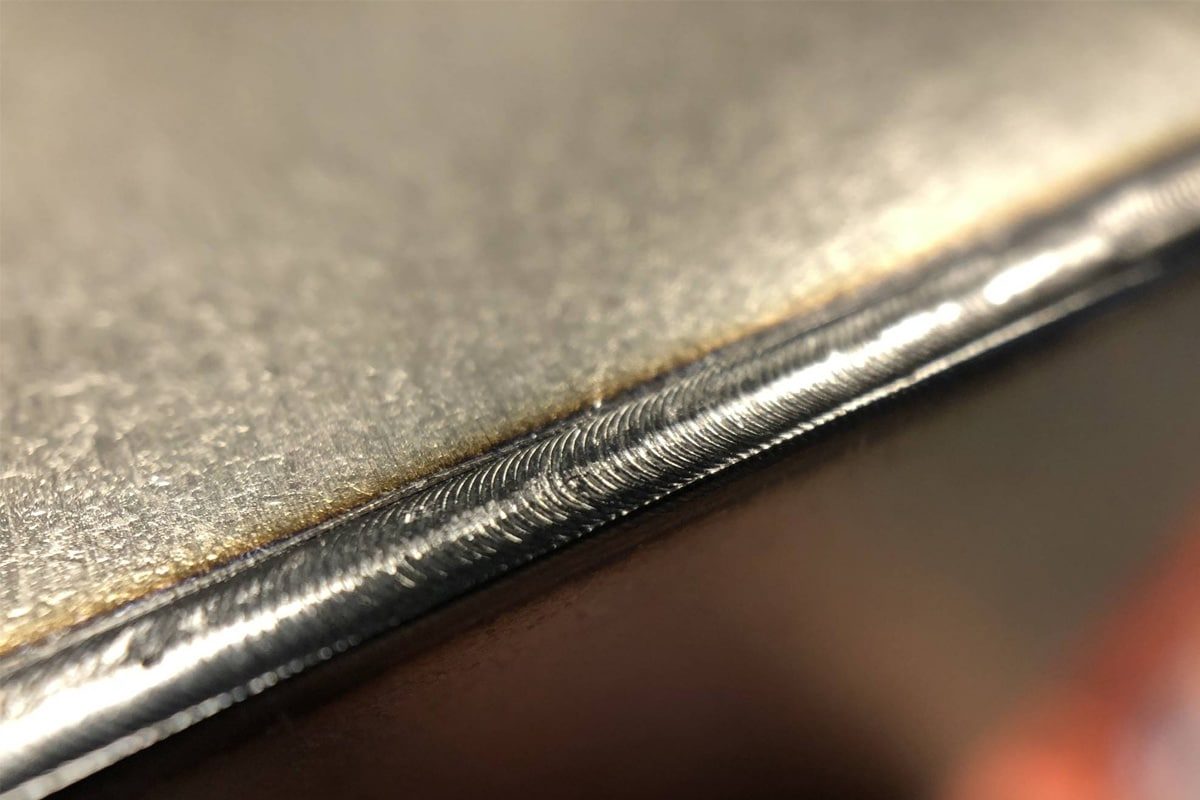
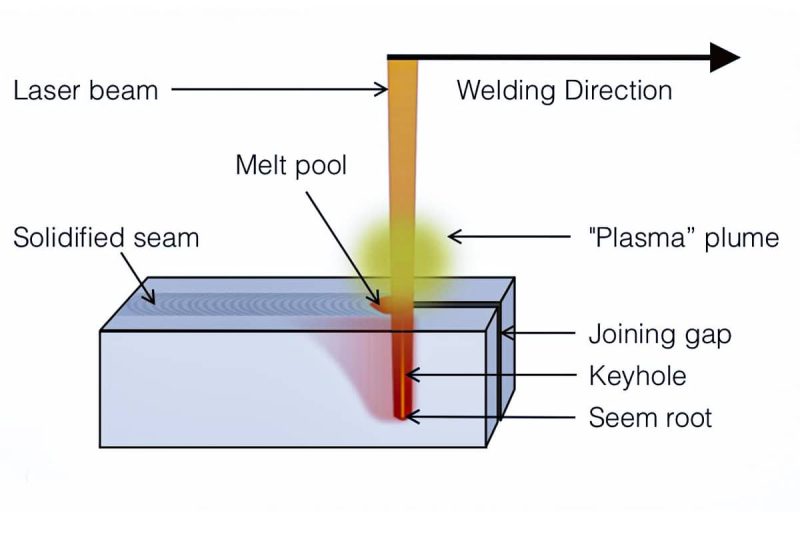
Zrozumienie spawania laserowego
Podstawy spawania laserowego
Typ spawania laserowego
- Spawanie laserowe falą ciągłą: odpowiednie do długotrwałego spawania o wysokiej intensywności, szeroko stosowane do łączenia i uszczelniania grubych płyt metalowych.
- Spawanie laserowe impulsowe: nagrzewanie materiału za pomocą krótkich impulsów o dużej energii, bardziej odpowiednie do spawania cienkich płyt lub mikrokomponentów, charakteryzujące się większą dokładnością sterowania.
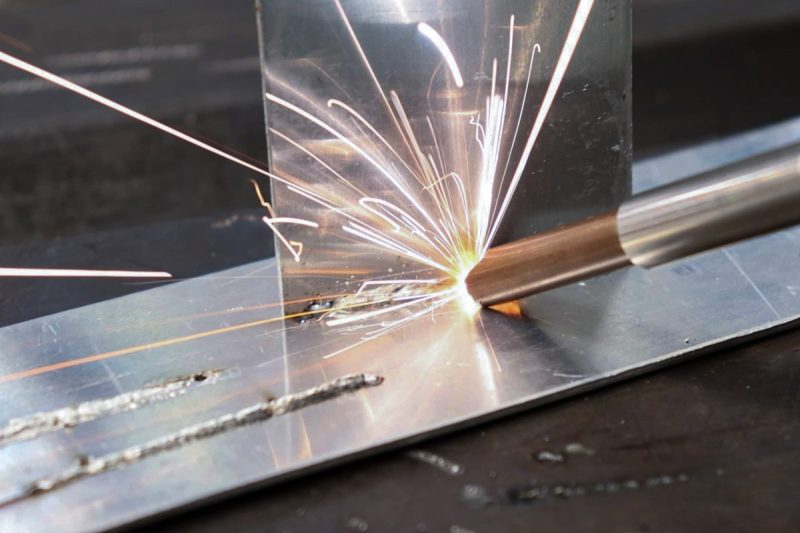
Czynniki wpływające na szerokość spoiny
Parametry lasera
- Moc lasera: Moc lasera jest jednym z najważniejszych parametrów wpływających na wyniki spawania. Im większa moc lasera, tym więcej ciepła jest generowane, a objętość strefy wpływu ciepła i jeziorka stopionego materiału również wzrasta, co zwiększa szerokość spoiny. Odwrotnie, jeśli moc jest zbyt niska, nie może zapewnić wystarczającej energii do stopienia materiału, a spoina może być niewystarczająca, co skutkuje wąskim spoiwem lub niepełnym spawaniem. Dlatego moc lasera musi być rozsądnie dobrana w zależności od grubości, rodzaju i prędkości spawania materiału, aby uzyskać optymalną szerokość spoiny.
- Prędkość spawania: Prędkość spawania ma istotny wpływ na wprowadzane ciepło. Gdy prędkość spawania jest niska, laser pozostaje w obszarze spawania przez dłuższy czas, co skutkuje większym transferem ciepła do materiału bazowego, tworząc większe jeziorko stopu i strefę wpływu ciepła, zwiększając tym samym szerokość spoiny. Z drugiej strony, zbyt duża prędkość spawania zmniejszy wprowadzane ciepło, co spowoduje niepełne spawanie, zbyt wąskie spoiny i potencjalnie słabe spoiny. Dlatego też rozsądna kontrola prędkości spawania jest kluczem do zapewnienia odpowiedniej szerokości spoiny.
- Długość fali: Długość fali lasera określa, w jaki sposób laser oddziałuje z materiałem. Lasery krótkofalowe (takie jak te emitowane przez generatory laserów światłowodowych) mogą być lepiej absorbowane przez materiały metalowe, ponieważ mają wyższą koncentrację energii i mogą dostarczać więcej energii na mniejszym obszarze, co poprawia wydajność spawania i sprawia, że spoina jest węższa. Mówiąc relatywnie, lasery długofalowe (takie jak te emitowane przez tuby laserowe CO2) mają słabą absorpcję materiałów metalowych, a rozkład energii podczas spawania jest stosunkowo szeroki, co łatwo prowadzi do większej szerokości spoiny. Dlatego lasery krótkofalowe są bardziej odpowiednie do spawania o wysokiej precyzji.
- Czas trwania impulsu: Spawanie laserem pulsacyjnym ma wyjątkową zaletę optymalizacji spawania poprzez regulację czasu trwania impulsu. Im krótszy czas trwania impulsu, tym krótszy czas wprowadzania ciepła przez laser, co pomaga zmniejszyć rozszerzanie się strefy wpływu ciepła i utworzyć mniejszą spoinę. Dłuższe czasy trwania impulsu skutkują większym wprowadzaniem ciepła i szerszą spoiną. Dzięki technologii kształtowania impulsu szerokość impulsu i interwał lasera można precyzyjnie kontrolować, aby zoptymalizować rozkład ciepła i morfologię spoiny podczas spawania.
- Jakość wiązki: Jakość i kontrola skupienia wiązki laserowej są kluczowe dla dokładności spawania. Lasery o lepszej jakości wiązki mają mniejsze rozmiary skupienia i bardziej skoncentrowaną energię, co pozwala na uzyskanie spawania o wyższej precyzji. Wyższa jakość wiązki pomaga zmniejszyć dyfuzję ciepła, dzięki czemu ciepło jest bardziej skoncentrowane w obszarze spawania, a szerokość spoiny staje się mniejsza. Jeśli jakość wiązki jest słaba, spowoduje to nierównomierne rozłożenie energii lasera, zwiększając tym samym szerokość spoiny.
Właściwości materiału
- Współczynnik absorpcji: Współczynnik absorpcji materiału przez laser ma bezpośredni wpływ na efekt spawania. Współczynnik absorpcji materiałów metalowych jest zwykle wysoki, zwłaszcza gdy laser krótkofalowy jest dopasowany do metalu, współczynnik absorpcji ulega dalszej poprawie. W procesie spawania laserowego wyższy współczynnik absorpcji oznacza, że energia lasera może być skutecznie przekształcona w energię cieplną, co skutkuje mniejszym spoiwem. Odwrotnie, jeśli współczynnik absorpcji materiału jest niski, efektywny współczynnik wykorzystania energii lasera jest słaby, co może spowodować, że spoina będzie zbyt szeroka lub niekompletna.
- Przewodność cieplna: Przewodność cieplna materiału wpływa na szybkość dyfuzji ciepła w podłożu. Materiały o wyższej przewodności cieplnej (takie jak miedź i aluminium) szybko rozproszy ciepło, co spowoduje nadmierne rozproszenie ciepła w obszarze spawania i szersze spoiny. Natomiast materiały o niższej przewodności cieplnej (takie jak Stal nierdzewna) może zatrzymać więcej ciepła skoncentrowanego w obszarze spawania, tworząc węższą spoinę. Dlatego podczas spawania materiałów o różnej przewodności cieplnej konieczne jest dostosowanie parametrów spawania zgodnie z ich właściwościami cieplnymi, aby zapewnić odpowiednią szerokość spoiny.
- Odbicie: Materiały o wysokim współczynniku odbicia (takie jak aluminium i miedź) będą generować większe odbicie lasera i zmniejszać wydajność absorpcji energii lasera, co wpływa na jakość spawania i może powodować zwiększenie szerokości spoiny. Aby przezwyciężyć ten problem, możesz wybrać typ lasera odpowiedni do materiałów silnie odblaskowych (takich jak użycie lasera o krótkiej długości fali) lub zwiększyć moc lasera, aby zrekompensować utratę odbicia. Ponadto użycie skupionej wiązki i odpowiedniej długości fali lasera może również pomóc zwiększyć współczynnik absorpcji lasera przez materiały odblaskowe.
Środowisko spawalnicze
- Gaz osłonowy: Gaz osłonowy odgrywa ważną rolę w spawaniu laserowym. Nie tylko zapobiega utlenianiu i zanieczyszczeniom podczas spawania, ale także wpływa na przewodzenie ciepła i szerokość spoiny poprzez kontrolowanie przepływu gazu. Na przykład argon i azot są często używane jako gazy osłonowe w spawaniu laserowym. Mogą one skutecznie zmniejszyć zasięg strefy wpływu ciepła i uniknąć generowania nadmiernych spoin. Wybór i kontrola gazu osłonowego muszą być dostosowane do konkretnych materiałów i wymagań spawalniczych.
- Warunki środowiskowe: Czynniki środowiskowe, takie jak temperatura i wilgotność, również mają pewien wpływ na efekt spawania laserowego. W środowiskach o niskiej temperaturze przewodnictwo cieplne materiałów metalowych może się zmieniać, co wpływa na zarządzanie termiczne podczas spawania. Ponadto środowiska o wysokiej wilgotności mogą powodować rozpraszanie energii lasera i wpływać na jakość spawania. Stabilne warunki środowiskowe pomagają utrzymać stabilność wiązki laserowej i zapewniają spójność szerokości spoiny podczas spawania.
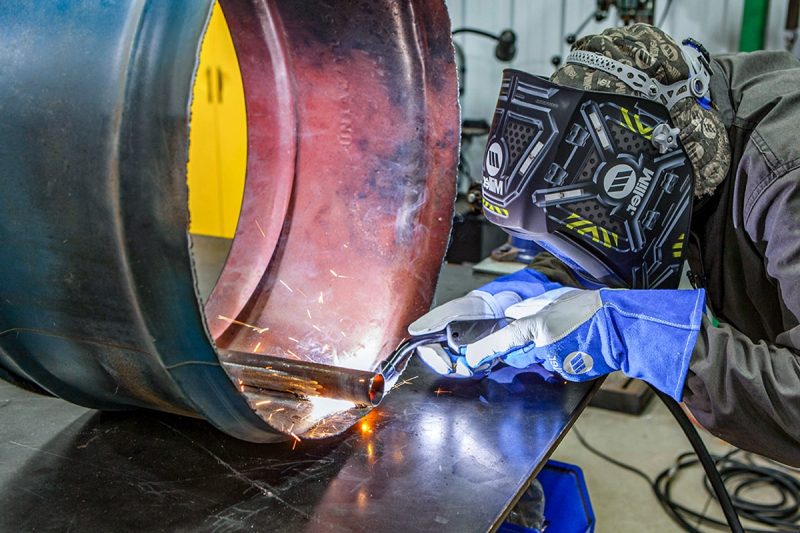
Technologia umożliwiająca uzyskanie minimalnej szerokości spoiny
Wybór typu lasera
- Generator lasera światłowodowego: Generator lasera światłowodowego jest jednym z najczęściej używanych źródeł laserowych w spawaniu laserowym. Posiada dużą moc, wysoką jakość wiązki i doskonałą zdolność ogniskowania. Wiązka generatora lasera światłowodowego może być precyzyjnie skupiona na bardzo małym obszarze, co zmniejsza szerokość spoiny i umożliwia wydajną obróbkę cienkich płyt. Generatory lasera światłowodowego są bardzo odpowiednie do zadań spawalniczych wymagających wysokiej precyzji i szybkości oraz mogą osiągać wysokiej jakości małe spoiny i zmniejszać rozszerzanie się strefy wpływu ciepła (HAZ) materiału.
- Rura laserowa CO2: Rura laserowa CO2 to kolejne źródło lasera powszechnie stosowane do spawania metali. Chociaż jakość wiązki rur laserowych CO2 nie jest na ogół tak dobra, jak w przypadku generatorów laserów światłowodowych, może ona zapewnić większą moc i głębszą głębokość penetracji, co jest odpowiednie do spawania grubszych materiałów. Chociaż nie jest tak dokładna jak laser światłowodowy, stosunkowo małe szerokości spoin można uzyskać dzięki rozsądnej regulacji mocy i zoptymalizowanej prędkości spawania.
Wybór długości fali lasera
Optymalizacja parametrów lasera
- Regulacja mocy lasera: Moc lasera jest głównym czynnikiem wpływającym na ciepło doprowadzone podczas spawania. Nadmierna moc spowoduje rozprzestrzenianie się nadmiernego ciepła na otaczający obszar, poszerzając tym samym spoinę, a nawet powodując wady spawalnicze. Odpowiednie zmniejszenie mocy może pomóc zmniejszyć ciepło doprowadzone i zawęzić szerokość spoiny, szczególnie podczas spawania cienkich płyt. Jednak zbyt niska moc może skutkować niewystarczającym spawaniem. Dlatego też rozsądne dostosowanie mocy lasera do właściwości materiału, prędkości spawania i wymagań spawalniczych może zapewnić precyzyjne spawanie i skutecznie kontrolować szerokość spoiny.
- Technologia kształtowania impulsów: Technologia spawania laserowego impulsowego umożliwia dokładną kontrolę ciepła wprowadzanego podczas spawania poprzez regulację częstotliwości, czasu trwania i energii impulsu laserowego. Im krótsza szerokość impulsu, tym krótszy czas wprowadzania ciepła i mniejsza akumulacja ciepła w obszarze spawania, co sprawia, że spoina jest węższa. Ponadto, poprzez regulację częstotliwości i energii impulsów, można kontrolować prędkość spawania i morfologię jeziorka stopionego, co z kolei wpływa na szerokość spoiny. Dzięki technologii kształtowania impulsów, szczególnie w mikrospawaniu, rozkład ciepła każdego impulsu można dokładnie kontrolować, aby skutecznie osiągnąć minimalną szerokość spoiny.
- Kontrola ogniskowania wiązki: Dokładność i szerokość spoiny spawania laserowego są ściśle powiązane z położeniem ogniska wiązki. Im mniejsze ogniskowanie wiązki laserowej, tym większa gęstość energii, która może być skoncentrowana w obszarze spawania, co pozwala uzyskać wąski i cienki spoin. Dlatego kontrola ogniskowania lasera jest bardzo ważna. Poprzez regulację położenia ogniskowania energia wiązki laserowej może być bardziej skoncentrowana w obszarze spawania, co zapobiega dyfuzji ciepła do otaczającego obszaru, a tym samym zmniejsza szerokość spoiny.
Przygotowanie materiału
- Czystość powierzchni: Czystość powierzchni materiału spawalniczego ma bezpośredni wpływ na efekt spawania laserowego. Tlenki, olej, rdza i inne zanieczyszczenia na powierzchni będą miały wpływ na szybkość absorpcji lasera, co spowoduje niezdolność do skutecznego skoncentrowania ciepła w obszarze spawania, co wpłynie na jakość spawania i zwiększy szerokość spoiny. Zapewnienie, że powierzchnia spawania jest czysta i wolna od zanieczyszczeń, jest warunkiem wstępnym optymalizacji jakości spawania. Zanieczyszczenia powierzchni można zazwyczaj usunąć poprzez czyszczenie chemiczne, czyszczenie mechaniczne lub czyszczenie laserowe.
- Powłoka powierzchniowa: W niektórych przypadkach, szczególnie w przypadku materiałów trudnych do spawania, powłoka powierzchniowa może znacznie poprawić wydajność absorpcji lasera. Materiały powłokowe (takie jak miedziowanie, cynkowanie itp.) mogą poprawić interakcję między laserem a materiałem i zwiększyć akumulację ciepła w obszarze spawania, pomagając w ten sposób dokładnie kontrolować szerokość spoiny podczas procesu spawania. Ponadto specjalne powłoki mogą również poprawić stabilność jeziorka stopionego podczas spawania i zmniejszyć wady podczas spawania.
Zaawansowana technologia spawania
- Hybrydowe spawanie laserowe: Hybrydowa technologia spawania laserowego łączy zalety laserowych i tradycyjnych metod spawania (takich jak spawanie TIG lub spawanie MIG) i poprawia wprowadzanie ciepła i dokładność spawania poprzez łączenie zalet różnych źródeł ciepła. Połączenie laserowych i tradycyjnych metod spawania może skutecznie zmniejszyć szerokość spoiny, szczególnie podczas spawania grubszych materiałów. Hybrydowa technologia spawania laserowego może zapewnić większą stabilność jeziorka stopionego materiału i mniejsze strefy wpływu ciepła, dzięki czemu uzyskuje się bardziej wyrafinowane efekty spawania.
- Technologia mikrospawania: Mikrospawanie laserowe to technologia spawania o wysokiej precyzji do obróbki ultramałych spoin, szczególnie odpowiednia do łączenia małych części. Technologia mikrospawania wykorzystuje precyzyjnie kontrolowane impulsy laserowe w celu uzyskania wydajnego transferu energii w bardzo małym obszarze spawania, zapewniając tworzenie bardzo wąskich spoin. Mikrospawanie jest powszechnie stosowane w takich gałęziach przemysłu, jak elektronika, instrumenty precyzyjne i urządzenia medyczne, i może osiągnąć wysoką dokładność spawania i zminimalizować wpływ termiczny obszaru spawania.
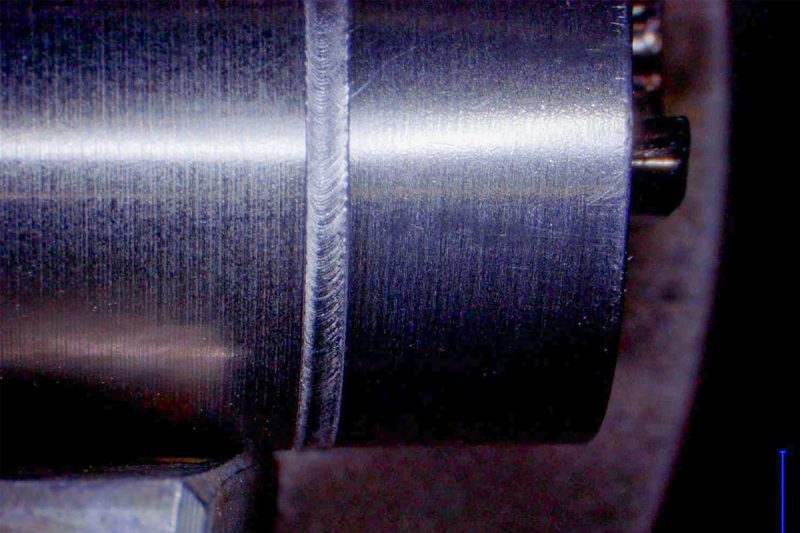
Wyzwania i rozwiązania
Zarządzanie temperaturą
Wyzwanie
Rozwiązanie
- Użyj dodatkowego chłodzenia gazem: Używanie odpowiedniego gazu osłonowego lub gazu pomocniczego (takiego jak argon, azot lub tlen) może nie tylko zapobiec utlenianiu obszaru spawania, ale także skutecznie usunąć nadmiar ciepła wytwarzanego podczas spawania, zmniejszając w ten sposób rozszerzanie się strefy wpływu ciepła. Przepływ i ciśnienie gazu pomocniczego muszą być zoptymalizowane w zależności od materiału spawalniczego, prędkości spawania i mocy lasera, aby zapewnić najlepszy efekt chłodzenia.
- Optymalizacja prędkości spawania: Prawidłowe zwiększenie prędkości spawania może zmniejszyć ilość ciepła wprowadzanego na jednostkę czasu i skrócić czas nagrzewania materiału, skutecznie zapobiegając przegrzaniu obszaru spawania. Wyższe prędkości spawania mogą powodować szybkie rozprzestrzenianie się ciepła na większym obszarze, zmniejszać lokalny wzrost temperatury, a tym samym kontrolować szerokość spoiny i strefę wpływu ciepła.
- Regulacja źródła ciepła: Poprzez regulację mocy lasera lub użycie lasera pulsacyjnego, ciepło dopływowe może być precyzyjnie kontrolowane podczas procesu spawania. Zwłaszcza w spawaniu impulsowym, krótkie impulsy i wyższe częstotliwości impulsów mogą zapewnić, że ciepło jest szybko skupione i rozprowadzone w obszarze spawania, aby uniknąć dyfuzji ciepła.
Odblaskowość materiału
Wyzwanie
Rozwiązanie
- Użyj laserów krótkofalowych: Lasery krótkofalowe (takie jak te produkowane przez generatory laserów światłowodowych) mają wyższy współczynnik absorpcji dla materiałów silnie odbijających. Lasery krótkofalowe mogą być lepiej absorbowane przez materiały, zmniejszać odbicia i zapewniać, że w procesie spawania zostanie efektywniej wykorzystana większa ilość energii lasera, co poprawia wydajność spawania i zmniejsza szerokość spoiny. W porównaniu z laserami CO2 o długiej długości fali, generatory laserów światłowodowych są bardziej odpowiednie do obróbki materiałów o wyższym współczynniku odbicia.
- Regulacja mocy lasera: W przypadku materiałów o wysokiej refleksyjności odpowiednie zmniejszenie mocy lasera może zapobiec nadmiernemu odbiciu energii. Niższe ustawienia mocy pomagają zmniejszyć odbicia i uniknąć marnotrawstwa energii, skutecznie kontrolując szerokość spoiny i optymalizując jakość spawania.
- Użyj materiałów powlekanych: Niektóre wysoce odblaskowe materiały metalowe, takie jak aluminium i miedź, mogą wykorzystywać technologię powlekania, taką jak powlekanie aluminium, miedziowanie i inne metody obróbki powierzchni. Te powłoki mają niższy współczynnik odbicia, co może poprawić wydajność absorpcji lasera i zmniejszyć interferencję odbicia w procesie spawania, tym samym lepiej kontrolując szerokość spoiny.
Stabilność procesu
Wyzwanie
Rozwiązanie
- Zaawansowany system sterowania laserem: Dzięki zastosowaniu zaawansowanych systemów sterowania laserem, kluczowe parametry, takie jak moc lasera, prędkość spawania, ogniskowanie wiązki itp., mogą być monitorowane i regulowane w czasie rzeczywistym, aby zapewnić spójność parametrów lasera podczas każdego procesu spawania. Nowoczesne systemy spawania laserowego są zazwyczaj wyposażone w czujniki o wysokiej precyzji i funkcje automatycznej regulacji, które mogą wykrywać temperaturę obszaru spawania, morfologię jeziorka stopionego i położenie wiązki w czasie rzeczywistym oraz automatycznie regulować moc lasera, aby utrzymać stabilność procesu spawania.
- Informacje zwrotne w czasie rzeczywistym i sterowanie w pętli zamkniętej: Zastosowanie informacji zwrotnej w czasie rzeczywistym i technologii sterowania w pętli zamkniętej umożliwia dostosowywanie parametrów w czasie rzeczywistym podczas procesu spawania, aby poradzić sobie ze zmianami właściwości materiału i środowiska spawania. Na przykład czujniki mogą monitorować rozmiar, kształt i temperaturę jeziorka stopionego metalu, a system może automatycznie dostosowywać moc lasera i prędkość spawania, aby zachować spójność jakości spawania. Technologia ta może znacznie poprawić niezawodność procesu spawania i uniknąć problemów ze spawaniem spowodowanych wahaniami procesu.
- Optymalizacja ścieżki spawania: Podczas procesu spawania optymalizacja planowania ścieżki lasera jest kolejnym ważnym sposobem na poprawę stabilności procesu. Poprzez dokładne kontrolowanie ścieżki spawania i sekwencji spawania można zmniejszyć odkształcenia materiału i zmiany w strefie wpływu ciepła, zapewniając spójny rozkład temperatury podczas każdego procesu spawania, a tym samym osiągając stabilne wyniki spawania.
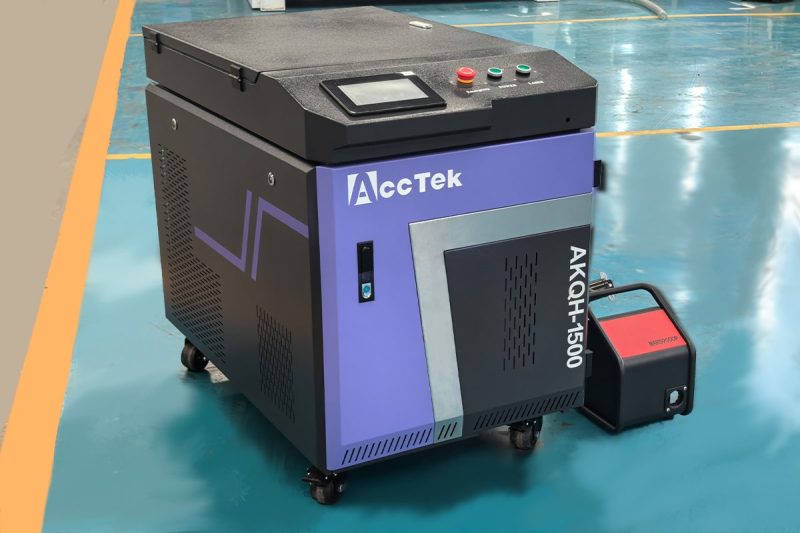
Podsumować
W tym procesie nasz spawarki laserowe stali się liderami w branży dzięki swojej doskonałej technologii i innowacyjnemu projektowi. Maszyny do spawania laserowego naszej firmy wykorzystują najnowszą technologię lasera światłowodowego, która umożliwia wydajne spawanie, zapewniając jednocześnie dokładną kontrolę temperatury podczas procesu spawania, a tym samym skutecznie kontrolując szerokość spoiny i zmniejszając strefę wpływu ciepła. Nasz sprzęt spawalniczy nie tylko ma możliwość precyzyjnej regulacji wiązki laserowej, ale jest również wyposażony w zaawansowany system kontroli temperatury, który może automatycznie regulować parametry podczas procesu spawania, optymalizując w ten sposób efekt spawania i zapewniając stabilną i spójną jakość w każdym punkcie spawania.
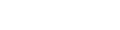
- [email protected]
- [email protected]
- +86-19963414011
- Nr 3 Strefa A, strefa przemysłowa Lunzhen, miasto Yucheng, prowincja Shandong.