape, or contour. It is used to separate materials into specific parts, create intricate designs, or achieve clean and precise cuts.
- Laser drilling: Laser drilling is specifically designed to create holes, apertures, or perforations in materials. It focuses on creating openings in the surface of the material without having to separate it into different parts. Laser drilling excels at producing precise holes of different shapes and sizes.
Material removal
- Laser cutting: Laser cutting removes material along a path, effectively dividing it into two distinct parts. It can cut the entire thickness of the material to form two separate parts.
- Laser drilling: Laser drilling only removes material where the hole is to be created. Rather than splitting the material into two parts, it creates holes or perforations in the material while leaving the surrounding material intact.
Cutting and drilling
- Laser cutting: Laser cutting is often used to cut complex shapes, patterns, or parts from flat materials. It’s ideal for cutting industrial components in materials such as sheet metal, acrylic, and wood, creating complex designs, and producing precision gaskets and seals, among other applications.
- Laser drilling: Laser drilling is specifically used to create holes in materials. It is commonly used where precise holes are required, such as cooling holes in turbine blades in aerospace, micro holes in printed circuit boards in electronics, and in medical equipment to make tiny holes in surgical instruments.
Holes and cuts
- Laser cutting: The result of laser cutting is usually a cut or separation along a path. The cut edges may have a characteristic laser-cut appearance, with the material separated into individual pieces.
- Laser drilling: Laser drilling creates holes or perforations in the material. These holes are typically characterized by precise dimensions and a rounded or shaped profile, with the surrounding material remaining intact.
Laser parameters
- Laser cutting: Laser cutting machines are optimized for cutting, focusing on factors such as cutting speed, power, and beam focus. The device is designed to move a laser beam along a predetermined cutting path.
- Laser drilling: Laser drilling machines are specifically used to drill holes, focusing on parameters such as hole size, shape, depth, and location. This equipment is usually equipped with precision drilling capabilities.
Laser cutting and laser drilling are both valuable laser-based processing technologies, but their primary purposes and results are different. Laser cutting involves cutting material along a defined path, and breaking it into pieces, while laser drilling focuses on making holes or openings within materials without separating them. The choice between laser cutting and laser drilling depends on the specific application and desired results.
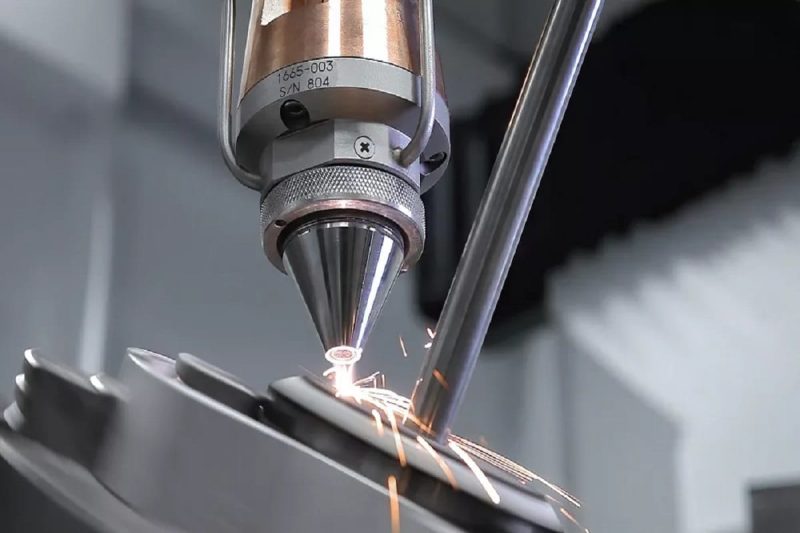
Advantages and disadvantages of laser drilling
Laser drilling is a precise and versatile processing technology with many advantages, but it also has certain limitations and disadvantages. When considering laser drilling for a specific application, it is important to understand these advantages and disadvantages. Here are the pros and cons of laser drilling:
Advantages of laser drilling
- Precision and Accuracy: Laser drilling is known for its ability to drill holes with exceptional precision and accuracy. It can process holes with diameters ranging from microns to millimeters, making it suitable for a variety of applications requiring high precision.
- Versatility: Laser drilling can be used on a variety of materials, including metals, plastics, ceramics, composites, and even some organic materials. This versatility makes it suitable for a variety of industries and materials.
- Speed and efficiency: Laser drilling is a relatively fast process that reduces production time and costs compared to traditional drilling methods. The non-contact nature of laser drilling also contributes to efficiency.
- Minimal heat-affected zone: Laser drilling generates very little heat, leaving only a small heat-affected zone (HAZ) around the hole. This is especially important when working with heat-sensitive materials or when maintaining the structural integrity of the material is critical.
- Minimal material waste: Laser drilling produces minimal waste as it removes material precisely from the desired location, which results in cost savings and environmental benefits.
- Complex geometries: Laser drilling can process holes with complex shapes, contours, and non-standard geometries, allowing for greater design flexibility and the ability to meet specific requirements. This may be challenging or impossible to achieve with traditional drilling methods.
- Non-contact process: Since laser drilling is a non-contact process, there is no tool wear or physical contact with the workpiece. This reduces wear and tear on the equipment, thereby extending the life of the tool.
Disadvantages of laser drilling
- Initial investment: The equipment and technology required for laser drilling can be expensive to purchase and install. For some businesses, this initial investment can be a barrier.
- Material limitations: While laser drilling can be used on a variety of materials, highly reflective or absorptive materials can be challenging due to the interaction of the laser with the material surface. In this case, special measures or a different laser type may be required.
- Safety issues: Laser drilling involves the use of high-powered lasers, which can be dangerous to the operator if proper safety precautions are not taken. Operators must follow strict safety protocols to prevent exposure to laser radiation.
- Heat: The laser drilling process generates heat, causing a heat-affected zone (HAZ) around the hole. This can be a disadvantage in some applications, especially when precise temperature control is required.
- Limited hole depth: Laser drilling is generally suitable for producing relatively shallow holes. The depth of the hole is limited by factors such as material thickness, laser power, and drilling speed. Extremely deep holes may require specialized equipment or alternative drilling methods.
- Cost considerations: While laser drilling is very effective for certain applications, it may not always be the most cost-effective compared to other drilling methods. For small-scale or low-volume production, it may not always be the most economical option.
- Complex setup and programming: Laser drilling requires precise programming and setup to ensure the desired hole characteristics, especially when creating holes with specific shapes and orientations. This complexity may require skilled operators and careful planning.
- Environmental considerations: Laser drilling produces fumes, debris, and waste materials that require proper handling and disposal and may increase environmental concerns and costs.
Laser drilling is a valuable machining process known for its precision, versatility, and minimal thermal impact. However, before choosing laser drilling as your preferred method, you must consider the specific requirements of your application, the material being drilled, and the associated costs and safety measures. When used correctly, laser drilling can provide superior advantages in hole quality and accuracy.
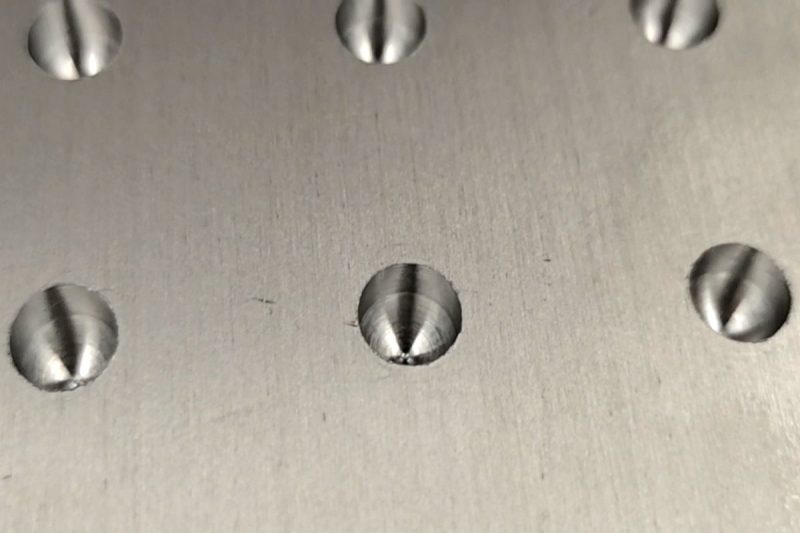
Laser drilling applications
Laser drilling is a versatile and precise machining process with a wide range of applications in various industries. Its ability to create holes as small as micron-sized with extremely high precision and minimal heat-affected zone makes it a valuable tool in many fields. Here are some common uses for laser drilling:
- Microelectronics and semiconductor industry: Laser drilling is critical for manufacturing integrated circuits (ICs), printed circuit boards (PCBs), and semiconductor devices. It is used to create micro vias, vias, and other tiny openings in silicon wafers, PCBs, and semiconductor materials.
- Aerospace and gas turbine: In the aerospace industry, laser drilling is used to create cooling holes and micro-perforations in turbine blades and engine components. These holes help dissipate heat and increase the efficiency and longevity of the jet engine.
- Medical devices: Laser drilling is used in the manufacture of medical devices, such as surgical instruments and implants. It is used to create precise holes in components such as orthopedic implants, dental implants, and surgical tools.
- Microfluidics: Microfluidic devices require precise channels and holes for fluid control and analysis. Laser drilling helps create these complex microchannels, ensuring accurate and efficient fluid manipulation.
- Automotive industry: Laser drilling is used in the automotive industry for applications such as fuel injectors, exhaust systems, and precision engine components. It creates precisely positioned small holes.
- Jewelry and watchmaking: Laser drilling is used to create intricate designs and patterns on precious metals and gemstones, such as diamonds. It is used to remove inclusions and enhance the appearance of the stone.
- Textile industry: Laser drilling is used to perforate fabrics and textiles to create patterns and designs for decorative purposes or to increase the breathability of clothing.
- Oil and gas industry: Laser drilling is used to create precise holes in oil and gas drilling equipment and components. It helps control fluid flow and improve drilling efficiency.
- Micromachining and MEMS (microelectromechanical systems): Laser drilling is essential for the production of micromachines and electronic devices. It is used to create holes in microfluidic chips, MEMS sensors, and microelectronic devices.
- Electronic packaging: Laser drilling is used in electronic packaging to create openings for interconnects and thermal management in advanced electronic devices.
- Optics and photonics: Laser drilling is used in the fabrication of optical components, including lenses, waveguides, and optical fibers, where precise hole location and size are critical.
- Custom manufacturing: Laser drilling provides the flexibility to create custom holes and openings for specific applications such as filtration systems, gaskets, and precision instrumentation.
- Art and design: Artists and designers use laser drilling to create intricate patterns and designs on a variety of materials, including wood, acrylic, and metal, for artistic and decorative purposes.
The widespread use of laser drilling highlights its importance in modern manufacturing and research, where precision and accuracy are critical. Its applications continue to expand as technology advances and industry demands smaller, more complex functions.
Summarize
Laser drilling is a superior machining process that embodies precision and versatility. Its ability to create tiny, complex holes with unparalleled precision has revolutionized industries from aerospace to microelectronics. As technology advances, laser drilling is expected to continue to push the boundaries of precision engineering, bringing new possibilities and applications to the world of manufacturing and design.
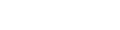
Contact information
- [email protected]
- [email protected]
- +86-19963414011
- No. 3 Zone A, Lunzhen Industrial Zone,Yucheng City , Shandong Province.
Get Laser Solutions