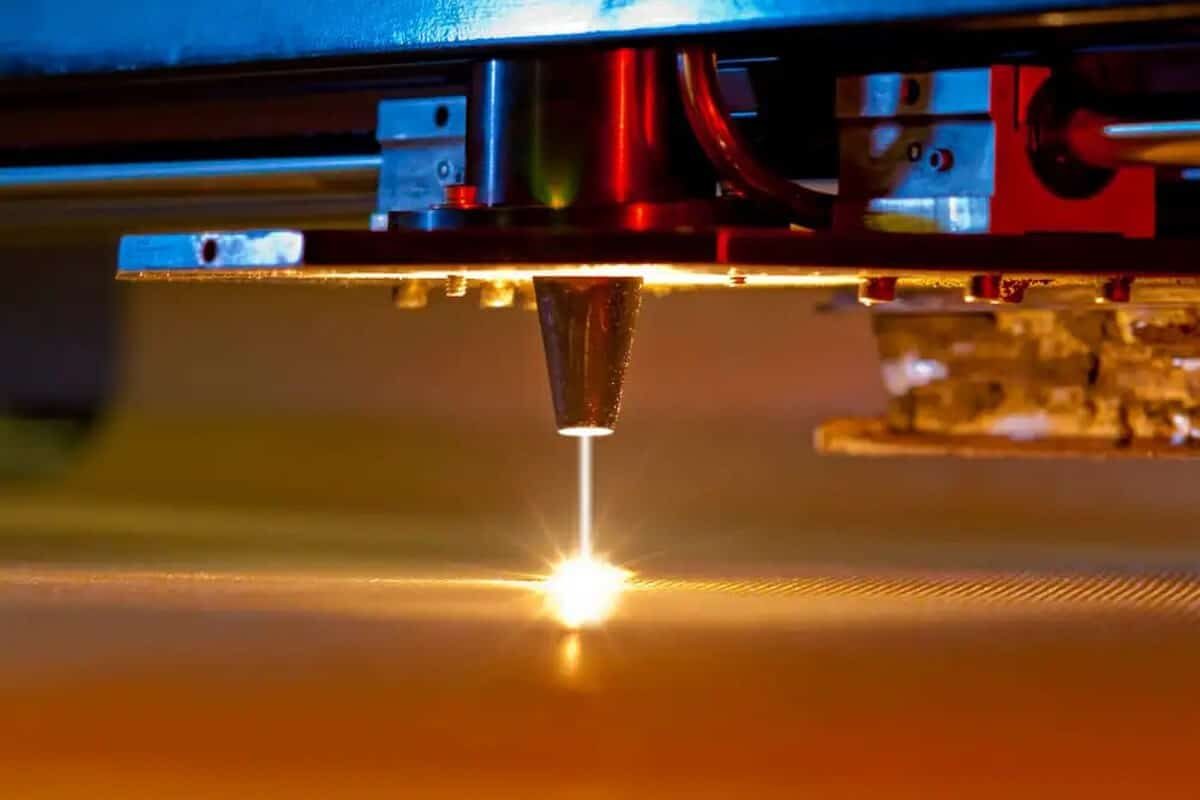
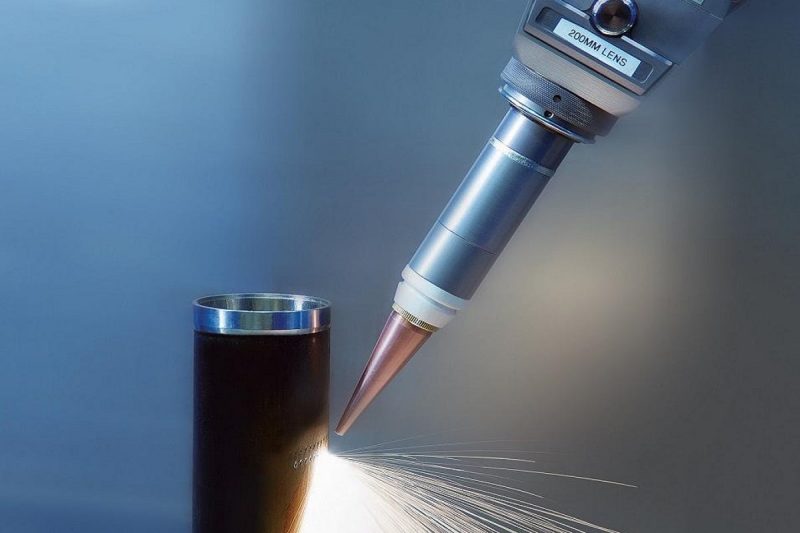
Basic principles of CO2 laser cutting machine
Before discussing the skills and training required to operate a CO2 laser cutting machine, let’s first understand the basic principles of a CO2 laser cutting machine. CO2 laser cutting machine uses a carbon dioxide laser source to focus the laser beam on a small area to locally heat the material to a temperature that instantaneously melts or vaporizes, thereby cutting the material. This process requires highly precise control and operation.
The main working principle of the CO2 laser-cutting machine includes the following steps:
- Laser generator generates laser beam: The laser generator generates a high-energy laser beam by exciting CO2 gas. This laser beam has a single wavelength, usually around 10.6 microns, and is suitable for cutting a variety of materials.
- The laser beam is transmitted to the cutting head: Through the optical system, the laser beam is transmitted to the cutting head, which includes lenses and reflectors to ensure that the laser can be focused on the workpiece surface.
- Focusing and positioning: The cutting head focuses the laser beam to a very small point on the surface of the workpiece, forming a focus with high energy density. At the same time, the precise positioning system ensures that the laser accurately irradiates the predetermined cutting position.
- Instant heating and cutting: When the laser beam is focused on the workpiece surface, the temperature of the area increases instantaneously, causing the material to melt or evaporate locally. This high-temperature state forms a cutting edge to achieve precise cutting of materials.
- CO2 laser cutting machines are suitable for a variety of materials, including metal, plastic, and wood. The key to its working principle is to utilize the high concentration of laser energy, a process that requires highly precise control and operation by the operator.
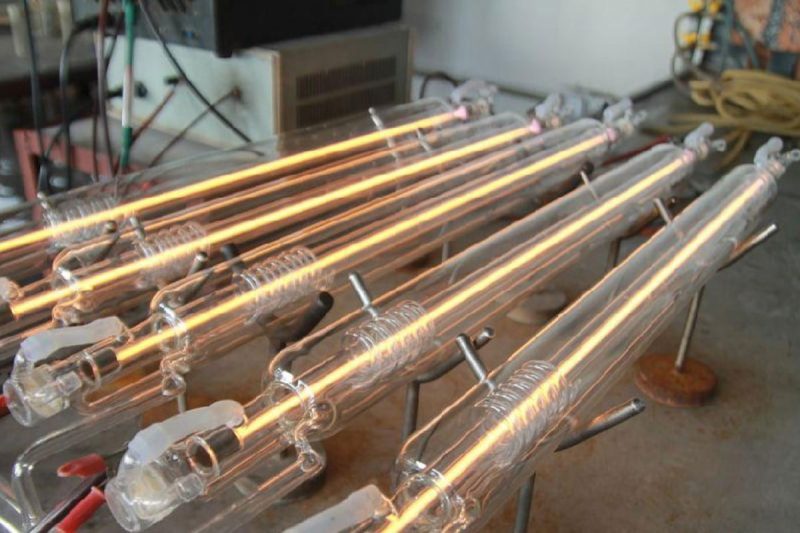
Importance of specific training and skills
The specific training and skills required to operate a CO2 laser cutting machine are critical to ensuring a safe, efficient, and quality cutting process. Here are a few ways these training and skills are important:
- Safety of high-energy lasers: CO2 laser cutting machines use high-energy lasers for cutting, which poses a potential threat to the safety of operators. Training can ensure that operators understand the characteristics of the laser and how to properly use protective equipment, such as laser safety glasses, to reduce the risk to the eyes from the laser.
- Complex machine operation: CO2 laser cutting machines usually have complex control systems and operating interfaces. Operators need to learn how to properly start and shut down equipment, adjust cutting parameters, load and unload materials, and other basic operations to ensure the safe and efficient operation of the machine.
- Understanding of material properties: Different materials respond differently to lasers, so operators need to understand the properties of various materials to adjust the parameters of the cutting machine. Training provides knowledge on cutting requirements and best practices for different materials, ensuring cutting quality and efficiency.
- Programming of cutting programs: Advanced applications require operators to be able to program cutting programs to achieve complex cutting tasks. Training sessions often include the use of cutting software and programming of cutting paths to increase the operator’s skill level.
- Safety awareness and emergency response: When operating a CO2 laser cutting machine, accidents may occur, such as equipment failure or abnormal material reaction. Training can teach operators correct safety awareness and how to respond to emergencies, ensuring that measures can be taken quickly and effectively in unpredictable situations.
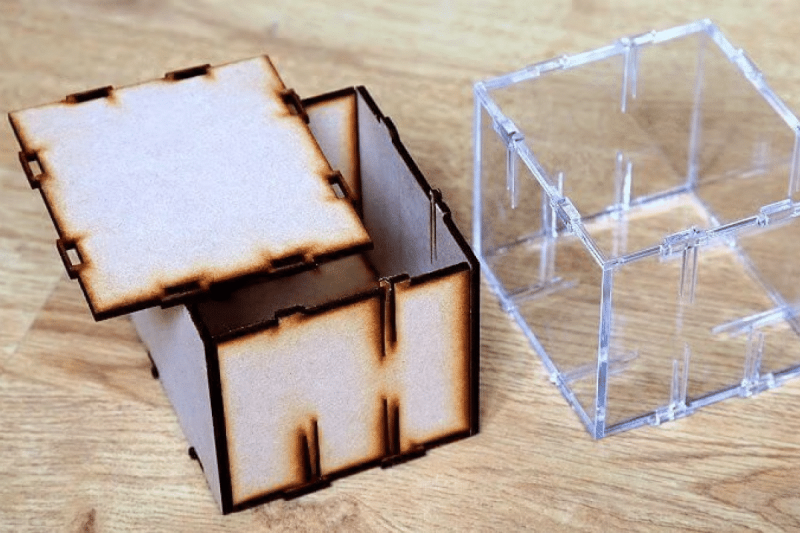
Potential Risks of Operating CO2 Laser Cutting Machines
Operating a CO2 laser-cutting machine involves some potential risks and requires operators to have appropriate safety awareness and training. Here are some possible risks:
- Laser radiation: CO2 laser cutting machines produce high-energy laser beams that may cause damage to human eyes. Direct exposure to laser radiation without appropriate protection may cause eye damage. Therefore, operators should wear laser protective glasses and ensure adequate safety precautions in the work area.
- Fire and smoke: CO2 laser cutting machines may generate high temperatures during the cutting process and cause fires. In addition, the burning of the material can produce toxic fumes. Operators need to understand fire emergency procedures and ensure that equipment and work areas are kept clean to prevent the generation of fire and harmful smoke.
- Mechanical injury: The cutting head and workpiece may cause mechanical injury to the operator when moving at high speed. Training can teach proper operating techniques, including loading and unloading materials and setting cutting parameters to reduce the risk of mechanical injury.
- Material reaction: Different materials react differently to laser light and may produce different gases, vapors, and particles. Reactions with certain materials may result in the release of toxic gases, so operators need to understand the properties of the materials and take appropriate protective measures, such as ventilation systems.
- Equipment failure: The CO2 laser cutting machine may malfunction during long-term operation, such as electrical failure or mechanical failure. Operators need to have troubleshooting skills and know when to shut down and seek professional repairs.
- Chemical Hazards: Exhaust fumes and waste generated during cutting may contain harmful chemicals. Operators need to be aware of these chemical hazards and take appropriate protective measures, such as wearing masks and protective clothing.
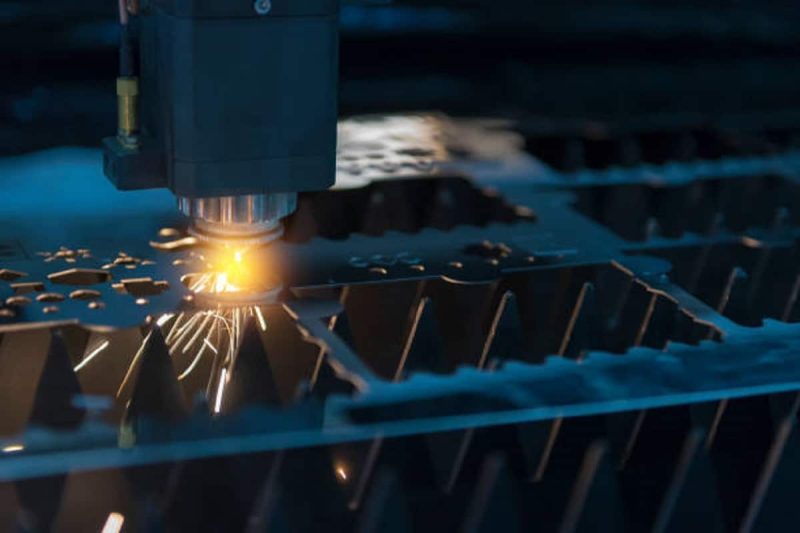
Specific safe operation skills requirements
Operating a CO2 laser cutting machine requires a series of safe operating skills to ensure a safe working environment and avoid accidents. Here are some key safety operations skills required:
- Proper use of laser protective equipment: Laser radiation is potentially harmful to the eyes, so operators should wear appropriate laser protective glasses. These glasses need to be compliant and certified to provide adequate protection.
- Work area identification and safety signs: Ensure that laser operating areas within the work area are properly marked and have appropriate safety signs in place to alert workers that laser operations are taking place.
- Follow equipment startup and shutdown procedures: Operators should be familiar with the correct startup and shutdown procedures for CO2 laser cutting machines to ensure the safe operation of the equipment. This includes steps such as power control of the device and cooling system startup and shutdown.
- Correct operation of the control panel: Proficient in operating the equipment’s control panel, including adjusting cutting parameters, setting cutting paths, and checking machine status. This helps ensure equipment is operating at its best and reduces potential operating errors.
- Safely load and unload materials: Operators need to know how to safely load and unload cutting materials to prevent mechanical injury and ensure a stable cutting process.
- Emergency shutdown procedures: Be familiar with and be able to quickly implement emergency shutdown procedures for equipment to respond to emergencies, such as equipment failure or operating errors. Helps mitigate the consequences of potential accidents.
- Regular maintenance and inspections: Understand the routine maintenance needs of equipment and be able to conduct regular equipment inspections to ensure that it is in optimal working condition. This helps prevent potential mechanical failure and reduces the risk of accidents.
- Clean the work area: Keep the work area tidy and clean up the waste residue and exhaust gas generated by cutting promptly to reduce the risk of fire and chemical hazards.
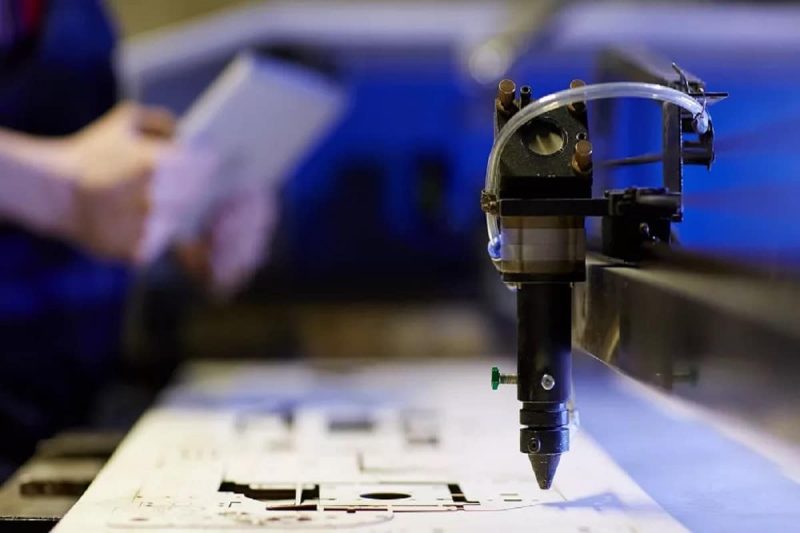
Development Trend of CO2 Laser Cutting Technology
Intelligence and automation
High power and efficiency
Multi-wavelength laser technology
High-precision cutting
Green environmental protection
Fusion laser cutting technology
Remote monitoring and maintenance
Summarize
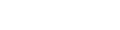
- [email protected]
- [email protected]
- +86-19963414011
- No. 3 Zone A, Lunzhen Industrial Zone,Yucheng City , Shandong Province.