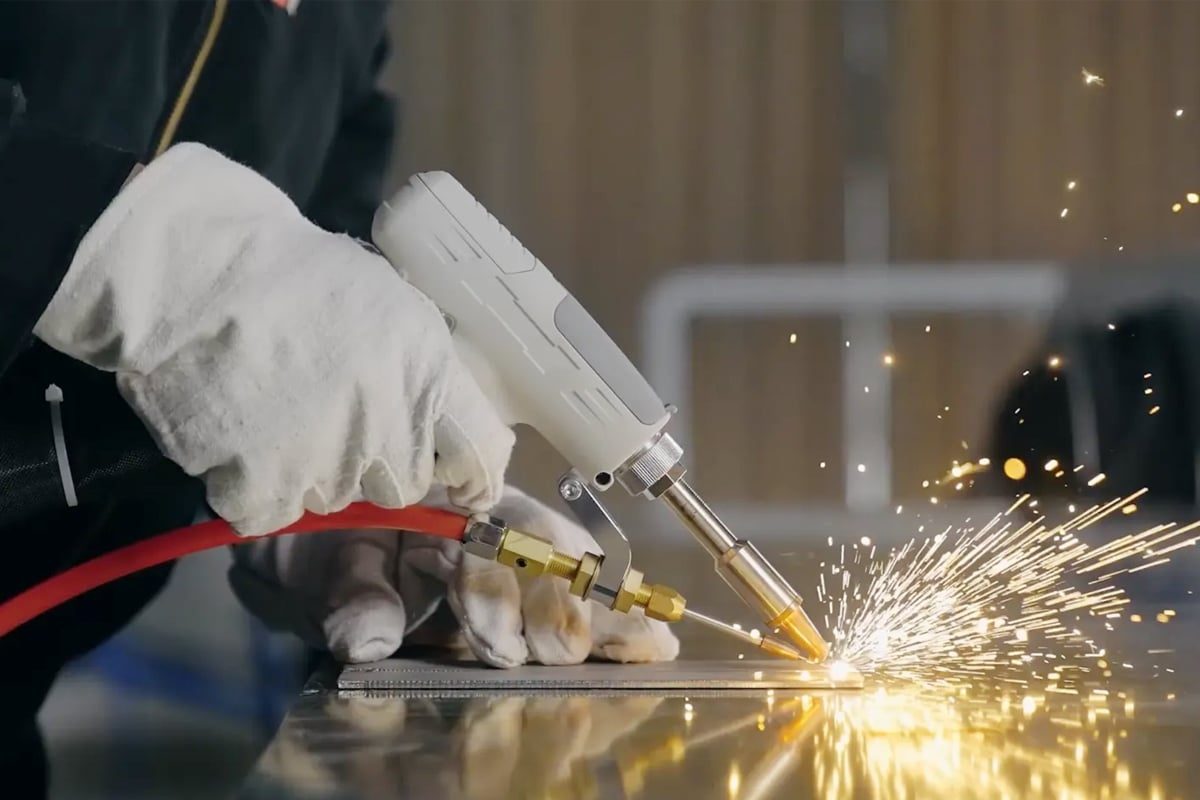
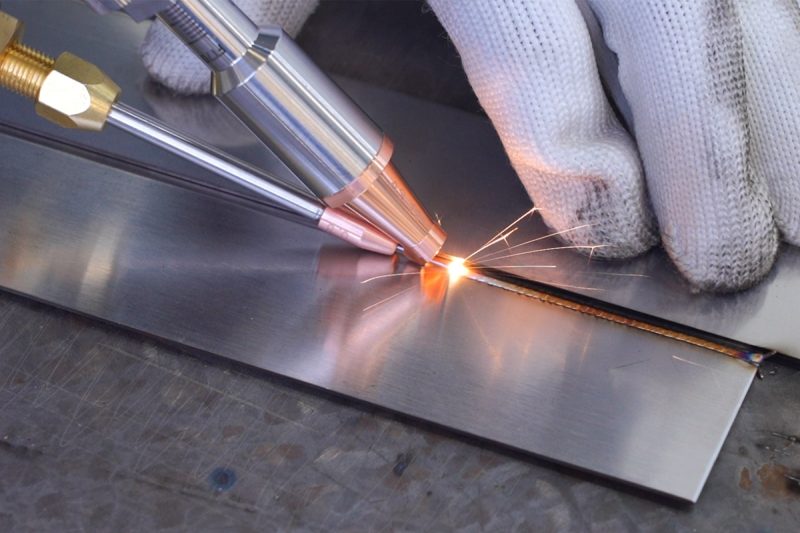
Principle and Process
Laser Welding
Principle
- Laser Generation: The process begins with the generation of a laser beam using a laser source. Common types of lasers used in welding include solid-state lasers (such as Nd lasers) and fiber lasers. These lasers produce a coherent, monochromatic beam.
- BeamFocusing: The laser beam is directed and focused onto a small, precise area of the workpiece using lenses or mirrors. This focusing produces a high energy density spot that is capable of melting the material at the focal point.
- Material Fusion: When the laser beam is irradiated onto the workpiece, the intense heat generated causes the material to melt. The molten material then coalesces and solidifies upon cooling, forming a weld. The process can be adjusted to control the depth and width of the weld by varying the laser power and focusing parameters.
Process
Laser welding can be divided into two main modes based on the interaction between the laser beam and the material:
- Conduction Mode Welding: In this mode, the laser power is relatively low, and heat conduction is the primary mechanism for melting the material. The laser beam heats the surface and the heat is conducted through the material to form a shallow weld. Conduction mode welding is typically used for thin materials and applications that require high surface quality.
- Keyhole Mode Welding: At higher laser powers, the laser beam creates a keyhole, or vapor-filled cavity, in the material. This keyhole allows the laser energy to penetrate deep into the material, creating a narrow, deep weld. Keyhole mode welding is useful for thicker materials and applications that require high penetration depth.
TIG Welding
Principle
- Arc Generation: TIG welding involves the creation of an arc between a non-consumable tungsten electrode and the workpiece. The arc generates intense heat, sufficient to melt the base material and form a weld pool.
- Shielding Gas: An inert gas, usually argon or helium, is used to protect the welding area from atmospheric contaminants. The shielding gas flows through the welding gun, protecting the molten weld pool and the tungsten electrode from oxidation and other atmospheric gases.
- Material Fusion: The heat generated by the arc melts the base material, forming a weld pool. In some cases, filler material is added to the weld pool to enhance the strength and integrity of the weld. The filler material is usually fed manually by the welder or automatically through a separate feeding system.
Process
TIG welding can be performed with or without filler material, depending on the specific requirements of the weld:
- Autogenous Welding: No filler material is used in this process, and the weld is formed by melting the edges of the base material only. Autogenous welding is often used for welding thin materials and applications that require high precision and minimal material addition.
- Filler Material Welding: When a filler material is used, it is fed into the weld pool either manually by the welder or by an automated system. The filler material melts and mixes with the parent material to form a strong, durable weld joint. This process is used for welding thicker materials and applications that require enhanced weld strength.
- Pulsed TIG Welding: Pulsed TIG welding is an advanced variation of TIG welding that involves regulating the electrical current to produce high and low-energy pulses. This technique helps control heat input, reduces distortion, and improves weld quality, especially in thin or heat-sensitive materials.
Principle and Process Comparison
Both laser welding and TIG welding are based on the principle of melting and coalescing materials to form a weld joint. However, they differ greatly in their mechanisms and execution:
- Heat Source: Laser welding uses a concentrated laser beam, while TIG welding relies on an arc between a tungsten electrode and the workpiece.
- Energy Density: Laser welding achieves high energy density through beam focusing, which allows for precise and controlled welding. TIG welding, while also precise, has a lower energy density compared to laser welding.
- Shielding: In TIG welding, inert gas shielding is essential to protect the welding area. Laser welding may also use shielding gas, but it is not always necessary, depending on the material and environment.
- Material Compatibility: Both technologies can weld a wide range of materials, but laser welding is usually preferred for high-precision applications, while TIG welding is favored for its versatility and quality in both manual and automated processes.
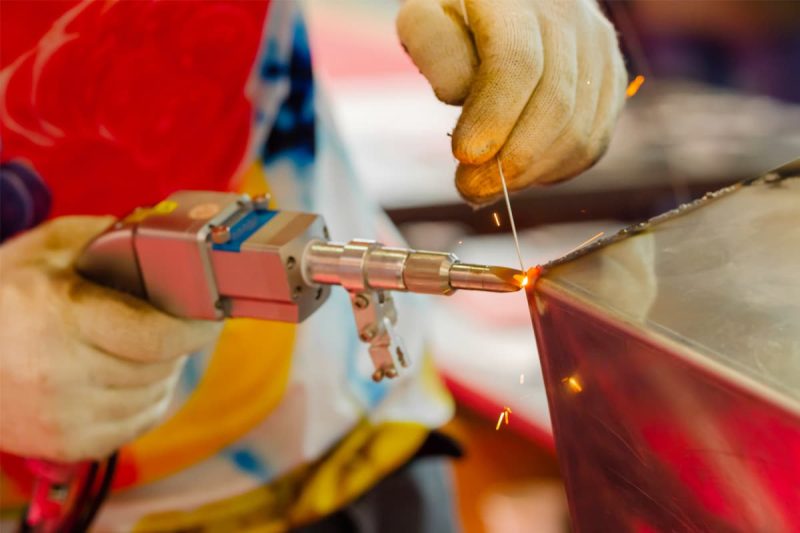
Weld Quality Comparison
Weld Strength
Laser Welding
TIG Welding
Weld Appearance
Laser Welding
TIG Welding
Heat Affected Zone (HAZ)
Laser Welding
TIG Welding
Precision and Accuracy
Laser Welding
TIG Welding
Accuracy and Precision
Laser Welding
TIG Welding
Post-Weld Treatment
Laser Welding
TIG Welding
Both laser and TIG welding produce high-quality welds, but they excel in different ways:
- Weld Strength: Both methods provide strong welds, but laser welding typically achieves higher joint strength due to deep penetration and minimal impurities.
- Weld Appearance: Laser welding produces smooth, clean welds with minimal spatter, while TIG welding also produces welds with a bright, aesthetically pleasing surface.
- Heat-Affected Zone: Laser welding has a smaller heat-affected zone, which reduces thermal distortion, while TIG welding generally has a larger heat-affected zone that can be managed by a skilled welder.
- Precision and Accuracy: Laser welding offers superior precision and control, making it ideal for complex applications. TIG welding also offers high precision, especially in the hands of a skilled welder.
- Post-Weld Treatment: Laser welding generally requires less post-weld treatment, saving time and money. TIG welding may require additional treatment, depending on the material and application.
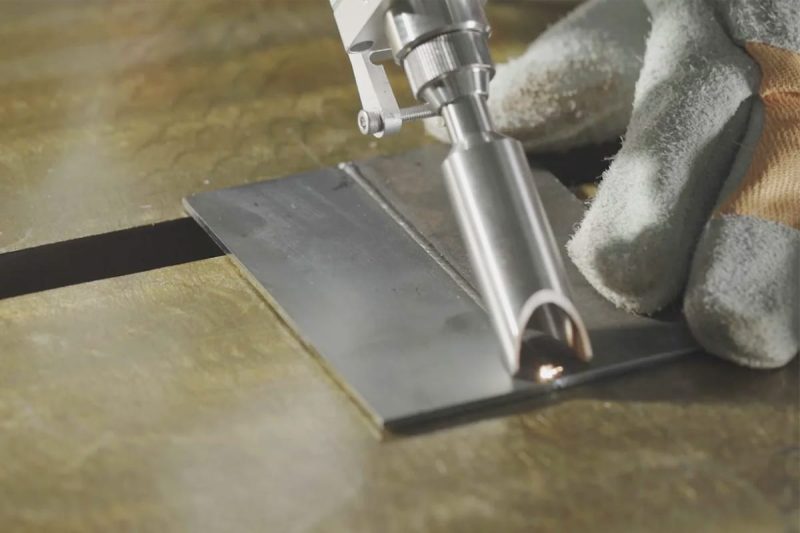
Cost Considerations
Initial Investment
Laser Welding
- Equipment Cost: Laser welding systems require a significant initial investment. The cost of the laser generator, focusing optics, cooling system, and control unit can be much higher than traditional welding equipment. High-power laser systems, such as fiber lasers and YAG lasers, are particularly expensive.
- Automation and Integration: Many laser welding applications involve automation, such as robotic arms and CNC machines, which further increases the initial investment. Integrating a laser welding system into an existing production line also adds upfront costs.
- Facility Requirements: Setting up a laser welding operation may require facility modifications, including specialized enclosures to ensure protection from laser radiation, ventilation systems, and protective equipment for operators.
TIG Welding
- Equipment Costs: The initial investment in TIG welding equipment is generally lower compared to laser welding. A basic TIG welding setup includes a power supply, welding gun, tungsten electrode, and shielding gas supply. While advanced TIG welders with features such as pulse and AC/DC capabilities cost more, they are still less expensive than laser systems.
- Manual VS Automatic: While TIG welding can be automated, it is typically performed manually. Manual setup costs are lower, while automatic TIG welding systems, which include a robotic arm and control unit, increase the initial investment but are still more affordable than laser welding automation.
- Facility Requirements: TIG welding is simple to set up, requiring minimal modifications to existing facilities. Standard safety equipment and proper shielding gas ventilation are generally sufficient.
Operating Costs
Laser Welding
- Energy Consumption: Laser welding systems, especially high-power lasers, consume a lot of electricity. However, its high efficiency and speed can offset energy costs by reducing welding time and increasing production output.
- Consumables: Laser welding uses fewer consumables than TIG welding. In many laser welding applications, no filler material is required, and shielding gas usage is minimal if required.
- Labor Costs: Laser welding systems, especially automated systems, require fewer operators. This can result in significant labor cost savings, especially in high-volume production environments. However, skilled technicians are required to program, operate, and maintain the system.
TIG Welding
- Energy Consumption: TIG welding generally consumes less electricity than laser welding, but requires longer welding times, which can result in higher energy costs over time.
- Consumables: TIG welding uses consumables such as tungsten electrodes, filler rods, and shielding gases (argon, helium). The cost of these consumables can add up, especially for high-volume or complex welding tasks.
- Labor Costs: TIG welding is labor-intensive and typically requires skilled welders to achieve high-quality welds. Labor costs can be quite high, especially for complex or delicate jobs that require a high level of expertise.
Maintenance
Laser Welding
- Complexity: Laser welding systems are complex and require regular maintenance to ensure optimal performance. This includes servicing the laser source, optics, cooling system, and control unit.
- Maintenance Costs: Laser welding systems can be expensive to maintain due to the specialized nature of the components and the need for trained technicians to perform repairs and servicing.
- Downtime: Scheduled maintenance and potential repairs can result in downtime that can impact productivity. However, modern laser systems are designed for high reliability to minimize unplanned downtime.
TIG Welding
- Simplicity: TIG welding equipment is simpler and generally easier to maintain. Regular maintenance includes checking and replacing consumables, cleaning the welding gun, and ensuring an adequate supply of shielding gas.
- Maintenance Costs: TIG welding has lower maintenance costs compared to laser welding. Replacement parts and consumables are readily available and affordable.
- Downtime: TIG welding equipment generally has less maintenance-related downtime. However, the manual TIG welding process is still affected by operator availability and skill level.
Long-term Economic Impacts
Laser Welding
- Productivity Improvements: The high speed and automation capabilities of laser welding can significantly increase productivity, reduce the total cost per weld, and increase production output.
- Quality and Precision: The precision and quality of laser welding reduce the need for rework and scrap, contributing to long-term cost savings. Minimal heat-affected zones and low distortion also improve product quality and reduce post-weld processing and associated costs.
- Return on Investment (ROI): Despite the high initial investment, the long-term ROI for laser welding can be high due to increased efficiency, reduced labor costs, and increased production volumes.
TIG Welding
- Flexibility: The versatility of TIG welding allows it to be used in a wide range of applications, providing flexibility and adaptability to a variety of industries. This is economically advantageous for businesses with varying welding needs.
- Skilled Labor: The reliance on skilled labor is both an advantage and a disadvantage. While skilled welders can produce high-quality welds, labor costs, and training requirements can affect long-term economic sustainability.
- Operating Costs: TIG welding has lower initial and maintenance costs, but can incur higher operating costs due to slower welding speeds and higher labor involvement. These factors must be balanced against the advantages of high weld quality and versatility.
Cost considerations for laser welding and TIG welding include several factors, including initial investment, operating costs, maintenance, and long-term economic impact:
- Initial Investment: Laser welding systems require a higher upfront investment than TIG welding equipment, especially when automation is involved.
- Operating Costs: While laser welding has a higher energy consumption, it uses fewer consumables and can reduce labor costs through automation. TIG welding has lower energy consumption but relies heavily on consumables and skilled labor.
- Maintenance: Laser welding systems are complex and costly to maintain, while TIG welding equipment is simpler and less expensive to maintain.
- Long-Term Economic Impact: Despite the high initial cost, laser welding can increase productivity, improve precision, and potentially provide a favorable return on investment. TIG welding offers flexibility and high-quality welds but may incur higher operating costs over time.
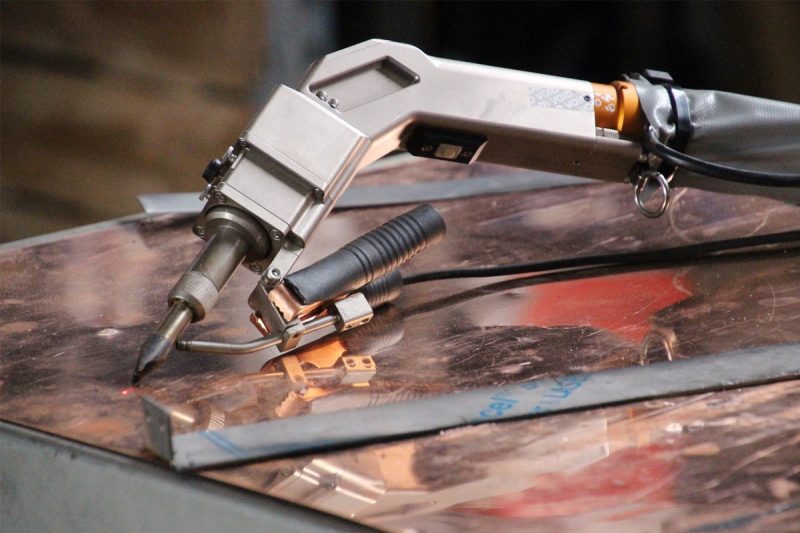
Factors Influencing Welding Method Selection
Material Types and Compatibility
Laser Welding
- Metals: Laser welding is very effective on a variety of metals, including stainless steel, carbon steel, aluminum, titanium, and nickel alloys. Its ability to weld dissimilar materials is particularly advantageous in industries that require complex assembly.
- Plastics and Composites: Laser welding can also be used with certain plastics and composites, provided they have compatible absorption characteristics.
- Reflective Materials: Welding highly reflective materials such as aluminum and copper can be challenging due to potential laser reflections, which can affect weld quality and equipment safety.
TIG Welding
- Versatility: TIG welding is versatile and can be used on nearly all metals, including stainless steel, aluminum, copper, magnesium, and exotic alloys such as Inconel.
- Thickness Range: TIG welding is suitable for both thin and thick sections, making it a flexible choice for a variety of applications.
- Material Properties: TIG welding is suitable for materials that require high weld quality and mechanical properties, such as aerospace alloys and critical automotive components.
Material Thickness
Laser Welding
- Thin Materials: Laser welding excels at welding thin materials, providing high precision and minimal heat-affected zones. It is ideal for applications such as electronics, medical devices, and thin-walled components.
- Thick Materials: While laser welding can be used for thicker materials, it may require multiple passes or a higher-powered laser, which can increase complexity and cost.
TIG Welding
- Thin to Thick Materials: TIG welding is suitable for a wide range of material thicknesses, from very thin sheets to thicker profiles. The ability to add filler material makes it suitable for welding thicker joints and reinforcing the weld area.
- Heat Control: The precise control of heat input in TIG welding allows for efficient welding of thin materials without causing burn-through or excessive distortion.
Joint Configuration and Accessibility
Laser Welding
- Complex Joints: Laser welding is suitable for complex joint configurations due to its precision and ability to reach hard-to-reach areas. It is often used in applications where it may be difficult to achieve the required precision with traditional welding methods.
- Edge Preparation: Laser welding requires minimal edge preparation, which can save time and reduce costs in the production process.
TIG Welding
- Versatile Joints: TIG welding can be used in a variety of joint configurations, including butt joints, lap joints, corner joints, and T-joints. The process can be adapted to different positions and orientations.
- Accessibility: TIG welding requires access to the joint area for both the welding gun and the filler material. In some cases, this can limit its suitability in narrow or hard-to-reach spaces.
Throughput and Speed
Laser Welding
- High-Volume Production: Laser welding is well suited for high-volume production due to its high speed and automation capabilities. Industries such as automotive and electronics benefit from the increased throughput and consistency provided by laser welding systems.
- Cycle Time: Fast welding speeds reduce cycle time, making laser welding an effective choice for mass production.
TIG Welding
- Low to Medium Volume: TIG welding has slower welding speeds than laser welding, so it is often used for low to medium-volume production.
- Customization: The manual nature of TIG welding allows for customization and flexibility in low-volume production, prototyping, and repair work.
Precision and Quality Requirements
Laser Welding
- High Precision: Laser welding offers exceptional precision, making it ideal for applications requiring tight tolerances and complex welds.
- Weld Quality: The process produces clean, high-quality welds with minimal spatter and oxidation. A small heat-affected zone reduces thermal distortion and maintains the mechanical properties of the material.
TIG Welding
- Control and Quality: TIG welding offers excellent control over the welding process, resulting in high-quality, aesthetically pleasing welds.
- Filler Materials: The ability to add filler materials during TIG welding helps achieve strong, durable welds, especially in thicker sections or joints that require reinforcement.
Cost Considerations
Laser Welding
- Initial Investment: The high initial investment in laser welding equipment, including the laser generator, optics, and automation systems, can be a barrier for some applications. However, the long-term benefits of increased productivity and reduced labor costs can offset the initial expense.
- Operating Costs: Laser welding systems have lower operating costs due to reduced consumable use and increased efficiency. Automation potential further reduces labor costs.
TIG Welding
- Lower Initial Cost: TIG welding equipment has a lower initial cost compared to laser welding systems, making it suitable for smaller operations and workshops.
- Consumable Costs: TIG welding involves consumable costs for tungsten electrodes, filler rods, and shielding gas. These ongoing expenses can add up, especially in high-volume applications.
- Labor Costs: TIG welding is labor-intensive and requires a skilled welder, which can increase labor costs, especially for complex or detailed work.
Selecting the appropriate welding method between laser welding and TIG welding requires evaluating several key factors:
- Material Type and Compatibility: Laser welding is suitable for many metals and some plastics, while TIG welding is suitable for almost all metals.
- Material Thickness: Laser welding excels in thin materials, while TIG welding is suitable for both thin and thick sections.
- Joint Configuration and Accessibility: Laser welding is well suited for complex joints and hard-to-reach areas, while TIG welding is suitable for a variety of joint configurations but requires the use of a welding gun and filler material.
- Production Volume and Speed: Laser welding is suitable for high-volume production with fast cycle times, while TIG welding is more suitable for small to medium-volume production and custom work.
- Precision and Quality Requirements: Laser welding offers superior precision and minimal heat distortion, while TIG welding offers excellent control and high-quality welds with the ability to add filler material.
- Cost Considerations: Laser welding has a higher initial investment but lower operating costs and labor savings, while TIG welding has a lower initial cost but higher consumable and labor costs.
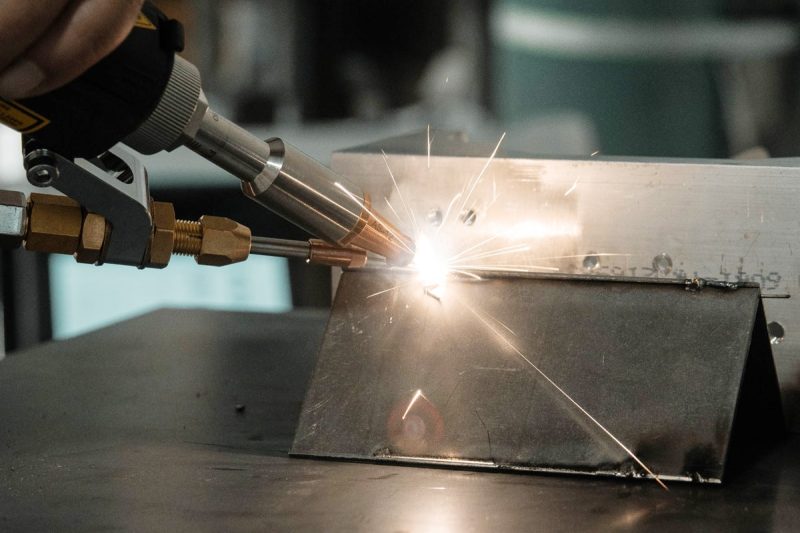
Applications
Laser Welding
Automotive Industry
- Component Welding: Laser welding is widely used in the automotive industry to weld complex components such as gears, transmission components, and sensors. The precision and speed of laser welding ensure high-quality, reliable joints for critical components.
- Body Panels and Frames: Laser welding is ideal for assembling body panels and frames because of its ability to weld thin materials with minimal distortion. It provides strong, clean welds that enhance the structural integrity and aesthetics of the vehicle.
- Battery Manufacturing: With the rise of electric vehicles, laser welding plays a vital role in the manufacturing of battery cells and packs. It ensures precise and strong welds, thereby improving the performance and safety of battery systems.
Aerospace Industry
- Structural Components: The aerospace industry requires high-strength, reliable welds for structural components. Laser welding is used to join components made from advanced materials such as titanium and aluminum alloys, which are common in aircraft and spacecraft.
- Engine Components: Precision and strength are critical for engine components. Laser welding provides the necessary precision and quality for welding engine components, ensuring they can withstand extreme conditions and pressures.
Medical Devices
- Surgical Devices: The medical industry requires precision and cleanliness. Laser welding is used to manufacture and repair surgical instruments, ensuring high-quality, sterile welds.
- Implants: Medical implants such as pacemakers and orthopedic devices require reliable and biocompatible welds. Laser welding provides the precision and control required to produce these critical components.
Electronics
- Microelectronics: The miniaturization of electronic devices requires precise welding techniques. Laser welding is used to assemble microelectronic components, ensuring a strong and accurate connection of small and delicate parts.
- Sensors and Connectors: Laser welding is used in the production of sensors and connectors, providing reliable and precise welds that increase the functionality and durability of electronic devices.
- Jewelry Design and Repair: Laser welding is popular in the jewelry industry and can be used to create intricate designs and repair delicate jewelry. Its precision and minimal heat input ensure high-quality welds without damaging surrounding materials.
TIG Welding
Aerospace Industry
- Critical Components: TIG welding is used to weld critical components in the aerospace industry, such as fuselage sections, fuel tanks, and landing gear. The process ensures strong, reliable welds that can meet the rigorous demands of aerospace applications.
- Repair and Maintenance: TIG welding is also used in the repair and maintenance of aircraft components, precisely controlling the welding process and producing high-quality welds that restore structural integrity.
Automotive Industry
- Exhaust Systems: TIG welding is commonly used to manufacture and repair automotive exhaust systems. The process provides clean, strong welds that can withstand high temperatures and corrosive environments.
- Frames and Chassis: The automotive industry uses TIG welding to assemble and repair vehicle frames and chassis. The versatility and precision of TIG welding make it suitable for working with a wide range of materials and thicknesses.
Construction
- Structural Welding: TIG welding is used to weld structural components such as pipelines, bridges, and buildings. The process ensures high-quality welds that help improve the safety and durability of the structure.
- Architectural Elements: The aesthetics of TIG welding make it suitable for architectural elements where strength and appearance are important, such as railings and decorative structures.
Food and Beverage Industry
- Stainless Steel Equipment: The food and beverage industry requires high-quality, sanitary welds on stainless steel equipment and tanks. TIG welding provides clean, precise welds that meet the industry’s exacting standards.
- Piping Systems: TIG welding is used to join stainless steel piping systems in food and beverage processing plants. The process ensures leak-free, sanitary welds that help maintain product quality and safety.
Art and Sculpture
- Metal Artwork: Artists and sculptors use TIG welding to create detailed and intricate metal artwork. The precision and control provided by TIG welding allow artists to produce high-quality, beautiful pieces.
- Sculpture Restoration: TIG welding is also used to repair and restore metal sculptures, providing strong and clean welds to preserve the integrity and appearance of the artwork.
Application Comparison
Both laser welding and TIG welding have their applications, which are often determined by the specific requirements of the industry and the nature of the workpieces involved:
- Precision and Speed: Laser welding excels in applications that require high precision and speed, such as microelectronics, medical devices, and automotive components. Minimal heat input and high welding speeds increase productivity and quality in these industries.
- Versatility and Weld Quality: TIG welding is favored for its versatility and ability to produce high-quality welds on a wide range of materials and thicknesses. Industries such as aerospace, automotive, and construction rely on TIG welding to weld critical components and structures.
- Material Compatibility: Laser welding is particularly effective for welding dissimilar materials and advanced alloys, making it suitable for high-tech and specialized applications. TIG welding has a wider range of material compatibility and excellent control capabilities, making it widely used in industries that require delicate and high-quality welds.
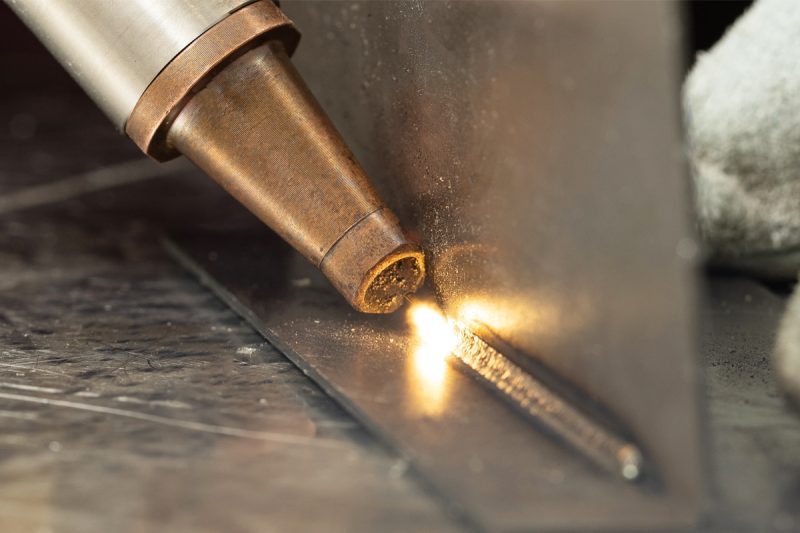
Summary
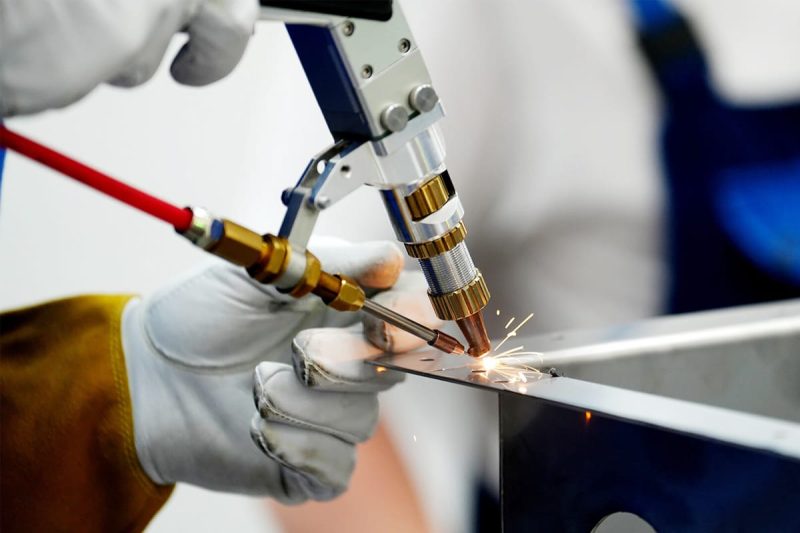
Get Laser Welding Solutions
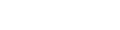
- [email protected]
- [email protected]
- +86-19963414011
- No. 3 Zone A, Lunzhen Industrial Zone,Yucheng City , Shandong Province.