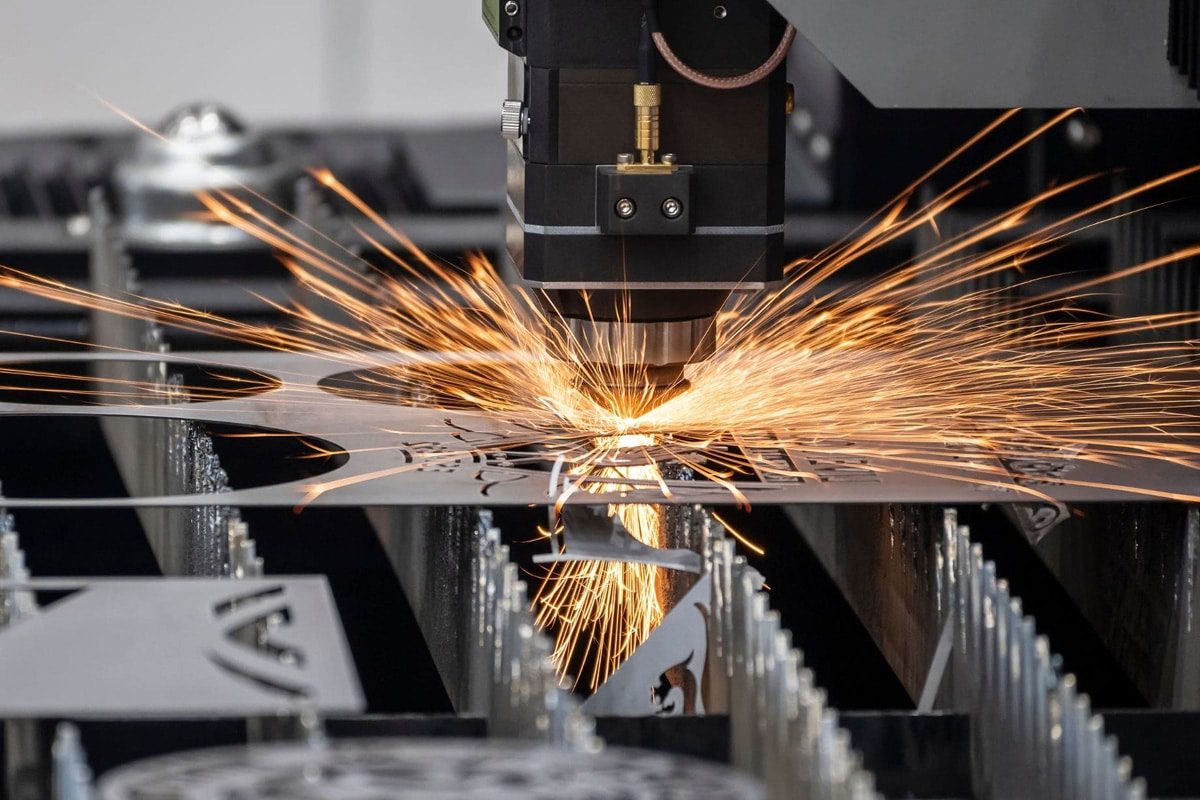
Hałas maszyny do cięcia laserowego
Maszyny do cięcia laserowego są szeroko stosowane w wielu gałęziach przemysłu ze względu na ich wysoką wydajność i precyzyjne możliwości cięcia, szczególnie w przemyśle wytwórczym, motoryzacyjnym i lotniczym. Jednak hałas generowany przez maszyny do cięcia laserowego podczas pracy jest również problemem, którego nie można ignorować. Nadmierny hałas nie tylko wpływa na środowisko pracy operatora, ale może również stanowić potencjalne zagrożenie dla zdrowia. Dlatego szczególnie ważne jest zrozumienie źródła hałasu, czynników wpływających i środków zaradczych.
Hałas maszyn do cięcia laserowego pochodzi głównie z kilku aspektów: dźwięku pracy części mechanicznych, takich jak silniki i wentylatory, wibracji podczas cięcia, hałasu układów wydechowych i wentylacyjnych oraz dźwięku układów transportu materiałów. Różna moc cięcia, prędkość i właściwości materiału będą wpływać na poziom tych hałasów. Dobra konstrukcja maszyny i wydajne systemy chłodzenia i wentylacji mogą pomóc w redukcji hałasu, podczas gdy dostosowanie parametrów podczas cięcia i właściwości materiału również będą miały wpływ na hałas w pewnym stopniu.
Jeśli chodzi o kontrolę hałasu, racjonalne wykorzystanie sprzętu do izolacji akustycznej, zoptymalizowana konstrukcja maszyny oraz regularna konserwacja i smarowanie sprzętu są skutecznymi środkami redukcji hałasu. To nie tylko poprawia środowisko pracy operatora, ale także skutecznie zmniejsza ryzyko zdrowotne wynikające z długotrwałego narażenia na hałas w środowiskach o wysokim poziomie hałasu. Zrozumienie i podjęcie odpowiednich środków kontroli hałasu jest kluczem do zapewnienia bezpiecznego i zdrowego środowiska produkcyjnego.
Spis treści
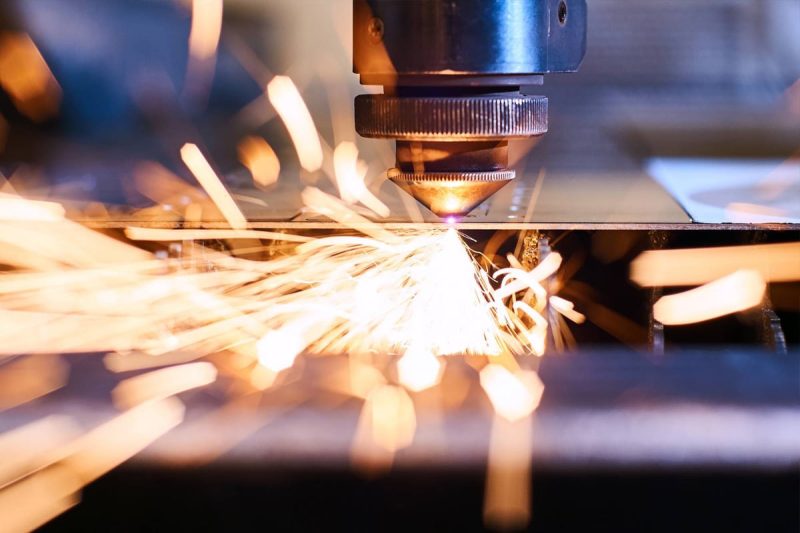
Zrozumienie hałasu w maszynach do cięcia laserowego
Źródła hałasu maszyny do cięcia laserowego są złożone i można je podzielić na cztery główne kategorie: części mechaniczne, wibracje podczas cięcia, systemy wydechowe i wentylacyjne oraz systemy transportu materiałów. Każdy rodzaj źródła hałasu ma różne częstotliwości i charakterystyki, które wpływają na poziom hałasu sprzętu podczas pracy. Poniżej przedstawiono szczegółową analizę tych źródeł hałasu:
Elementy mechaniczne (silniki EG, wentylatory)
Częstotliwość
Elementy mechaniczne, takie jak silniki i wentylatory, generują hałas o częstotliwościach, które zależą przede wszystkim od mocy i prędkości sprzętu. Częstotliwości hałasu silnika wynoszą zazwyczaj od 50 Hz do 300 Hz, przy czym niższe częstotliwości pochodzą głównie z dużych lub dużej mocy silników. Wentylatory generują hałas o średniej i wysokiej częstotliwości, zazwyczaj w zakresie od 500 Hz do 2000 Hz, i mają tendencję do wyższych częstotliwości, szczególnie gdy wentylator pracuje z dużą prędkością.
Charakterystyczny
Hałas silnika jest stosunkowo stabilny, zwykle występuje jako niskoczęstotliwościowy, ciągły szum. Hałas wentylatora to głównie ostry, ciągły hałas o wysokiej częstotliwości, szczególnie podczas pracy z dużą prędkością, hałas może być bardziej wyraźny. Starzejące się silniki lub wentylatory zwykle wytwarzają głośniejszy hałas, szczególnie gdy występuje brak smarowania lub zużycie części. Hałas nie tylko wzrośnie, ale może mu również towarzyszyć hałas, taki jak tarcie mechaniczne.
Wibracje podczas cięcia
Częstotliwość
Podczas procesu cięcia interakcja między laserem a materiałem powoduje hałas wibracyjny. Częstotliwość wibracji jest ściśle związana z grubością i charakterystyką materiału. Podczas cięcia cieńszych materiałów częstotliwość hałasu wynosi zwykle od 200 Hz do 1000 Hz; podczas cięcia grubszych materiałów, zwłaszcza stali lub innych twardych materiałów o grubości większej niż 10 mm, częstotliwość hałasu generowanego przez wibrację wynosi zwykle od 100 Hz do 500 Hz.
Charakterystyczny
Hałas wibracyjny zwykle objawia się nieregularnymi, krótkimi dźwiękami uderzeniowymi. Wibracje cienkich materiałów wytwarzają dźwięki o wyższej częstotliwości, które są zwykle ostrzejsze; grube materiały powodują hałas wibracyjny o niskiej częstotliwości i ciągły, który brzmi matowo. Ponadto intensywność hałasu wibracyjnego zmienia się wraz z grubością materiału i prędkością cięcia. Podczas szybszego cięcia wibracje będą bardziej wyraźne, a poziom hałasu odpowiednio wzrośnie.
Systemy wydechowe i wentylacyjne
Częstotliwość
Częstotliwości hałasu układu wydechowego i wentylacyjnego zwykle mieszczą się w zakresie od 500 Hz do 4000 Hz. Im wyższa prędkość wentylatora, tym wyższa częstotliwość wytwarzanego hałasu. Duże urządzenia wydechowe zazwyczaj wytwarzają hałas o niższej częstotliwości, podczas gdy małe, szybkoobrotowe wentylatory mają tendencję do wytwarzania dźwięków o wyższej częstotliwości.
Charakterystyczny
Hałas układu wydechowego i wentylacyjnego jest zazwyczaj ciągłym i ostrym szumem wiatru, który jest bardziej wyraźny, gdy wentylator pracuje z dużą prędkością. Jeśli układ wentylacyjny nie jest prawidłowo zaprojektowany lub kanał powietrzny jest zablokowany, przepływ powietrza zostanie zablokowany, co zwiększy hałas. Ponadto rezonans w kanale wentylacyjnym może również wzmacniać pewne częstotliwości hałasu, czyniąc go bardziej ostrym. Ponieważ układ wydechowy musi pracować nieprzerwanie przez długi czas, tego rodzaju hałas może zawsze występować podczas procesu cięcia.
Systemy transportu materiałów
Częstotliwość
Częstotliwości hałasu systemów transportu materiałów wynoszą zazwyczaj od 100 Hz do 2000 Hz, w zależności od ciężaru materiału i sposobu działania systemu. Lekkie materiały zazwyczaj wytwarzają hałas o wyższej częstotliwości podczas transportu, podczas gdy ciężkie materiały wytwarzają hałas o niższej częstotliwości.
Charakterystyczny
Hałas podczas transportu materiałów jest często przerywany i powstaje w miarę załadunku, rozładunku lub transportu materiałów. Ciężkie materiały zazwyczaj wytwarzają dźwięki zderzeń o niskiej częstotliwości, które są cięższe, podczas gdy lekkie materiały mogą wytwarzać dźwięki stukania o wyższej częstotliwości, które są lżejsze, ale bardziej ostre. Jeśli części mechaniczne w systemie nie są dobrze utrzymane, tarcie i zacinanie się będą wytwarzać dodatkowy hałas, taki jak ostre dźwięki szlifowania lub dźwięki zderzeń metalu z metalem.
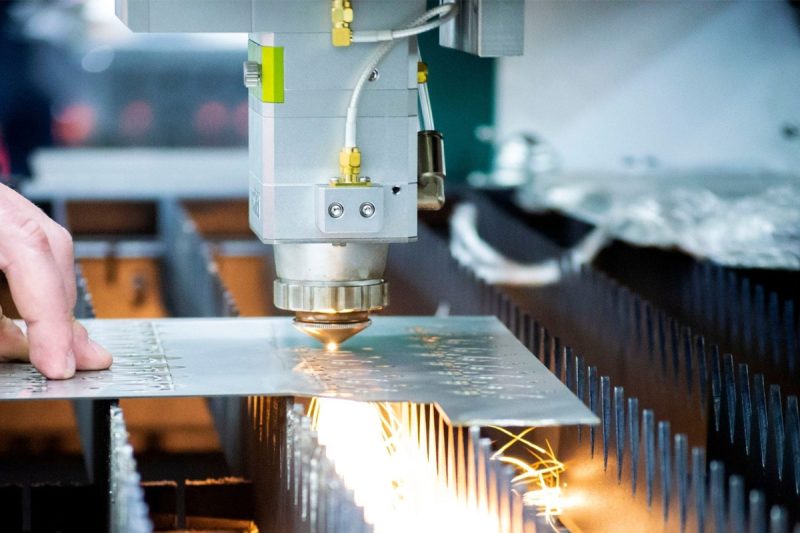
Czynniki wpływające na poziom hałasu
Projektowanie maszyn i materiały budowlane
Konstrukcja i materiały konstrukcyjne maszyny do cięcia laserowego mają znaczący wpływ na poziom hałasu. Dobrze zaprojektowana maszyna może skutecznie redukować wibracje i hałas, zazwyczaj wykorzystując wytrzymałe ramy i bardzo sztywne materiały w celu zmniejszenia efektów rezonansu. Wysokiej jakości materiały konstrukcyjne, takie jak stal lub stopy aluminium, mogą pochłaniać i tłumić wibracje, zmniejszając rozprzestrzenianie się fal dźwiękowych. Ponadto odpowiednia konstrukcja, taka jak rozsądny układ komponentów i metody połączeń, może skutecznie zmniejszyć wzajemne zakłócenia między różnymi komponentami, zmniejszając tym samym ogólny poziom hałasu.
Parametry cięcia
Parametry cięcia, w tym moc cięcia i prędkość, bezpośrednio wpływają na stan pracy i poziom hałasu maszyny do cięcia laserowego. Ogólnie rzecz biorąc, wyższa moc i prędkość będą prowadzić do silniejszych wibracji, co zwiększy hałas. Na przykład podczas cięcia ciężkich materiałów należy zwiększyć moc, aby zapewnić jakość cięcia, co często powoduje silniejsze wibracje i hałas. Dlatego też właściwe dostosowanie parametrów cięcia, zwłaszcza podczas obróbki różnych materiałów, może skutecznie zmniejszyć hałas, zapewniając jednocześnie efekt cięcia.
Właściwości materiału
Charakterystyka ciętego materiału, w tym grubość, gęstość i skład, mają wpływ na poziom hałasu. Mówiąc ogólnie, ciężkie lub twarde materiały, takie jak grube blachy stalowe lub stopy, zwykle generują więcej hałasu podczas cięcia. Dzieje się tak, ponieważ gdy twardsze materiały są cięte laserem, generowane ciepło i wibracje są bardziej znaczące, co powoduje wzrost intensywności fali dźwiękowej. Ponadto skład materiału również wpływa na charakterystykę dźwięku podczas cięcia. Częstotliwość i intensywność hałasu generowanego przez materiały o różnym składzie podczas cięcia mogą być różne.
Systemy chłodzenia i wentylacji
Wydajność układu chłodzenia jest bezpośrednio związana ze stanem roboczym wentylatora, co z kolei wpływa na poziom hałasu. Konstrukcja układu chłodzenia musi zapewniać, że ciepło i dym wytwarzane podczas procesu cięcia są skutecznie odprowadzane. Jeśli układ chłodzenia jest nieefektywny, obciążenie wentylatora wzrośnie i będzie musiał pracować z większą prędkością, aby utrzymać normalną temperaturę sprzętu, co spowoduje dodatkowy hałas. Optymalizacja konstrukcji układu chłodzenia i wentylacji może nie tylko poprawić wydajność roboczą sprzętu, ale także zmniejszyć poziom hałasu podczas pracy.
Skuteczność środków dźwiękoszczelnych
W projektowaniu maszyn do cięcia laserowego rozsądne środki izolacji akustycznej mogą znacznie obniżyć poziom hałasu. Montaż obudów dźwiękoszczelnych i stosowanie materiałów pochłaniających dźwięk to powszechne metody redukcji hałasu. Jednak skuteczność tych środków jest ściśle związana z jakością i konstrukcją sprzętu dźwiękoszczelnego. Wysokiej jakości obudowy dźwiękoszczelne i materiały pochłaniające dźwięk mogą skutecznie blokować i pochłaniać dźwięk, podczas gdy sprzęt dźwiękoszczelny, który jest źle zaprojektowany lub wykonany z gorszych materiałów, może mieć ograniczoną skuteczność. Dlatego podczas instalowania środków izolacji akustycznej konieczne jest kompleksowe rozważenie cech materiału, koncepcji projektowych i rzeczywistych scenariuszy zastosowań, aby uzyskać najlepszy efekt redukcji hałasu.
Konserwacja i smarowanie ruchomych części
Ruchome części maszyny do cięcia laserowego będą generować dodatkowy hałas z powodu tarcia i zużycia podczas pracy. Dlatego dobra konserwacja i regularne smarowanie są niezbędne do zmniejszenia hałasu. Regularne kontrole i konserwacja ruchomych części, takich jak prowadnice, przekładnie i silniki, mogą nie tylko zmniejszyć tarcie, ale także wydłużyć żywotność sprzętu. Stosowanie odpowiednich środków smarnych może zmniejszyć tarcie między częściami mechanicznymi, tym samym zmniejszając hałas podczas pracy. Ponadto utrzymywanie ruchomych części w czystości może zapobiec wpływowi brudu i zanieczyszczeń na działanie sprzętu, co dodatkowo zmniejsza poziom hałasu.
Podsumowując, na poziom hałasu maszyny do cięcia laserowego wpływa wiele czynników. Poprzez optymalizację projektu, dostosowanie parametrów cięcia, dobór odpowiednich materiałów, poprawę wydajności układu chłodzenia, skuteczne środki izolacji akustycznej i dobrą konserwację, hałas można znacznie zmniejszyć. Popraw komfort i bezpieczeństwo środowiska pracy.
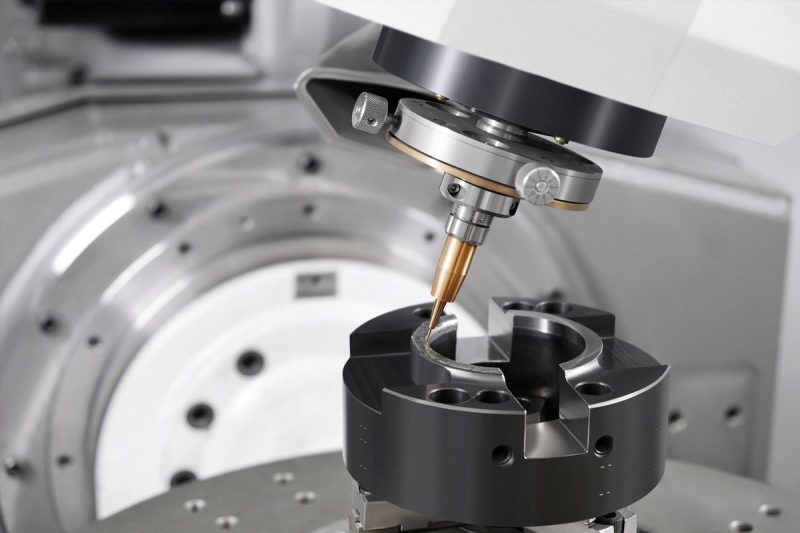
Zagadnienia BHP
Hałas generowany podczas pracy maszyny do cięcia laserowego nie tylko wpływa na komfort środowiska pracy, ale może również stanowić zagrożenie dla zdrowia i bezpieczeństwa operatorów. Poniżej przedstawiono szczegółową analizę istotnych kwestii zdrowia i bezpieczeństwa:
Potencjalne zagrożenia dla zdrowia związane z narażeniem na wysoki poziom hałasu
Długotrwałe narażenie na hałas o wysokiej intensywności może prowadzić do szeregu problemów zdrowotnych. Przede wszystkim najczęstszym skutkiem jest utrata słuchu, zwłaszcza utrata słuchu o wysokiej częstotliwości, która może stopniowo się pogarszać bez zauważenia. Ciągła stymulacja hałasem może powodować uszkodzenie komórek słuchowych w uchu, co prowadzi do nieodwracalnego upośledzenia słuchu. Ponadto hałas o wysokiej intensywności może również powodować szumy uszne, czyli gdy nie ma zewnętrznej stymulacji dźwiękowej, w uchu nadal występuje brzęczenie lub inny dźwięk. Ten objaw może znacznie wpływać na codzienne życie i wydajność pracy.
Oprócz problemów ze słuchem hałas może mieć również znaczący wpływ na zdrowie psychiczne. Badania pokazują, że długotrwałe narażenie na hałas może prowadzić do problemów ze zdrowiem psychicznym, takich jak stres, lęk i depresja. Hałas nie tylko zakłóca koncentrację w pracy i zmniejsza produktywność, ale może również wpływać na jakość snu, powodując szereg problemów zdrowotnych związanych ze snem, takich jak zmęczenie i obniżona odporność.
Przepisy dotyczące bezpieczeństwa i higieny pracy związane z narażeniem na hałas w miejscu pracy
Aby chronić zdrowie pracowników, wiele krajów i regionów uchwaliło przepisy dotyczące bezpieczeństwa i higieny pracy dotyczące narażenia na hałas w miejscu pracy. Przepisy te zazwyczaj ustalają dopuszczalne limity narażenia na hałas, a gdy limity te zostaną przekroczone, pracodawcy muszą podjąć odpowiednie środki w celu zmniejszenia hałasu. Przepisy te wymagają również regularnego monitorowania poziomu hałasu w miejscu pracy i zapewnienia odpowiednich badań lekarskich w celu wczesnego wykrywania problemów zdrowotnych związanych z hałasem.
Na przykład amerykańska Agencja Bezpieczeństwa i Higieny Pracy (OSHA) wymaga od pracowników stosowania środków kontroli hałasu lub zapewnienia odpowiedniego sprzętu ochrony osobistej (takiego jak nauszniki i zatyczki do uszu) podczas pracy w środowisku o poziomie hałasu przekraczającym 85 decybeli. Gdy wiele firm stosuje się do tych przepisów, często wdrażają oceny narażenia na hałas i plany kontroli, aby zapewnić, że środowisko pracy spełnia normy bezpieczeństwa.
Znaczenie wdrażania środków kontroli hałasu w celu ochrony pracowników
Skuteczne środki kontroli hałasu są niezbędne do ochrony zdrowia pracowników. Firmy powinny przyjąć różne strategie w celu zmniejszenia poziomu hałasu w miejscu pracy, takie jak:
- Udoskonalenia konstrukcyjne: Należy wziąć pod uwagę kontrolę hałasu podczas projektowania i rozmieszczania sprzętu, stosując wysokiej jakości materiały i rozwiązania konstrukcyjne w celu zmniejszenia generowania hałasu.
- Zamontuj izolację akustyczną: Zastosowanie obudów dźwiękochłonnych i materiałów pochłaniających dźwięk może znacznie zredukować hałas generowany przez Twój sprzęt.
- Optymalizacja procesów operacyjnych: Dostosuj parametry cięcia i procedury operacyjne, np. zmniejsz prędkość lub moc cięcia, aby ograniczyć wibracje i hałas.
- Środki ochrony osobistej: należy zapewnić pracownikom odpowiednie nauszniki i zatyczki do uszu, aby chronić ich przed hałasem o dużym natężeniu.
- Regularne szkolenia i edukacja: Zapewnij pracownikom szkolenia z zakresu ochrony przed hałasem, aby zwiększyć ich wiedzę na temat zagrożeń związanych z hałasem i świadomość konieczności samoobrony.
Wdrażając powyższe środki, przedsiębiorstwa mogą nie tylko spełnić wymagania przepisów dotyczących bezpieczeństwa i higieny pracy, ale także stworzyć bezpieczniejsze i wygodniejsze środowisko pracy. To nie tylko chroni zdrowie pracowników, ale także poprawia zadowolenie pracowników z pracy i wydajność produkcji, ostatecznie osiągając sytuację korzystną dla obu stron, zarówno dla przedsiębiorstw, jak i pracowników.
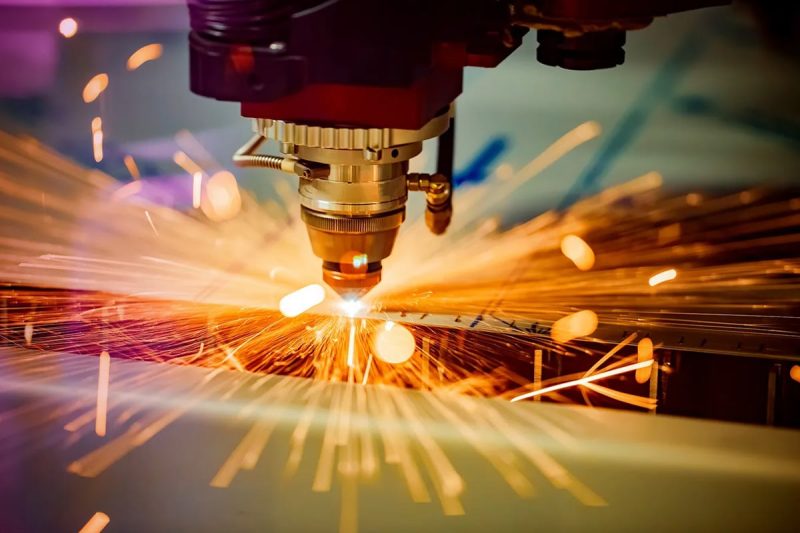
Technologia redukcji szumów
Technologia redukcji hałasu odgrywa kluczową rolę w działaniu maszyn do cięcia laserowego. Poniżej przedstawiono szczegółową analizę kilku powszechnych technologii redukcji hałasu:
Obudowa przeciwhałasowa
Obudowa dźwiękoszczelna to konstrukcja stosowana do otoczenia źródła hałasu i skutecznego blokowania rozprzestrzeniania się fal dźwiękowych. Zazwyczaj hałas generowany przez części robocze maszyny do cięcia laserowego (takie jak silniki, wentylatory itp.) można zmniejszyć za pomocą obudowy dźwiękoszczelnej. Wysokiej jakości obudowy dźwiękoszczelne zazwyczaj wykorzystują wiele warstw materiałów, z solidną metalową warstwą zewnętrzną i materiałami pochłaniającymi dźwięk na warstwie wewnętrznej, aby uzyskać dobrą izolację akustyczną. Projekt obudowy dźwiękoszczelnej musi w pełni uwzględniać wentylację i emisję ciepła, aby zapobiec uszkodzeniu sprzętu z powodu przegrzania.
Skuteczność dźwiękoszczelnej osłony zależy również od jej uszczelnienia. Dobre uszczelnienie może zapobiec wyciekaniu fal dźwiękowych. Ponadto, rozsądna konstrukcja może również ułatwić operatorom wykonywanie codziennych czynności konserwacyjnych i napraw bez demontażu osłony, biorąc pod uwagę zarówno efekt redukcji hałasu, jak i łatwość obsługi.
System izolacji drgań
System izolacji wibracji głównie redukuje hałas poprzez redukcję przenoszenia drgań sprzętu. Gdy maszyna do cięcia laserowego jest uruchomiona, z powodu ruchu części mechanicznych, mogą być generowane silne drgania. Drgania te będą przenoszone przez podstawę sprzętu i podłoże, co spowoduje wzrost hałasu otoczenia. Poprzez zainstalowanie podkładek izolujących drgania lub podpór sprężynowych na spodzie sprzętu, przenoszenie drgań może być skutecznie zmniejszone.
Materiały izolujące wibracje mają zazwyczaj wysoką elastyczność i właściwości pochłaniania wstrząsów, które mogą pochłaniać i tłumić energię wibracji. Dobrze zaprojektowany system izolacji wibracji może również poprawić stabilność sprzętu, wydłużyć jego żywotność i obniżyć koszty konserwacji. Ponadto podczas instalacji sprzętu wybór odpowiedniego miejsca instalacji i fundamentu może również poprawić efekt izolacji wibracji.
Materiały pochłaniające dźwięk
Zastosowanie materiałów pochłaniających dźwięk to kolejna skuteczna technologia redukcji hałasu. Dzięki porowatej strukturze materiały pochłaniające dźwięk mogą pochłaniać energię fal dźwiękowych i redukować odbity i przenoszony hałas. Typowe materiały pochłaniające dźwięk to wełna mineralna, płyta pilśniowa poliestrowa i pianka poliuretanowa. Materiały te można nakładać na ściany, podłogi lub sufity wokół maszyny do cięcia laserowego, aby stworzyć środowisko akustyczne, które redukuje hałas.
Wybierając materiały pochłaniające dźwięk, należy je rozsądnie dopasować do ich charakterystyki odpowiedzi częstotliwościowej i charakterystyki widmowej źródła hałasu. Różne materiały pochłaniające dźwięk mają różny wpływ na pochłanianie hałasu o różnych częstotliwościach. Dlatego bardzo ważne jest, aby wybierać i rozmieszczać materiały zgodnie z rzeczywistą sytuacją.
Regularna konserwacja i smarowanie
Regularna konserwacja i smarowanie są ważnymi elementami utrzymania normalnej pracy sprzętu i są również kluczowe dla zmniejszenia poziomu hałasu. Zużycie i tarcie ruchomych części może powodować dodatkowy hałas, więc regularna kontrola i konserwacja ruchomych części, takich jak prowadnice, przekładnie i silniki, może skutecznie zmniejszyć hałas roboczy sprzętu.
Stosowanie właściwego środka smarnego może zmniejszyć tarcie i obniżyć poziom hałasu. Ponadto utrzymywanie części mechanicznych w czystości i zapobieganie gromadzeniu się kurzu i zanieczyszczeń może również poprawić wydajność pracy sprzętu i zmniejszyć niepotrzebny hałas. Regularna konserwacja może również wykryć potencjalne problemy na wczesnym etapie i uniknąć wysokiego poziomu hałasu spowodowanego awarią sprzętu.
Podsumowując, technologie redukcji hałasu obejmują obudowy dźwiękoszczelne, systemy izolacji wibracji, materiały pochłaniające dźwięk, regularną konserwację i smarowanie itp. Dzięki połączeniu tych technologii można nie tylko skutecznie zmniejszyć poziom hałasu maszyny do cięcia laserowego, ale także poprawić wydajność i żywotność sprzętu, tworząc bezpieczniejsze i wygodniejsze środowisko pracy dla operatorów.
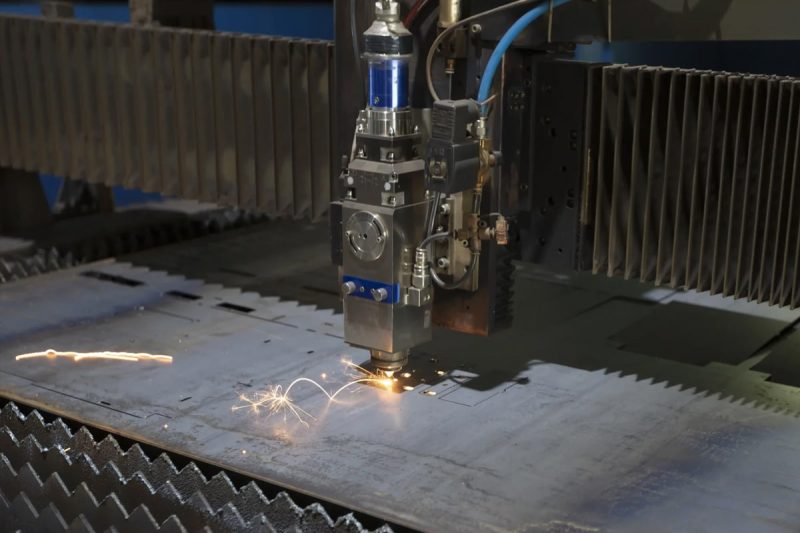
Podsumować
Problem hałasu maszyn do cięcia laserowego nie może być ignorowany. Hałas nie tylko wpływa na środowisko pracy operatorów, ale może również stanowić potencjalne zagrożenie dla ich zdrowia. Zrozumienie źródeł hałasu i czynników wpływających na niego może pomóc firmom opracować skuteczne strategie zarządzania. Wdrażając rozsądną technologię redukcji hałasu oraz środki bezpieczeństwa i higieny pracy, można znacznie poprawić środowisko pracy, a także zwiększyć wydajność i bezpieczeństwo pracy.
Dzięki utrzymaniu dobrego działania sprzętu i połączeniu nowoczesnych technologii redukcji hałasu, takich jak obudowy dźwiękochłonne, systemy izolacji wibracyjnej i materiały pochłaniające dźwięk, firmy mogą skutecznie obniżyć poziom hałasu i stworzyć cichsze i bezpieczniejsze miejsce pracy. Jednocześnie regularna konserwacja i smarowanie sprzętu może również pomóc w zmniejszeniu hałasu i poprawie ogólnej wydajności sprzętu.
Jeśli masz jakiekolwiek pytania lub potrzeby dotyczące kontroli hałasu maszyny do cięcia laserowego, skontaktuj się z AccTek. Zapewnimy Ci dostosowane rozwiązania, aby zapewnić wydajną pracę i bezpieczne użytkowanie sprzętu oraz stworzyć bardziej idealne środowisko pracy dla Twojej firmy.
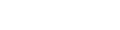
Informacje kontaktowe
- [email protected]
- [email protected]
- +86-19963414011
- Nr 3 Strefa A, strefa przemysłowa Lunzhen, miasto Yucheng, prowincja Shandong.
Uzyskaj rozwiązania laserowe