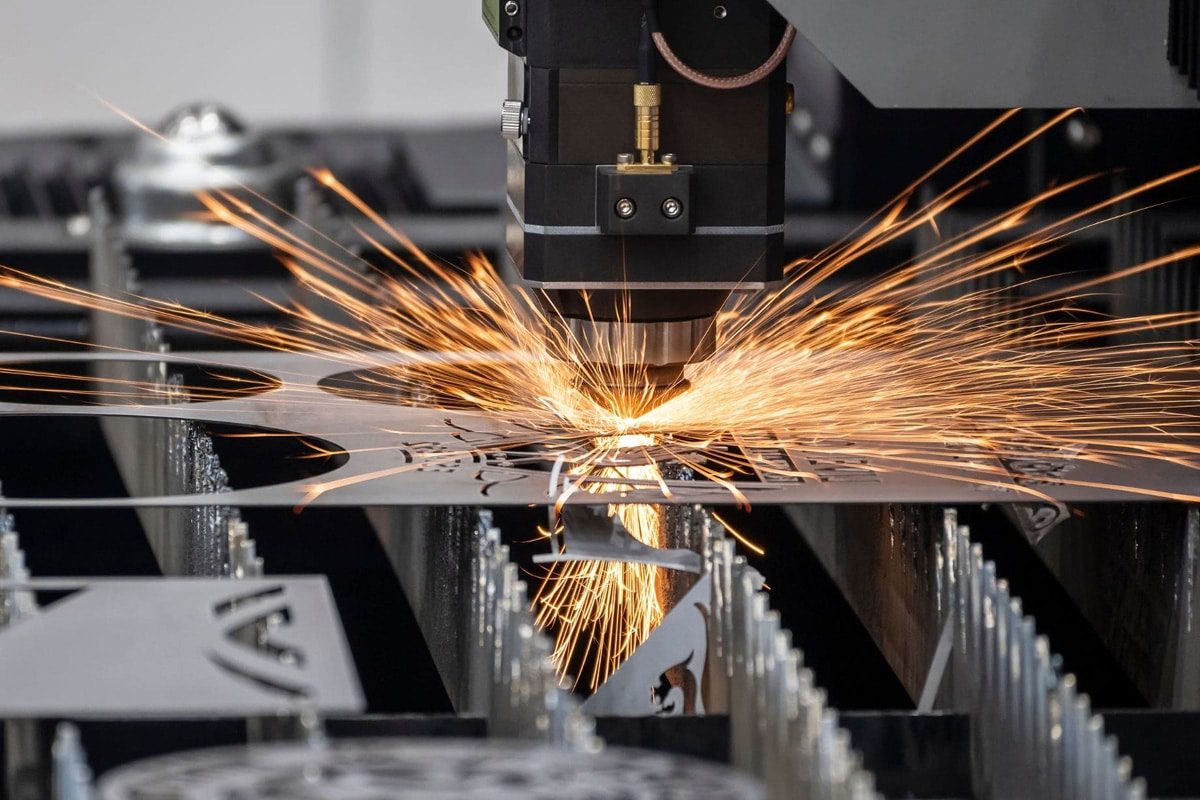
Noise of Laser Cutting Machine
Laser cutting machines are widely used in many industries due to their high efficiency and precise cutting capabilities, especially in the manufacturing, automotive and aviation fields. However, the noise generated by laser cutting machines during operation is also an issue that cannot be ignored. Excessive noise not only affects the operator’s working environment, but may also pose a potential threat to health. Therefore, it is particularly important to understand the source of noise, influencing factors and countermeasures.
The noise of laser cutting machines mainly comes from several aspects: the running sound of mechanical parts such as motors and fans, vibration during cutting, noise of exhaust and ventilation systems, and sound of material handling systems. Different cutting power, speed and material properties will affect the level of these noises. Good machine design and efficient cooling and ventilation systems can help reduce noise, while parameter adjustment during cutting and material properties will also affect noise to a certain extent.
In terms of noise control, the rational use of sound insulation equipment, optimized machine design, and regular maintenance and lubrication of equipment are all effective means of noise reduction. This not only improves the operator’s working environment, but also effectively reduces the health risks of long-term exposure to high noise environments. Understanding and taking appropriate noise control measures is the key to ensuring a safe and healthy production environment.
Table of Contents
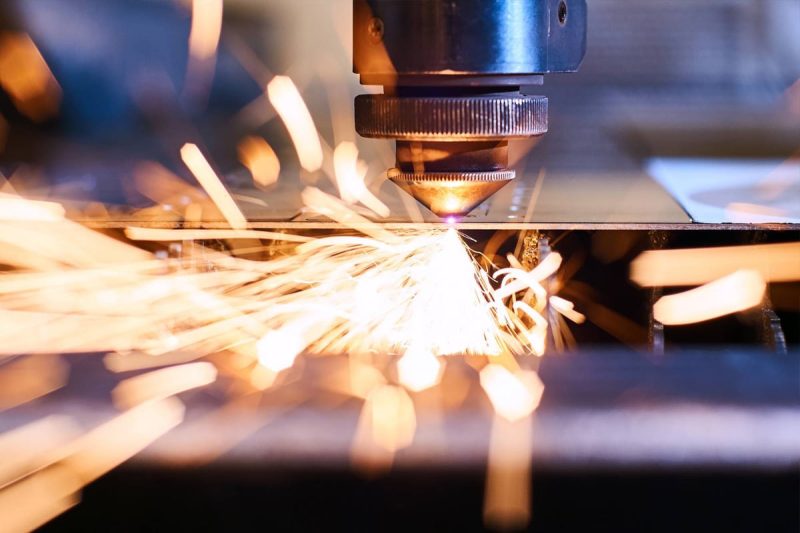
Understanding Noise in Laser Cutting Machines
The noise sources of laser cutting machines are complex and can be divided into four main categories: mechanical parts, vibration during cutting, exhaust and ventilation systems, and material handling systems. Each type of noise source has different frequencies and characteristics, which affect the noise level of the equipment during operation. The following is a detailed analysis of these noise sources:
Mechanical Components (E.G. Motors, Fans)
Frequency
Mechanical components, such as motors and fans, generate noise at frequencies that depend primarily on the power and speed of the equipment. Motor noise frequencies are typically between 50 Hz and 300 Hz, with lower frequencies coming primarily from large or high-power motors. Fans generate medium- and high-frequency noise, typically ranging from 500 Hz to 2000 Hz, and tend toward the high end, especially when the fan is running at high speed.
Characteristic
The noise of the motor is relatively stable, usually presenting as a low-frequency, continuous hum. The noise of the fan is mainly sharp, continuous high-frequency noise, especially when running at high speed, the noise may be more obvious. Aging motors or fans usually produce louder noise, especially when there is a lack of lubrication or parts wear. The noise will not only increase but may also be accompanied by noise, such as mechanical friction.
Vibration During Cutting
Frequency
During the cutting process, the interaction between the laser and the material causes vibration noise. The frequency of the vibration is closely related to the thickness and characteristics of the material. When cutting thinner materials, the noise frequency is usually between 200 Hz and 1000 Hz; when cutting thicker materials, especially steel or other hard materials with a thickness of more than 10 mm, the noise frequency generated by the vibration is usually between 100 Hz and 500 Hz.
Characteristic
Vibration noise usually manifests as irregular, short impact sounds. The vibration of thin materials produces higher-frequency sounds, which are usually sharper; thick materials will cause low-frequency and continuous vibration noise, which sounds dull. In addition, the intensity of vibration noise will change with the thickness of the material and the cutting speed. When cutting faster, the vibration will be more obvious and the noise level will increase accordingly.
Exhaust and Ventilation Systems
Frequency
Exhaust and ventilation system noise frequencies typically range from 500 Hz to 4000 Hz. The higher the fan speed, the higher the frequency of the noise produced. Large exhaust equipment generally produces lower frequency noise, while small, high-speed fans tend to produce higher frequency sounds.
Characteristic
The noise of the exhaust and ventilation system is usually a continuous and sharp wind noise, which is more obvious when the fan is running at high speed. If the ventilation system is not designed properly or the air duct is blocked, the air flow will be blocked, which will increase the noise. In addition, the resonance in the ventilation duct may also amplify certain frequencies of noise, making it more harsh. Since the exhaust system needs to run continuously for a long time, this kind of noise may always exist during the cutting process.
Material Handling Systems
Frequency
The noise frequencies of material handling systems are usually between 100 Hz and 2000 Hz, depending on the weight of the material and how the system operates. Lightweight materials generally produce higher frequency noise when being handled, while heavy materials produce lower frequency noise.
Characteristic
Noise during material handling is often intermittent, and is generated as materials are loaded, unloaded or conveyed. Heavy materials usually produce low-frequency collision sounds, which are heavier, while light materials may produce higher-frequency knocking sounds, which are lighter but more sharp. If the mechanical parts in the system are not well maintained, friction and jamming will produce additional noise, such as sharp grinding sounds or metal-to-metal collision sounds.
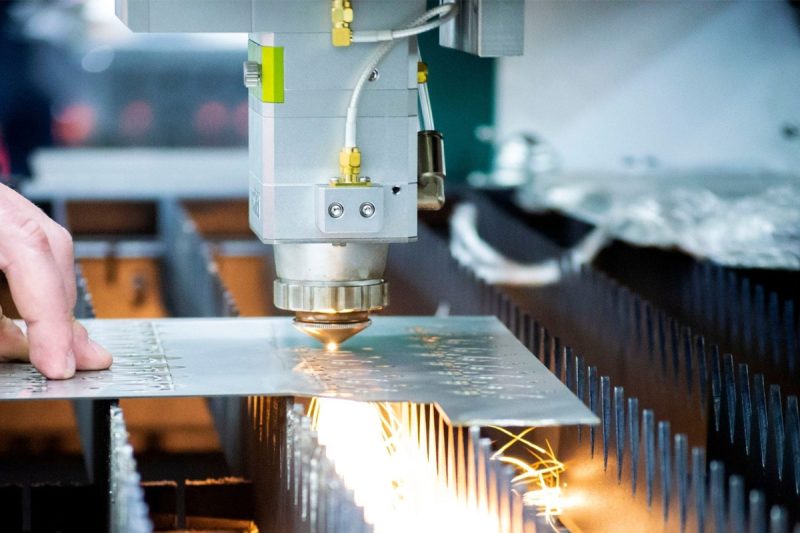
Factors That Influence Noise Levels
Machine Design and Construction Materials
The design and construction materials of a laser cutting machine have a significant impact on noise levels. A well-designed machine can effectively reduce vibration and noise, usually using heavy-duty frames and highly rigid materials to reduce resonance effects. High-quality construction materials such as steel or aluminum alloys can absorb and attenuate vibrations, reducing the propagation of sound waves. In addition, proper structural design, such as reasonable component layout and connection methods, can effectively reduce the mutual interference between various components, thereby reducing the overall noise level.
Cutting Parameters
Cutting parameters, including cutting power and speed, directly affect the operating status and noise level of the laser cutting machine. Generally speaking, higher power and speed will lead to stronger vibration, which will increase noise. For example, when cutting heavy materials, the power needs to be increased to ensure the cutting quality, which often causes stronger vibration and noise. Therefore, properly adjusting the cutting parameters, especially when processing different materials, can effectively reduce noise while ensuring the cutting effect.
Material Properties
The characteristics of the material being cut, including thickness, density and composition, all have an impact on noise levels. Generally speaking, heavy or hard materials, such as thick steel plates or alloys, usually produce more noise when cutting. This is because when harder materials are cut by laser, the heat and vibration generated are more significant, resulting in an increase in sound wave intensity. In addition, the composition of the material will also affect the sound characteristics when it is cut. The frequency and intensity of the noise generated by materials with different compositions during cutting may be different.
Cooling and Ventilation Systems
The efficiency of the cooling system is directly related to the working state of the fan, which in turn affects the noise level. The design of the cooling system must ensure that the heat and smoke generated during the cutting process are effectively discharged. If the cooling system is inefficient, the load on the fan will increase and it will need to run at a higher speed to maintain the normal temperature of the equipment, which will cause additional noise. Optimizing the design of the cooling and ventilation system can not only improve the working efficiency of the equipment, but also reduce the noise level during operation.
Effectiveness of Soundproofing Measures
In the design of laser cutting machines, reasonable sound insulation measures can significantly reduce noise levels. The installation of soundproof enclosures and the use of sound-absorbing materials are common noise reduction methods. However, the effectiveness of these measures is closely related to the quality and design of the soundproofing equipment. High-quality soundproof enclosures and sound-absorbing materials can effectively block and absorb sound, while soundproofing equipment that is poorly designed or made from inferior materials may have limited effectiveness. Therefore, when installing sound insulation measures, it is necessary to comprehensively consider material characteristics, design concepts and actual application scenarios to achieve the best noise reduction effect.
Maintenance and Lubrication of Moving Parts
The moving parts of the laser cutting machine will generate additional noise due to friction and wear during operation. Therefore, good maintenance and regular lubrication are essential to reduce noise. Regular inspection and maintenance of moving parts such as guides, gears and motors can not only reduce friction but also extend the service life of the equipment. Using suitable lubricants can reduce friction between mechanical parts, thereby reducing noise during operation. In addition, keeping moving parts clean can prevent dirt and debris from affecting the operation of the equipment, further reducing the noise level.
In summary, the noise level of a laser cutting machine is affected by many factors. By optimizing the design, adjusting cutting parameters, selecting appropriate materials, improving the efficiency of the cooling system, effective sound insulation measures, and good maintenance, the noise can be significantly reduced. Improve the comfort and safety of the work environment.
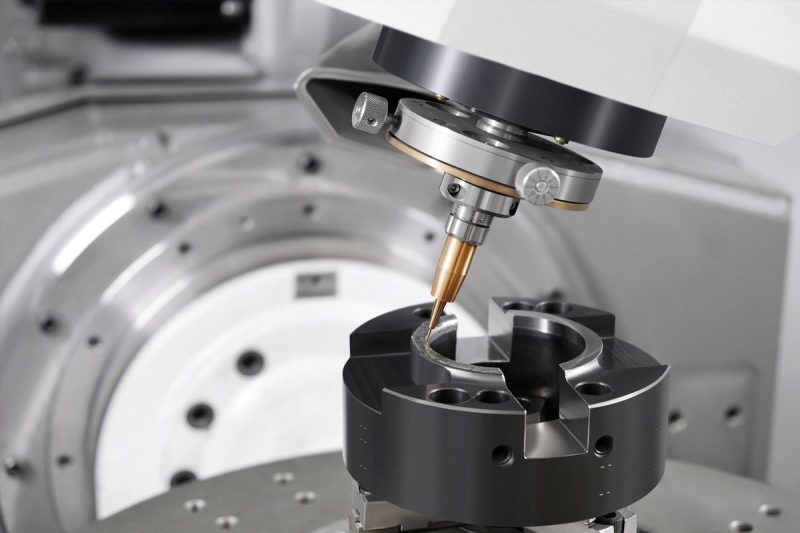
Health and Safety Issues
The noise generated during the operation of the laser cutting machine not only affects the comfort of the working environment, but may also pose a threat to the health and safety of the operators. The following is a detailed analysis of the relevant health and safety issues:
Potential Health Risks Associated with Exposure to High Levels of Noise
Long-term exposure to high-intensity noise may lead to a series of health problems. First of all, the most common impact is hearing loss, especially high-frequency hearing loss, which may gradually worsen without being noticed. Continuous stimulation of noise can cause damage to the auditory cells in the ear, leading to irreversible hearing impairment. In addition, high-intensity noise may also cause tinnitus, that is, when there is no external sound stimulation, there is still a buzzing or other sound in the ear. This symptom may greatly affect daily life and work efficiency.
In addition to hearing problems, noise can also have a significant impact on mental health. Research shows that long-term noise exposure can lead to mental health problems such as stress, anxiety and depression. Noise will not only interfere with work concentration and reduce productivity, but may also affect sleep quality, causing a series of sleep-related health problems, such as fatigue and reduced immunity.
Occupational Health and Safety Regulations Related to Noise Exposure in the Workplace
To protect workers’ health, many countries and regions have enacted occupational health and safety regulations for noise exposure in the workplace. These regulations usually set permissible exposure limits for noise, and when these limits are exceeded, employers must take appropriate measures to reduce the noise. These regulations also require regular monitoring of noise levels in the workplace and provide appropriate health checks to detect noise-related health problems early.
For example, the U.S. Occupational Safety and Health Administration (OSHA) requires workers to use noise control measures or provide appropriate personal protective equipment (such as earmuffs and earplugs) when working in an environment with noise levels exceeding 85 decibels. When many companies follow these regulations, they often implement noise exposure assessments and control plans to ensure that the work environment meets safety standards.
The Importance of Implementing Noise Control Measures to Protect Workers
Effective noise control measures are essential to protecting worker health. Companies should adopt a variety of strategies to reduce noise levels in the workplace, such as:
- Design improvements: Consider noise control in equipment design and layout, using high-quality materials and construction design to reduce noise generation.
- Install soundproofing: Using soundproof enclosures and sound-absorbing materials can significantly reduce the noise generated by your equipment.
- Optimize operating processes: Adjust cutting parameters and operating procedures, such as reducing cutting speed or power, to reduce vibration and noise.
- Personal Protective Equipment: Provide workers with appropriate earmuffs and earplugs to protect them from high-intensity noise.
- Regular training and education: Provide training on noise protection knowledge to employees to enhance their understanding of noise risks and self-protection awareness.
By implementing the above measures, enterprises can not only meet the requirements of occupational health and safety regulations, but also create a safer and more comfortable working environment. This not only protects the health of workers, but also improves employee job satisfaction and production efficiency, ultimately achieving a win-win situation for both enterprises and employees.
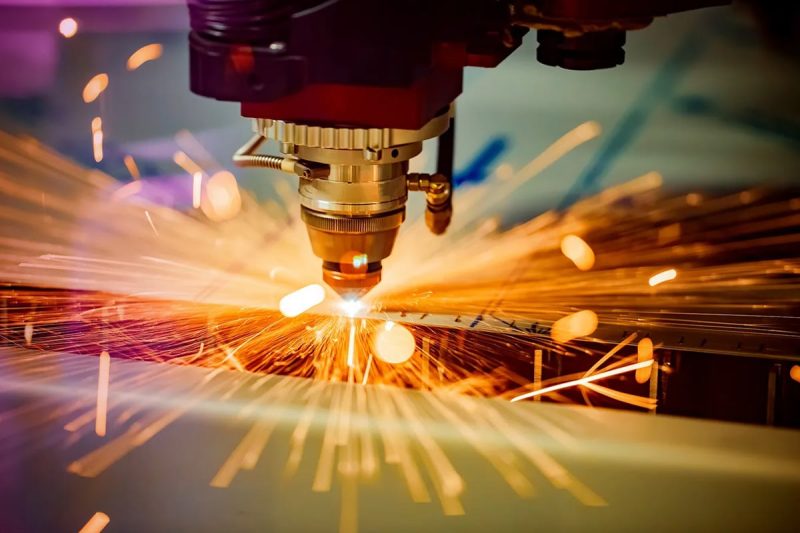
Noise Reduction Technology
Noise reduction technology plays a vital role in the operation of laser cutting machines. The following is a detailed analysis of several common noise reduction technologies:
Noise Enclosure
A soundproof enclosure is a structure used to surround a noise source and effectively block the propagation of sound waves. Usually, the noise generated by the operating parts of the laser cutting machine (such as motors, fans, etc.) can be reduced by a soundproof enclosure. High-quality soundproof enclosures usually use multiple layers of materials, with a solid metal outer layer and sound-absorbing materials on the inner layer to achieve good sound insulation. The design of the soundproof enclosure must fully consider ventilation and heat emission to prevent damage to the equipment due to overheating.
The effectiveness of the soundproof cover also depends on its sealing. A good seal can prevent sound wave leakage. In addition, a reasonable design can also make it convenient for operators to carry out daily maintenance and repairs without disassembling the cover, thus taking into account both noise reduction effect and ease of operation.
Vibration Isolation System
The vibration isolation system mainly reduces noise by reducing the transmission of equipment vibration. When the laser cutting machine is running, due to the movement of mechanical parts, strong vibrations may be generated. These vibrations will be transmitted through the equipment base and the ground, resulting in an increase in environmental noise. By installing vibration isolation pads or spring supports at the bottom of the equipment, the transmission of vibration can be effectively reduced.
Vibration isolation materials usually have high elasticity and shock absorption properties, which can absorb and attenuate vibration energy. A well-designed vibration isolation system can also improve the stability of the equipment, extend its service life, and reduce maintenance costs. In addition, when installing the equipment, choosing a suitable installation location and foundation can also improve the vibration isolation effect.
Sound-Absorbing Materials
The use of sound-absorbing materials is another effective noise reduction technology. Through its porous structure, sound-absorbing materials can absorb sound wave energy and reduce reflected and transmitted noise. Common sound-absorbing materials include mineral wool, polyester fiberboard and polyurethane foam. These materials can be applied to the walls, floors or ceilings around the laser cutting machine to form an acoustic environment that reduces noise.
When selecting sound-absorbing materials, they should be reasonably matched according to their frequency response characteristics and the spectrum characteristics of the noise source. Different sound-absorbing materials have different effects on the absorption of noise of different frequencies. Therefore, it is very important to select and layout materials according to the actual situation.
Regular Maintenance and Lubrication
Regular maintenance and lubrication are important parts of maintaining the normal operation of the equipment and are also crucial to reducing noise levels. Wear and friction of moving parts can cause additional noise, so regular inspection and maintenance of moving parts such as guides, gears and motors can effectively reduce the operating noise of the equipment.
Using the proper lubricant can reduce friction and lower noise levels. In addition, keeping mechanical parts clean and preventing the accumulation of dust and debris can also improve equipment operating efficiency and reduce unnecessary noise. Regular maintenance can also detect potential problems early and avoid high noise levels caused by equipment failure.
In summary, noise reduction technologies include soundproof enclosures, vibration isolation systems, sound-absorbing materials, regular maintenance and lubrication, etc. By using these technologies in combination, not only can the noise level of the laser cutting machine be effectively reduced, but also the performance and service life of the equipment can be improved, creating a safer and more comfortable working environment for operators.
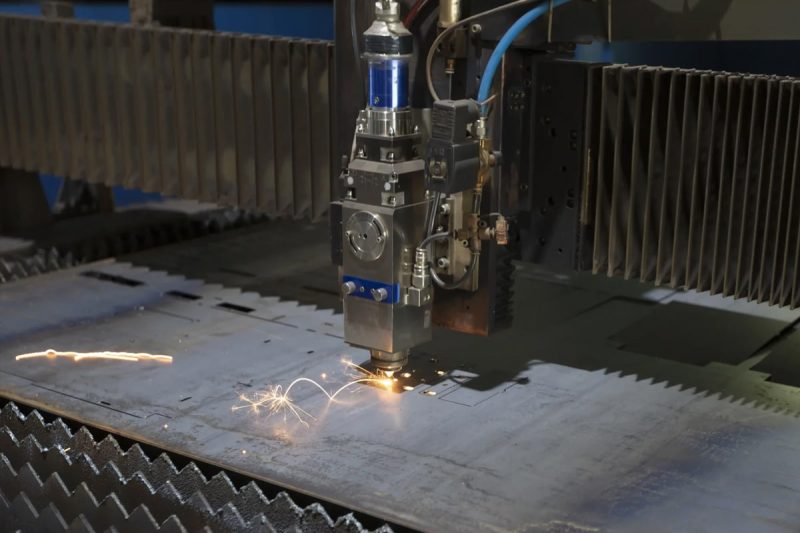
Summarize
The noise problem of laser cutting machines cannot be ignored. Noise not only affects the working environment of operators, but may also pose a potential threat to their health. Understanding the sources of noise and its influencing factors can help companies develop effective management strategies. By implementing reasonable noise reduction technology and health and safety measures, the operating environment can be significantly improved and work efficiency and safety increased.
By maintaining good equipment operation and combining modern noise reduction technologies such as soundproofing enclosures, vibration isolation systems and sound-absorbing materials, companies can effectively reduce noise levels and create a quieter and safer workspace. At the same time, regular equipment maintenance and lubrication can also help reduce noise and improve the overall performance of the equipment.
If you have any questions or needs about laser cutting machine noise control, please feel free to contact AccTek. We will provide you with customized solutions to ensure the efficient operation and safe use of the equipment and create a more ideal working environment for your company.
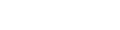
Contact information
- [email protected]
- [email protected]
- +86-19963414011
- No. 3 Zone A, Lunzhen Industrial Zone,Yucheng City , Shandong Province.
Get Laser Solutions