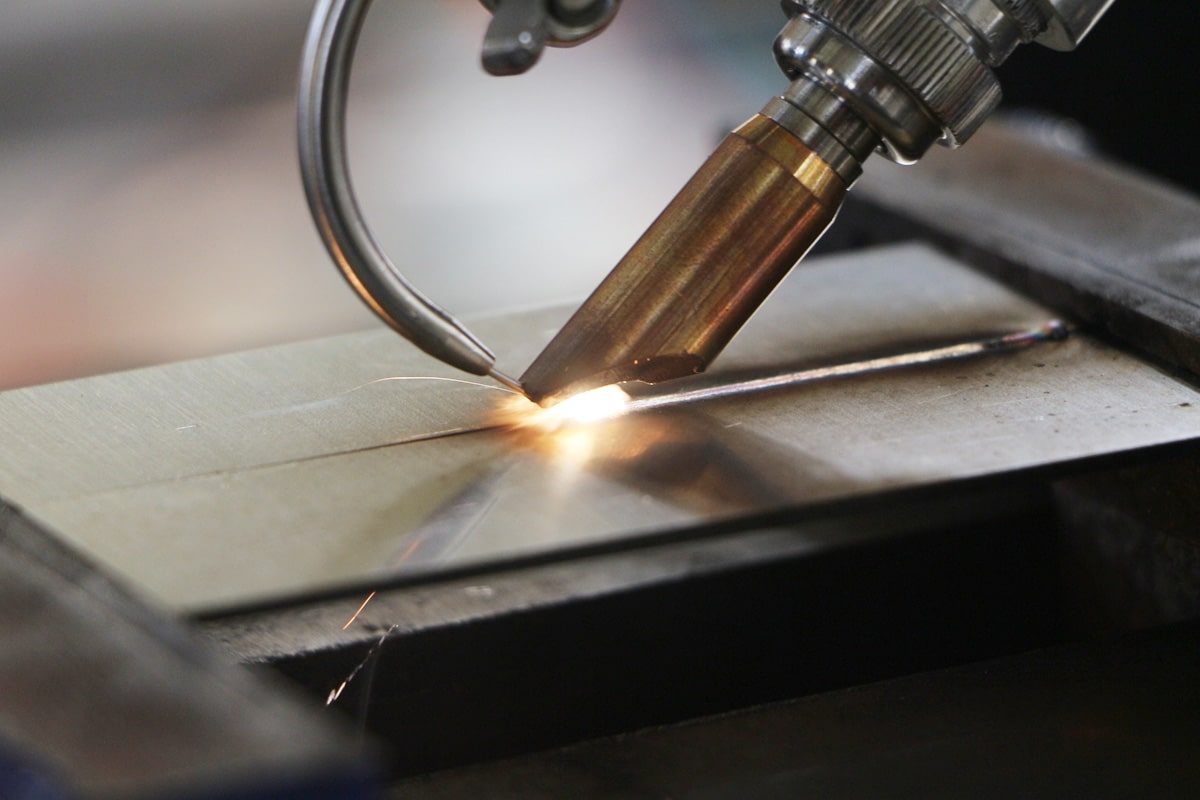
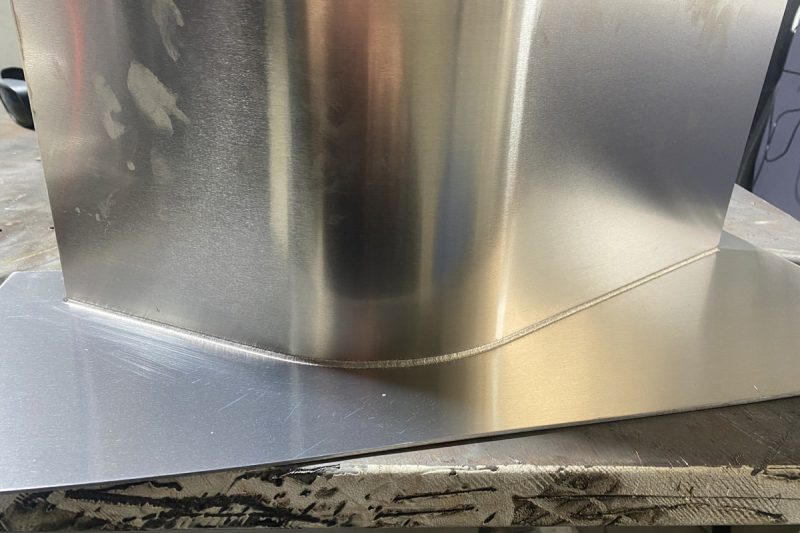
Aluminum Welding Basics
Characteristics of Aluminum
The unique physical properties of aluminum make the welding process significantly different from that of other metals, such as steel:
- High thermal conductivity: The thermal conductivity of aluminum is about 4 times that of steel, which means that during the welding process, heat will quickly spread to the entire weldment, making it difficult to maintain enough heat in local areas for effective welding.
- Low melting point: The melting point of aluminum is approximately 660°C, which is much lower than the melting point of steel. Therefore, it is easy to cause metal burn-through due to overheating during welding, especially for thin-walled aluminum.
- Oxide film: Aluminum easily forms a dense oxide film (Al₂O₃) in the air. The melting point of this oxide layer is as high as 2050°C, which is much higher than the melting point of aluminum itself. If this oxide film is not removed or treated, it will affect the welding quality and cause welding defects.
- Aluminum’s strength-to-weight ratio: Aluminum is only one-third as dense as steel, but its strength is higher, especially when alloyed. This makes aluminum a favored material in the automotive, aerospace and other industries, but it also requires welding processes that can take into account both strength and lightweight.
Challenges of Welding Aluminum
- Heat treatment effects: Aluminum is sensitive to heat, and the heat generated during welding can weaken the material, especially for aluminum alloys that have been strengthened by heat treatment. Welding causes local annealing, which leads to a decrease in strength.
- Thermal deformation: Due to the high thermal expansion coefficient of aluminum, thermal deformation is easy to occur during welding. Especially when welding over a large area, aluminum sheets may bend and deform due to uneven heating, affecting the welding quality and the accuracy of the finished product.
- Porosity and cracks: When welding aluminum, the molten pool easily absorbs hydrogen from the air, causing pores in the welding area. In addition, due to rapid cooling during welding, weld cracks may be induced, which is particularly common in aluminum alloy materials.
- Welding surface treatment: Before welding, the oxide layer and other contaminants on the aluminum surface must be thoroughly removed. If not handled properly, the oxide film will affect the fusion of the weld and may cause welding quality problems such as lack of fusion and pores.
The Importance of Proper Welding Technique
- Clean the surface: Before welding, be sure to use mechanical or chemical methods to remove the oxide film on the aluminum surface. This can be done by grinding or using a special cleaner to ensure the quality of the weld.
- Advantages of laser welding: Fiber laser welding machines are characterized by high precision and high efficiency, and are particularly suitable for welding aluminum. Laser welding can provide more stable and uniform welds, reduce heat-affected zones, and improve welding quality.
- Shielding gas: Although the process of fiber laser welding machines is different from traditional welding methods, shielding gas is still important. Using argon or helium can effectively prevent oxidation in the welding area and ensure the cleanliness and strength of the weld.
- Optimization of welding parameters: When welding aluminum, the welding current, voltage, and welding speed need to be precisely controlled. High current and slow welding may cause overheating and material burn-through, while low current and fast welding may result in insufficient penetration and incomplete weld fusion.
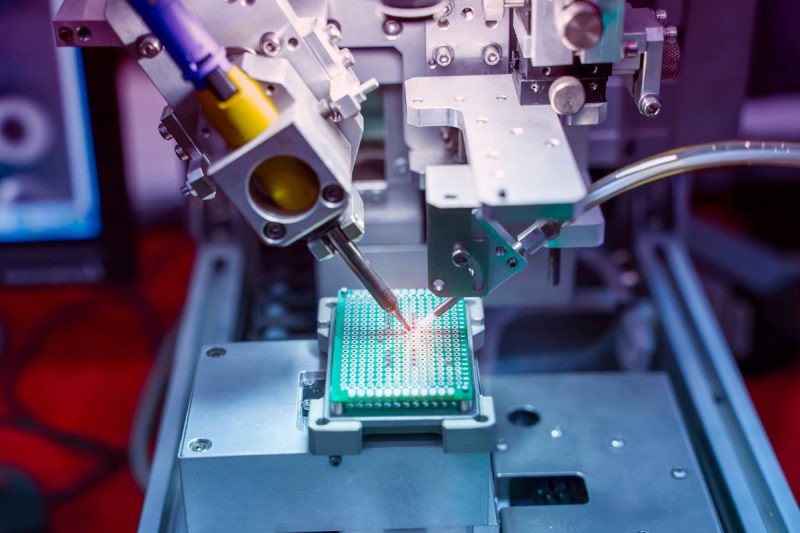
Laser Welding Basics
Laser Welding Principle
- High energy density: The biggest feature of laser welding is its high energy density, which means that even in a short time, the laser beam can generate enough heat to melt the material. This high energy density not only increases the welding speed, but also reduces the thermal impact on the surrounding materials.
- Deep fusion welding and thermal conduction welding: According to the different laser power densities, laser welding can be divided into deep fusion welding and thermal conduction welding. Deep fusion welding is usually used for welding thick materials, with large fusion depth and high weld strength; while thermal conduction welding is suitable for thin materials, with fast welding speed, small weld width and small heat-affected zone.
Types of Laser Welding Processes
Laser welding processes are mainly divided into the following categories:
- Continuous laser welding: This welding process is suitable for scenarios that require high production efficiency. The laser beam is continuously emitted during the welding process, which is suitable for welding long welds or thick materials. Its advantage is that it can ensure uniform weld quality without interruption.
- Pulse laser welding: Pulse laser welding is suitable for welding thin materials or precision welding. During the welding process, the laser generator emits energy in the form of pulses to provide a short-term high-energy laser beam. Pulse laser welding can reduce the thermal impact on the material and is suitable for those application scenarios that require high precision in the welding area.
- Hybrid laser welding: This is a process that combines laser welding with other welding processes (such as arc welding), which is usually used for welding that requires a higher penetration depth. Hybrid laser welding achieves higher welding strength and speed by combining the high energy density of the laser with the material filling capacity of traditional welding.
Advantages of Laser Welding
The widespread use of laser welding in modern manufacturing is due to its many advantages in various types of industrial welding. Here are some of the main advantages of laser welding process:
- High precision: Laser welding can achieve very high positioning accuracy, which is particularly suitable for those fields that require precision processing, such as aerospace and electronic manufacturing.
- High weld strength: Laser welding can produce welds with good mechanical properties due to its deep penetration welding characteristics. The weld strength can usually reach or exceed the strength of the parent material, which is particularly important in some high-demand application scenarios.
- Small heat-affected zone: Due to the concentrated and fast laser energy, the heat-affected zone of the material during welding is very small, which reduces the deformation and thermal damage of the material, making it excellent in welding thin-walled and precision parts.
- Adapt to a variety of materials: Laser welding can be used for almost any metal material, including aluminum, copper, stainless steel, etc., which are difficult to weld. It can also adapt to different material properties by adjusting the laser wavelength and power level.
- High degree of automation: The laser welding process can be easily integrated into an automated production line and combined with robotics to achieve fully automated operation. This not only improves production efficiency, but also ensures the consistency and quality of welding.
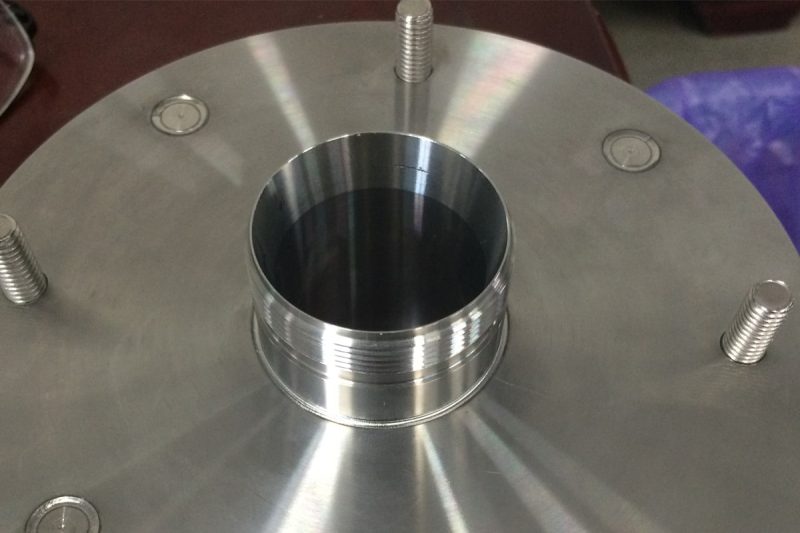
Laser Welding Aluminum
Laser Sources and Power Levels
- Laser type: Fiber laser generators are the first choice for welding aluminum because they can produce high power density at a small focus, which is suitable for highly reflective and highly thermally conductive materials such as aluminum. Although CO2 laser generators can also be used for aluminum welding, their wavelength is similar to the surface reflectivity of aluminum, and usually there will be greater energy loss.
- Power control: Due to the high thermal conductivity of aluminum, the heat during welding is easy to diffuse, resulting in the heat in the welding area not being easy to concentrate. Therefore, higher power is usually required when laser welding aluminum to ensure that enough energy is concentrated on the welding point. The power control should be kept in a stable range to prevent uneven welding or overheating of the welding area.
Focusing Optics and Beam Delivery Systems
- Optical system: When welding aluminum, high-quality lenses and reflectors must be used to focus the laser beam. Focusing optics can concentrate the energy of the laser beam into a very small area, increasing the energy density on the surface of the material, thereby ensuring that the aluminum can be effectively melted.
- Beam transmission: In order to maintain the high energy density of the laser beam, the beam transmission system must be kept in good alignment and clean condition. If any errors or energy losses occur during the beam transmission process, the welding quality will be affected. Therefore, regular inspection and maintenance of the beam transmission system is necessary.
Protective Gas and Atmosphere Control
During the laser welding of aluminum, the selection of shielding gas and atmosphere control are crucial. Aluminum is easily oxidized at high temperatures, and shielding gas must be used during welding to prevent oxidation and the formation of pores.
- Common shielding gases: Argon is the most commonly used shielding gas because it can form an inert atmosphere at high temperatures, preventing aluminum from reacting with oxygen in the air, thereby avoiding the formation of oxide layers and pores in the weld zone. Helium can also be used as an alternative gas. It is lighter than argon and can better cover the weld zone without inducing oxidation.
- Atmosphere control: The flow rate and coverage of the shielding gas must be carefully controlled to ensure that a uniform inert atmosphere is formed throughout the welding process. Too high or too low a gas flow rate will result in an uneven atmosphere, which will affect the welding quality.
Surface Cleaning and Preparation
The surface of aluminum is very easy to oxidize, and surface cleaning and preparation before welding are key steps to ensure welding quality. The oxide layer and contaminants on the aluminum surface can cause welding defects, so they must be removed by appropriate cleaning methods.
- Cleaning method: The oxide layer and oil stains on the surface of aluminum can be removed by mechanical grinding, chemical cleaning or sandblasting. Chemical cleaning usually uses acidic or alkaline solutions, which can effectively remove the oxide layer. Surface contamination should be minimized before welding to improve the stability and quality of welding.
- The importance of surface treatment: If the surface of aluminum is not properly treated, problems such as pores, cracks or insufficient weld strength may occur during welding. Good surface treatment can improve the uniformity of the welding pool and avoid welding defects.
Auxiliary Equipment and Accessories
The selection of auxiliary equipment and accessories is equally important during the laser welding of aluminum. These equipment include welding fixtures, welding tables, and cooling systems, which can assist in the smooth progress of the welding process.
- Welding fixtures: Aluminum is prone to deformation at high temperatures, so the use of suitable fixtures during welding can fix the material and reduce deformation. High-precision fixtures can ensure the alignment of the weld joint and reduce position errors in welding.
- Cooling system: In order to avoid overheating of aluminum during welding, a cooling system is essential. The cooling system can help dissipate heat quickly and reduce the temperature of the heat-affected zone, thereby reducing material deformation and welding defects.
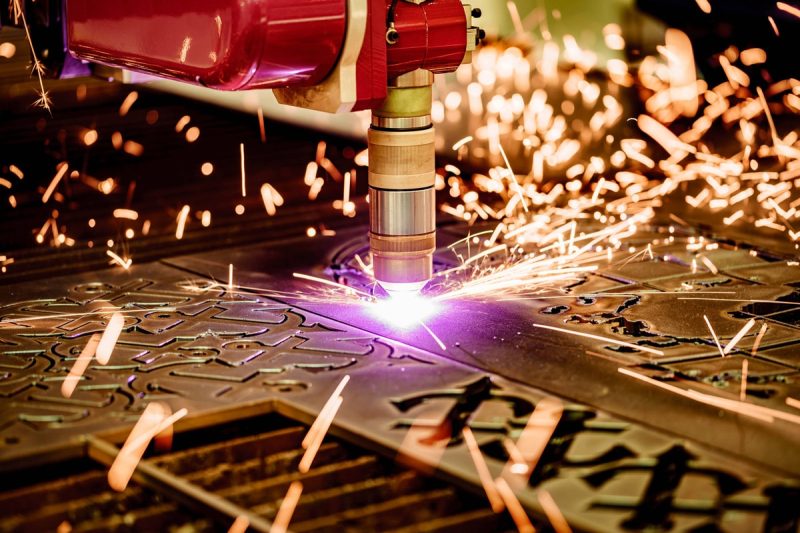
Safety Precautions and Precautions
Personal Protective Equipment (PPE)
Laser welding produces high-temperature, high-brightness laser beams and may cause the generation of spattering metal and smoke, so operators need to be equipped with appropriate personal protective equipment (PPE).
- Laser goggles: Lasers of different wavelengths have different hazards, and laser beams directly or reflected into the operator’s eyes can cause serious damage. Therefore, operators must wear special laser goggles suitable for their laser type to prevent laser radiation from damaging the eyes.
- Protective clothing and gloves: High-temperature metal spatter during welding may cause burns to the skin. Operators should wear high-temperature resistant and fire-resistant protective clothing and gloves to ensure physical safety during welding operations.
- Masks and respiratory protection: Harmful gases and fumes may be generated during laser welding, especially when welding aluminum or other coated materials. Operators should be equipped with appropriate respiratory protection to avoid inhaling harmful substances.
Ventilation and Fume Exhaust
During laser welding, the melting and gasification of materials will produce a large amount of smoke and harmful gases, such as aluminum oxide particles, carbon monoxide and other toxic gases. These substances are not only harmful to the health of the operator, but also pollute the environment.
- Fume exhaust system: An efficient fume exhaust and ventilation system must be equipped to promptly exhaust the fume and harmful gases generated during welding from the working area. The ventilation system should be regularly inspected and maintained to ensure its efficient operation.
- Filter device: The fume exhaust system should be equipped with appropriate filtering devices to remove particulate matter and harmful gases in the air to prevent them from polluting the operator and the surrounding environment.
Equipment Maintenance and Inspection
Laser welding equipment requires regular maintenance and inspection to ensure its safe operation and prevent potential mechanical failures. Mechanical wear, optical device contamination or laser source failure may lead to dangerous accidents.
- Optical system maintenance: The transmission and focusing systems of the laser beam must be cleaned and calibrated regularly. If optical devices such as lenses and reflectors are contaminated or damaged, it will cause the laser beam to deviate or lose energy, affecting the welding quality and may cause harm to equipment and personnel.
- Equipment inspection: Before each welding, the operator should check all safety functions of the equipment, such as the cooling system of the laser source, electrical connections, emergency stop buttons, etc., to ensure that the equipment is in good condition.
Safety Considerations
The laser welding system should be equipped with multiple safety mechanisms to ensure that the operation can be stopped immediately in abnormal situations to avoid accidents.
- Emergency stop button: The equipment should be equipped with an emergency stop button. Once an abnormal situation (such as equipment failure or operating error) occurs, the operator can immediately stop the equipment operation to avoid the expansion of the accident.
- Safety interlock device: Laser welding equipment is usually equipped with a safety interlock system to ensure that the laser generator is automatically shut down when the equipment door is opened or the operator enters the working area to prevent safety accidents caused by misoperation.
- Two-step trigger mechanism: Laser welding systems usually have a two-step trigger mechanism to ensure that the operator needs to confirm that the system is ready before the laser is started to prevent the laser from being triggered by mistake.
- Area isolation and shielding: The laser welding operation area should be properly isolated to prevent unrelated personnel from entering. In addition, the use of laser shielding devices can prevent the reflection or scattering of the laser beam from harming the surrounding environment.
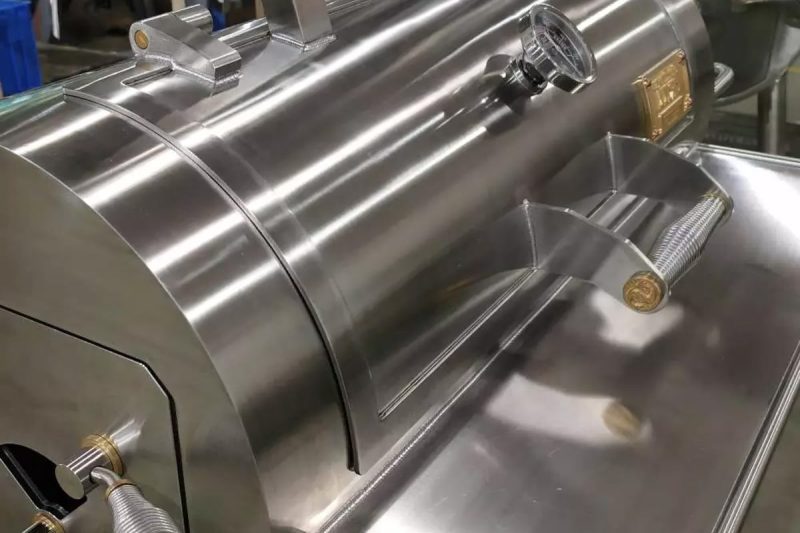
Applications of Laser Welding of Aluminum
Automotive Industry
Electronics
Aerospace
Buildings
Consumer Products
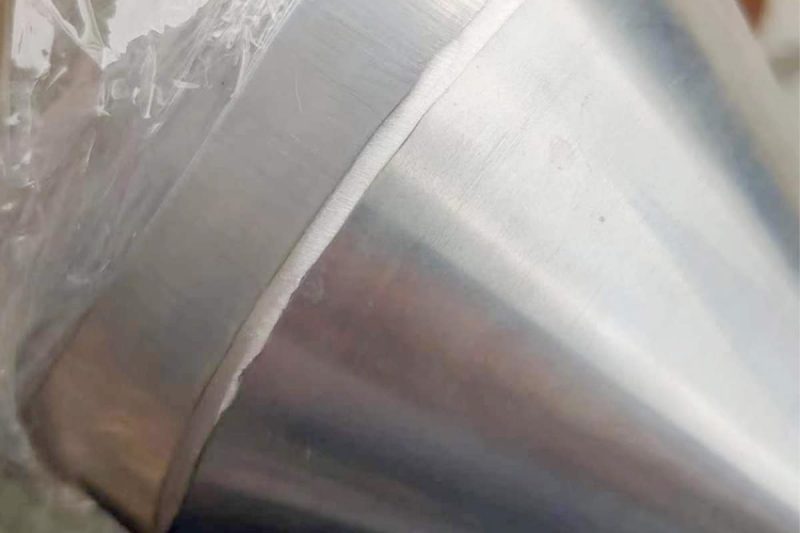
Laser Welding Aluminum Technology and Best Practices
Welding Parameters and Settings
Laser Welding Modes
Avoid Common Defects and Problems
Post-Weld Cleaning and Finishing
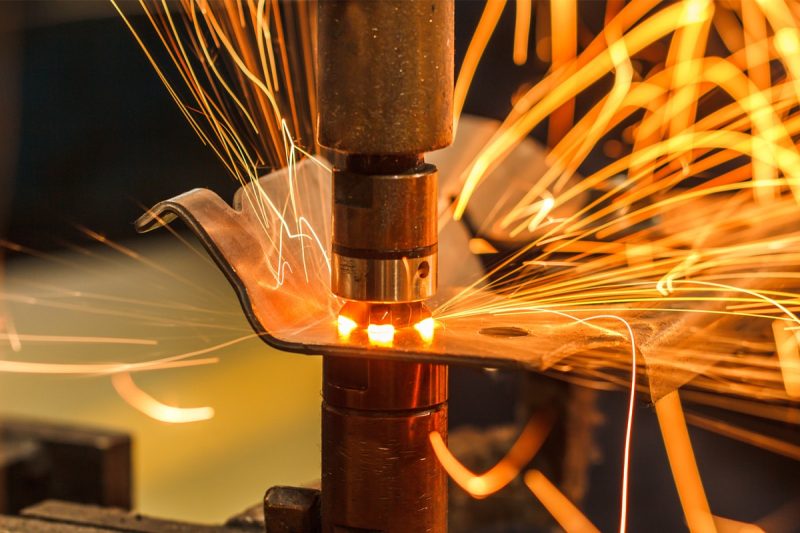
Summary
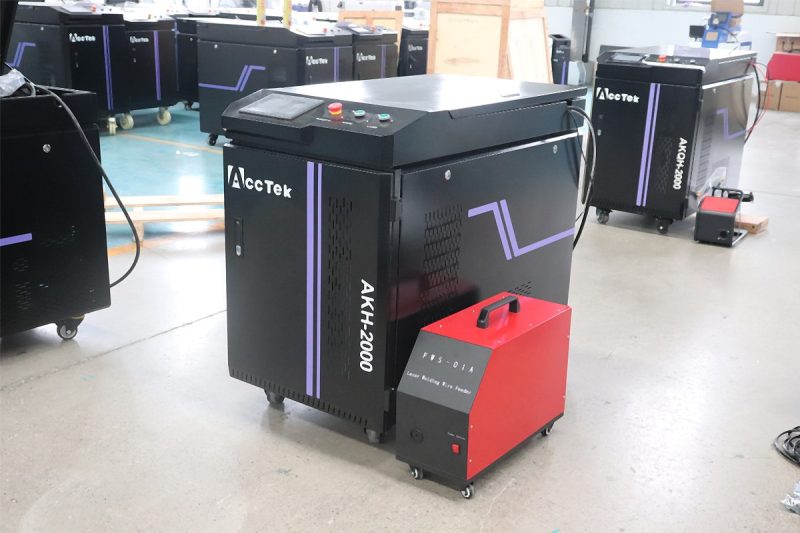
Get Laser Solutions
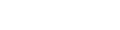
- [email protected]
- [email protected]
- +86-19963414011
- No. 3 Zone A, Lunzhen Industrial Zone,Yucheng City , Shandong Province.