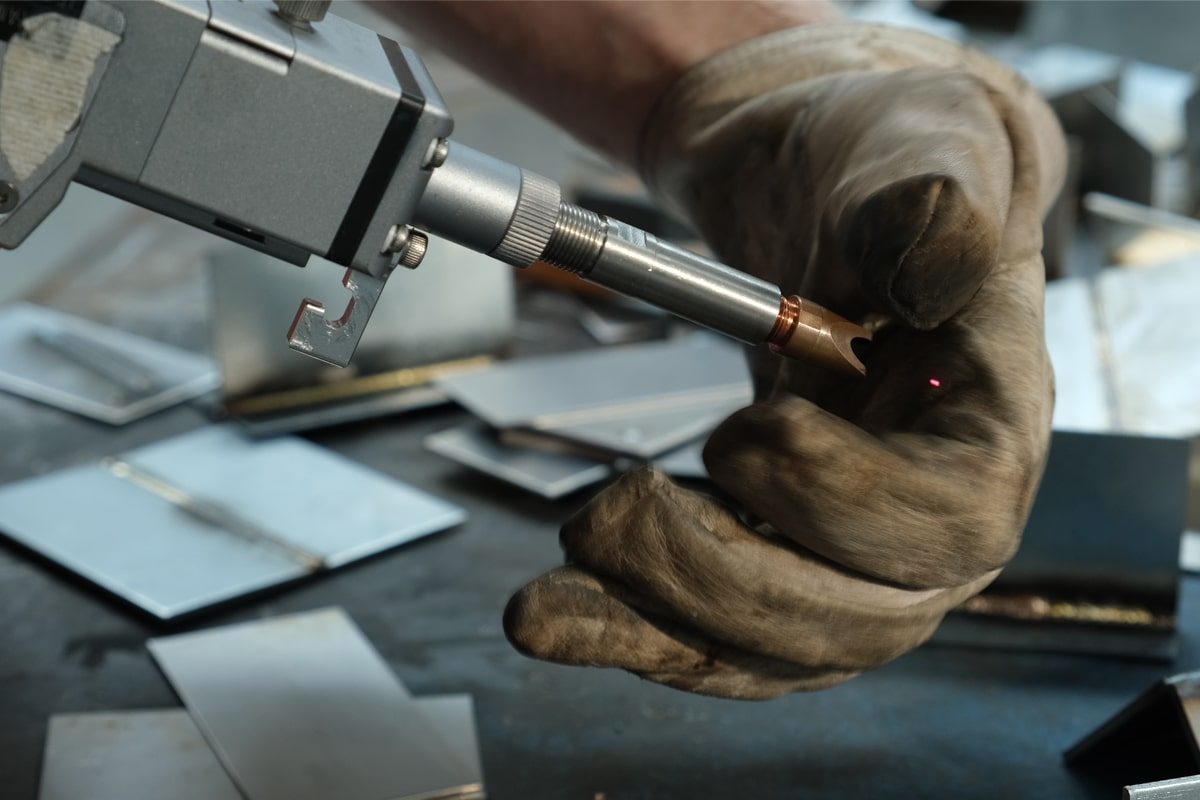
Laser Welding Machines: Comprehensive Guide
Welcome to your comprehensive guide to laser welding machines, your in-depth look at one of the most advanced technologies shaping the modern manufacturing landscape. In an age where precision, efficiency, and quality are paramount, laser welding stands out as a highly efficient method that offers unparalleled capabilities in industries ranging from automotive and aerospace to electronics and medical devices.
In this comprehensive guide, we’ll explore its capabilities, benefits, applications, and key considerations for implementation. This article delves into the fundamentals of laser welding, studying the complex interactions between laser beams and materials to achieve precise and reliable connections. From understanding the different types of laser welding technology to exploring advanced methods and emerging trends, we leave no stone unturned to provide you with the knowledge you need to realize the full potential of laser welding technology. Whether you’re a seasoned industry professional looking to optimize your production processes, or a newbie eager to master the cutting-edge technologies that drive innovation, this guide has you covered.
Table of Contents
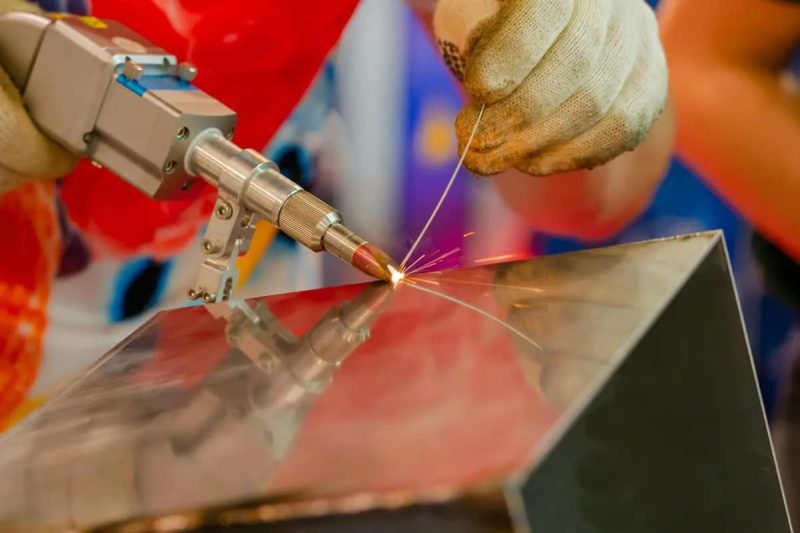
Advantages of Laser Welding
In it, we explore the many advantages that make laser welding an important technology for modern manufacturing. Laser welding offers many advantages that elevate it over traditional welding methods and revolutionize the production process in different industries.
Precision and Accuracy
One of the most significant advantages of laser welding is its high degree of precision and accuracy. The laser’s focused beam allows precise control to create complex welds with minimal margin of error. This precision ensures consistent quality and dimensional accuracy, making laser welding ideal when precision applications are a concern, such as the aerospace and electronics industries.
Speed and Efficiency
Laser welding is significantly faster and more efficient than traditional welding techniques. The concentrated heat source of the laser beam is beneficial to the rapid melting of materials, effectively reducing welding time and increasing output. This efficiency means higher productivity and lower production costs, making laser welding the first choice for high-volume manufacturing operations.
Minimum Heat Affected Zone
Unlike traditional welding methods that rely on intense heat to join materials, laser welding creates a minimal heat-affected zone (HAZ). The focused nature of the laser beam ensures that heat input is localized, thereby reducing deformation, warping, and metallographic changes in the surrounding area. This minimization of the heat-affected zone is beneficial when welding heat-sensitive materials or components with tight dimensional tolerances.
Versatility
Laser welding machines offer unparalleled versatility and are capable of welding a wide range of materials, including metals, plastics, ceramics, and composites. Whether joining dissimilar materials or adapting to complex geometries, laser welding excels where traditional methods fall short. Additionally, laser welding can be integrated into automated systems, further extending its versatility and applicability in a variety of manufacturing processes.
Contactless
Another significant advantage of laser welding is its non-contact nature. There is no physical contact between the welding tool and the workpiece during the welding process, reducing the risk of contamination, deformation, or damage to precision components. This feature is valuable in industries where cleanliness and precision are critical, such as electronics and medical device manufacturing.
In summary, the advantages of laser welding, including precision and accuracy, speed and efficiency, minimal heat-affected zone, versatility, and non-contact operation, make it a transformative technology driving innovation and excellence in modern manufacturing.
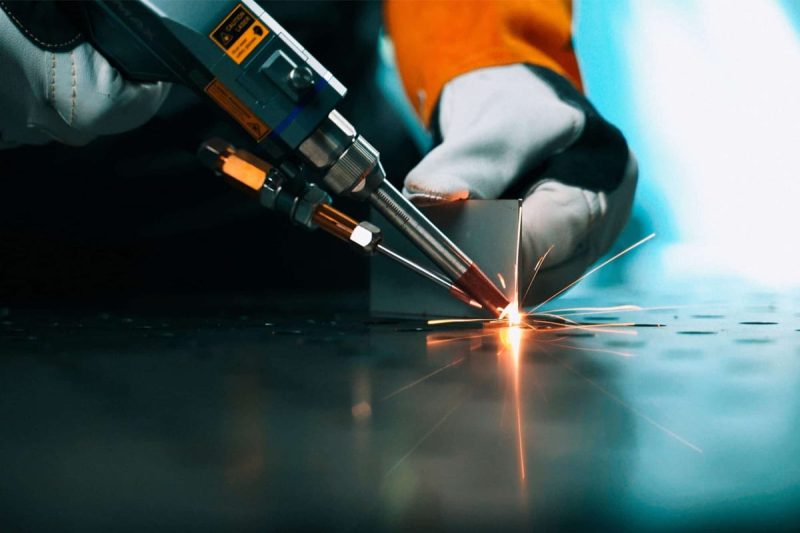
Disadvantages of Laser Welding
While laser welding offers many advantages, it is important to realize that, like any technology, it has its limitations and disadvantages. Here are some of the main disadvantages of laser welding:
Initial Investment Cost
One of the main disadvantages of laser welding is the large initial investment required to purchase and set up the necessary equipment. Laser welding machines are complex and sophisticated systems that incorporate advanced optics, precision controls, and high-power laser generators. Therefore, the upfront costs associated with purchasing and installing a laser welding system can be high, especially for small and medium-sized businesses.
Skill Requirements
Operating a laser welding machine requires specialized training and expertise. Unlike some traditional welding methods that require a higher level of operator skill, laser welding requires a high degree of precision and control. Operators must have a thorough understanding of laser technology, material properties, and welding parameters to ensure successful results. This skill requirement can create challenges for companies looking to adopt laser welding without access to trained personnel or training resources.
Limited Thickness Range
While laser welding is good at joining thin to moderately thick materials, it may not be suitable for welding very thick sections. Compared to some other welding methods, laser welding is limited in the depth of penetration achievable, which may limit its suitability in certain applications, such as heavy-duty manufacturing or structural welding. Additionally, achieving consistent weld quality across different material thicknesses can be challenging and may require specialized techniques or equipment.
Reflective Material
Laser welding is less effective on highly reflective materials such as copper, aluminum, and certain alloys. These materials tend to reflect much of the laser energy, making the welding process less efficient and can lead to problems such as poor weld penetration or surface defects. While techniques like beam shaping or using specific wavelengths can help alleviate this limitation to some extent, welding reflective materials with lasers remains a challenge compared to other welding methods.
Security Question
Laser welding involves the use of high-intensity laser beams, which can pose a safety risk if not handled properly. Direct exposure to laser beams can cause severe burns or eye damage, so strict safety protocols and protective measures are required. In addition, the laser welding process may produce harmful fumes, vapors or particulate matter, requiring adequate ventilation and personal protective equipment to ensure worker safety.
In summary, while laser welding offers numerous advantages in terms of precision, efficiency, and versatility, its limitations and associated challenges must be considered. Addressing factors such as initial investment cost, skill requirements, material compatibility and safety considerations can maximize the benefits of laser welding while minimizing potential drawbacks.
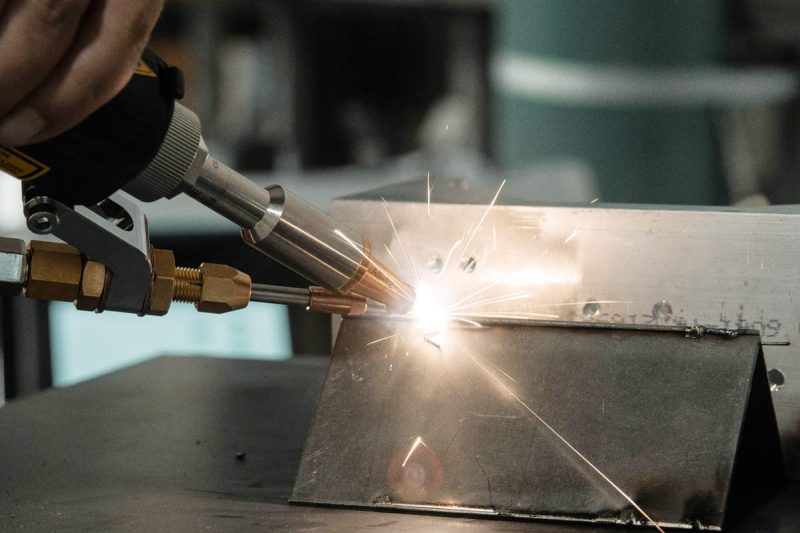
What Are The Costs of Laser Welding?
When considering implementing laser welding technology, it is crucial to understand the associated costs. When purchasing a laser welding machine, it is important to evaluate the initial investment and ongoing costs to make an informed decision. The following is an overview of cost considerations associated with laser welding:
Initial Equipment Investment
The major cost component of using laser welding is the initial investment in equipment. Laser welding machine prices vary widely, depending on factors such as power output, technical features, and manufacturer reputation. AccTek Laser’s entry-level machines start at $4,000, while high-end industrial-grade machines can cost upwards of $30,000 or more. In addition, ancillary equipment such as laser safety shields, cooling units, and fume extraction systems may increase the overall initial investment.
Maintenance and Service
Like any precision machinery, laser welding systems require regular maintenance and upkeep to ensure optimal performance and longevity. Maintenance tasks may include cleaning optics, calibrating laser parameters, and replacing consumable parts such as protective windows, nozzles, and gas filters. Routine maintenance costs typically range from a few hundred to a few thousand dollars per year. Maintenance costs may vary depending on the complexity and level of use of the system, but a budget should be made for continued operation.
Consumables and Supplies
Laser welding also has costs associated with consumables and supplies. These may include welding gases such as argon or helium, shielding gases to prevent oxidation, and filler materials for some types of welding. In addition, consumables such as protective lens caps, nozzle tips, and coolant may need to be replenished regularly, and the cost of consumables can vary greatly depending on the make and model of the machine, intensity of use, and the specific consumables required. The annual cost of consumables can range from a few hundred to a few thousand dollars.
Energy Consumption
Laser welding machines require large amounts of electricity to operate, especially the high-power systems used in industrial applications. Energy consumption costs can vary depending on factors such as laser power output, duty cycle, and local electricity prices. Understanding and managing energy consumption is critical to controlling operating costs and optimizing the cost-effectiveness of your laser welding process. Electricity rates are typically measured in cents per kilowatt hour (kWh) and can range from a few cents to a few cents per kWh. Higher electricity bills will result in higher energy consumption costs for operating a laser welding machine.
Training and Skills Development
Investing in training and skill development for operators and technicians is another cost consideration associated with laser welding. Proper training ensures personnel have the knowledge and expertise to operate equipment safely and efficiently, minimizing the risk of errors, accidents, and downtime. Laser welding machine training and skill development costs range from hundreds to thousands of dollars per person, depending on factors such as the type of training, training provider, and level of expertise required.
In summary, while laser welding offers numerous advantages in terms of accuracy, efficiency, and versatility, the associated costs must be considered to make an informed decision. By evaluating factors such as equipment investment, maintenance and service, consumables, energy consumption, and training, companies can effectively assess the financial impact of adopting laser welding technology and ensure it is cost-effectively integrated into the manufacturing process.
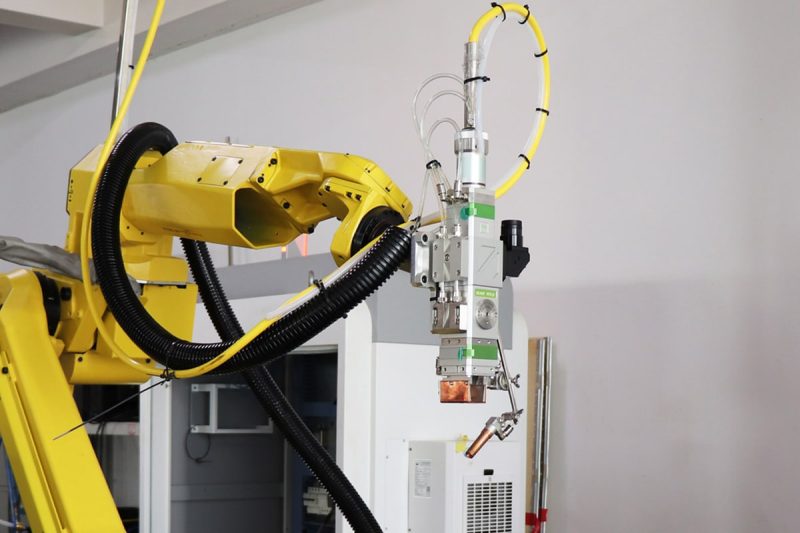
Laser Welding Gas Requirements
Laser welding relies on precise control of the gas environment to achieve optimal welding quality, efficiency, and safety. The selection and management of welding gases play a vital role in the success of the laser welding process. The following is an overview of laser welding gas requirements:
Protective Gas
Shielding gases are used to protect the weld pool from atmospheric contaminants, such as oxygen and nitrogen, which can cause defects such as porosity and oxidation. Common shielding gases used for laser welding include argon, helium, and mixtures of these gases. Argon is generally favored for its affordability and effectiveness in shielding most metals, while helium has superior thermal conductivity, improving penetration and reducing heat-affected zones in some applications.
Auxiliary Gas
Assist gases serve a variety of purposes in laser welding, including enhancing weld penetration, controlling spatter, and improving overall process stability. Oxygen and nitrogen are commonly used as assist gases, with oxygen being particularly effective at increasing cutting and welding speeds in certain materials, while nitrogen is favored for its ability to reduce oxidation and refine weld bead geometry.
Purge Gas
In applications where welding is performed on the back side of a joint or in an enclosed space, purge gas is used to create an inert atmosphere that prevents oxidation and ensures weld quality. Argon is commonly used as a purge gas due to its inertness and economy. The flow rate and distribution of the purge gas must be carefully controlled to maintain the required atmosphere and prevent contamination.
Cooling Gas
High-power laser welding systems generate large amounts of heat and require effective cooling to maintain system performance and prevent damage to critical components. Cooling gas, usually in the form of a cooling air stream or water circulation, is used to dissipate heat from laser optics, focusing lenses, and other heat-sensitive components.
Gas Quality and Purity
Welding gas quality and purity are key factors in achieving consistent welding quality and process stability. Impurities such as moisture, oil, and particles can adversely affect laser beam quality, causing defects and reducing productivity. Therefore, using high-quality gases from reputable suppliers and implementing appropriate gas filtration and purification systems is beneficial for optimal laser welding performance.
In summary, by understanding the specific gas requirements for shielding, auxiliary, purging, and cooling, manufacturers can optimize their laser welding processes to meet their application needs while ensuring high-quality, efficient, and reliable welds.
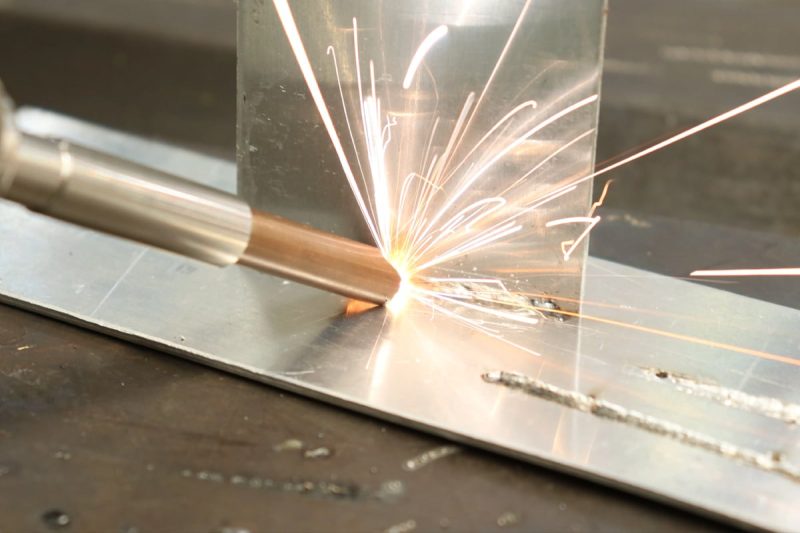
What Metals Are Compatible with Laser Welding?
Understanding the compatibility of different metals with laser welding allows for optimal welding quality, efficiency, and performance. The following is an overview of metals commonly welded using laser welding processes:
Carbon Steel
Carbon steel is one of the most widely used metals in manufacturing because of its affordability, versatility, and strength. Laser welding is highly compatible with carbon steel, allowing precise control of welding parameters and producing strong and durable joints. Applications for laser welding carbon steel components span a variety of industries, including automotive, construction, and machine manufacturing.
Stainless Steel
Stainless steel is prized for its corrosion resistance, aesthetics, and mechanical properties, making it a popular choice for applications that require durability and hygiene. Laser welding is particularly suitable for joining stainless steel because it produces clean, precise welds with minimal distortion and heat-affected zones. From food processing equipment to medical devices, laser-welded stainless steel components are ubiquitous in modern manufacturing.
Aluminum
Aluminum and its alloys are valued for their lightweight properties, high strength-to-weight ratio, and excellent thermal conductivity. Laser welding provides an efficient method of joining aluminum components, providing strong, beautiful welds with minimal distortion. Applications for laser welding aluminum range from aerospace and automotive parts to consumer electronics and building structures.
Titanium
Titanium is prized for its exceptional strength, corrosion resistance, and biocompatibility, making it the material of choice for aerospace, medical and marine applications. Laser welding is ideal for joining titanium alloys, allowing precise control of heat input and minimizing the risk of contamination. Laser-welded titanium components are integral to critical applications such as aircraft structures, medical implants, and marine equipment.
Copper and Brass
Copper and brass alloys are valued for their electrical, thermal, and decorative properties, making them important materials in electronics, plumbing, and the decorative arts. While laser welding of copper and brass presents challenges due to their high reflectivity and thermal conductivity, specialized techniques such as pulse shaping and wavelength optimization can successfully weld these materials. Laser welding of copper and brass components can be used in electrical connectors, heat exchangers, and architectural decoration.
Nickel Alloy
Nickel alloys have excellent corrosion resistance, high-temperature strength, and oxidation resistance and are suitable for demanding applications in aerospace, chemical processing, and power generation. Laser welding provides precise control of the welding process, enabling the production of high-quality welds in nickel alloys with minimal distortion and metallurgical changes. Laser welding of nickel alloy components is integral to critical applications such as gas turbines, chemical reactors, and nuclear power plants.
Taken together, laser welding technology offers a versatile and effective way to join a variety of metals, from carbon and stainless steel to aluminum, titanium, copper, brass, and nickel alloys. By understanding the unique properties and welding characteristics of each metal, manufacturers can utilize laser welding processes to produce high-quality, reliable welds based on the specific requirements of their application.
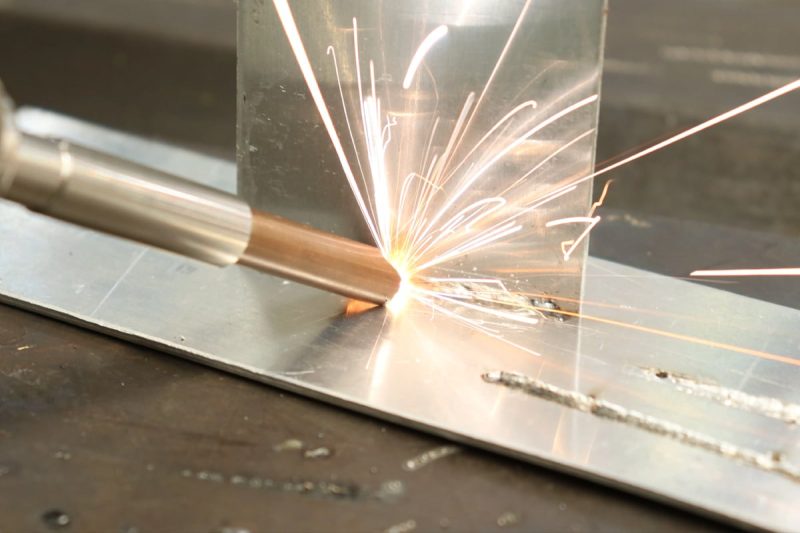
Applications of Laser Welding In Various Industries
Laser welding technology is widely used in various industries because of its precision, efficiency, and versatility. The following is a detailed introduction to the application of laser welding in key areas:
Automobile Industry
In the automotive industry, laser welding plays a vital role in vehicle production, enabling complex parts to be manufactured with high precision and efficiency. Laser welding is used to join body panels, chassis components, exhaust systems, fuel tanks, and engine components. Laser welding produces strong, durable welds with minimal heat-affected zones, making it ideal for automotive applications where structural integrity, weight reduction, and aesthetics are important.
Electronic Manufacturing
Laser welding is widely used in electronics manufacturing to assemble parts with precision features and tight tolerances. It is used to connect electronic housings, connectors, sensors, and microelectronic devices. Laser welding allows precise control of heat input, resulting in clean, beautiful welds without damaging sensitive electronic components. Its non-contact nature also minimizes the risk of contamination, making it ideal for cleanroom environments.
Medical Equipment
The medical device industry relies on laser welding to manufacture implants, surgical instruments, diagnostic equipment, and medical device housings. Laser welding can produce small, complex welds with minimal thermal distortion, making it ideal for assembling microscopic components used in medical devices. In addition, laser welding also has the advantage of biocompatible welding on materials such as titanium and stainless steel, ensuring compatibility with the human body.
Aerospace and Defense
In the aerospace and defense sectors where reliability, performance, and safety are critical, laser welding is widely used to join critical components in aircraft, spacecraft, missiles, and defense systems. Laser welding is used to weld airframe structures, engine components, fuel tanks, landing gear, and weapons systems. Its ability to produce high-strength welds with minimal weight loss makes it indispensable for aerospace applications where weight reduction and fuel efficiency are key priorities.
In addition to these industries, laser welding is also used in areas such as shipbuilding, energy, jewelry manufacturing, and consumer goods production. Its versatility, precision, and ability to weld a variety of materials make it a versatile and indispensable technology in modern manufacturing. As advances in laser technology continue to drive improvements in speed, efficiency, and capabilities, laser welding applications are expected to expand further, bringing new possibilities to different industries.
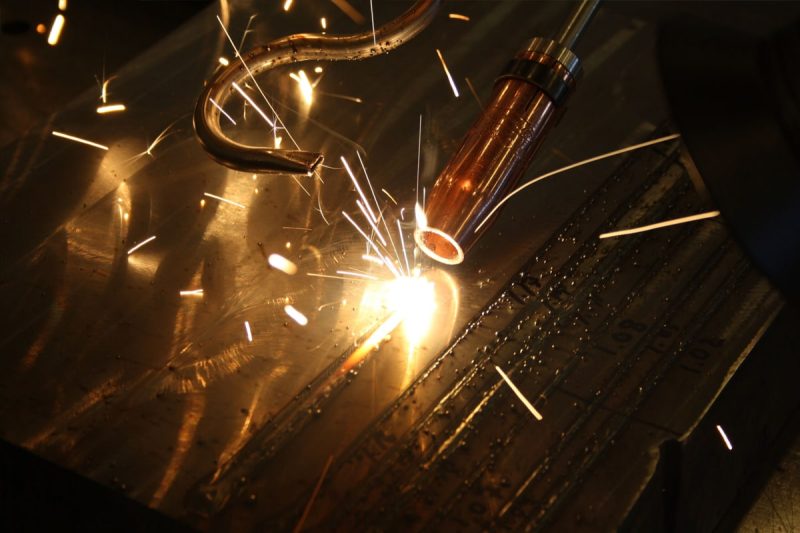
Common Hazards Associated with Using Laser Welding Machines
While laser welding machines offer many advantages, the potential hazards associated with their operation must be recognized and mitigated. The following is an overview of common hazards associated with using laser welding machines:
Optical Radiation
Laser welding machines emit high-intensity optical radiation in the form of laser beams, which can cause serious eye damage and skin burns if not properly controlled or shielded. Direct or indirect exposure to laser beams may cause permanent damage to the eyes and skin. Therefore, it is critical to implement appropriate laser safety measures, including the use of protective eyewear, enclosures, and interlocks, to minimize the risk of optical radiation hazards.
Heat and Smoke
Laser welding generates intense heat that causes materials to melt and vaporize, creating dangerous fumes, vapors, and particles. Inhaling welding fumes and exposure to high temperatures can pose health risks to operators, including respiratory irritation, lung damage, and heat-related illnesses. Proper ventilation, exhaust systems, and personal protective equipment (PPE) such as respirators and heat-resistant clothing can effectively mitigate heat and smoke hazards in laser welding environments.
Electrical Hazards
Laser welding machines require electricity to operate, and if not properly installed, grounded, and maintained, they present the risk of electrocution, electrocution, and fire. Electrical hazards may result from incorrect wiring, damaged electrical components, or improper handling of electrical connections. Regular inspection, maintenance, and compliance with electrical safety standards can serve as preventive measures to prevent electrical accidents and ensure the safe operation of laser welding equipment.
Fire Hazard
The strong heat generated during laser welding can ignite flammable materials such as dust, gas, lubricants, and combustible workpiece materials, causing fires and explosions. Additionally, sparks and hot particles generated during welding may pose an ignition hazard to the surrounding environment. Implementing fire prevention measures, such as removing combustible materials, keeping work areas clean, and installing fire detection and suppression systems, can help minimize fire hazards in laser welding operations.
Mechanical Hazards
Laser welding machines contain moving parts such as robotic arms, workpiece manipulators, and tooling fixtures that can create mechanical hazards if not properly guarded or controlled. Accidental contact with moving parts or pinch points can result in crushing injuries, cuts, or amputation. Implementing machine guarding, safety interlocks, and operator training programs can help mitigate mechanical hazards and ensure the safe operation of laser welding equipment.
In summary, by implementing appropriate safety measures, training programs and risk assessments, manufacturers can minimize the risks associated with laser welding operations and create a safe work environment for all involved.
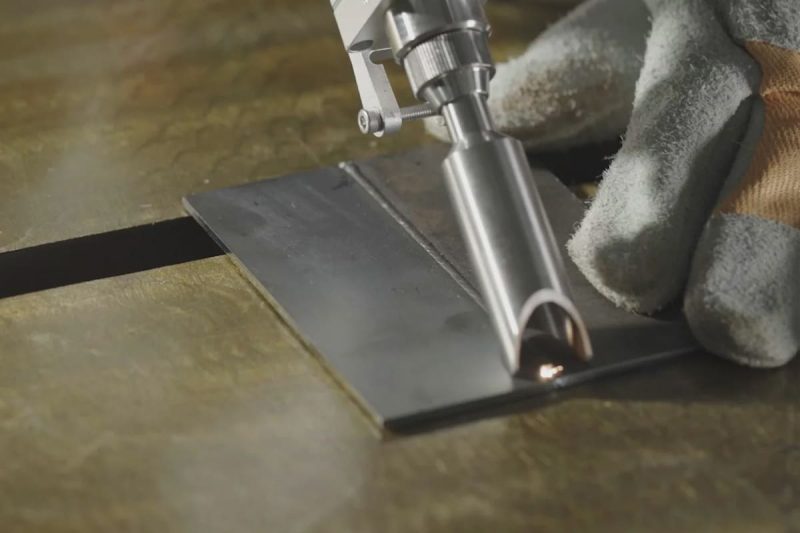
The Use of Welding Wire In Laser Welding
Laser welding is a versatile and precise joining method with many advantages, including high speed, minimal distortion, and excellent weld quality. While laser welding is typically performed without filler material, the use of welding wire can enhance the process and expand its suitability for certain applications. The following is an overview of the use of welding wire in laser welding:
Filler
Welding wire, also called filler wire or filler rod, is a consumable material used to add additional material to the weld during the welding process. In laser welding, filler wire is usually fed into the welding area manually or via an automated wire feed system. Adding filler material can help fill gaps between workpiece edges, improve joint strength, and control weld bead geometry.
Alloy Compatibility
The welding wire is selected to achieve the required welding characteristics and ensure compatibility with the welding base metal. Welding wires are available in a variety of compositions and alloys to match the properties of base metals such as carbon steel, stainless steel, aluminum, titanium, and nickel alloys. Matching the composition and properties of the welding wire to those of the base metal is an important prerequisite for producing high-quality welds with uniform mechanical properties.
Control Weld Geometry
Laser welding applications require precise control over the welding geometry, and using welding wire helps achieve the desired welding profile and size. By adjusting the feed rate and positioning of the welding wire relative to the laser beam, operators can control the size, shape, and depth of penetration of the weld bead. This level of control is particularly beneficial for applications that require consistent weld size and aesthetics, such as decorative welds in automotive body panels or trim components.
Gap Bridging and Joint Tolerances
Where there are variations in fit, joint alignment, or gap tolerances between workpiece edges, welding wire can be used to bridge gaps and compensate for dimensional differences. Adding filler material helps ensure complete penetration and fusion of the joint, even in situations where a perfect fit is not possible. This feature is beneficial for welding dissimilar materials, joining parts with complex geometries, or repairing worn or damaged parts.
Process Optimization
The use of welding wire in laser welding can also promote process optimization and efficiency improvements. By adding a filler material to control deposition rate and heat input, operators can fine-tune welding parameters for optimal weld quality, productivity, and material utilization. Additionally, using welding wire increases overall process reliability by reducing the likelihood of welding defects such as lack of fusion, lack of penetration, or undercuts.
In summary, although laser welding is typically performed without filler material, the use of welding wire can provide many benefits in terms of welding control, joint quality, and process optimization. By selecting the appropriate welding wire and adjusting wire feed parameters, manufacturers can enhance the capabilities of laser welding technology and expand its applicability across a wide range of industries and applications.
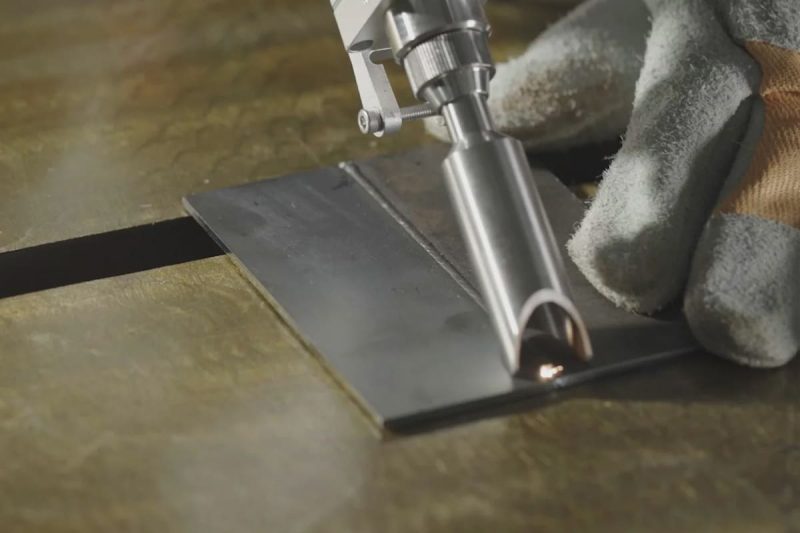
Laser Welding Care and Maintenance
Maintaining your laser welding machine is critical to ensuring optimal performance, reliability, and longevity. Regular maintenance and service procedures help prevent breakdowns, minimize downtime, and extend the life of critical components. The following is an overview of key maintenance tasks for laser welding machines:
Regular Cleaning
Regular cleaning prevents laser welding machine contamination, maintains optical clarity and ensures consistent performance. Cleaning procedures may include using a lint-free cloth and an appropriate cleaning solution to remove dust, dirt, and debris from optical components such as lenses, mirrors, and protective windows. In addition, cleaning of the workpiece fixture, machine housing, and surrounding work area helps maintain a clean and safe operating environment for laser welding operations.
Alignment Check
Proper alignment of optics is critical to achieving precise beam delivery and consistent weld quality in laser welding. Regular inspection of optical alignment ensures that the laser beam is properly focused and directed onto the workpiece, minimizing beam divergence and energy loss. Alignment checks may involve using an alignment tool, laser alignment system, or laser beam profiler to verify the alignment of the laser optics and make any necessary adjustments to optimize performance.
Cooling System Maintenance
Laser welding machines rely on cooling systems to dissipate the heat generated during operation and maintain stable operating temperatures of key components such as laser sources, optics, and power supplies. Regular cooling system maintenance, including checking coolant levels, inspecting hoses and fittings for leaks or damage, and cleaning coolant filters and heat exchangers, can help ensure effective heat dissipation and prevent overheating-related problems.
Calibration
Calibration of laser welding machines helps maintain the accuracy of welding parameters such as laser power, pulse duration, beam quality, and focus size. Regular calibration checks using calibrated instruments, reference standards, or built-in calibration procedures can help verify the accuracy of machine settings and ensure compliance with specified tolerances. Calibration intervals may vary based on the level of use, environmental conditions, and manufacturer’s recommendations.
Routine Inspection
Routine inspections of your laser welding machine can help detect potential problems, wear, or damage before they escalate into expensive repairs or downtime. Inspections may include visual inspection of machine components such as cables, connectors, motors, and bearings for signs of wear, corrosion, or fatigue. Additionally, monitoring system performance metrics such as laser output power, beam quality, and process stability can help detect deviations from normal operation and trigger corrective actions as needed.
In summary, by implementing a proactive maintenance program that includes regular cleaning, alignment checks, cooling system maintenance, calibration, and routine inspections, manufacturers can maximize the efficiency and longevity of their laser welding equipment while minimizing unplanned downtime and the risk of expensive repairs
Summarize
Taken together, this comprehensive guide to laser welding machines provides a comprehensive exploration of the features, benefits, applications, and maintenance considerations of this transformative technology. From precision and efficiency to versatility and reliability, laser welding machines offer unparalleled advantages to industries as diverse as automotive, electronics, medical devices, aerospace, and more. By understanding the fundamentals, potential hazards, and best practices associated with laser welding, manufacturers can harness the full potential of this advanced technology to drive innovation, optimize production processes, and achieve superior weld quality. Whether you are a seasoned industry professional or new to laser welding technology, this guide serves as a comprehensive resource for you to master the intricacies of laser welding machines and unlock new possibilities in modern manufacturing.
Driven by evolving technologies and industry rules, the versatility of laser welding equipment will continue to improve, bringing a more efficient and reliable production environment to the industrial manufacturing field. Only by comprehensively utilizing the various advantages of laser welding machines and flexibly maintaining them according to specific needs can we maximize the production efficiency of laser welding. If you are considering laser welding, please contact AccTek Laser and we will come up with the best option for your needs.
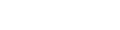
Contact information
- [email protected]
- [email protected]
- +86-19963414011
- No. 3 Zone A, Lunzhen Industrial Zone,Yucheng City , Shandong Province.
Get Laser Solutions