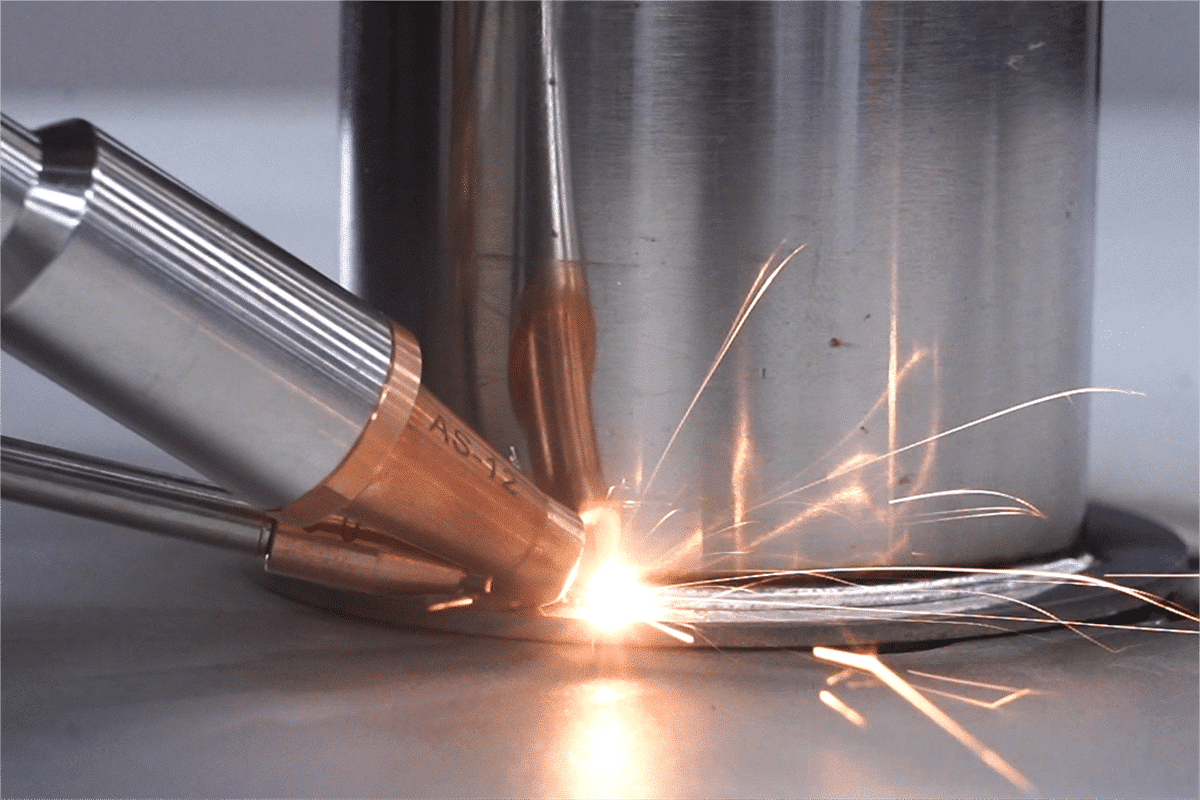
Optimizing Laser Welding Machine Operating Costs: A Comprehensive Analysis
Laser welding machine has revolutionized the metal manufacturing industry by providing precise and efficient welding solutions. By digitally precisely controlling parameters such as laser pulse width, energy, peak power, and repetition frequency, the workpiece is melted to form a specific molten pool, thereby realizing laser welding of the workpiece and completing precision welding that cannot be achieved with traditional processes. As businesses increasingly adopt this advanced technology, The operating costs associated with laser welding machines have become a concern for many people. In this article, we will take an in-depth look at the various factors that affect the operating costs of these machines and explore various strategies to reduce the operating costs of laser welding machines without compromising quality or efficiency.
Table of Contents
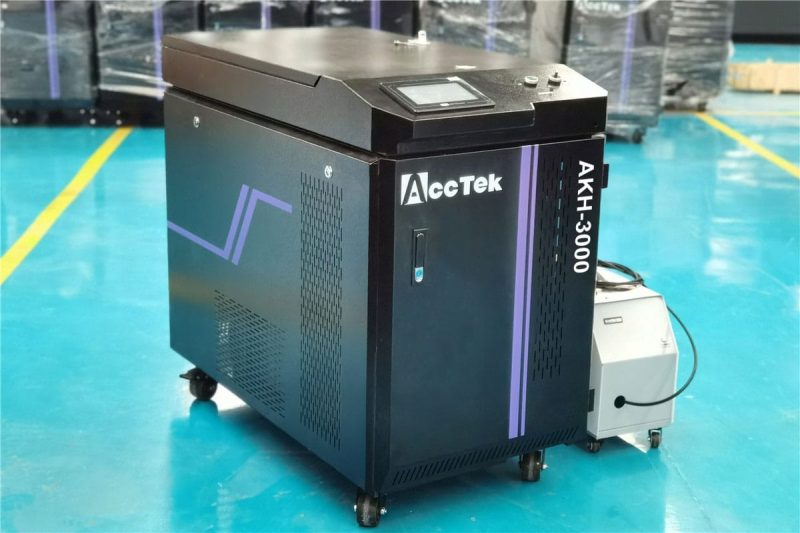
Understanding laser welding machine
Laser welding machine is a highly versatile and precise welding equipment that offers numerous advantages in terms of speed, accuracy, and minimal heat-affected zones. Before analyzing the operating costs of laser welding machines, let us first understand the basic laser welding machine information.
How does a laser welding machine work?
The laser welding machine is an advanced welding equipment that joins metal materials together through the use of a high-energy laser beam. The working principle behind the laser welding machine involves concentrating a highly focused laser beam onto the material’s surface, creating a localized melt zone. This molten region is where the welding occurs, and upon cooling, it forms a strong bond. Unlike traditional welding methods that use an electric arc or flame, laser welding relies on the intense heat generated by the laser.
What materials can laser welding machine be used for?
Laser welding machines can be applied to stainless steel, carbon steel, aluminum, titanium, and other metal materials. Laser welding’s compatibility with different materials is one of its strengths. The ability to weld dissimilar materials is particularly valuable in certain applications. For instance, in the automotive industry, a laser welding machine is used to join steel and aluminum components. Materials compatibility is determined by the materials’ melting points, thermal conductivities, and other physical properties.
Why choose laser welding machine?
As a new type of welding equipment, laser welding machine has been welcomed by many users since its inception. This is because it has advantages that traditional welding does not have, including:
- High Welding Precision: The laser welding machine is highly precise, making it ideal for applications where accuracy is crucial.
- Fast Welding Speed: The high energy density of the laser beam allows for rapid welding, increasing productivity.
- Minimal Heat Affected Zone (HAZ): Laser welding generates a small HAZ, reducing the risk of material distortion or damage.
- Minimal Distortion: The precise control of the laser beam minimizes distortion in the welded materials.
- Automation: Laser welding machines are easily adaptable for automated systems, further enhancing welding efficiency.
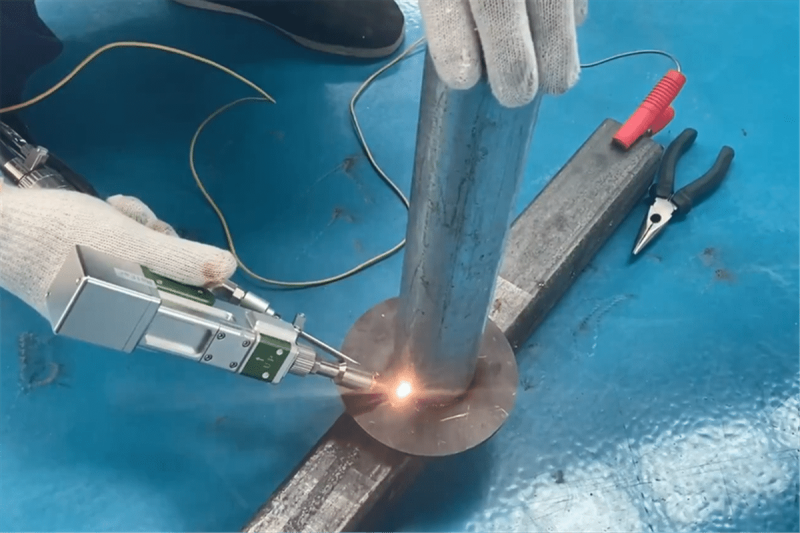
What are the factors that affect the costs of laser welding machines?
The cost of laser welding machines can vary significantly based on several factors. Here are the main factors that affect laser welding operating costs:
- Initial Investment. The first and most significant cost associated with laser welding machines is the initial investment. The price of a handheld laser welding machine is usually between 5,000 and 30,000 US dollars, which is related to the power of the laser welding machine and the brand of the laser generator. If you consider purchasing a robotic laser welding machine, the price will be more expensive, usually between $17,000-$40,000. While high-quality machines with advanced features may come with a substantial price tag, they often offer better performance and durability, ultimately impacting long-term operating costs.
- Energy Consumption. Energy consumption is a critical component of operating costs for any manufacturing equipment, and laser welding machines are no exception. These machines use high-powered lasers to weld materials, and the energy required can be substantial. Normally, a 1000W laser welding machine consumes about 5 kw/h of electricity per hour, and a 3000W laser welding machine consumes about 12 kw/h of electricity per hour. Understanding the energy efficiency of the machine and implementing energy-saving measures can significantly impact operational expenses.
- Maintenance and Repairs. Regular maintenance is essential to ensure the optimal performance and longevity of a laser welding machine. Maintenance costs include routine inspections, cleaning, and replacement of consumables such as optics and nozzles. Routine inspections and cleaning usually only take time, but if the machine breaks down, professional technicians often need to come to repair it, which costs about a few hundred dollars. If the problem with the machine is more serious, or your machine needs more expensive replacement parts, this could cost between a thousand and two thousand dollars.
- Laser welding machines require regular replacement of various optical components during use. Among them, about 40-50 protective lenses are needed every year, and about 20-25 copper nozzles are needed every year. The cost of this part is about US$350-500. Monitoring the consumption rates of these items and sourcing them from reliable suppliers can help control costs. Additionally, investing in high-quality consumables may lead to better performance and longer intervals between replacements.
- Labor Costs. While laser welding machines automate the welding process to a large extent, skilled operators are still required to set up the machine, monitor the welding process, and perform quality control checks. Labor costs include salaries, training, and any additional benefits provided to operators.
- Facility Requirements. The facility where the laser welding machine operates can also increase operating costs. Appropriate ventilation and safety measures must be taken, which may require investment in facility upgrades or modifications to meet the specific requirements of the machine. Creating a work environment that complies with regulations and ensures safety costs approximately $500-1,000, but this cost is only a one-time investment and is not a long-term expense.
- Software and Technology Upgrades. As technology advances, software updates and technological enhancements may become available for laser welding machines. While these upgrades can improve efficiency and performance, they also come with additional costs. This fee usually costs about US$200 per year.
- Scrap and Rework Costs. Laser welding machines aim for precision, but errors can still occur. The cost of scrapped or reworked materials must be considered in the overall operating costs.
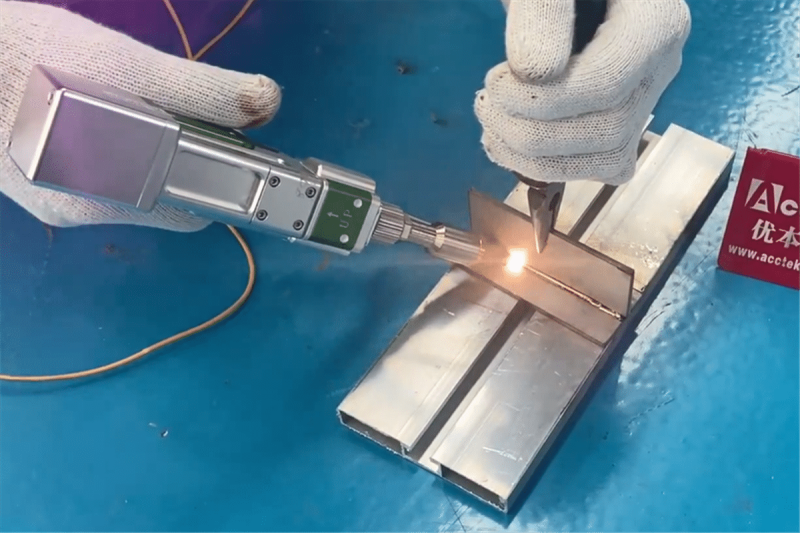
How to reduce the cost of laser welding machine?
Reducing the operating costs of laser welding machines requires a combination of strategic investments, efficient practices, and ongoing maintenance. By choosing the right equipment, optimizing settings, implementing energy-efficient practices, prioritizing maintenance, and investing in automation, businesses can achieve substantial cost savings while maintaining high-quality welding outputs. Additionally, a well-trained workforce, coupled with a data-driven approach, ensures that your laser welding operations remain efficient and cost-effective in the long run. Here are specific ways to reduce laser welding machine operating costs.
Choose the right laser welding machine
The first step in minimizing operating costs is to invest in the right laser welding machine for your specific application. Consider factors such as power requirements, processing speed, and the type of materials you’ll be working with. A machine that appropriately functions for your needs will operate more efficiently, potentially reducing energy consumption and maintenance costs.
Optimize machine settings
Fine-tuning the settings of your laser welding machine is crucial for achieving optimal performance. Adjust parameters such as power, pulse duration, and frequency to match the requirements of your specific welding application. Running the machine at the right settings not only improves welding quality but also reduces unnecessary wear and tear, extending the lifespan of the equipment.
Implement energy-efficient practices
Energy consumption is a significant contributor to operating costs. Implementing energy-efficient practices can lead to substantial savings. Consider adopting the following measures:
- Utilize Pulse Welding: Pulse welding uses short bursts of energy, reducing the overall heat input and energy consumption. This method is particularly effective for thin materials and can result in cost savings.
- Optimize Cooling Systems: Ensure that cooling systems are functioning at their best. Regular maintenance, cleaning, and the use of high-efficiency cooling solutions can prevent overheating and reduce energy consumption.
- Implement Power Management Systems: Invest in power management systems that can regulate energy usage based on demand. This ensures that the machine is only drawing the power it needs at any given time.
Regular maintenance and calibration
Preventive maintenance is essential to keep laser welding machines operating at peak efficiency. Regularly inspect and clean optical components, check for misalignments, and replace worn-out parts promptly. Calibration is equally crucial; it ensures that the machine operates with precision, reducing the likelihood of errors that could result in rework and increased costs. Unplanned downtime due to equipment failure can result in significant production losses, making proactive maintenance a cost-effective strategy.
Train operators effectively
Human error can contribute to increased operating costs. Properly trained operators are more likely to use the equipment efficiently and follow best practices. Provide ongoing training to your team to keep them updated on the latest techniques, maintenance procedures, and safety protocols. A well-trained workforce can help identify issues early, reducing downtime and preventing costly repairs, positively impacting overall operating costs.
Invest in automation and robotics
Integrating automation and robotics into your laser welding processes can lead to significant cost savings. Automated systems operate consistently and efficiently, minimizing errors and reducing the need for human intervention. While the initial investment may be substantial, the long-term benefits in terms of increased productivity and reduced labor costs can outweigh the upfront expense.
Explore cost-effective consumables
Consumables such as laser optics, nozzles, and gases contribute to operating costs. Research and invest in high-quality but cost-effective consumables that offer durability and performance. Evaluate different suppliers and negotiate bulk purchase agreements to secure better deals, ultimately reducing the overall cost of consumables.
Implement a data-driven approach
Utilize data analytics to monitor and optimize your laser welding processes continually. Collect data on parameters such as power usage, machine uptime, and error rates. Analyzing this data can help identify trends, optimize machine settings, and predict potential issues before they result in costly downtime. At the same time, analysis of error rate parameters can continuously improve welding quality and help minimize scrap and rework costs.
Summarize
Optimizing the operating costs of laser welding machines requires a comprehensive approach that considers various factors, from initial investment to ongoing expenses. Businesses must strike a balance between cutting costs and investing in quality to ensure the long-term efficiency and profitability of their operations. Regular assessment, preventive maintenance, and staying abreast of technological advancements are key strategies to keep operating costs in check while maximizing the benefits of laser welding technology. AccTek Laser is a professional laser welding machine manufacturer dedicated to providing customers with high-quality products and excellent services. As an enterprise with its own R&D team, we continue to develop and innovate to provide customers with better welding solutions. Follow AccTek Laser to learn more about laser welding machines.
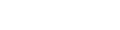
Contact information
- [email protected]
- [email protected]
- +86-19963414011
- No. 3 Zone A, Lunzhen Industrial Zone,Yucheng City , Shandong Province.
Get Laser Solutions