
W jaki sposób cięcie laserem CO2 minimalizuje ilość odpadów materiałowych?
Technologia cięcia laserem CO2 jest szeroko stosowana w produkcji, szczególnie w obróbce metali, cięciu tworzyw sztucznych, grawerowaniu drewna i innych dziedzinach. Cięcie laserowe jest cenione za precyzję, szybkość i elastyczność. Jednak odpady materiałowe to problem, którego nie można ignorować podczas procesu cięcia. Sposób minimalizacji odpadów materiałowych poprzez cięcie laserem CO2 jest nie tylko związany z kontrolą kosztów, ale również bezpośrednio wpływa na wydajność produkcji i zrównoważony rozwój środowiska. W tym artykule zbadamy, jak zmniejszyć odpady materiałowe poprzez optymalizację procesów i technologii cięcia laserowego.
Spis treści
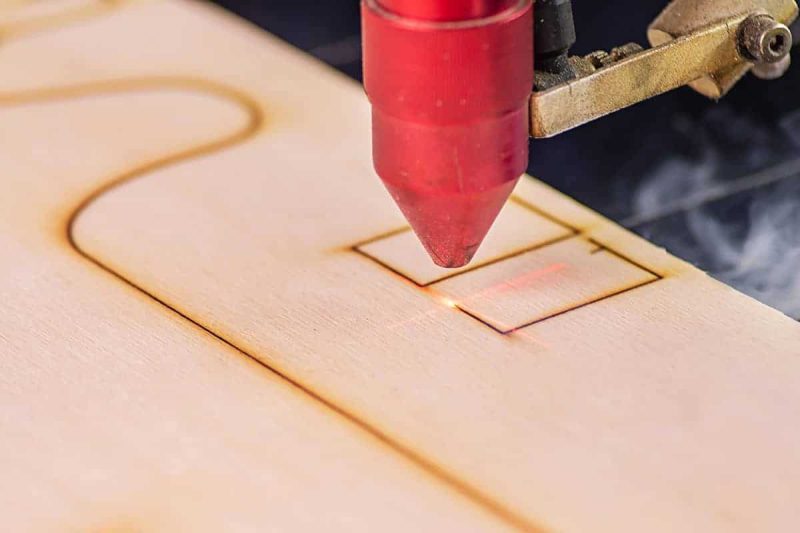
Precyzyjna kontrola parametrów cięcia
Zaletą cięcia laserem CO2 jest jego doskonała precyzja, która może zminimalizować straty materiału poprzez precyzyjną kontrolę wielu parametrów cięcia. Główne parametry obejmują moc lasera, prędkość cięcia i przepływ gazu. Optymalizacja tych parametrów może poprawić wyniki cięcia i zwiększyć wydajność produkcji przy jednoczesnym zmniejszeniu strat.
Regulacja mocy lasera
Moc lasera bezpośrednio określa ilość ciepła wprowadzanego podczas procesu cięcia. Nadmierna moc doprowadzi do nadmiernej ablacji materiału i nieregularnych krawędzi, co spowoduje niepotrzebne straty. Rozsądne dostosowanie mocy lasera, w zależności od rodzaju i grubości różnych materiałów, może zapewnić, że wiązka lasera dokładnie skoncentruje energię na obszarze cięcia, zmniejszy wpływ cieplny otaczającego obszaru i zapobiegnie nadmiernej utracie materiału. Odpowiednie ustawienia mocy mogą również zmniejszyć topienie i przypalanie podczas procesu cięcia oraz poprawić jakość powierzchni cięcia.
Optymalizacja prędkości cięcia
Dostosowanie prędkości cięcia jest kluczowe dla zmniejszenia strat materiału. Zbyt niska prędkość zwiększy dopływ ciepła, powodując przegrzanie powierzchni cięcia, co może skutkować przypaleniami krawędzi lub nadmiernym topnieniem, marnotrawieniem materiału i obniżeniem jakości cięcia. Zbyt wysoka prędkość cięcia może skutkować niekompletnymi lub nieregularnymi cięciami, co skutkuje nieobciętym materiałem resztkowym. Dlatego optymalizacja prędkości cięcia w celu zapewnienia, że dostosowuje się ona do charakterystyki i grubości różnych materiałów, może skutecznie zmniejszyć niepotrzebne straty i poprawić jakość cięcia.
Kontrola przepływu gazu
Przepływ gazu odgrywa kluczową rolę w procesie cięcia laserem CO2, ponieważ pomaga schłodzić obszar cięcia i usunąć stopiony metal. Zbyt duży przepływ gazu może prowadzić do nierównej powierzchni cięcia lub rozpryskiwania żużlu, niestabilnego przepływu powietrza i zwiększonej ilości odpadów; natomiast zbyt mały przepływ gazu może prowadzić do niezadowalającego efektu cięcia, uniemożliwiając skuteczne oddmuchiwanie stopionego metalu lub uniknięcie utleniania. Dlatego też, poprzez dokładną regulację przepływu gazu, można zagwarantować stabilność cięcia i wysokiej jakości efekt cięcia, redukując niepotrzebne odpady materiałowe.
Dzięki precyzyjnej kontroli parametrów cięcia można nie tylko poprawić jakość cięcia, ale także skutecznie zoptymalizować efektywność wykorzystania materiału, zmniejszyć ilość odpadów i zwiększyć wydajność produkcji.
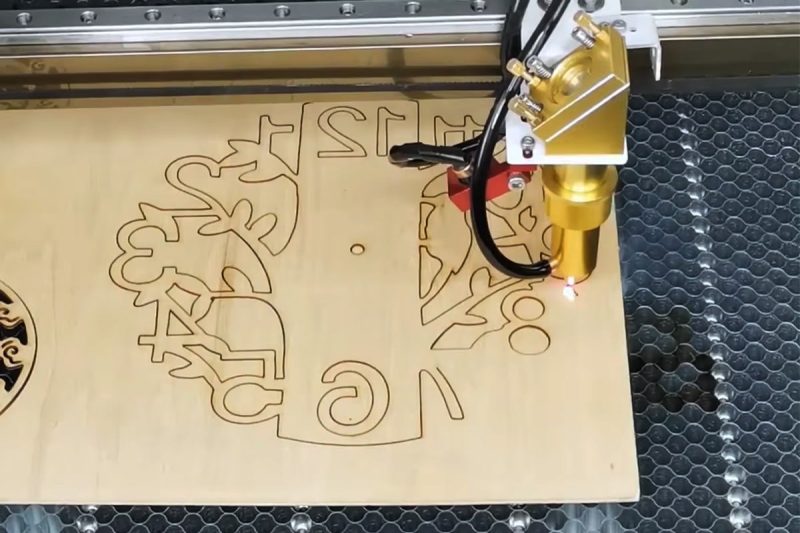
Optymalizacja układu materiałów
Znaczenie rozmieszczenia materiałów w cięciu laserem CO2 jest oczywiste. Rozsądne rozmieszczenie może nie tylko zwiększyć wydajność wykorzystania materiałów, ale także zmniejszyć ilość odpadów oraz poprawić dokładność cięcia i wydajność produkcji. Optymalizacja projektu układu umożliwia zminimalizowanie niewykorzystanych przerw, oszczędzanie materiałów i redukcję kosztów. W praktycznych zastosowaniach optymalizacja rozmieszczenia materiałów obejmuje wiele aspektów, w tym układ części, projekt ścieżki cięcia i układ sekwencji cięcia.
Efektywne projektowanie typografii
Efektywne projektowanie układu jest kluczem do maksymalizacji wykorzystania materiałów. Korzystanie z profesjonalnego oprogramowania do projektowania układu może pomóc projektantom w dokładnym rozmieszczeniu układu części. Dzięki funkcji automatycznego projektowania układu projektanci mogą obliczyć najlepsze rozmieszczenie części w krótkim czasie, aby zminimalizować odpady tak bardzo, jak to możliwe. Podczas projektowania układu bardzo ważne jest zaplanowanie ścieżki cięcia i zminimalizowanie odstępu między częściami (tj. odpadami). Rozsądne ustawienie odstępu może nie tylko zmniejszyć odpady materiałowe, ale także skrócić późniejszy czas i koszty postprodukcji.
Podczas projektowania układu należy również wziąć pod uwagę specyfikacje i grubość materiałów. Różne strategie układu są wymagane dla materiałów o różnych rozmiarach. Na przykład w przypadku materiałów o dużych rozmiarach rozsądne rozmieszczenie ścieżki i kierunku cięcia może nie tylko zmniejszyć ilość odpadów, ale także uniknąć odkształceń materiału lub złego cięcia; podczas gdy w przypadku materiałów o małych rozmiarach układ musi maksymalizować wykorzystanie powierzchni cięcia każdego kawałka materiału, aby uniknąć odpadów.
Jednocześnie oprogramowanie może symulować proces cięcia i obliczać najlepszą sekwencję cięcia, aby zapewnić, że każda część zostanie wycięta w odpowiednim miejscu, redukując niepotrzebne przerwy i odpady oraz poprawiając wydajność produkcji. Na przykład podczas procesu cięcia unikanie zbyt wielu pustych obszarów może zapewnić, że każdy kawałek materiału zostanie w pełni wykorzystany.
Unikaj zbędnego cięcia
Cięcie nadmiarowe odnosi się do wielokrotnego cięcia lub niepotrzebnego powtarzanego cięcia z powodu nierozsądnego projektu lub niewłaściwego planowania ścieżki cięcia. Cięcie nadmiarowe nie tylko marnuje materiały, ale także wydłuża czas produkcji i zmniejsza wydajność pracy. W procesie cięcia laserowego kluczowe jest unikanie powtarzanego cięcia lub bezsensownych ścieżek w jak największym stopniu, aby poprawić wykorzystanie materiału.
Rozsądne planowanie ścieżek cięcia może zapewnić, że każda część osiągnie oczekiwany efekt, gdy zostanie po raz pierwszy przecięta, bez generowania dodatkowych odpadów z powodu późniejszej regulacji ścieżki lub dodatkowego cięcia. Szczególnie w produkcji masowej unikanie zbędnego cięcia jest szczególnie ważne dla poprawy wydajności produkcji i oszczędzania materiałów. Na przykład użycie oprogramowania optymalizacyjnego do określenia kolejności cięcia i upewnienia się, że ścieżka cięcia każdej części jest tak krótka, jak to możliwe i bez przecięć, może znacznie zmniejszyć występowanie zbędnego cięcia.
Jednocześnie unikanie zbyt wielu przerw w cięciu, ruchów lub powtarzających się czynności podczas procesu cięcia może zmniejszyć niepotrzebne zużycie energii i marnowanie czasu oraz poprawić ogólną wydajność produkcji. Dzięki racjonalnemu planowaniu sekwencji i ścieżki cięcia można zapewnić, że każda czynność cięcia jest konieczna, skutecznie unikając w ten sposób zbędnego cięcia i marnowania materiału.
Inteligentny skład tekstu i współpraca procesowa
Dzięki ciągłemu rozwojowi technologii cięcia laserowego coraz więcej inteligentnego oprogramowania do układu może współpracować z linią produkcyjną, aby dostosować projekt układu w czasie rzeczywistym, aby spełnić różne wymagania materiałowe. Poprzez analizę danych i uczenie maszynowe inteligentny układ może optymalizować ścieżkę cięcia i układ na podstawie danych historycznych i informacji zwrotnych w czasie rzeczywistym, nie tylko biorąc pod uwagę rozmiar i kształt materiału, ale także dokonując optymalnych korekt na podstawie wymagań procesu. Ta inteligentna metoda układu znacznie poprawia wykorzystanie materiałów i zmniejsza potrzebę ręcznej interwencji.
Na przykład inteligentny system może automatycznie dostosowywać ścieżkę cięcia i sekwencję podczas procesu produkcji, dynamicznie dostosowywać się do charakterystyki różnych materiałów i rytmu produkcji oraz optymalizować układ i ścieżkę cięcia w czasie rzeczywistym, aby zminimalizować odpady. Ta technologia może sprawić, że proces produkcji będzie bardziej wydajny i inteligentny, znacznie zmniejszyć odpady materiałowe i poprawić dokładność cięcia.
Optymalizacja układu materiałów jest kluczowym czynnikiem w poprawie wykorzystania materiałów i redukcji odpadów podczas cięcia laserem CO2. Dzięki wydajnemu projektowaniu układu, unikaniu zbędnego cięcia i inteligentnej technologii układu, niepotrzebne odpady mogą być skutecznie zredukowane, wydajność produkcji może zostać zwiększona, a koszty mogą zostać obniżone. Rozsądny układ może nie tylko zoptymalizować wykorzystanie materiałów, ale także poprawić jakość cięcia, zapewniając, że każdy proces cięcia jest wydajny i dokładny. W nowoczesnej produkcji optymalizacja układu materiałów stała się ważną strategią poprawy wydajności produkcji i redukcji odpadów.
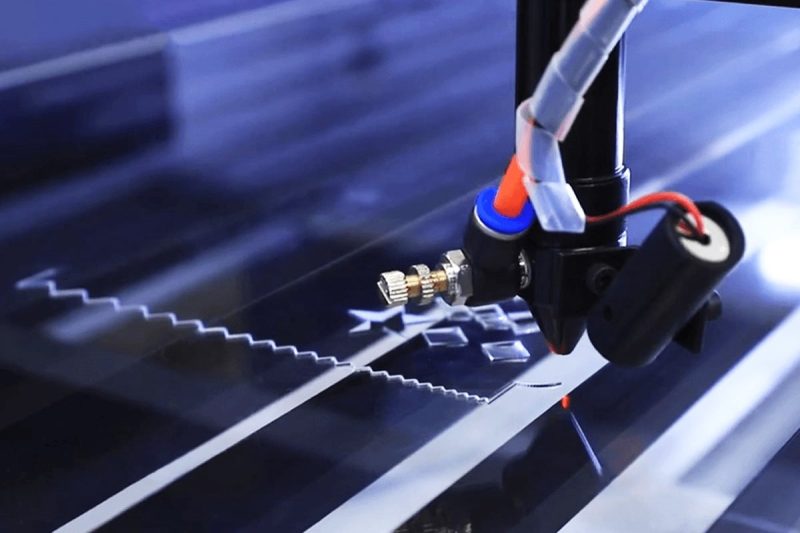
Użyj wysokiej jakości maszyny do cięcia laserowego
Wydajność i technologia sprzętu bezpośrednio wpływają na dokładność cięcia i odpady materiałowe. Aby osiągnąć cel wysokiej wydajności i niskich odpadów w procesie cięcia laserem CO2, bardzo ważne jest wybranie wysokiej jakości maszyny do cięcia laserowego. Wysokiej jakości maszyny do cięcia laserowego są nie tylko wyposażone w zaawansowaną technologię sterowania wiązką i precyzyjne systemy regulacji ostrości, ale także mają stabilną wydajność i wydajne możliwości cięcia, co może zapewnić dokładność cięcia przy jednoczesnym zminimalizowaniu odpadów materiałowych.
Precyzyjna kontrola wiązki
Nowoczesne, wysokiej klasy maszyny do cięcia laserem CO2 są wyposażone w zaawansowaną technologię sterowania wiązką, aby zapewnić, że wiązka lasera jest zawsze skupiona na obszarze cięcia materiału. Technologia ta obejmuje wysoce precyzyjną regulację wiązki lasera i system sterowania ogniskowaniem, który może dokładnie skupić energię lasera na powierzchni materiału, co skutkuje mniejszą strefą wpływu ciepła i czystszymi krawędziami cięcia. Zmniejszenie strefy wpływu ciepła i przypalenia nie tylko pomaga poprawić jakość cięcia, ale także zmniejsza niepotrzebne marnotrawstwo materiału.
Precyzyjna kontrola wiązki jest podstawą zapewnienia wysokiej jakości cięcia. Gdy położenie ogniska lasera jest dokładne, energia wiązki lasera może być skoncentrowana i przeniesiona na materiał, unikając nadmiernego rozpraszania energii na otaczający obszar, tym samym zmniejszając utratę ciepła i niepotrzebne straty materiału. Ponadto precyzyjna kontrola wiązki może również utrzymać powierzchnię cięcia płaską i wolną od wad podczas cięcia złożonych kształtów i drobnych detali, unikając w ten sposób marnowania materiału.
Automatyczny system regulacji
Zaawansowane maszyny do cięcia laserem CO2 są wyposażone w automatyczny system regulacji, który może automatycznie regulować moc lasera, przepływ gazu, prędkość cięcia i inne parametry na podstawie danych zwrotnych w czasie rzeczywistym, aby zapewnić, że każda ścieżka cięcia jest w najlepszym stanie. Ta funkcja automatycznej regulacji odgrywa ważną rolę w procesie cięcia i może optymalizować parametry cięcia w czasie rzeczywistym dla różnych materiałów i warunków cięcia, aby uniknąć niestabilności spowodowanej nieprawidłową obsługą przez człowieka lub zmianami środowiskowymi.
Na przykład, automatyczna regulacja mocy lasera i przepływu gazu może być dynamicznie optymalizowana w zależności od grubości i rodzaju materiału, zapewniając umiarkowane ciepło wejściowe podczas procesu cięcia i redukując ablację materiału i odkształcenia spowodowane nadmiernym ciepłem wejściowym. Jednocześnie, automatyczna regulacja prędkości cięcia może być regulowana w zależności od charakterystyki materiału i złożoności cięcia, zapewniając w ten sposób ciągłość i jakość ścieżki cięcia. Dzięki temu wydajnemu monitorowaniu i regulacji w czasie rzeczywistym, maszyna tnąca laserem może nie tylko zwiększyć wydajność produkcji, ale także znacząco ograniczyć zbędne odpady.
Ponadto, automatyczny system regulacji może również dokonywać korekt na podstawie danych zwrotnych w czasie rzeczywistym podczas procesu cięcia, korygując wszelkie błędy spowodowane zmianami położenia przedmiotu obrabianego, właściwości materiału lub dokładności sprzętu, utrzymując w ten sposób stabilną jakość cięcia i minimalne straty materiału. Ta funkcja regulacji w czasie rzeczywistym znacznie zmniejsza straty spowodowane błędami ludzkimi lub opóźnieniami technologicznymi, zapewniając, że każde cięcie jest wykonywane w najlepszych warunkach.
Technologia cięcia wieloosiowego
Wiele wysokiej klasy maszyn do cięcia laserem CO2 jest również wyposażonych w technologię cięcia wieloosiowego, która umożliwia uzyskanie bardziej złożonych i precyzyjnych ścieżek cięcia. Technologia wieloosiowa umożliwia cięcie w wielu kierunkach jednocześnie, co nie tylko zwiększa wydajność cięcia, ale także zmniejsza ilość odpadów materiałowych. Na przykład niektóre maszyny do cięcia mogą regulować położenie głowicy laserowej, aby dokładniej dostosować kąt i ścieżkę cięcia, dzięki czemu każda ścieżka cięcia minimalizuje przerwy i zmniejsza generowanie bezużytecznych odpadów.
Technologia wieloosiowa umożliwia maszynom do cięcia laserowego wykonywanie bardziej elastycznego planowania ścieżki podczas procesu cięcia, zwłaszcza podczas cięcia złożonych części, co może skutecznie zapobiegać nadmiernym stratom spowodowanym niewłaściwym planowaniem ścieżki. Ponadto technologia cięcia wieloosiowego może również zmniejszyć występowanie powtarzających się cięć i zbędnych ścieżek, tym samym jeszcze bardziej redukując straty materiału i koszty produkcji.
Długość fali lasera i technologia ogniskowania
Różne maszyny do cięcia laserem CO2 mogą wykorzystywać wiązki laserowe o różnych długościach fal, a wybór długości fali lasera ma istotny wpływ na dokładność i wydajność cięcia. Generatory laserowe CO2 zazwyczaj wykorzystują lasery o długości fali 10,6 mikronów, co ma bardzo wysoki współczynnik absorpcji podczas cięcia metali i niektórych materiałów niemetalicznych, dzięki czemu może skutecznie poprawić efekt cięcia. Wysokiej jakości maszyny do cięcia laserem CO2 są wyposażone w zaawansowane systemy optyczne, aby zapewnić, że wiązka lasera może być skupiona na powierzchni materiału i osiągnąć cięcie o wysokiej precyzji.
Dzięki precyzyjnej kontroli długości fali lasera i skupienia wiązki, maszyny do cięcia laserem CO2 mogą osiągać wydajne i wysokiej jakości rezultaty cięcia różnych materiałów. Wyższa jakość wiązki oznacza lepszą koncentrację energii lasera, co zmniejsza rozpraszanie energii i odpady, zapewniając bardziej wydajne wykorzystanie materiałów.
Wybór wysokiej jakości Maszyna do cięcia laserem CO2 jest kluczem do osiągnięcia wydajnego cięcia i zmniejszenia strat materiału. Kompleksowe zastosowanie precyzyjnej kontroli wiązki, automatycznego systemu regulacji, technologii cięcia wieloosiowego, długości fali lasera i technologii ogniskowania może nie tylko poprawić dokładność cięcia, ale także znacznie zmniejszyć strefę wpływu ciepła i zmniejszyć ablację materiału i straty. Dzięki ciągłemu rozwojowi technologii cięcia laserowego, nowoczesne maszyny do cięcia laserowego są w stanie osiągnąć wydajne i precyzyjne cięcie, tym samym znacznie poprawiając wykorzystanie materiału i zmniejszając koszty produkcji, zapewniając jednocześnie jakość cięcia.
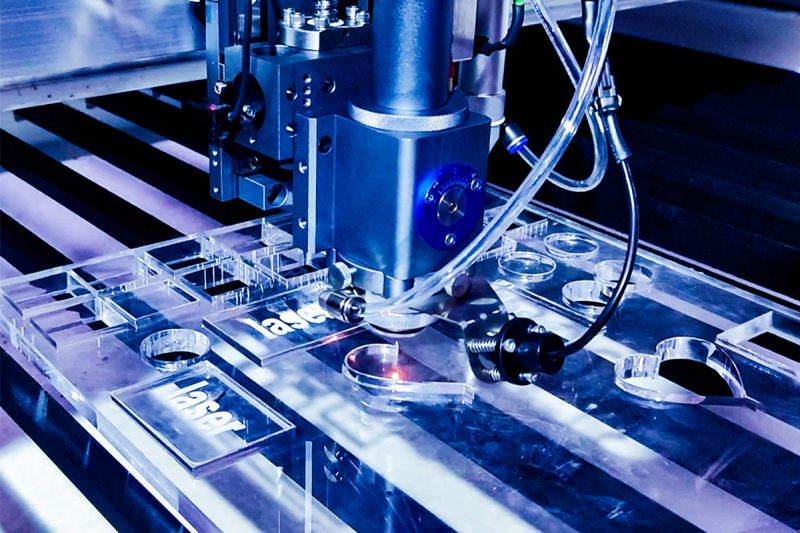
Rozsądny wybór materiałów do cięcia
Wybór odpowiedniego materiału do cięcia jest kluczowy dla zmniejszenia strat materiału podczas cięcia laserem CO2. Maszyny do cięcia laserem CO2 są głównie używane do cięcia materiałów niemetalicznych, zwłaszcza niektórych tworzyw termoplastycznych, drewna, papieru i tkanin. Absorpcyjność, przewodność cieplna, współczynnik odbicia i inne cechy różnych materiałów podczas cięcia laserowego mają bezpośredni wpływ na efekt cięcia i straty materiału. Dlatego wybór odpowiedniego materiału do cięcia jest ważnym krokiem w celu zwiększenia wydajności i zmniejszenia strat.
Wybór odpowiednich materiałów
Zaletą maszyny do cięcia laserem CO2 jest jej wysoka wydajność w cięciu materiałów niemetalicznych. Przy wyborze materiałów do cięcia kluczowe znaczenie ma absorpcja i współczynnik odbicia materiału. W przypadku maszyn do cięcia laserem CO2 wybór materiałów o wysokiej absorpcji długości fali lasera CO2 może pomóc w zwiększeniu wydajności cięcia i zmniejszeniu ilości odpadów.
- Papier i tektura: Papier i tektura mają wysoki współczynnik absorpcji dla laserów CO2, co pozwala zachować wysoką wydajność i zmniejszyć ilość odpadów podczas cięcia. Materiały te są często stosowane w dziedzinie opakowań, reklamy i projektowania.
- Tworzywa sztuczne (np. akryl, PVC): Lasery CO2 zapewniają dobre cięcie tworzyw termoplastycznych (np. akryl, PVC itp.) i umożliwiają precyzyjną kontrolę krawędzi tnącej, co pozwala uniknąć niepotrzebnych stref wpływu ciepła i marnowania materiału.
- Drewno i materiały kompozytowe: Maszyny do cięcia laserem CO2 są również szeroko stosowane do cięcia drewna i materiałów kompozytowych. Materiały te dobrze pochłaniają lasery CO2, co pozwala na czyste cięcie, zmniejsza przypalanie i uszkodzenia cieplne oraz zapewnia maksymalne wykorzystanie materiału.
Wybierz odpowiednią grubość materiału
Oprócz rodzaju materiału, grubość materiału również wpływa na efekt cięcia laserem CO2. W przypadku cieńszych materiałów zbyt duża moc lasera może powodować nadmierne wprowadzanie ciepła, co skutkuje nadmiernymi strefami wpływu ciepła, powodując nadmierną ablację i marnotrawstwo materiałów. Z kolei w przypadku grubszych materiałów zbyt mała moc lasera może skutkować niepełnym cięciem.
- Cienkie materiały: Podczas cięcia cienkich materiałów należy unikać nadmiernej mocy lasera lub niskich prędkości cięcia. Ustaw moc i prędkość odpowiednio, aby uniknąć nadmiernego spalania i marnotrawstwa.
- Grubsze materiały: Grubsze materiały wymagają większej mocy lasera, aby zapewnić dokładne cięcie, ale nadal należy unikać nadmiernej mocy, która może powodować utratę ciepła lub nierówne krawędzie.
Związek między przewodnością cieplną a cięciem laserowym
Przewodność cieplna różnych materiałów ma również znaczący wpływ na skuteczność cięcia laserowego. Materiały o wysokiej przewodności cieplnej (takie jak metale) będą szybko odprowadzać ciepło z obszaru cięcia, co może skutkować niepełnym cięciem lub nadmiernymi strefami oddziaływania ciepła, zwiększając straty materiału. Natomiast materiały o niższej przewodności cieplnej (takie jak drewno i plastik) pomagają koncentrować ciepło, poprawiając w ten sposób wyniki cięcia i zmniejszając straty.
W przypadku cięcia laserem CO2 powszechnie stosowane materiały niemetalowe, takie jak tworzywa sztuczne i drewno, charakteryzują się niską przewodnością cieplną, co pozwala na efektywne wykorzystanie energii lasera i zmniejszenie strefy wpływu ciepła w trakcie procesu cięcia.
Wpływ obróbki powierzchni materiału na efekt cięcia
Obróbka powierzchniowa materiałów jest również kluczowa w cięciu laserem CO2. W przypadku materiałów niemetalicznych, brud powierzchniowy, smar, warstwa tlenku itp. zmniejszą wydajność absorpcji lasera, co spowoduje marnotrawstwo energii. Dlatego przed cięciem laserowym upewnienie się, że powierzchnia materiału jest czysta i wolna od zanieczyszczeń, może skutecznie poprawić wydajność cięcia i zmniejszyć ilość odpadów.
Na przykład czyste powierzchnie z tworzywa sztucznego lub drewna pochłaniają energię lasera wydajniej, co skutkuje bardziej wydajnym cięciem i mniejszą ilością odpadów. Jeśli powierzchnia materiału zawiera olej lub zanieczyszczenia, szybkość absorpcji energii lasera zostanie zmniejszona, efekt cięcia będzie słaby, a odpady będą generowane.
W przypadku maszyn do cięcia laserem CO2 bardzo ważne jest wybranie odpowiedniego materiału niemetalicznego i grubości materiału. Podczas procesu cięcia szybkość absorpcji materiału, przewodność cieplna i stan obróbki powierzchni będą miały bezpośredni wpływ na wydajność wykorzystania energii lasera, a tym samym na marnotrawstwo materiału. Rozsądny wybór odpowiednich materiałów i dostosowanie parametrów cięcia może nie tylko poprawić wydajność cięcia, ale także zminimalizować marnotrawstwo materiału i obniżyć koszty produkcji. Poprzez optymalizację doboru materiałów i ustawień cięcia firmy mogą osiągnąć wyższe wykorzystanie materiału, zapewniając jednocześnie jakość cięcia.
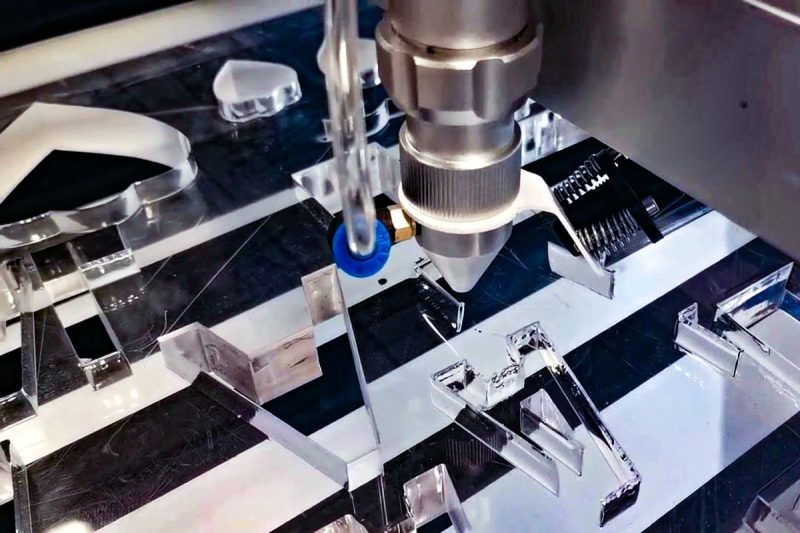
Utrzymuj i optymalizuj wydajność sprzętu
Utrzymanie dobrej wydajności maszyny do cięcia laserowego jest kluczowym czynnikiem zapewniającym dokładność cięcia, poprawiającym wydajność produkcji i zmniejszającym marnotrawstwo materiałów. Regularna konserwacja sprzętu może nie tylko wydłużyć żywotność maszyny do cięcia laserowego, ale także zapewnić stabilność sprzętu podczas procesu cięcia, skutecznie zmniejszając tym samym marnotrawstwo spowodowane awarią sprzętu lub pogorszeniem wydajności. Aby zmaksymalizować wydajność sprzętu, maszyna do cięcia laserowego wymaga serii regularnych inspekcji, konserwacji i optymalizacji. Oto kilka kluczowych kroków i sugestii dotyczących konserwacji:
Regularnie sprawdzaj optykę
Elementy optyczne, takie jak głowice laserowe, reflektory i soczewki, bezpośrednio wpływają na jakość ogniskowania wiązki laserowej i dokładność cięcia. Z biegiem czasu te elementy optyczne mogą ulec uszkodzeniu lub degradacji z powodu kurzu, zanieczyszczeń lub wysokich temperatur, co wpłynie na jakość cięcia laserowego. Aby zapewnić najlepszą wydajność maszyny do cięcia laserowego, konieczne jest regularne sprawdzanie i czyszczenie elementów optycznych. Konkretne operacje są następujące:
- Wyczyść elementy optyczne: Używaj bezpyłowej ściereczki i profesjonalnego płynu czyszczącego do regularnego czyszczenia soczewki i obiektywu. Unikaj używania szorstkich materiałów, aby uniknąć zarysowania powierzchni elementów optycznych. Utrzymywanie soczewki i obiektywu w czystości może zapewnić jakość ogniskowania wiązki laserowej i zmniejszyć utratę energii.
- Sprawdź ustawienie optyczne: Ustawienie głowicy lasera, reflektora i soczewki ma bezpośredni wpływ na ścieżkę i położenie ogniska wiązki laserowej. Regularne sprawdzanie ustawienia elementów optycznych w celu upewnienia się, że wiązka laserowa jest dokładnie skupiona na obszarze cięcia, pomoże poprawić jakość cięcia i zmniejszyć ilość odpadów.
Konserwacja i czyszczenie głowicy laserowej
Głowica laserowa jest jednym z głównych elementów maszyny do cięcia laserowego, odpowiedzialnym za skupianie wiązki laserowej na materiale. Z czasem głowica laserowa może zostać zanieczyszczona lub zużyta, co skutkuje niedokładnym skupianiem lasera i wpływa na efekt cięcia. Dlatego regularne czyszczenie i konserwacja głowicy laserowej są niezbędne. Podczas czyszczenia należy unikać zarysowania lub uszkodzenia powierzchni głowicy laserowej, aby uniknąć wtórnych uszkodzeń. Podczas czyszczenia należy zwrócić szczególną uwagę na następujące punkty:
- Sprawdź komponenty optyczne głowicy laserowej: Soczewki i lustra wewnątrz głowicy laserowej należy regularnie sprawdzać, aby upewnić się, że nie ma na nich plam, zarysowań ani innych wad. Jeśli są uszkodzone lub zanieczyszczone, należy je natychmiast wymienić.
- Sprawdź układ chłodzenia: Głowica laserowa jest zazwyczaj wyposażona w układ chłodzenia, aby zapewnić stabilną pracę głowicy laserowej w wysokich temperaturach. Regularnie sprawdzaj układ chłodzenia i odprowadzania ciepła, aby upewnić się, że działają prawidłowo, co pozwoli uniknąć pogorszenia wydajności głowicy laserowej z powodu przegrzania.
Kalibracja i optymalizacja parametrów cięcia laserowego
Wydajność maszyny do cięcia laserowego zależy nie tylko od jakości sprzętu, ale także od jego parametrów cięcia. Z czasem stan roboczy i wydajność cięcia sprzętu mogą się zmieniać, dlatego maszyna do cięcia laserowego musi być regularnie kalibrowana i optymalizowana. W zależności od materiału, parametry takie jak moc lasera, prędkość cięcia, przepływ gazu i pozycja ogniskowania mogą wymagać regulacji. Zapewnienie, że ustawienia parametrów maszyny do cięcia laserowego są zawsze w najlepszym stanie, może znacznie zmniejszyć marnotrawstwo materiału podczas procesu cięcia.
- Regularnie kalibruj moc lasera i prędkość cięcia: W procesie cięcia laserowego moc i prędkość cięcia są kluczowymi czynnikami wpływającymi na wyniki cięcia i marnotrawstwo materiału. Regularnie kalibruj sprzęt, aby mieć pewność, że moc lasera i prędkość cięcia zawsze znajdują się w optymalnym zakresie roboczym, aby uniknąć nadmiernego dopływu ciepła lub niepełnego cięcia.
- Zoptymalizuj położenie ogniska i jakość wiązki: Położenie ogniska lasera i jakość wiązki bezpośrednio determinują dokładność i efekt cięcia. Kalibrując położenie ogniska, upewnij się, że energia wiązki lasera jest skoncentrowana w obszarze cięcia, skutecznie poprawiając dokładność cięcia i zmniejszając straty spowodowane niedokładnym cięciem.
Regularnie sprawdzaj przepływ gazu i układ chłodzenia
Pomocniczy przepływ gazu ma kluczowe znaczenie dla stabilności procesu cięcia laserowego. Zbyt wysoki lub zbyt niski przepływ gazu może wpłynąć na jakość cięcia i zwiększyć straty materiału. Dlatego regularna kontrola i optymalizacja przepływu gazu jest niezbędnym środkiem, aby utrzymać wydajną pracę maszyny do cięcia laserowego. Stabilność przepływu gazu ma bezpośredni wpływ na efekt cięcia, jakość krawędzi tnącej i stopień strat materiału.
Ponadto nie można ignorować konserwacji układu chłodzenia. Źródło lasera i komponenty optyczne maszyny do cięcia laserowego muszą działać w odpowiednim zakresie temperatur, aby uniknąć przegrzania lub niewystarczającego chłodzenia, które mogą spowodować uszkodzenie sprzętu. Zapewnienie normalnej pracy układu chłodzenia może nie tylko wydłużyć żywotność sprzętu, ale także poprawić dokładność cięcia i zmniejszyć ilość odpadów spowodowanych awarią sprzętu.
Zapobieganie awariom sprzętu i terminowa naprawa
Awaria sprzętu jest jedną z głównych przyczyn problemów w procesie cięcia laserowego. Aby uniknąć przerw w produkcji i marnotrawstwa materiałów spowodowanego awarią sprzętu, niezbędne są regularne kontrole sprzętu i zapobieganie awariom. Regularne kontrole części mechanicznych, układów elektrycznych, źródeł laserowych itp. w celu upewnienia się, że są w dobrym stanie technicznym, mogą skutecznie zapobiegać awariom sprzętu. Ponadto, gdy zostaną znalezione problemy, naprawy i wymiana uszkodzonych części powinny być przeprowadzane niezwłocznie, aby uniknąć niskiej wydajności produkcji lub marnotrawstwa materiałów z powodu awarii sprzętu.
Regularna konserwacja i optymalizacja sprzętu nie tylko pomagają wydłużyć żywotność maszyny do cięcia laserowego, ale także zapewniają, że sprzęt jest zawsze w najlepszym stanie roboczym, co poprawia dokładność cięcia, stabilność i wykorzystanie materiału. Poprzez sprawdzanie i czyszczenie elementów optycznych, kalibrację parametrów cięcia, optymalizację przepływu gazu i układów chłodzenia itp., odpady spowodowane spadkiem wydajności sprzętu mogą zostać znacznie zredukowane. Ponadto terminowa konserwacja i zapobieganie awariom są również ważnymi środkami zapewniającymi ciągłą i wydajną pracę sprzętu. Dzięki kompleksowemu zarządzaniu i optymalizacji wydajności sprzętu, maszyna do cięcia laserowego może utrzymać wydajną pracę przez długi czas, zminimalizować odpady materiałowe i poprawić wydajność produkcji.
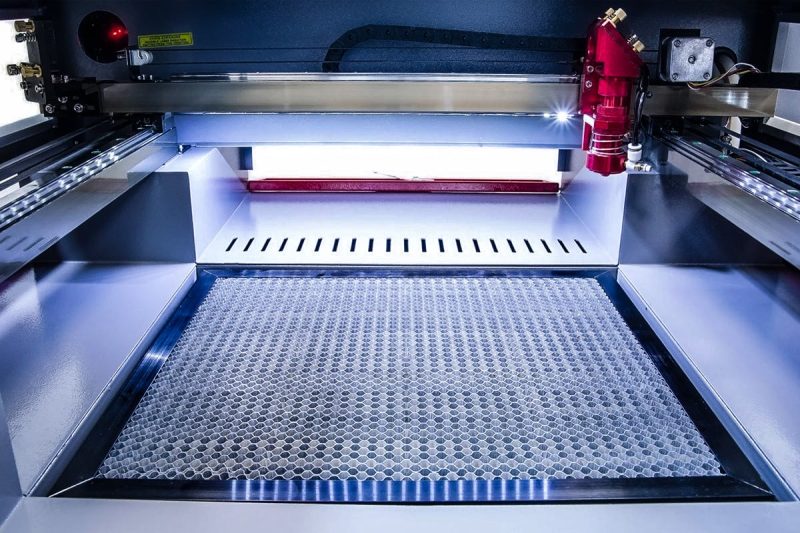
Podsumować
Cięcie laserem CO2 to wydajna i precyzyjna technologia cięcia, ale w praktycznych zastosowaniach odpady materiałowe nadal stanowią istotną kwestię. Poprzez precyzyjną kontrolę parametrów cięcia, optymalizację rozmieszczenia materiałów i dobór odpowiedniego sprzętu i materiałów, odpady materiałowe można zminimalizować, wydajność produkcji można poprawić, a koszty można obniżyć. Dzięki ciągłemu rozwojowi technologii laserowej i poprawie wydajności sprzętu, cięcie laserem CO2 w przyszłości będzie bardziej przyjazne dla środowiska i ekonomiczne oraz przyniesie więcej możliwości zrównoważonego rozwoju dla przemysłu wytwórczego.
Pod tym względem, Laser AccTek Maszyna do cięcia laserem CO2, dzięki swojej doskonałej technologii, precyzyjnemu systemowi sterowania i wydajnym możliwościom cięcia, może zapewnić klientom bardziej wydajne i przyjazne dla środowiska rozwiązania do cięcia, pomagając firmom zminimalizować marnotrawstwo materiałów i poprawić wydajność produkcji oraz opłacalność. Jeśli potrzebujesz maszyny do cięcia laserem CO2, skontaktuj się z nami natychmiast, aby uzyskać wycenę.
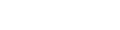
Informacje kontaktowe
- [email protected]
- [email protected]
- +86-19963414011
- Nr 3 Strefa A, strefa przemysłowa Lunzhen, miasto Yucheng, prowincja Shandong.
Uzyskaj rozwiązania laserowe