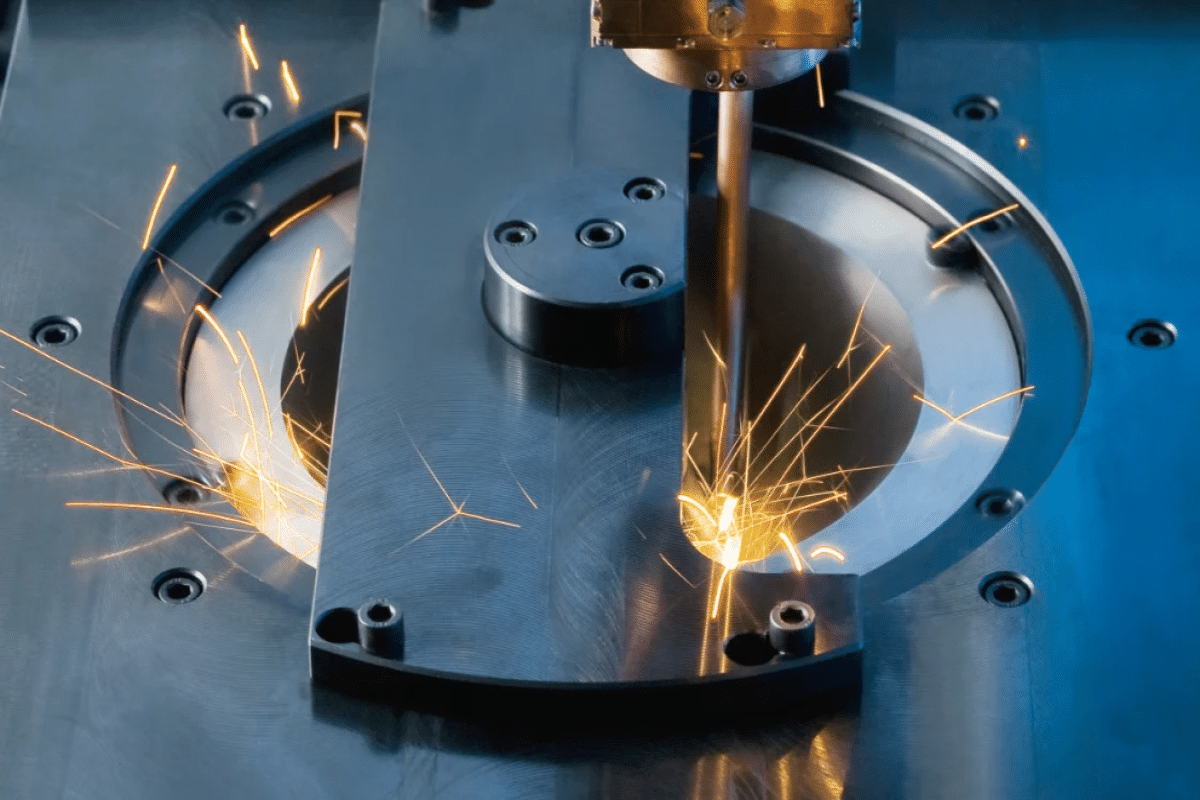
Optimization of Laser Welding Speed And Productivity
Laser welding technology has emerged in modern manufacturing and has attracted the attention of many manufacturers with its high efficiency and speed. The slow speed and limited production capacity of traditional welding methods have attracted much attention to laser welding technology. The concentrated effect of its high-energy laser beam makes the welding process faster, while the high energy density ensures excellent welding results. As technology continues to advance, manufacturers are actively exploring the potential of laser welding machines in terms of speed and productivity.
This article will take an in-depth look at the efficiency of laser welding machines in terms of speed and productivity and analyze the key factors that affect welding speed and productivity. By detailing strategies for improving welding speed and productivity, we’ll reveal how laser welding technology can become a productivity boost for the manufacturing industry.
Table of Contents
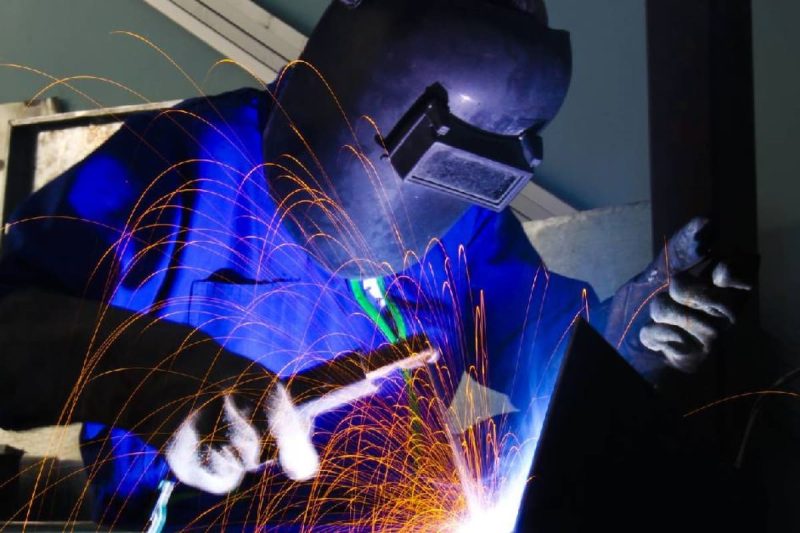
Working principle of laser welding machine
The laser welding machine is a high-precision industrial equipment that uses a laser beam for welding. Its working principle is based on the high energy density and directionality of the laser, which can highly concentrate the welding heat in the welding area to achieve an efficient and precise welding process. The following is the basic working principle of a laser welding machine:
- Laser generator: The core component of the laser welding machine is the laser generator, which is usually used to generate a single-wavelength or multi-wavelength laser beam.
- Generation of laser beam: The laser beam generated by the laser generator is focused and directed through optical elements such as lenses and mirrors, which ensures high precision during the welding process.
- Focus focusing: The focusing system focuses the laser beam to a very small focus. Such focusing can generate high temperatures in the welding area and cause local melting of the workpiece surface.
- Workpiece processing: The laser welding machine irradiates the focused laser beam onto the workpiece, melts the surface of the workpiece through high temperature, and forms a molten pool.
- Molten pool formation and cooling: During laser welding, the metal forms a molten pool under the irradiation of the laser beam, and then cools to form a welded joint.
- Weld seam control: Controlling the movement trajectory and welding parameters of the laser beam can accurately control the formation of weld seams and achieve complex welding patterns and shapes.
- Real-time monitoring: Some advanced laser welding machines are equipped with real-time monitoring systems, which can monitor parameters such as temperature and weld quality during the welding process to ensure welding quality.
The working principle of a laser welding machine gives it unique advantages in precision and speed. Its high efficiency and precision make laser welding technology one of the indispensable processes in modern manufacturing.
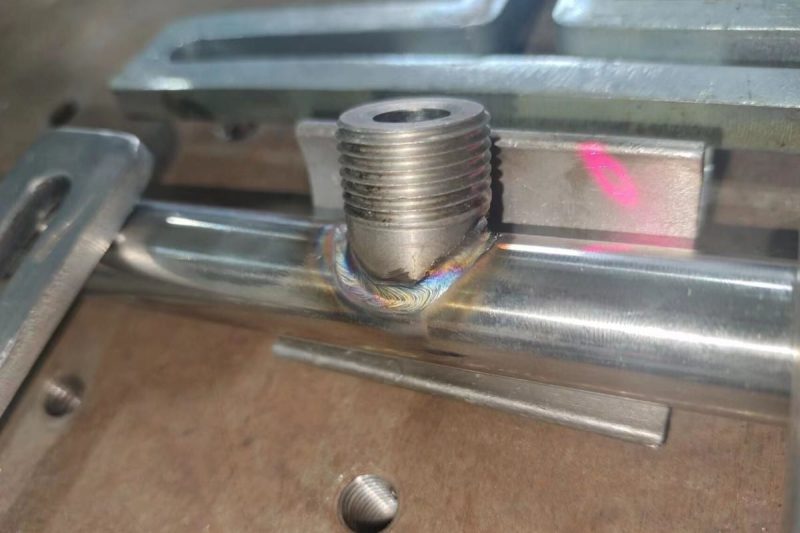
How efficient are laser welding machines in terms of speed and productivity
With their high precision and high efficiency, laser welding machines have become a key driver of speed and productivity in modern manufacturing. The following are several important points of the efficiency of laser welding machines in these two aspects:
High-speed welding process
Laser welding machines use the concentrated action of high-energy laser beams to make the welding process very fast. Compared with traditional welding methods, laser welding can complete more welding tasks in a short time, thus significantly increasing the welding speed. This is particularly important for efficient operations on large-scale production lines, resulting in significant time savings.
Superior Productivity Improvement
Laser welding machines excel at increasing productivity. Its high-energy-density laser beam can quickly melt materials and form uniform, strong welded joints. This not only improves the quality of welding but also greatly reduces the waiting time on the production line. Manufacturers can complete more products in less time and achieve significant improvements in production efficiency.
Improved multi-material applicability
Laser welding machines are suitable for a variety of materials, including metals, plastics, and ceramics. This multi-material applicability enables laser welding technology to cover a wider range of manufacturing areas, thereby demonstrating excellent productivity improvement potential in different industries. Manufacturers have more flexibility in selecting appropriate materials without worrying about sacrificing welding efficiency.
Precision welding and high-quality output
Laser welding machines achieve very precise welding due to their high focus. This means that manufacturers can weld on smaller sizes and more complex structures, providing greater space for product design and manufacturing. High-quality welding output not only improves the overall quality of the product but also reduces the adjustment and repair work in subsequent processes, further improving productivity.
Automation and intelligent applications
Laser welding machines can be combined with automation systems to achieve highly automated production lines. Through the intelligent control system, operators can adjust welding parameters more accurately, improve equipment utilization, and reduce operational complexity. This kind of automation and intelligent application helps to further improve overall production efficiency.
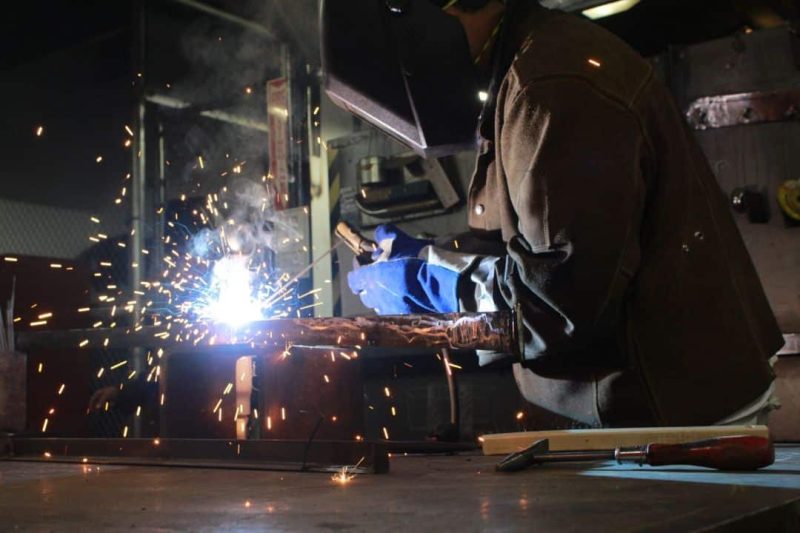
Factors affecting welding speed and productivity
The speed and productivity of laser welding technology are key considerations in manufacturing, and the efficiency of these two aspects is affected by a combination of factors. The following are key factors that affect welding speed and productivity:
Material properties
Different types of materials absorb laser light to different degrees, which directly affects the efficiency of welding. Some materials have higher absorption of laser and are easily heated, thereby increasing the welding speed, while some materials may have poor absorption of laser and require longer welding time. Therefore, the thermal conductivity and optical properties of materials are important factors affecting laser welding speed.
Welding machine equipment performance
The performance of a laser welding machine is directly related to welding speed and productivity. High-power laser sources can provide higher energy density and accelerate the welding process. At the same time, the accuracy, stability, and adaptability of the welding machine to different workpieces also have a significant impact on production efficiency.
Setting of process parameters
Reasonable setting of welding process parameters is the key to ensuring efficient welding. The process parameters of laser welding include laser power, focal length, laser beam diameter, etc. By adjusting these parameters, different welding depths and weld widths can be achieved, thus affecting the overall welding speed.
Welding speed and power matching
The matching relationship between welding speed and laser power directly affects productivity. In some cases, too fast a welding speed may result in poor weld quality, while too low a speed may result in low production efficiency. Therefore, it is necessary to find the best matching of welding speed and power while ensuring welding quality.
Environmental factors
Environmental factors such as temperature and humidity may also affect laser welding. In high-temperature environments, welding parameters may need to be adjusted to accommodate changes such as thermal expansion of the material. Therefore, the control of the production environment is also the key to ensuring the stability and consistency of laser welding.
Welding mode selection
Different welding modes, such as pulsed laser welding and continuous laser welding, have different effects on speed and productivity. Choosing the appropriate welding mode depends on the specific application needs, as well as welding speed and quality requirements.
By deeply understanding these factors and taking corresponding optimization measures, manufacturers can maximize the speed and productivity of laser welding, resulting in a more efficient manufacturing process.
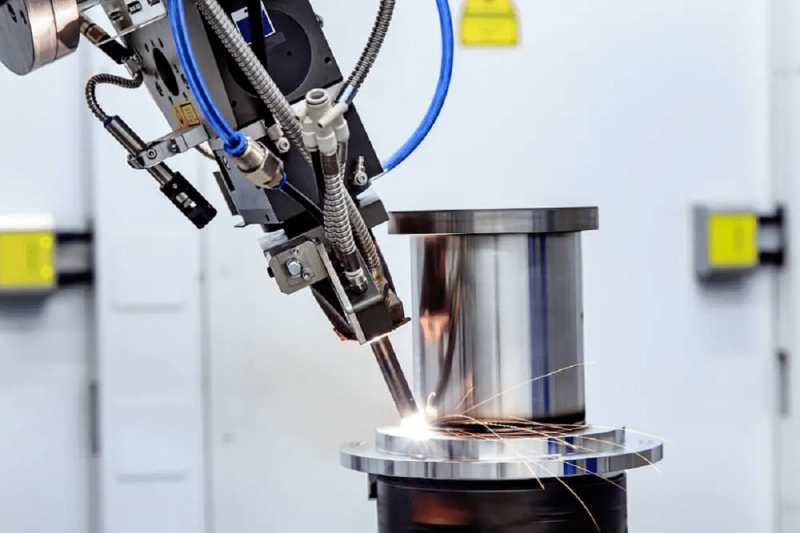
Strategies to improve welding speed and productivity
Improving welding speed and productivity is one of the important goals of the manufacturing industry in pursuing efficiency and competitiveness. In the field of laser welding, adopting a series of scientific strategies can effectively improve welding speed and productivity:
Introduce advanced laser welding technology and equipment
With the continuous advancement of science and technology, the emergence of a new generation of laser welding technology and equipment has provided strong support for improving speed and productivity. High-power laser sources, more advanced laser beam control systems, and intelligent welding machines can significantly improve welding efficiency. Manufacturers can consider upgrading equipment to accommodate more efficient and precise production needs.
Refined process optimization
Precisely adjusting welding process parameters is key to increasing speed and productivity. By optimizing parameters such as laser power, focal length, and pulse frequency, higher welding speeds can be achieved while ensuring welding quality. Systematic process optimization enables faster production without sacrificing quality.
Automation and intelligent applications
The introduction of automation systems and intelligent technology can effectively improve the speed and productivity of laser welding. The automation system can realize automatic control of the welding process, thereby reducing operator intervention, reducing the occurrence of human errors, and improving work efficiency. The intelligent data analysis and monitoring system can monitor parameters in the welding process in real-time, thereby adjusting the process promptly to ensure the consistency and efficiency of production.
Optimal selection of materials
Choosing materials suitable for laser welding is also an important factor in improving speed and productivity. Materials with better laser absorption properties can absorb laser energy faster and achieve more efficient welding. Manufacturers can optimize material selection to meet specific welding needs.
Process improvement and engineering design optimization
Continuous improvement of processes and optimization of engineering design are also important ways to increase welding speed and productivity. By redesigning the welding process, improving equipment layout, and optimizing the workpiece structure, welding complexity can be reduced and production efficiency improved.
Training and technical support
Provide professional training for operators so that they can fully understand and master laser welding technology and operate the equipment more skillfully. In addition, providing timely technical support to help solve problems that may be encountered during the laser welding process helps improve overall production efficiency.
By adopting these strategies, manufacturers can comprehensively improve the speed and productivity of laser welding, achieve more efficient production, reduce costs, and improve product quality, thereby gaining greater advantages in the fierce market competition.
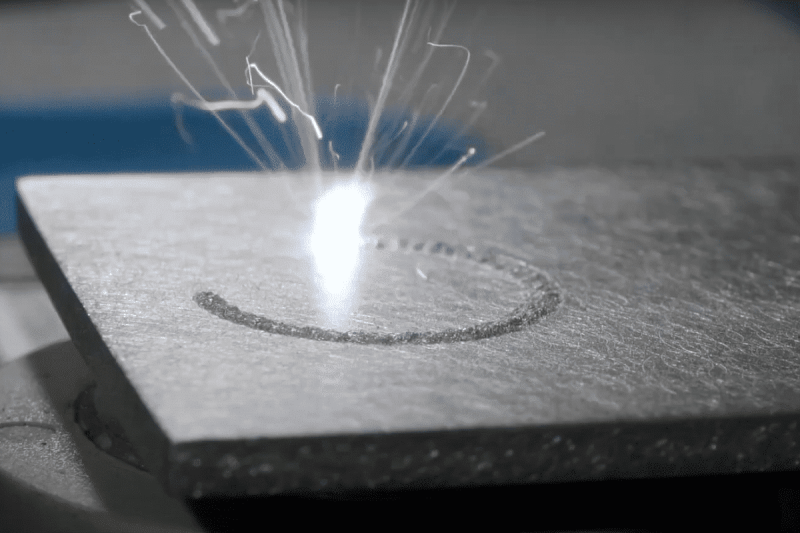
Future development trends of laser welding technology
Laser welding technology plays an increasingly important role in modern manufacturing, and future development trends will revolve around improving efficiency, expanding application areas, and technological innovation. The following are the future development trends of laser welding technology:
- High-power laser sources and ultra-fast laser pulses: Future laser welding technology will continue to pursue higher-power laser sources and ultra-fast laser pulses to increase the energy density of the laser beam and achieve faster and more precise welding.
- Multi-wavelength laser technology: By using multi-wavelength laser sources, it can better adapt to the characteristics of different materials, improve the flexibility and applicability of welding, and make it useful in a wider range of manufacturing and processing scenarios.
- Intelligence and automation: The introduction of intelligent sensing technology, machine learning, and artificial intelligence will improve the real-time monitoring and adjustment capabilities of the welding process, making it more adaptive to different working conditions, reducing human intervention, and improving production efficiency.
- Laser additive manufacturing: Laser additive manufacturing combines laser welding and material deposition technologies to build objects directly from digital models, and is suitable for manufacturing parts with complex structures, such as aerospace engine parts and medical implants.
- Green laser welding technology: Green laser welding technology will gradually receive more attention. This technology uses low-energy laser sources to reduce the impact on the environment and is in line with the trend of sustainable development.
- 3D laser printing: By combining laser welding technology with material deposition technology, 3D laser printing can realize direct printing of complex structures, pushing the manufacturing industry towards a more flexible and customized production method.
- Interdisciplinary integration: The future development of laser welding technology will involveinterdisciplinary integration, including materials science, electronic technology, optics, and other fields. This interdisciplinary collaborative effort will advance laser welding technology to more comprehensively meet diverse manufacturing needs.
Summarize
The rise of laser welding technology not only injects new vitality into the manufacturing industry but also opens up new possibilities for improving speed and productivity. By deeply exploring the efficiency of laser welding machines in terms of speed and productivity, we understand their significant advantages in modern industry, but we also recognize that in the process of pursuing higher efficiency, we face many challenges.
The key factors and optimization strategies for improving the speed and productivity of laser welding technology are not only exploration and innovation in the technical field but also a critical path for the transformation and upgrading of the manufacturing industry. With the promotion of intelligent manufacturing, we can expect laser welding technology to achieve a higher degree of automation and smarter production methods in the future.
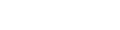
Contact information
- [email protected]
- [email protected]
- +86-19963414011
- No. 3 Zone A, Lunzhen Industrial Zone,Yucheng City , Shandong Province.
Get Laser Solutions