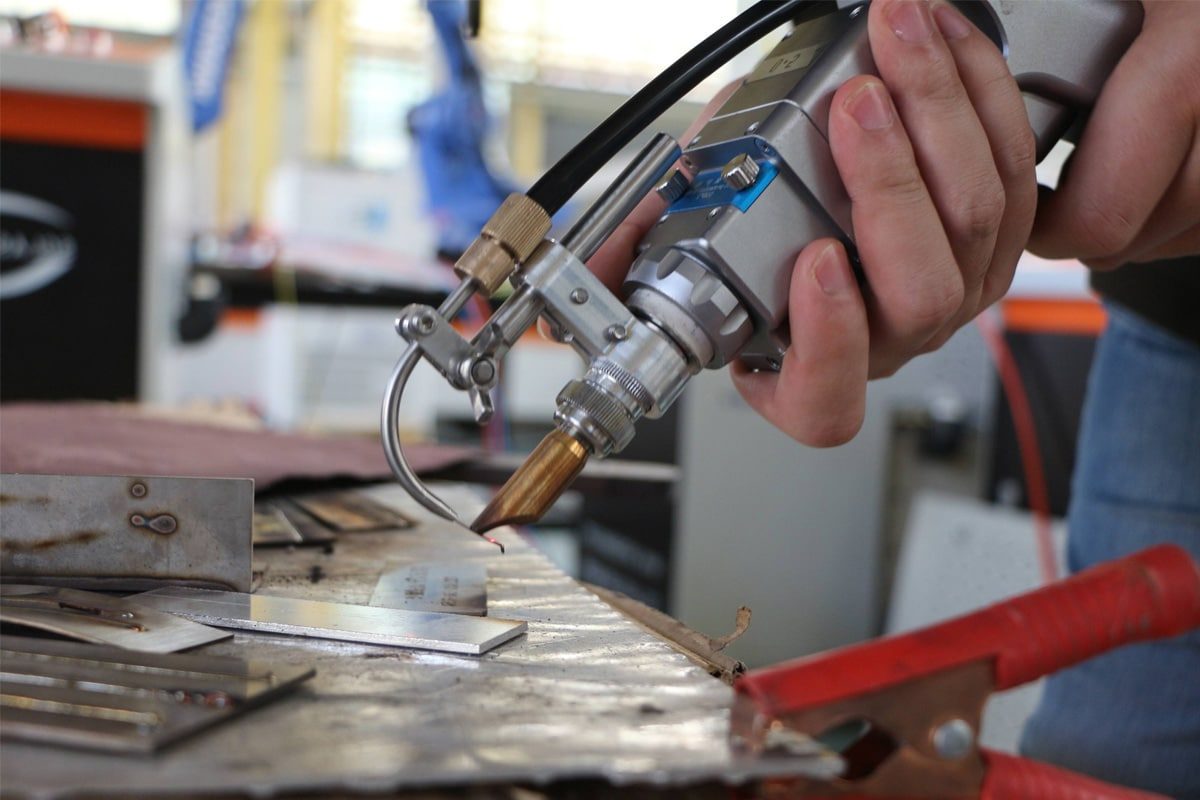
Laser Welding Carbon Steel Guide
Laser welding is an advanced and highly precise welding technology that achieves material fusion by concentrating a high-energy laser beam. Compared with traditional welding methods, laser welding has the advantages of a small heat-affected zone, fast welding speed, and high weld strength, and has been widely used in the field of carbon steel. Carbon steel, as alloy steel with moderate carbon content, has become a common material in many industries due to its excellent mechanical properties, low cost, and good welding adaptability. From automobile manufacturing to construction engineering, to mechanical equipment and energy sectors, carbon steel plays an irreplaceable role. With the continuous advancement of laser welding technology, the welding process of carbon steel has become more efficient and precise, overcoming many limitations in traditional welding. This welding method can not only achieve deep melting welding of materials but also reduce deformation problems and provide more stable and uniform welding effects, enabling it to meet the requirements of stringent industrial standards and special environments. Therefore, the potential and advantages of laser welding in carbon steel applications are increasingly recognized by the industry, and it has become an ideal choice for industrial manufacturers pursuing high-quality and low-cost production.
In this guide, we will explore the laser welding characteristics of carbon steel in depth, from the properties of carbon steel materials to the specific process, equipment selection, and key parameter control of laser welding, to give you a comprehensive understanding of the core points of this technology. In addition, we will also introduce some common challenges and troubleshooting methods in the actual welding process to help you maximize the welding quality. Whether you are a technician, engineer, or reader interested in laser welding, this guide will provide you with practical and detailed information to guide you to better understand and apply the potential and advantages of laser welding technology in carbon steel welding.
Spis treści
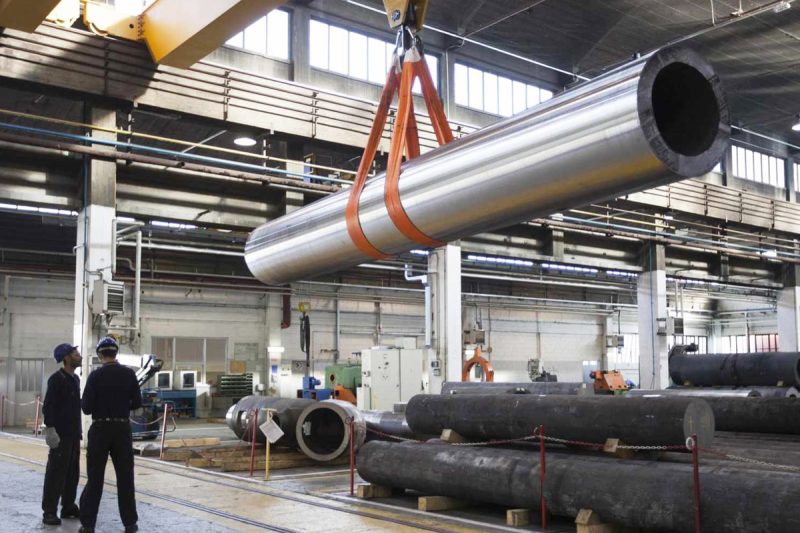
Properties of Carbon Steel
Carbon Steel Properties Overview
Carbon steel is an iron-carbon alloy with a carbon content between 0.02% and 2.1%, which is widely used in various industries. According to the carbon content, carbon steel can be divided into three categories: low carbon steel (carbon content <0.25%), medium carbon steel (carbon content 0.25%-0.6%), and high carbon steel (carbon content >0.6%). Its performance characteristics include good strength and toughness, excellent weldability, and relatively low production cost, making it the material of choice for many application scenarios.
Types and Characteristics of Carbon Steel
- Low carbon steel: has lower strength but excellent ductility, suitable for large-scale structural welding and cold bending. Usually used to manufacture parts that require higher plasticity and forming ability, such as automobile bodies and building structures.
- Medium carbon steel: has good mechanical strength and wear resistance, and is widely used in the manufacture of mechanical parts such as gears, bearings, and cutting tools. Suitable for applications that require a certain degree of strength and toughness.
- High carbon steel: It has high strength and hardness and is often used to make parts that require high hardness and wear resistance, such as knives and springs. However, due to its high carbon content, it is prone to cracks and welding defects during welding, so special processes and precautions need to be taken during the welding process.
Weldability of Carbon Steel
Different types of carbon steel have different weldability. Low carbon steel has the best weldability, is easy to weld, and is not prone to cracks. When welding medium carbon steel, the heat input must be controlled to avoid overheating and affecting the welding performance. Due to its high carbon content, high carbon steel is prone to cracks and welding defects during welding, so special attention must be paid to the welding process, such as using appropriate preheating and post-heat treatment and using suitable welding materials to ensure welding quality and the stability of the overall structure.
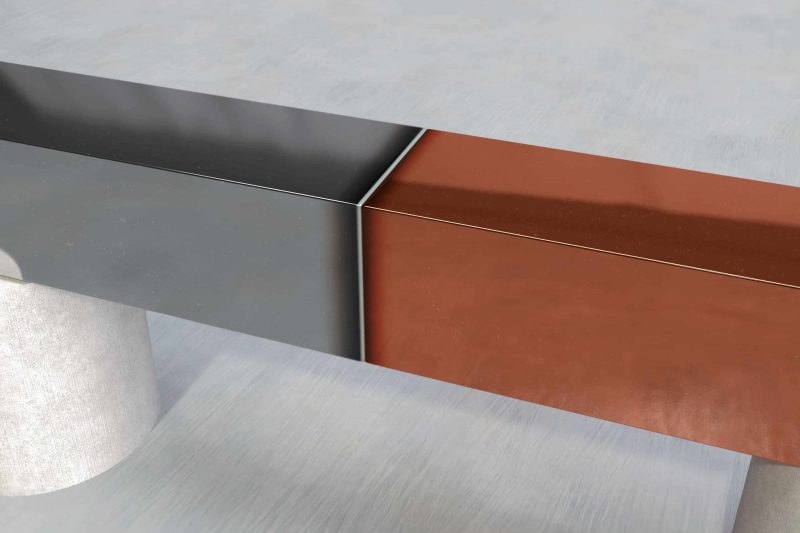
Principle of Laser Welding Carbon Steel
Understanding the Laser Welding Process
Laser welding is a process that uses high-energy laser beams to rapidly heat carbon steel materials. The laser beam is concentrated on the welding area and generates extremely high temperatures instantly, causing the surface of the carbon steel to quickly melt and form a weld. Due to the extremely high energy density of the laser, its heat affected zone (HAZ) is relatively small, thereby reducing thermal deformation of the surrounding unwelded material. This precise control results in significantly improved weld quality, higher strength and good appearance.
Interaction of Laser with Carbon Steel
When the laser beam irradiates the surface of carbon steel, the laser energy is quickly absorbed by the material, causing the surface temperature to rise rapidly. At this time, the carbon steel begins to melt locally, forming a molten pool. As the laser beam moves, the molten pool expands and continues to be heated by the laser. During the cooling process, the molten pool solidifies rapidly to form a dense weld structure. The entire welding process is very fast, and the heat input time is extremely short, so the thermal deformation is small, and high-precision welding can be achieved.
Key Parameters Affecting Carbon Steel Welding
The quality of laser welding is affected by several key parameters:
- Laser power: The higher the laser power, the higher the energy concentration and the higher the melting speed. However, too high power may cause the weld to be too deep or even burn through.
- Welding speed: The adjustment of welding speed directly affects the formation of the molten pool and the width of the weld. Too fast speed may lead to incomplete welding, while too slow speed may cause overheating and deformation.
- Focal length: The laser focal length determines the degree of focus of the laser beam on the surface of the material. The appropriate focal length can ensure that the laser beam is optimally concentrated in the welding area, thereby improving the welding quality.
- Gas shielding: Gas shielding (such as argon or nitrogen) is used during the welding process to prevent oxidation and keep the welding area clean, thereby improving the quality and strength of the weld.
Reasonable adjustment of the above parameters can ensure the stability of the welding process and obtain high-quality welds, thereby meeting the strict requirements of welding quality in different industrial applications.
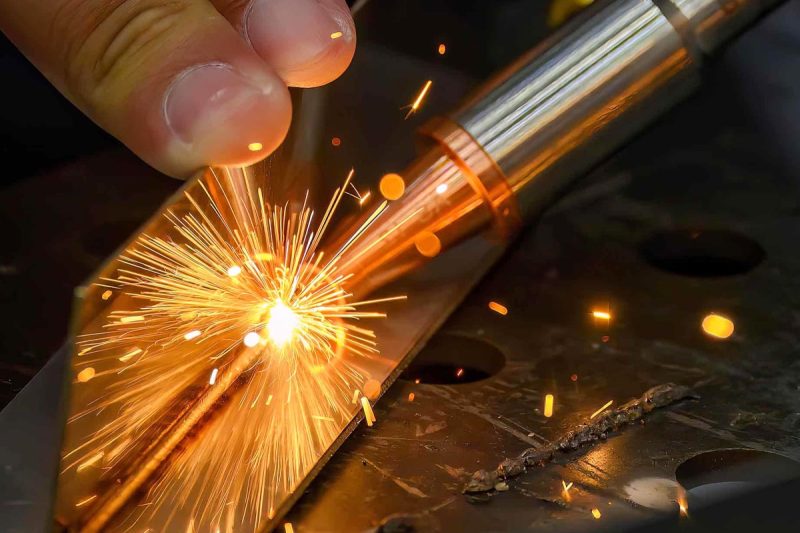
Preparation for Laser Welding of Carbon Steel
Material Selection and Preparation
Selecting the right carbon steel material is the key to successful welding. Carbon steels of different thicknesses and carbon contents have different requirements for laser welding parameters such as heat input, welding speed, and gas shielding. For example, low-carbon steel is suitable for large-scale structural welding and has good weldability, while high-carbon steel is suitable for applications that require high strength and hardness. When selecting materials, the mechanical properties and formability of the material also need to be considered. In addition, ensuring that the surface of the material is flat and free of defects (such as cracks or scratches) will greatly improve the welding effect.
Carbon Steel Joint Design Considerations
Reasonable design of joint form is crucial to the strength and quality of welding. Common joint forms include butt joint, fillet joint, and lap joint. The design of the joint should take into account the stress conditions and processing technology of the weld. For example, the use of butt joints can effectively improve the welding strength, but it is also necessary to ensure that the welding gap is moderate to avoid welding defects. In addition, the angle and size of the joint should be optimized according to actual needs to improve the stability and consistency of welding.
Surface Cleaning and Pre-Welding
Before welding, it is very important to ensure the cleanliness of the carbon steel surface. Impurities such as oil, oxide layer, and rust on the surface should be removed to ensure that the laser beam can effectively penetrate the material during the welding process and prevent welding defects. Physical methods (such as mechanical grinding, and sandblasting) or chemical cleaning agents can be used for surface treatment to ensure that the welding area is clean and smooth. In addition, pre-welding treatment can also include drying and heat treatment to reduce stress concentration during welding and further improve welding quality and structural strength.
Through the above preparations, the welding quality of laser welding of carbon steel can be effectively improved and the smooth progress of the welding process can be ensured.

Carbon Steel Laser Welding Equipment
Types of Laser Welding Systems
Common laser welding systems include fiber laser generators, CO2 laser generators, and semiconductor laser generators. Among them, fiber laser generators are widely used for their high efficiency and excellent beam quality, especially in carbon steel welding, which can achieve smaller welds and higher welding speeds. CO2 laser generators are suitable for a wider range of materials, but their beam quality and efficiency are slightly inferior to those of fiber laser generators. Semiconductor laser generators are suitable for low-power applications and are usually used for welding small equipment.
Understanding the differences between various laser welding systems can help you choose the best solution for your project. AccTek’s fiber laser welders excel in carbon steel welding applications with their high efficiency and excellent beam quality. Our fiber laser systems not only achieve smaller welds but also maintain consistent and accurate welding at high speeds, making them ideal for processing needs that require high quality and high efficiency. Whether it’s a small device that requires precision processing or a high-power industrial application, AccTek’s fiber laser welders can meet your demanding welding needs. Welcome to consult, our team will provide you with the best solution.
Choice of Laser Source and Parameters
Selecting the appropriate laser source power and welding parameters is the key to ensuring welding quality. Generally speaking, for thicker carbon steel materials (such as more than 3 mm), it is recommended to use a laser power of more than 3kW to ensure sufficient heat input and penetration. At the same time, the welding speed, focal length, and spot diameter should be adjusted according to the welding process requirements to achieve the best welding effect. Reasonable parameter selection can effectively reduce welding defects and improve welding strength and quality.
Sprzęt pomocniczy i akcesoria
Auxiliary equipment is equally important in the laser welding process. Gas protection equipment (such as argon or nitrogen) is used to protect the welding area, prevent oxidation and contamination, and ensure the purity of the weld. In addition, the cooling system helps control the temperature of the laser generator and welded parts during the welding process, preventing overheating, thereby maintaining equipment performance and extending service life. By properly configuring auxiliary equipment and accessories, the stability and reliability of the welding process can be significantly improved.
In summary, selecting suitable laser welding equipment and parameters, combined with effective auxiliary facilities, is the key to achieving high-quality carbon steel laser welding.
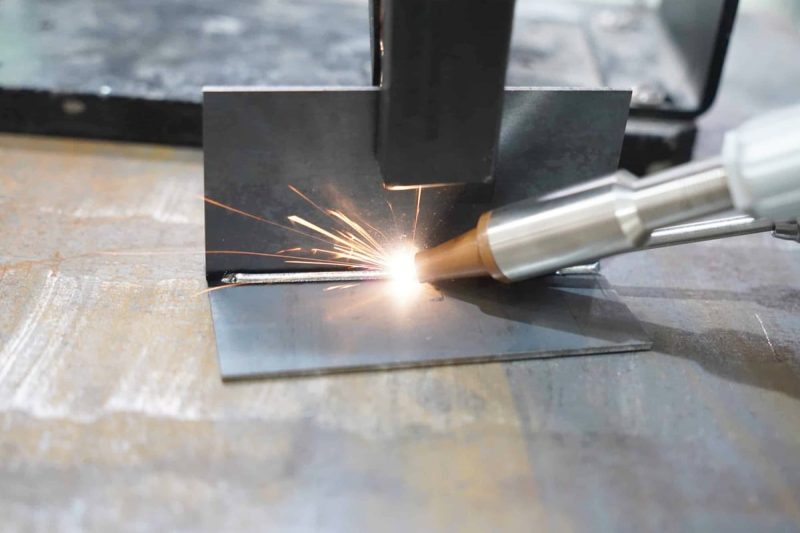
Common Challenges and Troubleshooting
Quality Assurance and Inspection
The first step to ensure welding quality is to conduct a comprehensive quality inspection. Using non-destructive testing techniques (such as ultrasonic testing, X-ray testing, etc.) can effectively identify potential defects in the weld. By regularly visually inspecting the weld surface, operators should pay attention to whether there are pores, cracks, or other surface defects. These measures ensure that potential problems in the welding process are discovered at an early stage, thereby preventing them from seriously affecting the integrity of the structure later.
Welding Quality Assessment
Weld quality assessment is a systematic process that includes regular checks on weld strength and appearance. By evaluating the mechanical properties and visual appearance of welds, it is ensured that the quality of welds meets industry standards and customer requirements. In addition, mechanical tests such as tensile tests and impact tests can quantify weld strength and further ensure the reliability of welded structures.
Nondestructive Testing Methods
Nondestructive testing methods play an important role in welding quality control. Ultrasonic testing can detect defects inside the weld, while X-ray testing is suitable for observing the internal structure of the weld. These testing methods can quickly and accurately identify potential welding defects, helping engineers make timely adjustments to improve welding quality and enhance the safety of the finished product.
Quality Control Measures
Effective quality control measures are key to ensuring welding quality. Regular maintenance of welding equipment can maintain the optimal performance of the equipment and prevent welding defects caused by equipment failure. In addition, optimizing process parameters such as laser power, welding speed, and gas shielding can greatly improve welding quality. Implementing sampling inspections and regularly checking the quality of welded parts can ensure that welding standards are always met during production, thereby reducing the risk of rework and scrap. Through these comprehensive measures, challenges in the welding process can be effectively managed to ensure the quality and safety of the final product.
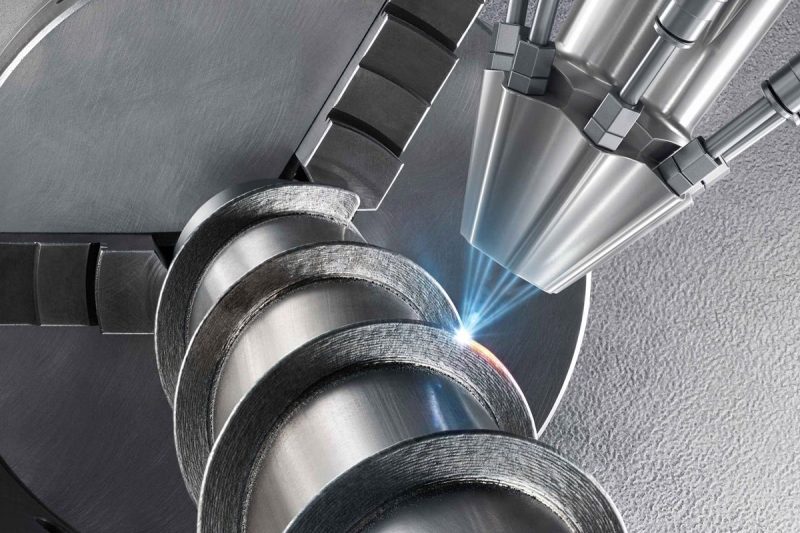
Application of Laser Welding Carbon Steel
Auto Industry
- Frame assembly: Laser welding plays a key role in the manufacture of frame assemblies. Its high welding strength and production efficiency ensure the structural safety and durability of the frame while reducing material deformation and enhancing the overall performance of the vehicle body.
- Exhaust system: In the manufacture of the exhaust system, laser welding can achieve efficient and precise welding, and improve the sealing and durability of the exhaust pipe to meet automotive emission standards and safety requirements.
Architecture
- Steel structure: In the construction industry, laser welding is widely used in the manufacture of steel structures, which can provide high-quality connections, reduce weld defects, and enhance the seismic resistance and overall stability of buildings.
- Pipeline: For pipeline welding in large projects, laser welding technology reduces construction time and cost with its fast welding speed and excellent welding quality, ensuring the smooth progress of the project.
Mechanical Equipment Manufacturing
Laser welding is crucial in mechanical equipment manufacturing, especially in the manufacture of high-precision mechanical equipment (such as CNC machine tools and industrial robots). It can achieve fine welds, improve the functionality and reliability of mechanical parts, and ensure the superior performance of the equipment.
Sektor energetyczny
- Oil and gas pipelines: In the energy industry, laser welding provides an efficient seamless welding solution for oil and gas pipelines, ensuring the pressure resistance and sealing of pipelines under extreme conditions and reducing the risk of leakage.
- Power plants: In power plants, laser welding technology ensures the safe and stable operation of equipment, improves welding quality, reduces maintenance costs, and ensures the reliability of energy delivery.
Shipbuilding and Maritime Industry
The application of laser welding in the shipbuilding and shipping industries enables it to meet the high requirements of welding strength and durability, ensuring the structural integrity of ships in harsh environments. Through this welding technology, the corrosion resistance and service life of ships can be improved, and the overall operational efficiency can be improved.
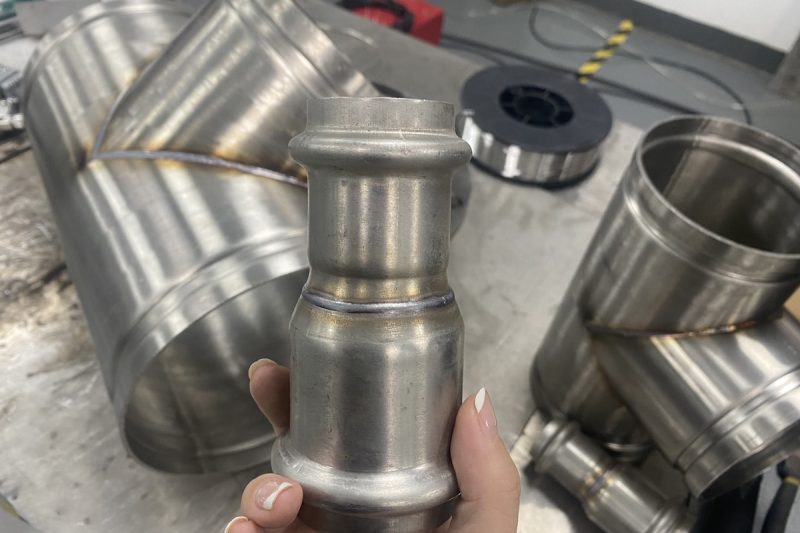
Best Practices and Tips
Proper Handling and Storage of Carbon Steel Materials
When handling and storing carbon steel materials, they need to be placed in a dry, ventilated environment to avoid moisture and pollution to prevent rust or oxidation on the material surface. This can significantly reduce the cleaning work before welding and improve welding efficiency. Regularly check the environmental conditions in storage areas and take protective measures, such as using rust inhibitors or covering materials, to ensure the long-term stability of the materials.
Carbon Steel Welding Parameter Optimization
Optimization of welding parameters is crucial to welding quality. Through systematic experiments, the optimal laser power, welding speed, and focal length can be determined to maximize the strength and aesthetics of the weld. During the actual welding process, fine-tuning of parameters is performed, and the welding effect is continuously monitored according to the thickness, type, and environmental conditions of the material to achieve the best results.
Post-Weld Processing and Finishing Technology
After welding, proper deburring and surface treatment should be performed to improve the aesthetics and durability of the welded parts. Commonly used treatment techniques include polishing, sandblasting, and coating, which can remove spatter and oxide layers generated during welding, enhance the corrosion resistance of the welded parts, and improve the appearance to meet customer requirements.
Laser Welding Machine Maintenance
To ensure the stable operation of the laser welding machine, regular maintenance of the equipment is essential. Maintenance includes checking the laser optical path, cleaning optical components, calibrating the laser output power, etc. In addition, regularly update the software and firmware to maintain the technological advancement of the equipment, extend the service life of the equipment, and reduce the failure rate. Through good maintenance, ensure that the welding quality is always in the best condition.
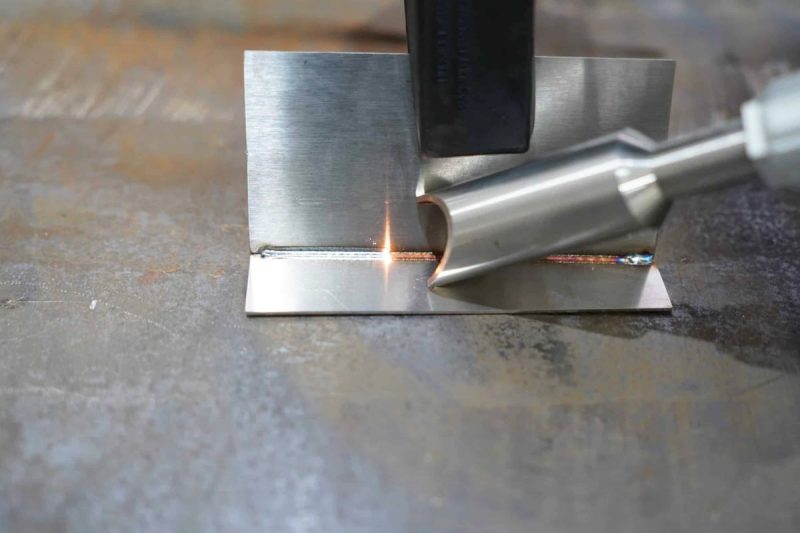
Względy bezpieczeństwa
Hazards Associated with Laser Welding
During laser welding, operators are exposed to a variety of potential dangers due to the use of high-energy laser beams. Among them, the strong light produced by the laser can cause vision damage, and the high temperature during welding may cause burns or fires. In addition, the smoke and harmful gases produced during welding may also have an impact on health. Therefore, it is crucial to develop and strictly follow safety precautions.
Sprzęt ochrony osobistej (ŚOI)
Operators should wear appropriate personal protective equipment (PPE) during welding operations to ensure comprehensive protection. Protective glasses are necessary to effectively prevent eye damage from strong light and lasers. Gloves and protective clothing should be made of high-temperature resistant and flame-retardant materials to avoid accidents caused by thermal burns and flames. Depending on the working environment, respiratory protection equipment may also be necessary to protect operators from harmful fumes and gases.
Safety Protocols and Guidelines
Following the safety protocols and guidelines in the operator’s manual is key to ensuring safe operation. Operators should be trained and familiar with the operating procedures of welding equipment and its potential hazards. The workplace should be inspected regularly to ensure that safety standards are met, including ventilation, firefighting equipment, and first aid facilities. In addition, emergency procedures should be developed to ensure that an emergency response can be quickly and effectively responded to in the event of an accident, minimizing personal injury and property damage.
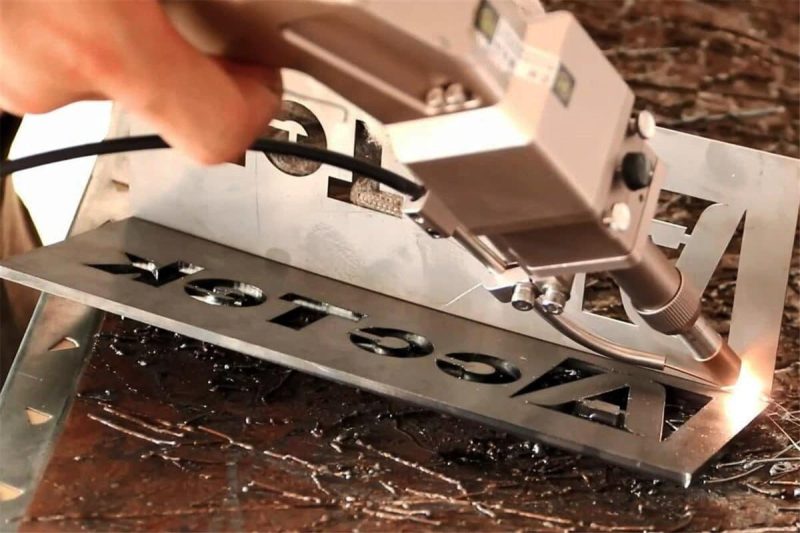
Podsumować
Laser welding of carbon steel is an efficient and precise welding technology widely used in multiple industries such as automotive manufacturing, construction, and energy. The advantage lies in the ability to achieve high-quality welds while reducing heat-affected zones and material distortion. By selecting appropriate equipment and process parameters, and implementing strict quality control and safety measures, laser welding can significantly improve welding efficiency, reduce production costs, and ensure the strength and durability of welded structures. The continuous advancement of this technology also provides more possibilities for future industrial applications.
Choosing the right laser welding equipment and process is the key to improving production efficiency and welding quality. At AccTek, we provide efficient and reliable laser welding solutions dedicated to meeting your business needs. Our team will tailor the most suitable equipment configuration for you and provide continuous technical support to ensure that your operation is always in the best condition. Let us work together to improve welding quality, reduce operating costs, and move towards sustainable development together. Contact AccTek now to start your new chapter in laser welding!
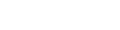
Informacje kontaktowe
- [email protected]
- [email protected]
- +86-19963414011
- Nr 3 Strefa A, strefa przemysłowa Lunzhen, miasto Yucheng, prowincja Shandong.
Uzyskaj rozwiązania laserowe