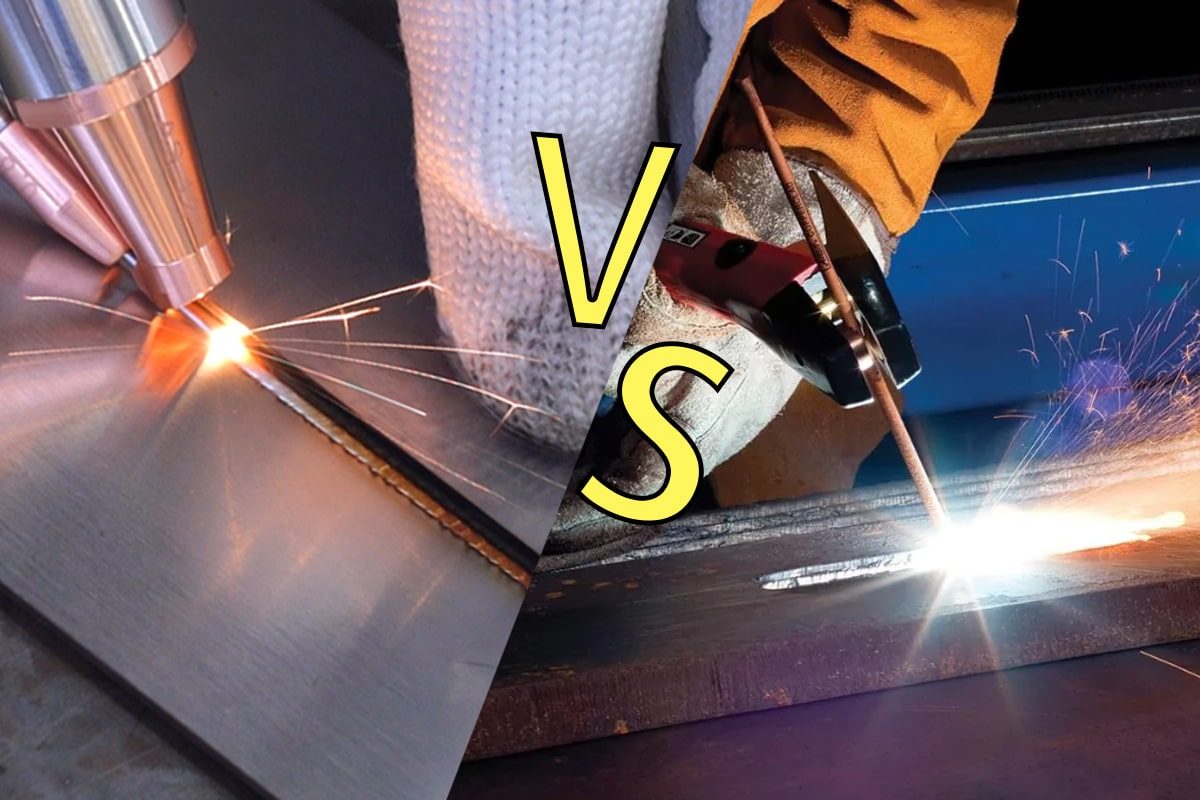
Laser Welding Vs Arc Welding
In modern manufacturing and industrial fields, welding technology plays a vital role. Different industries rely on welding processes to achieve efficient material connection and structural reliability of products. Among the many welding methods, laser welding and arc welding are the two most widely used technologies with their own characteristics. As the manufacturing industry continues to increase its requirements for precision, speed and material compatibility, it is particularly important to understand the advantages and disadvantages of these two welding processes.
As a high-energy-density precision welding technology, laser welding relies on a focused laser beam to quickly melt materials to achieve high-quality, low-deformation connections. Laser welding is widely used in high-end manufacturing fields such as automobiles, aerospace, and medical due to its excellent precision and speed, and is particularly suitable for welding thin plates and complex parts. In automated production lines, the contactless nature and high energy utilization of laser welding make it an ideal choice for improving production efficiency. Arc welding is a welding method with a long history, relatively simple operation, and affordable. Arc welding uses an arc generated by electric current to melt metal, and is suitable for welding from thin plates to heavy structures. It is favored because of its low equipment cost and flexible operation. However, arc welding has a large heat-affected zone, which is prone to material deformation, and its accuracy is not as good as laser welding.
Table of Contents
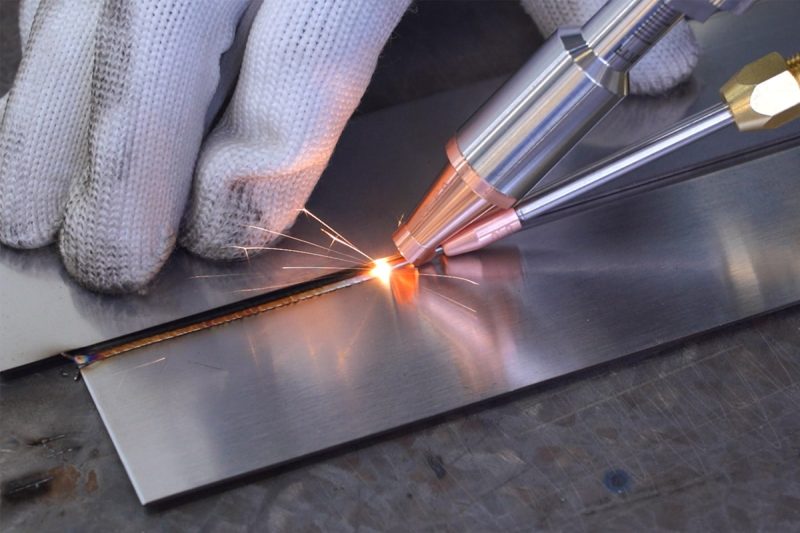
Laser Welding Overview
Laser welding is a high-precision, high-efficiency welding technology that uses a focused high-energy laser beam to locally melt and join metals or other materials together. Since the development of laser technology in the 1960s, laser welding has become one of the key processes in precision manufacturing, especially suitable for joining materials that require high strength and low deformation. Laser welding is widely used in the aerospace, automotive, medical device, and electronics industries, meeting the high requirements for precision and speed in these fields.
Laser Welding Principle and Process
The core principle of laser welding is to use the high-energy beam generated by the laser to irradiate the surface of the material and quickly heat it to the melting point or even the vaporization point. During the welding process, the beam emitted by the laser generator is focused by a lens or reflector, concentrating the energy in a very small area to form a high-energy density heat source. This high temperature can quickly melt the surface of the material, and precise welding operations can be achieved by controlling the movement and power of the laser. As the beam moves, the molten pool gradually cools and solidifies, forming a strong weld.
The laser welding process is generally divided into the following steps:
- Material preparation: Ensure that the surface of the material to be welded is clean, and remove oxides, oil, and other contaminants to avoid affecting the welding quality.
- Laser beam focusing: Use a lens or reflector to focus the laser beam on the welding area to ensure that the energy density is high enough.
- Molten pool formation: The laser beam irradiates the surface of the material, quickly heats, and melts to form a molten pool, and the molten pool gradually expands during the movement of the laser.
- Solidification and cooling: After the laser beam is removed, the molten pool cools to form a continuous weld.
Types of Laser Welding Technologies
Laser welding processes can be divided into two main types, depending on how the laser interacts with the material:
Laser Beam Welding
- This method is mainly used for shallow welding. The laser beam heats the surface of the material and melts it locally. Since the heat diffuses slowly and the molten pool is shallow, it is generally suitable for connecting thin materials or for scenes with high requirements on the appearance of the weld. Laser beam welding is suitable for welding precision electronic devices or thin-walled metal materials.
Laser Keyhole Welding
- Under high-energy laser irradiation, the material does not just melt on the surface. The powerful energy of the laser evaporates the metal and forms a small hole (called a “keyhole”) in the welding area. This small hole is deep and narrow, allowing the laser to penetrate deep into the material and transfer energy to the surrounding materials through multiple reflections. This technology is suitable for deep-penetration welding of thick materials and is widely used in industries such as automobiles, aviation, and shipbuilding that require high weld strength.
Advantages and Limitations of Laser Welding
Advantages of Laser Welding:
- High precision: Laser welding can accurately focus energy into a very small area, control the depth and range of welding, and achieve extremely high welding accuracy, which is particularly suitable for the processing of complex parts.
- Small heat-affected zone: Due to the high concentration of energy in laser welding, the heat-affected zone is small, which reduces material deformation and internal stress, thereby ensuring welding quality.
- Fast welding speed: Laser welding can complete welding in a very short time, greatly improving production efficiency, and is particularly suitable for large-scale automated production lines.
- Non-contact processing: Laser welding does not require direct contact with the workpiece, so it does not introduce external force or cause mechanical damage.
- Applicable to a variety of materials: In addition to traditional metal materials, laser welding can also be applied to non-metallic materials such as plastics and ceramics, with a wide range of applications.
Limitations of Laser Welding:
- High equipment cost: Laser welding equipment is complex, and the cost of laser generators, control systems, and auxiliary equipment is high, especially high-power laser systems, which may put economic pressure on small and medium-sized enterprises.
- High requirements for material surface: Laser welding has strict requirements on the cleanliness of the workpiece surface. Any oil, oxide or other impurities will affect the absorption efficiency of the laser and the welding quality.
- Suitable for thin materials or precision welding: Although laser welding can weld a variety of materials, it may not be as efficient as traditional welding processes on thick structural materials.
Application of Laser Welding in Various Industries
- Automobile manufacturing: Laser welding is widely used in the automobile industry, especially in body welding, door welding, and engine parts welding. Due to its high speed and high precision, it greatly improves the automation level of the production line. In addition, laser welding is also used to weld mixed metals, such as aluminum alloy and steel.
- Aerospace: In the aerospace field, welding materials often require lightweight and high strength. Due to its high precision and excellent weld quality, laser welding is widely used for aircraft and spacecraft structures, including turbine blades, engine casings, and other components.
- Electronics and microelectronics industry: Since laser welding can achieve precise welding of tiny areas and has a very small heat-affected zone, it has been widely used in the electronics industry, especially in microelectronics manufacturing. For example, the welding of small precision parts such as mobile phones, circuit boards, and battery packaging.
- Medical devices: Laser welding plays an important role in the manufacture of medical devices. It is used to weld precise and demanding metal instruments, such as surgical instruments, implants, and various stainless steel and titanium alloy devices.
- Energy industry: In the fields of new energy, solar energy, and battery manufacturing, laser welding is widely used because of its non-contact, high efficiency, and adaptability to a variety of materials, especially in the packaging and joining of new energy batteries.
Through the various technologies and advantages of laser welding, many industries have greatly improved production efficiency and welding quality, while making great progress in precision manufacturing and automation.
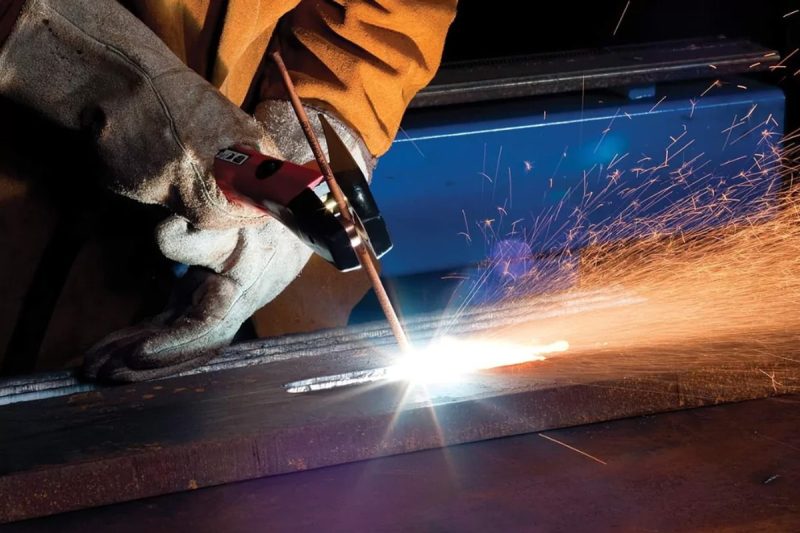
Arc Welding Overview
Arc welding is a method of melting metals and welding using the high temperatures generated by an electric arc. This welding method has a history of more than 100 years and has become one of the most widely used welding processes in industrial manufacturing after continuous development and improvement. Arc welding can process a variety of metal materials, from steel and stainless steel to alloy materials such as aluminum and copper, and occupies an important position in the fields of construction, shipbuilding, oil and gas, and heavy equipment manufacturing. Arc welding is popular for its simple equipment, flexible operation, and low cost.
Arc Welding Principle and Process
The basic principle of arc welding is to melt the metal on the electrode and the workpiece surface through the arc generated between the electrode and the workpiece to form a molten pool, thereby completing the welding. When the electrode approaches the workpiece, the current passes through the air to generate a high-temperature arc, which melts the metal in the local area of the electrode and the workpiece and forms a connection in the molten pool. As the arc moves, the molten pool gradually cools and solidifies into a solid weld.
The arc welding process usually includes the following steps:
- Arc generation: Bring the welding electrode close to the workpiece to form an arc between the electrode and the workpiece.
- Metal melting: The high temperature (up to 5000-6000℃) generated by the arc melts the metal to form a molten pool.
- Molten pool filling: The material of the electrode mixes with the molten metal on the surface of the workpiece to form a filler, which gradually fills the molten pool.
- Cooling and solidification: After the arc moves, the molten pool cools rapidly and solidifies into a weld.
- During the arc welding process, the control of welding parameters (such as current, voltage, welding speed) and welding posture determines the quality of the weld and the welding effect.
Types of Arc Welding Techniques
There are many types of arc welding technology. According to the use of welding electrodes and shielding gas, arc welding can be divided into many types. Some common types include:
Shielded Metal Arc Welding
Also known as manual welding or stick arc welding. A flux-coated electrode is used as an electrode. When the electrode melts, it forms a shielding gas and slag, isolating the oxygen and nitrogen in the air and preventing oxidation of the welding area. This technology is widely used in construction, maintenance, and structural steel welding, and is favored because of its simple equipment and strong portability.
MIG/MAG welding
Also known as MIG/MAG welding. A continuous feed wire is used as the electrode, and a protective gas (such as argon, or carbon dioxide) is sprayed through the nozzle during the welding process to isolate the air. This technology is suitable for automated welding and has a fast welding speed. It is widely used in automobile manufacturing, machinery, and pipeline welding.
Gas Tungsten Arc Welding
Also known as TIG welding, it uses a non-melting tungsten electrode to heat the workpiece through a high-energy arc while using an inert gas (usually argon) to protect the welding area. This method is suitable for precision welding and has high weld quality. It is often used for welding materials such as stainless steel, aluminum, and nickel, and is widely used in aerospace, medical equipment, and precision manufacturing.
Submerged Arc Welding
The welding is performed by using an electric arc under a granular flux, which forms a protective layer to isolate the air and provide some alloying elements to enhance the weld performance. This technology is often used for welding thick and heavy plates and is widely used in the manufacture of large structures, pipelines, and pressure vessels.
Advantages and Limitations of Arc Welding
Advantages of Arc Welding:
- Low equipment cost: Arc welding equipment is relatively simple, with low initial investment cost and economical maintenance cost, which is suitable for large-scale industrial applications.
- Flexible operation: Arc welding can adapt to a variety of welding positions and complex structures, and can be operated indoors, outdoors, or in confined spaces.
- Strong material compatibility: Arc welding can weld a variety of metals, including low carbon steel, stainless steel, aluminum, copper, etc., and has a wide range of applicability.
- Wide application: From thin plates to heavy structural materials, arc welding has strong adaptability in thickness and structural form, especially in heavy equipment and construction industries.
Limitations of Arc Welding:
- Large heat-affected zone: Arc welding has a large heat input, which can easily cause a wide heat-affected zone, which may cause deformation, cracks, or other heat treatment-related problems of the material.
- Relatively low welding accuracy: Compared with high-precision welding processes such as laser welding, arc welding lacks welding accuracy, and the fineness and aesthetics of the weld are low.
- High smoke and gas emissions: A large amount of smoke and harmful gases are generated during arc welding, which may affect the health of operators and the environment, so good ventilation and protective equipment are required.
- High technical requirements: Especially in manual welding, the skill level of the welder has a great impact on the welding quality, and insufficient technical proficiency will lead to welding defects.
Application of Arc Welding in Various Industries
- Construction industry: Arc welding is widely used in the welding of building structures, especially in the construction of steel structures and bridges. The high-strength welds and operability of arc welding make it one of the preferred processes for steel structure welding.
- Shipbuilding industry: A large amount of steel welding is required in hull manufacturing, and arc welding can handle heavy steel plates and provide good mechanical properties. In particular, submerged arc welding is widely used in the welding of large hulls and shells.
- Oil and gas industry: In pipeline welding, the flexibility and strong material compatibility of arc welding make it the main welding method for oil and gas pipelines, which can ensure reliability under high-pressure environments.
- Heavy equipment manufacturing: In the manufacturing of heavy equipment such as mining equipment, construction machinery, and agricultural machinery, arc welding is widely used in the welding of large structural parts, such as buckets, frames, and booms. These parts require high-strength and durable welding technology.
- Repair and maintenance: Due to the simple and convenient operation of arc welding equipment, it is widely used in the repair and maintenance of various types of mechanical equipment. From automobile repair to industrial equipment repair, arc welding is a common tool for maintenance personnel.
As a long-standing and proven welding technology, arc welding still occupies an important position in modern industry due to its strong adaptability, low cost and wide application.
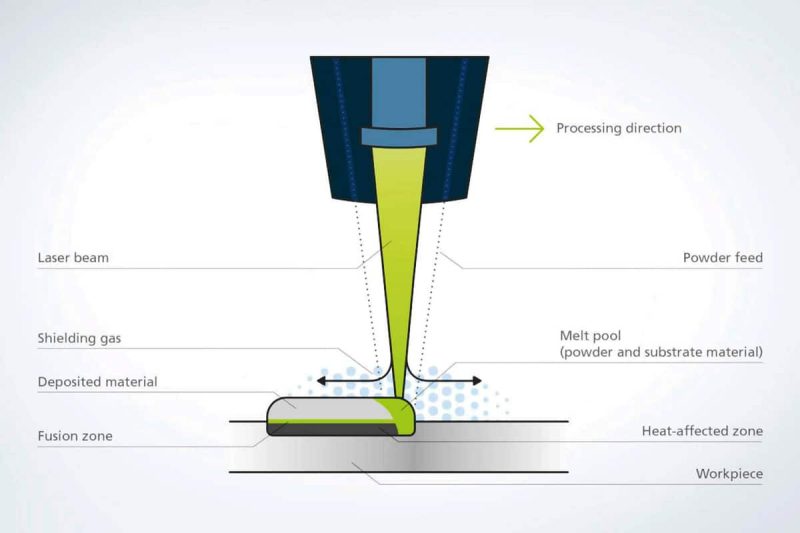
Laser Welding Principle
Laser welding is an advanced welding technology that uses a high-energy-density laser beam to quickly heat, melt, and precisely connect materials. Its main advantages include high welding speed, low heat input, precise control, and applicability to a variety of materials. Laser welding has become a mainstream welding process in the fields of automotive manufacturing, aerospace, electronics, and medical equipment due to its non-contact and high-precision characteristics.
How Laser Welding Works
The core working principle of laser welding is to use the high energy concentration characteristics of the laser beam to focus the energy into a very small welding area, quickly heat and melt the material to form a molten pool. As the beam moves, the molten pool solidifies to form a weld. The entire welding process is usually divided into the following steps:
- Laser beam generation: A high-intensity laser beam is generated by a laser generator, which can be a fiber laser generator, a CO₂ laser generator, or a solid-state laser generator. The laser beam is characterized by a single wavelength, high directivity, and high energy density.
- Laser beam focusing: The laser beam is focused to a very small point, usually only about 0.1 mm in diameter, by an optical system (such as a lens or a reflector). This allows for very high power densities (hundreds to thousands of watts per square millimeter), sufficient to melt metal quickly.
- Material melting and welding: When the laser beam is irradiated onto the surface of the material, the material absorbs the laser energy and quickly heats to the melting point, forming a molten pool. As the laser beam moves along the welding path, the molten pool gradually expands and forms a solid weld after cooling.
- Cooling and solidification: After the laser beam moves, the molten pool area cools, and the molten metal solidifies to form a continuous weld. By controlling the laser power, welding speed, and focus position, the shape and quality of the weld can be precisely controlled.
Interaction Between Laser and Metal
The key to laser welding lies in the interaction between laser energy and metal materials, which is specifically manifested in the following stages:
- Laser energy absorption: When the laser beam irradiates the metal surface, the metal absorbs part of the laser energy, which depends on the reflectivity of the metal and the wavelength of the laser. For example, high-reflectivity materials such as aluminum and copper have low absorption rates for certain wavelengths of lasers, so higher power or more suitable wavelengths are required for welding. For common steel and stainless steel, the absorption rate is higher and laser welding is more efficient.
- Heat conduction and melting: The laser energy absorbed by the metal diffuses into the material through heat conduction, thereby heating the material and reaching the melting point. The higher power density causes the material to melt locally and quickly, forming a molten pool. During the movement of the laser beam, the metal in the molten pool continues to solidify and eventually forms a weld.
- Keyhole Effect: In high-power laser welding, the energy of the laser beam not only melts the material, but also vaporizes part of the metal, generates local pressure, and pushes the molten metal to form a small hole. This keyhole effect allows the laser beam to penetrate deep into the material, further transmit energy through multiple reflections, and improve the welding depth and efficiency. Keyhole welding is very suitable for thick materials or deep penetration welding.
- Dynamic behavior of the molten pool: During the welding process, the fluidity and surface tension of the molten pool affect the quality and shape of the weld. Appropriate laser power and welding speed can keep the molten pool stable and avoid welding defects such as spatter and porosity.
Key Parameters Affecting Laser Welding
In the laser welding process, there are several key parameters that directly affect the welding quality and effect. These parameters include but are not limited to laser power, welding speed, focus position and shielding gas.
- Laser power: The power of the laser determines the energy intensity applied to the material. Higher power is suitable for thick plate welding or deep penetration welding, but if the power is too high, it may cause excessive melting or spattering of the material; lower power is suitable for thin plates or precision welding, which can effectively reduce heat input and deformation.
- Welding speed: The welding speed refers to the speed at which the laser beam moves on the surface of the material. Faster welding speed can reduce the size of the heat-affected zone and material deformation, but too fast speed may cause incomplete or unstable welds; slower speed is conducive to deep penetration welding, but it may increase heat input, resulting in too wide welds or a larger heat-affected zone.
- Focal position: The position of the laser beam’s focus relative to the workpiece surface is the key to controlling the weld depth and weld shape. Focusing below the workpiece surface can increase the weld depth and is suitable for thick plate welding; focusing above the surface is suitable for surface precision welding. Accurately controlling the focus position helps optimize the shape and strength of the weld.
- Shielding gas: Shielding gas (such as argon, helium or carbon dioxide) is often used in laser welding to prevent the molten pool from reacting with oxygen and nitrogen in the air, thereby avoiding weld oxidation or pore formation. Different gases have different effects on weld formation and quality. Argon is usually used to improve weld surface finish, while helium is used to enhance weld depth.
- Laser wavelength: The wavelength of the laser affects the absorption efficiency of the material. Different materials have different sensitivities to laser wavelengths, and choosing the right wavelength helps improve energy efficiency and welding results. For example, fiber laser generators are usually in the 1μm wavelength range, which is suitable for welding steel, stainless steel and other materials, while CO₂ laser generators have a longer wavelength (10.6μm) and are more suitable for welding non-metallic materials.
- Welding environment: Environmental conditions such as humidity, temperature and air flow may also affect the stability of laser welding, especially when working in the open air or in harsh environments, and necessary protective measures must be taken to ensure welding quality.
By precisely controlling these parameters, laser welding can achieve high-quality, low-distortion welding results that meet the needs of a variety of industrial applications.
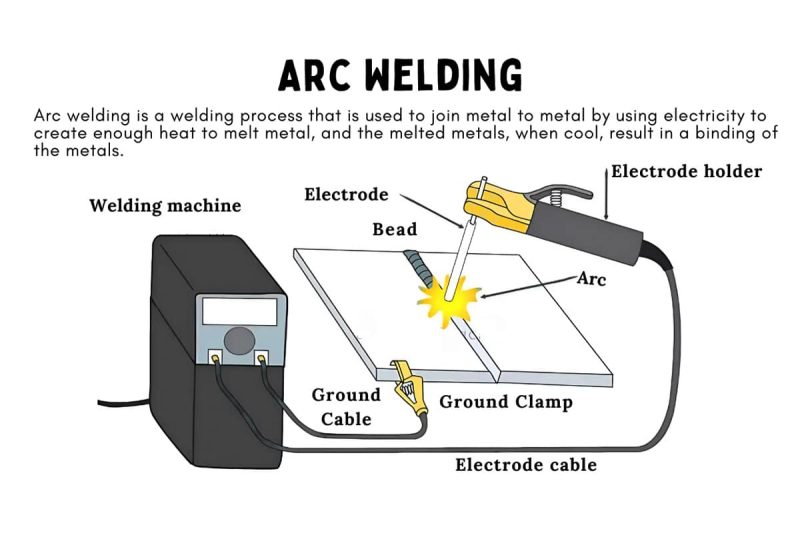
Arc Welding Principle
Arc welding is a welding process widely used in the industrial field. Its main feature is to use the high temperature generated by the arc to melt the metal and achieve a firm connection of the material. By using the arc between the electrode and the workpiece as a heat source, arc welding can process a variety of metal materials and is suitable for a variety of welding scenarios, such as construction, shipbuilding, oil pipelines, and automobile manufacturing. Arc welding has the advantages of low equipment cost and flexible operation, but it also has some limitations, such as a large heat-affected zone and relatively low welding accuracy. Understanding the working principle and key parameters of arc welding will help optimize the welding effect and improve the quality of the weld.
How Arc Welding Works
The basic working principle of arc welding is to generate a high-temperature arc through the current between the electrode and the workpiece, melting the metal on the electrode and the workpiece surface to form a molten pool. As the arc moves across the workpiece surface, the molten pool gradually cools and solidifies, eventually forming a solid weld. The operation process of arc welding usually includes the following steps:
- Arc generation: When the welding electrode contacts the workpiece, the circuit is closed, and current flows. The electrode is then separated from the workpiece, and the generated arc transmits energy through the air or shielding gas, causing the metal in the local area to quickly heat to the melting point.
- Electrode melting and filling: The high temperature of the arc not only melts the workpiece but also melts the welding electrode. The molten metal of the electrode enters the molten pool and combines with the molten metal of the workpiece to fill the welding area gradually.
- Formation and movement of the molten pool: As the arc moves along the welding path, the molten pool is continuously formed and moved, and the area behind the molten pool cools rapidly after leaving the arc and solidifies into a weld.
- Protection and cooling: In some arc welding techniques, such as metal arc welding (MIG/MAG welding), inert gases (such as argon, carbon dioxide, etc.) are used to protect the molten pool to prevent oxygen and nitrogen in the air from reacting with the high-temperature metal to form oxides or pores, which affect the quality of the weld.
Arc and Weld Pool Formation
The core of arc welding is the formation of arc and molten pool, which determine the efficiency and quality of welding.
Arc Formation
The arc is generated by high current and low voltage. The air between the electrode and the workpiece is broken down by the current, becoming a conductive medium and forming an arc in a plasma state. This plasma has an extremely high temperature (usually up to 5000 to 6000°C), which is enough to melt metal. The shape and stability of the arc are crucial to the success of welding. A stable arc can transfer heat evenly and ensure that the molten pool is formed evenly and stably.
Molten Pool Formation and Dynamic Behavior
During arc welding, when the arc generates enough heat on the surface of the material, the local metal melts to form a molten pool. The shape, size, and fluidity of the molten pool will affect the final quality of the weld. The metal in the molten pool mixes with the molten electrode metal to form a connection. The dynamic behavior of the molten pool in arc welding is a complex process, which is affected by many factors such as arc current, welding speed, heat conduction, etc. The solidification rate of the molten pool, surface tension, and gravity all determine the morphology and surface finish of the weld.
Welding Position and Molten Pool Flow
Changes in welding position, such as flat welding, vertical welding, horizontal welding, etc., will affect the flow behavior of the molten pool. In flat welding, the molten pool has better fluidity and the weld formation is more stable; while in vertical welding or overhead welding, the molten pool is affected by gravity and is prone to sagging or uneven flow. Therefore, welders need to adjust welding parameters and techniques according to the welding position to ensure the control of the molten pool.
Key Parameters Affecting Arc Welding
Many parameters in arc welding directly affect the welding effect and weld quality. Understanding and controlling these parameters can help welders achieve ideal welding results.
- Welding current: Current is one of the key parameters that determine the heat input of the welding process. A higher current can generate greater heat, increase the size of the molten pool and the depth of the weld, and is suitable for welding thicker materials; while a lower current is suitable for thinner materials to avoid excessive melting and deformation. Too high a current will cause the weld to overflow and the molten pool to be unstable, while too low a current will cause insufficient melting and insufficient weld strength.
- Welding voltage: Voltage controls the length and stability of the arc. Higher voltage will produce a longer arc, making the heat distribution more even, which is suitable for the formation of wide welds; lower voltage will produce a shorter arc, and the heat is concentrated in a smaller area, which is suitable for deep welding. Changes in voltage directly affect the shape and stability of the arc, which in turn affects the fluidity of the molten pool and the shape of the weld.
- Welding speed: Welding speed refers to the speed at which the arc moves on the workpiece, which has an important impact on the shape of the molten pool, the size of the heat-affected zone (HAZ), and the quality of the weld. Higher welding speeds will reduce the time for molten pool formation, reduce heat-affected zone, and reduce deformation, but may cause discontinuous welds or poor fusion; slower welding speeds increase heat input and are suitable for deep-melting welding, but may cause overheating of materials, too wide welds, or large deformation.
- Electrode type and diameter: The choice of electrode directly affects the welding effect. Different types of electrodes (such as welding rods, electric welding wires, etc.) are suitable for different materials and welding methods. The diameter of the electrode also affects the stability of the arc and the width of the weld. Thicker electrodes are suitable for welding thicker materials and can form wide and thick welds, while thinner electrodes are suitable for precision welding or thin plate welding.
- Welding environment: Environmental factors, such as temperature, humidity, wind speed, etc., also affect arc welding. Excessive wind speed may blow away the shielding gas, resulting in oxidation or pore formation of the weld. To ensure welding quality, appropriate protective measures such as wind barriers and heated workpieces are required under harsh outdoor conditions.
- Shielding gas: In metal arc welding (MIG/MAG welding) and tungsten arc welding (TIG welding), shielding gas is used to isolate the air and prevent the molten pool from contacting oxygen and nitrogen. Different shielding gases (such as argon, carbon dioxide, helium, etc.) have different effects on the morphology, penetration depth, and surface finish of the weld. For example, argon can provide a better surface finish, while carbon dioxide helps to increase the depth of the weld.
By precisely controlling these key parameters, arc welding can achieve higher welding quality and adapt to the needs of different materials, thicknesses, and welding positions.
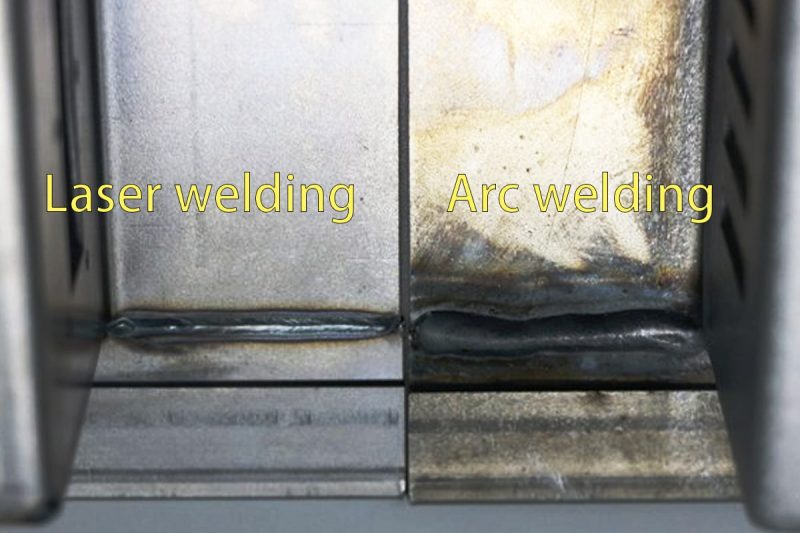
Comparison Between Laser Welding and Arc Welding
Laser welding and arc welding are two important welding processes in the industrial field, each with unique advantages and limitations. Laser welding is known for its high speed, high precision, and low heat input, while arc welding is widely used for its easy operation, wide range of applications, and low cost. There are significant differences between the two in terms of efficiency, accuracy, heat-affected zone, welding quality, equipment requirements, and cost, so the choice of which welding technology should be based on specific project needs and budget.
Efficiency and Speed
In terms of efficiency and speed, laser welding is significantly better than arc welding. The high energy density of laser welding enables it to complete welding at a very fast speed, especially for thin materials or precision welding. The welding speed of laser welding can reach several meters per minute or even higher, which is suitable for mass production scenarios, such as high-speed assembly line operations in the automotive manufacturing and electronics industries.
In contrast, arc welding has a slower welding speed, especially when dealing with thicker materials or complex welding positions, the efficiency will drop significantly. In addition, the preparation and cleaning time of arc welding is usually longer, including steps such as welding electrode replacement and slag removal, so arc welding is more suitable for occasions with low-speed requirements such as small batches, thick plates, or field construction.
Precision and Accuracy
Laser welding is known for its high precision and controllability. The laser beam can be focused to a very small point, thus achieving extremely high welding accuracy, which is suitable for fine metal processing and welding of complex parts. Laser welding has a high degree of automation and can be integrated with CNC equipment or robots to achieve high-precision welding path control. This makes laser welding popular in industries that require high precision and consistency, such as microelectronics, medical device manufacturing, etc.
Arc welding is relatively low precision and mainly depends on the skills of the operator. Although modern arc welding equipment can improve accuracy through automatic control, it is limited by the instability of the arc and the large heat input, and it is difficult to achieve the accuracy level of laser welding. Especially in thin plates and precision welding, arc welding may cause overheating or deformation of the material, thus affecting the welding quality.
Heat-Affected Zone and Deformation
Another major advantage of laser welding is its low heat input and relatively small heat-affected zone (HAZ). Due to the high energy density and precise control of the laser beam, only the welding area will heat and melt rapidly, and the surrounding materials will be less affected by the heat. This not only reduces the deformation of the material but also improves the mechanical properties after welding. Therefore, laser welding is very suitable for welding heat-sensitive materials or occasions requiring high strength and low deformation.
Arc welding has a large heat input, which causes the materials around the weld to be greatly affected by heat, forming a wider heat-affected zone. This will increase the deformation and residual stress of the material, especially in thick materials or large-area welding. To reduce thermal deformation, arc welding usually requires multiple welding and post-processing, such as heat treatment or correction, which increases the complexity and cost of welding.
Weld Quality and Strength
Laser welding generally provides excellent weld quality, especially when welding thin plates and precision parts. Due to the automated control of the laser welding process and the small heat-affected zone, it can produce consistent welds with smooth weld surfaces and little spatter or porosity. Laser welds are generally stronger, especially in deep penetration welding, which can achieve a good weld depth to width ratio, thereby improving the overall strength of the weld.
The welding quality of arc welding is more dependent on the skills of the operator. The uniformity and surface quality of the weld may be affected by factors such as operating instability, welding current and electrode selection. Although arc welding can also produce high-strength welds, especially when welding thick plates, defects such as spatter, slag and pores often appear in the weld, which usually requires additional grinding and cleaning. For some high-strength materials, the weld strength of arc welding may not be comparable to that of the parent material.
Equipment and Setup
The design of laser welding equipment is usually complex but with the advancement of technology, modern portable laser welding machines have become a highlight in the welding industry. These devices not only integrate laser generators, optical systems, and automatic control units but also have efficient shielding gas devices to ensure the quality and performance of materials during welding. The user-friendly operation interface of portable laser welding machines allows operators to quickly get started and reduce reliance on complex settings. At the same time, the maintenance of modern laser welding machines is relatively simple, which can effectively reduce the frequency of equipment failures and ensure continuous production efficiency.
In contrast, conventional arc welding equipment is relatively simple in construction, usually including basic components such as welding power source and welding electrode. This type of equipment is usually operated manually or semi-automatically, and is suitable for use in various industrial applications, especially in on-site construction, where its portability and adaptability make it popular. However, arc welding equipment may face problems such as large heat-affected zones and inconsistent weld quality during the welding process, especially in demanding welding applications, and it is often difficult to achieve ideal results.
Cost Considerations
From a cost perspective, arc welding has obvious advantages. Arc welding equipment is relatively cheap, with low maintenance and operating costs, and is particularly suitable for small-volume, low-precision welding needs. Arc welding is simple to operate, and the required training and technical requirements are low, so the overall welding cost is relatively controllable.
The initial investment in laser welding is large, and the equipment procurement, installation, and maintenance costs are relatively high. The precision operation and automation requirements of laser welding also mean higher operating and training costs. However, the high efficiency and high quality of laser welding can quickly dilute the cost in mass production, and the long-term cost-effectiveness of laser welding is more prominent.
Laser and arc welding each have advantages and are suitable for different scenarios. Laser welding is known for its high speed, high precision, and low heat input, and is ideal for projects that require high welding quality and accuracy, while arc welding has more advantages in terms of lower cost, adaptability to thick plate welding, and on-site construction. When selecting a welding method, project needs such as welding quality, material thickness, accuracy requirements, and budget should be considered comprehensively.
Today’s laser welding machines already have on-site construction capabilities and are easy to carry. AccTek’s portable laser welding machine can not only achieve high-precision and fast welding but is also reasonably priced and easy to move, making it especially suitable for on-site processing operations. This type of equipment can significantly improve production efficiency and bring stable long-term benefits to the company.
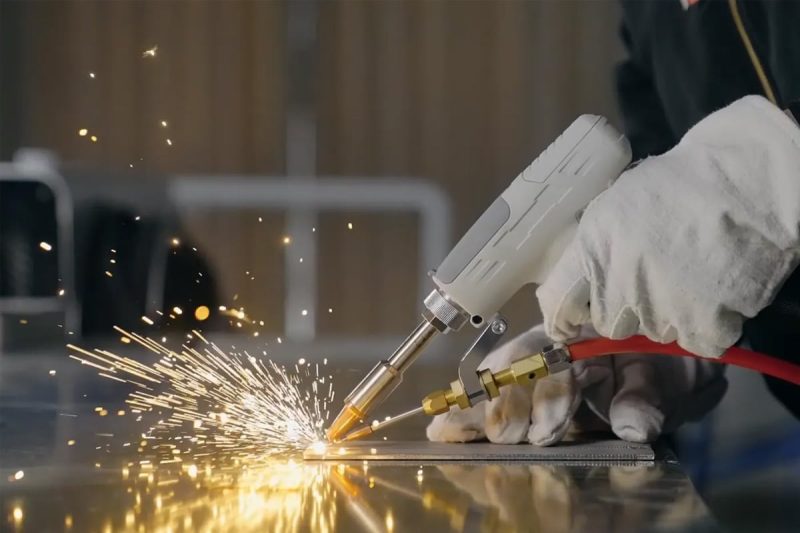
Applications of Laser Welding and Arc Welding
In modern industry, laser welding and arc welding are both indispensable welding technologies. Although each has its own unique advantages and application scenarios, laser welding has shown increasingly obvious advantages in many industries due to its precision, efficiency, and flexibility.
Automotive
In the field of automobile manufacturing, laser welding is widely used in body manufacturing and chassis connection. Its high precision and low heat input characteristics make the connection of body parts tighter, thereby improving the safety and reliability of the whole vehicle. The high speed and degree of automation of laser welding technology also make it very effective in mass production, and can quickly complete large-scale welding tasks. Although arc welding is still used in the welding of some thick-walled parts, the precise control and welding quality provided by laser welding make it the first choice in many critical applications.
Aerospace
In the aerospace industry, components must withstand high stress and temperature differences under extreme conditions. Laser welding can provide excellent connection strength and weld quality when welding high-strength materials such as titanium alloys and aluminum alloys. The low heat-affected zone characteristics of laser welding reduce thermal damage to the material and help ensure the reliability of welded components. Although arc welding also has certain applications in this field, the advantages of laser welding in welding complex geometries have made it gradually become an important choice in the aerospace industry.
Electronics and Microelectronics Industry
Laser welding is particularly effective in welding electronic and microelectronic components. Due to its high precision and controllability, laser welding is suitable for welding tiny circuit boards, battery connectors, and other sensitive electronic components. This non-contact welding method can effectively reduce heat input, thereby avoiding thermal damage to tiny components. In contrast, arc welding often faces the risk of thermal damage when welding small electronic components, so laser welding is undoubtedly more suitable.
Medical Device Manufacturing
In the manufacture of medical devices, the precision and non-contamination of welding are crucial. Laser welding is very suitable for welding materials such as stainless steel and titanium alloys due to its precise weld seam and small heat-affected zone. It is widely used in the production of surgical tools and implants. In contrast, arc welding has difficulty meeting the standards of laser welding when processing these demanding medical devices.
Laser welding has shown significant advantages in many industries, especially in applications requiring high precision and fast processing, showing its irreplaceable value. Although arc welding still has its place in some areas, the flexibility and welding quality provided by laser welding have made it increasingly dominant in modern welding technology. When selecting welding technology, a reasonable evaluation of the advantages and disadvantages of both based on specific needs and application scenarios can effectively improve production efficiency and product quality.
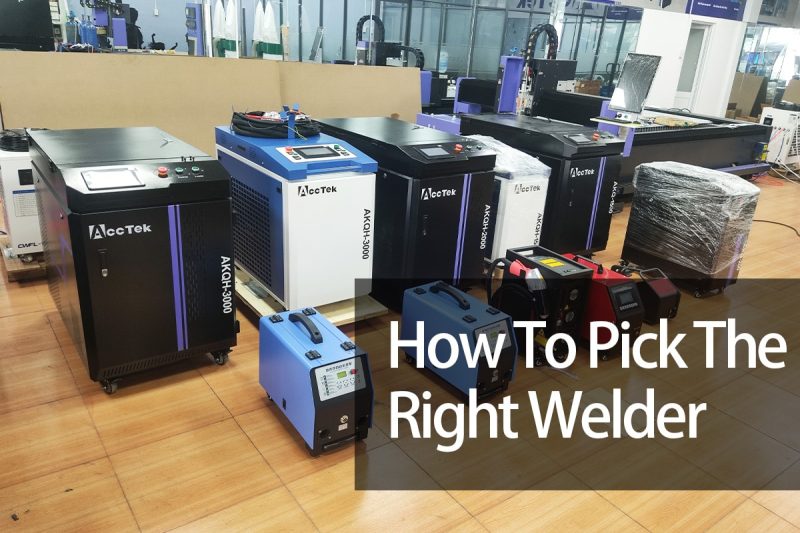
Choosing the Right Welding Technology
Choosing the right welding technology is essential to ensure welding quality, project cost control, and production efficiency. Each welding method has its advantages and limitations when dealing with different materials, specifications, and applications. Whether it is laser welding or arc welding, there are many factors to consider when making a selection, including material compatibility, project specifications, process requirements, budget, and available resources. Reasonable selection of welding methods can not only optimize the production process but also reduce costs and improve welding quality and efficiency.
Factors to Consider When Choosing a Welding Method
When selecting welding technology, it is necessary to combine specific project requirements and actual conditions, and mainly consider the following factors:
- Material type and thickness: Different materials and material thicknesses require different welding techniques. For example, thin sheet materials are more suitable for laser welding, while thick plates or structural steels are often welded with arc welding.
- Welding precision and complexity: Complex parts, fine welds, or high-precision welding requirements usually require precision welding techniques such as laser welding.
- Welding speed: The demand for large-scale, high-speed production often tends to favor welding techniques with a high degree of automation, such as laser welding, which can complete high-quality welding in a short time.
- Heat effect and deformation control: Heat-sensitive materials or projects requiring a low heat-affected zone are often suitable for laser welding; while for insensitive structural steel or thicker materials, arc welding can provide deep penetration welding.
Project Specifications and Goals
The specific specifications and goals of the project directly affect the choice of welding technology. For large-scale automated production lines, such as automobile manufacturing and electronic product production, laser welding can effectively improve production efficiency and meet the needs of high-quality and large-scale production due to its fast speed, high precision, and ability to integrate automated equipment. In addition, the non-contact nature of laser welding also reduces the use of consumables and cleaning work during the welding process, thereby improving production continuity.
Arc welding is one of the most commonly used welding methods in construction, shipbuilding, and heavy equipment manufacturing. With its strong adaptability and portability, arc welding technology can operate reliably under harsh construction conditions, especially when welding thick plates or complex structures. For example, in the welding of oil and gas pipelines, the deep penetration characteristics and low-cost advantages of arc welding make it the most popular welding method.
Budget and Resource Considerations
Budget and resource availability are key factors in the selection of welding technology. Laser welding equipment is expensive, including hardware investment such as laser source, control system, and cooling device, and maintenance cost and operation technology requirements are also high. Therefore, although laser welding can bring high benefits, the initial investment is large and it is usually suitable for industries with high mass production and a high degree of automation.
Although arc welding equipment is low-cost, relatively simple to maintain, and operators do not need to undergo high-intensity technical training, it is still more suitable for projects that do not require high welding precision. Especially in environments such as construction sites and field maintenance, arc welding is suitable for some small and medium-sized projects with limited budgets because of its flexible operation and cheap consumables. However, the limitation of arc welding is that its precision is relatively low, especially when processing thin plates and heat-sensitive materials, excessive heat input can easily lead to quality problems such as deformation and cracks. In addition, the welding speed of arc welding is relatively slow, which is not suitable for application scenarios that require fast and precise operations.
In contrast, laser welding machines not only have the advantages of high precision and high speed but can also effectively reduce thermal effects and ensure the beauty and quality of welds. Today’s laser welding equipment is also very light and compact, easy to carry, fully adaptable to on-site work, and has a wider range of material applicability. Therefore, laser welding is undoubtedly a better choice for projects that pursue precision, efficiency, and long-term return on investment.
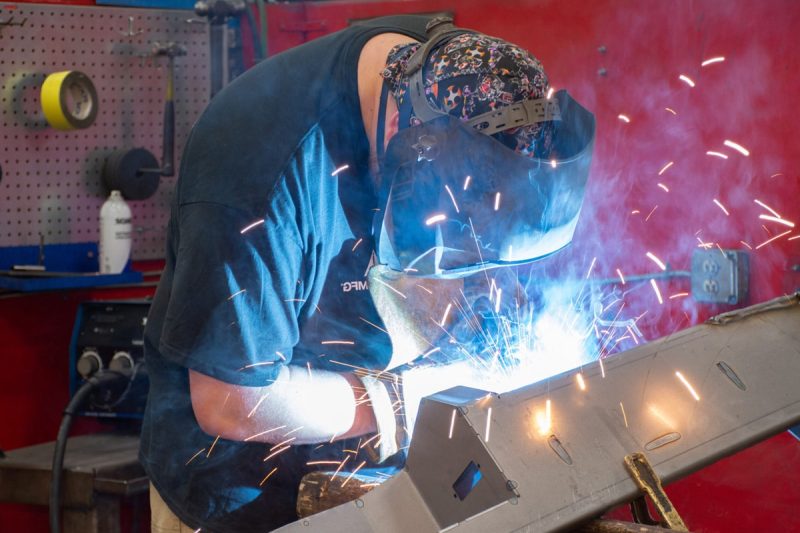
Environmental and Safety Considerations
In modern industry, environmental and safety issues are becoming more and more important. The choice of welding technology not only affects the quality and efficiency of welding but also involves the impact on the environment and the protection of workers’ health and safety. In the comparison between laser welding and arc welding, laser welding shows some unique advantages.
Emissions and Environmental Impact
Laser welding usually produces less smoke and harmful gas emissions due to its high efficiency and low heat input. This feature makes laser welding more environmentally friendly. Compared with arc welding, the latter may release more welding smoke and toxic gases during the welding process, increasing the negative impact on the environment. In industries that need to strictly comply with environmental regulations, the low emission characteristics of laser welding undoubtedly provide more favorable conditions for enterprises.
In addition, laser welding usually produces smaller welds, which means that the amount of material and subsequent processing required is relatively reduced, further reducing the impact on the environment. By choosing laser welding, companies can not only improve welding efficiency but also demonstrate social responsibility in terms of environmental protection.
Occupational Health and Safety Hazards
In terms of occupational health and safety, the non-contact nature of laser welding greatly reduces the risk of operators being exposed to welding heat and welding fumes. During laser welding operations, the temperature of the welding area is usually lower, which can reduce the risk of burns caused by high temperatures for workers. In addition, the safety protection measures equipped with the laser welding system (such as laser protective glasses and safety shields) can effectively protect the eyes and skin of operators and reduce potential injuries.
In contrast, arc welding requires direct contact with the welding power source, so workers face a higher risk of electric shock, burns, and smoke inhalation during operation. Although arc welding also has corresponding safety protection measures, overall, laser welding has a more obvious advantage in protecting workers’ health.
Regulatory Compliance and Standards
In terms of regulatory compliance and standards, the low emissions and safety characteristics of laser welding give it certain advantages in meeting environmental and safety regulations. Many industries are gradually strengthening environmental standards and safety specifications for welding processes, and the use of laser welding can make it easier to meet these increasingly stringent regulatory requirements. At the same time, when companies improve their welding processes, they can also demonstrate their commitment to sustainable development by choosing laser welding technology.
Overall, laser welding demonstrates significant advantages in terms of environmental protection and worker safety. For those companies that pay attention to environmental protection and employee safety, investing in laser welding equipment can not only improve production efficiency but also establish a good corporate image in the industry. Choosing laser welding is not only an upgrade of technology but also a commitment to sustainable development.
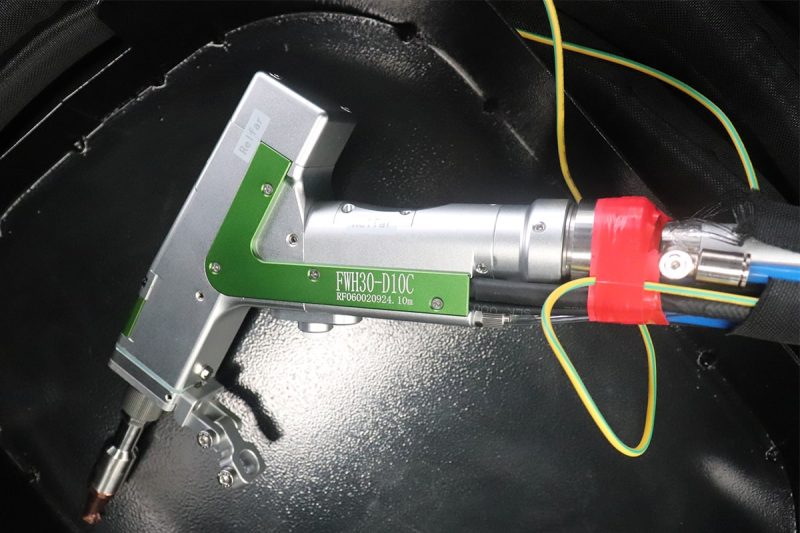
Summarize
Laser welding machines have gradually occupied an important position in modern industrial welding technology, especially in areas where welding quality, precision, and efficiency are extremely high. Compared with traditional arc welding, laser welding has a lower heat-affected zone and can achieve high-speed and high-precision welding, thereby reducing material deformation and subsequent processing requirements. This makes laser welding widely used in industries such as automotive manufacturing, aerospace, medical devices, and electronics and has become an ideal choice for improving production efficiency and product quality.
In addition, the advantages of laser welding in terms of environmental protection and worker safety cannot be ignored. Since laser welding produces less smoke and harmful gases and has lower heat input during operation, it is easier to meet environmental regulations and protect employee health. The sustainability of this technology allows companies to demonstrate their emphasis on social responsibility while pursuing economic benefits. In summary, laser welding machines provide modern industry with an efficient, safe, and environmentally friendly welding solution, and are an important force in promoting the development of the industry.
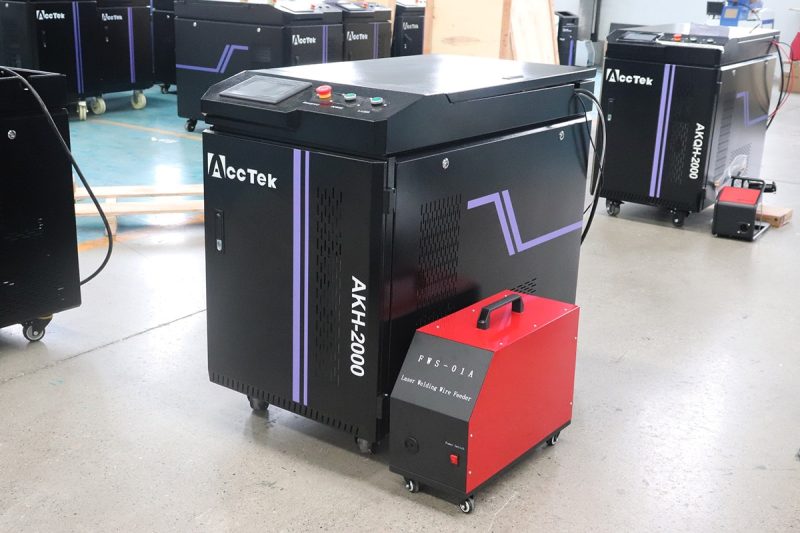
Get Laser Solutions
When pursuing efficient and precise welding solutions, AccTek’s laser welding machine is undoubtedly your best choice. Our laser welding equipment not only has advanced technology, but also can meet the stringent requirements of various industries for welding quality and speed, and also demonstrates excellent performance and reliability. Whether you are in the field of automotive manufacturing, aerospace, electronics, or medical equipment, our laser welding machine can help you improve production efficiency and reduce costs.
In addition, we provide comprehensive after-sales service to ensure that you have no worries during use. Our professional team is always ready to answer your questions, provide technical support and maintenance services, and help you achieve the best welding results. Please do not hesitate to contact us immediately to get your tailor-made laser solution and let the AccTek laser welding machine become your successful partner!
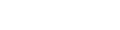
Contact information
- [email protected]
- [email protected]
- +86-19963414011
- No. 3 Zone A, Lunzhen Industrial Zone,Yucheng City , Shandong Province.
Get Laser Solutions