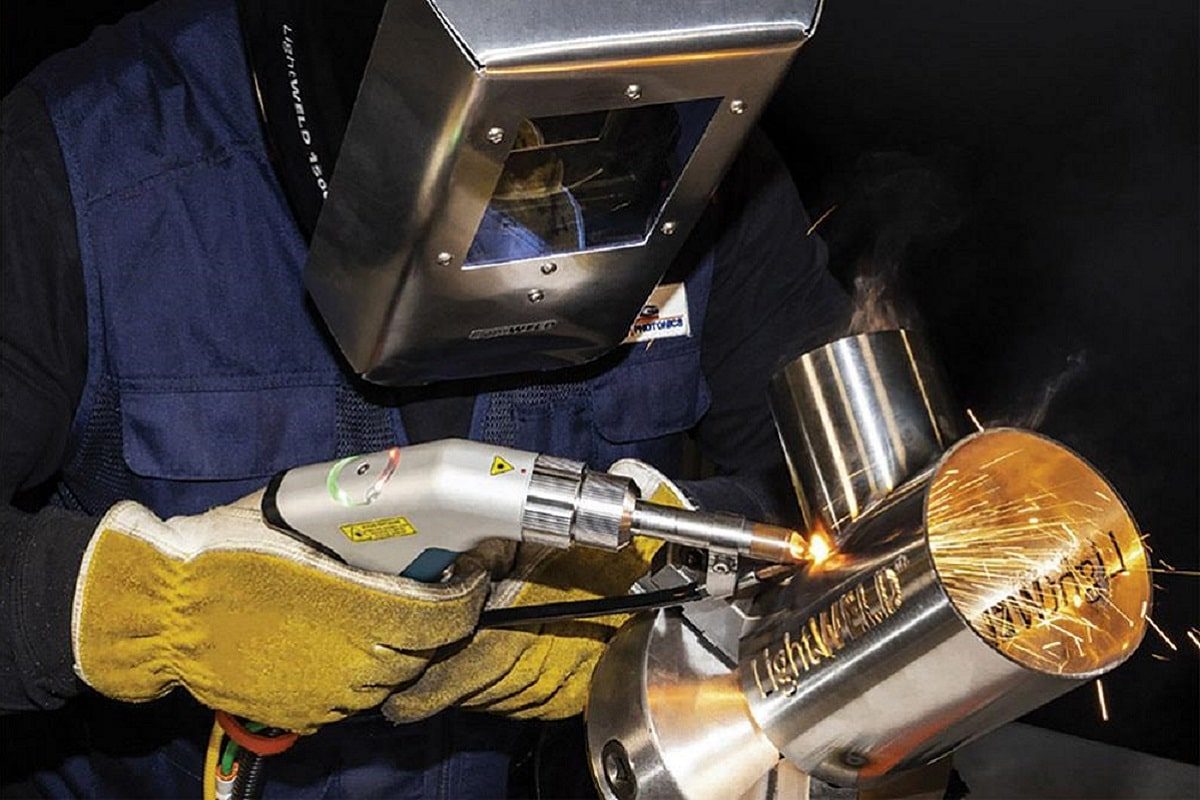
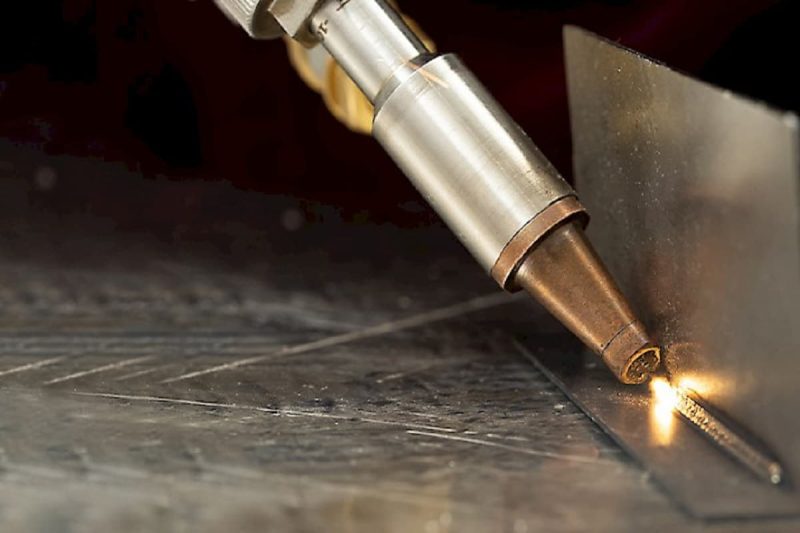
What is laser welding?
How laser welding works
Laser welding uses a focused laser beam to join metal or thermoplastic. Can be used in many industries from aerospace and medical devices to fine jewelry manufacturing. The following is the basic working principle of laser welding:
- Laser source: Commonly used laser sources include carbon dioxide laser generators, fiber laser generators, and diode laser generators. These laser sources are capable of producing monochromatic, highly coherent, and highly directional laser beams.
- Beam focusing: The laser beam needs to be focused through a lens or reflector to concentrate the energy of the beam into the welding area to quickly heat the workpiece.
- Absorption and conduction: After the laser beam irradiates the surface of the workpiece, the energy will be absorbed by the workpiece instead of reflected. The extent to which laser energy is absorbed depends on the type and color of the material.
- Melting and fusion: The high energy density of the laser beam will quickly heat the welding area above the melting point, causing the workpiece material to melt instantly.
- Cooling and solidification: Once the laser beam stops irradiating, the welding area cools rapidly and the molten metal solidifies. The workpieces have been firmly connected.
Advantages of laser welding
Laser welding is very versatile and can be combined with traditional arc welding to form hybrid laser arc welding. The resulting weld combines the advantages of laser welding and arc welding. Laser welding has several advantages over traditional welding technologies, including:
- High precision: Laser welding has very high positioning accuracy and weld quality, and can achieve micron-level welding accuracy. The welds produced by laser welding are also generally of higher quality, making them particularly suitable for applications that require high-precision welding, such as microelectronics manufacturing and medical devices.
- Contactless: Laser welding is a non-contact process that does not damage the workpiece surface and does not require physical contact. Very advantageous when working with brittle materials or delicate parts in laser welding.
- Environmental protection: Compared with traditional welding, laser welding usually produces less waste and harmful gas emissions and is more environmentally friendly.
- Low heat input: The heat input of laser welding is low because the welding area is very small, reducing deformation and the size of the heat-affected zone. This is very important when welding thin sheet materials and heat-sensitive components.
- Faster processing time: Laser welding is fast and can quickly complete welding tasks and improve production efficiency. In addition, laser welding does not require filler materials, reducing material waste. And, the process has proven to be more cost-effective than traditional welding.
- Wide applicability: Laser welding can be used on a variety of materials, including metals, plastics ceramics, etc., which makes it widely used in various industrial fields.
- Laser welding is very versatile and can be combined with traditional arc welding to form hybrid laser arc welding. The resulting weld combines the advantages of laser welding and arc welding.
Disadvantages of laser welding
Laser welding is a modern welding technology with high precision and efficiency, but it also has some shortcomings and limitations. Here are some of the main disadvantages of laser welding:
- High cost: The purchase and maintenance costs of laser equipment are relatively high, including laser generators, optical components, cooling systems, etc. This may limit the adoption of laser welding by smaller businesses or manufacturers with limited budgets.
- High material selection requirements: Laser welding has relatively high requirements on the material and quality of the workpiece. It is more suitable for highly conductive materials, such as metals, while for some non-conductive or transparent materials, its application range is limited.
- Difficulty in processing high melting point materials: Compared with high melting point materials, such as tungsten, molybdenum, etc., laser welding requires higher power and longer welding time, which may lead to thermal effects and deformation problems.
- High cleaning requirements: Laser welding has very high requirements for the quality of the workpiece surface. Even tiny stains, oxide layers, or grease may affect the welding quality. Therefore, careful surface preparation and cleaning is usually required before welding.
- Safety issues: Laser beams have high energy and may cause damage to human eyes and skin. Therefore, operators need to take necessary safety measures, such as wearing appropriate protective glasses and clothing.
- Visible light interference: Visible light lasers are likely to be interfered with by visible light, which requires measures to ensure that the light in the work area is properly controlled.
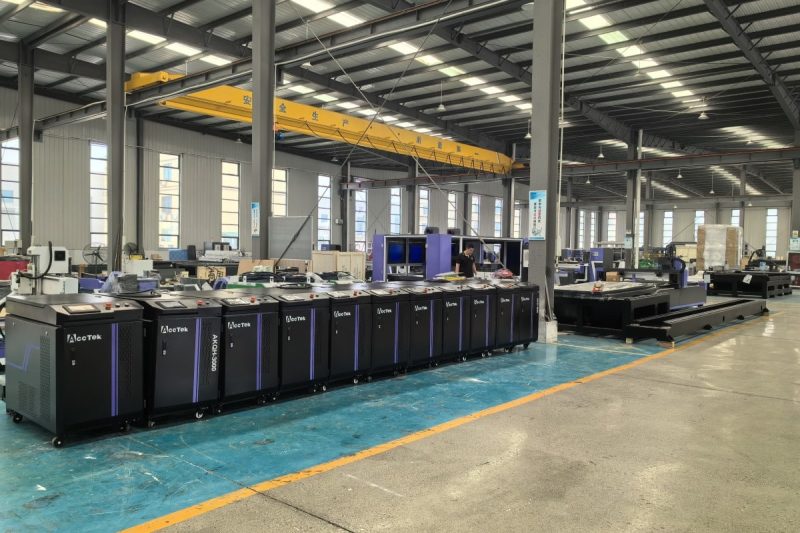
What is traditional welding?
How Traditional Welding Works
Conventional welding techniques are a set of traditional methods for joining metals or other materials that have been around for many years and are used in a wide variety of manufacturing and repair fields. Here are some common traditional welding techniques:
- Arc welding: Arc welding is a common traditional welding method that uses an arc to generate high temperatures to melt the welding materials and workpieces, and then cool and solidify them to form a weld. The main arc welding methods include manual arc welding, gas-shielded welding (MIG), manual metal arc welding (SMAW/ARC), and TIG welding (GTAW).
- Gas welding: Using a flame to heat welding materials, melting them, and joining them. The most common gas welding method is acetylene-oxygen welding, which uses a flame of acetylene and oxygen to heat the workpiece and is suitable for sheet metal, pipes, and metal repairs.
- Resistance welding: Joining two metal pieces together by using an electric current to pass through the workpiece to generate heat. The main resistance welding methods include spot welding, seam welding, and soldering.
- Pressure Welding: Pressure welding is a method of joining two pieces of metal together through the application of heat and pressure and includes resistance spot welding, resistance seam welding, and electronics.
Advantages of traditional welding
However, traditional welding processes remain a durable manufacturing solution for many industries, and laser welding offers several advantages over traditional welding methods. The specific points are as follows:
- Low cost: Traditional welding equipment is generally relatively inexpensive, and training operators is less expensive. This reduces initial investment and operating costs and is suitable for businesses with limited budgets.
- Widely applicable: Traditional welding technology can be used on a variety of different types of materials, from metals to plastics, and on sheets of various thicknesses. This versatility makes it suitable for a variety of applications.
- Welding large structures: Traditional welding techniques are suitable for welding large structures such as bridges, buildings, and shipbuilding. It has strong connectivity and applicability.
- Durability: Traditional welding techniques generally produce strong connections, suitable for applications requiring high-strength connections, such as vehicles and engineering structures.
- Automation application: Traditional welding technology can be combined with automation and robotics to improve production efficiency, especially for mass production.
- Substrate adaptability: Traditional welding methods are suitable for various types of substrates, including different kinds of metallic and non-metallic materials.
- Repair and Restoration: Traditional welding techniques still have an important role in repair and maintenance, especially when away from power sources or in complex environments.
- Fusion Depth: Conventional welding typically has a larger weld depth and is suitable for applications requiring deeper welds.
- Availability of welding materials: Traditional welding methods often use common filler materials, which are often readily available.
Disadvantages of traditional welding
Traditional welding technologies still have value in many applications, but they also have some disadvantages and limitations. Here are some of the main disadvantages of traditional welding technologies compared to laser welding technologies:
- Lower accuracy: The welding process may produce large weld widths and heat-affected zones, which may lead to workpiece deformation, dimensional instability, or inaccuracies in the welded connection.
- Large thermal impact: The heat input generated by traditional welding technology is relatively high, which can easily cause large-scale thermal impact on the workpiece, which may adversely affect the performance and quality of the workpiece, especially in the case of heat-sensitive materials.
- Lower production efficiency: Traditional welding usually requires a relatively long welding time because of the slow welding speed. This limits the efficiency of large-scale production and may increase manufacturing costs.
- Higher waste and gas emissions: Traditional welding usually requires more filler materials and waste materials and produces large amounts of waste and harmful gas emissions, which hurt the environment.
- Large safety risks: The flames and heat spatter generated during traditional welding may cause danger to operators and the surrounding environment.
- Cleaning and post-processing requirements: Traditional welding processes often require subsequent cleaning and processing steps to remove welding residues or improve weld quality,this increases production time and cost.
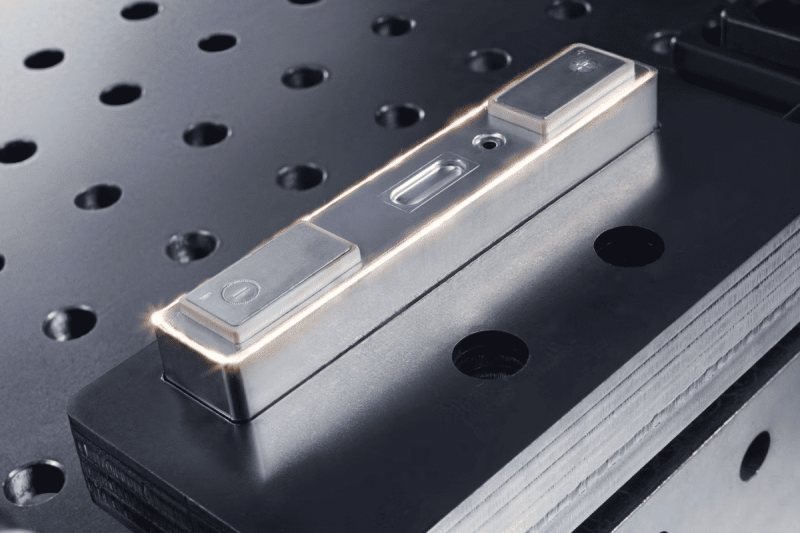
Laser welding VS conventional welding: which welding method to choose?
Material type
Accuracy requirements
Thermal impact
Production efficiency
Cost considerations
Material thickness
Environmental and safety requirements
Summarize
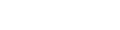
- [email protected]
- [email protected]
- +86-19963414011
- No. 3 Zone A, Lunzhen Industrial Zone,Yucheng City , Shandong Province.