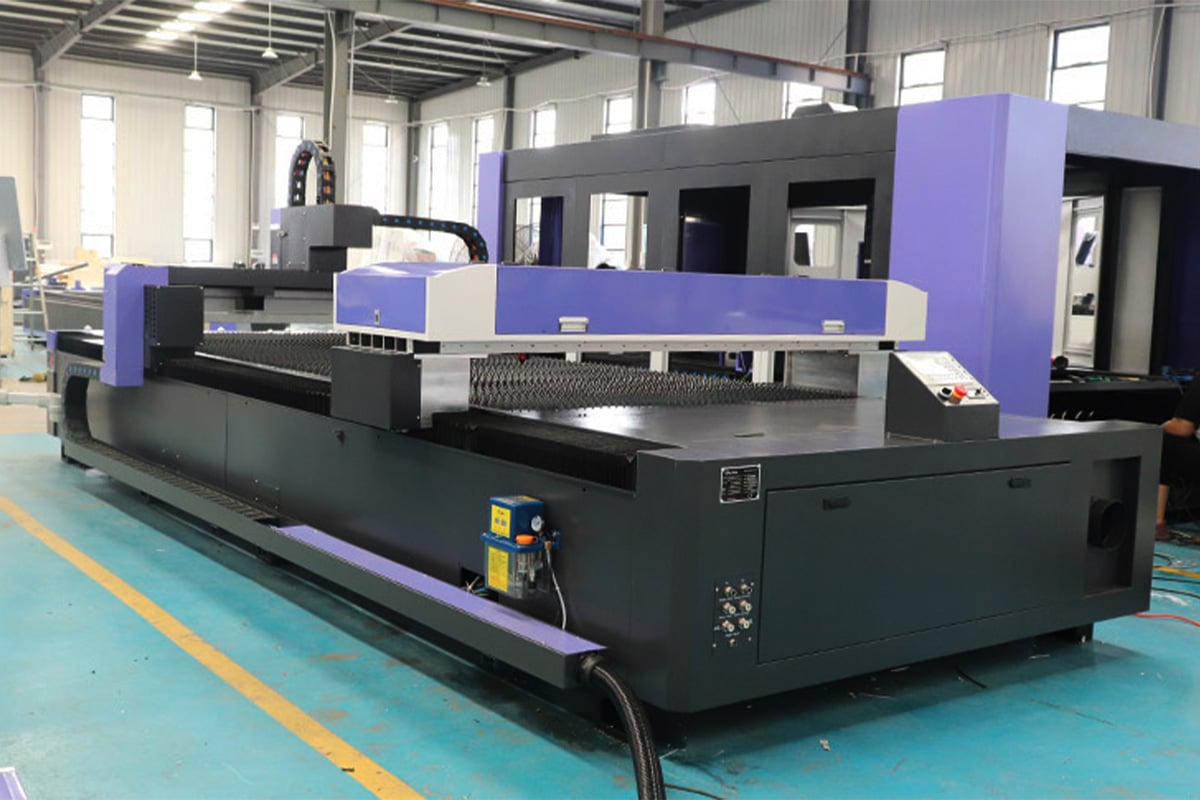
How to Achieve the Minimum Incision Width in CO2 Laser Cutting?
CO2 laser cutting technology has been widely used in the cutting process of various materials such as metal processing, plastic, wood, cloth, etc. due to its advantages of high precision, high speed, and non-contact processing. Kerf Width refers to the width of the incision formed by the laser beam during the cutting process. This indicator directly affects the precision and quality of the cutting. A smaller incision width can achieve a more refined processing effect, improve product precision, reduce material waste, and reduce production costs. Therefore, it is an important criterion for measuring laser cutting quality.
The control of the incision width is not only to improve product quality but also closely related to the utilization rate of materials, the convenience of subsequent processing, and the overall production efficiency. For manufacturers, the optimization of the incision width is directly related to the control of production costs. Especially in large-scale production, too large an incision width may lead to material waste and affect the smooth progress of subsequent processes. Therefore, precise control of the incision width is an important link to achieve efficient and low-cost production.
Spis treści
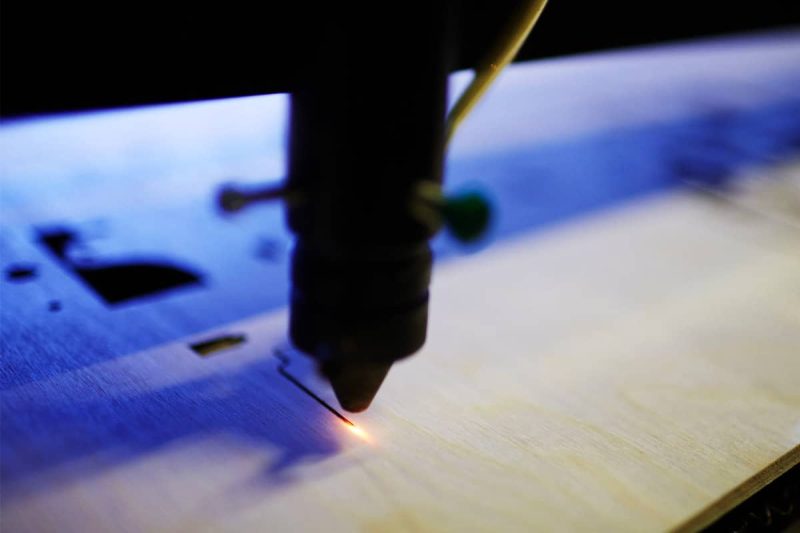
Key factors affecting CO2 laser cutting kerf width
The cutting effect of CO2 laser cutting technology is affected by many factors, and the kerf width is one of the most critical indicators. By reasonably adjusting and optimizing these factors, manufacturers can improve production efficiency and reduce material loss while ensuring high precision. The following are several key factors affecting the kerf width and their optimization strategies:
Laser focus size: The size of the laser focus directly affects the diameter of the spot, and the smaller the spot, the narrower the incision width. The more precise the focus, the higher the concentration of the laser beam energy, thereby improving the cutting accuracy. To optimize the incision width, it is important to choose the right focal length lens. Generally, a short focal length lens can provide a smaller focus diameter, thereby achieving a more refined cutting effect. For different materials and cutting requirements, the focus size can be optimized by adjusting the focal length to ensure the best cutting effect.
Laser power: The laser power directly determines the thermal energy intensity of the laser beam, which affects the melting, evaporation, and cutting effects during the cutting process. If the laser power is too high, it is easy to cause the incision to be too wide or even burn through the material; if the power is too low, it may not be able to completely penetrate the material, resulting in incomplete cutting. It is crucial to adjust the laser power to the optimal value according to the thickness and properties of different materials. For example, for thicker materials, the power needs to be appropriately increased, while for thin materials, the power can be reduced to avoid the incision being too wide. By accurately adjusting the power, manufacturers can achieve precise and efficient cutting.
Cutting speed: Cutting speed also plays an important role in laser cutting. Properly increasing the cutting speed can not only reduce the heat-affected zone and reduce the impact of molten material on the edge of the cut but also improve production efficiency. However, if the cutting speed is too fast, the laser beam may not have enough time to fully penetrate the material, resulting in incomplete cutting; conversely, too slow speed may cause the cut to be too wide and produce excess melt. To optimize the cutting effect, the cutting speed needs to be accurately adjusted according to the type and thickness of the material to ensure that the cut width is minimized.
Auxiliary gas type and pressure: Auxiliary gas plays a vital role in laser cutting. Commonly used auxiliary gases are oxygen, nitrogen, and air. Oxygen can enhance the combustion reaction during the cutting process and is suitable for cutting materials such as iron and steel; nitrogen can reduce oxidation and is suitable for materials such as stainless steel; air is widely used in a variety of materials due to its economy. In addition to the gas type, the gas pressure also affects the cutting quality. Appropriate gas pressure can help remove the melt and prevent it from adhering to the edge of the incision, thereby reducing the incision width. Lower gas pressure may result in the inability to effectively remove the melt and increase the incision width, so the appropriate gas pressure and type must be selected to optimize the cutting effect.
Material properties: The properties of different materials can significantly affect the accuracy of laser cutting. The material’s properties such as absorption rate, thermal conductivity, and melting point directly affect the transmission efficiency of the laser beam and the cutting quality. Highly reflective materials (such as aluminum, copper, etc.) tend to cause the laser beam to reflect and scatter, thereby reducing the cutting effect. For these materials, it is necessary to optimize the laser parameters, especially to increase the power density, to ensure that the laser can effectively penetrate the material. On the contrary, low-reflective materials such as steel are easier to cut. When cutting different materials, manufacturers should adjust the cutting parameters according to the material characteristics to ensure the best cutting quality and the smallest incision width.
Cutting path optimization: Optimization of the cutting path is also crucial to controlling the incision width. A smooth cutting path can reduce the error of the laser beam when the direction changes and avoid irregular incisions. Especially when cutting complex shapes, a reasonable design of the path and reducing turns and emergency stops can significantly improve cutting accuracy. In addition, optimizing the feed and retract strategies can also help reduce material ablation and avoid incision deformation caused by excessive heating. When designing the path, quick turns and uneven routes should be avoided as much as possible to ensure that the energy is evenly distributed during the cutting process, thereby controlling the incision width.
By precisely controlling and optimizing these key factors, manufacturers can reduce production costs, improve material utilization, and increase production efficiency while ensuring high-precision cutting.
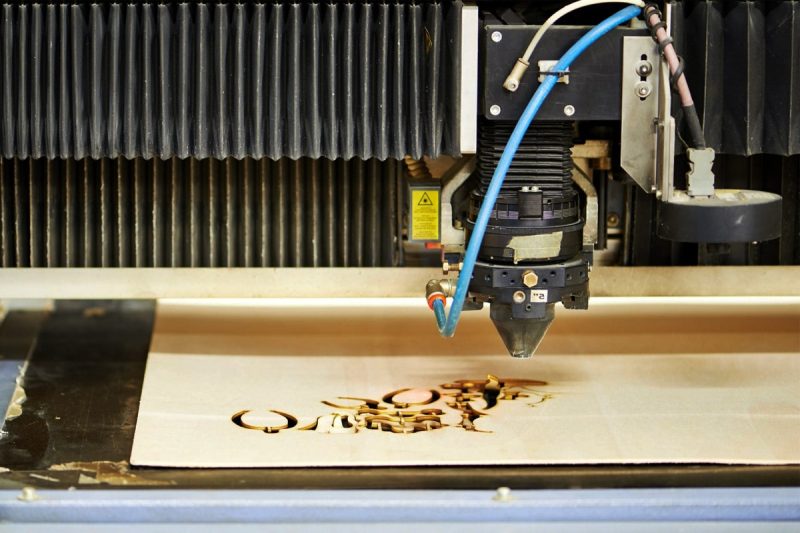
Optimization strategy to achieve minimum kerf width
To achieve the minimum kerf width in CO2 laser cutting, multiple optimization strategies must be considered. These strategies can not only improve cutting accuracy but also effectively reduce material waste and improve production efficiency. The following are the key optimization methods to achieve the minimum kerf width:
Optimize the optical system: The quality of the optical system directly affects the focusing effect of the laser beam, which in turn affects the fineness of the incision. Selecting a high-quality optical lens can ensure that the laser beam is evenly focused on the surface of the target material, thereby obtaining a stable and precise cutting effect. Using a short focal length lens (such as a 2.5-inch focal length) is an important strategy for optimizing the focusing of the laser beam. A short focal length lens can focus a smaller spot diameter, thereby reducing the diffusion of the laser beam and greatly reducing the incision width. A smaller spot can not only improve cutting accuracy but also reduce the thermal impact on the material and ensure stability during the cutting process.
Accurately adjust the laser power and speed: Laser power and cutting speed are two important factors that affect the incision width. The best cutting effect can be achieved by accurately adjusting the combination of laser power and speed. Using pulse mode can reduce the continuous heating time, thereby reducing the heat-affected zone (HAZ) and reducing the melting phenomenon at the edge of the incision. The pulse mode makes the laser energy distribution more uniform and avoids the overheating problem caused by high-power continuous output. At the same time, adjusting the laser power in combination with the thickness of the material can ensure that the laser beam can both completely penetrate the material and control the width of the incision. For thinner materials, reduce the power appropriately to avoid excessive heat accumulation; for thicker materials, increase the power appropriately to ensure cutting quality, but still pay attention to controlling the incision width.
Adjust auxiliary gas parameters: Auxiliary gas plays an important role in CO2 laser cutting. It not only helps to remove the melt produced during the cutting process but also controls the cutting quality by optimizing the gas pressure. Properly increasing the gas pressure can effectively remove the slag produced during the cutting process and prevent it from adhering to the edge of the incision, thereby maintaining a narrow incision width. When selecting an auxiliary gas, nitrogen is one of the commonly used gases, especially for materials that need to reduce oxidation and improve the cutting finish. Nitrogen can not only effectively reduce the oxidation of the material surface, but also maintain the smoothness of the incision during the cutting process, thereby obtaining a higher-quality cutting effect.
Optimize software and CNC parameters: High-precision CNC systems can effectively improve the accuracy of laser cutting and help reduce cutting deviations caused by mechanical errors. Using advanced CNC systems, you can optimize the cutting path and reduce errors caused by changes in the direction of the laser beam. Accurate path planning helps reduce errors caused by turns and uneven paths during cutting. In addition, the use of an automatic focusing system is also an important strategy for optimizing the incision width. The automatic focusing system can automatically adjust the laser focus position according to the thickness, shape, and cutting requirements of the material to ensure that the laser beam is always focused at the best position, thereby avoiding uneven or too wide incisions due to incorrect focus position.
Reduce the heat-affected zone (HAZ): The size of the HAZ is closely related to the heat accumulation during the laser cutting process. Excessive heat can cause excessive melting of the material surface, thereby increasing the incision width and affecting the cutting quality. To reduce the heat-affected zone, high-speed cutting is an effective strategy. High-speed cutting can accelerate the movement of the laser beam, thereby reducing the accumulation of heat on the material surface and avoiding melting and widening of the incision edge. However, when using high-speed cutting, it is necessary to ensure that the energy of the laser beam is sufficient to penetrate the material. To further optimize the cutting quality, cooling technology can be combined, such as spray cooling or dual gas injection, which can effectively reduce the temperature of the cutting area, avoid overheating, and ensure a more precise and stable cutting effect.
By combining the above optimization strategies, manufacturers can effectively achieve the minimum kerf width in CO2 laser cutting. With the continuous advancement of technology and continuous optimization of equipment, these strategies will help to further improve cutting accuracy, reduce material waste, and improve production efficiency.
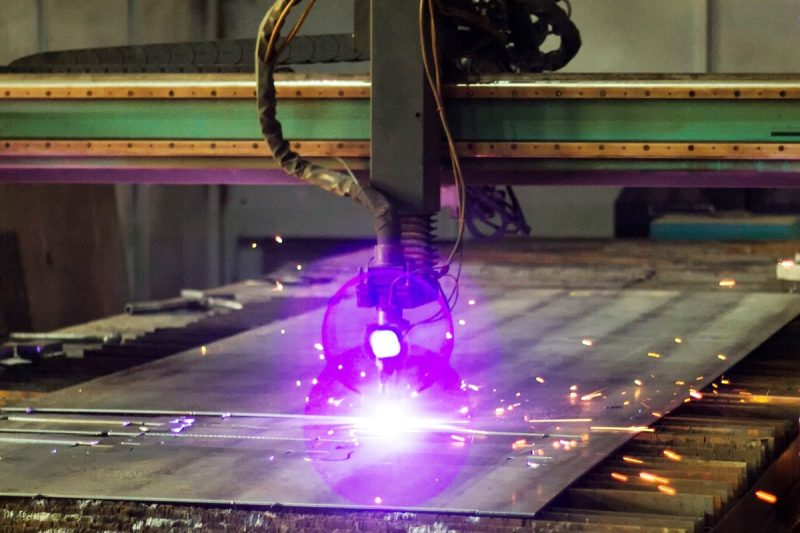
Podsumować
Achieving the minimum kerf width is not just a simple parameter adjustment, but a process that requires comprehensive consideration of many factors. By accurately optimizing the laser focus, power setting, cutting speed, auxiliary gas type and pressure, and software control, manufacturers can maximize production efficiency and reduce material waste while ensuring cutting quality. Precise adjustment of the laser focus can ensure the spot size of the cutting area and avoid excessive heat-affected zones during the cutting process, thereby ensuring a fine and smooth cut. The precise combination of power and cutting speed can avoid excessive heat accumulation and reduce the impact of the melt on the cut width. The right auxiliary gas can not only remove slag but also prevent oxidation, further improving the cutting quality. At the same time, the use of advanced CNC software and automatic focusing technology can continuously optimize the cutting path and laser beam focus to ensure the stability and consistency of the cutting effect.
With the continuous development of technology, the performance and control accuracy of CO2 laser cutting machines are also constantly improving. Manufacturers can achieve more accurate cutting effects by continuously adjusting and optimizing the above factors, combined with the continuous advancement of optical technology, automated control systems, and efficient cooling technology. Ultimately, achieving the minimum incision width not only improves cutting accuracy, but also brings higher production efficiency, reduces material costs, and significantly improves the economic benefits of the production line in long-term use. Therefore, for users of Maszyny do cięcia laserem CO2, continuous learning and mastering of these optimization strategies will be the key to improving overall production capacity and competitiveness.
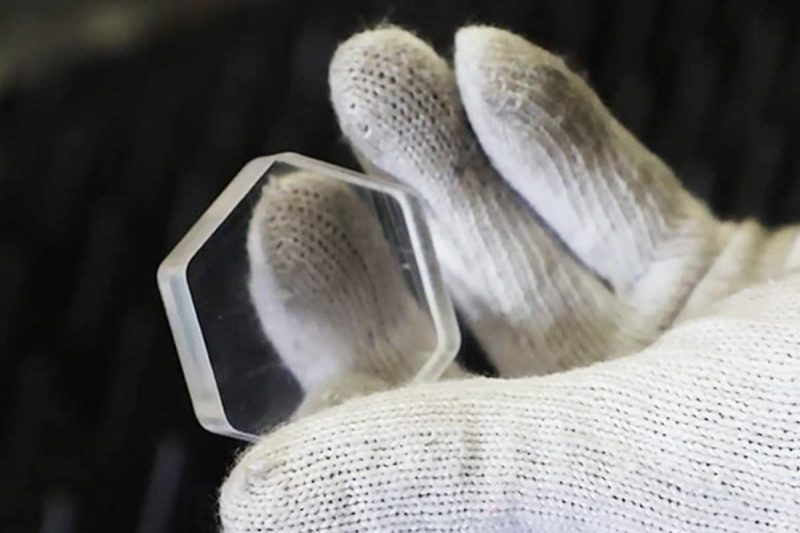
Uzyskaj rozwiązania laserowe
Laser AccTek provides high-precision CO2 laser cutting equipment that supports intelligent focusing, automatic path optimization, and efficient auxiliary gas control to ensure the minimum incision width and achieve precision processing. Skontaktuj się z nami to get customized laser-cutting solutions to improve your production efficiency and processing accuracy!
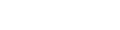
Informacje kontaktowe
- [email protected]
- [email protected]
- +86-19963414011
- Nr 3 Strefa A, strefa przemysłowa Lunzhen, miasto Yucheng, prowincja Shandong.
Uzyskaj rozwiązania laserowe