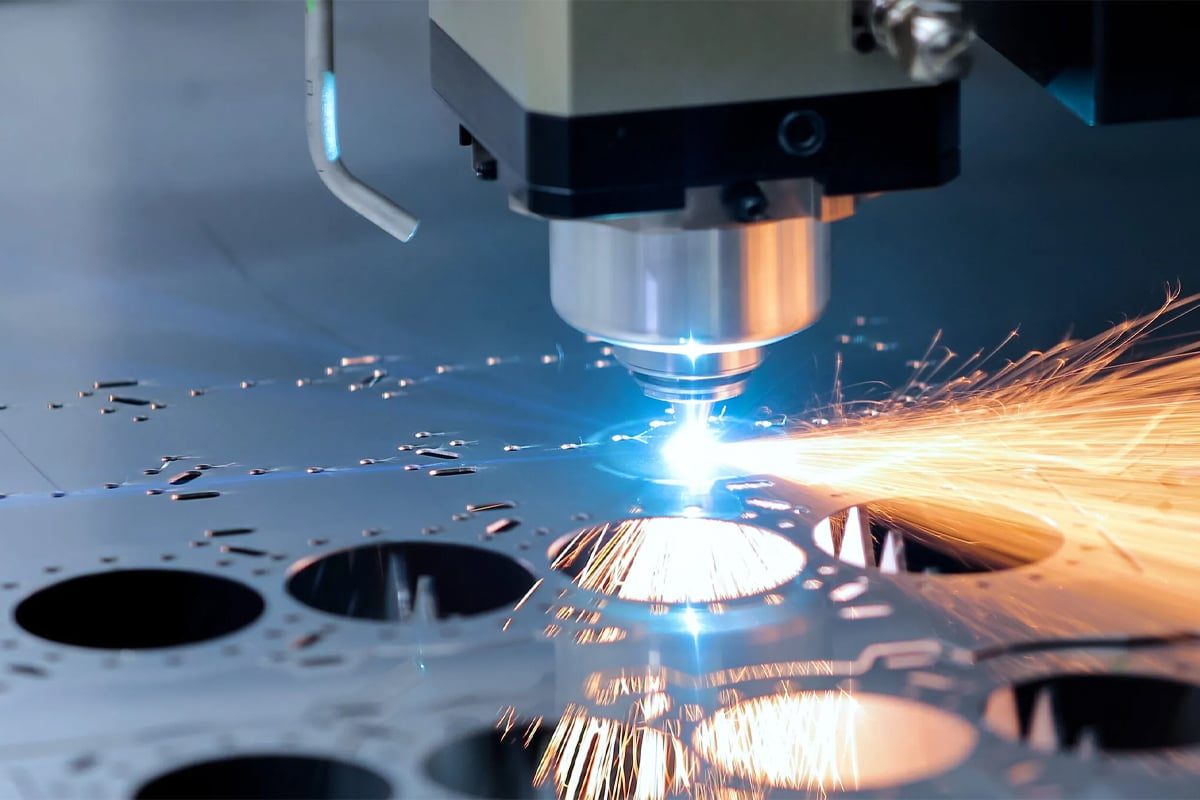
Motor Guide for Laser Cutting Machines
Laser cutting machines have become indispensable tools in modern manufacturing, offering unparalleled precision, speed, and versatility when cutting a wide range of materials. At the heart of these precision machines is the motor system, a critical component that drives the motion of the cutting head and table. The performance, precision, and efficiency of a laser cutting machine depend largely on the type and quality of its motor system.
This article provides a comprehensive look at the different types of motors used in laser cutting machines, including servo motors, stepper motors, and linear motors. We explore their strengths, weaknesses, and applications, helping manufacturers and operators make informed decisions when selecting and optimizing motor systems for specific applications. By understanding the nuances of motor technology, you can improve the performance and reliability of your laser cutting operations, ensure high-quality results, and increase productivity.
Table of Contents

Types of Motors Used in Laser Cutting Machines
Laser-cutting machines rely on various types of motors to achieve precise and efficient movement of the cutting head and crosshead. The choice of motor can significantly affect the machine’s performance, accuracy, and suitability for the application. Next, we explore the three main types of motors used in laser cutting machines: stepper motors, servo motors, and linear motors. Each type has unique characteristics, advantages, disadvantages, and ideal applications.
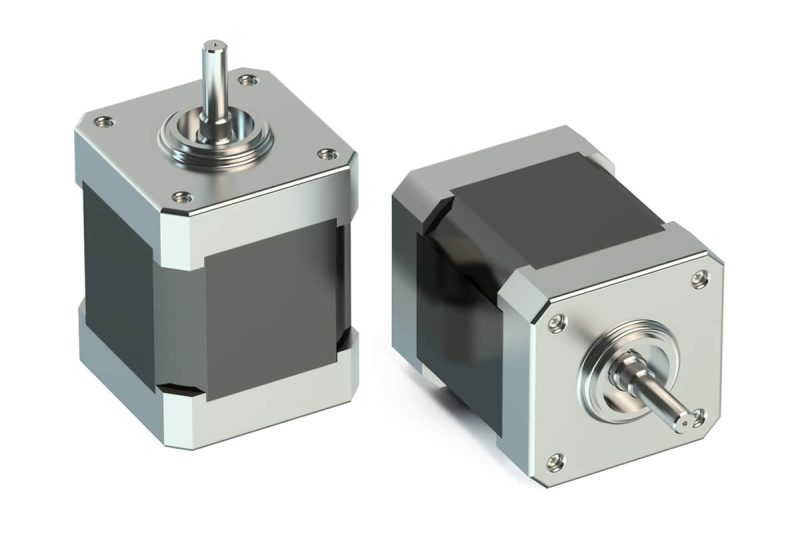
Stepper Motors
Overview
Stepper motors are widely used in laser cutting machines because of their simplicity, reliability, and cost-effectiveness. These motors operate by dividing the entire rotation into a series of equal steps, allowing precise control of angular position without the need for a feedback system. Stepper motors are often used in open-loop systems, where they move in discrete steps based on input pulses from a controller.
Advantages
- Simplicity: Stepper motors are simple in design and easy to control with basic electronics.
- Cost-Effectiveness: They are generally cheaper than servo motors, making them a good choice for budget-conscious applications.
- High Torque at Low Speeds: Stepper motors can produce high torque at low speeds, which is very beneficial for applications that require precise movement.
- Good Holding Torque: They maintain a strong holding torque when stationary, ensuring that the cutting head or table remains in place during operation.
Disadvantages
- Limited Speed: Stepper motors have a limited speed range and tend to lose torque at higher speeds, limiting their use in high-speed applications.
- Heat: They generate a lot of heat during operation, especially at higher currents, which may require additional cooling measures.
- Resonance Issues: Stepper motors can resonate, causing vibration and noise at certain speeds.
- No Feedback Mechanism: The lack of feedback means that if synchronization is missed, the system cannot self-correct, which can cause inaccuracies.
Applications
- Entry-Level and Budget Machines: Ideal for small workshops and educational environments where cost is a major consideration.
- 2D Cutting Applications: Ideal for tasks that do not require extremely high speeds, such as cutting thin materials.
- Prototyping and Hobbyist Projects: Commonly used in DIY laser cutters and other small applications.
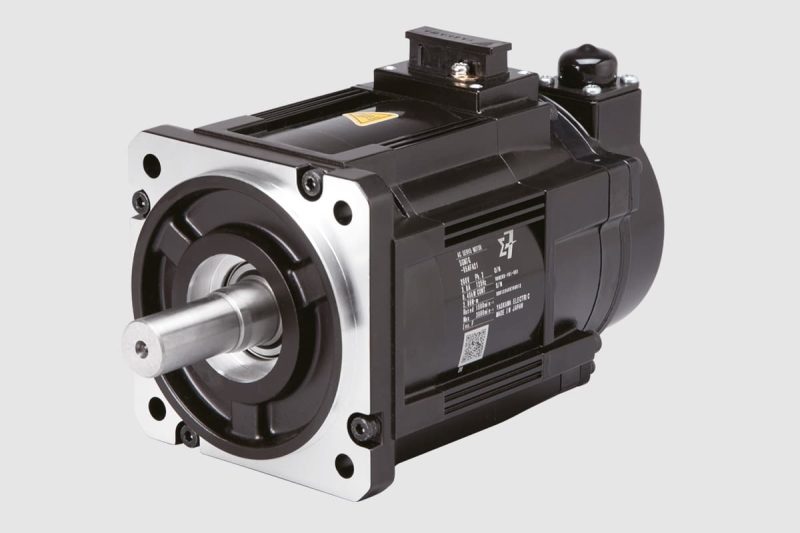
Servo Motors
Overview
Servo motors are known for their high precision, high efficiency, and ability to provide controlled motion over a wide speed range. Unlike stepper motors, they operate using a closed-loop system that involves feedback from sensors to ensure that the motor accurately follows the desired path. This makes servo motors ideal for applications that require complex motion control and high-speed operation.
Advantages
- High Precision and Accuracy: Servo motors have excellent control capabilities over position, speed, and torque, making them ideal for high-precision applications.
- Fast Response Time: They respond quickly to control signals, allowing for rapid changes in direction and speed.
- Maintaining Torque at High Speeds: Servo motors maintain their torque capabilities over a wide speed range, providing consistent performance.
- Feedback Mechanism: Closed-loop control systems ensure that any position errors are corrected in real-time, improving accuracy and reliability.
Disadvantages
- Cost: Servo motors are generally more expensive than stepper motors, both for the motor itself and the associated control system.
- Complexity: The need for feedback systems and complex controllers increases the complexity of the system, requiring more advanced technical knowledge to set up and maintain.
- Possibility of Overheating: High-performance servo motors generate a lot of heat, requiring an effective cooling system.
- Maintenance: Servo motors may require more maintenance due to their complex design and the need for additional components such as encoders.
Applications
- High-Precision Cutting: Used in high-end laser cutting machines for industries where precision is critical, such as aerospace and medical device manufacturing.
- High-Speed Operation: Ideal for applications that require fast cutting speeds, such as automotive and electronics manufacturing.
- Complex Motion Control: Ideal for tasks involving complex motion and curves, benefiting from the precise control capabilities of servo motors.
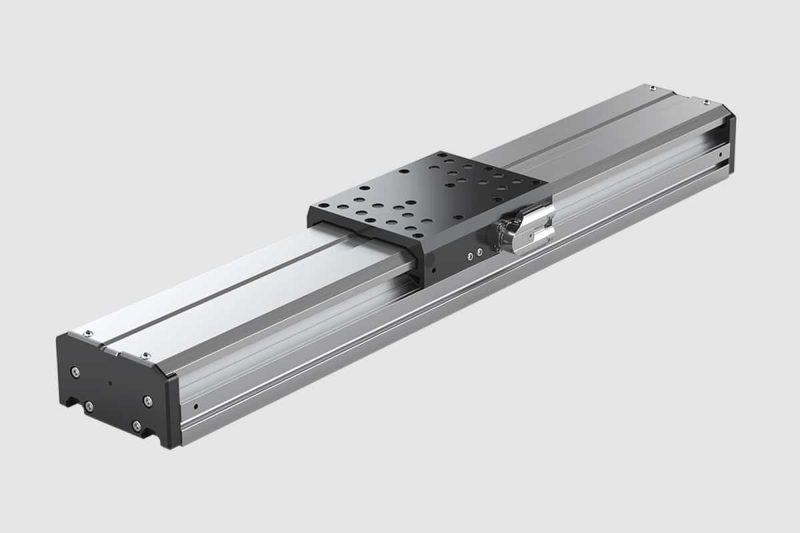
Linear Motors
Overview
Linear motors provide direct linear motion without mechanical conversion from rotary to linear motion. They are essentially flat rotary motors with a fixed magnet track and moving coil assembly. Linear motors provide high-speed and high-precision linear positioning for applications that require fast and accurate linear motion.
Advantages
- Direct Linear Motion: No mechanical conversion mechanism is required, reducing potential failure points and mechanical losses.
- High Precision and High Speed: Capable of very high speeds and precise linear positioning, ideal for high-speed cutting operations.
- Smooth Operation: Provides smooth, continuous motion without the cogging or stepping effects associated with rotary to linear conversion systems.
- High Efficiency: Due to the direct conversion of electrical energy to linear motion, linear motors are more efficient than traditional motor systems.
- Low Maintenance: Fewer moving parts, lower maintenance requirements, and higher reliability.
Disadvantages
- Cost: Linear motors are generally more expensive than stepper and servo motors, both in terms of initial cost and integration cost.
- Complex Installation: Requires precise alignment and mounting, increasing setup time and complexity.
- Limited Availability: Not as widely available as traditional motors, which can limit replacement or customization options.
- Thermal Management: High-speed operation generates a lot of heat, requiring an effective thermal management solution.
Applications
- Advanced Manufacturing: Used in high-end laser cutting machines for industries that require superior precision, such as semiconductor and aerospace manufacturing.
- High-SpeedMachining: Ideal for applications that require high-speed linear motion, such as textile cutting and large-format sheet metal processing.
- Precision Engineering: Suitable for tasks involving detailed and complex cutting patterns, benefiting from the high accuracy and smooth operation of linear motors.
Understanding the types of motors used in laser cutting machines can help select the right motor system to meet specific application requirements. Stepper motors provide a cost-effective solution with good accuracy for small and simple machines. Servo motors provide high accuracy, high speed, and dynamic response for demanding industrial applications. Linear motors provide unmatched linear positioning accuracy and speed for advanced manufacturing processes. By carefully considering the advantages, disadvantages, and applicable applications of each motor type, manufacturers and operators can optimize their laser-cutting machines for improved performance and productivity.
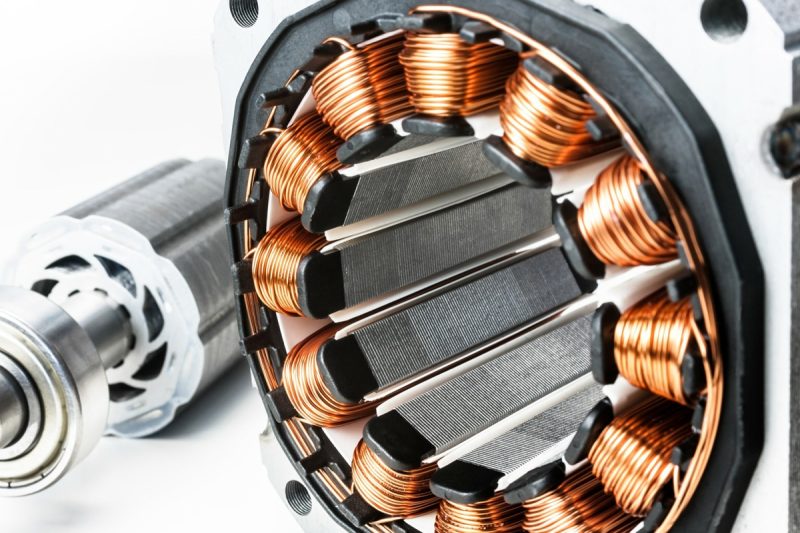
Motor Comparison
When choosing the right motor for your laser cutting machine, it is important to understand how different types of motors compare in terms of performance, cost, complexity, and application suitability. This section compares stepper motors, servo motors, and linear motors in detail, highlighting their key attributes and how they can meet various cutting needs.
Precision and Accuracy
- Stepper Motors: Stepper motors have good precision and accuracy due to their ability to move in discrete steps. However, they can lose steps under high loads or at high speeds, which can reduce the overall accuracy of a system without feedback.
- Servo Motors: Servo motors offer superior precision and accuracy. Their closed-loop control system ensures that the position of the motor is constantly monitored and adjusted, making them ideal for applications that require high precision.
- Linear Motors: They excel in precision and accuracy in linear motion, eliminating mechanical conversions and providing direct, high-precision linear motion. They are particularly well-suited for applications that require ultra-high precision.
Speed
- Stepper Motors: Stepper motors have a limited speed range. They perform well at low to medium speeds but lose torque and precision at high speeds.
- Servo Motors: Servo motors can achieve high speeds while maintaining precision and torque, making them suitable for high-speed cutting operations.
- Linear Motors: Linear motors excel in high-speed applications due to their direct linear motion capabilities. They can achieve fast acceleration and deceleration without sacrificing precision.
Torque and Load Handling
- Stepper Motors: Provide high torque at low speeds, which is beneficial for some applications, but may lose torque at higher speeds.
- Servo Motors: Provide consistent torque across their speed range, allowing them to handle varying loads without compromising performance.
- Linear Motors: Handle high-speed linear motion with strong forces, but their torque characteristics depend on the specific design and application.
Cost
- Stepper Motors: Stepper motors are the most cost-effective option. They offer good performance at a low price, making them suitable for budget-conscious applications.
- Servo Motors: Servo motors are more expensive than stepper motors because they feature advanced control systems and feedback mechanisms. However, their superior performance often justifies their higher cost.
- Linear Motors: Linear motors are the most expensive option. Their higher cost stems from their advanced design and the precision they offer, which is necessary for specific high-performance applications.
Complexity
- Stepper Motors: Stepper motors are relatively simple to install and operate. Their open-loop control systems reduce the need for complex electronics and feedback systems.
- Servo Motors: Servos are more complex due to their closed-loop control systems. They require complex controllers and feedback devices, adding to the complexity of setup and maintenance.
- Linear Motors: Linear motors are complex to install and align. Their direct drive systems require precise setup and calibration to ensure optimal performance.
Maintenance and Reliability
- Stepper Motors: Stepper motors are rugged and reliable, with fewer parts that can fail. They require minimal maintenance, making them suitable for low-maintenance applications.
- Servo Motors: Servo motors are reliable, but require regular maintenance due to their more complex systems. Proper maintenance ensures they operate at peak performance.
- Linear Motors: Linear motors have fewer moving parts, resulting in less wear and tear. However, their advanced components may require specialized maintenance to ensure longevity and reliability.
Environmental Considerations
- Stepper Motors: Perform well in standard industrial environments, but may require additional cooling measures in high heat situations.
- Servo Motors: Capable of operating in a variety of environments, but require proper cooling and maintenance to effectively handle heat generation.
- Linear Motors: Due to their high-speed operation and alignment sensitivity, they require precise environmental control, making them suitable for controlled manufacturing environments.
Summary Table
Criteria | Stepper Motors | Servo Motors | Linear Motors |
---|---|---|---|
Precision | Good | Excellent | Superior |
Speed | Low to Moderate | High | Very High |
Torque | High at Low Speeds | Consistent Across Speeds | Smooth, Consistent Linear Force |
Cost | Low | Moderate to High | High |
Complexity | Simple | Complex | Highly Complex |
The comparison of stepper motors, servo motors, and linear motors shows that each has unique advantages for different applications and requirements. Stepper motors are simple and cost-effective, making them ideal for less demanding tasks. Servo motors offer high precision, high speed, and high adaptability, making them the preferred choice for high-performance industrial applications. Linear motors excel at high-speed, high-precision linear motion and are suitable for advanced and specialized manufacturing processes.
Understanding the specific needs of an application (such as accuracy, speed, load handling, complexity, and budget) allows for the selection of the right motor for a laser-cutting machine. By carefully evaluating these factors, manufacturers and operators can optimize their machines for improved performance, efficiency, and reliability.
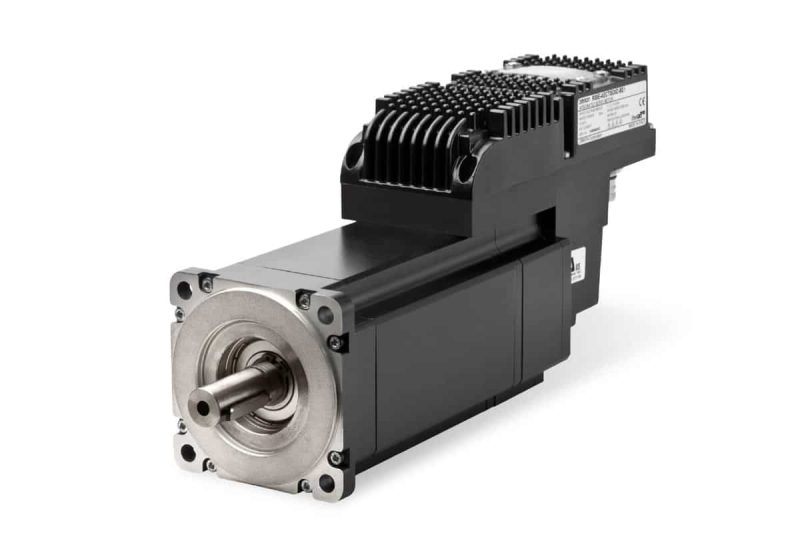
How to Choose the Right Motor
Choosing the right motor for your laser cutting machine is a critical step in ensuring optimal performance, precision, and efficiency. This section will guide you through a systematic approach to selecting the right motor, covering key aspects such as application needs, motor type, power and torque requirements, control system compatibility, budget, maintenance, integration, support, scalability, and validation.
Determine Your Application Needs
Precision and Accuracy
Evaluate the level of precision and accuracy required for your cutting tasks. High-precision applications, such as medical device manufacturing, may require more sophisticated motor systems like servo or linear motors.
Speed and Responsiveness
Consider the cutting speed and responsiveness needed for your operations. High-speed production lines will benefit from motors that can accelerate and decelerate quickly.
Material and Thickness
Identify the types of materials and their thicknesses that you will be cutting. Different materials may require different motor capabilities in terms of torque and speed.
Evaluate Motor Types
Stepper Motors
Stepper motors are cost-effective and suitable for applications requiring moderate precision without feedback systems. They offer high torque at low speeds but may lose steps at higher speeds.
Servo Motors
Servo motors provide high precision, speed, and dynamic response due to their closed-loop feedback systems. They are ideal for high-precision and high-speed applications but are more expensive and complex.
Linear Motors
Linear motors offer direct linear motion with high precision and speed, making them perfect for advanced manufacturing processes. They are the most expensive and require precise installation and alignment.
Consider Power and Torque Requirements
Power Rating
Determine the power rating required to perform your cutting tasks efficiently. The power rating indicates the motor’s ability to perform work over time.
Torque Rating
Evaluate the torque requirements, considering the resistance and load the motor will handle. High torque is essential for cutting thicker materials or handling high-resistance tasks.
Assess Control Systems Compatibility
Existing Control Systems
Ensure the selected motor is compatible with your existing control systems, drives, and software. Integration with your current setup is crucial for seamless operation.
Control Complexity
Consider the complexity of the control system required. Stepper motors are simpler to control, while servo and linear motors may require advanced controllers and feedback mechanisms.
Budget Considerations
Initial Cost
Evaluate the initial cost of the motor and its components. Stepper motors are generally the most affordable, while servo and linear motors are more expensive but offer superior performance.
Total Cost of Ownership
Consider the total cost of ownership, including maintenance, energy consumption, and potential downtime. Investing in higher-quality motors can result in long-term savings through improved efficiency and reliability.
Maintenance and Reliability
Maintenance Requirements
Assess the maintenance needs of the motor. Stepper motors have low maintenance requirements, while servo and linear motors require regular maintenance to ensure optimal performance.
Reliability
Choose a motor known for its reliability in your specific application. Servo motors are reliable for industrial applications, whereas stepper motors are dependable for simpler tasks.
Integration and Compatibility
Mechanical Integration
Ensure the motor can be mechanically integrated into your laser cutting machine. Proper mounting and alignment are crucial for optimal performance.
Electrical Integration
Check the electrical compatibility of the motor with your existing systems. Proper wiring and connections are necessary for seamless operation.
Manufacturer and Supplier Support
Reputation and Experience
Select a reputable manufacturer or supplier with experience in providing motors for laser cutting machines. Reliable suppliers offer quality products and valuable expertise.
After-Sales Support
Ensure robust after-sales support, including technical assistance, maintenance services, and availability of spare parts. Strong support can minimize downtime and extend the motor’s lifespan.
Future Scalability
Scalability
Choose a motor that can accommodate future upgrades or changes in production requirements. Scalability ensures your motor system remains relevant as your business grows.
Technology Trends
Stay informed about advancements in motor technology. Investing in motors with the latest features and capabilities can future-proof your laser-cutting machine.
Test and Validate
Performance Testing
Before finalizing your choice, conduct performance testing to validate the motor’s capabilities in real-world conditions. Testing ensures the motor meets your application needs and performs reliably.
Feedback and Adjustment
Gather feedback from operators and make any necessary adjustments to the motor system. Continuous improvement based on practical insights can enhance performance and efficiency.
Choosing the right motor for your laser cutting machine involves a comprehensive assessment of your application needs, motor types, power and torque requirements, control system compatibility, budget, maintenance, integration, support, scalability, and validation. By carefully evaluating these factors, you can select a motor that enhances the performance, precision, and reliability of your laser cutting operations, ensuring high-quality results and improved productivity.
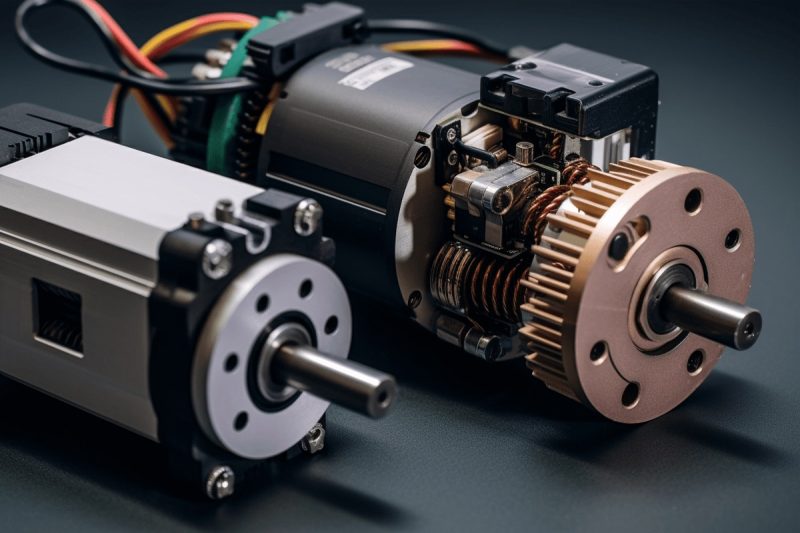
Troubleshooting Common Problems
Effective troubleshooting can help maintain the performance and reliability of your laser-cutting machine’s motor. Promptly identifying and resolving problems can prevent downtime, reduce maintenance costs, and extend the life of your equipment. This section provides a comprehensive guide to troubleshooting common motor problems for your laser-cutting machine.
Motor Overheating
Causes
- Inadequate Cooling or Airflow: Blocked vents or malfunctioning cooling fans can reduce airflow, causing the motor to overheat.
- Excessive Load or Friction: Overloading the motor or having insufficient lubrication can increase friction, leading to overheating.
- Electrical Issues: Problems such as overvoltage, undervoltage, or electrical faults can cause the motor to overheat.
Solutions
- Ensure Proper Cooling: Check that all cooling fans are operational and vents are unobstructed. Clean or replace air filters regularly.
- Reduce Load: Ensure the motor is not overloaded. Lubricate moving parts according to the manufacturer’s recommendations to reduce friction.
- Stabilize Electrical Supply: Inspect electrical connections and ensure the motor is receiving the correct voltage. Use surge protectors or voltage stabilizers if necessary.
Unusual Noises
Causes
- Worn or Damaged Bearings: Bearings that are worn out or damaged can produce grinding or squealing noises.
- Misalignment of Components: Misaligned motor shafts or mechanical components can cause vibrations and unusual noises.
- Loose or Damaged Parts: Loose bolts, screws, or damaged parts can create rattling or banging sounds.
Solutions
- Inspect and Replace Bearings: Regularly inspect bearings for wear and replace them if necessary.
- Realign Components: Check the alignment of the motor shaft and other mechanical components. Adjust as needed to ensure proper alignment.
- Secure Loose Parts: Tighten all bolts and screws. Replace any damaged parts to eliminate noise sources.
Vibration
Causes
- Imbalanced Components: Imbalances in the motor or connected components can cause vibrations.
- Loose Connections: Loose mechanical connections or fasteners can lead to vibration.
- Worn or Damaged Parts: Worn-out or damaged parts, such as gears or belts, can cause the motor to vibrate.
Solutions
- Balance Components: Ensure all rotating components are properly balanced. Use balancing weights if necessary.
- Tighten Connections: Check and tighten all mechanical connections and fasteners.
- Replace Worn Parts: Inspect and replace any worn or damaged parts to reduce vibrations.
Motor Stalling
Causes
- Overloading the Motor: Excessive load can cause the motor to stall.
- Electrical Supply Issues: Problems such as voltage drops or fluctuations can cause the motor to stall.
- Mechanical Obstructions: Obstructions in the motor’s path can prevent it from moving freely, leading to stalling.
Solutions
- Reduce Load: Ensure the motor is not overloaded. Distribute the load evenly and avoid sudden increases in demand.
- Check Electrical Supply: Inspect the electrical supply for stability. Use voltage regulators if necessary to maintain a consistent power supply.
- Remove Obstructions: Inspect the motor and its path for any obstructions. Clear any debris or blockages that may be causing the stall.
Loss of Precision
Causes
- Wear in Mechanical Components: Wear and tear in gears, belts, or other mechanical components can lead to a loss of precision.
- Issues with Feedback Systems: Problems with encoders or other feedback systems can result in inaccurate positioning (specific to servo motors).
- Loose or Misaligned Parts: Loose or misaligned mechanical parts can cause deviations in movement.
Solutions
- Replace Worn Components: Regularly inspect and replace worn gears, belts, and other mechanical components.
- Calibrate Feedback Systems: Inspect and calibrate encoders and other feedback systems to ensure accurate positioning.
- Tighten and Align Parts: Check all mechanical parts for tightness and proper alignment. Make adjustments as necessary to restore precision.
Electrical Issues
Causes
- Faulty Wiring: Damaged or loose wiring can cause electrical issues.
- Component Failures: Failures in components such as relays, switches, or drives can disrupt motor operation.
- Power Supply Problems: Issues with the power supply, such as fluctuations or interruptions, can affect motor performance.
Solutions
- Inspect Wiring: Regularly inspect wiring for signs of damage or wear. Tighten any loose connections and replace damaged wires.
- Test Components: Test and replace any faulty electrical components to restore proper motor function.
- Stabilize Power Supply: Use voltage regulators or uninterruptible power supplies (UPS) to ensure a stable power supply.
Software and Control System Issues
Causes
- Software Glitches: Bugs or glitches in the control software can cause erratic motor behavior.
- Incorrect Settings: Incorrect settings or parameters in the control system can lead to performance issues.
- Firmware Issues: Outdated or corrupted firmware can affect motor control.
Solutions
- Update Software: Ensure the control software is up to date and free from bugs. Apply any available patches or updates.
- Check Settings: Verify that all settings and parameters in the control system are correctly configured for your specific application.
- Update Firmware: Update the motor control firmware to the latest version provided by the manufacturer.
Troubleshooting common motor issues in laser cutting machines requires a systematic approach to identify and resolve problems promptly. Regular maintenance, careful inspection, and timely repairs can prevent issues from escalating and ensure the smooth operation of your machine. By understanding the causes and solutions for common motor problems, operators can maintain optimal performance and reliability, ensuring high-quality cutting results and minimal downtime.
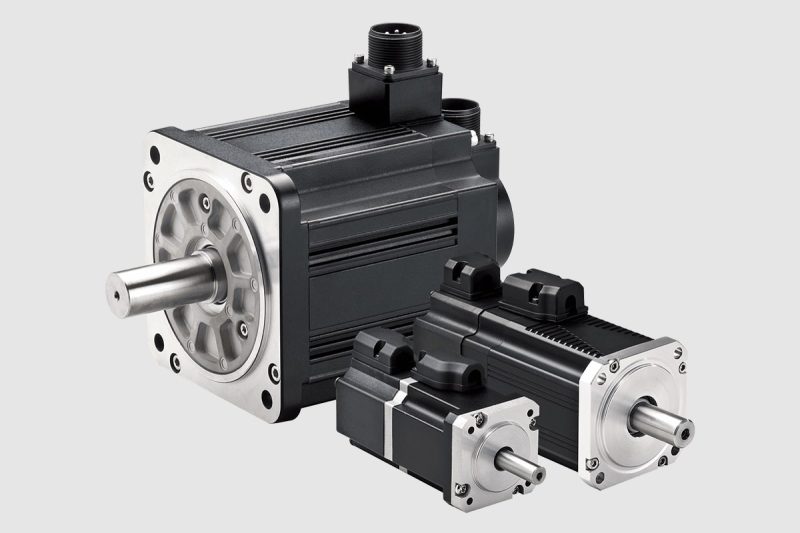
Summary
Choosing the right motor for your laser cutting machine can help achieve optimal performance, precision, and efficiency. This comprehensive guide explores the various types of motors used in these machines, including stepper motors, servo motors, and linear motors, each of which has unique benefits and applications. We discuss the importance of understanding application needs, evaluating motor types, considering power and torque requirements, assessing control system compatibility, and weighing budget considerations. Effective maintenance and troubleshooting strategies are outlined to ensure long-term motor performance and reliability. By following these guidelines, manufacturers, and operators can make informed decisions to improve the efficiency and precision of their laser-cutting machines, ensuring high-quality results and continued productivity.
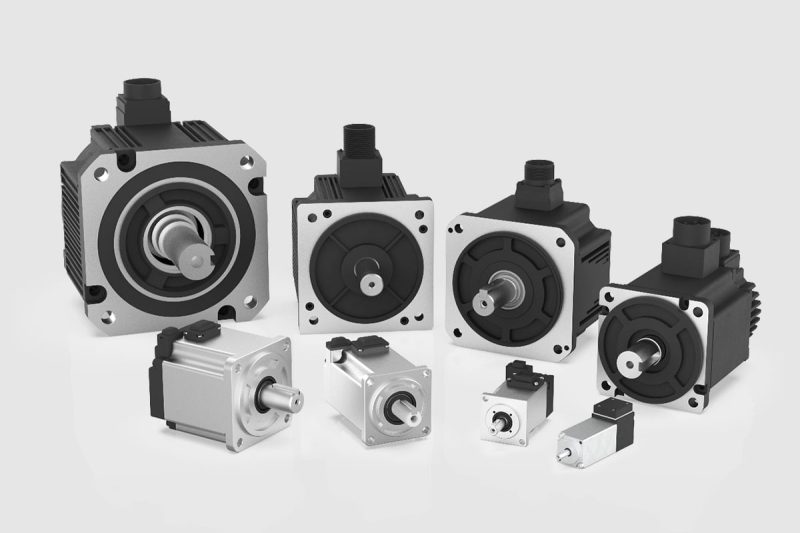
Get Laser Cutting Solutions
At AccTek Laser, we understand the critical role that motor systems play in the performance and precision of laser-cutting machines. Our comprehensive range of laser-cutting solutions is designed to meet the diverse needs of various industries. Whether you require high precision for intricate designs or high speed for large-scale production, we have the expertise and technology to provide the perfect solution.
Our team of experts works closely with you to assess your specific requirements and recommend the most suitable motor systems, including stepper motors for cost-effective applications, servo motors for high-precision tasks, and linear motors for advanced, high-speed operations. We also offer robust maintenance and support services to ensure your laser-cutting machines operate at peak efficiency.
By choosing AccTek Laser, you benefit from cutting-edge technology, exceptional performance, and reliable support, ensuring your laser cutting operations achieve the highest standards of quality and productivity. Contact us today to learn more about our laser-cutting solutions and how we can help you optimize your production processes.
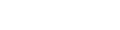
Contact information
- [email protected]
- [email protected]
- +86-19963414011
- No. 3 Zone A, Lunzhen Industrial Zone,Yucheng City , Shandong Province.
Get Laser Solutions