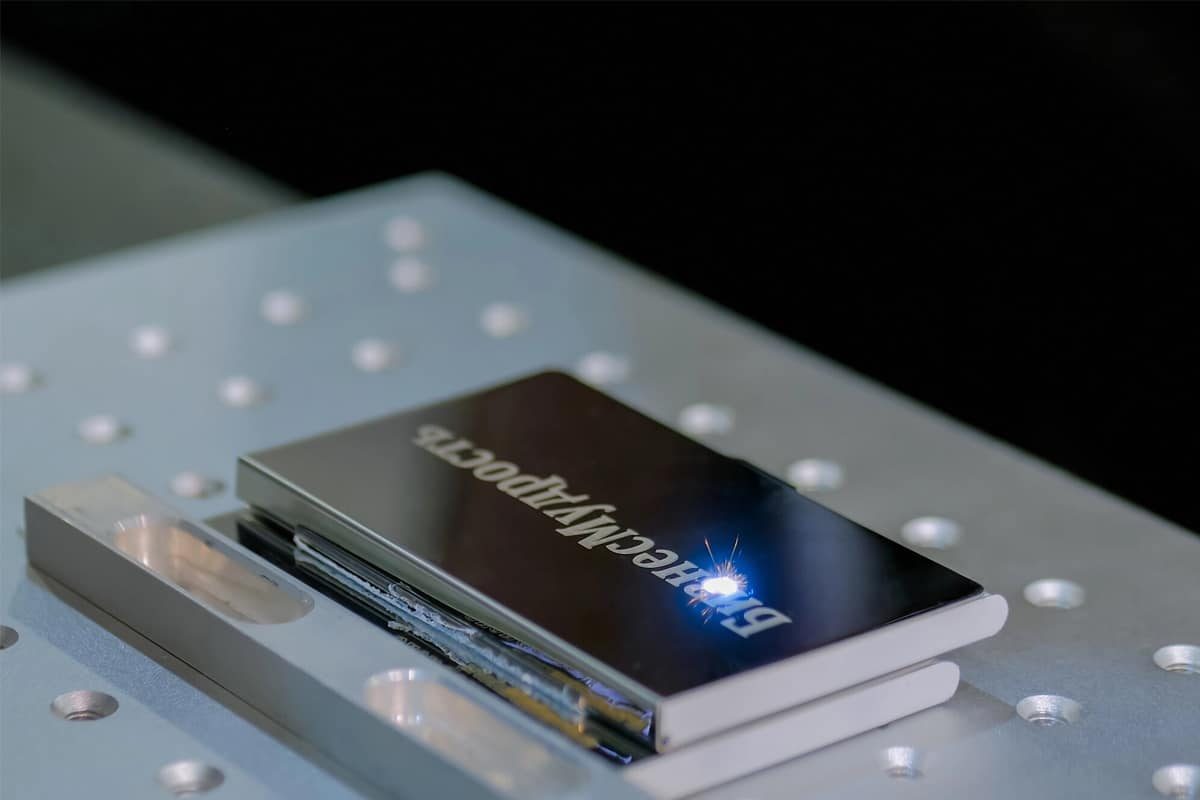
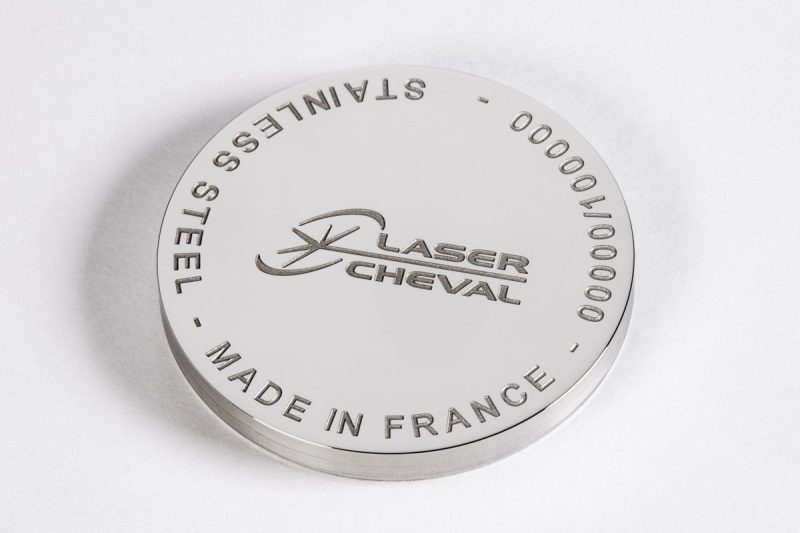
Introduction to Laser Technology
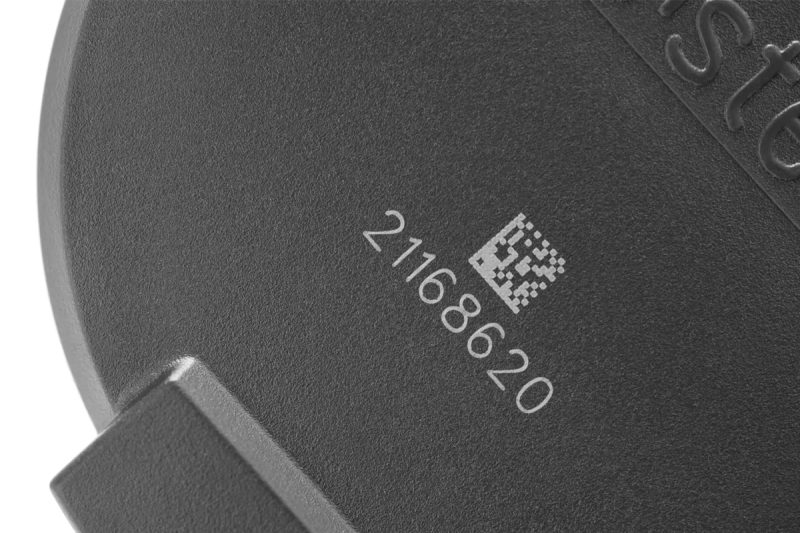
Understanding the Laser Marking Machine
Definition of Laser Marking
Working Principle of Laser Marking
Types of Laser Marking Methods
Several laser marking methods exist, each suited to specific materials and applications.
- Annealing Marking: This method is primarily used on metals such as stainless steel, titanium, and chrome. The laser heats the surface of the metal, causing an oxidized layer to form. The result is a color change that ranges from black to various shades of blue, yellow, or green, depending on the metal and temperature used. Annealing is non-invasive, meaning no material is removed, making it ideal for applications where maintaining the surface’s smoothness is essential, such as in medical devices and high-end watches.
- Color Change Marking: This method is commonly used on plastics. The laser alters the chemical properties of the plastic’s surface, resulting in a visible color change. The process does not affect the surface’s texture, making it suitable for sensitive applications where the material’s physical properties cannot be compromised. Color change marking is often used in the automotive and electronics industries, where components are marked with part numbers, logos, or safety information.
- Foaming: Used primarily for marking plastics and some metals, foaming creates raised marks by melting the surface material and trapping gas bubbles beneath. These bubbles give the marked area a lighter, more opaque appearance. Foaming is particularly effective on dark-colored materials, as it creates high-contrast marks that are easily readable. This method is often employed in industries where product traceability is critical, such as in packaging, electronics, and consumer goods.
- Carbon Migration: This method is specific to metals like steel or carbide alloys. The laser brings carbon to the material’s surface, creating dark marks that contrast with the base metal. These marks are exceptionally durable and resistant to wear, making carbon migration an ideal choice for marking tools, industrial parts, or automotive components that are exposed to harsh environments.
Common Materials for Laser Marking
Laser marking machines are highly versatile and can mark a wide range of materials.
- Metals: Stainless steel, aluminum, brass, copper, titanium, and carbide alloys are frequently marked in industries like aerospace, automotive, and medical manufacturing. These materials are typically used for high-durability applications, making laser marking an ideal solution for permanent identification.
- Plastics: ABS, polycarbonate, polypropylene, and acrylic are widely used in industries such as electronics, automotive, and consumer goods. Laser marking on plastics is often used for branding, part identification, or safety warnings.
- Ceramics: Ceramic materials are common in medical and electronic devices, where laser marking is used for traceability and compliance with industry regulations.
- Glass: Glass is often marked in the packaging, beverage, and luxury goods industries. The laser can create precise, non-invasive marks without causing micro-cracks or compromising the glass’s integrity.
- Organic Materials: Wood, leather, and paper are also marked using lasers, often in luxury goods or promotional products industries, where logos, serial numbers, or decorative designs are needed.
Applications of Laser Marking
Laser marking machines are used across various industries for diverse applications.
- Medical Devices: Laser marking is essential for adding serial numbers, regulatory marks, and batch codes on surgical instruments and medical implants. These marks ensure traceability and compliance with strict healthcare regulations.
- Automotive Industry: Car parts, such as engine components, brake systems, and exhaust parts, are often marked with QR codes, barcodes, and serial numbers to ensure quality control and traceability throughout the manufacturing and supply chain processes.
- Electronics: Printed circuit boards (PCBs), semiconductor components, and electronic enclosures are frequently marked with identification numbers and logos. Laser marking ensures that even the smallest, most delicate components are marked without affecting their function.
- Jewelry: Laser marking allows intricate details, logos, and personalized inscriptions to be added to jewelry pieces. The precision and permanence of laser marking make it ideal for the luxury market, where branding and customization are essential.
- Aerospace: In the aerospace sector, parts are marked with essential information, including part numbers, safety certifications, and batch numbers. These marks must withstand extreme conditions such as high temperatures, pressure changes, and exposure to chemicals.
Advantages of Laser Marking
Laser marking offers several key advantages over traditional marking methods:
- Permanent and Durable Marks: Laser marking produces marks that are resistant to wear, heat, and chemicals. This durability makes it ideal for long-term applications in harsh environments, such as automotive engines or medical implants.
- Non-Contact Process: Because laser marking is a non-contact process, there is no need for physical tools to touch the material being marked. This reduces wear and tear on both the marking machine and the material itself, prolonging the equipment’s lifespan and maintaining the material’s integrity.
- High Precision and Detail: Laser marking can create extremely precise and intricate marks, even on small or complex components. This precision makes it suitable for detailed designs, logos, and fine text on products.
- Versatility: Laser marking machines can work with a wide range of materials, from metals and plastics to ceramics and glass. This versatility makes them adaptable to numerous industries and applications.
- Eco-Friendly: Laser marking does not require inks, chemicals, or additional consumables, making it an environmentally friendly option. It reduces waste and eliminates the need for hazardous materials used in other marking processes.
- Cost-Effective: Although the initial investment in a laser marking machine can be higher than other marking methods, the long-term cost benefits are significant. The non-contact process minimizes maintenance costs and the speed and efficiency of laser marking lead to higher production rates.
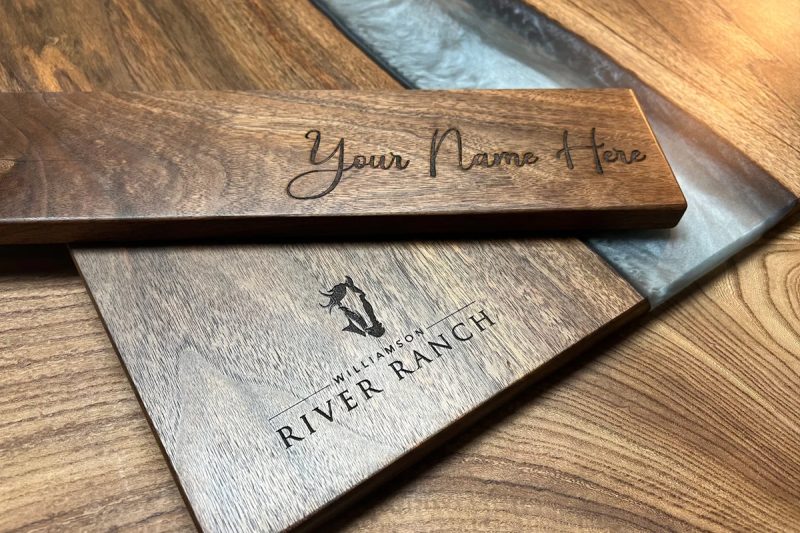
Understanding the Laser Engraving Machine
Definition of Laser Engraving
Working Principle of Laser Engraving
Types of Laser Engraving Methods
Laser engraving includes several specialized methods tailored to different materials and applications:
- Etching: This is a shallow engraving process, where the laser removes a minimal layer of material, resulting in fine, precise lines. It is ideal for detailed designs on metals, plastics, and glass, commonly used for engraving text, logos, and graphics. Etching is also faster than deeper engraving methods, making it suitable for high-volume applications.
- Deep Engraving: In this method, the laser removes more material to create a pronounced cavity. Deep engraving is often used on metals and is suitable for applications that require durability, such as molds, stamps, and parts exposed to friction or impact. Deep engravings are typically used in industrial applications where markings must remain legible over time.
- 3D Engraving: This advanced method involves varying the laser’s intensity and focus to create multi-dimensional effects. By adjusting the laser’s depth in different areas, 3D engraving can create images with realistic depth and texture. This technique is popular in jewelry, artistic applications, and luxury products for adding unique aesthetic effects.
Common Materials for Laser Engraving
Laser engraving machines are versatile and compatible with a wide range of materials, including:
- Metals: Stainless steel, aluminum, brass, and copper are frequently engraved for their durability and high contrast.
- Plastics: Acrylic, polycarbonate, ABS, and polypropylene are commonly engraved for branding, identification, and decoration.
- Wood: Hardwoods like oak and maple, as well as softwoods and MDF, are widely used in signage, artwork, and personalized items.
- Glass: Glass engraving is popular in the beverage industry and for decorative items, producing frosted, detailed engravings.
- Leather: Natural and synthetic leathers are engraved for custom goods, luxury products, and branding.
- Ceramics and Stone: Laser engraving is effective on ceramics, marble, granite, and stone for marking monuments, awards, and decorative items.
Applications of Laser Engraving
Laser engraving machines serve numerous applications across different industries due to their ability to produce highly detailed, durable, and tactile markings:
- Industrial Parts and Tools: Serial numbers, specifications, and identifiers are engraved on metal parts for traceability and compliance, especially in aerospace, automotive, and heavy equipment.
- Signage and Nameplates: Engraving is used for durable, weather-resistant signage and industrial nameplates on machinery or products.
- Jewelry and Luxury Goods: Laser engraving creates intricate designs, logos, or personalization on jewelry, watches, and other luxury items, adding value and customization.
- Gifts and Awards: Personalized messages, names, and designs are engraved on trophies, plaques, and gifts for a unique, high-quality finish.
- Electronics: Logos, model numbers, and safety information are engraved on electronics and components to ensure clear identification and regulatory compliance.
- Architectural and Interior Design: Engraved wood, glass, and stone are often used in high-end architectural projects, producing decorative and functional elements that add a personalized touch to spaces.
Advantages of Laser Engraving
Laser engraving offers a range of benefits, making it a preferred solution in applications requiring lasting marks and high detail:
- Permanent and Durable Markings: The engraving process creates deep, resilient marks that resist abrasion, chemicals, and environmental elements, making it ideal for parts that face frequent handling or exposure to harsh conditions.
- Precision and Detail: Laser engraving achieves fine, intricate details, allowing for high-resolution text, logos, and designs. It is particularly beneficial in industries that require precision and quality, such as luxury goods and medical devices.
- Versatility with Materials: Laser engraving is compatible with a wide array of materials, including metals, plastics, wood, glass, and stone, making it highly versatile across industries.
- Non-Contact Process: The non-contact nature of laser engraving means there is minimal wear on the material and no physical tool wear, reducing maintenance needs and extending machine life.
- Eco-Friendly: Laser engraving does not require inks, chemicals, or solvents, making it an environmentally friendly marking solution that produces minimal waste.
- Customization and Flexibility: Laser engraving allows for quick adjustments in design, depth, and pattern, making it highly adaptable for different products and orders. This flexibility is particularly beneficial in custom manufacturing and personalized products.
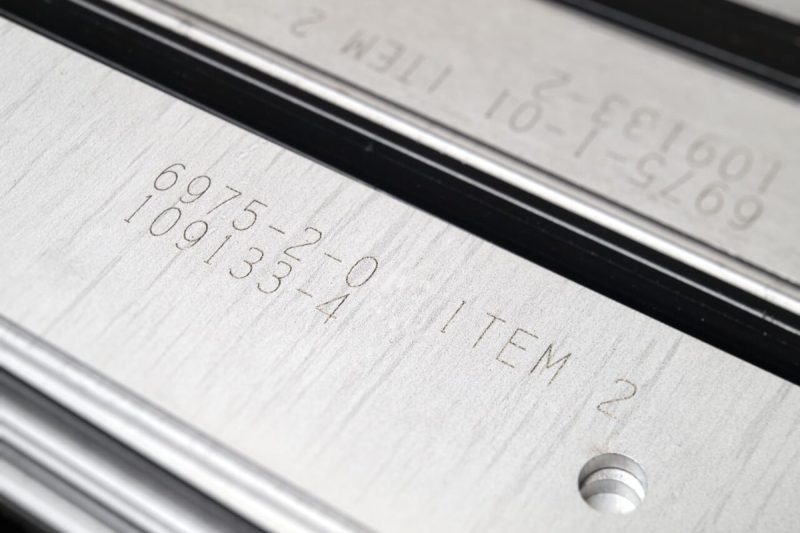
Key Differences Between Laser Marking and Laser Engraving
Depth of Material Penetration
- Laser Marking: Laser marking is a surface-level process that modifies the material’s color, reflectivity, or texture without removing any material. The laser alters only the top layer, creating a high-contrast mark that does not penetrate deeply.
- Laser Engraving: Laser engraving, by contrast, is a material-removal process. The laser vaporizes or melts the material, creating a recessed mark. The depth of engraving can be controlled, allowing for both shallow etchings and deep engravings. This makes engraving suitable for applications requiring tactile, visible marks.
Speed and Efficiency
- Laser Marking: Laser marking is generally faster because it only affects the material’s surface, making it ideal for high-speed, high-volume applications. This process is commonly used for marking products in a fast-paced production line where efficiency is key.
- Laser Engraving: Laser engraving tends to be slower as it involves removing material, which requires more laser passes and higher energy. Engraving can be time-consuming, particularly with hard materials or deep engraving needs, and is usually reserved for applications where quality and permanence outweigh speed.
Material Compatibility
- Laser Marking: Laser marking is compatible with a broad range of materials, including metals, plastics, glass, and ceramics. It is especially suited for materials that require traceability and branding without compromising surface structure, such as medical devices, plastics, and delicate components.
- Laser Engraving: Laser engraving also works on a wide variety of materials, including metals, wood, glass, ceramics, leather, and plastics. However, engraving is often preferred on materials that can handle material removal and on surfaces where deep, tactile marks are desired, such as wood plaques or metal tags.
Quality and Precision
- Laser Marking: Laser marking achieves high-contrast, precise marks that are ideal for fine details, such as small text, barcodes, and logos. The surface-level nature of marking also means it can produce intricate designs without causing structural changes to the material.
- Laser Engraving: Laser engraving is highly precise but also adds depth, allowing it to create intricate, tactile designs. However, because it removes material, the edges of engravings may appear rougher than the smooth marks of laser marking. Engraving’s precision is valued in applications requiring permanent, resilient markings.
Durability and Legibility
- Laser Marking: Laser-marked surfaces are durable, resistant to fading, and maintain their contrast well in conditions involving light wear and tear. However, because laser marking doesn’t penetrate the surface, it may not withstand harsh abrasions or heavy contact over time as well as engraving.
- Laser Engraving: Laser engraving creates recessed marks that are highly resistant to wear, chemicals, and environmental factors. Engravings remain legible over the product’s life, even in demanding conditions. This durability makes engraving ideal for parts and products exposed to frequent handling or extreme environments.
Cost Considerations
- Laser Marking: Laser marking machines are generally more cost-effective for high-speed, low-energy applications, especially in high-volume production. The lower power requirements and faster processing times translate to reduced operational costs. Laser marking is a practical choice for manufacturers needing efficient, low-cost marking solutions for high production rates.
- Laser Engraving: Laser engraving machines can be more expensive to operate due to the energy required for material removal and the slower process speeds. Additionally, engraving requires more robust machinery capable of handling harder materials, which may increase initial costs. However, the durability of engraving can justify the investment for products with long lifespans or heavy use.
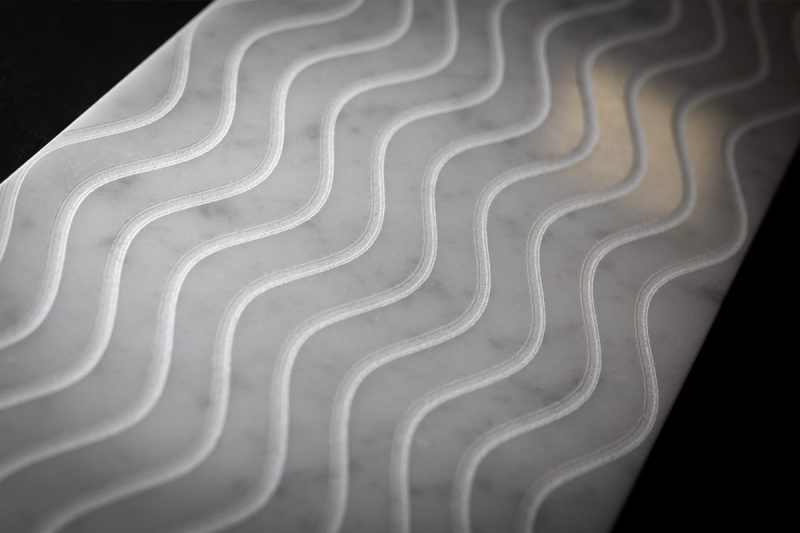
Choosing the Right Technology for Your Needs
Factors to Consider
Material Type
Depth and Durability of Mark
Precision and Detail Requirements
Production Speed
Aesthetic and Functional Needs
Budget Constraints
Industry-Specific Recommendations
Automotive Industry
- Recommendation: Laser engraving for components exposed to wear (e.g., engine parts) and laser marking for parts needing high-contrast serial numbers or barcodes.
- Reason: Engraving provides durability for parts under extreme conditions while marking ensures quick, efficient traceability for high-volume production.
Medical Device Manufacturing
- Recommendation: Laser marking is often preferred for medical devices and instruments.
- Reason: Marking maintains the material’s integrity, crucial for biocompatibility, and provides high-contrast marks for regulatory compliance without altering the surface, essential for instruments that need to remain sterile.
Electronics Industry
- Recommendation: Laser marking is ideal for electronics, including circuit boards and casings.
- Reason: Marking enables small, detailed codes and logos on delicate components without impacting functionality, ensuring high contrast and precision.
Aerospace and Defense
- Recommendation: Laser engraving for parts requiring resilience and laser marking for codes and identifiers.
- Reason: Engraving creates robust markings on metal components subject to wear while marking is ideal for traceable identifiers on parts.
Jewelry and Luxury Goods
- Recommendation: Laser engraving for personalized designs and laser marking for branding.
- Reason: Engraving produces permanent, intricate designs that add value to luxury items while marking provides high-precision logos without affecting surface quality.
Consumer Goods and Personalization
- Recommendation: Laser engraving for personalized items and laser marking for branding or traceability.
- Reason: Engraving provides a tactile effect for custom designs on items like gifts while marking ensures clear branding on consumer products.
Industrial Manufacturing and Tools
- Recommendation: Laser engraving for tools exposed to frequent handling and laser marking for component identification.
- Reason: Engraving creates long-lasting, durable marks on tools while marking provides efficient, high-speed identification for components.
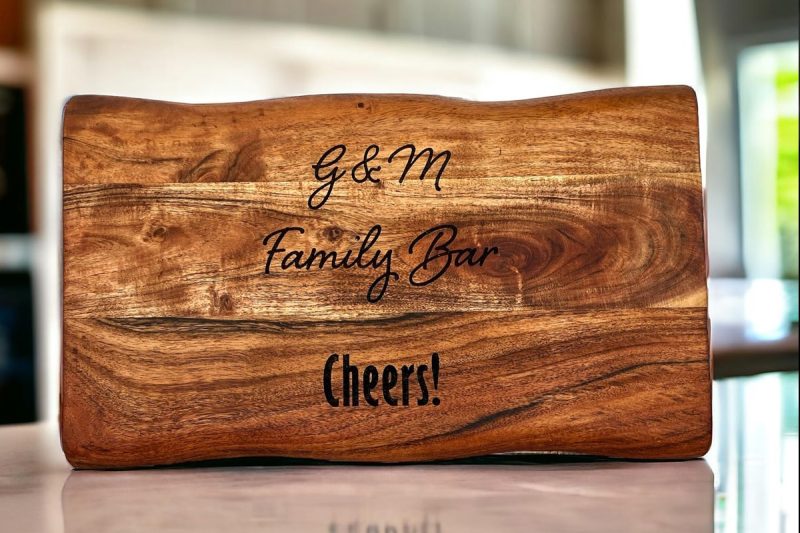
Summary
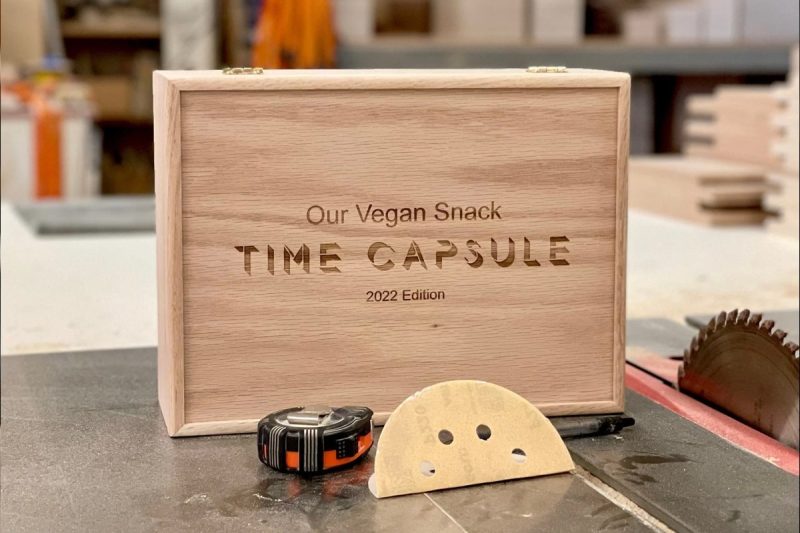
Get Laser Marking Solutions
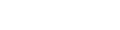
- [email protected]
- [email protected]
- +86-19963414011
- No. 3 Zone A, Lunzhen Industrial Zone,Yucheng City , Shandong Province.