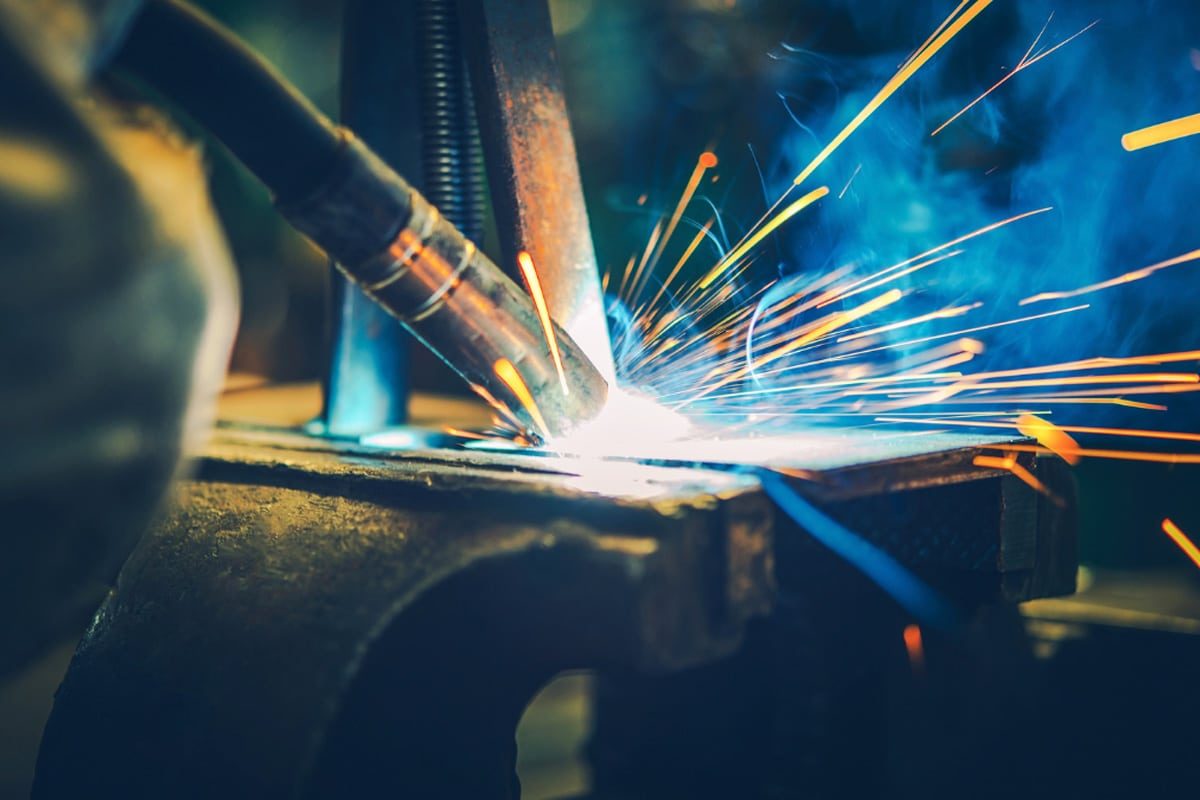
Laser Welding of Dissimilar Materials Guide
In modern manufacturing, the demand for welding dissimilar materials is growing rapidly. With the diversification of material types, welding technology is facing unprecedented challenges, especially in high-precision industries such as automobiles, aerospace, and electronic equipment. The welding of dissimilar materials requires not only high strength and high durability but also compatibility issues between different materials. These problems are usually reflected in the differences in the physical properties, chemical composition, melting temperature, thermal expansion coefficient, etc. of the materials. Therefore, when welding dissimilar materials, heat input, welding parameters and the selection of filler materials must be precisely controlled.Laser welding machines, as a high-energy density and high-precision welding technology, has become an ideal choice for welding dissimilar materials because it can achieve efficient and accurate heat input and a narrow heat-affected zone.
However, despite the many advantages of laser welding technology, welding dissimilar materials still faces certain challenges, especially when the physical and metallurgical properties of the materials are quite different. The thermal expansion behavior, melting temperature, and compatibility of the filler materials between different materials may lead to cracks in the welding area, the formation of brittle compounds, and a decrease in the strength of the welded joint. Solving these problems requires precise control of the laser welding process and a reasonable selection of laser parameters, filler materials, and welding technology. Therefore, although laser welding provides a new solution for the welding of dissimilar materials, its successful application still needs to consider many key factors.
Table of Contents
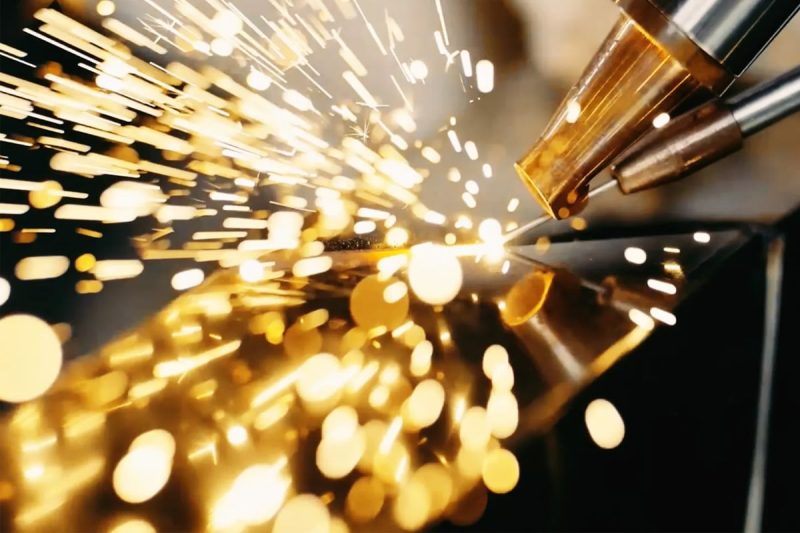
Challenges of Welding Dissimilar Materials
The process of welding dissimilar materials often comes with its own set of challenges. Differences in the physical properties of different materials, metallurgical incompatibilities, and the complexity of weld designs can all have a significant impact on weld quality and performance. Here are the most common challenges when welding dissimilar materials.
Differences in Physical Properties
- Thermal conductivity: One of the main challenges when welding dissimilar materials is the difference in thermal conductivity. Different materials have different thermal conductivity properties, which means that the speed and range of heat propagation in the materials will be different. For materials with poor thermal conductivity, such as certain high-alloy metals, the temperature of the welding area may be concentrated at a certain point, resulting in local overheating or uneven melting. This uneven temperature distribution not only affects the quality of the welded joint but can also cause stress concentration and structural weakening.
- Melting temperature: Different materials have different melting temperatures, and this difference can have an impact during the welding process. In the welding of dissimilar materials, the material with a low melting point may melt prematurely, while the material with a high melting point has difficulty reaching a suitable temperature for welding. At this time, the low melting point material may over-melt, while the high melting point material fails to form a suitable joint, affecting the firmness and reliability of the weld.
- Thermal expansion coefficient: Different materials have different thermal expansion coefficients, which means that they expand or contract at different rates during heating or cooling. When two materials are welded together, the difference in thermal expansion coefficients can cause stress in the weld joint area. This stress may cause cracks or deformation in the joint during the welding process, affecting the stability and durability of the welded structure.
Metallurgical Incompatibility
- Formation of brittle intermetallic compounds: When two metallic materials are welded, metallurgical incompatibilities often result in the formation of brittle intermetallic compounds in the area of the welded joint. The formation of these compounds is often caused by the atomic structure and chemical reactions of different metals, and they are often weaker than the parent metal. Brittle intermetallic compounds can significantly reduce the strength and toughness of welded joints, thereby affecting the overall performance of the weld.
- Difficulty Achieving Strong and Durable Welds: Due to the brittleness of intermetallic compounds, it is difficult to achieve a weld with both strength and toughness when welding dissimilar materials. Even during the welding process at high temperatures and pressure, the weld may crack, fall off, or have other defects due to factors such as thermal stress, excessive cooling rate, or metallurgical incompatibility, thus affecting the durability and stability of the welded structure.
Joint Design Considerations
- Installation and compatibility issues: When welding dissimilar materials, it is not only necessary to consider the selection of appropriate welding technology and materials, but also to pay attention to the installation and compatibility of the materials. The differences in stress distribution and thermal expansion behavior of dissimilar material welded joints may cause uneven stress or deformation in the joint area, affecting the stability and connection quality of the welded joint. In addition, the surface morphology, size of the materials, and their positional relationship during the assembly process will have an important impact on the welding effect.
- Choosing the right filler material and welding technology: To overcome the challenges when welding dissimilar materials, it is crucial to choose the right filler material and welding technology. The chemical composition, melting temperature, and thermal expansion coefficient of the filler material need to match the parent material to ensure the strength, toughness, and durability of the welded joint. Metallurgical incompatibility and physical differences between different materials may require special welding methods such as laser welding, laser-arc hybrid welding, etc., to more accurately control the heat input and welding quality.
In summary, although welding dissimilar materials can bring better functions and applications, it also faces many challenges. By deeply understanding these challenges and adopting appropriate welding techniques and methods, the welding quality can be effectively improved and the stability and durability of the welded joint can be ensured.
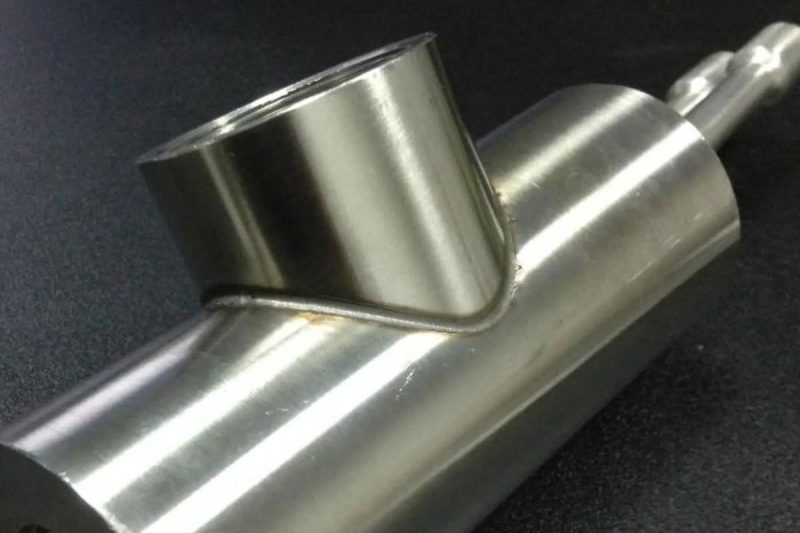
Advantages of Laser Welding of Dissimilar Materials
Although there are some challenges in welding dissimilar materials, laser welding has become an ideal technology to solve these problems due to its unique advantages. The following are several key advantages of laser welding dissimilar materials, demonstrating its wide application potential in modern manufacturing.
High Energy Density: The high energy density of laser welding allows it to release a large amount of heat energy in a very short time. This feature is particularly suitable for welding dissimilar materials because it effectively avoids excessive heat transfer to surrounding areas. High energy density can quickly heat the material to the melting point, thereby reducing the phenomenon of over-expansion or overheating of the weld area, which is important for applications that require precise control of heat input. Laser welding can ensure effective connection between materials with different melting temperatures and avoid welding defects caused by uneven heat distribution.
Precise Heat Input Control: Laser welding technology can precisely control the heat input. By adjusting the power, focus position, and scanning speed of the laser, the heat input can be maintained throughout the welding process. This advantage is particularly important for welding dissimilar materials because different materials have different thermal expansion and melting behaviors during welding. Precise control of heat input can reduce thermal stress and material deformation, and prevent cracks or uneven weld joints caused by thermal expansion differences.
Narrow Heat Affected Zone (HAZ): The heat-affected zone (HAZ) of laser welding is much smaller than that of traditional welding methods. The narrow heat-affected zone means that only the area near the joint will be affected by high temperatures during welding, avoiding thermal damage to a large area of material. For dissimilar materials, reducing the heat-affected zone helps reduce stress problems caused by the difference in thermal expansion between materials, and reduces the occurrence of cracks and deformation. A narrow HAZ also helps maintain the original properties of the material, especially in the welding of high-strength or brittle materials.
Fast welding speed and high efficiency: Laser welding is fast, which can significantly improve production efficiency, especially in the scene of welding a large number of dissimilar materials. Due to the high efficiency of laser welding, manufacturers can complete more welding tasks in a shorter time, which helps to reduce the production cost per unit product and shorten the production cycle. The high-speed welding process can not only increase production but also improve the efficiency of the overall workflow, especially for large-scale production or automated production lines.
Versatility and flexibility: Laser welding has extremely high versatility and flexibility, and can weld dissimilar materials of different thicknesses, shapes, and materials. This makes laser welding widely used in various complex production needs, whether it is metal or alloy, it can provide reliable welding solutions. Laser welding is not limited by material thickness or shape, and can easily cope with the welding needs of small precision components and large complex structures.
In addition, laser welding is capable of welding a variety of dissimilar material combinations, such as welding metal to plastic, or welding between different metal alloys. This flexibility not only increases the application range of welding but also allows manufacturers to process different material combinations on the same production line, thereby improving the versatility and flexibility of the production line.
Laser welding technology provides an ideal solution for welding dissimilar materials with its advantages such as high energy density, precise heat control, narrow heat-affected zone, high efficiency, and versatility. It can not only effectively overcome the physical and metallurgical challenges in welding dissimilar materials, but also improve welding quality, reduce production costs, and shorten production cycles. With the continuous advancement of laser technology, welding dissimilar materials is no longer a technical problem, but a challenge that can be efficiently solved. For manufacturers, the use of laser welding technology can greatly improve production efficiency and product quality, and meet the needs of modern manufacturing for precision and diversity.
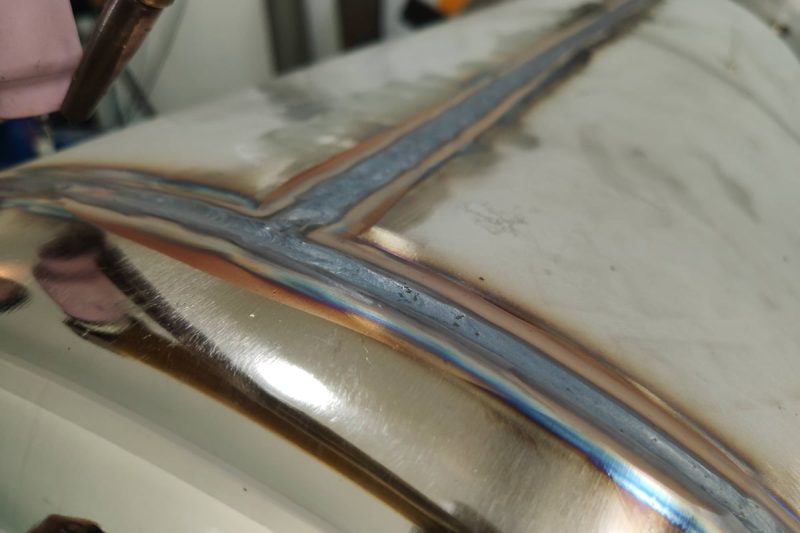
Key Considerations for Laser Welding Dissimilar Materials
In addition to understanding the benefits of laser welding, there are several key factors to consider when welding dissimilar materials:
Material Pairing and Compatibility
When choosing dissimilar materials for welding, compatibility must be considered, especially in terms of chemical composition, melting temperature, and thermal expansion coefficient. These factors directly affect the stability and quality of the weld.
- Chemical composition compatibility: Differences in the chemical composition of different materials may lead to the formation of unfavorable compounds or oxides during welding, thus affecting the welding quality. Appropriate filler materials need to be selected to avoid these adverse reactions.
- Melting temperature matching: Differences in the melting temperatures of dissimilar materials may lead to uneven heat distribution during welding, which in turn affects the welding effect. Controlling the temperature of the welding heat source to ensure that both materials can melt smoothly is the key.
- Thermal expansion coefficient difference: Different thermal expansion coefficients between materials can cause stress during welding and increase the risk of cracks. This problem can be alleviated by optimizing welding design and proper heat treatment.
- Alloy filler materials: For materials that are difficult to be compatible with, the use of alloy filler materials can help improve welding results and enhance the strength and durability of the weld.
- Welding process selection: Selecting a suitable welding process, such as laser welding, TIG welding, etc., can effectively reduce the incompatibility between materials and ensure a stable welding process.
By rationally selecting alloy filler materials, welding methods and controlling heat input, the stability and quality of welding of dissimilar materials can be effectively improved.
Optimal Laser Parameters
In laser welding, choosing the right laser parameters is the key to ensuring welding quality, especially when welding dissimilar materials. The following is a brief expansion of laser parameters:
- Laser power: Laser power directly affects the depth and width of the weld. When the power is too low, sufficient melting depth may not be achieved, resulting in incomplete welding; while too high power may cause overheating, burn-through, or material deformation. The different thermal conductivity and melting temperatures of dissimilar materials require precise adjustment of laser power to ensure uniform temperature in the weld area and avoid defects.
- Pulse frequency: Pulse frequency affects the heating and cooling rates of laser welding. Higher pulse frequencies are suitable for thinner materials, while lower frequencies are suitable for thicker materials. When welding dissimilar materials, the pulse frequency needs to balance the difference in thermal conductivity of the two materials to avoid cracks or joint weakening caused by too fast or too slow cooling.
- Scanning speed: Scanning speed affects heat input and welding quality. Too fast scanning speed may cause the molten pool to fail to fully fuse, resulting in incomplete welding; too slow may cause overheating, resulting in cracks in the joint area, or too large a heat-affected zone. Selecting the right scanning speed can ensure that heat is evenly distributed in the weld area.
- Focus position and spot size: The position of the laser focus determines the concentration of the heat source, affecting the accuracy and quality of welding. Focus positions that are too high or too low can affect welding results, resulting in overheating or incomplete melting. Correctly setting the focus and spot size helps achieve the ideal heat input, especially when welding different materials, which needs to be adjusted according to the material’s light absorption and thermal conductivity.
- Heat input control: The heat input during welding determines the quality and performance of the welded joint. Excessive heat input may cause excessive melting of the material, resulting in thermal cracks or deformation; while too low heat input may result in insufficient welding. By precisely controlling parameters such as laser power, scanning speed, and pulse frequency, heat input can be optimized to ensure welding quality.
- Choice of welding method: Different welding methods (such as pulsed laser welding or continuous laser welding) are suitable for different materials and applications. Pulsed laser welding can better control heat input, reduce overheating, and is suitable for welding heat-sensitive dissimilar materials.
In short, precise adjustment of laser welding parameters can ensure uniform temperature distribution in the welding area and avoid welding defects, especially when welding dissimilar materials. By adjusting factors such as laser power, pulse frequency, scanning speed, etc., the welding quality can be greatly improved and the strength and stability of the welded joint can be ensured.
Choice of Filling Material
Filler materials are very important when welding dissimilar materials. The right filler material can improve the strength, corrosion resistance, and wear resistance of the welded joint. The selection should be based on factors such as the composition, melting temperature, and thermal expansion coefficient of the welding material.
- Enhance welding strength: Suitable filler materials can improve the strength of welded joints, especially when welding dissimilar materials, to balance the strength differences between different materials and avoid welded joints being too fragile.
- Improve corrosion resistance: Selecting corrosion-resistant filler materials (such as nickel-based alloys, chromium alloys, etc.) can enhance the corrosion resistance of joints, especially for welding materials such as stainless steel and aluminum alloys.
- Improve wear resistance: For welded joints that need to withstand friction, the use of wear-resistant filler materials (such as hardened alloys) can extend the service life of the joints.
- Match the composition and temperature of the welding material: The filler material should match the composition and melting temperature of the parent material to ensure stability during the welding process and avoid defects caused by incompatibility.
To sum up, choosing the appropriate filler material can significantly improve the welding quality and ensure the performance of the joint in terms of mechanics, corrosion resistance, and wear resistance.
When laser welding dissimilar materials, material pairing and compatibility, optimization of laser parameters, and selection of filler materials are key factors to ensure welding quality and effect. Reasonable selection of compatible material combinations can improve the stability of the welding process and avoid welding defects; precise adjustment of laser parameters ensures uniform heat distribution to avoid overheating and poor welding; appropriate filler materials can enhance the mechanical properties and durability of the welded joint. Taking all these factors into consideration, high-quality welding of dissimilar materials can be achieved to meet the high standards of modern manufacturing.
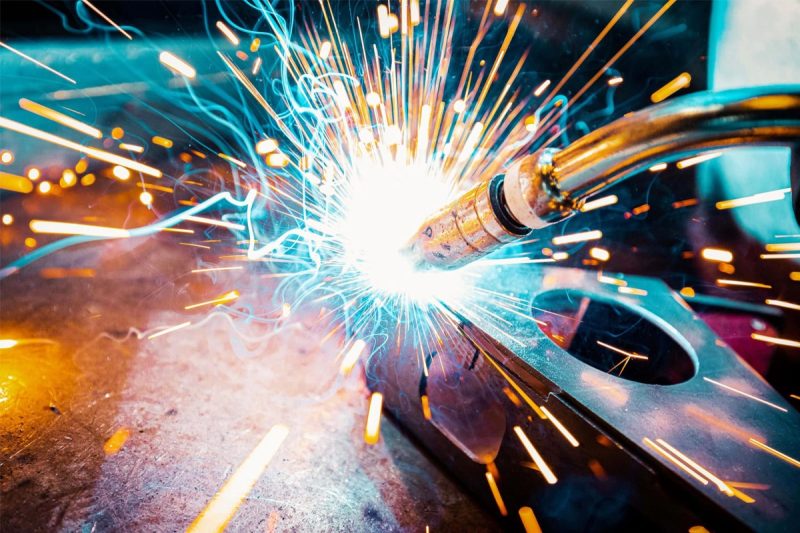
Summarize
Laser welding of dissimilar materials is an effective means to solve welding problems in modern manufacturing. Despite many challenges, such as physical property differences, metallurgical incompatibility, and design issues, laser welding can achieve high-quality and efficient welding due to its advantages such as high energy density, precisely controlled heat input, and narrow heat-affected zone. By rationally selecting materials, optimizing laser welding parameters, and filling materials, the difficulties of welding dissimilar materials can be overcome and the strength and reliability of welded structures can be improved.
If you are looking for professional laser welding solutions, AccTek Laser provides you with efficient and precise welding technology to help your production achieve more efficient process optimization. We provide customized laser welding equipment for customers in different industries. Please contact us for more details.
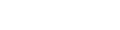
Contact information
- [email protected]
- [email protected]
- +86-19963414011
- No. 3 Zone A, Lunzhen Industrial Zone,Yucheng City , Shandong Province.
Get Laser Solutions