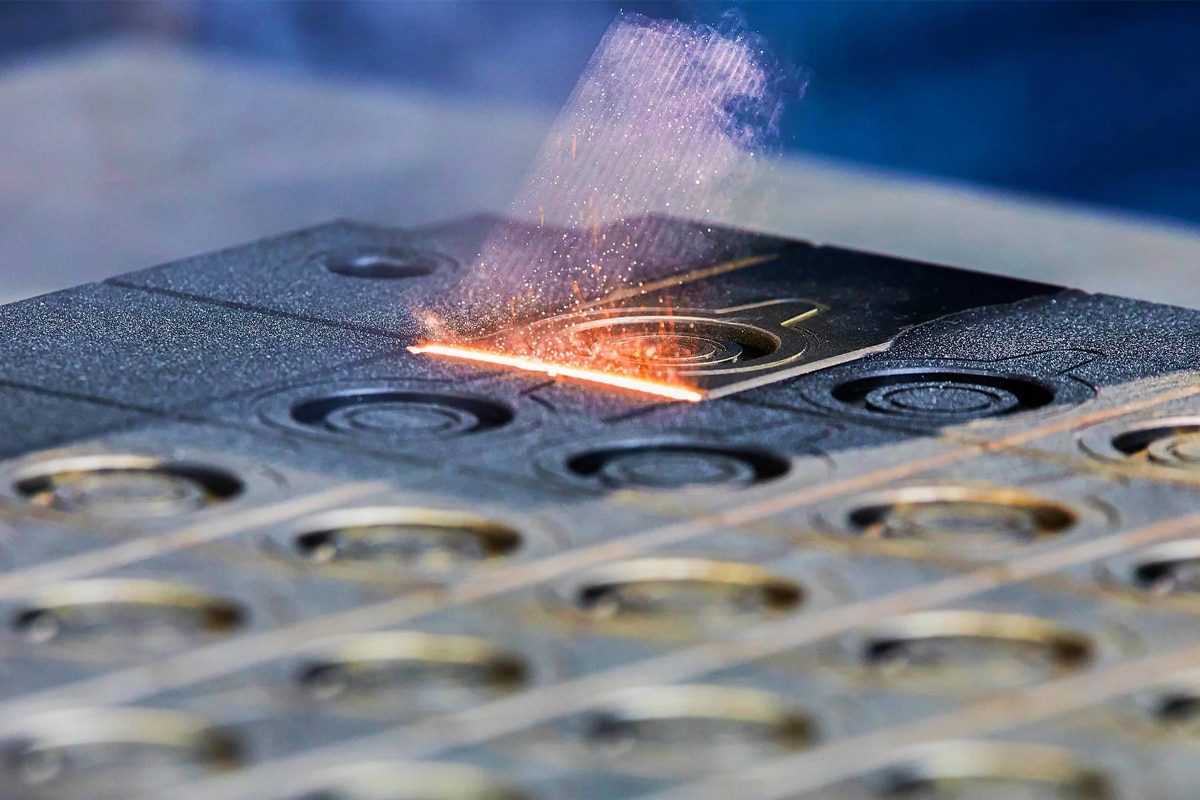
Badanie skuteczności czyszczenia laserowego: kompleksowa analiza
Wśród stale rozwijających się metod czyszczenia przemysłowego, czyszczenie laserowe stało się rewolucyjną technologią, zapewniając precyzyjne, przyjazne dla środowiska i skuteczne rozwiązanie usuwania zanieczyszczeń z różnych powierzchni. Od rdzy i farby po olej i pozostałości, czyszczenie laserowe przyciąga uwagę branż ze względu na możliwość osiągnięcia doskonałych wyników bez użycia środków chemicznych lub materiałów ściernych. Ale jak skuteczne jest czyszczenie laserowe? W tym artykule szczegółowo omawiamy technologię czyszczenia laserowego. Badamy, jak działa technologia czyszczenia laserowego, odkrywamy jej zalety, ograniczenia i zastosowania, oceniamy jej skuteczność w porównaniu z tradycyjnymi metodami czyszczenia i badamy czynniki wpływające na skuteczność czyszczenia laserowego. Dołącz do nas w podróży do złożonego świata czyszczenia laserowego, gdzie precyzja łączy się z produktywnością i zrównoważonym rozwojem.
Spis treści
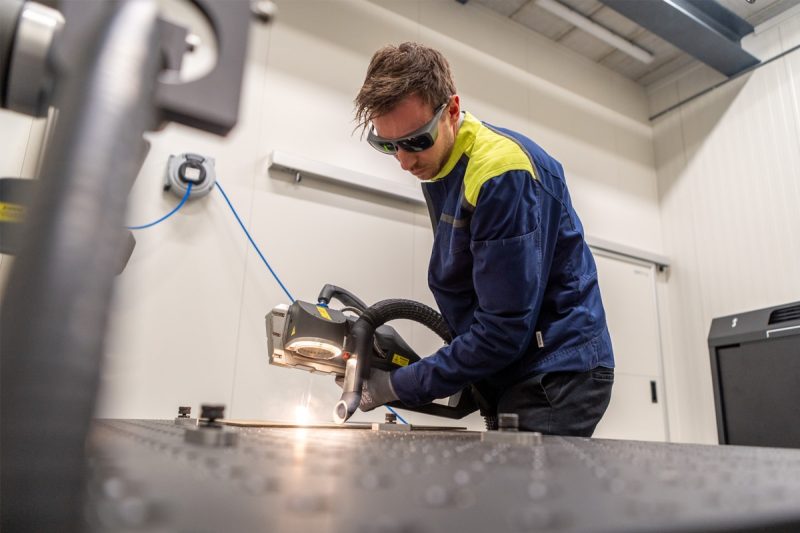
Co to jest czyszczenie laserowe?
Pulsacyjne czyszczenie laserowe to wydajna i precyzyjna technologia czyszczenia powierzchni. Podstawowa zasada czyszczenia laserem pulsacyjnym polega na oddziaływaniu intensywnych impulsów światła laserowego z czyszczonym materiałem. Kiedy wiązka lasera uderza w powierzchnię, szybko podgrzewa zanieczyszczenia lub powłoki do temperatur parowania lub sublimacji. Gwałtowne rozprężanie się pary powoduje powstawanie fal uderzeniowych, które skutecznie usuwają niepożądany materiał z powierzchni, pozostawiając czyste podłoże.
Rodzaje generatorów laserowych stosowanych do czyszczenia
Do czyszczenia laserowego zazwyczaj wykorzystuje się kilka typów generatorów laserowych, z których każdy ma unikalne zalety i cechy odpowiednie do określonych zadań czyszczenia:
- Generatory lasera światłowodowego: Te generatory laserowe wykorzystują światłowody do dostarczania impulsów laserowych o wysokiej energii. Generatory lasera światłowodowego są znane ze swoich kompaktowych rozmiarów, wysokiej jakości wiązki i doskonałej niezawodności, co czyni je idealnymi do zastosowań związanych z precyzyjnym czyszczeniem.
- Generator laserowy z przełączaniem Q: Generator laserowy z przełączaniem Q wykorzystuje mechanizm z przełączaniem Q do kontrolowania uwalniania energii zmagazynowanej we wnęce lasera, generując w ten sposób krótkie impulsy o wysokiej mocy szczytowej. Generatory laserowe z przełączaniem Q dostarczają intensywne impulsy energii w kontrolowany sposób, dzięki czemu idealnie nadają się do usuwania uporczywych zanieczyszczeń i powłok.
- Generator laserowy Nd: YAG: Laser Nd: YAG (granat itrowo-aluminiowy domieszkowany neodymem) to generator laserowy ogólnego przeznaczenia powszechnie stosowany w sprzątaniu przemysłowym. Mogą pracować w trybie fali impulsowej i ciągłej, zapewniając elastyczność i możliwość dostosowania do różnych wymagań w zakresie czyszczenia.
- Generator lasera ekscymerowego: Generatory lasera ekscymerowego wytwarzają pulsacyjne światło ultrafioletowe (UV) poprzez wzbudzanie mieszaniny rzadkich gazów i halogenów. Ze względu na krótką długość fali i minimalną strefę wpływu ciepła lasery te są szczególnie skuteczne w czyszczeniu powierzchni wrażliwych na uszkodzenia termiczne, takich jak materiały półprzewodnikowe.
Zastosowania czyszczenia laserowego
- Obróbka metali: Usuwanie rdzy, farby i tlenków z powierzchni metalowych w przemyśle motoryzacyjnym, lotniczym i produkcyjnym.
- Renowacja obiektów historycznych: Oczyść delikatne artefakty, posągi i pomniki historyczne, nie powodując uszkodzeń materiałów znajdujących się pod spodem.
- Produkcja elektroniki: usuwanie pozostałości, tlenków i powłok z płytek półprzewodnikowych, płytek drukowanych (PCB) i komponentów elektronicznych.
- Precyzyjne czyszczenie: Przygotowanie powierzchni do klejenia, spawania lub powlekania w zastosowaniach wymagających wysokiego poziomu czystości i jakości powierzchni.
- Usuwanie farby: Precyzyjne i skuteczne usuwanie farby i powłok z samolotów, samochodów i sprzętu przemysłowego.
Ogólnie rzecz biorąc, czyszczenie laserowe stanowi wszechstronne, wydajne i przyjazne dla środowiska rozwiązanie do zadań związanych z czyszczeniem i przygotowaniem powierzchni w różnych gałęziach przemysłu, zdolne do precyzyjnego usuwania zanieczyszczeń przy jednoczesnym zachowaniu integralności podłoża.
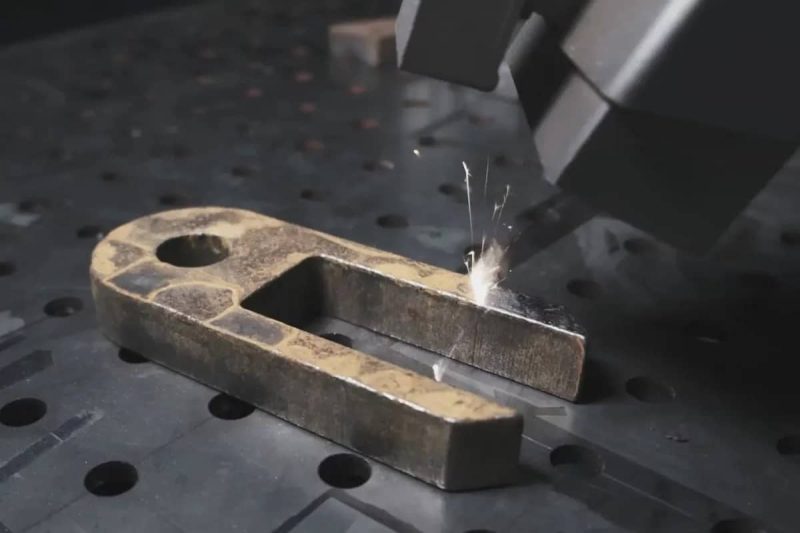
Jak działa czyszczenie laserowe?
Czyszczenie laserowe polega na użyciu silnej wiązki lasera w celu usunięcia zanieczyszczeń, powłok, tlenków i innych niepożądanych materiałów z powierzchni. Proces obejmuje kilka kluczowych etapów zapewniających precyzyjne i skuteczne czyszczenie:
Interakcja lasera i materiałów
Kiedy wiązka lasera uderza w powierzchnię, wchodzi w interakcję z obecnymi w niej materiałami, niezależnie od tego, czy są to zanieczyszczenia, powłoki czy podłoża. Oddziaływanie to polega głównie na absorpcji energii lasera przez materiał. Stopień absorpcji zależy od takich czynników, jak właściwości optyczne materiału, długość fali lasera oraz obecność jakichkolwiek powłok lub obróbki powierzchni.
Mechanizm usuwania zanieczyszczeń
Po pochłonięciu energii lasera szybko nagrzewa materiał do temperatury parowania lub sublimacji. To szybkie nagrzewanie powoduje wydalanie materiału z powierzchni poprzez różne mechanizmy:
- Ablacyjne: W przypadku stałych zanieczyszczeń lub powłok intensywne ciepło powoduje ich odparowanie lub rozpad na małe cząstki, które następnie są wyrzucane z powierzchni.
- Pękanie naprężeniowe: W niektórych przypadkach szybkie nagrzewanie i rozszerzanie materiału może powodować naprężenia termiczne, powodując powstawanie pęknięć, a następnie odrywanie się od powierzchni.
- Tworzenie fali uderzeniowej: Szybka ekspansja odparowanego materiału tworzy fale uderzeniowe, które pomagają usunąć pobliskie zanieczyszczenia lub powłoki, dodatkowo ułatwiając ich usuwanie.
Obróbka powierzchniowa
Po usunięciu niepożądanego materiału z powierzchni pozostaje czyste podłoże gotowe do dalszej obróbki lub aplikacji. Czyszczenie laserowe pozostawia minimalne pozostałości i nie wprowadza dodatkowych zanieczyszczeń, dzięki czemu idealnie nadaje się do zadań związanych z precyzyjnym czyszczeniem i przygotowaniem powierzchni.
Selektywne czyszczenie
Jedną z głównych zalet czyszczenia laserowego jest jego zdolność do selektywnego usuwania określonych materiałów, pozostawiając nienaruszone podłoże. Tę selektywność osiąga się poprzez dostosowanie parametrów, takich jak moc lasera, czas trwania impulsu i wielkość plamki, tak aby celować w żądane zanieczyszczenia lub powłoki bez uszkadzania znajdującej się pod spodem powierzchni.
Ogólnie rzecz biorąc, czyszczenie laserowe zapewnia precyzyjne, wydajne i przyjazne dla środowiska rozwiązanie do usuwania zanieczyszczeń i przygotowywania powierzchni do różnych zastosowań i branż. Jego wszechstronność, selektywność i minimalny wpływ na podłoże sprawiają, że jest to pierwszy wybór do zadań wymagających dużej czystości i jakości powierzchni.
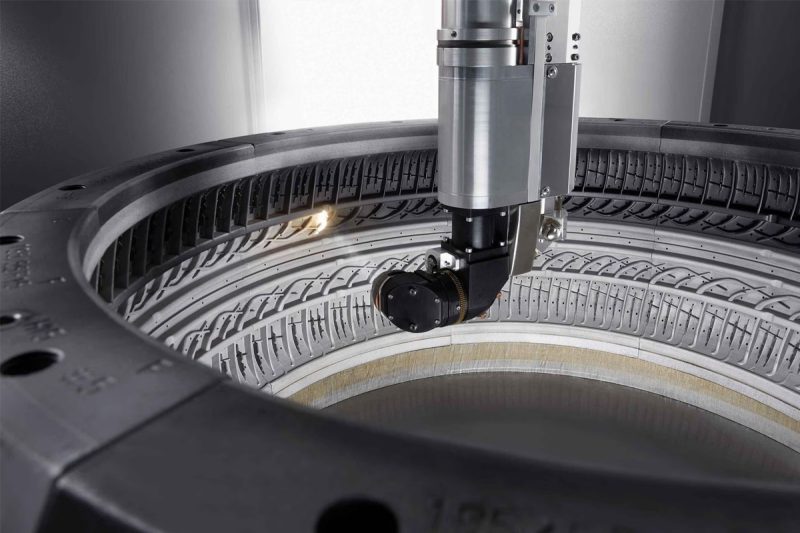
Jakie czynniki wpływają na skuteczność czyszczenia laserowego?
Skuteczność czyszczenia laserowego zależy od delikatnego współdziałania różnych czynników, począwszy od parametrów lasera po właściwości materiału i zanieczyszczeń. Zrozumienie tych czynników jest niezbędne do optymalizacji procesów czyszczenia w szerokim zakresie zastosowań. We wstępie omówimy trzy główne kategorie czynników wpływających na skuteczność czyszczenia laserowego: parametry lasera, właściwości materiału i charakterystykę zanieczyszczeń.
Parametry lasera
- Długość fali: Długość fali wiązki laserowej określa jej interakcję z powierzchnią materiału. Różne materiały mają różną charakterystykę absorpcji przy różnych długościach fal. Dobór odpowiedniej długości fali zapewnia efektywne pochłanianie energii, a co za tym idzie skuteczne czyszczenie. Na przykład metale często dobrze absorbują w zakresie bliskiej podczerwieni, podczas gdy materiały organiczne mogą wymagać krótszych długości fal w widmie widzialnym lub ultrafioletowym.
- Czas trwania impulsu: Czas trwania każdego impulsu lasera, często mierzony w nanosekundach lub pikosekundach, wpływa na ilość energii dostarczanej na powierzchnię. Krótsze czasy trwania impulsów są zazwyczaj bardziej skuteczne w przypadku precyzyjnych zadań czyszczących, ponieważ minimalizują przenoszenie ciepła i zmniejszają ryzyko uszkodzenia podłoża.
- Moc: Moc wiązki lasera decyduje o intensywności energii dostarczanej na powierzchnię. Wyższe poziomy mocy mogą zwiększyć szybkość i skuteczność czyszczenia, ale nadmierna moc może prowadzić do uszkodzenia podłoża lub nadmiernego usuwania materiału. Zrównoważenie mocy z innymi parametrami ma kluczowe znaczenie dla osiągnięcia optymalnych wyników czyszczenia.
Właściwości materiału
- Absorpcyjność: Absorpcyjność materiału określa, jak skutecznie pochłania on energię lasera. Materiały o dużej chłonności są czyszczone skuteczniej, ponieważ pochłaniają większą część padającego światła lasera. Obróbka powierzchni lub powłoki mogą zmieniać chłonność materiału, wpływając na jego reakcję na czyszczenie laserowe.
- Przewodność cieplna: Materiały o wysokiej przewodności cieplnej szybciej rozpraszają ciepło, co może mieć wpływ na skuteczność czyszczenia laserowego. Podłoża o niskiej przewodności cieplnej mogą ulegać miejscowemu nagrzewaniu, co prowadzi do uszkodzeń termicznych lub niepełnego oczyszczenia. Zrozumienie właściwości termicznych materiału jest kluczowe dla optymalizacji parametrów czyszczenia.
Charakterystyka zanieczyszczeń
- Typ: Rodzaj zanieczyszczenia występującego na powierzchni decyduje o jej reakcji na czyszczenie laserowe. Różne zanieczyszczenia mogą wymagać określonych parametrów lasera lub strategii czyszczenia, aby skutecznie je usunąć. Na przykład zanieczyszczenia organiczne, takie jak tłuszcz lub farba, mogą inaczej reagować na czyszczenie laserowe w porównaniu z materiałami nieorganicznymi, takimi jak rdza lub tlenki.
- Grubość: Grubość warstwy zanieczyszczeń wpływa na ilość energii potrzebnej do usunięcia. Grubsze warstwy mogą wymagać większej mocy lasera lub wielokrotnych przejść czyszczących, aby uzyskać całkowite usunięcie. Aby dobrać odpowiednie parametry czyszczenia, niezbędne jest zrozumienie grubości warstwy zanieczyszczeń.
- Czynniki przyczepności: Siła przyczepności pomiędzy zanieczyszczeniem a podłożem wpływa na łatwość usuwania podczas czyszczenia laserowego. Zanieczyszczenia o silnej przyczepności mogą wymagać wyższych poziomów energii lub dodatkowych technik przygotowania powierzchni w celu ułatwienia oderwania. Ocena współczynników przyczepności pomaga określić najskuteczniejszą metodę czyszczenia.
Uwzględniając kompleksowo te czynniki i odpowiednio dostosowując parametry czyszczenia laserowego, praktycy mogą zoptymalizować wydajność, zminimalizować uszkodzenia podłoża i osiągnąć doskonałe wyniki czyszczenia w przypadku różnych zastosowań i materiałów.
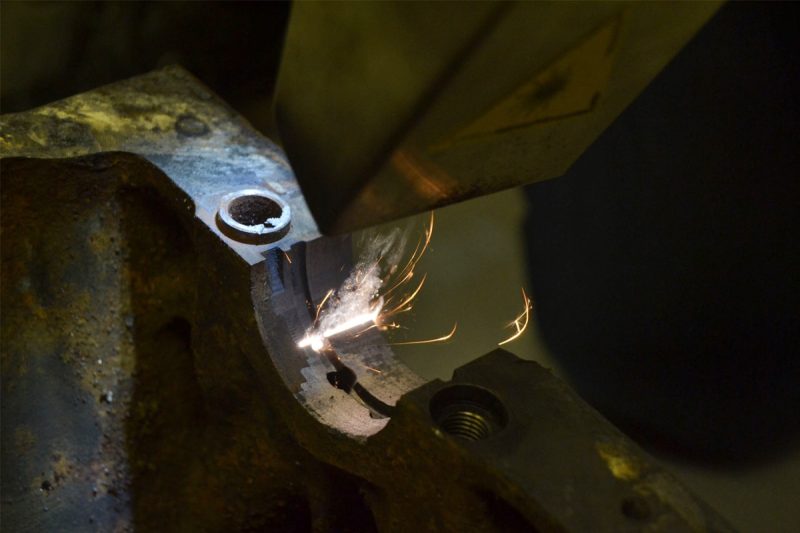
Zalety czyszczenia laserowego
Czyszczenie laserowe oferuje wiele korzyści, które znacząco wpływają na jego skuteczność i atrakcyjność w różnych gałęziach przemysłu. Oto niektóre z kluczowych zalet:
Czyszczenie bezkontaktowe
Czyszczenie laserowe jest procesem bezkontaktowym, co oznacza, że pomiędzy narzędziem czyszczącym a obrabianą powierzchnią nie dochodzi do fizycznego kontaktu. Eliminuje to ryzyko mechanicznego uszkodzenia delikatnych podłoży, takich jak zarysowania czy odkształcenia, które mogą wystąpić w przypadku ściernych metod czyszczenia, takich jak piaskowanie czy szlifowanie. Czyszczenie bezdotykowe pozwala również na obróbkę skomplikowanych lub nieregularnych powierzchni bez naruszania ich integralności.
Nieścierny
W przeciwieństwie do tradycyjnych metod czyszczenia, które opierają się na materiałach ściernych w celu usunięcia zanieczyszczeń, czyszczenie laserowe nie wymaga żadnego fizycznego ścierania. Zamiast tego wykorzystuje energię skupionych wiązek laserowych do usuwania i odparowywania niepożądanych materiałów z powierzchni. Ta nieścierna natura pozwala zachować integralność i wykończenie podłoża, dzięki czemu czyszczenie laserowe jest szczególnie odpowiednie w przypadku wrażliwych materiałów lub powierzchni podatnych na uszkodzenia.
Przyjazny dla środowiska
Czyszczenie laserowe to przyjazne dla środowiska rozwiązanie czyszczące, które eliminuje potrzebę stosowania agresywnych środków chemicznych, rozpuszczalników i materiałów ściernych. Wytwarza minimalną ilość odpadów i nie generuje szkodliwych produktów ubocznych ani emisji, co czyni go zrównoważoną alternatywą dla tradycyjnych metod czyszczenia. Dodatkowo czyszczenie laserowe można przeprowadzić bez użycia wody, co zmniejsza zużycie wody i wymagania dotyczące oczyszczania ścieków.
Precyzyjne i kontrolowane czyszczenie
Czyszczenie laserowe zapewnia niezrównaną precyzję i kontrolę nad procesem czyszczenia. Operatorzy mogą dostosowywać parametry, takie jak moc lasera, czas trwania impulsu i wielkość plamki, aby dostosować operację czyszczenia do konkretnych wymagań. Ta precyzja pozwala na selektywne usuwanie zanieczyszczeń, pozostawiając nienaruszone podłoże, zapewniając spójne i jednolite rezultaty czyszczenia na całej powierzchni.
Mniejsze zapotrzebowanie na materiały eksploatacyjne i odpady
W przeciwieństwie do metod czyszczenia ściernego, które wymagają ciągłego uzupełniania materiałów eksploatacyjnych, takich jak materiały ścierne lub środki ścierne, czyszczenie laserowe jest procesem niewymagającym materiałów eksploatacyjnych. Nie ma konieczności zakupu, obsługi lub utylizacji materiałów ściernych, co pozwala zaoszczędzić koszty i zmniejszyć ilość wytwarzanych odpadów. Ponadto, ponieważ czyszczenie laserowe wytwarza minimalną ilość pozostałości lub odpadów wtórnych, istnieje mniejsza potrzeba czyszczenia lub utylizacji po czyszczeniu.
Ogólnie rzecz biorąc, zalety czyszczenia laserowego, takie jak bezkontaktowe działanie, działanie czyszczące nie powodujące ścierania, dbałość o środowisko, precyzyjna kontrola oraz mniejsza ilość materiałów eksploatacyjnych i odpadów, czynią go atrakcyjnym i wszechstronnym rozwiązaniem. Nadaje się do różnorodnych zastosowań czyszczących w różnych gałęziach przemysłu, od motoryzacji i lotnictwa po produkcję elektroniki i renowację zabytków.
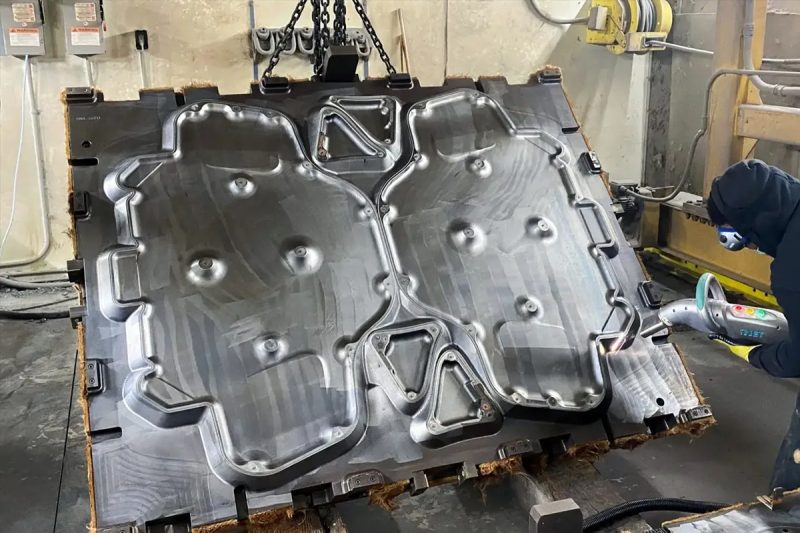
Ograniczenia i wyzwania czyszczenia laserowego
Czyszczenie laserowe niewątpliwie ma wiele zalet, jednak jak każda technologia ma ograniczenia i wyzwania, z którymi należy się liczyć. Oto kilka kluczowych czynników, o których należy pamiętać:
Uszkodzenia materialne i przebarwienia
Chociaż czyszczenie laserowe jest zasadniczo bezścierne i bezdotykowe, nadal istnieje ryzyko uszkodzenia materiału lub odbarwienia, szczególnie w przypadku wrażliwych podłoży. Wysoka intensywność lasera lub długotrwała ekspozycja mogą powodować uszkodzenia termiczne, zmieniać właściwości powierzchni lub powodować zmiany koloru lub tekstury. Staranny dobór parametrów lasera i badanie reprezentatywnych próbek może pomóc w ograniczeniu tego ryzyka.
Względy bezpieczeństwa
Czyszczenie laserowe obejmuje wiązki laserowe o dużej intensywności, które mogą być potencjalnie niebezpieczne dla operatorów i osób postronnych, jeśli nie zostaną podjęte odpowiednie środki bezpieczeństwa. Zapobieganie narażeniu oczu na szkodliwe promieniowanie laserowe może chronić oczy, dlatego operatorzy powinni nosić odpowiednie okulary ochronne lub okulary chroniące przed działaniem lasera, odpowiednie dla określonej używanej długości fali. Dodatkowo może być wymagany system odciągu oparów w celu usunięcia wszelkich odparowanych zanieczyszczeń lub cząstek powstałych podczas procesu czyszczenia, aby zapewnić bezpieczne środowisko pracy.
Koszty wyposażenia i eksploatacji
Wdrożenie technologii czyszczenia laserowego wymaga inwestycji w specjalistyczny sprzęt, w tym w systemy laserowe, optykę i systemy sterowania. Początkowe nakłady kapitałowe mogą być znaczne, należy także wziąć pod uwagę bieżące koszty konserwacji i eksploatacji. Chociaż czyszczenie laserowe oferuje długoterminowe korzyści, takie jak ograniczenie materiałów eksploatacyjnych i odpadów oraz zwiększona wydajność, organizacje muszą porównać te korzyści z kosztami początkowymi.
Ograniczona skuteczność wobec niektórych substancji zanieczyszczających
Chociaż czyszczenie laserowe jest bardzo skuteczne w usuwaniu wielu rodzajów zanieczyszczeń, może być mniej odpowiednie w przypadku niektórych materiałów i substancji. Na przykład materiały silnie odblaskowe lub przezroczyste mogą nie absorbować skutecznie energii lasera, zmniejszając skuteczność czyszczenia. Podobnie grube lub mocno przylegające zanieczyszczenia mogą wymagać wielu metod czyszczenia lub ponownego napełniania, aby je całkowicie usunąć. Zrozumienie ograniczeń czyszczenia laserowego i jego przydatności do konkretnego zastosowania ułatwia osiągnięcie zadowalających rezultatów.
Pomimo tych ograniczeń i wyzwań, czyszczenie laserowe pozostaje wszechstronną i cenną technologią czyszczenia, zapewniającą precyzyjne, przyjazne dla środowiska i wydajne rozwiązania dla szerokiego zakresu zastosowań. Stawiając czoła tym wyzwaniom poprzez staranne planowanie, ocenę ryzyka i wdrażanie odpowiednich środków bezpieczeństwa, organizacje mogą wykorzystać pełny potencjał czyszczenia laserowego, minimalizując jednocześnie potencjalne wady.
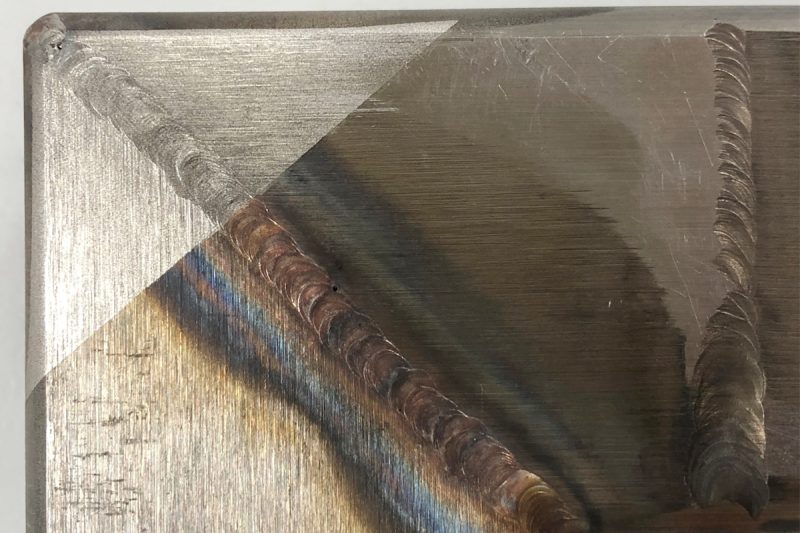
Analiza porównawcza czyszczenia laserowego i tradycyjnych metod czyszczenia
Czyszczenie laserowe porównuje się z tradycyjnymi metodami czyszczenia w oparciu o różne kryteria, w tym skuteczność czyszczenia, uszkodzenie powierzchni, wpływ na środowisko, bezpieczeństwo, koszt i wydajność, wszechstronność i inne:
Skuteczność czyszczenia
- Czyszczenie laserowe: Czyszczenie laserowe zapewnia wysoką precyzję i skuteczność w usuwaniu zanieczyszczeń, powłok i tlenków z powierzchni. Umożliwia dokładne czyszczenie nawet trudno dostępnych miejsc i skomplikowanych geometrii.
- Metody tradycyjne: Tradycyjne metody, takie jak obróbka strumieniowo-ścierna, czyszczenie chemiczne lub szorowanie mechaniczne mogą być skuteczne, ale mogą być pracochłonne i mniej precyzyjne. Mogą również generować odpady wtórne lub wymagać wielu etapów dokładnego czyszczenia.
Uszkodzenie powierzchni
- Czyszczenie laserowe: Czyszczenie laserowe jest bezdotykowe i nieścierne, co minimalizuje ryzyko uszkodzenia lub zniekształcenia powierzchni. Można go stosować na delikatnych materiałach, nie naruszając ich integralności.
- Metody tradycyjne: Niektóre tradycyjne metody, takie jak obróbka strumieniowo-ścierna lub szorowanie mechaniczne, mogą powodować uszkodzenia powierzchni, zarysowania lub zniekształcenia, szczególnie na bardziej miękkich lub delikatnych podłożach.
Wpływ środowiska
- Czyszczenie laserowe: Czyszczenie laserowe jest przyjazne dla środowiska, ponieważ nie wymaga użycia środków chemicznych ani materiałów ściernych. Wytwarza minimalną ilość odpadów i nie generuje szkodliwych emisji.
- Metody tradycyjne: Tradycyjne metody czyszczenia mogą obejmować użycie środków chemicznych, rozpuszczalników lub materiałów ściernych, które mogą być szkodliwe dla środowiska. Mogą również generować ścieki lub emisje do powietrza wymagające oczyszczenia.
Bezpieczeństwo
- Czyszczenie laserowe: Czyszczenie laserowe wymaga odpowiednich środków bezpieczeństwa w celu ochrony przed narażeniem na promieniowanie laserowe. Operatorzy muszą nosić odpowiednią ochronę oczu, a w celu usunięcia oparów lub cząstek może być konieczne odsysanie oparów.
- Metody tradycyjne: Metody tradycyjne mogą stwarzać zagrożenia dla bezpieczeństwa, takie jak narażenie na niebezpieczne chemikalia, wdychanie pyłu lub oparów lub obrażenia spowodowane materiałami lub sprzętem ściernym.
Koszt i wydajność
- Czyszczenie laserowe: Chociaż technologia czyszczenia laserowego wymaga wyższych inwestycji w kapitał początkowy, zapewnia długoterminowe oszczędności dzięki zmniejszeniu kosztów robocizny, materiałów eksploatacyjnych i usuwania odpadów. Zapewnia także wyższą wydajność i produktywność.
- Tradycyjne metody: Tradycyjne metody czyszczenia mogą wiązać się z niższymi kosztami początkowymi, ale mogą być pracochłonne i czasochłonne. Mogą również wymagać częstego uzupełniania materiałów eksploatacyjnych lub usuwania odpadów, co z czasem prowadzi do wyższych kosztów operacyjnych.
Wszechstronność
- Czyszczenie laserowe: Czyszczenie laserowe jest wszechstronne i można je dostosować do różnych materiałów, powierzchni i zanieczyszczeń. Zapewnia precyzyjną kontrolę nad parametrami czyszczenia, dzięki czemu nadaje się do szerokiego zakresu zastosowań.
- Metody tradycyjne: Tradycyjne metody czyszczenia różnią się wszechstronnością i skutecznością w zależności od rodzaju materiału i zanieczyszczenia. Niektóre metody mogą mieć ograniczone zastosowanie do określonych powierzchni lub warunków.
Podsumowując, choć tradycyjne metody czyszczenia mają swoje zalety, czyszczenie laserowe oferuje szereg korzyści w zakresie wydajności, precyzji, przyjazności dla środowiska i długoterminowych oszczędności. Jednakże wybór pomiędzy czyszczeniem laserowym a metodami tradycyjnymi ostatecznie zależy od takich czynników, jak specyficzne wymagania dotyczące czyszczenia, charakter powierzchni i zanieczyszczeń oraz dostępne zasoby i wiedza specjalistyczna.
Podsumować
Podsumowując, czyszczenie laserowe wykazuje doskonałą skuteczność czyszczenia, zapewniając precyzyjne, przyjazne dla środowiska i opłacalne rozwiązanie zadań czyszczenia powierzchni. Jego zdolność do dokładnego czyszczenia przy jednoczesnym zachowaniu integralności powierzchni i minimalizacji wpływu na środowisko sprawia, że jest to pierwszy wybór dla branż poszukujących optymalnej wydajności czyszczenia i zrównoważonego rozwoju.
W tym artykule szczegółowo przyglądamy się skuteczności czyszczenia laserowego, badając jego skuteczność według różnych kryteriów. Dyskusja na temat efektywności czyszczenia za pomocą maszyn do czyszczenia laserowego służy nie tylko efektywnemu czyszczeniu, ale także promowaniu zrównoważonego rozwoju czyszczenia laserowego. Laser AccTek zapewnia nie tylko najnowocześniejsze rozwiązania laserowe maszyny czyszczące ale także rozwiązania szyte na miarę, zapewniające bezpieczne środowisko pracy. Skonsultuj się z nami już dziś i przekonaj się, jak nasza wiedza może przekształcić Twoje miejsce pracy w wydajną i bezpieczną przestrzeń.
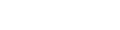
Informacje kontaktowe
- [email protected]
- [email protected]
- +86-19963414011
- Nr 3 Strefa A, strefa przemysłowa Lunzhen, miasto Yucheng, prowincja Shandong.
Uzyskaj rozwiązania laserowe