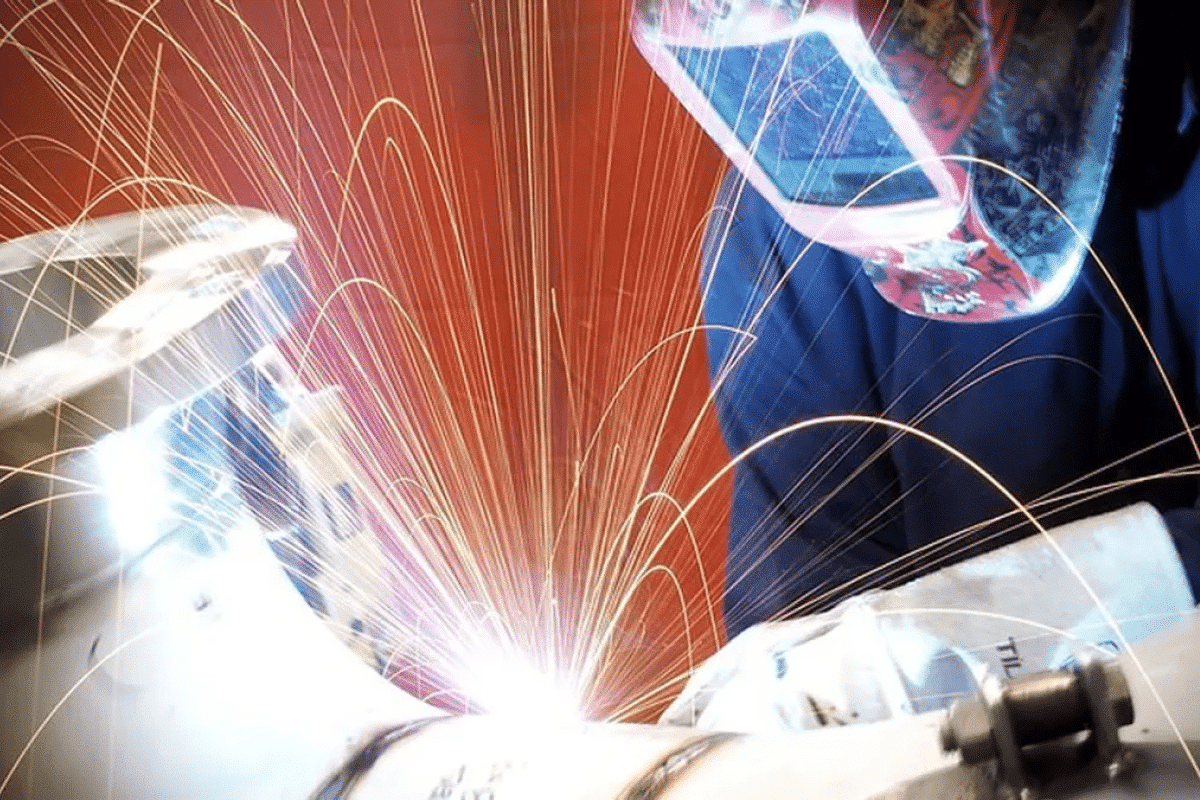
Laser Welding: Material Selection And Limitations
Laser welding is a new industrial technology in industrial welding processing. It has the advantages of fast welding speed, high precision, high efficiency, and smooth and beautiful welds. Laser welding machines are widely used and can weld a variety of materials. But which materials cannot be used with laser welding machines? This article will discuss the material selection and limitations of laser welding, explore the types of materials that laser welding can weld and the materials that are not suitable for laser welding, and analyze the reasons in depth.
Table of Contents
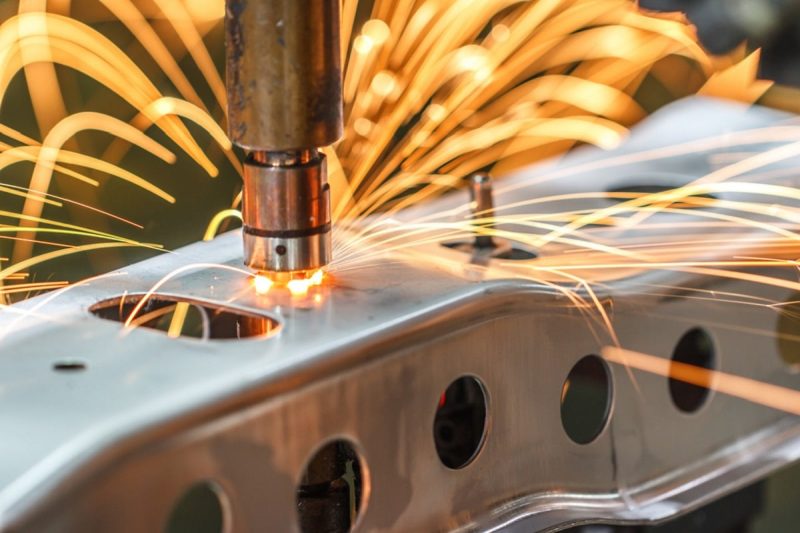
Basic principles of laser welding
Before delving into suitable materials for laser welding, it is necessary to understand the basic principles of laser welding. Laser welding is a welding method that uses the high energy of a laser beam to locally heat the surface of the workpiece to melt it instantly and form a welded joint after solidification.
The basic steps of laser welding include the generation, modulation, and focusing of the laser beam. First, the laser generator generates an extremely intense laser beam, and then the laser beam is modulated and focused through the optical system so that it can accurately illuminate the welding area. In the welding area, the high energy density of the laser quickly heats the workpiece surface above the critical temperature, causing it to melt instantly to form a molten pool. The molten pool then cools and solidifies, forming a strong weld.
It is a new welding method mainly used for welding thin-walled materials and precision parts. It can achieve welding effects such as spot welding, stack welding, and seal welding. This welding method has the characteristics of small weld width, small heat-affected zone, fast welding speed, beautiful appearance, and no need for post-weld processing. But this also puts forward certain requirements for the selection of materials.
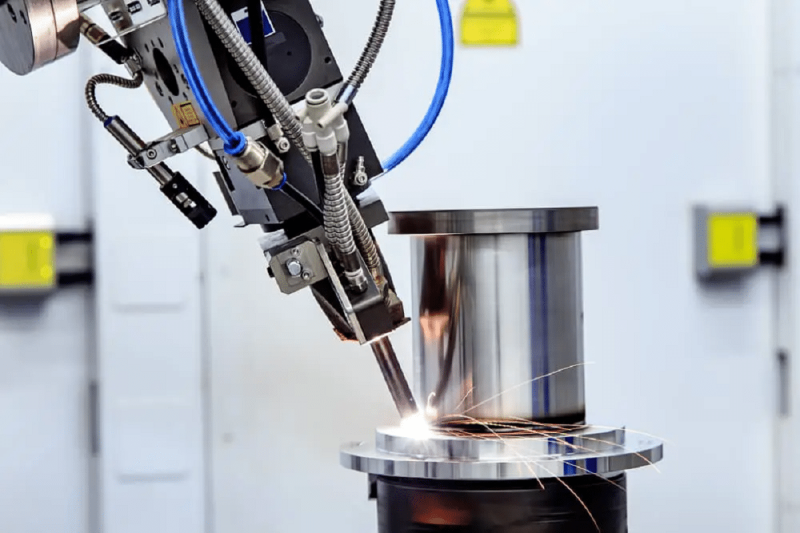
Materials that can be welded by laser
Lasers can weld many different types of materials together. Compared with traditional thermal welding or electric welding methods, it has a wider range of applications and can weld a variety of metal and non-metal materials. Mainly include the following categories:
Metal materials
Laser welding is widely used in the welding of metal materials and is suitable for a variety of metal materials, including but not limited to the following categories:
Stainless steel
Due to the welding speed and small heat-affected zone of the laser welding machine, the overheating phenomenon and large linear expansion coefficient of stainless steel welding are alleviated, and the welding seam has no defects such as pores and inclusions. Compared with carbon steel, stainless steel is easier to obtain deep-penetration narrow welds due to its low thermal conductivity, high energy absorption rate, and high melting efficiency. Welding thin plates with a low-power laser welding machine can produce well-formed joints with smooth and beautiful welds.
Aluminum alloy
Aluminum and aluminum alloys are highly reflective materials with good thermal conductivity, and laser welding can achieve efficient welding. When welding aluminum and its alloys, as the temperature rises, voids may appear in the root and the weld bead may be poorly formed. Laser welding can effectively reduce the heat-affected zone and avoid material deformation and cracks.
Titanium alloy
Titanium alloys are also one of the ideal choices for laser welding due to their high strength and corrosion resistance. Laser welding enables high-quality welds without destroying the properties of titanium alloys.
Non-metallic materials
Laser welding is not only suitable for metallic materials, but can also be used to weld some non-metallic materials, especially in applications with high precision and low thermal impact. The following are some non-metallic materials that laser welding can weld:
Plastic
Laser welding excels in welding plastic materials. This welding method can be used on polymers, thermoplastics and thermosets and is widely used in the manufacture of medical devices, electronics and automotive parts.
Ceramic
Laser welding can be used to weld ceramic materials, including alumina ceramics and zirconia ceramics. This has important applications in electronics, optics and aerospace, as laser welding offers the advantages of high precision and no contact.
Rubber and elastic materials
For some non-metallic materials with good elasticity, laser welding can also be considered. This may have applications in special areas such as the manufacturing of medical devices and flexible electronic devices.
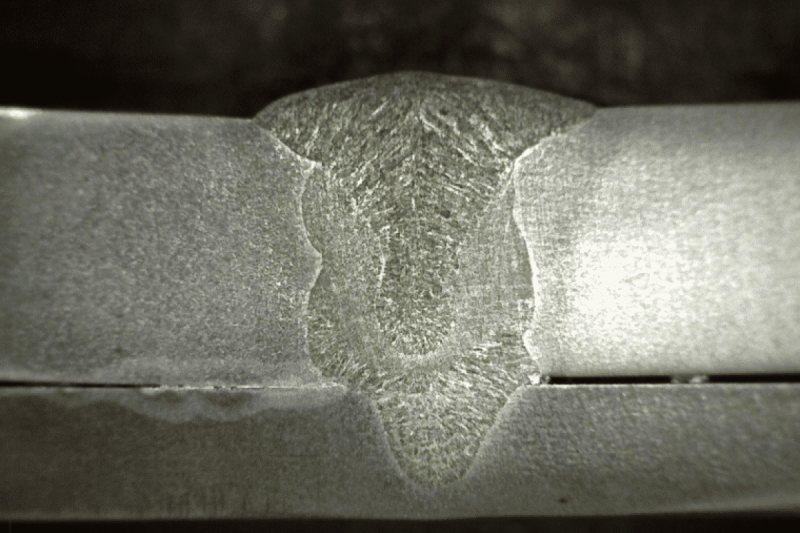
Materials that cannot be laser welded
However, it is worth noting that not all materials are suitable for laser welding. Here are some materials that laser welding generally cannot weld effectively:
Highly reflective materials
Laser welding relies on the high energy of the laser beam to heat the material surface. Therefore, for highly reflective materials, the laser beam may be reflected and cannot be effectively heated, making welding difficult. Typical highly reflective materials include copper and copper alloys. Problems of lack of fusion and penetration may occur after processing. Therefore, concentrated energy, high-power heat sources and preheating measures are required.
Transparent material plastic
Laser welding is not suitable for welding transparent materials because the laser beam cannot produce sufficient absorption in highly transparent materials. This includes glass and some plastics.
Temperature sensitive materials
Some materials with high temperature sensitivity, such as thermoplastics, may be affected by excessive heat in the high-temperature environment of laser welding, resulting in a decline in material performance.
Highly reflective metallic coating
Some materials are covered with highly reflective metal coatings, which can cause the laser beam to be reflected and unable to effectively heat the substrate.
Highly hygroscopic materials
Laser welding requires a relatively dry environment, and for materials that are highly hygroscopic, moisture may be interfered with during the welding process.
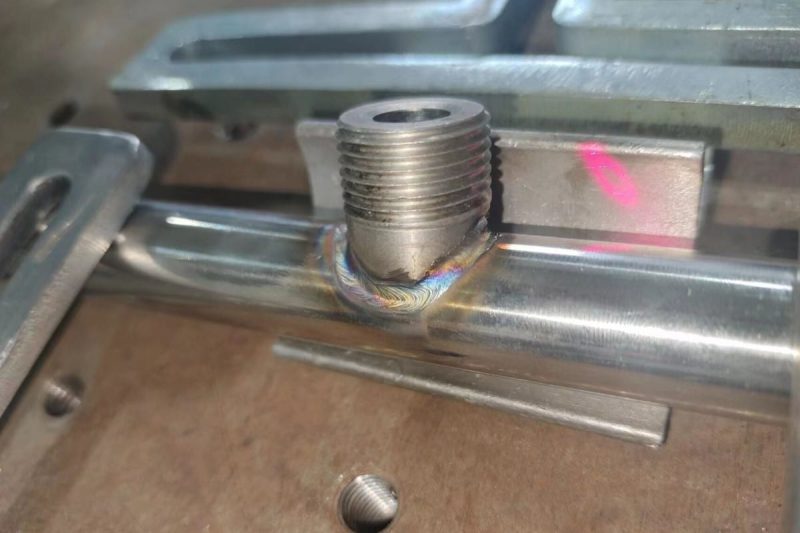
What factors determine the weldability of a material?
The weldability of laser welding is affected by many factors, mainly covering the thermal properties, optical properties, chemical properties, and physical properties of the material. The following is a detailed description of these factors from these four aspects:
Optical properties of materials
- Absorption coefficient: The ability of a material to absorb a laser beam depends on its absorption coefficient. A high absorption coefficient means the material is more easily heated by the laser beam, which facilitates welding.
- Transparency: Materials with high transparency are usually not suitable for laser welding because it is difficult for the laser to produce sufficient absorption in transparent materials. Materials should have high absorptivity, low reflectivity, and transmittance to ensure efficient and stable welding
Thermal properties of materials
- Melting point and boiling point: The melting point and boiling point of the material directly affect the suitability of laser welding. A lower melting point facilitates laser welding, making it easier to melt materials instantly.
- Thermal conductivity: Thermal conductivity affects the rate of heat transfer in the welding area. Higher thermal conductivity may cause the weld to cool too quickly, causing cracks or deformation.
Chemical properties of materials
- Oxidation: Highly oxidizing materials may form oxides during the welding process, affecting the quality of the weld. When selecting materials suitable for laser welding, consider their oxidation properties.
- Chemical reaction: Whether the material will undergo chemical reaction at high temperatures, especially interacting with gases in the welding environment, may affect the quality of the weld.
Physical properties of materials
- Coefficient of expansion: The thermal expansion coefficient of a material affects thermal deformation during welding. Matching welding materials and processes can reduce the risk of deformation.
- Hardness: The hardness of the material will affect the formation and solidification process of the molten pool during laser welding, which may affect the welding quality.
Taking the above factors into consideration, the suitability of laser welding for a specific material can be more accurately assessed. In practical applications, a comprehensive analysis of these factors helps to select appropriate welding parameters and processes to ensure the efficiency of laser welding and weld quality.
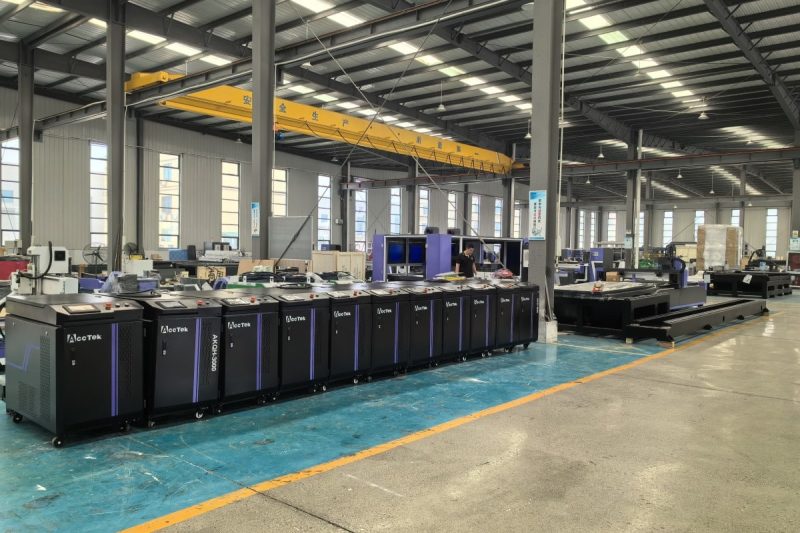
Challenges and application directions of laser welding
Although laser welding has achieved remarkable success in many fields, it still faces some challenges in the future that may affect its application scope and effectiveness. The following are the challenges that laser welding technology may face:
Material adaptability
- Reflective materials: For highly reflective materials, such as aluminum and copper, it is difficult for laser welding to effectively heat the surface, making welding difficult.
- Transparent materials: It is difficult for the laser beam to produce sufficient absorption in transparent materials, making laser welding of transparent materials challenging.
Process Control
- High-temperature gradient: The high-temperature gradient produced by laser welding may cause thermal deformation and residual stress in the welding area, affecting the welding quality.
- Weld seam control: For welding of complex shapes, laser welding faces certain challenges in precise control of the weld seam.
Cost and equipment complexity
- Equipment cost: Laser welding equipment is relatively expensive to acquire and maintain, which can be a limiting factor in some applications.
- Complexity: Laser welding systems often require highly complex equipment and process control, and require high operator skills.
Production efficiency
- Production speed: For some large-scale production situations, laser welding may not be as fast as other traditional welding methods, limiting its application in high-volume environments.
Development of high-energy laser sources
- The quality and efficiency of laser welding are affected by the power of the laser source. More powerful, stable, and reliable high-energy laser sources are needed in the future to increase welding speed and depth and accommodate a wider range of materials.
Environmentally friendly
- Modern manufacturing is increasingly focused on environmental sustainability, so laser welding technology needs to reduce waste generation, energy consumption, and negative environmental impact during the process.
Summarize
Laser welding is a process that can weld materials of different properties and thicknesses. The weldability of a material depends on its optical, thermal, and chemical properties. It is suitable for welding a variety of metal and non-metal materials and has the characteristics of high efficiency and precision. However, it is still affected by material properties, and there are certain limitations for some specific materials. With the continuous development of laser technology, it is believed that laser welding will have wider applications in the future and overcome more material challenges.
AccTek Laser is a trusted partner for those looking for reliable, advanced laser welding solutions. Our cutting-edge laser welding machines are designed to meet the diverse needs of the industry, delivering precision and efficiency for a variety of materials. Our team of experts is ready to provide assistance and guidance, ensuring laser welding technology is seamlessly integrated into their manufacturing process. Please feel free to contact AccTek Laser for a consultation and to experience the future of laser welding technology.
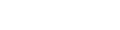
Contact information
- [email protected]
- [email protected]
- +86-19963414011
- No. 3 Zone A, Lunzhen Industrial Zone,Yucheng City , Shandong Province.
Get Laser Solutions