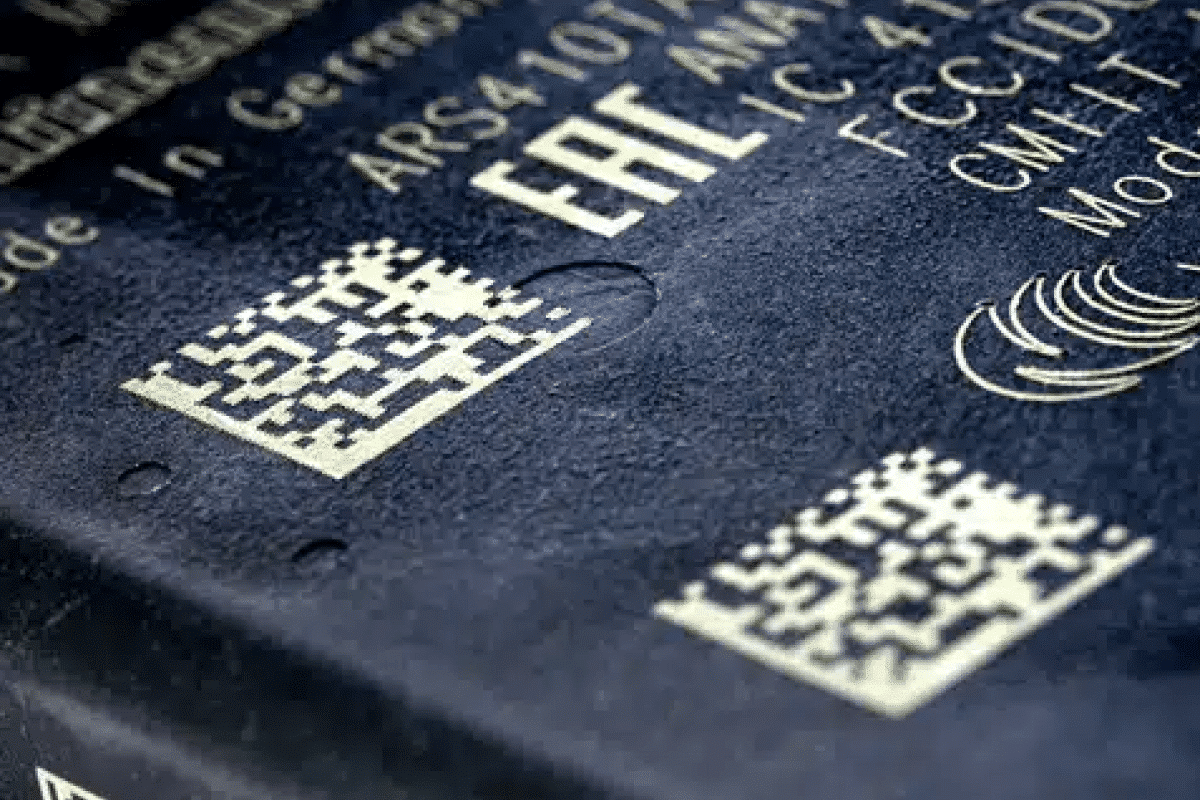
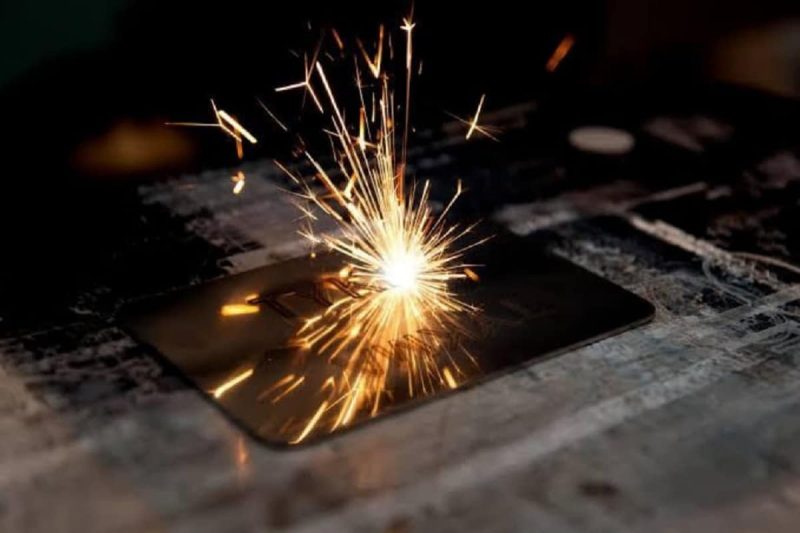
What is laser marking?
The principle of laser marking
The working principle of laser marking is to use a laser beam to process the surface of the material. The high-density energy of the laser beam causes changes in the chemical or physical properties of the material surface. The process flow is as follows:
- Choose appropriate laser equipment: According to the properties and requirements of the target material, select laser equipment with appropriate power and wavelength. Different types of lasers (such as CO2 laser, fiber laser, or Nd: YAG laser, etc.) are suitable for different materials and applications.
- Laser irradiation: Start the laser equipment and focus the laser beam on a specific position on the surface of the material. The high energy of the laser beam causes reactions such as evaporation, oxidation, or color change on the surface of the material, leaving the desired pattern or text on the surface.
- Control and debugging: Operators usually monitor and debug laser equipment in real-time, including adjusting laser parameters, such as power, scanning speed, and focal length, to control the marking effect and ensure that the resulting pattern is visible.
- Closure and cleanup: After completing all marking tasks, turn off the laser equipment and remove the material from the work platform. If auxiliary equipment such as coolant is used, cleaning and maintenance are also required.
Advantages of laser marking
laser marking technology has many advantages over screen printing technology, making it popular in the field of industrial marking. Here are the main advantages of laser marking technology compared to screen printing technology:
- Non-contact: The advancement of laser marking is that the laser beam does not directly contact the processed materials, does not produce mechanical extrusion or stress, and does not damage the processed items. This is very important for applications with high surface requirements.
- High precision: Laser marking can achieve very fine markings, including text, graphics, barcodes, etc. It can achieve tiny marks on small parts that screen printing usually cannot.
- Fast: Laser marking can achieve a fast marking process, especially suitable for high-volume production lines. It is usually faster than screen printing.
- Low cost: Automatically controlled by computer, the entire production process does not require manual intervention, saving a lot of labor costs.
- Wide range of applications: The laser marking machine system can restore the design on the appropriate carrier, such as metal, plastic, glass wood, ceramics, leather or stone, etc. This process is very accurate.
- Durability: Laser-marked marks are typically very durable and resistant to abrasion, chemical attack, and environmental changes. This makes it very useful in applications where long-term identification is required.
Disadvantages of laser marking
Compared with screen printing technology, laser marking technology also has some potential disadvantages:
- High initial cost: Laser marking equipment is generally relatively expensive, which makes it potentially less affordable for some small and medium-sized businesses or applications. In comparison, screen printing equipment usually costs less.
- Limited applicability: Laser marking has certain limitations on its applicability to different types of materials and surfaces. Some materials have limited ability to absorb laser light and may require a higher power laser source for marking. Screen printing technology is more flexible and has wider applicability in this regard.
- Environmental factors: The laser marking process produces high-energy laser beams, which may require additional cooling systems and carefully designed work environments. Smoke, odors, or harmful gases may also be produced during laser marking, requiring proper ventilation and exhaust gas treatment.
- Safety and eye protection: The laser beam used in laser marking is potentially dangerous and may pose a threat to the eyes of the operator. Therefore, protective eyewear is required to reduce the risk.
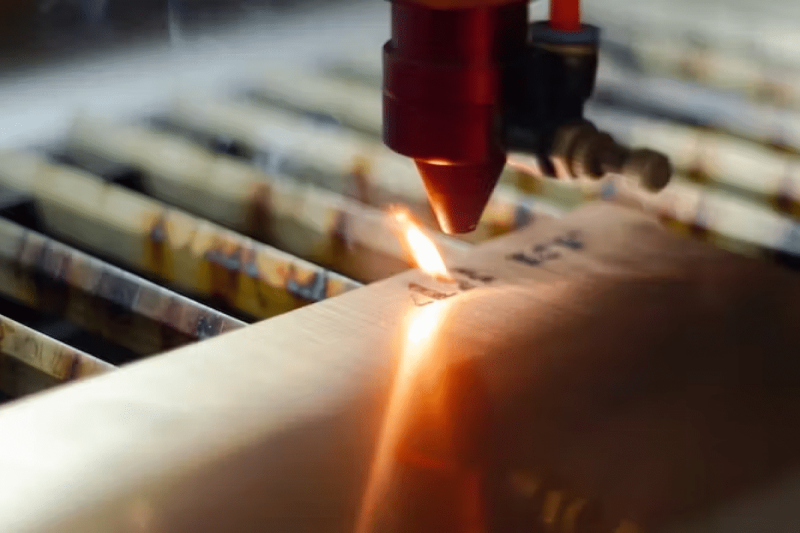
What is screen printing?
The principle of screen printing
The printing principle of the screen process is based on using a screen to transfer ink or ink to create the desired pattern or mark on the printed material. The printing process of the screen printing process is as follows:
- Preparing Materials: Ink or ink is placed on one end of the screen. Place a piece of printed material (such as paper, fabric, glass, or plastic) beneath the screen.
- To print: Use a squeegee or squeegee to scrape across the top of the screen, transferring ink or ink to the openings in the screen. Since the mesh of the screen has a certain aperture, the ink or ink is only transferred to the printing material through the openings to form the desired pattern or text.
- Drying and Curing: After printing is complete, the ink or ink needs to dry and cure to ensure that the pattern does not blur or remove. This can be done by natural drying or using equipment such as ovens, UV lamps, etc.
- Repeat printing: For multi-color printing or multi-layer printing, the above steps can be repeated, using different screen and ink colors each time to build a colorful pattern layer by layer.
Advantages of screen printing
although screen printing is not as good as laser marking in some aspects, it still has some advantages that make it very valuable in specific application scenarios. Here are some of its advantages:
- Wide Applicability: Screen printing can be applied to a variety of different types of materials, including paper, plastic, glass, and fabric.
- Low cost: Compared with laser marking equipment, screen printing equipment is usually lower in cost and suitable for small and medium-sized production.
- Large area printing: Screen printing is suitable for applications that require printing on larger surfaces, such as billboards, posters, and large packaging. Can handle large-size printing tasks.
- Multi-color printing: Screen printing can use multiple colors of ink to achieve colorful printing effects.
- Durability: Screen-printed markers are generally somewhat durable and able to withstand some wear and environmental effects, especially when the appropriate inks and coatings are used.
- Flexibility: Screen printing technology can be used in many different industries, including advertising, packaging, textiles, electronics, glass manufacturing, etc., making it highly flexible.
Disadvantages of Screen Printing
Compared with laser marking technology, screen printing technology has some obvious shortcomings, which may affect its choice in different application scenarios:
- Limited resolution: The resolution of screen printing is relatively low, which means that screen printing may not provide clear marks or patterns on printed details or small objects.
- Limited color options: Screen printing requires a separate screen for each color, and when printing in multiple colors multiple prints and registrations may be required, adding complexity and cost.
- Plate-making cost: Screen printing requires making a screen or screen, which involves expensive plate-making costs. If printing patterns or content need to be changed frequently, plate-making costs can become a burden.
- Slower production speed: Relative to laser marking, screen printing production speed is generally slower. This may not be efficient enough for applications requiring high throughput and rapid production.
- Limited Materials Available: Screen printing is available on a wide range of materials, but there may be limitations in some cases. For example, on some special materials, such as curved or uneven surfaces, screen printing may not provide a uniform printing effect.
- Environmental considerations: Some printing inks may contain harmful substances, which may have adverse effects on the environment and require certain measures.
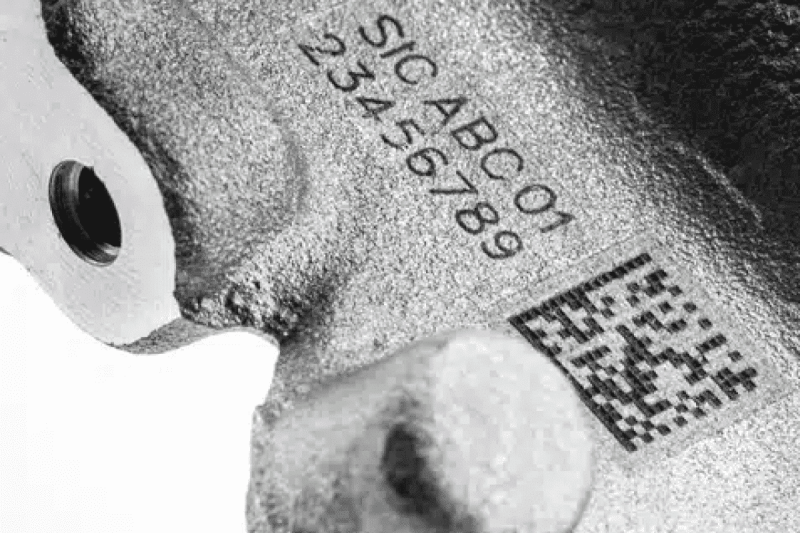
Laser marking vs. screen printing: which technology should you choose
Accuracy and resolution
Durability
Speed and productivity
Applied Materials
Plate making cost
Material thickness
Environmental and safety requirements
Summarize
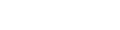
- [email protected]
- [email protected]
- +86-19963414011
- No. 3 Zone A, Lunzhen Industrial Zone,Yucheng City , Shandong Province.