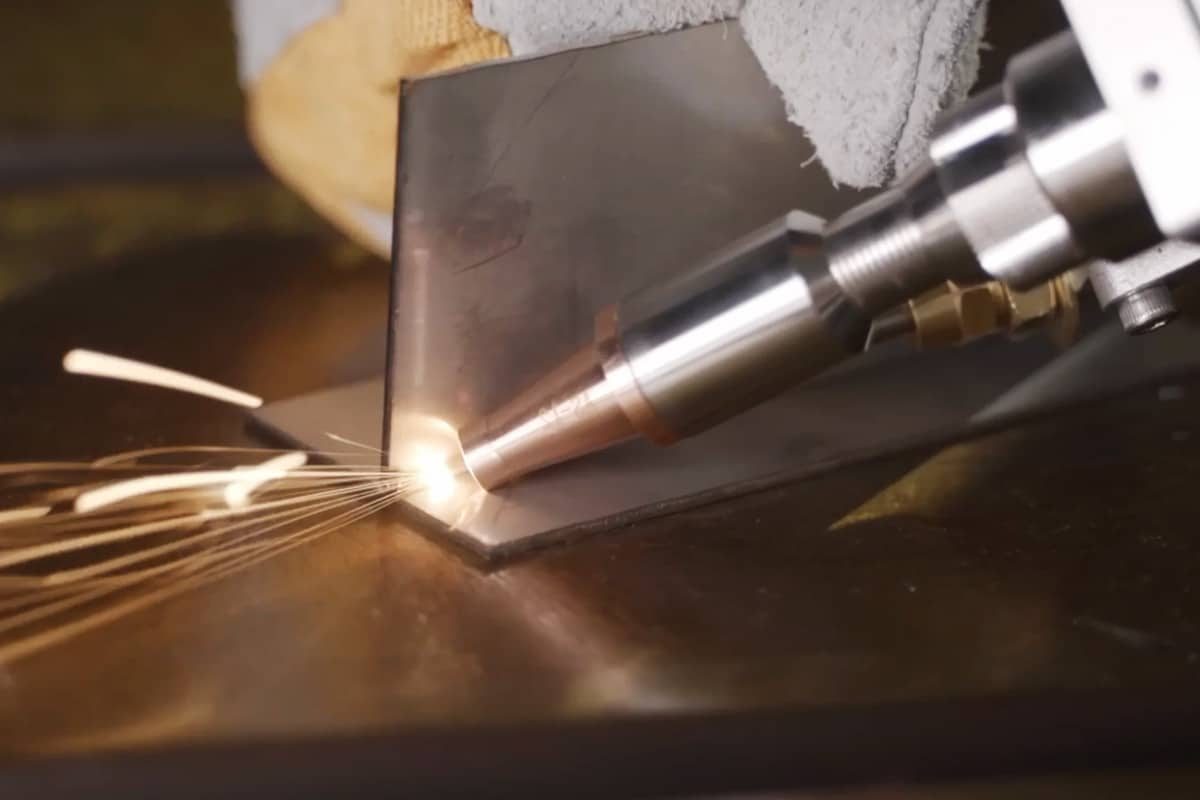
Laser Welding Joint Design
Laser welding has been widely used in aerospace, automobile manufacturing, electronic equipment, medical equipment, and other industries due to its high precision, low heat input, and high efficiency. Compared with traditional welding methods, laser welding has the advantages of narrow welds, fast welding speed, small heat-affected zone, and low deformation, making it an ideal choice for high-demand manufacturing fields. However, despite the many advantages of laser welding, the stability of welding quality and the reliability of the final product are still highly dependent on the design of the welded joint. Reasonable joint design can ensure the integrity and mechanical strength of the weld and reduce defects such as cracks, pores, and weld penetration that may occur during the welding process, while optimizing energy input, improving production efficiency, and reducing rework rate and production costs.
In laser welding applications, joint design needs to consider multiple factors, including the metallurgical properties of the substrate, welding method, laser power, weld shape, assembly accuracy, and subsequent processing requirements. An excellent joint design can fully utilize the advantages of laser welding to achieve high-quality, low-cost welding results. This article will explore the basic principles, influencing factors, and optimization strategies of laser welding joint design in depth to help companies and engineers improve welding quality, optimize production processes, and extend the service life of welded structures in practical applications.
Table of Contents
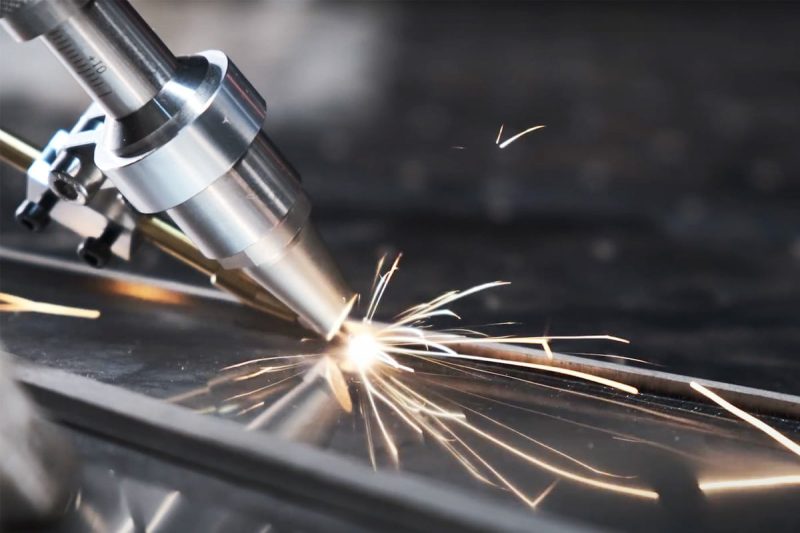
Basic principles of laser welding joint design
As a high-precision and high-efficiency welding process, laser welding is widely used in industries such as automotive manufacturing, aerospace, electronic equipment, and medical devices. Reasonable welding joint design is crucial to the integrity, strength, and production efficiency of the weld. Optimized joint design can not only reduce welding defects and improve welding quality but also reduce production costs and improve overall manufacturing efficiency. This article will discuss the key components of laser welding joints and their role in optimizing welding quality, and analyze how to achieve efficient and stable welding results through scientific design.
Key components of laser welded joints
Substrate
The choice of base material directly affects the quality of welding and the performance of the final product. When selecting welding materials, there are several key factors to consider:
- Mechanical properties: The strength, hardness, ductility, and other properties of the material will affect the stability of the welded joint.
- Metallurgical properties: Including the alloy composition, compatibility, and post-weld microstructure changes of the material to ensure the reliability of the weld.
- Thermal conductivity and melting temperature: affect the absorption and transfer of laser energy. High thermal conductivity materials (such as copper) may require a higher power laser generator, while low thermal conductivity materials (such as titanium) should avoid structural damage caused by overheating.
Connector Configuration
Different types of joint configurations are suitable for different welding needs. Common joint types include:
- Butt Joint: Suitable for high-strength welding applications, with excellent weld performance, but high processing accuracy requirements.
- Lap Joint: Suitable for thin plate welding, simple process, and fast welding speed, but attention should be paid to reducing stress concentration.
- T-Joint: Commonly used in structural welding, with strong weld bearing capacity, but it is necessary to ensure sufficient penetration to avoid welding defects.
In addition, during the welding process, the gap size, assembly accuracy, and alignment of the joint will directly affect the quality of the weld. Optimizing these parameters can reduce welding deformation and improve joint strength.
Filling material
In some laser welding applications, filler materials can be used to optimize weld quality. The main effects include:
- Enhance welding strength, prevent welding cracks, and improve the mechanical properties of the weld.
- Adjust metallurgical properties and improve the weld structure by optimizing alloy composition.
- Reduce welding defects such as pores and lack of fusion, and improve welding stability.
The selection of filler material should match the characteristics of the base material and be reasonably adjusted in combination with the welding process.
Key components of laser welded joints
Optimized weld joint design needs to meet the following objectives simultaneously:
- Ensure weld integrity and strength: Rationally design the joint structure to ensure good fusion and sufficient mechanical strength in the welding area.
- Reduce welding defects: Reduce common problems such as pores, cracks, and lack of fusion by optimizing material selection, joint structure, and welding process.
- Optimize process efficiency and productivity: Design reasonable joint configuration to increase welding speed, reduce material waste, and reduce processing costs, thereby improving overall production efficiency.
The design of laser welding joints is crucial to welding quality and production efficiency. By rationally selecting the base material, optimizing the joint structure and filling materials, and fine-tuning the welding process, the welding quality can be effectively improved, defects can be reduced, and production efficiency can be improved. Scientific joint design can not only ensure the strength and stability of the weld but also optimize the manufacturing process, helping companies maintain their competitiveness in the field of high-precision manufacturing.
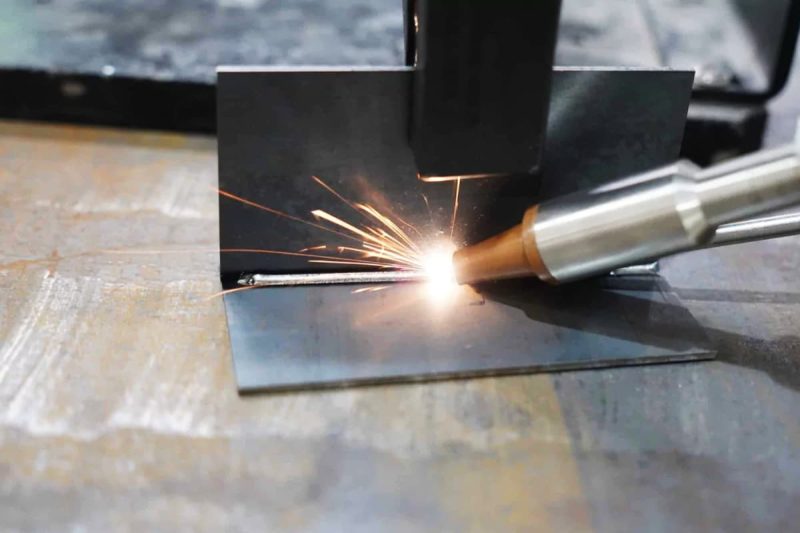
Factors Affecting Laser Welding Joint Design
The design of laser welding joints not only involves the selection of basic structures, but is also affected by multiple factors, including material properties, joint configuration, welding parameters, and application requirements. Proper consideration of these factors can help optimize welding quality, improve weld strength, reduce defects, and improve production efficiency.
Material properties
The physical and chemical properties of the substrate play a vital role in the performance of laser-welded joints. When designing welded joints, it is important to focus on the following key aspects:
- Compatibility of the substrate: The welding compatibility of different metal materials determines the quality of the weld. For example, alloys of similar composition usually have good fusion properties, while dissimilar metal welding may produce cracks or welding defects due to different thermal expansion coefficients or the formation of brittle intermetallic compounds.
- Mechanical and metallurgical properties: Mechanical properties (such as hardness, ductility, and tensile strength) affect the reliability of the weld. Metallurgical properties determine the changes in alloying elements during welding. For example, some high-carbon steels may produce hardened structures during welding, increasing the risk of cracks. Therefore, welding process parameters need to be adjusted for different material properties to ensure welding quality.
- Thermal conductivity and melting temperature: The thermal conductivity and melting point of the material affect the transmission and absorption of laser energy. For example, high thermal conductivity metals (such as copper and aluminum) dissipate heat quickly and require higher laser power or more concentrated energy input. Materials with higher melting points may require increased welding energy to ensure sufficient melting and joint strength.
Connector Configuration
The type, assembly accuracy, and alignment of the joint directly affect the stability of the welding process and the quality of the weld. Common joint types include:
- Butt Joint: Suitable for welding scenarios that require high strength and low deformation. The gap of the butt joint needs to be strictly controlled to ensure complete fusion and avoid defects such as incomplete fusion or slag inclusion.
- Lap Joint: Suitable for thin plate welding, the overlapping part of the weld can provide better strength. However, due to the stacking effect, gas may remain in the gap, and the welding parameters need to be optimized to reduce porosity.
- T-Joint: Usually used for structural parts that bear greater stress. The welding of T-joints needs to ensure sufficient penetration to avoid cracking caused by stress concentration.
In addition, in the design of welded joints, it is also necessary to consider:
- Assembly and gap size: Too large a gap may result in insufficient weld filling, while too small a gap may result in incomplete fusion or weld deformation. Therefore, accurate assembly and gap control are critical to welding quality.
- Laser beam transmission and part processing channel: Ensure that the laser beam can reach the welding area smoothly to avoid affecting the welding effect due to beam obstruction or reflection. At the same time, in the automated production line, the part fixing method and the design of the welding channel also need to be optimized to ensure welding stability and consistency.
Welding parameters
Reasonable adjustment of welding parameters can optimize weld quality and reduce welding defects. Common key parameters include:
- Laser power: affects welding depth and molten pool formation. High power is suitable for deep penetration welding, while low power is suitable for precision welding.
- Focus position and beam diameter: Accurate control of the focus affects energy density and welding depth. Smaller beam diameters are suitable for high-precision welding, while larger beams can be used for wide weld requirements.
- Welding speed and travel direction: Too fast welding speed may lead to insufficient penetration and affect weld strength, while too slow may cause welding deformation or expansion of the heat-affected zone (HAZ). Therefore, the welding speed needs to be adjusted in combination with the material and joint structure.
- Shielding gas and atmosphere control: Appropriate shielding gas (such as argon, nitrogen, or mixed gas) can reduce oxidation during welding and optimize weld quality. Different materials have different requirements for gas. For example, titanium alloys need to be completely isolated from oxygen, while stainless steel can be protected by argon to reduce welding discoloration and oxidation.
Application Requirements
In addition to material and process factors, weld joint design must also meet the needs of specific application scenarios, including:
- Functional and structural requirements: Select the appropriate joint type and weld structure based on the final use of the product. For example, laser welding in the automotive industry usually requires high strength and lightweight, while electronic equipment welding emphasizes refinement and heat-affected zone control.
- Surface finish and appearance: In some applications, such as consumer electronics or medical devices, the aesthetics of the weld is critical. This requires optimizing welding parameters, reducing weld spatter and slag, and improving surface finish.
- Post-weld processing and secondary processing: Some welding processes may require additional post-processing, such as grinding, heat treatment, or coating, to meet the quality standards of the final product. Therefore, when designing weld joints, the feasibility and cost of subsequent processing must also be considered.
The design of laser welding joints is affected by many factors, including the characteristics of the substrate, joint configuration, welding parameters, and the final application requirements. By rationally selecting materials, optimizing joint structure, accurately controlling welding process parameters, and adjusting according to specific application requirements, the welding quality can be effectively improved, defects can be reduced, and production efficiency can be improved. Scientific and reasonable joint design can not only ensure the strength and stability of the weld but also optimize the manufacturing process, improving production competitiveness while ensuring product quality.
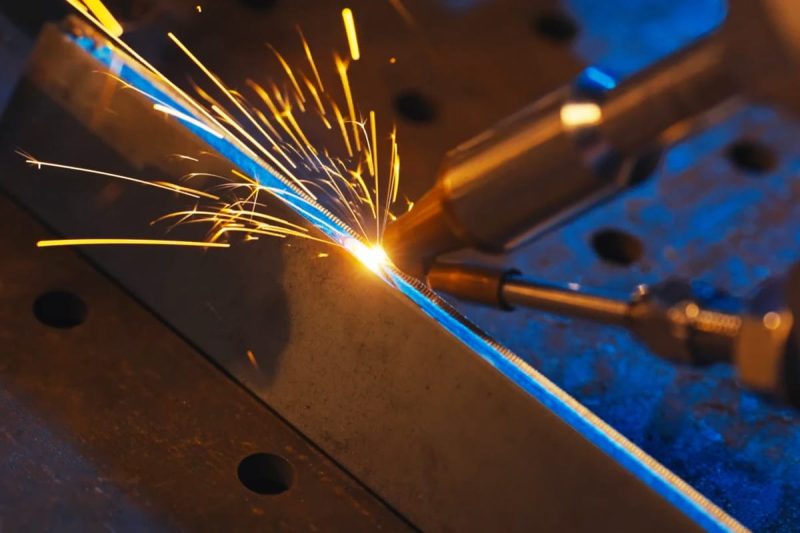
Optimization strategy for laser welding joint design
The goal of optimizing laser welding joint design is to improve welding quality, ensure the integrity and strength of the weld, reduce defects, and improve production efficiency. The main optimization strategies include the following aspects:
Minimize heat affected zone (HAZ)
A large heat-affected zone (HAZ) can affect material properties and even cause weld embrittlement. By optimizing laser power, welding speed, and beam focus, heat input can be effectively controlled to reduce the heat-affected zone. In addition, a reasonable selection of joint types, such as butt joints or lap joints, can also help reduce heat accumulation and improve welding stability.
Improve welding strength
The key to ensuring the strength of welded joints lies in optimizing heat distribution, controlling gap size, and accurately aligning the workpieces. A proper welding process can reduce stress concentration and avoid problems such as lack of fusion. In some applications, the use of matching filler materials can enhance the bond of the weld and improve the overall strength and durability of the joint.
Ensure welding quality
Welding quality is affected by many factors, including laser power, focus position, welding speed, and the use of shielding gas. Reasonable adjustment of these parameters can reduce defects such as pores and cracks. In addition, the use of online monitoring technology for quality inspection can ensure the consistency of the weld and improve the product qualification rate.
Optimizing the design of laser welding joints is an important means to improve welding quality and production efficiency. By reducing the heat-affected zone, increasing weld strength, and strictly controlling welding quality, the welding effect can be effectively improved to meet the high standards of industrial manufacturing.
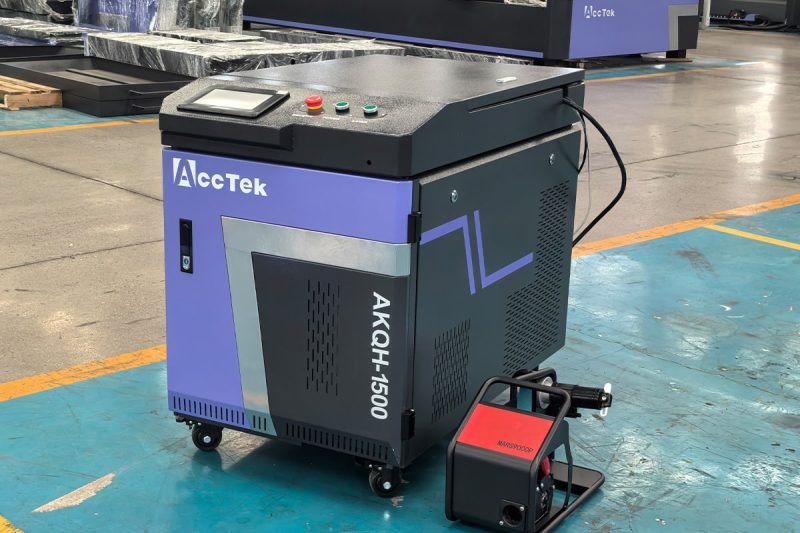
Summarize
Laser welding joint design is a key factor in determining welding quality and production efficiency. By deeply understanding the basic principles, influencing factors, and optimization strategies of joint design, manufacturers can ensure the integrity of the weld, reduce defects, and improve the overall welding quality. Reasonable joint design can not only improve welding strength but also optimize the production process to meet the needs of different application scenarios.
If you are looking for efficient and precise laser welding solutions, AccTek Laser offers advanced laser welding machines that meet the highest quality and efficiency standards. Our equipment uses advanced laser technology to ensure welding stability and consistency to help you achieve your production goals. Contact us to learn more about how our products can help you optimize your welding process!
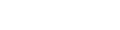
Contact information
- [email protected]
- [email protected]
- +86-19963414011
- No. 3 Zone A, Lunzhen Industrial Zone,Yucheng City , Shandong Province.
Get Laser Solutions