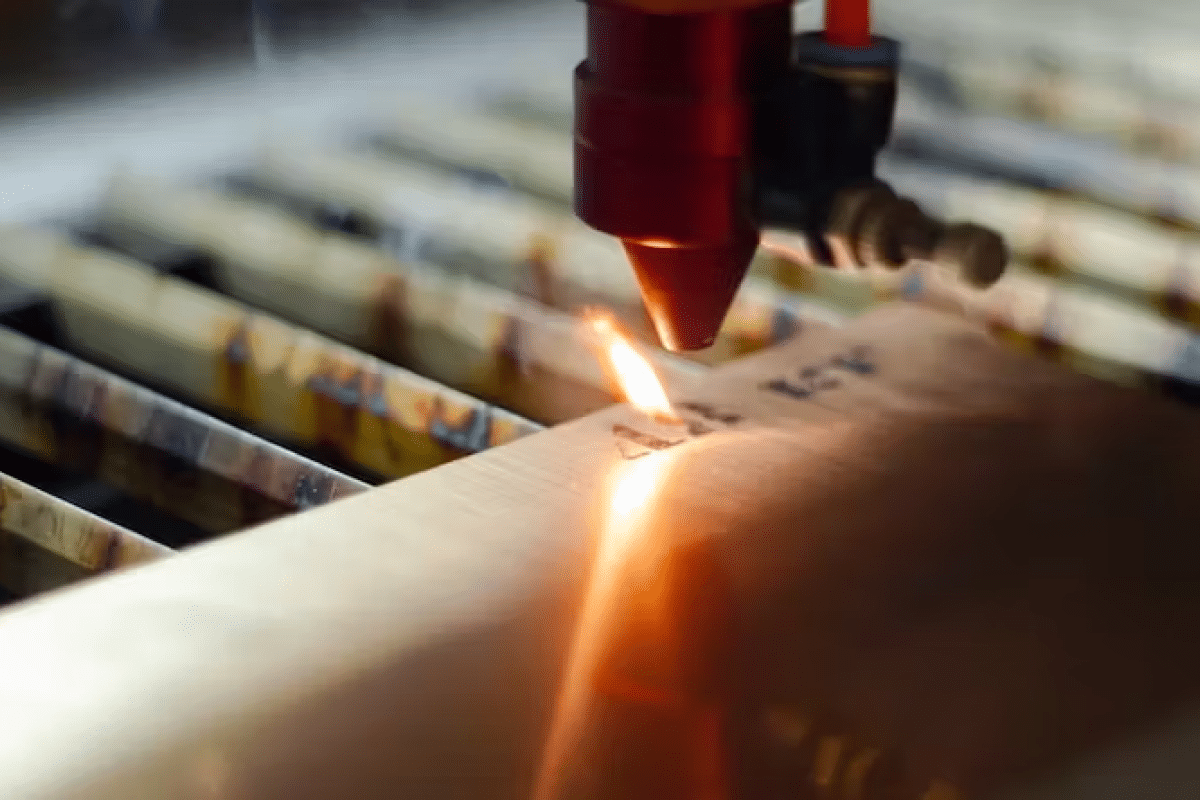
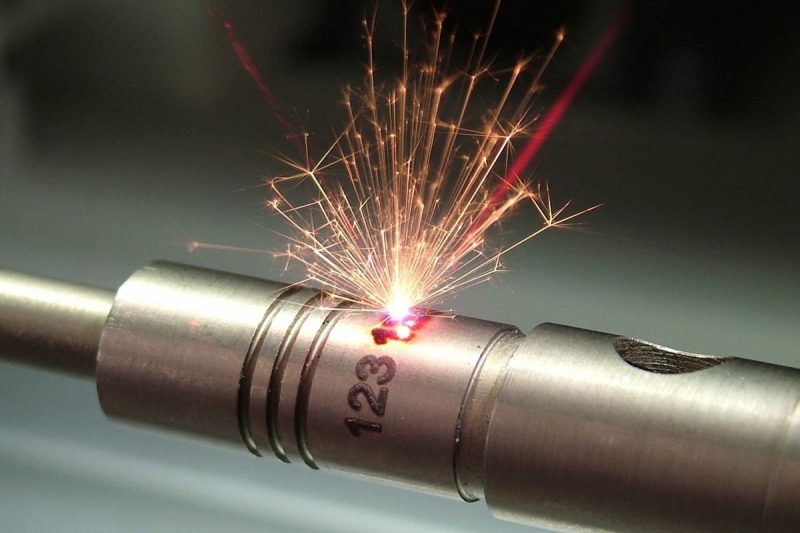
Basic principles of laser marking machine
A laser marking machine is a device that uses a laser beam to mark, etch, or cut the surface of a workpiece. The basic principle involves the emission, focusing, and action of laser light on the workpiece surface. The following are the basic principles of laser marking machines:
- Laser emission: Laser marking machines use laser generators as light sources. Laser generators usually use materials such as gas, solid, or semiconductor to generate laser light through energy level transitions. These laser generators can release high-energy, high-purity beams in a very short time.
- Modulation of laser: The laser beam emitted by the laser generator is modulated, and power control, frequency adjustment, and pulse width adjustment can be performed as needed. This modulation enables the laser to achieve optimal results under different process requirements.
- Focusing of the beam: The laser marking machine focuses the laser beam to a very small focus through the optical system. The focused laser beam can reach extremely high energy density to produce the desired marking, etching, or cutting effects on the workpiece surface.
- Acting on the workpiece surface: The focused laser beam is guided to the workpiece surface. By controlling the movement path and parameters of the laser beam, various shapes of marks, text, or patterns can be formed on the workpiece surface. At the same time, the high energy of the laser can also produce effects such as vaporization, heat melting, or chemical reactions on the surface of the workpiece to achieve different processing effects.
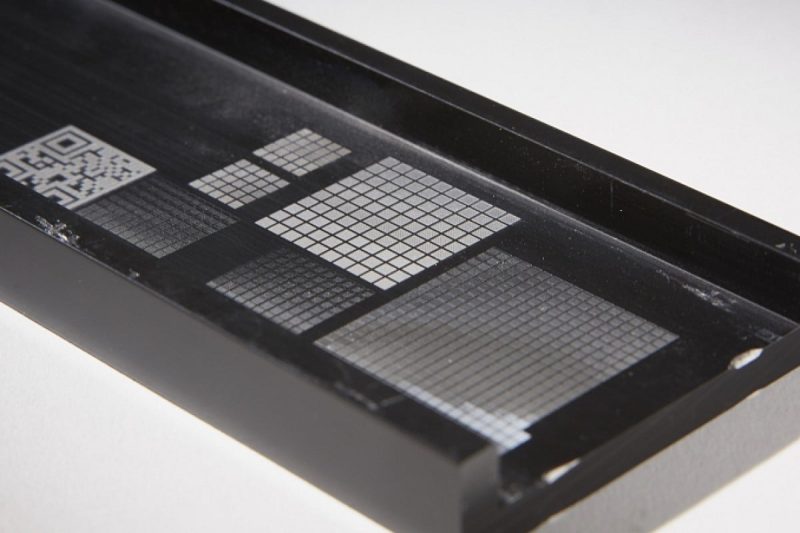
Maintenance requirements related to laser marking
To ensure that laser marking equipment can operate stably for a long time and maintain high-quality marking effects, regular maintenance is required. The following are maintenance requirements related to laser marking:
- Cleaning and Dusting: Regularly clean the mirrors, lenses, and work surfaces of laser marking equipment to ensure the quality and output power of the laser beam. At the same time, remove dust and debris in and around the device to prevent it from affecting the normal operation of the device.
- Lubrication and maintenance: The moving parts of the equipment, such as bearings and guide rails, need to be lubricated regularly to reduce friction and wear. At the same time, regularly check the transmission system and optical path of the equipment to ensure its normal operation and replace worn parts promptly.
- Optical system adjustment: Regularly calibrate the focus and alignment of the laser beam to ensure precision and consistency of marking results. Check the working status and output power of the laser generator, and promptly adjust and replace damaged laser generator components.
- Cooling system maintenance: The cooling system is the key to the normal operation of the laser generator. The filters and water pumps in the cooling system need to be cleaned and replaced regularly to maintain the normal operating temperature and stability of the laser generator. Check coolant concentration and flow to ensure cooling system efficiency and performance.
- Electrical system maintenance: Regularly check the electrical connections and grounding conditions of the equipment to ensure the electrical safety of the equipment. At the same time, check the wear degree of cables and switches, and replace aging or damaged parts in time.
- Safety protection device inspection: Regularly check the functions of safety doors, warning lights, and other protective devices of laser marking equipment to ensure the safety of operators when the equipment is working.
- Operating procedures training: Establish strict operating procedures and provide adequate training to operators so that they understand the safe operation methods and emergency response measures of laser marking equipment.
- Logging and Monitoring: Record the operating status, maintenance records, and alarm information of the equipment, monitor and inspect the equipment regularly, and discover and solve potential faults promptly.
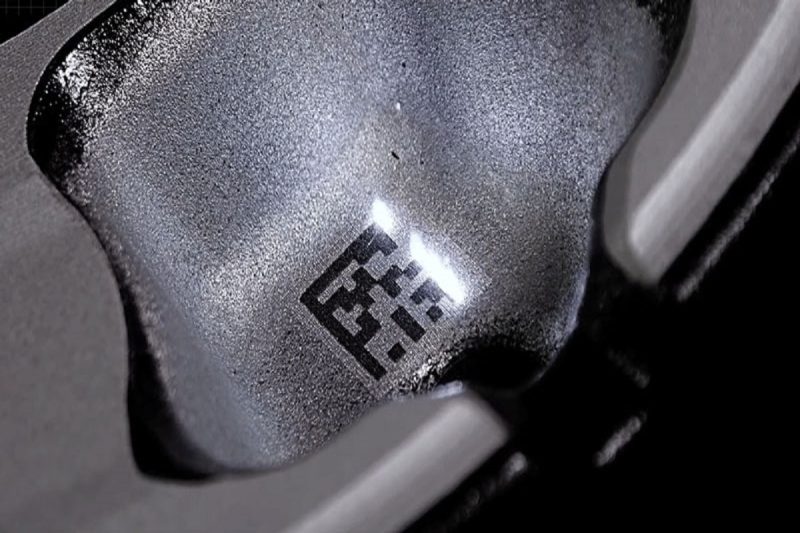
Repair requirements related to laser marking
During the long-term operation of the laser marking machine, it is inevitable that the machine will malfunction or be damaged and the laser marking machine will need to be repaired. Maintenance requirements related to laser marking include the following aspects:
- Laser maintenance: The laser generator is the core component of laser marking equipment. If the laser generator fails or is damaged, the equipment may not work properly. Therefore, it is necessary to regularly check the working status and output power of the laser generator to discover and solve possible problems with the laser generator promptly. If the laser generator fails, it may be necessary to replace the damaged laser generator component or the entire laser generator, which usually requires repair by a professional technician.
- Optical system adjustment: The precision and alignment of the optical system are critical to the quality of laser marking. If there is deviation or misalignment in the optical system, the marking effect may be unsatisfactory. Therefore, it is necessary to regularly check the adjustment of the optical system, adjust and calibrate the optical components in time, and ensure the focus and alignment of the laser beam.
- Cooling system repair: The cooling system is an important part of laser marking equipment. If the cooling system fails, it may cause the laser generator to overheat and fail to work properly. Therefore, it is necessary to regularly check the working status of the cooling system and the operation of water pumps, filters, and other components, and promptly clean, replace, or repair components that may have problems.
- Electrical system maintenance: The electrical system of laser marking equipment includes cables, switches, control boards, and other components. If the electrical system fails or is short-circuited, the equipment may not be powered on or controlled normally. Therefore, it is necessary to regularly check the electrical connections and grounding conditions, and promptly replace aging or damaged cables, switches, and other components to ensure the electrical safety of the equipment.
- Safety protection device maintenance: Laser marking equipment should be equipped with effective safety protection devices, such as laser safety doors, warning lights, etc. If the safety protection device fails, it may pose a threat to the safety of the operator. Therefore, safety protection devices need to be inspected and repaired regularly to ensure their normal function.
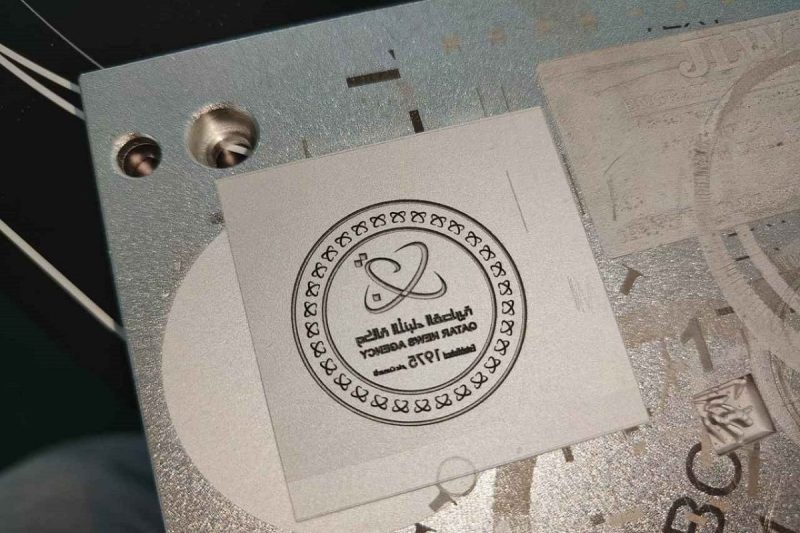
Safety considerations for laser marking equipment
Laser marking equipment involves high-energy laser beams during use, so safety issues are of paramount importance. The following are safety considerations for laser marking equipment:
- Laser radiation safety: The laser beam generated by the laser generator used in laser marking equipment has high energy and may cause harm to the human body. Therefore, measures must be taken to prevent damage to personnel caused by laser radiation. Measures usually taken include setting up safety doors, safety warning signs, and laser beam shielding settings, as well as requiring operators to wear protective glasses.
- Equipment stability: Laser marking equipment usually needs to be fixedly installed at the production site or on the workbench to ensure that the equipment does not cause accidental injury or damage due to movement or vibration during operation. Stable equipment improves work stability and safety.
- Operator training: Regular maintenance and inspection of all operating laser marking equipment is an important means to ensure the safe operation of the equipment. Regularly check all parts of the equipment to discover and resolve potential safety hazards and failures promptly to prevent accidents during the use of the equipment.
- Safety warning signs: Set obvious safety warning signs around the laser marking equipment to remind personnel to pay attention to the existence of laser radiation and avoid unnecessary approaches and operations. Properly setting safety warning signs can effectively reduce accidental injuries to operators.
- Emergency stop device: Laser marking equipment should be equipped with an emergency stop device in the event of an emergency. The operator can immediately cut off the power supply of the equipment and take corresponding emergency measures to reduce the losses caused by the accident.
Summarize
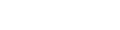
- [email protected]
- [email protected]
- +86-19963414011
- No. 3 Zone A, Lunzhen Industrial Zone,Yucheng City , Shandong Province.