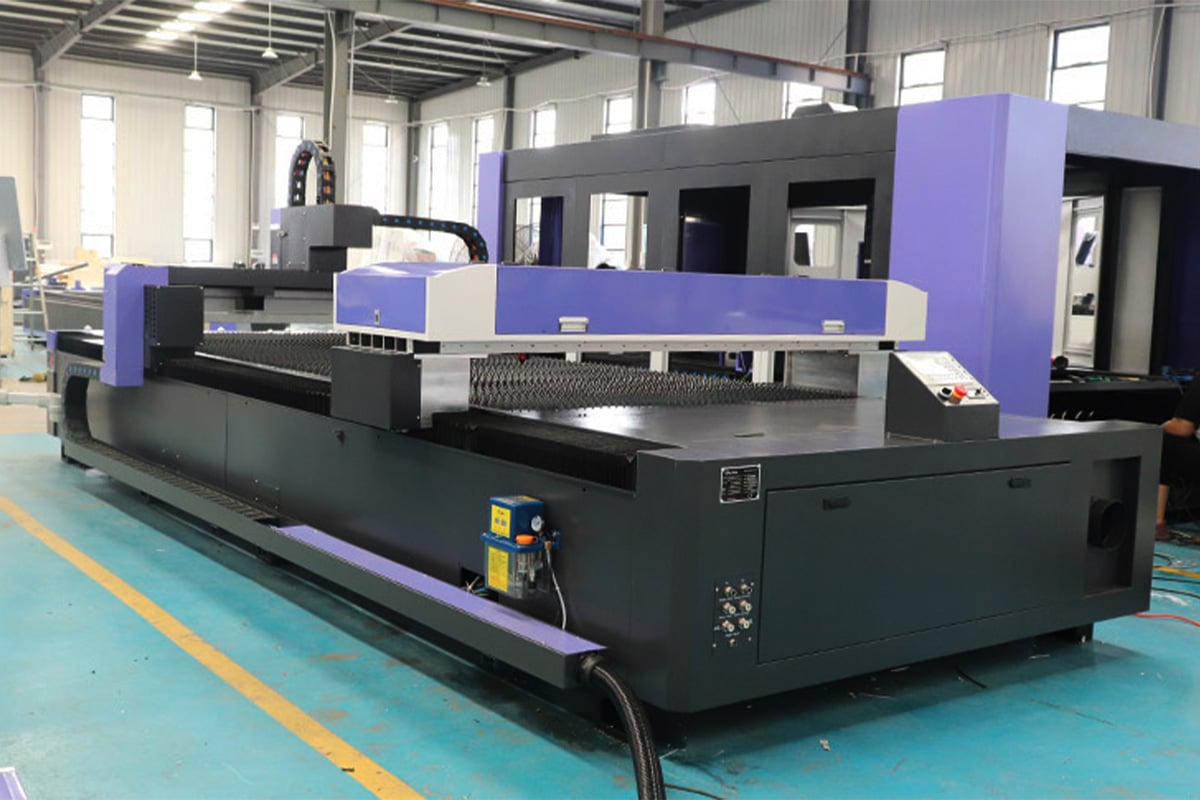
Jak osiągnąć minimalną szerokość nacięcia podczas cięcia laserem CO2?
Technologia cięcia laserem CO2 jest szeroko stosowana w procesie cięcia różnych materiałów, takich jak obróbka metalu, plastiku, drewna, tkanin itp. ze względu na jej zalety wysokiej precyzji, dużej prędkości i obróbki bezkontaktowej. Szerokość nacięcia odnosi się do szerokości nacięcia utworzonego przez wiązkę lasera podczas procesu cięcia. Wskaźnik ten bezpośrednio wpływa na precyzję i jakość cięcia. Mniejsza szerokość nacięcia może zapewnić bardziej wyrafinowany efekt obróbki, poprawić precyzję produktu, zmniejszyć ilość odpadów materiałowych i obniżyć koszty produkcji. Dlatego jest to ważne kryterium pomiaru jakości cięcia laserowego.
Kontrola szerokości nacięcia nie służy tylko poprawie jakości produktu, ale jest również ściśle związana ze stopniem wykorzystania materiałów, wygodą późniejszego przetwarzania i ogólną wydajnością produkcji. Dla producentów optymalizacja szerokości nacięcia jest bezpośrednio związana z kontrolą kosztów produkcji. Szczególnie w przypadku produkcji na dużą skalę zbyt duża szerokość nacięcia może prowadzić do marnotrawstwa materiału i wpływać na płynny przebieg kolejnych procesów. Dlatego precyzyjna kontrola szerokości nacięcia jest ważnym ogniwem umożliwiającym osiągnięcie wydajnej i taniej produkcji.
Spis treści
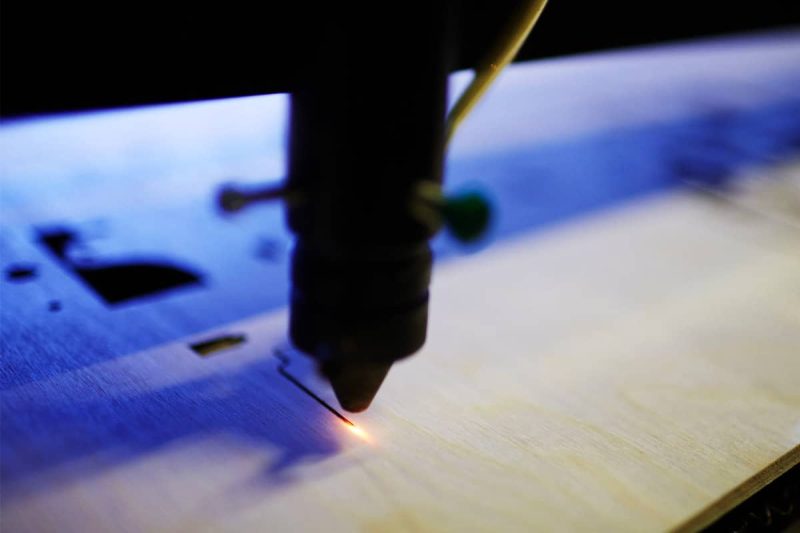
Kluczowe czynniki wpływające na szerokość szczeliny cięcia laserem CO2
Na efekt cięcia technologią cięcia laserem CO2 wpływa wiele czynników, a szerokość szczeliny jest jednym z najważniejszych wskaźników. Poprzez rozsądne dostosowanie i optymalizację tych czynników producenci mogą poprawić wydajność produkcji i zmniejszyć straty materiału, zapewniając jednocześnie wysoką precyzję. Poniżej przedstawiono kilka kluczowych czynników wpływających na szerokość szczeliny i strategie ich optymalizacji:
Rozmiar ogniska lasera: Rozmiar ogniska lasera bezpośrednio wpływa na średnicę plamki, a im mniejsza plamka, tym węższa szerokość nacięcia. Im dokładniejsze ogniskowanie, tym wyższe stężenie energii wiązki lasera, co poprawia dokładność cięcia. Aby zoptymalizować szerokość nacięcia, ważne jest wybranie obiektywu o odpowiedniej ogniskowej. Ogólnie rzecz biorąc, obiektyw o krótkiej ogniskowej może zapewnić mniejszą średnicę ogniskowania, co pozwala uzyskać bardziej wyrafinowany efekt cięcia. W przypadku różnych materiałów i wymagań dotyczących cięcia rozmiar ogniskowania można zoptymalizować, dostosowując ogniskową, aby zapewnić najlepszy efekt cięcia.
Moc lasera: Moc lasera bezpośrednio określa intensywność energii cieplnej wiązki lasera, która wpływa na topienie, parowanie i efekty cięcia podczas procesu cięcia. Jeśli moc lasera jest zbyt wysoka, łatwo jest spowodować, że nacięcie będzie zbyt szerokie lub nawet przepali materiał; jeśli moc jest zbyt niska, może nie być w stanie całkowicie przeniknąć do materiału, co spowoduje niepełne cięcie. Istotne jest, aby dostosować moc lasera do optymalnej wartości zgodnie z grubością i właściwościami różnych materiałów. Na przykład w przypadku grubszych materiałów moc należy odpowiednio zwiększyć, podczas gdy w przypadku cienkich materiałów moc można zmniejszyć, aby uniknąć zbyt szerokiego nacięcia. Dzięki dokładnej regulacji mocy producenci mogą osiągnąć precyzyjne i wydajne cięcie.
Prędkość cięcia: Prędkość cięcia odgrywa również ważną rolę w cięciu laserowym. Prawidłowe zwiększenie prędkości cięcia może nie tylko zmniejszyć strefę wpływu ciepła i zmniejszyć wpływ stopionego materiału na krawędź cięcia, ale także poprawić wydajność produkcji. Jednak jeśli prędkość cięcia jest zbyt duża, wiązka lasera może nie mieć wystarczająco dużo czasu, aby całkowicie przeniknąć przez materiał, co skutkuje niepełnym cięciem; z drugiej strony zbyt mała prędkość może spowodować, że cięcie będzie zbyt szerokie i wytworzy nadmiar stopu. Aby zoptymalizować efekt cięcia, prędkość cięcia musi być dokładnie dostosowana do rodzaju i grubości materiału, aby zapewnić zminimalizowanie szerokości cięcia.
Rodzaj i ciśnienie gazu pomocniczego: Gaz pomocniczy odgrywa kluczową rolę w cięciu laserowym. Powszechnie stosowanymi gazami pomocniczymi są tlen, azot i powietrze. Tlen może zwiększyć reakcję spalania podczas procesu cięcia i nadaje się do cięcia materiałów takich jak żelazo i stal; azot może zmniejszyć utlenianie i nadaje się do materiałów takich jak stal nierdzewna; powietrze jest szeroko stosowane w różnych materiałach ze względu na swoją ekonomiczność. Oprócz rodzaju gazu, ciśnienie gazu wpływa również na jakość cięcia. Odpowiednie ciśnienie gazu może pomóc usunąć stop i zapobiec jego przywieraniu do krawędzi nacięcia, zmniejszając tym samym szerokość nacięcia. Niższe ciśnienie gazu może spowodować niemożność skutecznego usunięcia stopu i zwiększenia szerokości nacięcia, dlatego należy wybrać odpowiednie ciśnienie i rodzaj gazu, aby zoptymalizować efekt cięcia.
Właściwości materiału: Właściwości różnych materiałów mogą znacząco wpłynąć na dokładność cięcia laserowego. Właściwości materiału, takie jak współczynnik absorpcji, przewodnictwo cieplne i temperatura topnienia, bezpośrednio wpływają na wydajność transmisji wiązki laserowej i jakość cięcia. Materiały o wysokim współczynniku odbicia (takie jak aluminium, miedź itp.) mają tendencję do odbijania i rozpraszania wiązki laserowej, co zmniejsza efekt cięcia. W przypadku tych materiałów konieczna jest optymalizacja parametrów lasera, zwłaszcza w celu zwiększenia gęstości mocy, aby zapewnić, że laser będzie mógł skutecznie penetrować materiał. Z kolei materiały o niskim współczynniku odbicia, takie jak stal, są łatwiejsze do cięcia. Podczas cięcia różnych materiałów producenci powinni dostosować parametry cięcia zgodnie z charakterystyką materiału, aby zapewnić najlepszą jakość cięcia i najmniejszą szerokość nacięcia.
Optymalizacja ścieżki cięcia: Optymalizacja ścieżki cięcia jest również kluczowa dla kontrolowania szerokości nacięcia. Gładka ścieżka cięcia może zmniejszyć błąd wiązki laserowej przy zmianie kierunku i uniknąć nieregularnych nacięć. Szczególnie podczas cięcia złożonych kształtów rozsądne zaprojektowanie ścieżki i zmniejszenie liczby zakrętów i zatrzymań awaryjnych może znacznie poprawić dokładność cięcia. Ponadto optymalizacja strategii podawania i cofania może również pomóc zmniejszyć ablację materiału i uniknąć deformacji nacięcia spowodowanej nadmiernym nagrzewaniem. Podczas projektowania ścieżki należy w jak największym stopniu unikać szybkich zakrętów i nierównych tras, aby zapewnić równomierne rozłożenie energii podczas procesu cięcia, kontrolując w ten sposób szerokość nacięcia.
Dzięki precyzyjnej kontroli i optymalizacji tych kluczowych czynników producenci mogą obniżyć koszty produkcji, poprawić wykorzystanie materiałów i zwiększyć wydajność produkcji, gwarantując jednocześnie wysoką precyzję cięcia.
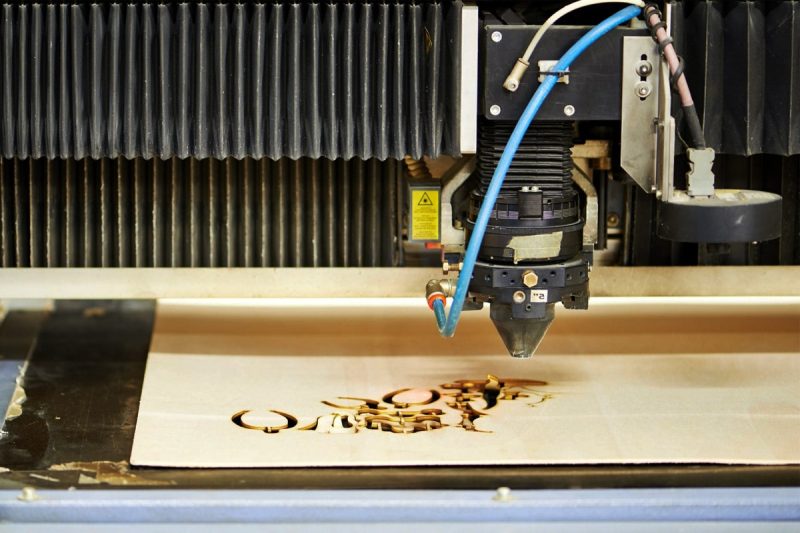
Strategia optymalizacji w celu uzyskania minimalnej szerokości szczeliny
Aby osiągnąć minimalną szerokość szczeliny podczas cięcia laserem CO2, należy rozważyć wiele strategii optymalizacji. Strategie te mogą nie tylko poprawić dokładność cięcia, ale także skutecznie zmniejszyć ilość odpadów materiałowych i poprawić wydajność produkcji. Poniżej przedstawiono kluczowe metody optymalizacji w celu osiągnięcia minimalnej szerokości szczeliny:
Zoptymalizuj układ optyczny: Jakość układu optycznego ma bezpośredni wpływ na efekt skupiania wiązki laserowej, co z kolei wpływa na precyzję nacięcia. Wybór wysokiej jakości soczewki optycznej może zapewnić równomierne skupienie wiązki laserowej na powierzchni materiału docelowego, co pozwoli uzyskać stabilny i precyzyjny efekt cięcia. Użycie soczewki o krótkiej ogniskowej (takiej jak ogniskowa 2,5 cala) jest ważną strategią optymalizacji skupiania wiązki laserowej. Soczewka o krótkiej ogniskowej może skupić mniejszą średnicę plamki, zmniejszając w ten sposób dyfuzję wiązki laserowej i znacznie zmniejszając szerokość nacięcia. Mniejsza plamka może nie tylko poprawić dokładność cięcia, ale także zmniejszyć wpływ termiczny na materiał i zapewnić stabilność podczas procesu cięcia.
Dokładnie dostosuj moc i prędkość lasera: Moc lasera i prędkość cięcia to dwa ważne czynniki wpływające na szerokość nacięcia. Najlepszy efekt cięcia można uzyskać, dokładnie dostosowując kombinację mocy lasera i prędkości. Użycie trybu pulsacyjnego może skrócić czas ciągłego nagrzewania, zmniejszając tym samym strefę wpływu ciepła (HAZ) i zjawisko topnienia na krawędzi nacięcia. Tryb pulsacyjny sprawia, że rozkład energii lasera jest bardziej równomierny i zapobiega problemowi przegrzania spowodowanemu ciągłym wyjściem dużej mocy. Jednocześnie dostosowanie mocy lasera w połączeniu z grubością materiału może zapewnić, że wiązka lasera może całkowicie przeniknąć materiał i kontrolować szerokość nacięcia. W przypadku cieńszych materiałów odpowiednio zmniejsz moc, aby uniknąć nadmiernego gromadzenia się ciepła; w przypadku grubszych materiałów odpowiednio zwiększ moc, aby zapewnić jakość cięcia, ale nadal zwróć uwagę na kontrolowanie szerokości nacięcia.
Dostosuj parametry gazu pomocniczego: Gaz pomocniczy odgrywa ważną rolę w cięciu laserem CO2. Nie tylko pomaga usunąć stop powstający podczas procesu cięcia, ale także kontroluje jakość cięcia poprzez optymalizację ciśnienia gazu. Prawidłowe zwiększenie ciśnienia gazu może skutecznie usunąć żużel powstający podczas procesu cięcia i zapobiec jego przywieraniu do krawędzi nacięcia, utrzymując w ten sposób wąską szerokość nacięcia. Przy wyborze gazu pomocniczego azot jest jednym z powszechnie stosowanych gazów, szczególnie w przypadku materiałów, które muszą zmniejszyć utlenianie i poprawić wykończenie cięcia. Azot może nie tylko skutecznie zmniejszyć utlenianie powierzchni materiału, ale także utrzymać gładkość nacięcia podczas procesu cięcia, uzyskując w ten sposób efekt cięcia wyższej jakości.
Optymalizacja oprogramowania i parametrów CNC: Wysokoprecyzyjne systemy CNC mogą skutecznie poprawić dokładność cięcia laserowego i pomóc zredukować odchylenia cięcia spowodowane błędami mechanicznymi. Korzystając z zaawansowanych systemów CNC, możesz zoptymalizować ścieżkę cięcia i zredukować błędy spowodowane zmianami kierunku wiązki laserowej. Dokładne planowanie ścieżki pomaga zredukować błędy spowodowane zakrętami i nierównymi ścieżkami podczas cięcia. Ponadto, użycie automatycznego systemu ogniskowania jest również ważną strategią optymalizacji szerokości nacięcia. Automatyczny system ogniskowania może automatycznie regulować położenie ogniskowania lasera zgodnie z grubością, kształtem i wymaganiami cięcia materiału, aby zapewnić, że wiązka laserowa jest zawsze skupiona w najlepszej pozycji, unikając w ten sposób nierównych lub zbyt szerokich nacięć spowodowanych nieprawidłową pozycją ogniskowania.
Zmniejsz strefę wpływu ciepła (HAZ): Rozmiar HAZ jest ściśle związany z akumulacją ciepła podczas procesu cięcia laserowego. Nadmierne ciepło może powodować nadmierne topienie powierzchni materiału, zwiększając tym samym szerokość nacięcia i wpływając na jakość cięcia. Aby zmniejszyć strefę wpływu ciepła, skuteczną strategią jest cięcie z dużą prędkością. Cięcie z dużą prędkością może przyspieszyć ruch wiązki laserowej, zmniejszając tym samym akumulację ciepła na powierzchni materiału i zapobiegając topieniu i poszerzaniu się krawędzi nacięcia. Jednak podczas cięcia z dużą prędkością należy upewnić się, że energia wiązki laserowej jest wystarczająca do penetracji materiału. Aby jeszcze bardziej zoptymalizować jakość cięcia, można połączyć technologię chłodzenia, taką jak chłodzenie natryskowe lub podwójny wtrysk gazu, co może skutecznie obniżyć temperaturę obszaru cięcia, uniknąć przegrzania i zapewnić bardziej precyzyjny i stabilny efekt cięcia.
Łącząc powyższe strategie optymalizacji, producenci mogą skutecznie osiągnąć minimalną szerokość szczeliny w cięciu laserem CO2. Dzięki ciągłemu rozwojowi technologii i ciągłej optymalizacji sprzętu, strategie te pomogą w dalszym zwiększaniu dokładności cięcia, zmniejszeniu strat materiału i zwiększeniu wydajności produkcji.
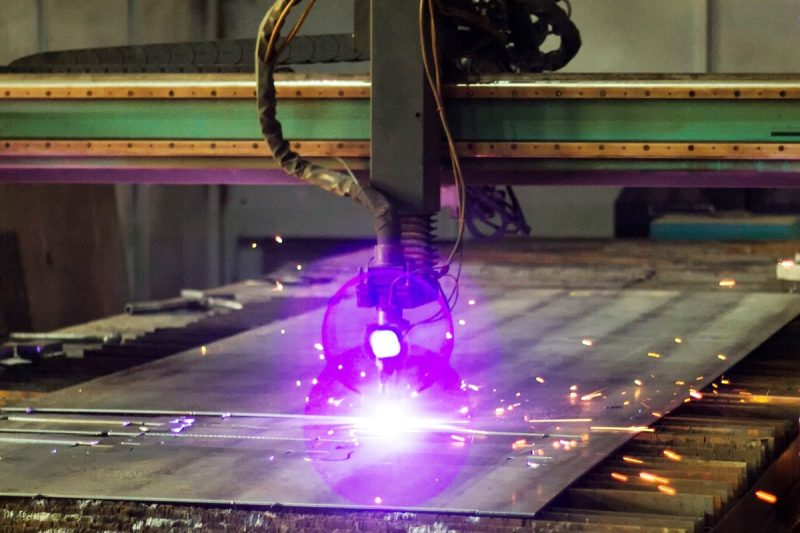
Podsumować
Osiągnięcie minimalnej szerokości szczeliny to nie tylko prosta regulacja parametrów, ale proces wymagający kompleksowego rozważenia wielu czynników. Dzięki dokładnej optymalizacji ogniskowania lasera, ustawienia mocy, prędkości cięcia, rodzaju i ciśnienia gazu pomocniczego oraz kontroli oprogramowania producenci mogą zmaksymalizować wydajność produkcji i zmniejszyć straty materiału, zapewniając jednocześnie jakość cięcia. Precyzyjna regulacja ogniskowania lasera może zapewnić rozmiar plamki obszaru cięcia i uniknąć nadmiernych stref wpływu ciepła podczas procesu cięcia, zapewniając tym samym dokładne i gładkie cięcie. Precyzyjne połączenie mocy i prędkości cięcia może zapobiec nadmiernemu gromadzeniu się ciepła i zmniejszyć wpływ stopu na szerokość cięcia. Odpowiedni gaz pomocniczy może nie tylko usunąć żużel, ale także zapobiec utlenianiu, co dodatkowo poprawia jakość cięcia. Jednocześnie zastosowanie zaawansowanego oprogramowania CNC i technologii automatycznego ogniskowania może stale optymalizować ścieżkę cięcia i ogniskowanie wiązki laserowej, aby zapewnić stabilność i spójność efektu cięcia.
Dzięki ciągłemu rozwojowi technologii wydajność i dokładność sterowania maszynami do cięcia laserem CO2 również stale się poprawiają. Producenci mogą osiągnąć dokładniejsze efekty cięcia poprzez ciągłe dostosowywanie i optymalizowanie powyższych czynników, w połączeniu z ciągłym rozwojem technologii optycznej, zautomatyzowanych systemów sterowania i wydajnej technologii chłodzenia. Ostatecznie osiągnięcie minimalnej szerokości nacięcia nie tylko poprawia dokładność cięcia, ale także przynosi wyższą wydajność produkcji, obniża koszty materiałów i znacznie poprawia korzyści ekonomiczne linii produkcyjnej w długotrwałym użytkowaniu. Dlatego dla użytkowników Maszyny do cięcia laserem CO2Ciągła nauka i doskonalenie tych strategii optymalizacji będzie kluczem do zwiększenia ogólnej zdolności produkcyjnej i konkurencyjności.
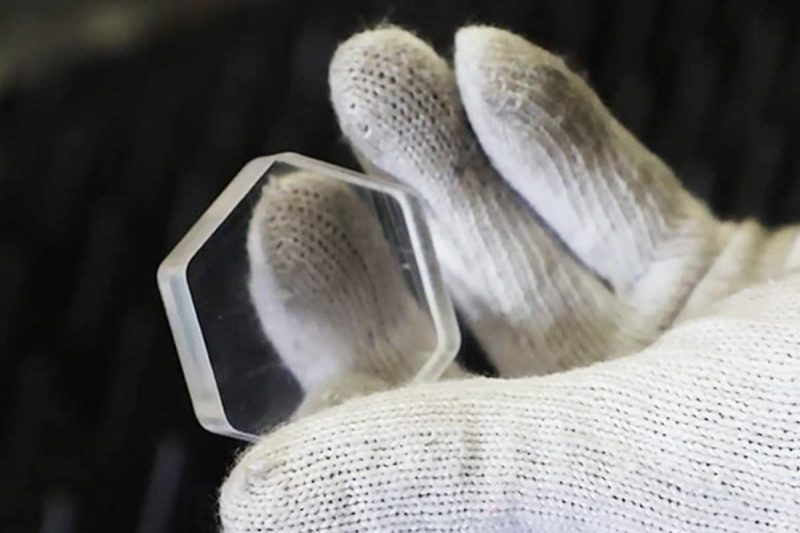
Uzyskaj rozwiązania laserowe
Laser AccTek dostarcza wysoce precyzyjny sprzęt do cięcia laserowego CO2, który obsługuje inteligentne ustawianie ostrości, automatyczną optymalizację ścieżki i wydajną kontrolę gazów pomocniczych w celu zapewnienia minimalnej szerokości nacięcia i osiągnięcia precyzyjnej obróbki. Skontaktuj się z nami aby uzyskać dostosowane rozwiązania w zakresie cięcia laserowego, które zwiększą wydajność produkcji i dokładność przetwarzania!
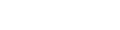
Informacje kontaktowe
- [email protected]
- [email protected]
- +86-19963414011
- Nr 3 Strefa A, strefa przemysłowa Lunzhen, miasto Yucheng, prowincja Shandong.
Uzyskaj rozwiązania laserowe