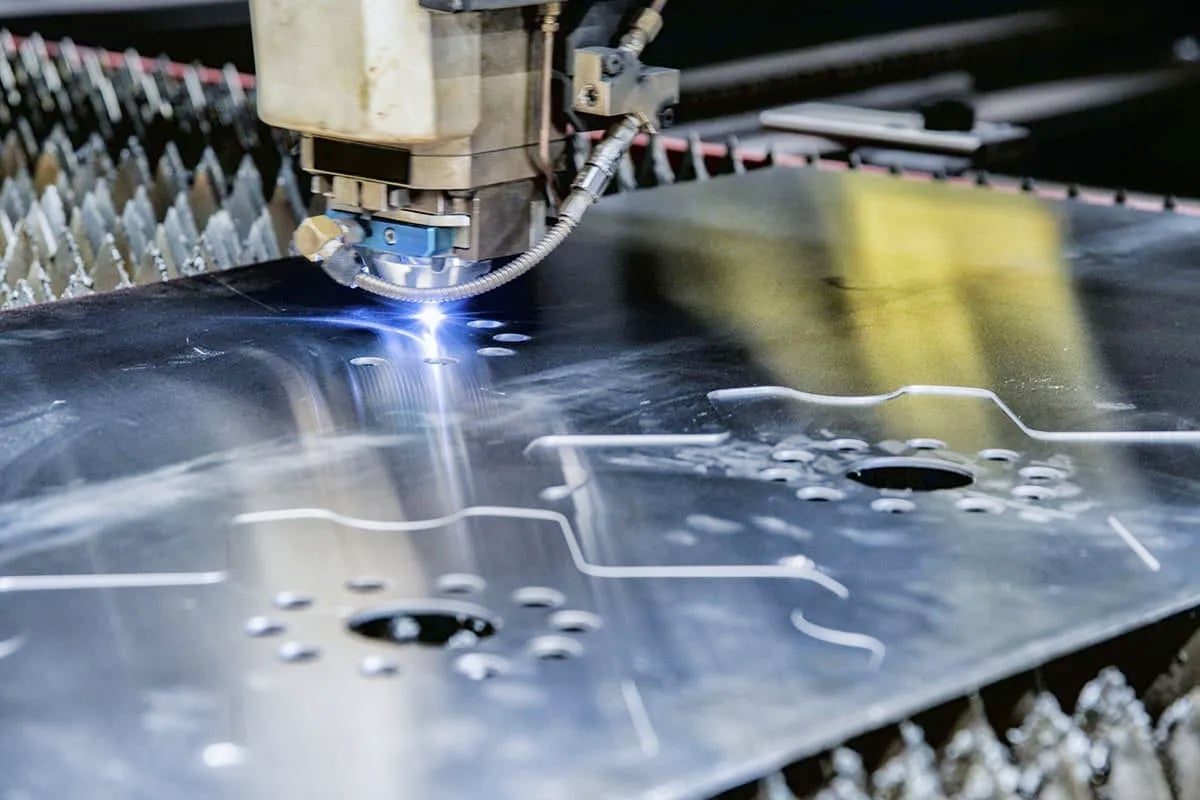
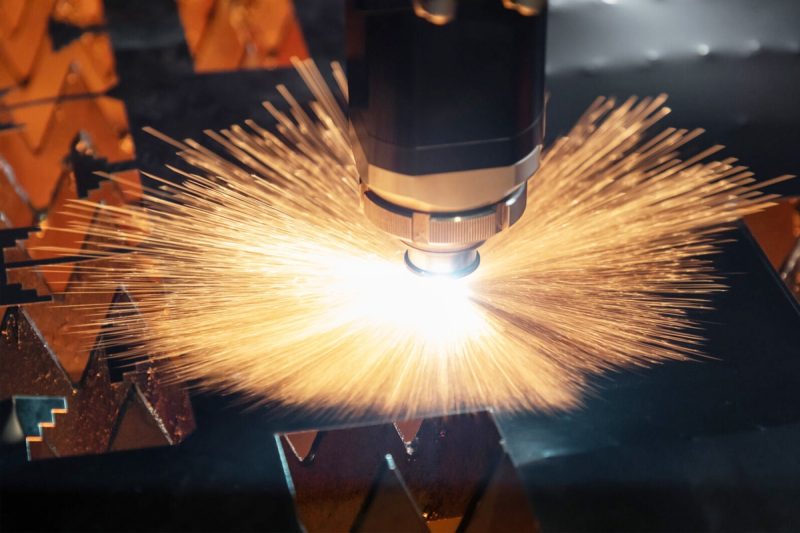
Laser Cutting Process Overview
Working Principle
Laser cutting involves directing a high-power laser beam at the material to be cut. The focused laser beam melts, burns, or vaporizes the material, resulting in a clean and precise cut. The process can be divided into the following key steps:
- Laser Generation: The laser beam is generated by a laser source, which can be a CO2 laser generator or a fiber laser generator. The type of laser generator used depends on the material to be cut and the specific requirements of the task.
- Beam Guidance and Shaping: The generated laser beam is directed to the cutting area via a series of mirrors or optical fibers. The beam is then focused to a very small, precise spot by a lens. This focus increases the intensity of the beam, enabling it to cut materials with high precision.
- Material Interaction: The focused laser beam is directed onto the surface of the material. The high energy density of the laser beam causes the material to heat up rapidly, resulting in melting, burning, or vaporization. The type of interaction (melting, burning, or vaporization) depends on the material properties and the laser settings.
- Assist Gas: Assist gases (such as oxygen, nitrogen, or air) are often used with lasers. These gases help blow away molten material from the cutting area, increasing cutting efficiency and improving cut quality. For example, oxygen can aid in cutting metals by creating an exothermic reaction, which increases the cutting power of the laser.
- Motion Control: The laser cutting head is mounted on a computer control system that moves along the desired cutting path. This system ensures precise and accurate cuts, even for complex shapes and patterns.
- Post-Processing: After the cutting process, the material may be post-processed to remove any remaining burrs or imperfections and achieve the desired finish.
Types of Materials Commonly Cut with Lasers
Laser-cutting technology is very versatile and can be used to cut a wide variety of materials. Here are some of the most commonly cut materials:
- Metals: Laser cutting is widely used to cut metals such as steel, stainless steel, aluminum, copper, and brass. Fiber lasers are particularly well suited for cutting metals due to their high power and efficiency. The process produces clean cuts with minimal burrs and high dimensional accuracy.
- Plastics: Various types of plastics, including acrylic (PMMA), polycarbonate, polyethylene, and PVC, are commonly cut using laser technology. Each plastic has its own cutting characteristics and odor profile. For example, acrylic leaves a clean cut with a sweet chemical odor, while PVC releases harmful chlorine-containing fumes.
- Wood: Laser cutting is commonly used to cut and engrave wood products, including plywood, MDF, and natural wood. The process allows for precise cuts and intricate designs. A burnt wood odor is a common byproduct.
- Textiles and Fabrics: Lasers are used to cut synthetic fibers such as polyester, nylon, and Kevlar. The technology allows for intricate patterns and clean edges, making it ideal for applications in the fashion and interior decoration industries.
- Paper and Paperboard: Laser cutting is used in the packaging and printing industries to cut paper, paperboard, and other paper products. The process allows for precise and detailed cuts to achieve custom designs and intricate patterns.
- Foams and Composites: A variety of foams and composites can be cut with lasers and are often used for packaging, insulation, and protective coverings. Due to the binders and fillers contained in these materials, the cutting process produces a strong chemical odor.
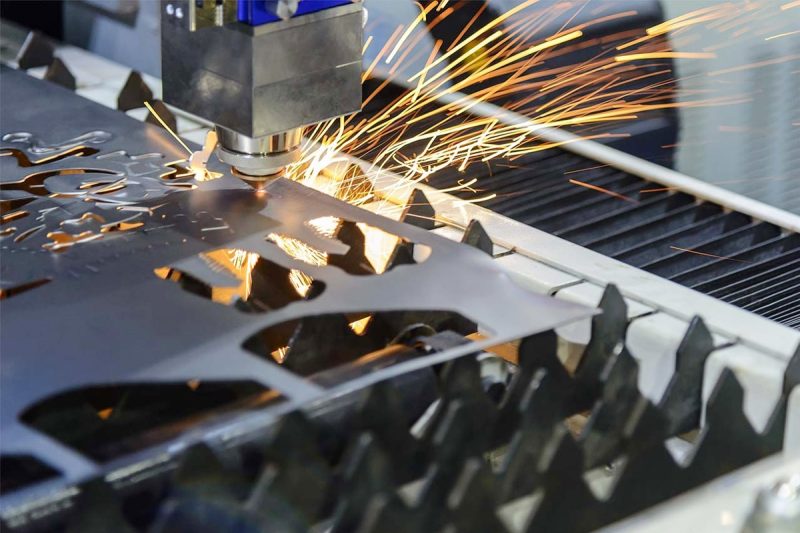
Causes of Odors
Vaporization and Combustion of Materials
The core mechanism of laser cutting involves the application of a high-power laser beam to a material, which causes rapid heating and subsequent phase changes. Depending on the material and the intensity of the laser, these phase changes can result in vaporization or combustion:
- Vaporization: Vaporization occurs when the energy of the laser beam is sufficient to change the material directly from a solid state to a vapor. The process often releases volatile organic compounds (VOCs) and other substances into the air, which can lead to characteristic odors associated with different materials. For example, vaporizing wood can release a familiar burnt wood smell due to the release of various organic compounds.
- Combustion: In some cases, the material being cut can burn, especially flammable materials. Combustion occurs when the material reacts with oxygen in the air, producing heat, light, and combustion products such as carbon dioxide, water vapor, and various other gases. The combustion of organic materials such as plastics and textiles often produces a complex series of compounds that can produce strong, unpleasant odors.
Gas and Fume Release
The laser cutting process produces a lot of gases and fumes, which are the main causes of odors:
- Assist Gases: Laser cutting often uses assist gases such as oxygen, nitrogen, or air to assist the cutting process. These gases can react with the material being cut to produce various byproducts. For example, oxygen can enhance the combustion of the material, which releases more gases and odors.
- Material Decomposition: When the laser cuts the material, it breaks down its molecular structure, releasing gases and fumes. For example, cutting acrylic (PMMA) releases monomers and other decomposition products that have a unique, usually sweet chemical odor. Similarly, cutting PVC releases hydrogen chloride gas, which has a pungent, irritating odor and is also harmful to health.
- Fume Composition: The exact composition of the fumes varies depending on the material. Metals generally release fewer organic compounds, but release metal oxides and other inorganic compounds. In contrast, cutting organic materials such as plastics, wood, and composites tends to produce a variety of organic vapors and particles, each of which adds to the overall odor.
Chemical Reactions Between Materials and Laser Energy
Odors can also be produced by chemical reactions caused by high-energy laser beams. These reactions can be quite complex and depend on the chemical composition of the material and the specific laser parameters used:
- Thermal Decomposition: The intense heat from the laser causes thermal decomposition of the material, resulting in the breakdown of complex molecules into simpler molecules. This decomposition produces a variety of gases, many of which have strong odors. For example, the thermal decomposition of polyurethane foam releases isocyanates, which have odors and can be harmful.
- Oxidation: Oxidation reactions occur when cutting metals or other metal-containing materials with a laser. For example, cutting steel in the presence of oxygen produces iron oxide, which may not have a strong odor but contributes to the overall odor of burning metal.
- Polymerization: Certain materials, particularly certain plastics and resins, polymerize when exposed to laser energy. This process releases a variety of organic compounds into the air, each with its unique odor. For example, cutting certain epoxy resins produces phenol and formaldehyde vapors, both of which have strong, unpleasant odors.
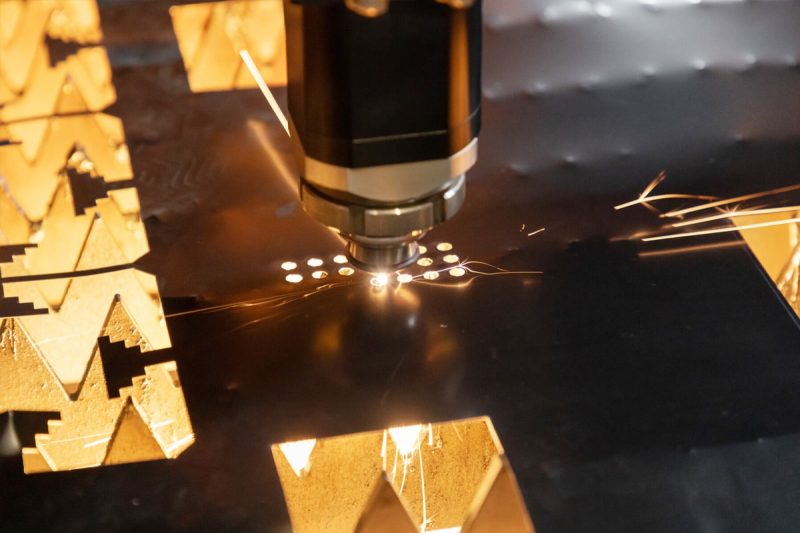
Odor Types
Overview of Common Odors When Cutting with Lasers
Burnt Odors
Burnt odors are probably the most common and noticeable odors produced during the laser cutting process. These odors come from the thermal decomposition or burning of materials when exposed to the high-energy laser beam. The specific smell of the burnt odor varies depending on the material being cut:
- Wood: Cutting wood produces a typical burnt wood odor, similar to the smell of a campfire or burnt bread. This odor is usually strong and can permeate the air.
- Plastics: Different plastics emit different burnt odors when cut. For example, acrylic (PMMA) has a sweet, chemical-burnt odor, while PVC produces a pungent odor due to the release of chlorine compounds.
- Textiles and Fabrics: Cutting synthetic fabrics such as polyester and nylon produces a burnt odor that is often described as plasticky or chemical in nature.
Chemical Odors
Chemical odors are produced by volatile organic compounds (VOCs) and other chemicals released when the material is heated or decomposed by the laser. These odors can be very varied and are often specific to the composition of the material:
- Plastics: Cutting plastics such as PVC and polycarbonate releases a variety of chemical compounds, creating odors ranging from sweet and fruity to pungent and acrid.
- Foams and composites: Binders and fillers in these materials often release strong chemical fumes when cut, resulting in a noticeable chemical odor.
- Resins and coatings: Materials with surface coatings or embedded resins can emit chemical odors as these substances evaporate or decompose.
Smoke Odors
Smoke odors are produced when materials burn or partially burn, releasing a mixture of gases, vapors, and fine particles. These odors are often more complex and may include burning and chemical odors:
- Wood and paper: Cutting these materials produces fumes with the odor of burnt organic matter, often described as smoky or ash-like.
- Plastics: Fumes from cutting plastics may have a pungent chemical odor, sometimes accompanied by visible smoke or fumes.
Particulate Odors
Particulate odors come from fine particles and aerosols produced during the laser-cutting process. These particles may carry the odor of the material itself as well as any odors from combustion or chemical reactions:
- Metals: While metals generally produce less odor, fine metal oxides and other particles generated during the cutting process may produce a metallic or pungent odor.
- Composites: Cutting composite materials releases a mixture of particles, each with its odor signature, often resulting in a complex, multifaceted odor.
Factors Affecting Odor Intensity and Type
Material Composition
Laser Parameters
Assist Gases
Ventilation and Filtration Systems
Environmental Conditions
Cutting Duration and Frequency
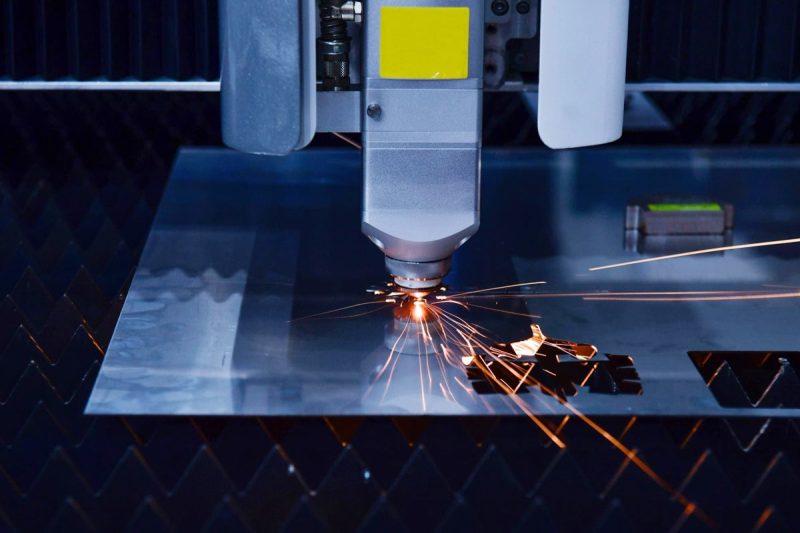
Health and Safety Issues
Respiratory Irritation
Respiratory irritation is one of the most immediate health issues associated with laser-cutting machine odors. The cutting process releases a variety of gases and particles that can irritate the respiratory tract, causing symptoms such as:
- Cough and Throat Irritation: Inhalation of fumes and smoke can cause coughing and a sore or tingling throat. This is often due to the presence of fine particles and irritating gases such as nitrogen oxides and sulfur compounds.
- Shortness of Breath: High levels of fumes can cause difficulty breathing or shortness of breath, especially in poorly ventilated areas. This is particularly concerning for people with respiratory conditions such as asthma or chronic obstructive pulmonary disease (COPD).
- Eye Irritation: Fumes can also irritate the eyes, causing redness, tearing, and discomfort.
Toxicity
Toxicity is a major concern when cutting certain materials, especially those that release harmful chemicals when vaporized or burned. The specific toxicity risk depends on the material being cut:
- Plastics: Cutting plastics such as polyvinyl chloride (PVC) can release toxic gases such as hydrogen chloride, which is highly corrosive and can cause severe respiratory distress. Polycarbonate and other plastics may release bisphenol A (BPA) and other harmful compounds.
- Composites and Foams: These materials often contain various adhesives and fillers that can release toxic substances, including isocyanates and formaldehyde, both of which are known respiratory hazards.
- Metals: While metals generally produce fewer odors, cutting painted or otherwise treated metals can release toxic fumes. For example, cutting galvanized steel produces zinc oxide fumes, which can cause metal fume fever, a flu-like illness.
Allergic Reactions
Some people may have allergic reactions to compounds released during laser cutting. These reactions range from mild to severe and include:
- Skin Reactions: Direct contact with particulate matter or airborne compounds can cause skin irritation or allergic dermatitis. This is particularly common with certain adhesives and chemical coatings.
- Respiratory Allergies: Inhalation of fumes and particulate matter can trigger allergic reactions in sensitive individuals, resulting in symptoms such as wheezing, coughing, and shortness of breath. People with asthma are particularly susceptible.
- Headaches and Nausea: Exposure to certain chemical fumes, especially those with strong odors, can cause headaches, dizziness, and nausea. These symptoms may indicate a mild allergic reaction or sensitivity to the compound.
Long-Term Effects
Long-term exposure to fumes and odors from laser cutting can cause serious long-term health effects. These effects depend on the duration and intensity of exposure, as well as the specific materials involved:
- Chronic Respiratory Diseases: Long-term exposure to fine particulate matter and toxic fumes can lead to chronic respiratory diseases such as bronchitis, asthma, and even chronic obstructive pulmonary disease (COPD). Workers exposed to high levels of dust and fumes are particularly susceptible.
- Cancer Risks: Some compounds released during the laser cutting process, such as formaldehyde and certain volatile organic compounds, are known carcinogens. Long-term exposure to these substances increases the risk of various cancers, especially lung cancer.
- Nervous System Effects: Long-term exposure to certain chemicals, such as those found in some plastics and composites, can have neurotoxic effects. Symptoms may include memory loss, cognitive impairment, and other neurological disorders.
- Reproductive and Developmental Toxicity: Certain chemicals released during the laser cutting process, such as BPA and phthalates, have been linked to reproductive and developmental problems. These substances can affect the reproductive health of both men and women and may pose a risk to pregnant workers.
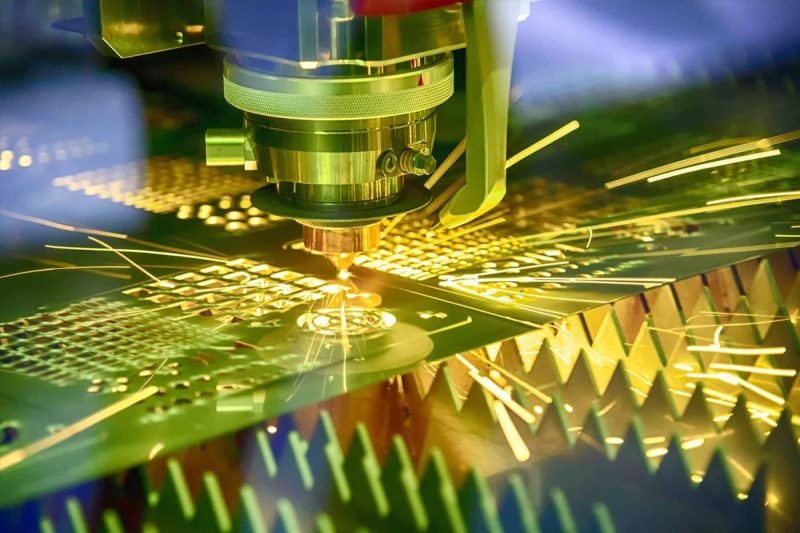
Odor Mitigation
Ventilation Systems
Ventilation is one of the most effective ways to manage and mitigate odors in laser-cutting operations. Proper ventilation systems help remove fumes and odors from the workplace, improving air quality and reducing health risks.
- Local Exhaust Ventilation (LEV): LEV systems capture fumes at the source, preventing them from spreading into the wider work environment. These systems use hoods, ducts, and fans to extract fumes directly from the laser cutting area and exhaust them outside the building or filter them through advanced filtration systems.
- General Ventilation: In addition to LEV, general ventilation systems can help dilute and remove contaminants from the air. This involves using fans and vents to ensure a constant flow of fresh air into the work area while exhausting contaminated air.
- Air Filtration: Installing an air filtration unit equipped with HEPA filters and activated carbon filters can further improve air quality. HEPA filters capture fine particles, while activated carbon filters absorb VOCs and other gaseous pollutants.
Material Selection
The choice of materials used for laser cutting can significantly affect the type and intensity of odors generated. Choosing materials that produce fewer or less harmful emissions can mitigate odor issues.
- Low-Emission Materials: Whenever possible, choose materials that produce fewer or less harmful emissions when cut. For example, choose acrylic (PMMA) over PVC because acrylic releases fewer toxic fumes.
- Pre-Treated Materials: Use materials that have been pre-treated to reduce the release of volatile compounds. For example, some types of wood can be treated to minimize the release of organic compounds that cause odors.
- Avoid Coatings and Contaminants: Materials with coatings, adhesives, or other surface treatments can generate additional odors and fumes. Choosing raw or minimally treated materials can help mitigate these issues.
Process Optimization
Optimizing the laser-cutting process can help minimize odor generation and improve overall efficiency.
- Laser Parameters: Adjusting the power, speed, and focus of the laser can reduce the amount of material that evaporates and burns, thereby reducing odor generation. For example, using the lowest effective power setting can minimize the thermal decomposition of materials.
- Cut Path Optimization: Effectively planning the cut path can reduce the time and energy required to cut, which can reduce the amount of material evaporated and the amount of odor produced.
- Assist Gas: Selecting the right assist gas, such as nitrogen instead of oxygen, can help reduce the intensity of odors. Nitrogen can help achieve a cleaner cut with fewer byproducts.
Personal Protective Equipment (PPE)
While engineering controls such as ventilation and material selection are the primary methods of odor mitigation, personal protective equipment (PPE) provides additional protection for workers.
- Respirators: High-quality respirators with filters specifically designed to capture particulate matter and volatile organic compounds (VOCs) protect workers from inhaling hazardous materials.
- Protective Clothing: Use gloves and protective clothing to prevent skin contact with potentially harmful particles and fumes. This is especially important when working with materials known to release toxic substances.
- Eye Protection: Safety goggles or masks should be worn to protect the eyes from fumes and particles.
- Training and Use: Ensure workers are trained in the proper use of PPE and understand its importance in maintaining health and safety.
Regular Maintenance
Regular maintenance of your laser cutting equipment and ventilation systems can ensure that they operate efficiently and mitigate odors.
- Equipment Maintenance: Regularly inspect and maintain your laser cutting machine to ensure that it is operating efficiently and not producing excessive fumes. This includes cleaning the cutting area, checking for wear, and ensuring that all components are functioning properly.
- Ventilation System Maintenance: Regularly inspect and maintain ventilation systems, including cleaning or replacing filters, inspecting ducts and fans, and ensuring that airflow is unobstructed.
- Monitor Air Quality: Continuously monitor workplace air quality to identify and address any issues. Use air quality sensors to measure levels of volatile organic compounds, particulate matter, and other pollutants.
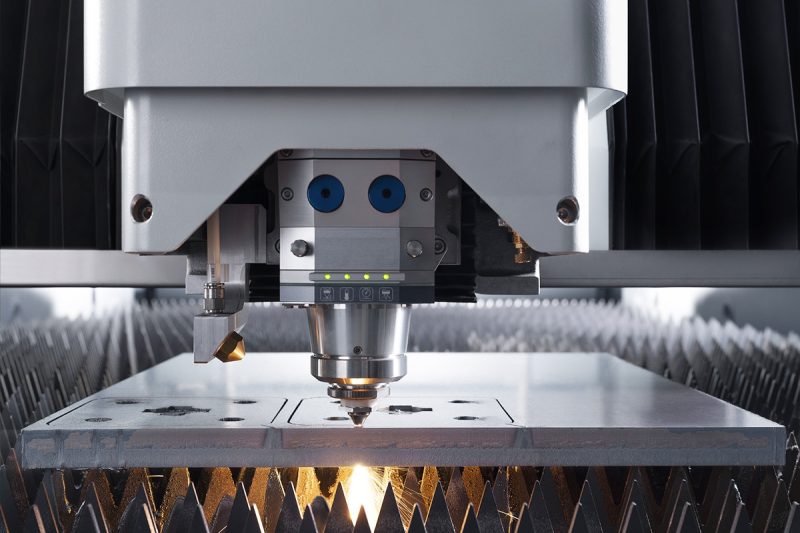
Summary
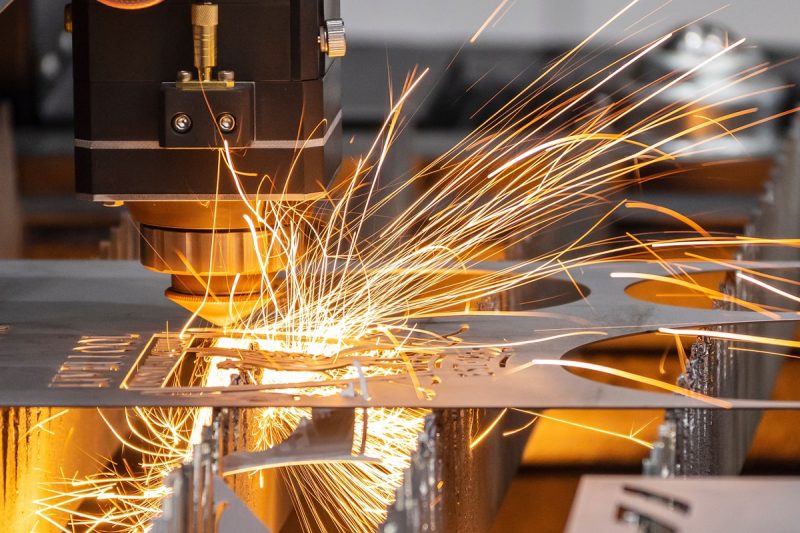
Get Laser Cutting Solutions
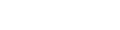
- [email protected]
- [email protected]
- +86-19963414011
- No. 3 Zone A, Lunzhen Industrial Zone,Yucheng City , Shandong Province.